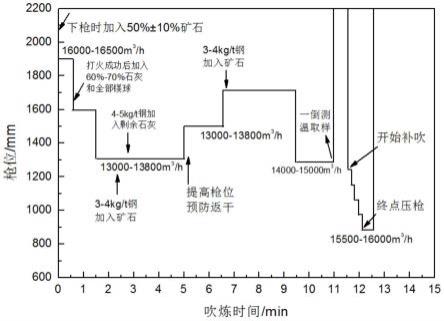
1.本发明属于转炉炼钢技术领域,具体涉及一种中小型转炉快节奏全铁水冶炼控制方法。
背景技术:2.转炉冶炼的过程中一般需要加入铁水与废钢作为原料,废钢作为转炉稳定的金属料和冷却剂,可以对冶炼过程起到很好的降温作用,缓和吹炼过程的升温速率,还能够提高转炉冶炼的出钢量。但也存在一些特殊情况不加废钢冶炼,比如加废钢行车检修、铁水热量低、短期内没有废钢或者工艺需要,此时,废钢属于限制性因素,需要采用全铁水冶炼;再如当某一转炉需要较长周期检修时,而高炉正常出铁,则会出现短期内铁水富余,其他转炉需要消化多余铁水的现象,此时,铁水为限制性因素,也会存在全铁水冶炼的情况。
3.当进行全铁水冶炼时,由于装入制度发生较大变化,吹炼的热力学与动力学条件都发生改变,易导致吹炼过程喷溅率提高,终点温度高、磷高比例加大,常需要进行数次补吹才能出钢,对生产节奏和质量控制均产生较大影响。而当处于铁水为限制性因素的全铁水冶炼时,尤其是装入量相对较少的中小型转炉,由于要在短期内消化多余铁水,需要生产时尽量减少辅助工序的停等时间,还要尽可能做到吹炼过程平稳、终点可控,尽可能缩短每炉钢的冶炼周期,保证铁水消化速度。
4.目前,对于全铁水的冶炼控制方法并没有形成统一的标准和要求。2020年3月6日公开的公开号为cn110863075a的专利,公开了一种转炉炼钢全铁水开炉及其吹炼的方法,但该专利仅针对转炉结构改造及铁水代替焦炭进行烘炉的方法进行了简要介绍,并未涉及全铁水冶炼的具体控制方法和过程。
5.2019年3月5日公开的公开号为cn109423533a的专利,公开了一种全量铁水转炉冶炼控制方法,其通过控制全铁水冶炼时的倒渣、兑铁、供氧、造渣、温度和终点,可以避免全铁水冶炼过程的喷溅和终点高温过氧化。但该方法对于兑铁时的控制有严格要求:不仅需要加入矿石后前后摇炉将其铺平,还要在慢速加入少量铁水后停止兑铁,让其与炉内矿石进行反应,此过程耗费了大量时间,严重影响了全铁水冶炼的周期,与消化铁水的目的相悖。并且由于矿石的氧化性极高,在兑铁时会与铁水中的c发生反应生成大量co气体,co气体的进一步燃烧会导致炉口冲出大量火焰,对工作人员的安全和设备的稳定运行造成大的隐患。
6.2021年12月24日公开的公开号为cn113832288a的专利,公开了一种全铁水冶炼控制喷溅的方法,其通过对烧结矿初期加入、过程加料及供氧枪位、流量进行说明,帮助减少吹炼过程中的喷溅。但其要求开吹前即加入90%
±
5%烧结矿,大量烧结矿堆积在炉内可能导致兑铁时火大,存在部分安全隐患;加入烧结矿后需进行底吹强搅,并按照角度进行摇炉处理后方可下枪吹炼,此过程对生产节奏会产生较大影响,不利于消化铁水;下枪开始冶炼,需要根据累计供氧量分批次加料,工艺相对复杂。
技术实现要素:7.本发明的目的在于提供一种中小型转炉快节奏全铁水冶炼控制方法,通过此方法进行全铁水冶炼时,利用中小型转炉装入量相对较小(40-80t为宜)、矿石用量相对较少的特点,结合矿石与枪位、加料时机的搭配控制,不需要借助外界工具、增加额外步骤,达到降低全铁水吹炼难度和缩短全铁水冶炼周期的目的,保证全铁水快节奏冶炼。
8.本发明具体技术方案如下:
9.本发明提供的一种中小型转炉快节奏全铁水冶炼控制方法,包括以下步骤:
10.1)对于需要进行全铁水冶炼的炉次,根据热平衡及物料平衡计算原料矿石、辅料石灰和镁球的加入量,终点碱度按3.0-3.5、氧化镁含量按5wt%-7wt%控制;
11.2)进行全铁水冶炼的炉次,在吹炼前通过高位料仓进行矿石备料,并将步骤1)计算的矿石总量的50wt%
±
10wt%放至汇总料仓备用,溅渣后进行不留渣操作,将炉渣翻空等兑;
12.3)按新装入制度兑入铁水,兑铁结束后下枪,氧枪距离开氧点0.2-0.3m时同步打开汇总料仓,将步骤2)准备的矿石加入到炉内;
13.4)下枪后按照枪位1.8-2.0m,氧气流量16000-16500m3/h进行打火,时间控制30-45s,打火成功后即下枪至1.5-1.7m,并加入步骤1)计算量60wt%-70wt%的石灰和步骤1)计算量的全部镁球,待火焰稳定后,继续下枪进行吹炼。
14.步骤2)中,选取步骤1)计算矿石总量的50wt%
±
10wt%放至汇总料仓备用,原因为炉内无废钢,若初期加入矿石量较少,则矿石前期熔化、还原的吸热量无法平衡铁水氧化的放热量,前期熔池温度会因为不加废钢而上升太快,碳氧反应提前开始;若加入矿石量太多,则会导致前期熔池温度压得太死,还易导致矿石量太大而结坨造成喷溅,不利于前期吹炼,所以选择总量的50wt%
±
10wt%。
15.步骤3)中,由于此时炉内为全空状态,所以兑铁速度不需特别控制,以2-2.5t/s为宜,此步骤对比其他已公布全铁水冶炼方法可节省大量装入时间。
16.步骤3)中,氧枪距离开氧点0.2-0.3m时同步打开汇总料仓,将提前准备在汇总料仓的矿石加入到炉内,目的为利用氧枪开氧瞬间的氧气射流将所加矿石均匀的吹散至熔池表面,此步骤可很好的解决单批次向熔池加入大量矿石易结坨进而造成吹炼前中期大喷的隐患问题。
17.步骤4)中,由于炉内无留渣、无废钢,打火相对容易,时间控制在30-45s即可。
18.步骤4)中,所述下枪进行吹炼具体为:
19.4-1)吹炼2-5min枪位按照1.2-1.4m、氧气流量13000-13800m3/h进行控制,过程中按每批次4-5kg/t钢的原则加入剩余量的石灰,按每批次3-4kg/t钢的原则向炉内加入矿石,此步骤加入矿石量控制在步骤1)计算矿石总量的25wt%
±
5wt%,每批次矿石加入时提枪0.1-0.15m,防止炉内反应剧烈烧枪,待炉内反应稳定后再恢复到原枪位。
20.4-2)吹炼5-6.5min,炉内碳氧反应已经开始激烈进行,此时将枪位提高至1.4-1.6m,不包括1.4m(枪位高于吹炼2-5min时枪位),氧气流量不变,预防返干。
21.4-3)吹炼6.5min后到9.5min,炉内碳氧反应速度达到峰值,渣中氧化铁含量消耗较快,此时枪位提高至1.6-1.8m,不包括1.6m(枪位高于吹炼5-6.5min时枪位),氧气流量不变,同时过程中按照每批3-4kg/t钢的原则向炉内分批次加入剩余量的矿石,每批次矿石加
入时提枪0.1-0.15m,防止炉内反应剧烈烧枪,待炉内反应稳定后再恢复到原枪位。
22.4-4)吹炼9.5min后,c、o反应速率趋于平缓,此时将吹炼枪位降低至1.2-1.4m,氧气流量提高至14000-15000m3/h,同时不再向熔池内加入物料。
23.4-5)终点采用高拉补吹法进行控制,以降低难度并保证出钢率;一倒终点c含量控制在0.25%-0.35%,补吹时按0.2-0.25m/10s的幅度逐步降低枪位至0.8-0.9m,氧气流量提高至15500-16000m3/h,进行终点压枪20-30s,保证炉内钢水温度和成分均匀。
24.步骤4-1)中,吹炼2-5min枪位为比正常吹炼时降低0.1-0.15m、氧气流量降低500-1000m3/h。本发明在吹炼2-5min通过适当降低枪位和氧压,目的在于不影响前期反应速率的同时减少氧枪向熔池内供氧量,促进熔池内铁水与初期加入矿石间的反应,加速矿石消耗速度。此操作可有效防止前期加入的大量矿石淤积在熔池上层导致中期c、o反应激烈引起爆发性喷溅的问题,还能够为中期开始分批加入矿石提供空间。
25.步骤4-1)中,吹炼2-5min加入矿石量控制在步骤1)计算矿石总量的25wt%
±
5wt%,原因为开吹时已加入大量矿石,点火后加入大量造渣料,熔池内前期温度得到有效抑制。若在此阶段盲目将剩余矿石全部或大部分加入,会导致前期熔池温度过低,则不利于碳氧反应进行和均匀升温,所以控制在总量的25wt%
±
5wt%,留下剩余矿石在吹炼中后期调整炉渣和温度加入。
26.步骤4-3)中,吹炼6.5min后到9.5min枪位提高至1.6-1.8m,氧压不变,同时向炉内加入矿石,是因为中期碳氧反应速度达到峰值,渣中氧化铁含量消耗较快,通过进一步提高枪位及补充矿石,可保证熔池内氧化铁含量,有效防止返干,促进吹炼的平稳进行。
27.步骤4-5)中,终点控制通过高拉补吹时0.2-0.25m/10s的幅度逐步降低枪位的方式,可促进氧气射流对熔池内各位置钢水的有效搅拌,结合终点20-30s的压枪时间,保证终点钢水温度、成分的均匀性,进一步提高出钢率和钢水质量。
28.本发明的设计的中小型转炉快节奏全铁水冶炼控制方法,设计思路及原理在于:
29.1、本发明开吹即加入总量50wt%
±
10wt%的矿石,一是可通过矿石前期熔化、还原的吸热量平衡铁水氧化的放热量,控制前期熔池温度不会因不加废钢而上升太快,同时防止因矿石量一次性加入太多而导致结坨现象的产生,不利于前期吹炼。
30.2、本发明进行兑铁时,不需要提前加矿石到炉内或进行其他操作,炉内为空炉状态,兑铁时速度也不需做特别控制,此两步可省去大量时间,为缩短冶炼节奏、提高铁水消化速度提供有力保障。
31.3、本发明独创性的在氧枪距离开氧点0.2-0.3m时同步打开汇总料仓,将提前准备的矿石加入到炉内,可利用氧枪开氧瞬间的氧气射流将所加矿石均匀的吹散至熔池表面,很好的解决单批次向熔池加入大量矿石易结坨进而造成吹炼前中期大喷的隐患问题。
32.4、本发明在吹炼2-5min时枪位比正常吹炼时降低0.1-0.15m、氧气流量降低500-1000m3/h,目的为在不影响前期反应速率的同时减少氧枪向熔池内供氧量,促进熔池内铁水与初期加入矿石间的反应,加速矿石消耗速度。此操作可有效防止前期加入的大量矿石淤积在熔池上层导致中期c、o反应激烈引起爆发性喷溅的问题,还能够为中期开始分批加入矿石提供空间。
33.5、本发明吹炼2-5min加入矿石量控制在总量的25wt%
±
5wt%,原因为开吹时已加入大量矿石,点火后加入大量造渣料,熔池内前期温度得到有效抑制。若在此阶段盲目将
剩余矿石全部或大部分加入,会导致前期熔池温度过低,则不利于碳氧反应进行和均匀升温,所以控制在总量的25wt%
±
5wt%,留下剩余矿石在吹炼中后期调整炉渣和温度加入。
34.6、本发明通过终点控制高拉补吹时0.2-0.25m/10s的幅度逐步降低枪位的方式,可促进氧气射流对熔池内各位置钢水的有效搅拌,结合终点20-30s的压枪时间,保证终点钢水温度、成分的均匀性,进一步提高出钢率和钢水质量。
35.通过本发明进行全铁水的冶炼,可以有效解决全铁水冶炼过程中反应活跃、易喷溅和终点难控制问题,帮助现场全铁水冶炼取得以下效果:
36.1、使用本方法进行全铁水冶炼,由于不需要提前加入废钢或矿石在炉内,兑铁时也不需要控制速度,装入时间由正常冶炼的平均80s降低至平均32s,有效减少了冶炼时的装入时间。
37.2、使用本方法进行全铁水冶炼,得益于吹炼各阶段矿石分配合理、枪位及流量控制合适,使得反应平稳、升温均匀,全铁水冶炼过程喷溅率由未采用此方法前的平均26.8%降低至平均13.6%,终点温度高、磷高不能出钢比例由平均32.1%降低至平均14.5%,有效促进了现场全铁水冶炼生产顺行及质量控制;
38.3、使用本方法进行全铁水冶炼,由于装入时间缩短,吹炼过程和终点控制难度降低,使得冶炼周期由正常加废钢炉次的平均28.7min降低至25.5min,有效缩短了冶炼周期,提高了铁水消化速度;
39.4、使用本方法进行全铁水冶炼,可使得现场吹炼过程喷溅、终点补吹次数降低,利于钢铁料消耗的降低和钢水质量的提高,对于企业的节能降本及环保控制均有一定的促进作用。
40.与现有技术相比,本发明提供的一种中小型转炉快节奏全铁水冶炼控制方法,能够达到缩短转炉冶炼全铁水周期,保证吹炼过程平稳、终点可控,降低全铁水吹炼难度和短期内消化铁水的目的,保证转炉吹炼全铁水时的稳定、高效,提供转炉生产作业率。
附图说明
41.图1为中小型转炉全铁水冶炼控制方法过程操作示意图。
具体实施方式
42.实施例1
43.一种中小型转炉快节奏全铁水冶炼控制方法,包括以下步骤:
44.某钢厂公称容量65t转炉进行全铁水冶炼hrb400ea钢种,正常装入量为58t铁水+14t废钢,现根据消化富裕铁水要求需要进行全铁水冶炼。入炉铁水条件及初炼钢水要求如表1所示:
45.表1、入炉铁水条件及初炼钢水要求
46.类别温度/℃c/%si/%mn/%p/%s/%铁水13404.420.450.210.1260.023钢种要求-≤0.19
‑‑
≤0.030≤0.025
47.1)、全铁水装入量为65t,首先根据铁水成分进行热平衡和物料平衡计算,终点碱度按3.0-3.5、氧化镁含量按5wt%-7wt%控制,确定原辅料用量:
48.矿石用量:3880kg,石灰用量:3250kg,镁球用量:381kg。
49.2)、吹炼前通过高位料仓称量1980kg矿石放至汇总料仓备用,正常留渣量溅渣2.5min后,将炉渣溅干后翻入渣锅,确保炉内为全空状态。
50.3)、向转炉内以2t/s的速度兑入65t铁水,兑铁结束后下枪,氧枪下至3.8m时同步打开汇总料仓,将1980kg矿石加入炉内,利用氧枪3.5m时开氧瞬间的氧气射流将矿石均匀的吹散至熔池内,防止矿石结团而导致的前期喷溅。
51.4)、下枪后按照枪位2.0m,氧气流量16200m3/h进行打火30s,打火成功后将氧枪下至1.6m同步加入2050kg石灰、381kg镁球。
52.5)、吹炼2-5min按照枪位1.2m、氧气流量降至13600m3/h进行吹炼(加废钢炉次此阶段吹炼平均枪位为1.3m、氧气流量为14200m3/h),过程中分别在吹炼2.2min、2.8min、3.5min、4.6min分别加入240kg、215kg、228kg、241kg矿石,共加入924kg矿石,每次加入矿石时提枪0.1m,待炉内反应稳定后再恢复到原枪位,另分别在吹炼2.5min、2.9min、3.8min、4.4min分四批次加入321kg、298kg、285kg、296kg石灰,共加入1200kg石灰。
53.6)吹炼5-6.5min按照枪位1.5m氧气流量不变进行吹炼,预防中期返干。
54.7)吹炼6.5min后-9.5min按照枪位1.7m,氧气流量不变进行吹炼,并分别在吹炼7.3min、7.8min、8.4min、9.1min以244kg、250kg、238kg、244kg加入976kg矿石,补充熔池内氧化铁含量,防止过程返干及平衡温度,每次加入矿石时提枪0.1m,待炉内反应稳定后再恢复到原枪位;
55.8)、吹炼9.5min时将枪位降低至1.4m、氧气流量提高至14400m3/h继续吹炼,吹炼11min时提枪进行一倒测温取样。测温取样后下枪补吹,补吹时按0.2m/10s的幅度逐步降低枪位至0.85m,氧气流量进一步提高至15800m3/h,压枪30s后进行终点测温取样并准备出钢。
56.8)本炉冶炼一倒及终点钢水温度、成分及炉渣成分如表2所示,由表2可看到,终点钢水温度及成分均满足作业指导书要求,终渣成分合理。
57.表2、全铁水冶炼hrb400ea钢种终点成分、温度及炉渣成分
58.类别温度/℃c/%p/%s/%碱度rtfemgo一倒16320.280.0470.023///终点16550.090.020.0233.312.6%6.4%
59.本炉冶炼过程未发生喷溅,终点钢水温度、磷均在内控范围内,一倒补吹后直接进行出钢操作。本炉单炉冶炼周期为25.5min,正常加废钢炉次冶炼周期为28.6min,单炉冶炼周期缩短3.1min;按此装入制度计算铁水消化速度,理论情况下单炉座一天可消化铁水3670.6t,正常加废钢炉次可消化2920.3t,则一天可以多消化铁水750.3t,多消化铁水比例达25.7%,取得了很好的效果,满足了现场生产的需要。
60.实施例2
61.一种中小型转炉快节奏全铁水冶炼控制方法,包括以下步骤:
62.某钢厂公称容量65t转炉进行全铁水冶炼q235b钢种,正常装入量为56t铁水+16t废钢,现根据消化富裕铁水要求需要进行全铁水冶炼。入炉铁水条件及初炼钢水要求如表3所示:
63.表3、入炉铁水条件及初炼钢水要求
64.类别温度/℃c/%si/%mn/%p/%s/%铁水13524.50.330.180.1180.028钢种要求-≤0.15
‑‑
≤0.030≤0.030
65.1)全铁水装入量为64t,首先根据铁水成分进行热平衡和物料平衡计算,终点碱度按3.0-3.5、氧化镁含量按5wt%-7wt%控制,确定原辅料用量:
66.矿石用量:3820kg,石灰用量:2688kg,镁球用量:352kg。
67.2)、吹炼前通过高位料仓称量1980kg矿石并将其放至汇总料仓备用,正常留渣量溅渣2.6分钟,将炉渣溅干后翻入渣锅,确保炉内为全空状态。
68.3)、向转炉内以2.2t/s的速度兑入64t铁水,兑铁结束后正常下枪,氧枪下至3.75米时同步打开汇总料仓加入1980kg矿石,利用氧枪3.5m时开氧瞬间的氧气射流将矿石均匀的吹散至熔池内,防止矿石结团而导致的前期喷溅。
69.4)、下枪后按照枪位1.9m,氧气流量16200m3/h打火30s,打火成功后将氧枪下至1.55m同步加入1820kg石灰、352kg镁球。
70.5)、吹炼2-5min按照枪位1.25m、氧气流量降至13800m3/h进行吹炼(加废钢炉次此阶段吹炼平均枪位为1.35m、氧气流量为14300m3/h),过程中分别在2.6min、3.2min、4min、4.4min加入矿石221kg、210kg、198kg、226kg,共加入855kg矿石,每次加入矿石时提枪0.1m,待炉内反应稳定后再恢复到原枪位,另分别在2.2min、3.5min、4.7min加入石灰292kg、306kg、270kg,共加入868kg石灰。
71.6)吹炼5-6.5min按照枪位1.6m,氧气流量不变进行吹炼,预防中期返干。
72.7)、吹炼6.5min后-9.5min按照枪位1.8m,氧气流量不变进行吹炼,过程中分别在6.8min、7.6min、8.1min、8.5min以241kg、237kg、252kg、255kg共加入985kg矿石,补充熔池内氧化铁含量,防止过程返干及平衡温度,每次加入矿石时提枪0.1m,待炉内反应稳定后再恢复到原枪位。
73.8)、吹炼9.5min时将枪位降低至1.38m、氧气流量提高至14500m3/h继续吹炼,吹炼10.8min时提枪进行一倒测温取样。测温取样后下枪补吹,补吹时按0.2m/10s的幅度逐步降低枪位至0.88m,氧气流量进一步提高至16000m3/h,压枪25s后进行终点测温取样并准备出钢。
74.9)、本炉冶炼一倒及终点钢水温度、成分及炉渣成分如表4所示,由表4可看到,终点钢水温度及成分均满足作业指导书要求,终渣成分合理。
75.表4、全铁水冶炼q235b钢种终点成分、温度及炉渣成分
76.类别温度/℃c/%p/%s/%碱度rtfemgo一倒16420.250.0490.023///终点16630.080.0230.023.212.9%6.0%
77.本炉冶炼过程未发生喷溅,终点钢水温度、磷均在内控范围内,一倒补吹后直接进行出钢操作。本炉单炉冶炼周期为25.2min,正常加废钢炉次冶炼周期为28.4min,单炉冶炼周期缩短3.2min;按此装入制度计算铁水消化速度,则理论情况下单炉座一天可消化铁水3657.1t,正常加废钢炉次每天可消化2839.4t,则每天可以多消化铁水817.7t,多消化铁水比例达28.8%,取得了很好的效果,满足了现场生产的需要。
78.实施例3
79.一种中小型转炉快节奏全铁水冶炼控制方法,包括以下步骤:
80.某钢厂公称容量65t转炉进行全铁水冶炼q355bd钢种,正常装入量为58t铁水+13.5t废钢,现根据消化富裕铁水要求需要进行全铁水冶炼。入炉铁水条件及初炼钢水要求如表5所示:
81.表5、入炉铁水条件及初炼钢水要求
82.类别温度/℃c/%si/%mn/%p/%s/%铁水13574.60.410.150.1040.032钢种要求-≤0.14
‑‑
≤0.030≤0.030
83.1)全铁水装入量为66t,首先根据铁水成分进行热平衡和物料平衡计算,终点碱度按3.0-3.5、氧化镁含量按5wt%-7wt%控制,确定原辅料用量:
84.矿石用量:4029kg,石灰用量:2896kg,镁球用量:368kg。
85.2)、吹炼前通过高位料仓称量2160kg矿石并将其放至汇总仓备用,正常留渣量溅渣2.8分钟,将炉渣溅干后翻入渣锅,确保炉内为全空状态。
86.3)、向转炉内以2.4t/s的速度兑入66t铁水,兑铁结束后正常下枪,氧枪下至3.8米时同步打开汇总料仓加入2160kg矿石,利用氧枪3.5m时开氧瞬间的氧气射流将矿石均匀的吹散至熔池内,防止矿石结团而导致的前期喷溅。
87.4)、下枪后按照枪位2m,氧气流量16500m3/h打火35s,打火成功后将氧枪下至1.6m同步加入2010kg石灰、368kg镁球。
88.5)、吹炼2-5min按照枪位1.28m、氧气流量降至13600m3/h进行吹炼(加废钢炉次此阶段吹炼平均枪位为1.4m、氧气流量为14200m3/h),过程中分别在2.6min、3.3min、4min、4.5min加入矿石215kg、224kg、240kg、231kg,共加入910kg矿石,每次加入矿石时提枪0.1m,待炉内反应稳定后再恢复到原枪位,另分别在3min、3.6min、4.9min加入石灰308kg、294kg、284kg,共加入886kg石灰。
89.6)、吹炼5-6.5min按照枪位1.55m,氧气流量不变进行吹炼,预防中期返干。
90.7)吹炼6.5后-9.5min按照枪位1.75m,氧气流量仍保持13600m3/h进行吹炼,过程中分别在6.7min、7.5min、8min、8.4min加入矿石230kg、248kg、226kg、255kg共加入959kg矿石,补充熔池内氧化铁含量,防止过程返干及平衡温度,每次加入矿石时提枪0.1m,待炉内反应稳定后再恢复到原枪位。。
91.8)、吹炼9.5min时将枪位降低至1.34m、氧气流量提高至14300m3/h继续吹炼,吹炼11min时提枪进行一倒测温取样。测温取样后下枪补吹,补吹时按0.22m/10s的幅度逐步降低枪位至0.9m,氧气流量进一步提高至16000m3/h,压枪22s后进行终点测温取样并准备出钢。
92.9)、本炉冶炼一倒及终点钢水温度、成分及炉渣成分如表6所示,由表6可看到,终点钢水温度及成分均满足作业指导书要求,终渣成分合理。
93.表6、全铁水冶炼q235b钢种终点成分、温度及炉渣成分
94.类别温度/℃c/%p/%s/%碱度rtfemgo一倒16420.250.0110.03///终点16540.080.0080.0273.313.1%6.2%
95.本炉冶炼过程未发生喷溅,终点钢水温度、磷均在内控范围内,一倒补吹后直接进
行出钢操作。本炉单炉冶炼周期为25.6min,正常加废钢炉次冶炼周期为28.7min,单炉冶炼周期缩短3.1min;按此装入制度计算铁水消化速度,则理论情况下单炉座一天可消化铁水3712.5t(时间除冶炼周期得到炉数,炉数
×
铁水装入量=每天铁水总量),正常加废钢炉次每天可消化2910.1t,则每天可以多消化铁水802.4t,多消化铁水比例达27.5%,取得了很好的效果,满足了现场生产的需要。
96.目前,本发明方法在现场已普遍推广使用,不再一一进行案例列举。现场全铁水冶炼未采用本方法前,吹炼模式并不统一,为更好的体现本发明在现场使用后的优势,特将前后部分对比数据统计如表7所示。
97.表7、现场采用本方法全铁水冶炼前后数据对比
98.类别炉数过程喷溅率温高、磷高比例平均冶炼周期钢铁料消耗冒烟比例未用本方法68326.8%32.1%28.7min1058kg/t钢13.2%使用本方法35913.6%14.5%25.5min1045kg/t钢5.6%
99.备注:冒烟指由于大喷带出大量烟尘而导致的现场烟大问题。
100.现场实践证明,该方法在中小型转炉冶炼全量铁水时,具有安全、稳定、高效、快节奏等优点,可在转炉炼钢生产领域中推广应用。