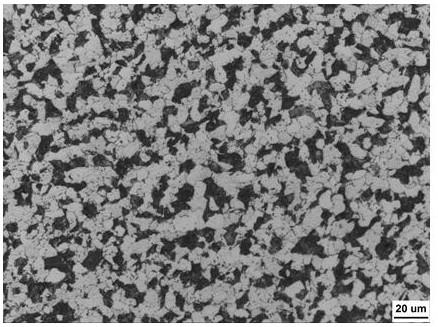
1.本发明属于金属成型与压力加工技术领域,涉及一种温锻齿轮钢及其生产方法。
技术背景
2.一般而言,对于形状不太复杂的低碳、低合金钢小型精密模锻件,采用冷锻工艺就可以成形;对于形状复杂的中小型中碳钢精密模锻件,冷锻方法难以解决其成形问题,或单纯采用冷锻工艺成本偏高,则可采用温锻成形。一般来说,钢的再结晶温度大约在750℃左右,在700℃以上进行锻造时,由于变形能可得到动态释放,成形阻力急剧减小;在700~850℃锻造时,锻件氧化皮较少,表面脱碳现象较轻微,锻件尺寸变化较小;在950℃以上锻造时,虽然变形抗力更小,但锻件氧化皮和表面脱碳现象严重,锻件尺寸变化较大。因而在700~850℃的范围内锻造可得到质量和精度都比较好的锻件。
3.采用温锻工艺的目的是获得精密锻件,温锻在于可以提高锻件的精度和质量,同时又没有冷锻那样大的变形力。温锻工艺的应用与锻件材料、锻件大小、锻件复杂程度有密切的关系。温锻是在冷锻基础上发展起来的一种少无切削塑性成形工艺。它的变形温度通常认为是在室温以上、再结晶温度以下的温度范围内,常见的温锻温度范围,黑色金属一般是200℃~850℃,对有色金属一般是室温以上到350℃以下。
4.温锻成形在一定程度上兼具了冷锻与热锻的优点。温锻是由于金属被加热,坯料的变形力比冷锻小,成形比冷锻容易,可以采用比冷锻大的变形量,从而减少工序数目,减少模具费用和设备吨位,模具寿命也比冷锻时高。与热锻比,因加热温度低,氧化和脱碳减轻,锻件尺寸公差等级较高,表面粗糙度较低。
5.温锻、冷锻和热锻的技术经济比较如表1所示。
6.表1温锻、冷锻和热锻的技术经济比较 。
7.虽然齿轮钢采用温锻工艺加工相较于热锻和冷锻有较多的优点,但是采用温锻工艺,由于是在奥氏体未再结晶区变形,变形引起的存储能无法释放,使整体自由能上升,在后续的渗碳过程中奥氏体晶粒容易长大,淬火后转变为粗大马氏体组织,对齿轮钢的性能不利。因此,客户对齿轮钢材料提出了明确要求,要求齿轮钢材料硬度控制在150~190hb,带状组织控制在2.5级以内,且金相组织级别不超过3级。这些要求通常需要对热轧齿轮钢原料进行等温正火才能满足要求,但这会大大增加齿轮钢原料的生产成本。
技术实现要素:8.本发明旨在提供一种温锻齿轮钢及其生产方法,可生产成品为φ30mm~φ80mm规格轧制圆钢,其产品氧化物夹杂及全氧含量低,组织均匀,晶粒度达8.5~9.0级,带状组织≤2.5级,金相组织≤2.5级,客户加工后综合机械性能优良,工艺性能稳定性较好,能够很好的满足客户使用需求。
9.本发明的技术方案:温锻齿轮钢及其生产方法,钢的化学组成重量百分比为c=0.16%~0.20%,si=0.25%~0.35%,mn=0.90%~1.10%,p≤0.015%,s=0.020~0.040%,cr=1.00%~1.20%,ni=1.00%~1.20%,al=0.030%~0.050%,n=0.009%~0. 013%,其余为fe和不可避免的杂质。关键工艺步骤包括:(1)铸坯生产:采用正常齿轮钢冶炼生产工艺生产合格的铸坯,铸坯断面尺寸为280
×
280mm,要求铸坯化学成分满足设计要求,铸坯断面宏观偏析碳极差≤0.02%,铸坯枝晶组织长度不大于8mm。
10.(2)铸坯高温加热及开坯轧制:铸坯加热预热段温度≤650℃,加热段温度1210
±
20℃,均热段温度1220
±
20℃,均热段保温时间≥80min,总加热时间300~400min;开坯轧制7道次轧制,初道次压下量≥80mm,开坯尺寸为150
×
150mm,开坯后集中堆冷。
11.(3)二火高温加热及控轧控冷:轧制坯二火加热预热段温度≤680℃,加热段温度1210
±
20℃,均热段温度1220
±
20℃,均热段保温时间≥60min,总加热时间180~260min;二火轧制采用15架橫立式连轧机组+kocks轧机轧制。
12.步骤(3)中,轧制过程温度控制如下:对规格为φ30~36mm的铸坯:开轧温度1100
±
30℃,预冷两个水箱分别开启20%和100%,进kocks温度780~810℃,终冷水箱不开启,上冷床温度750~780℃,冷床采用一齿一钢密排缓冷,进精轧温度850-880℃。
13.对规格为φ37~56mm的铸坯:开轧温度1100
±
30℃,预冷两个水箱分别开启100%和50%,进kocks温度780-810℃,终冷三个水箱各开启20%,上冷床温度750~780℃,冷床采用一齿一钢密排缓冷,精轧机组空过。
14.对规格为φ57~80mm的铸坯:开轧温度1100
±
30℃,预冷两个水箱分别开启100%和70%,确保进kocks温度780~810℃,终冷前两个水箱各开启30%,第3个水箱开启20%,上冷床温度750~780℃,冷床采用隔齿布钢密排缓冷,预精轧、精轧空过。
15.发明原理:铸坯凝固过程中,表层因激冷生成细小枝晶(激冷层),随着表层凝固厚度增加,铸坯内部向外传热能力降低,铸坯开始呈现定向凝固,形成由外向内的长条状树枝晶(柱状晶)。由于选分结晶的原因, 溶质元素向熔池(液相区)积聚, 当柱状晶增长而生成搭桥现象时,富集溶质元素的钢液被封闭而不能与其它液体交换,在该处形成c、s等元素的正偏析,同时,上部钢液不能补充此处的凝固收缩,从而伴随有残余缩孔。随着连铸设备和生产技术的发展,虽然铸坯的宏观偏析有了较大改善,但是,不能完全消除,而且当冶炼和连铸工艺参数控制出现异常时,铸坯宏观偏析有加重的趋势,这就需要后期轧制生产采取必要的措施来减小铸坯偏析的影响。
16.根据热力学分析,在等温等压条件下,不管浓度梯度如何,组元原子总是从化学位高的地方自发地转移到化学位低的地方,只有当每种组元的化学位置系统中各点都相等
时,才达到动态平衡。由于在一般情况下化学位梯度大都与浓度梯度方向一致,因而当扩散沿高浓度向低浓度方向进行时,掩盖了化学位梯度的作用。只有当两者方向相反,则化学位梯度的本质作用才显露出来。可见,扩散的驱动力不是浓度梯度,而是化学位梯度。可用f=-m/x表示,式中负号说明扩散驱动力与化学位下降方向一致。
17.此外,温度梯度及应力梯度造成的自由能差、表面自由能差以及电场和磁场的作用也能推动原子进行扩散。
18.因态金属中要进行扩散必须满足以下条件下:(1)要有足够高的温度。因为固态扩散是依靠原子热激活进行的,当低于一定温度时,好像扩散过程被“冻结”一样,所以只有在足够高的温度才能进行。
19.(2)要有足够长的时间。因为扩散原子在晶体中每跃迁一次最多只能移动0.3~0.5mm距离,要扩散1mm距离,必须跃迁亿万次才能实现,而且原子的跃迁过程是随机的,所以每一次的跳越与前一次没有任何关系,只有经过相当长的时间才能造成物质的宏观定向迁移。
20.(3)扩散原子在基体金属中必须有一定固溶度,使之能够溶入基体晶格,形成固溶体,才能进行固态扩散。
21.(4)要有驱动力。扩散过程都是在扩散驱动力作用下进行的,驱动力有化学位梯度、温度梯度、应力梯度等。
22.本发明的有益效果:本发明方法生产的钢种采用mn、cr、ni为主的合金成分体系,产品具有较大冲击韧性和较高的疲劳寿命,满足大载荷、高转速齿轮钢的应用需求。采用现有的齿轮钢冶炼生产工艺,同时配合特别设计的控轧控冷工艺,生产的齿轮钢材料性能优良,完全满足温锻齿轮钢的加工和使用要求。本发明利用钢厂现有设备和工艺条件,通过增加较小的生产成本,且不增加投资和生产组织难度,又为下游客户提高了生产效率,节能减耗,具有较高的经济和社会效益。
附图说明
23.图1 为实施例1金相组织 500x照片。
24.图2 为实施例1带状组织100x照片。
具体实施方式
25.下面结合实施例对本发明做进一步说明。
26.实施例1:温锻齿轮钢及其生产方法,钢的化学组成重量百分比为c=0.17%,si=0.28%,mn=0.98%,p≤0.010%,s=0.025%,cr=1.13%,ni=1.11%,al=0.033%,n=0.012%,其余为fe和不可避免的杂质;工艺步骤包括:(1)生产合格的铸坯:铸坯断面尺寸为280
×
280mm,铸坯断面宏观偏析碳极差0.017%,铸坯枝晶组织长度为7mm。
27.(2)铸坯高温加热及开坯轧制:铸坯加热预热段温度633℃,加热段温度1225℃,均热段温度1227℃,均热段保温时间95min,总加热时间353min;开坯轧制7道次轧制,初道次压下量82mm,开坯尺寸为150
×
150mm,开坯后集中堆冷。
28.(3)二火高温加热及控轧控冷:轧制坯二火加热预热段温度655℃,加热段温度1223℃,均热段温度1225℃,均热段保温时间71min,总加热时间196min;二火轧制采用15架橫立式连轧机组+kocks轧机轧制。轧制过程温度控制按表2执行。
29.实施例2:温锻齿轮钢及其生产方法,钢的化学组成重量百分比为c=0.18%,si=0.27%,mn=0.99%,p≤0.011%,s=0.026%,cr=1.15%,ni=1.13%,al=0.035%,n=0.011%,其余为fe和不可避免的杂质;工艺步骤包括:(1)生产合格的铸坯:铸坯断面尺寸为280
×
280mm,铸坯断面宏观偏析碳极差0.018%,铸坯枝晶组织长度为7mm。
30.(2)铸坯高温加热及开坯轧制:铸坯加热预热段温度635℃,加热段温度1223℃,均热段温度1225℃,均热段保温时间97min,总加热时间357min;开坯轧制7道次轧制,初道次压下量82mm,开坯尺寸为150
×
150mm,开坯后集中堆冷。
31.(3)二火高温加热及控轧控冷:轧制坯二火加热预热段温度653℃,加热段温度1227℃,均热段温度1226℃,均热段保温时间73min,总加热时间195min;二火轧制采用15架橫立式连轧机组+kocks轧机轧制。轧制过程温度控制按表3执行。
32.实施例3:锻齿轮钢及其生产方法,钢的化学组成重量百分比为c=0.17%,si=0.27%,mn=0.97%,p≤0.012%,s=0.026%,cr=1.12%,ni=1.13%,al=0.032%,n=0.011%,其余为fe和不可避免的杂质;工艺步骤包括:(1)生产合格的铸坯:铸坯断面尺寸为280
×
280mm,铸坯断面宏观偏析碳极差0.018%,铸坯枝晶组织长度为8mm。
33.(2)铸坯高温加热及开坯轧制:铸坯加热预热段温度635℃,加热段温度1229℃,均热段温度1225℃,均热段保温时间99min,总加热时间356min;开坯轧制7道次轧制,初道次压下量82mm,开坯尺寸为150
×
150mm,开坯后集中堆冷。
34.(3)二火高温加热及控轧控冷:轧制坯二火加热预热段温度652℃,加热段温度1225℃,均热段温度1226℃,均热段保温时间75min,总加热时间192min;二火轧制采用15架橫立式连轧机组+kocks轧机轧制。轧制过程温度控制按表4执行。
35.表2实施例1轧制过程温度控制按表。
36.表3实施例2轧制过程温度控制表。
37.表4实施例3轧制过程温度控制表
。
38.表5各实施例产品性能检测指标。
39.从表5和图1、图2的测试结果可见,采用本发明设计生产方法生产的轧制圆钢,其硬度控制稳定、金相组织均匀、带状组织及奥氏体晶粒均达到较高水平,全部满足设计指标要求,产品经客户试用检测合格。