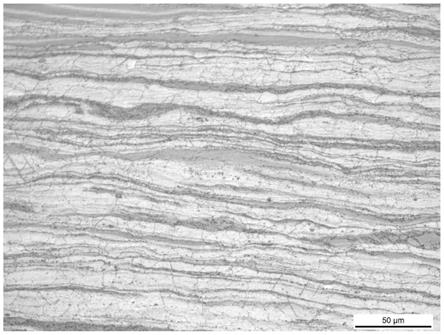
1.本发明属于合金材料加工技术领域,具体涉及一种低成本高强度镁合金材料,并进一步去公开其制备方法。
背景技术:2.镁合金作为最为轻质的结构材料,因其具有较低的密度、较高的比刚度和比强度,在对质量“克克计较”的航天器结构领域具有广阔的应用前景。同时,高强度镁合金材料的成功开发和稳定性供货也是促进其在结构领域应用的重要因素。目前,对减重要求极为迫切的结构件也已采用镁-稀土合金材料替换原来的铝合金材料,并通过进一步结构设计和优化,实现替代之后结构减重>30%的效果,如载人航天器前锥支架、后锥支架和武器舵支架结构等均采用镁合金材料进行制备。
3.但是,由于镁合金材料的弹性模量较铝合金低,对于航天器结构来说,在相同的基频要求下,采用镁合金材料制备的结构需要在结构局部进行增加壁厚、加强筋等补强设计,从而导致采用镁合金材料替换铝合金材料所取得的减重效果大幅度降低;为了降低结构关键局部加强所带来的结构质量增加幅度,在结构的其他非关键局部位置进行减薄、去加强筋等设计,但这种情况下为了满足结构承载的要求,需要所采用的镁合金材料具有较高的性能,诸如较高的屈服强度。而在目前众多的镁合金牌号体系中,仅有镁-稀土合金的强度相对较高,能够满足航天器结构不同工况下的承载要求。因此,目前在航天器结构中应用的镁合金材料种类大部分为镁-稀土合金材料。但是,高强镁-稀土合金材料的价格均较高,如5a06铝合金的市场价格约100元/kg,而镁-稀土合金的平均价格则>800元/kg,对于成本要求严格的某些航天器来说,采用高强度镁-稀土合金材料替换传统的铝合金时材料往往由于材料成本较高,使得设计师只能转而选择成本相对偏低的性能较好的树脂基复合材料。因此,开发低成本的高强度镁-稀土合金材料势在必行。
4.根据现有的镁-稀土制造技术,之所以造成现有高强度镁-稀土合金材料价格较高的主要原因包括:(1)高强度镁-稀土合金中往往通过添加大量的稀土元素(如gd、y、nd)等促进合金的强化相的形成和析出,提升合金的强度,而稀土元素市场价格较高,助推了高强度镁-稀土合金材料成本明显上升;(2)目前的高强度镁-稀土合金材料制备流程长且复杂,中间塑性加工工序较多也造成了材料的制备成本上升,如国内普遍采取的制备工艺为:熔炼―均匀化处理―锻造/轧制/挤压开坯―退火处理―塑性加工―时效处理―退火处理,整个工艺流程较长且复杂,造成材料制备周期长且质量控制困难。
5.因此,为了大幅度降低镁合金材料制备成本,进一步拓展镁合金工程应用范围,突破高强度镁合金的制造技术瓶颈及其在工程应用中的成本障碍,本发明提出了一种低成本高强度镁合金及其制备方法,在满足高强度指标要求的前提下,大幅度降低材料的制备成本。
技术实现要素:6.为此,本发明所要解决的技术问题在于提供一种低成本高强度镁合金材料,所述镁合金材料通过在合金成分中添加少量的硅和锰,避免采用贵金属及稀土元素,实现原材料层面成本的降低,在满足高强度指标要求的前提下,大幅度降低材料的制备成本;
7.本发明所要解决的第二个技术问题在于提供上述低成本高强度镁合金材料的制备方法,通过采用短流程的熔炼-半连续铸造板坯-热轧-时效-退火制备工艺,实现了该种高强度镁合金材料制备流程简单化,减少或缩短中间制备工序,大幅度降低制造成本。
8.为解决上述技术问题,本发明所述的一种低成本高强度镁合金材料,所述镁合金材料按其总量计,包括如下质量含量的组分:锌(zn)3-6wt%、硅(si)0.1-0.5wt%、锰(mn)0.2-0.5wt%、锆(zr)0.4-0.9wt%,其余为镁(mg)。需要说明的是,所述镁合金材料还可以含有允许且不可避免含量的杂质元素。
9.本发明还公开了一种制备所述低成本高强度镁合金材料的方法,包括如下步骤:
10.(1)按照选定镁合金材料的元素组成及配比量进行配料,取纯镁、纯锌、mgsi5中间合金、mgmn5中间合金和mgzr20中间合金加入至合金熔剂中进行熔炼处理,得到镁合金熔液,并经精炼处理后加入精炼剂混匀,得到所需金属液,备用;
11.(2)将所述金属液进行半连续铸造,并将得到的扁铸锭经扒皮、去头尾后,获得镁合金板坯;
12.(3)将所述镁合金板坯经均匀化热处理后进行轧制成形,并将所得镁合金板进行时效及退火处理,即得。
13.具体的,所述步骤(1)中,所述熔炼步骤工序为:按照选定镁合金材料的元素组成及配比量进行配料,加入所述合金熔剂并待其熔化后,通入sf6和co2混合保护气体,加入所述金属镁并升温至710℃-730℃,保温至金属镁全部熔化;然后升温至750℃-770℃,并依次加入所述纯锌、mgsi5中间合金、mgmn5中间合金和mg-zr20中间合金,熔化即得到所述镁合金熔液。
14.优选的,所述sf6和co2混合保护气体中二者的体积比为1:1000-1:3000。
15.具体的,所述合金熔剂以其总量计,包括如下质量含量的组分:mgcl
2 45-55wt%、kcl 20-25wt%、nacl 15-25wt%、bacl
2 5-10wt%;
16.所述合金熔剂的加入量占各个所述合金组分原料总量的2-4wt%。
17.具体的,所述步骤(1)中,所述精炼步骤工序为:将所述镁合金熔液降温至710-730℃,在不通电加热状态下通入干燥氩气对熔体进行精炼处理;待上述通气过程完成后重新加热至710-730℃,并加入所述精炼剂混匀后扒渣,即得所述金属液。
18.具体的,所述步骤(1)中,所述精炼剂以其总量计,包括如下质量含量的组分:mgcl
2 40-50wt%、kcl 20-25wt%、nacl 25-30wt%、naf 8-15wt%、caf
2 5-10wt%;
19.所述精炼剂的加入量占各个所述合金组分原料总量的3-5wt%。
20.具体的,所述步骤(2)中,所述半连续铸造步骤工序为在扁锭结晶器中进行水平热顶模半连续铸造;
21.所述半连续铸造步骤的参数包括:冷却水压0.05mpa-0.10mpa,冷却水流量15m3/h-20m3/h,结晶器内镁液温度680℃-710℃,铸造速度为60mm/min-100mm/min;结晶器液面采用sf6和co2的混合气体来进行保护,优选二者体积比例为1:1000-1:3000,更优选体积比
例为1:2000。
22.所述步骤(2)中,优选控制成型板坯的厚度为200-250mm。
23.具体的,所述步骤(3)中,所述均匀化热处理步骤的工艺参数包括:360℃-450℃下保温12h-20h。
24.具体的,所述步骤(3)中,所述轧制成形步骤采用双辊轧机进行热轧开坯及后续多道次轧制,根据需要可轧制成形不同规格的中厚板(25mm-40mm),所述轧制成型过程为一火轧制,中间不做退火处理;
25.所述轧制成型步骤参数包括:轧制温度360℃-440℃,单道次压下量5%-15%。
26.具体的,所述低成本高强度镁合金材料的制备方法,所述步骤(3)中:
27.所述时效处理步骤为单级时效处理,工艺参数包括:温度170℃-200℃,时间为8h-22h;
28.所述退火处理步骤参数包括:温度300℃-380℃,时间0.5h-2h。
29.本发明所述镁合金材料,在传统mg合金材料中添加zn和zr元素以促进合金强化相的形成和微观组织细化元素的基础上,采用低成本的si作为原料,由于si在熔炼过程中能够与mg优先形成mg2si相,而mg2si相可以作为形核的初始核心,对铸态组织的细化具有较为明显的作用;并且,si元素的添加能够使得镁合金轧制态的再结晶组织转变为混晶组织,对于轧制态的合金来说具有明显的细化作用;同时,mn中间合金的加入,能够在保证合金高强度的同时,提升合金的塑性,满足工程使用的延伸率指标要求。
30.本发明所述镁合金材料通过在合金成分中添加少量的硅和锰,避免采用贵金属及稀土元素,实现原材料层面成本的降低,在满足高强度指标要求的前提下,大幅度降低材料的制备成本。本发明中制备的高强度镁合金材料在满足替换传统的5a06铝合金材料进行结构减重的前提下,相对于高强度镁-稀土合金来说,成本降低>50%,具有较高的经济价值。
31.本发明所述镁合金材料的制备方法,采用半连续铸造扁铸锭的方式,可直接实现板锭开坯,减少锻造环节,众所周知,半连续铸造扁铸锭的制备难度明显高于半连续铸造圆铸锭,而合理的合金化元素能降低铸造工艺的实施难度,本发明所采用的合金化元素除zn外,其余均为微量、超微量元素且大多起到铸造初始组织细化和降低偏析的作用,可易于实现大规格扁铸锭的半连续铸造。
32.本发明所述镁合金材料的制备方法,采用轧制工艺一火次完成开坯和多道次轧制的方式,一次性制备不同厚度的镁合金板坯,并辅以常规的热处理工艺,避免了传统的多种工艺和工序并存,降低了中间工序环节、制备工艺的复杂性,实现了短流程镁合金制备工艺,大幅度降低了镁合金材料的制备成本,且有效保证了材料的强度性能,具有较高的工业应用价值。
附图说明
33.为了使本发明的内容更容易被清楚的理解,下面根据本发明的具体实施例并结合附图,对本发明作进一步详细的说明,其中,
34.图1为本发明实施例2中步骤(2)所得板坯样品的金相图;
35.图2为本发明实施例2中步骤(3)所得合金材料时效态样品的金相图。
具体实施方式
36.为使本发明实施例的目的、技术方案和优点更加清楚,下面将结合本发明实施例,对本发明实施例中的技术方案进行清楚、完整地说明。
37.实施例1
38.本实施例所述低成本高强度镁合金成分(质量百分比)为:锌(zn)5.7wt%、硅(si)0.3wt%、锰(mn)0.2wt%、锆(zr)0.45wt%,其余为镁(mg)和不可避免的杂质元素。
39.本实施例所述低成本高强度镁合金的制备方法,包括如下步骤:
40.(1)按照合金中各组分的质量百分比进行配料,加入占各合金成分物料总量3wt%的所述合金熔剂,并通入sf6和co2混合保护气体,加入所述金属镁并升温至710℃,保温至金属镁全部熔化;然后升温至750℃,依次加入所述纯锌、mgsi5中间合金、mgmn5中间合金和mgzr20中间合金,经搅拌熔化得到镁合金液;将所述镁合金液降温至730℃,通入干燥氩气对熔体精炼10min,并静置10min,此过程中不通电加热,待上述通气过程完成后再通电使得炉温恢复到730℃,加入占各合金成分物料总量4wt%的所述精炼剂,搅拌后静置5min,之后进行扒渣并静置15min,得到所述金属液;
41.所述合金熔剂包括:mgcl2(50wt%)、kcl(25wt%)、nacl(20wt%)、bacl2(5wt%)。
42.所述精炼剂包括:mgcl2(40wt%)、kcl(20wt%)、nacl(25wt%)、naf(10wt%)、caf2(5wt%);
43.(2)使用750mm
×
245mm的扁锭结晶器进行半连续铸造,半连续的铸造参数为:冷却水压0.05mpa,冷却水流量15m3/h,结晶器内镁液温度680℃,铸造速度为60mm/min,结晶器液面采用sf6和co2的混合气体来进行保护;所得半连续铸棒经扒皮、去头尾后,获得镁合金板坯,板坯的厚度为220mm;
44.(3)轧制工艺开始前,需对所述板坯进行均匀化热处理,控制工艺参数为360℃下进行保温15h;随后采用双辊轧机进行热轧开坯及后续多道次轧制,轧制温度360℃,单道次压下量5%,整个轧制过程为一火轧制,中间不做退火处理,轧制成形30mm板材;随后对轧制后的板材进行时效和去应力退火处理,时效处理工艺参数为:温度180℃,时间为10h;退火处理工艺参数为:温度300℃、时间为0.5h,即得所需合金材料。
45.采用sun10电子万能试验机对本实施例所获得合金板材进行本体取样,试样的力学性能测试结果如表1所示,可见,经时效与退火处理后,本合金具有290mpa以上的抗拉强度、240mpa以上的屈服强度和18%以上的高延伸率。
46.表1实施例1中板材的力学性能
[0047][0048]
可见,本实施例合成的所述镁合金材料具有理想的强度性能。
[0049]
实施例2
[0050]
本实施例所述低成本高强度镁合金成分(质量百分比)为:锌(zn)4.5wt%、硅(si)0.5wt%、锰(mn)0.3wt%、锆(zr)0.5wt%,其余为镁(mg)和不可避免的杂质元素。
[0051]
本实施所述低成本高强度镁合金的制备方法,包括如下步骤:
[0052]
(1)按照合金中各组分的质量百分比进行配料,加入占各合金成分物料总量2wt%的所述合金熔剂,并通入sf6和co2混合保护气体,加入所述金属镁并升温至720℃,保温至金属镁全部熔化;然后升温至760℃,依次加入所述纯锌、mgsi5中间合金、mgmn5中间合金和mgzr20中间合金,经搅拌熔化,得到镁合金液;将体系降温至730℃,通入干燥氩气对进行熔体精炼12min,并静置10min,此过程中不通电加热,待上述通气过程完成后再通电使得炉温恢复到730℃时,加入占各合金成分物料总量3wt%的所述精炼剂,搅拌后静置8min,之后进行扒渣并静置15min,得到所述金属液;
[0053]
所述合金熔剂包括:mgcl2(50wt%)、kcl(20wt%)、nacl(22wt%)、bacl2(8wt%);
[0054]
所述精炼剂包括:mgcl2(40wt%)、kcl(20wt%)、nacl(25wt%)、naf(8wt%)、caf2(7wt%);
[0055]
(2)使用750mm
×
245mm的扁锭结晶器进行半连续铸造,半连续的铸造参数为:冷却水压0.07mpa,冷却水流量18m3/h,结晶器内镁液温度700℃,铸造速度为80mm/min,结晶器液面采用sf6和co2的混合气体来进行保护;所得半连续铸棒经扒皮、去头尾后,获得镁合金板坯,板坯的厚度为220mm,所得板坯样品的金相图如附图1所示,可见,其基本不存在枝晶偏析,平均晶粒尺寸约为125.9μm;
[0056]
(3)轧制工艺开始前,需对所述板坯进行均匀化热处理,控制工艺参数为390℃下进行保温18h;随后采用双辊轧机进行热轧开坯及后续多道次轧制,轧制温度:400℃,单道次压下量10%,整个轧制过程为一火轧制,中间不做退火处理,轧制成形25mm板材;随后对轧制后的板材进行时效和去应力退火处理,时效处理工艺参数为:温度175℃,时间为20h;退火处理工艺参数为:温度350℃、时间为1h,即得所需合金材料。所述合金材料时效态样品的金相图如附图2所示,为细小的再结晶晶粒和沿轧制方向被拉长的初始晶粒组成的混晶组织,再结晶晶粒的平均尺寸约为9.8μm。
[0057]
采用sun10电子万能试验机对本实施例所获得合金板材进行本体取样,试样的力学性能测试结果如表2所示,经时效与退火处理后,本合金具有290mpa以上的抗拉强度、230mpa以上的屈服强度和20%以上的高延伸率。
[0058]
表2实施例2中板材的力学性能
[0059][0060]
可见,本实施例合成的所述镁合金材料具有理想的强度性能。
[0061]
实施例3
[0062]
本实施例所述低成本高强度镁合金成分(质量百分比)为:锌(zn):4.3%,硅(si):0.3%,锰(mn):0.3%,锆(zr):0.6%,其余为镁(mg)和不可避免的杂质元素。
[0063]
所述低成本高强度镁合金的制备方法,具体步骤如下:
[0064]
(1)按照合金中各组分的质量百分比进行配料,加入占各合金成分物料总量4wt%的所述合金熔剂,并通入sf6和co2混合保护气体,加入所述金属镁并升温至730℃,保温至金
属镁全部熔化;然后升温至770℃,依次加入所述纯锌、mgsi5中间合金、mgmn5中间合金和mgzr20中间合金,经搅拌熔化得到镁合金液;将所述镁合金液降温至730℃,通入干燥氩气对熔体精炼14min,并静置10min,此过程中不通电加热,待上述通气过程完成后再通电使得炉温恢复到730℃时,加入占各合金成分物料总量5wt%的所述精炼剂,搅拌后静置9min,之后进行扒渣并静置15min,得到所述金属液;
[0065]
所述合金熔剂包括:mgcl2(45wt%)、kcl(25wt%)、nacl(25wt%)、bacl2(5wt%);
[0066]
所述精炼剂包括:mgcl2(40wt%)、kcl(20%)、nacl(25wt%)、naf(10wt%)、caf2(5wt%);
[0067]
(2)使用750mm
×
245mm的扁锭结晶器进行半连续铸造,半连续的铸造参数为:冷却水压0.08mpa,冷却水流量20m3/h,结晶器内镁液温度710℃,铸造速度为100mm/min,结晶器液面采用sf6和co2的混合气体来进行保护;所得半连续铸棒经扒皮、去头尾后,获得镁合金板坯,板坯的厚度为220mm;
[0068]
(3)轧制工艺开始前,需对所述板坯进行均匀化热处理,控制工艺参数为420℃下进行保温20h;随后采用双辊轧机进行热轧开坯及后续多道次轧制,轧制温度420℃,单道次压下量12%,整个轧制过程为一火轧制,中间不做退火处理,轧制成形35mm板材;随后对轧制后的板材进行时效和去应力退火处理,时效处理工艺参数为:温度190℃,时间为20h;退火处理工艺参数为:温度380℃、时间为2h,即得所需合金材料。
[0069]
采用sun10电子万能试验机对本实施例所获得合金板材进行本体取样,试样的力学性能测试结果如表3所示,可见,经时效与退火处理后,本合金具有290mpa以上的抗拉强度、220mpa以上的屈服强度和20%以上的高延伸率。
[0070]
表3实施例3中板材的力学性能
[0071][0072]
可见,本实施例合成的所述镁合金材料具有理想的强度性能。
[0073]
实施例4
[0074]
本实施例所述低成本高强度镁合金成分(质量百分比)为:锌(zn)3wt%、硅(si)0.4wt%、锰(mn)0.3wt%、锆(zr)0.65wt%,其余为镁(mg)和不可避免的杂质元素。
[0075]
本实施所述低成本高强度镁合金的制备方法同实施例2。
[0076]
实施例5
[0077]
本实施例所述低成本高强度镁合金成分(质量百分比)为:锌(zn)6wt%、硅(si)0.1wt%、锰(mn)0.5wt%、锆(zr)0.4wt%,其余为镁(mg)和不可避免的杂质元素。
[0078]
本实施所述低成本高强度镁合金的制备方法同实施例2。
[0079]
综上,本发明所述镁合金材料通过在合金成分中添加少量的硅和锰,避免采用贵金属及稀土元素,实现原材料层面成本的降低,在满足高强度指标要求的前提下,大幅度降低材料的制备成本。
[0080]
以上对本发明实施例进行了详细介绍,本文中应用了具体个例对本发明的原理及
实施方式进行了阐述,以上实施例的说明只是用于帮助理解本发明的方法及其核心思想;同时,对于本领域的一般技术人员,依据本发明的思想,在具体实施方式及应用范围上均会有改变之处,综上所述,本说明书内容不应理解为对本发明的限制。