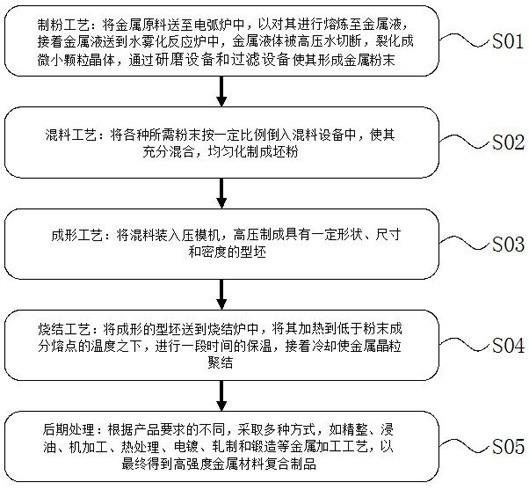
1.本发明涉及金属复合材料技术领域,特别涉及一种高性能金属复合材料及其制备方法。
背景技术:2.金属复合材料是指利用复合技术或多种、化学、力学性能不同的金属在界面上实现冶金结合而形成的复合材料,其极大地改善单一金属材料的热膨胀性、强度、断裂韧性、冲击韧性、耐磨损性、电性能、磁性能等诸多性能,因而被广泛应用到产品广泛应用于石油、化工、船舶、冶金、矿山、机械制造、电力、水利、交通、环保、酿造、制药等工业领域。
3.金属复合材料需要经过熔炼、过滤以及混合等多道工序,在物料混合的过程中,需要逐一添加各类所需的金属粉末,操作较为繁琐,且因上一道研磨工序的不完善性,金属粉末中含有少量的杂质,过滤组件对其进行拦截,不仅易影响金属粉末物料的配比,且长此以往,易造成过滤设备饱和堵塞,影响其过滤效果,进而易逐渐导致制备效率的降低。
4.针对以上问题,对现有装置进行了改进,提出了一种高性能金属复合材料及其制备方法。
技术实现要素:5.本发明的目的在于提供一种高性能金属复合材料及其制备方法,解决了背景技术中金属复合材料需要经过熔炼、过滤以及混合等多道工序,在物料混合的过程中,需要逐一添加各类所需的金属粉末,操作较为繁琐,且因上一道研磨工序的不完善性,金属粉末中含有少量的杂质,过滤组件对其进行拦截,不仅易影响金属粉末物料的配比,且长此以往,易造成过滤设备饱和堵塞,影响其过滤效果,进而易逐渐导致制备效率的降低的问题。
6.为实现上述目的,本发明提供如下技术方案:一种高性能金属复合材料,包括按质量分数计的以下成分:石墨烯17份、碳纳米管7份、聚丙烯54份、增韧剂11份、金属粉77份、膨化剂0.3份、矿物填料23份、耐刮擦助剂3份和抗老化剂1份;一种高性能金属复合材料的制备方法包括以下步骤:s01:制粉工艺:将金属原料送至电弧炉中,以对其进行熔炼至金属液,接着金属液送到水雾化反应炉中,金属液体被高压水切断,裂化成微小颗粒晶体,通过传送设备和过滤设备使其形成金属粉末;s02:混料工艺:将各种所需粉末按一定比例倒入混料设备中,使其充分混合,均匀化制成坯粉;s03:成形工艺:将混料装入压模机,高压制成具有一定形状、尺寸和密度的型坯;s04:烧结工艺:将成形的型坯送到烧结炉中,将其加热到低于粉末成分熔点的温度之下,进行一段时间的保温,接着冷却使金属晶粒聚结;s05:后期处理:根据产品要求的不同,采取多种方式,如精整、浸油、机加工、热处理、电镀、轧制和锻造等金属加工工艺,以最终得到高强度金属材料复合制品。
7.进一步地,混料设备的上端设置有传送设备,传送设备设置有四组,传送设备的下端设置有过滤设备,过滤设备的两侧均设置有调设组件,调设组件的上表面设置有吊接杆,吊接杆的一端与传送设备的下表面相连接。
8.进一步地,传送设备包括传送直框和设置在传送直框内侧的传送带,传送直框的一端设置有研磨组件,研磨组件的内部开设有研磨室,且研磨室对准在传送带的一端,混料设备包括混料筒和设置在混料筒上表面的混料端口,混料端口的侧表面设置有回收盒,回收盒设置有四组,回收盒与过滤设备相对应,回收盒的一侧安装有导料接板,回收盒的侧表面开设有连接通孔,连接通孔与导料接板相对应,回收盒的内部设置有回收室,回收室的内部设置有转轮导向件。
9.进一步地,过滤设备包括设置在混料设备和传送设备之间的柄框板和设置在柄框板内侧的过滤网板,柄框板两端的上下表面均开设有对接滑槽,柄框板的两侧端均开设有限位滑槽,对接滑槽的内表面设置有导向小块,限位滑槽的内侧开设有辅助推移长槽。
10.进一步地,调设组件包括卡设在柄框板外侧的u形夹设块和安装在u形夹设块一端的转板块,u形夹设块的内侧设置有卡接滑块,卡接滑块与限位滑槽相连接,转板块的一侧设置有摆动组件,摆动组件的一侧安装有摆动臂杆,摆动臂杆一端的侧表面设置有辅助小杆,辅助小杆设置有三组,u形夹设块上下表面的中央均设置有对接滑块,对接滑块与对接滑槽相匹配,对接滑块的内侧开设有容纳槽,容纳槽的内部设置有回位组件,辅助小杆的一端套设有活动转轮,活动转轮与辅助推移长槽相连接,辅助小杆的一侧设置有连接弹簧,连接弹簧的一端与限位滑槽的侧表面相连接。
11.进一步地,回位组件包括转动滚柱和设置在转动滚柱两端的驱动转轴,转动滚柱通过驱动转轴与容纳槽的内壁相连接,转动滚柱的表面开设有弧形导向槽,弧形导向槽设置有两组,两组弧形导向槽之间开设有转向直槽,转向直槽设置有两组,两组弧形导向槽和两组转向直槽相互连通,导向小块与弧形导向槽和转向直槽相连接。
12.进一步地,摆动组件包括安装在转板块一侧的定位环块和设置在定位环块内侧的中心盘,中心盘的侧表面开设有调节敞口,中心盘的内部安装有齿轮盘,定位环块的内侧开设有匹配容纳开口槽,匹配容纳开口槽设置有四组,匹配容纳开口槽与调节敞口相对应,匹配容纳开口槽的内底面设置有驱动转盘,驱动转盘的侧表面安装有推移转齿杆,推移转齿杆与齿轮盘相连接,中心盘的上表面安装有活动转盘,活动转盘的中央设置有驱动杆,驱动杆的一端与齿轮盘的中央相连接,活动转盘的一侧设置有延伸杆,延伸杆的一端与摆动臂杆相连接。
13.进一步地,u形夹设块的端面安装有套设盘块,套设盘块的侧表面安装有限位滑节块,转板块的侧表面开设有限位套接转槽,限位套接转槽与套设盘块和限位滑节块相连接,回收室包括开设在回收盒上表面的通入槽和开设在通入槽底端的弧形承接槽。
14.进一步地,转轮导向件包括安装在通入槽内侧的转杆和设置在转杆内部的转动调节轴,转杆的外表面套设有套接环,套接环的外表面设置有摆向导料杆,摆向导料杆的两侧均开设有导料递向槽,套接环的侧表面开设有转向导流槽,导料递向槽与转向导流槽相连通,导料递向槽的一端与连接通孔相对应。
15.与现有技术相比,本发明的有益效果是:1.本发明提出的一种高性能金属复合材料及其制备方法,回收盒与过滤设备相对
应,回收盒的一侧安装有导料接板,回收盒的侧表面开设有连接通孔,连接通孔与导料接板相对应,回收盒的内部设置有回收室,回收室的内部设置有转轮导向件,过滤设备包括设置在混料设备和传送设备之间的柄框板和设置在柄框板内侧的过滤网板,柄框板两端的上下表面均开设有对接滑槽,柄框板的两侧端均开设有限位滑槽,对接滑槽的内表面设置有导向小块,限位滑槽的内侧开设有辅助推移长槽,将所需的金属块放置在传送带上,通过传送将其投入研磨室至,将其研磨至粉体后顺着研磨室的下开口落至过滤网板的表面,研磨后的金属粉末顺着过滤网板掉落至混料筒的内部,未研磨完全的金属颗粒拦截在过滤网板的上表面,传送设备设置有四组,进而可同时投放四组不同类的金属粉末至混料筒中,以便于将各种所需金属粉末按一定比例混合,使其均匀化制成坯粉,以快速递进下一道工序,利于提升制备速率。
16.2.本发明提出的一种高性能金属复合材料及其制备方法,摆动组件包括安装在转板块一侧的定位环块和设置在定位环块内侧的中心盘,中心盘的侧表面开设有调节敞口,中心盘的内部安装有齿轮盘,定位环块的内侧开设有匹配容纳开口槽,匹配容纳开口槽设置有四组,匹配容纳开口槽与调节敞口相对应,匹配容纳开口槽的内底面设置有驱动转盘,驱动转盘的侧表面安装有推移转齿杆,推移转齿杆与齿轮盘相连接,中心盘的上表面安装有活动转盘,活动转盘的中央设置有驱动杆,驱动杆的一端与齿轮盘的中央相连接,活动转盘的一侧设置有延伸杆,延伸杆的一端与摆动臂杆相连接,当过滤网板上表面的金属颗粒饱和时,启动驱动转轴,转动滚柱在容纳槽的内部进行转动,利用弧形导向槽和导向小块的连接,弧形导向槽对导向小块进行牵引导向,使柄框板整体沿着u形夹设块的内侧进行平移,通过卡接滑块和三组辅助小杆对其进行限位,使过滤设备向混料端口的外侧平移,且利用活动转轮沿着辅助推移长槽的滚动,以提升过滤设备平移时的顺畅度,再启动驱动转盘,推移转齿杆带动齿轮盘沿着中心盘的内侧进行转动,齿轮盘带动活动转盘进行转动,使摆动臂杆以活动转盘为轴心进行摆动,利用限位套接转槽与套设盘块和限位滑节块的连接,u形夹设块带动过滤设备整体以转板块为轴心进行摆动,且三组辅助小杆对过滤设备的一端进行支托,与此同时,过滤网板上表面的金属颗粒滚至回收室的内部,推移转齿杆带动齿轮盘回转,过滤设备恢复到水平状态,再次转动驱动转轴,导向小块移至弧形导向槽的一端进入转向直槽中,利用连接弹簧的弹性,使导向小块滑向转向直槽的另一端,过滤设备快速恢复原位,进而以便于快速清理未研磨完全的金属颗粒,利于提升过滤网板的过滤效果,进一步提升制备速率。
17.3.本发明提出的一种高性能金属复合材料及其制备方法,u形夹设块的端面安装有套设盘块,套设盘块的侧表面安装有限位滑节块,转板块的侧表面开设有限位套接转槽,限位套接转槽与套设盘块和限位滑节块相连接,回收室包括开设在回收盒上表面的通入槽和开设在通入槽底端的弧形承接槽,转轮导向件包括安装在通入槽内侧的转杆和设置在转杆内部的转动调节轴,转杆的外表面套设有套接环,套接环的外表面设置有摆向导料杆,摆向导料杆的两侧均开设有导料递向槽,套接环的侧表面开设有转向导流槽,导料递向槽与转向导流槽相连通,导料递向槽的一端与连接通孔相对应,金属颗粒堆积在通入槽和弧形承接槽中,当需要对金属颗粒进行回收时,启动转动调节轴,带动摆向导料杆的一端不断刮接弧形承接槽的底部,弧形承接槽内部的金属颗粒被收进导料递向槽中,随着转杆的转动,金属颗粒沿着转向导流槽进入另一个导料递向槽中,当摆向导料杆的一端对准连接通孔
时,金属颗粒沿着导料接板排出回收室,利用弧形承接槽的弧形贴面,通入槽中的金属颗粒自动填补弧形承接槽的空缺口,以便于快速回收金属颗粒,无需手动操作,将其再次进行研磨,以避免影响各类物料的配比。
附图说明
18.图1为本发明高性能金属复合材料制备方法的制备流程图;图2为本发明高性能金属复合材料制备方法整体结构示意图;图3为本发明高性能金属复合材料制备方法传送设备结构示意图;图4为本发明高性能金属复合材料制备方法混料设备结构示意图;图5为本发明高性能金属复合材料制备方法过滤设备结构示意图;图6为本发明高性能金属复合材料制备方法调设组件结构示意图;图7为本发明高性能金属复合材料制备方法回位组件结构示意图;图8为本发明图6的b处放大图;图9为本发明图5的a处放大图;图10为本发明高性能金属复合材料制备方法辅助推移长槽结构示意图;图11为本发明高性能金属复合材料制备方法摆动组件拆分结构示意图;图12为本发明高性能金属复合材料制备方法限位套接转槽结构示意图;图13为本发明高性能金属复合材料制备方法回收室内部结构示意图;图14为本发明高性能金属复合材料制备方法转轮导向件结构示意图。
19.图中:1、混料设备;11、混料筒;12、混料端口;13、回收盒;14、导料接板;15、连接通孔;16、回收室;161、通入槽;162、弧形承接槽;17、转轮导向件;171、转杆;172、转动调节轴;173、套接环;174、摆向导料杆;175、导料递向槽;176、转向导流槽;2、传送设备;21、传送直框;22、传送带;23、研磨组件;24、研磨室;3、过滤设备;31、柄框板;32、过滤网板;33、对接滑槽;34、限位滑槽;35、导向小块;36、辅助推移长槽;4、调设组件;41、u形夹设块;411、卡接滑块;412、套设盘块;413、限位滑节块;42、转板块;421、限位套接转槽;43、摆动组件;431、中心盘;4311、活动转盘;4312、驱动杆;4313、延伸杆;432、定位环块;433、调节敞口;434、齿轮盘;435、匹配容纳开口槽;436、驱动转盘;437、推移转齿杆;44、摆动臂杆;45、辅助小杆;451、活动转轮;452、连接弹簧;46、对接滑块;47、容纳槽;48、回位组件;481、转动滚柱;482、驱动转轴;483、弧形导向槽;484、转向直槽;5、吊接杆。
具体实施方式
20.下面将结合本发明实施例中的附图,对本发明实施例中的技术方案进行清楚、完整地描述,显然,所描述的实施例仅仅是本发明一部分实施例,而不是全部的实施例。基于本发明中的实施例,本领域普通技术人员在没有做出创造性劳动前提下所获得的所有其他实施例,都属于本发明保护的范围。
21.为了解决在物料混合的过程中,需要逐一添加各类所需的金属粉末,操作较为繁琐的技术问题,如图1-5所示,提供以下优选技术方案:一种高性能金属复合材料,包括按质量分数计的以下成分:石墨烯17份、碳纳米管7份、聚丙烯54份、增韧剂11份、金属粉77份、膨化剂0.3份、矿物填料23份、耐刮擦助剂3份和
抗老化剂1份;一种高性能金属复合材料的制备方法包括以下步骤:s01:制粉工艺:将金属原料送至电弧炉中,以对其进行熔炼至金属液,接着金属液送到水雾化反应炉中,金属液体被高压水切断,裂化成微小颗粒晶体,通过传送设备2和过滤设备3使其形成金属粉末;s02:混料工艺:将各种所需粉末按一定比例倒入混料设备1中,使其充分混合,均匀化制成坯粉;s03:成形工艺:将混料装入压模机,高压制成具有一定形状、尺寸和密度的型坯;s04:烧结工艺:将成形的型坯送到烧结炉中,将其加热到低于粉末成分熔点的温度之下,进行一段时间的保温,接着冷却使金属晶粒聚结;s05:后期处理:根据产品要求的不同,采取多种方式,如精整、浸油、机加工、热处理、电镀、轧制和锻造等金属加工工艺,以最终得到高强度金属材料复合制品。
22.混料设备1的上端设置有传送设备2,传送设备2设置有四组,传送设备2的下端设置有过滤设备3,过滤设备3的两侧均设置有调设组件4,调设组件4的上表面设置有吊接杆5,吊接杆5的一端与传送设备2的下表面相连接,传送设备2包括传送直框21和设置在传送直框21内侧的传送带22,传送直框21的一端设置有研磨组件23,研磨组件23的内部开设有研磨室24,且研磨室24对准在传送带22的一端,混料设备1包括混料筒11和设置在混料筒11上表面的混料端口12,混料端口12的侧表面设置有回收盒13,回收盒13设置有四组,回收盒13与过滤设备3相对应,回收盒13的一侧安装有导料接板14,回收盒13的侧表面开设有连接通孔15,连接通孔15与导料接板14相对应,回收盒13的内部设置有回收室16,回收室16的内部设置有转轮导向件17,过滤设备3包括设置在混料设备1和传送设备2之间的柄框板31和设置在柄框板31内侧的过滤网板32,柄框板31两端的上下表面均开设有对接滑槽33,柄框板31的两侧端均开设有限位滑槽34,对接滑槽33的内表面设置有导向小块35,限位滑槽34的内侧开设有辅助推移长槽36。
23.具体的,将所需的金属块放置在传送带22上,通过传送将其投入研磨室24至,将其研磨至粉体后顺着研磨室24的下开口落至过滤网板32的表面,研磨后的金属粉末顺着过滤网板32掉落至混料筒11的内部,未研磨完全的金属颗粒拦截在过滤网板32的上表面,传送设备2设置有四组,进而可同时投放四组不同类的金属粉末至混料筒11中,以便于将各种所需金属粉末按一定比例混合,使其均匀化制成坯粉,以快速递进下一道工序,利于提升制备速率。
24.为了解决金属粉末中含有少量的杂质,过滤组件对其进行拦截,易造成过滤设备饱和堵塞,影响其过滤效果,进而易逐渐导致制备效率的降低的技术问题,如图6-12所示,提供以下优选技术方案:调设组件4包括卡设在柄框板31外侧的u形夹设块41和安装在u形夹设块41一端的转板块42,u形夹设块41的内侧设置有卡接滑块411,卡接滑块411与限位滑槽34相连接,转板块42的一侧设置有摆动组件43,摆动组件43的一侧安装有摆动臂杆44,摆动臂杆44一端的侧表面设置有辅助小杆45,辅助小杆45设置有三组,u形夹设块41上下表面的中央均设置有对接滑块46,对接滑块46与对接滑槽33相匹配,对接滑块46的内侧开设有容纳槽47,容纳槽47的内部设置有回位组件48,辅助小杆45的一端套设有活动转轮451,活动转轮451与辅
助推移长槽36相连接,辅助小杆45的一侧设置有连接弹簧452,连接弹簧452的一端与限位滑槽34的侧表面相连接,回位组件48包括转动滚柱481和设置在转动滚柱481两端的驱动转轴482,转动滚柱481通过驱动转轴482与容纳槽47的内壁相连接,转动滚柱481的表面开设有弧形导向槽483,弧形导向槽483设置有两组,两组弧形导向槽483之间开设有转向直槽484,转向直槽484设置有两组,两组弧形导向槽483和两组转向直槽484相互连通,导向小块35与弧形导向槽483和转向直槽484相连接。
25.摆动组件43包括安装在转板块42一侧的定位环块432和设置在定位环块432内侧的中心盘431,中心盘431的侧表面开设有调节敞口433,中心盘431的内部安装有齿轮盘434,定位环块432的内侧开设有匹配容纳开口槽435,匹配容纳开口槽435设置有四组,匹配容纳开口槽435与调节敞口433相对应,匹配容纳开口槽435的内底面设置有驱动转盘436,驱动转盘436的侧表面安装有推移转齿杆437,推移转齿杆437与齿轮盘434相连接,中心盘431的上表面安装有活动转盘4311,活动转盘4311的中央设置有驱动杆4312,驱动杆4312的一端与齿轮盘434的中央相连接,活动转盘4311的一侧设置有延伸杆4313,延伸杆4313的一端与摆动臂杆44相连接。
26.具体的,当过滤网板32上表面的金属颗粒饱和时,启动驱动转轴482,转动滚柱481在容纳槽47的内部进行转动,利用弧形导向槽483和导向小块35的连接,弧形导向槽483对导向小块35进行牵引导向,使柄框板31整体沿着u形夹设块41的内侧进行平移,通过卡接滑块411和三组辅助小杆45对其进行限位,使过滤设备3向混料端口12的外侧平移,且利用活动转轮451沿着辅助推移长槽36的滚动,以提升过滤设备3平移时的顺畅度,再启动驱动转盘436,推移转齿杆437带动齿轮盘434沿着中心盘431的内侧进行转动,齿轮盘434带动活动转盘4311进行转动,使摆动臂杆44以活动转盘4311为轴心进行摆动,利用限位套接转槽421与套设盘块412和限位滑节块413的连接,u形夹设块41带动过滤设备3整体以转板块42为轴心进行摆动,且三组辅助小杆45对过滤设备3的一端进行支托,与此同时,过滤网板32上表面的金属颗粒滚至回收室16的内部,推移转齿杆437带动齿轮盘434回转,过滤设备3恢复到水平状态,再次转动驱动转轴482,导向小块35移至弧形导向槽483的一端进入转向直槽484中,利用连接弹簧452的弹性,使导向小块35滑向转向直槽484的另一端,过滤设备3快速恢复原位,进而以便于快速清理未研磨完全的金属颗粒,利于提升过滤网板32的过滤效果,进一步提升制备速率。
27.为了更好地解决金属粉末物料的配比受到影响的技术问题,如图4、图13和图14所示,提供以下优选技术方案:u形夹设块41的端面安装有套设盘块412,套设盘块412的侧表面安装有限位滑节块413,转板块42的侧表面开设有限位套接转槽421,限位套接转槽421与套设盘块412和限位滑节块413相连接,回收室16包括开设在回收盒13上表面的通入槽161和开设在通入槽161底端的弧形承接槽162,转轮导向件17包括安装在通入槽161内侧的转杆171和设置在转杆171内部的转动调节轴172,转杆171的外表面套设有套接环173,套接环173的外表面设置有摆向导料杆174,摆向导料杆174的两侧均开设有导料递向槽175,套接环173的侧表面开设有转向导流槽176,导料递向槽175与转向导流槽176相连通,导料递向槽175的一端与连接通孔15相对应。
28.具体的,金属颗粒堆积在通入槽161和弧形承接槽162中,当需要对金属颗粒进行
回收时,启动转动调节轴172,带动摆向导料杆174的一端不断刮接弧形承接槽162的底部,弧形承接槽162内部的金属颗粒被收进导料递向槽175中,随着转杆171的转动,金属颗粒沿着转向导流槽176进入另一个导料递向槽175中,当摆向导料杆174的一端对准连接通孔15时,金属颗粒沿着导料接板14排出回收室16,利用弧形承接槽162的弧形贴面,通入槽161中的金属颗粒自动填补弧形承接槽162的空缺口,以便于快速回收金属颗粒,无需手动操作,将其再次进行研磨,以避免影响各类物料的配比。
29.以上所述,仅为本发明较佳的具体实施方式,但本发明的保护范围并不局限于此,任何熟悉本技术领域的技术人员在本发明披露的技术范围内,根据本发明的技术方案及其发明构思加以等同替换或改变,都应涵盖在本发明的保护范围之内。