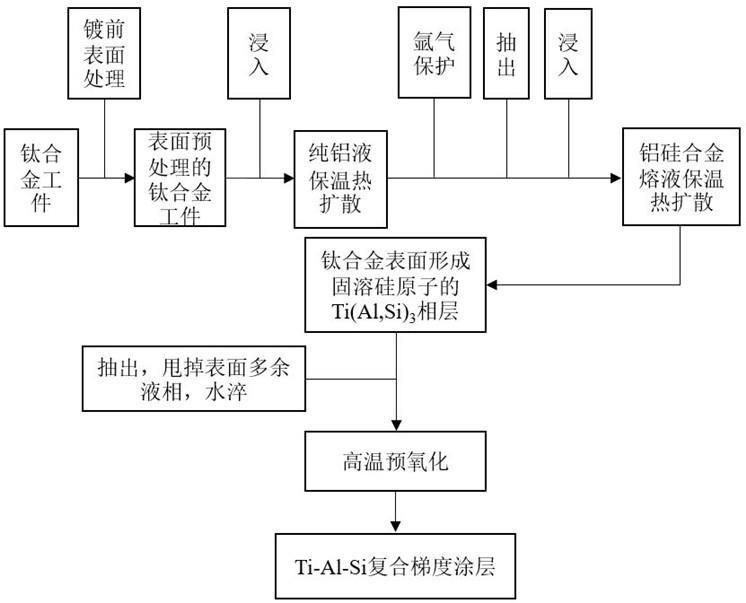
一种两步热浸渗铝法在钛合金表面制备ti-al-si复合梯度涂层的方法
技术领域
1.本发明涉及热浸镀制备涂层领域,特别是涉及一种两步热浸渗铝法在钛合金表面制备ti-al-si复合梯度涂层的方法。
背景技术:2.航空发动机作为飞机的心脏,不仅要承受极大的应力和高温,同时还要保证高推重比(推力/质量)。高温钛合金具有密度小、比强度高、耐腐蚀、高温性能好等优点,目前在发动机压气机盘、叶片、高压压气机转子、压气机机匣等部件均采用钛合金材料。随着高推重比发动机、高马赫数航空器的发展,对钛合金的抗高温氧化性能要求越来越高。但是我国目前最先进的高温钛合金ti65和ti750短时最高使用温度也只在650-750℃,随着温度上升,合金表层氧化膜极易发生破裂,造成过度氧化以及氧向基体扩散而引起氧脆。目前人们一方面通过添加抗高温氧化元素来设计新的高温钛合金,但是只有当合金元素加入量较高时,才会有较好效果。而且过量的合金元素会严重影响合金的力学性能,无法满足航天用材的安全性能要求。另一方面利用新技术在高温钛合金表面制备金属或非金属涂层,改善其抗高温氧化性能。人们采用了多种方法对钛合金进行表面改性,最初选择在钛合金表面形成一层镀铝涂层,目的是希望得到致密的tial3相层和氧化铝保护层,而且tial3是所有ti-al中间相中唯一能氧化形成三氧化二铝的相层。但是由于热浸镀过程中往往会生成多相层,由于不同涂层间或者涂层与基体之间的相结构、显微硬度、热膨胀系数等的不匹配而导致在高温下出现一定的应力,使得涂层出现裂纹将基体暴露在大气中,最终涂层开裂、脱落,失去对基体的保护作用。在铝中加入si,除了能够产生二氧化硅提高抗高温氧化性能外,还能减少热膨胀系数不匹配的问题。但是由于si会先于al与ti结合形成ti-si化合物,从而无法形成tial3相层。因此开发一种新的钛合金ti-al-si复合梯度涂层,利用多相层梯度结构消除应力开裂和准确控制硅的浓度梯度调节相层力学性能,提高涂层抗高温氧化性能,提升钛合金的服役温度。
技术实现要素:3.基于此,本发明的目的在于,提供一种两步热浸渗铝法在钛合金表面制备ti-al-si复合梯度涂层的方法,ti-al-si复合梯度涂层具有热稳定性好、致密性高、抗氧化性能好等特点,该制备方法具有合金相层梯度可控,涂层成分梯度可控、不受工件形状限制、操作简单、成本低廉等特点。
4.本发明采取的技术方案如下一种两步热浸渗铝法在钛合金表面制备ti-al-si复合梯度涂层的方法,是在钛合金表面依次形成ti-al二元合金相层、ti-al/ti-si混合相层、固溶si原子的ti(al,si)3相层、τ2相+al2o3层。
5.本发明的两步热浸渗铝法得到的钛合金ti-al-si复合梯度涂层,ti-al二元合金
相层、ti-al/ti-si混合相层、固溶si原子的ti(al,si)3相层与基体紧密结合,且呈现结构梯度分布,致密无裂纹;τ2相+al2o3层能够有效隔绝空气;si元素在多相合金层中呈现梯度分布,有效调节合金层的强韧性,防止层间开裂。
6.可以根据实际的使用需求,对所叙述的两步热浸渗铝法制备钛合金ti-al-si复合梯度涂层的梯度相组织结构进行多种设计,通过控制铝硅液中硅的含量和热浸镀时间、高温预氧化温度和时间来控制合金相层中硅浓度梯度以及ti-al-si化合物相层种类以及厚度。因此,所述两步热浸渗铝法制备钛合金ti-al-si复合梯度涂层具有良好的可控性。
7.本发明的另一目的在于,提供一种两步热浸渗铝法制备钛合金ti-al-si复合梯度涂层的方法,该制备方法包括以下步骤:(1)将分别装有纯铝和al-si合金的坩埚置于氩气气氛下的熔炼炉中加热到700℃-850℃范围内熔化保温;(2)将钛合金工件表面打磨平整,用酸洗加碱洗的方法去氧化皮和油污,然后置于干燥箱中晾干;(3)将步骤(2)中钛合金工件浸入步骤(1)中装有纯铝液的坩埚中,静置在700℃-850℃范围进行钛-铝原子互扩散反应;(4)往熔炼炉中补充一定量的氩气,将步骤(3)中钛合金工件从纯铝液中抽出,然后快速浸入到步骤(1)中装有al-si合金液的坩埚中;静置在700℃-850℃范围内进行硅原子热扩散反应;(5)控制步骤(3)中静置时间在10-30分钟范围内,确保铝液与基体中的钛反应生成tial3中间相层,控制步骤(4)中静置时间在20-40分钟范围内,确保硅原子往基体扩散,形成固溶硅原子的ti(al,si)3相层;(6)热浸镀一定时间后,将步骤(5)中的钛合金工件迅速抽出,甩掉表面多余的液相,水淬,放入850℃-950℃的高温氧化炉中预氧化4-8小时,确保铝硅原子继续向基体扩散形成ti-al二元合金相层、ti-al/ti-si混合相层,残留的ti(al,si)3相、以及大块τ2相+al2o3层。
8.本方法相对于专利号为zl201910644328.x.《一种钛合金原位自生铝硅梯度热浸镀涂层及其制备方法》的专利具有以下优点:(1)热浸镀工艺不受钛合金工件形状限制,无需制备与工件形状相似的石英玻璃器皿盛装纯铝液。
9.(2)硅源直接来自al-si合金液,可以精确控制硅源浓度。
10.(3)热浸镀用的纯铝液、al-si合金液可反复多次使用,节约成本,绿色节能。
11.(4)可以精确控制硅浓度,调控涂层中的合金相层种类、厚度、分布。
12.为了更好地理解和实施,下面结合附图详细说明本发明。
附图说明
13.图1为本发明的两步热浸渗铝法制备钛合金ti-al-si复合梯度涂层的流程图;图2为实施实例制得的ti-al-si复合梯度涂层的显微组织形貌图。
具体实施方式
14.如图1所示,完成梯度相组织结构设计后,按以下步骤两步热浸渗铝法制备钛合金ti-al-si复合梯度涂层:(1)将分别装有纯铝和al-si合金的坩埚置于氩气气氛下的熔炼炉中加热到700℃-850℃范围内熔化保温;(2)将钛合金工件表面打磨平整,用酸洗加碱洗的方法去氧化皮和油污,然后置于干燥箱中晾干;(3)将步骤(2)中钛合金工件浸入步骤(1)中装有纯铝液的坩埚中,静置在700℃-850℃范围进行钛-铝原子互扩散反应;(4)往熔炼炉中补充一定量的氩气,将步骤(3)中钛合金工件从纯铝液中抽出,然后快速浸入到步骤(1)中装有al-si合金液的坩埚中;静置在700℃-850℃范围内进行硅原子热扩散反应;(5)控制步骤(3)中静置时间在10-30分钟范围内,确保铝液与基体中的钛反应生成tial3中间相层,控制步骤(4)中静置时间在20-40分钟范围内,确保硅原子往基体扩散,形成固溶硅原子的ti(al,si)3相层;(6)热浸镀一定时间后,将步骤(5)中的钛合金工件迅速抽出,甩掉表面多余的液相,水淬,放入850℃-950℃的高温氧化炉中预氧化4-8小时,确保铝硅原子继续向基体扩散形成ti-al二元合金相层、ti-al/ti-si混合相层,表残留的ti(al,si)3相、以及大块τ2相+al2o3层。
15.实施实例(1)将分别装有纯铝和al-si合金的坩埚置于氩气气氛下的熔炼炉中加热到750℃熔化保温;(2)将ti65钛合金矩形片表面打磨平整,用酸洗加碱洗的方法去氧化皮和油污,然后置于干燥箱中晾干;(3)将步骤(2)中ti65钛合金矩形片浸入步骤(1)中装有纯铝液的坩埚中,静置在750℃进行钛-铝原子互扩散反应20分钟;(4)往熔炼炉中补充一定量的氩气,将步骤(3)中ti65钛合金矩形片从纯铝液中抽出,然后快速浸入到步骤(1)中装有al-si合金液的坩埚中;静置在750℃进行硅原子热扩散反应20分钟;(5)将步骤(4)中的ti65钛合金矩形片迅速抽出,甩掉表面多余的液相,水淬,放入950℃的高温氧化炉中预氧化4小时,得到ti-al-si复合梯度涂层。
16.(6)微观组织见图2,ti65合金表面依次形成ti3al、tial、tial3/ti5si3混合相层、ti(al,si)3相、大块τ2相+al2o3层。形成上述要求的ti3al+tial+tial3/ti5si3混合相层+ti(al,si)3相层的厚度约为70微米。