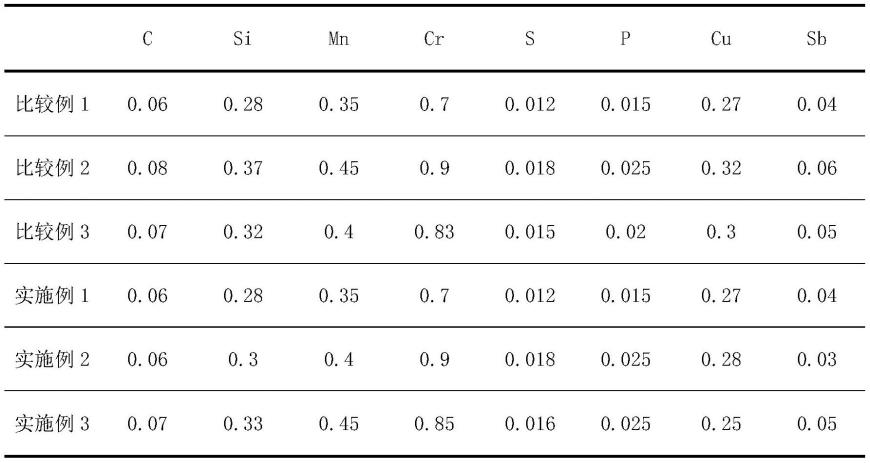
1.本发明属于钢铁冶金技术领域,尤其涉及一种热轧耐腐蚀圆钢及其制备方法。
背景技术:2.耐腐蚀钢的需求随着海洋石油的开发日益频繁,同时也为减轻大气腐蚀损失,在钢中添加合金元素,提高钢的耐蚀性能方面进行研究,提高其使用寿命,从而有了开发多种耐大气腐蚀低合金钢的需求。
3.耐腐蚀钢的炼钢难点控制在优质低碳钢中加入合金从而增加钢的耐腐蚀性。铜、磷、铬、钼、镍等是具有耐蚀效果的合金元素,这些合金元素能够富集于锈层,促使非晶态锈层的形成,改善锈层结构,提高致密度和对钢表面的粘结性,增强与大气海水的隔离作用,从而减缓了腐蚀速率,提高了钢的耐蚀性能。在上述合金元素中,铜是改善钢的耐大气腐蚀性能最好的合金元素。含有0.2%~0.5%铜的钢已在大气环境中呈现显著的耐蚀效果。对其机理的说法不一,托马晓夫等认为,钢与表面二次析出的铜之间的阴极接触,能促使钢的阳极化,并形成保护性较好的锈层。也有人认为,铜在基体与锈层之间形成以cu0为主要成分的、与基体结合牢固的阻挡层。也有人认为铜和磷等合金元素改变了锈层的吸湿性,从而提高了临界湿度。因而有利于提高钢的耐蚀性能。
4.耐腐蚀钢的轧制难点控制在优质低碳钢种加入合金元素,cu、cr、sb等元素时,对钢坯的再加热温度及时间要求较为严格,塑性变形过程中,为保证成品圆钢质量,需要防止轧制裂纹,需要严控变形温度。
技术实现要素:5.本发明所要解决的技术问题是针对上述现有技术提供一种热轧耐腐蚀圆钢的制备方法,将工艺要求与生产要求有机结合,即满足了连铸坯在炉时间的要求,又能保证各个轧制的工艺时间要求,保证了紧凑的生产节奏,用这种方法,可保证钢坯在炉时间,又能保证高温时快速轧制。
6.本发明解决上述问题所采用的技术方案为:一种热轧耐腐蚀圆钢,所述圆钢包含如下质量百分比的化学成分:c:≤0.12%,si:0.20~0.40%,mn: 0.35~0.65%,cr:0.70~1.10%,s:≤0.02%,cu:0.25~0.45%,sb:0.04~0.10%,p:≤ 0.03%,余量为fe及不可避免的杂质元素;sb的偏差按照+0.02%。
7.各元素范围的设置依据如下:
8.c:钢材含碳量与耐腐蚀性的关系是含碳量高耐腐蚀性差,但含碳量高耐磨性硬度会高,本发明控制其含量为0.12%。
9.si:是钢中的脱氧元素,并以固溶强化形式提高钢的强度。si含量低于0.20%时,脱氧效果变差,si含量较高时会导致韧性的降低。本发明si含量控制在0.20~0.40 %。
10.mn:提高钢的淬透性,通过固溶强化作用提高钢材的强度,降低相变温度,减少珠光体的渗碳体厚度与片层间距,还可以提高nb在钢中的固溶度。但mn易促进有害元素 p等
向晶界偏析,并且过高的mn会降低钢材冲击韧性,本发明mn含量控制在0.35~ 0.65%。
11.cr:碳化物形成元素,增加材料硬度,并阻止晶粒长大,但cr添加过高会导致塑韧性降低,并提高制造成本,因此,本发明将cr含量控制在0.7~1.1%。
12.p、sb:磷、锑作为杂质元素,它们对提高碳素钢的抗拉强度有一定的作用,但同时又增加钢的脆性,尤其是低温脆性。由于低合金钢熔点较高锑元素容易在高温下迁移聚集,从而导致低合金钢的高温回火脆性。合金钢在进行高温回火热处理成长期在高温下工作时,其中的锑元素容易在高温下迁移聚集。由于这些元素的熔点一般比合金元素低,它将“割裂〞材料基体而导致合金钢在高温下呈现脆性。因为合金钢的这种脆性发生在红热的温度下,故称为红脆。一般情况下,低合金钢均采用较高级的冶炼方法(如电炉冶炼)。本发明将sb含量控制在0.04~0.10%,将p含量控制在0.03%以下。
13.s:s与mn形成长条状硫化物夹杂,提高钢材切削性能。本发明将cr含量控制在 0.02%以下。
14.cu:少量的铜加入钢中可以提高低合金结构钢和钢轨钢的抗大气腐蚀性能,与磷配合使用时效果更为显著,能略微提高钢的高温抗氧化性能。能改善钢液的流动性,对铸造性能有利。在不锈耐酸钢中加入质量分数为2%~3%的铜,可改善钢对硫酸和盐酸的耐蚀性。本发明将cu含量控制在0.25~0.45%之间。
15.本发明提供一种制备上述热轧耐腐蚀圆钢的方法,按照元素成分设计冶炼钢水,将钢水浇铸成钢坯,缓冷后的方坯出加热炉后分成四个步骤进行流水线方式轧制:
16.第一步,除鳞除净表面氧化皮并加速连铸坯温降,随后连铸坯温度达到1030~1090℃即进行开坯,停留时间不要过长,整个过程控制在20秒以内完成;
17.第二步,往复式开坯,采用往复式轧机经9-13道次轧成中间方坯,每道次变形量≥ 11%,连铸坯至中间坯总变形量≥70.8%,整个过程控制在1.5分钟内完成;
18.第三步,切头及连轧,在开坯过程中,钢坯头尾因为压下量较大和mn的晶界偏析影响容易开裂,因此轧成的中间坯在进入连轧机前切头,一定要将头尾坏料切净。连轧中间坯经切头后直接进连轧机经6-10道次轧制成圆钢棒材,每道次变形量≥12%,中间坯至圆钢总变形量≥80%,圆钢终轧温度900~980℃,高于ar3。整个过程控制在1 分钟之内完成;
19.第四步 棒材在完成以上轧制后,转移至锯切辊道进行锯切。棒材锯切后下冷床集中对温度控制冷速,然后再下线收集打包。下线后圆钢获得所需各项强度、延伸率、冲击韧性指标,可直接加工成所需零部件。
20.优选地,钢水冶炼至少包括初炼、lf炉精炼和真空脱气处理。其中初炼是把合金原料块和铁水在转炉或电炉中冶炼,严格控制碳元素含量、铜、锑金属元素含量。
21.优选地,以连铸的方式获得连铸方坯作为钢坯,连铸时设计钢水浇铸过热度为15-30 ℃,连铸方坯成型后入坑缓冷。
22.优选地,钢坯再加热的温度为1150~1210℃,在此温度范围内保温让合金元素充分固溶、组织完全奥氏体化,高温段加热时间控制在2小时左右,严格控制高温段在炉时间。钢中的铜和锑长时间处在高温阶段易在晶界析出,会造成较重的轧制裂纹。
23.优选地,除鳞,开坯都需要严格控制时间,快速轧制,尽量减少在高温阶段的停留时间,只要控制好加热时间,同时4个轧制生产环节进行严格控制,从而保证圆钢成品质量。
24.与现有技术相比,本发明的优点在于:
25.1、将圆钢成型工艺精分成连续的多道工序,并对各道工序的完成时间进行限定,为圆钢的流水线生产提供批量轧制条件,在第一支坯料进入第二工序以后,第二支坯料即可进入第一步工序,第二支坯料进入第二步骤以后,第三支坯料即可进入第一步工序,以此类推......,这种生产方法将工艺要求与生产要求有机结合,即满足了连铸坯在炉时间的要求,又能保证各个轧制的工艺时间要求,保证了紧凑的生产节奏,用这种方法,可保证钢坯在炉时间,又能保证高温时快速轧制。生产节奏紧凑,能够显著提高生产效率。
26.2、钢坯到圆钢(棒材)的成型采用高温大压下+快速轧制+成品快速冷却的方式,其中
27.①
开坯前,钢坯进行除鳞,冷却至1050~1110℃,此开坯温度比传统再加热后就开坯的温度要低,有利于推迟变形奥氏体晶粒的再结晶,使奥氏体晶粒尽可能扁平化,进而促进再结晶后奥氏体晶粒的细化。
28.②
连轧阶段采用大压下工艺,可有效阻止奥氏体晶粒的再结晶,获得具有较多变形带的大变形的奥氏体晶粒,有助于在后续冷却相变阶段获得尺寸细小的铁素体与珠光体团,据此提高强度及塑韧性;
29.③
开坯后,要快速进连轧进行轧制,温度必须控制在950℃以上,在短时间内实现变形,减少cu、sb元素向晶界的析出,从而不产生轧制裂纹。
30.④
连轧结束后,快速送至冷床上,保证温度在700℃以上,同时下冷床温度控制在500 ℃左右,防止其极速冷却,组织转变更均匀,铁素体不集中产生,对组织和性能影响较大。这段对冷却时间的掌控,可以满足客户对屈服强度、抗拉强度、断后延伸率等机械性能要求。
具体实施方式
31.以下结合实施例对本发明作进一步详细描述。
32.实施例1
33.本实施例涉及的圆钢直径为75mm,其化学成分按质量百分比计为:c:0.06%, si:0.28%,mn:0.35%,cr:0.7%,s:0.012%,p:0.015%,cu:0.27%,sb:0.04%,余量为铁及不可避免的杂质元素。
34.上述圆钢依次经电炉冶炼、lf精炼生产出钢水;出炉后成型工序分以下四步进行:
35.①
第一支坯料在辊道上经高压水一次除鳞除尽表面氧化皮;此时温度为1085.3℃,随后进往复式轧机,经9道次轧成中间坯,单道次变形≥13%,中间坯规格170x175mm 2,这个过程实现大压下量快速轧制,减少轧制裂纹的产生及高温段的形变时间,以上过程控制在1.5分钟之内完成。
36.第一支中间坯在切头后进连轧温度为991.4℃,直接进入进入连轧机组,经8道次轧制成φ75mm圆钢,单道次变形量≥15%,终轧温度950.6℃,轧制完成后移至锯切辊道进行锯切,此时表面温度返温至793℃,锯切后上冷床温度为769.7℃,下冷床温度为536.5℃,随后下线堆冷,经矫直、滚磨精整工序后打包入库;圆钢直接加工成所需形状的零件。
37.实施例2
38.本实施例涉及的圆钢直径为75mm,其化学成分按质量百分比计为:c:0.06%, si:0.3%,mn:0.4%,cr:0.9%,s:0.018%,p:0.025%,cu:0.28%,sb:0.03%,余量为铁及不
可避免的杂质元素。
39.上述圆钢依次经电炉冶炼、lf精炼生产出钢水;出炉后成型工序分以下四步进行:
40.①
第二支坯料在辊道上经高压水一次除鳞除尽表面氧化皮;此时温度为1054.9℃,随后进往复式轧机,经9道次轧成中间坯,单道次变形≥13%,中间坯规格170x175mm 2,这个过程实现大压下量快速轧制,减少轧制裂纹的产生及高温段的形变时间以上过程控制在1.5分钟之内完成。
41.第二支中间坯在切头后进连轧温度为995.7℃,直接进入进入连轧机组,经8道次轧制成φ75mm圆钢,单道次变形量≥15%,终轧温度为982.9℃,轧制完成后移至锯切辊道进行锯切,此时表面温度为758.2℃,锯切后上冷床温度为776.4℃,下冷床温度为 497.7℃,随后下线堆冷,经矫直、滚磨精整工序后打包入库;圆钢直接加工成所需形状的零件。
42.实施例3
43.本实施例涉及的圆钢直径为75mm,其化学成分按质量百分比计为:c:0.07%, si:0.33%,mn:0.45%,cr:0.85%,s:0.016%,p:0.015%,cu:0.25%,sb:0.05%,,余量为铁及不可避免的杂质元素。
44.上述圆钢依次经电炉冶炼、lf精炼生产出钢水;出炉后成型工序分以下四步进行:
45.①
第三支坯料在辊道上经高压水一次除鳞除尽表面氧化皮;此时温度为1082.8℃,随后进往复式轧机,经9道次轧成中间坯,单道次变形≥13%,中间坯规格170x175mm,以上过程控制在1.5分钟之内完成。
46.第三支中间坯在切头后进连轧温度为995.8℃,直接进入进入连轧机组,经8道次轧制成φ75mm圆钢,单道次变形量≥15%,终轧温度为879.4℃,轧制完成后移至锯切辊道进行锯切,此时表面温度为799.2℃,锯切后上冷床温度为753.1℃,随后下线堆冷,下冷床温度为478.1℃,随后下线堆冷,经矫直、滚磨精整工序后打包入库;圆钢直接加工成所需形状的零件。
47.作为比较,本技术的发明人另外进行了三组对比试验,结合表1、2:比较例1-3均采用常规的速度轧制,轧制速度降为实施例1-3的80%。实施例1-3与比较例1-3相比,采用更快的开坯速度及连轧速度,以及更大的单道次压下量,并在轧制后进行冷床集中冷却,各项机械性能指标均有明显的优势,并且因为采用了坯料快速除鳞、快速开坯、连轧提速、冷床集中冷却四个步骤的流水线的轧制模式,生产节奏更快,效率更高,因此综合性价比更高。
48.表1各实施例与比较例圆钢的成分对比(wt%)
[0049][0050]
表2各实施例与比较例圆钢的性能对比
[0051][0052]
表3实施例的开坯机压下量与宽展量表
[0053][0054]
注意:在奇数道次进行一次翻钢操作。
[0055]
尽管以上详细地描述了本发明的优选实施例,但是应该清楚地理解,对于本领域的技术人员来说,本发明可以有各种更改和变化。凡在本发明的精神和原则之内所作的任何修改、等同替换、改进等,均应包含在本发明的保护范围之内。