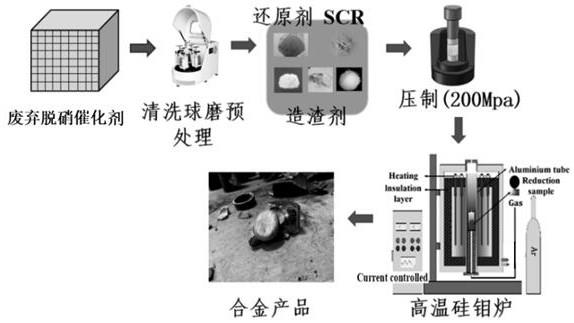
一种利用废弃脱硝催化剂制备ti-al-si合金的方法
技术领域
1.本发明涉及固废回收利用技术领域,特别涉及一种回收废弃脱硝催化剂直接制备ti-al-si合金的方法。
背景技术:2.在以煤炭资源为主要能源的当代,火力发电场排除的烟气是污染源之一。其中no
x
的排放会导致很严重的自然灾害,比如酸雨和光化学烟雾,因此no
x
的排放处理成为了有待解决的重要环境问题。在《火电厂氮氧化物防治技术政策(2021新版)》中规定:当排放物含量不能满足氮氧化物排放的要求时,应当增设烟气脱硝设施。
3.在众多的治理no
x
技术中,选择性催化还原法(selective catalytic reduction)是最为成熟且应用最广的脱硝技术。该法是在一定温度和催化剂作用下,利用氨或烃作为还原剂可选择性地将no
x
还原为氮气和水的方法。此法对大气环境质量的影响不大,是目前脱硝效率最高,最为成熟,且应用最广的脱硝技术。scr技术是还原剂(nh3)在催化剂的作用下,将烟气中no
x
还原为氮气和水。“选择性”指氨有选择地将no
x
进行还原的反应。催化反应温度在320℃~400℃。该技术无副产品,脱硝效率能达到80~90%以上。一般来说,脱硝催化剂的寿命约为25000小时,长时间使用会导致脱硝催化剂失活,一部分失活后的催化剂可以靠清洗补充催化剂元素可以重新激活使用,但是有很多无法修复的脱硝催化剂只能被掩埋处理。掩埋处理不仅占用了土地资源而且会对环境造成不可逆转的污染,其中的重金属会伴随着生态圈的循环进入人体,影响人类健康。
4.破损无法修复的废弃脱硝催化剂中有大量的重金属物质,其中tio2含量为80%~90%,sio2含量为6%~10%,wo3含量为4%~6%,v2o5含量为0.4%~1%。这些金属都有较高的回收价值,有效的回收这些金属可以实现资源循环利用,减少环境污染,提高使用效益。目前,废弃脱硝催化剂主要分为火法和湿法两种,大量的研究都是围绕着提取废弃脱硝催化剂中的v和w等金属,而对含量最多的ti有所忽略,只有少量的报道。并且通过湿法来回收废弃脱硝催化剂中的重金属,工艺过于复杂,不利于金属的回收利用。
技术实现要素:5.针对现有技术存在的上述不足,本发明的目的在于提供一种利用废弃脱硝催化剂直接制备ti-al-si合金的方法,解决现有废弃脱硝催化剂回收过程中,缺乏对金属钛的回收,且回收工艺复杂的问题。
6.为了解决上述技术问题,本发明采用的技术方案是这样的:
7.一种利用废弃脱硝催化剂制备ti-al-si合金的方法,具体步骤包括:
8.1)预处理废弃脱硝催化剂:对废弃脱硝催化剂依次进行去灰、清洗、球磨处理,并过100~200目筛;
9.2)混合原料:按如下质量组分混合原料,预处理后的废弃脱硝催化剂10~30份、还原剂10~30份、造渣剂30~50份;
10.3)压制原料:对步骤2)的混合原料进行压制,压样机压力为200~400mpa,然后放入坩埚中;
11.4)熔炼:将步骤3)装有混合原料的坩埚放入感应炉中,通入氩气,在1400~1700℃下进行熔炼,保温20~30min,得到表面覆盖炉渣的熔体;
12.5)冷却起锭:将步骤3)所得熔体冷却,通过起锭除去表面覆盖的炉渣,得到ti-al-si合金。
13.进一步,所述步骤2)混合原料中各质量组分为:预处理后的废弃脱硝催化剂20~30份、还原剂20~30份、造渣剂40~50份。
14.进一步,所述还原剂为铝和钙的粉末、或铝钙合金。
15.进一步,所述铝钙合金的质量组分不低于10份。
16.进一步,所述造渣剂为caco3、naco3、na3alf6和mgf2的混合物;其中各组分质量百分含量为caco320~30%、naco320~30%、na3alf615~25%和mgf215~25%。
17.进一步,所述造渣剂的质量比为caco3:naco3:na3alf6:mgf2=28:28:22:22。
18.进一步,所述步骤4)熔炼温度为1550~1700℃,保温时间为30min。
19.进一步,所述废弃脱硝催化剂是损坏无法再次激活的催化剂。
20.进一步,所述步骤4)所述氩气纯度≥99.999%。
21.进一步,熔炼前先将废弃脱硝催化剂和造渣剂高温焙烧5h去除水分。
22.相比现有技术,本发明具有如下有益效果:
23.1、本发明所提供的废弃脱硝催化剂的直接回收方法无湿法处理过程,通过一步法实现了废弃脱硝催化剂的资源回收利用,制备工艺简单,便于控制。
24.2、本发明提供了一种有效回收废弃脱硝催化剂直接制备ti-al-si合金的方法,以铝钙合金作为还原剂,caco3、naco3、na3alf6和mgf2作为造渣剂,na3alf6和mgf2可以降低熔渣的熔点,而且起到了保护炉衬的作用,经过感应炉高温熔炼后,在无湿法的过程下,实现了废弃脱硝催化剂贵重金属的回收利用。并且,造渣剂的密度和粘度较低,可以更好的实现渣金分离提高废弃脱硝催化剂中有价金属的回收率。
25.3、采用本发明方法钛的回收率可达98%,硅的收得率可达98%,w的收得率可达98%,v的收得率可达97%。
附图说明
26.图1是本发明制备ti-al-si合金的工艺流程图;
27.图2是实施例1的x射线衍射(xrd)分析图谱;
28.图3是实施例1的扫描电镜(sem)和x射线能谱分析(eds)面扫图。
具体实施方式
29.为了使本领域技术人员更好地理解本发明的技术方案,下面结合具体实施例对本发明作进一步的说明,但本发明的实施方式不仅限于此。
30.参见图1,本发明提供一种废弃脱硝催化剂直接制备ti-al-si合金的方法,具体步骤包括:
31.1)预处理废弃脱硝催化剂:对废弃脱硝催化剂依次进行去灰、清洗、球磨处理,并
过100目筛;以便之后能得到较纯的ti-al-si合金。
32.2)混合原料:按如下质量组分混合原料,预处理后的废弃脱硝催化剂10~30份、还原剂10~30份、造渣剂30~50份;
33.3)压制原料:对步骤2)的混合原料进行压制,然后放入坩埚中;
34.4)熔炼:将步骤3)装有混合原料的坩埚放入感应炉中,通入氩气,在1400~1700℃下进行熔炼,保温20~30min,得到表面覆盖炉渣的熔体。在氩气气氛下进行,可以防止还原产物被氧化;
35.5)冷却起锭:将步骤3)所得熔体冷却,通过起锭除去表面覆盖的炉渣,得到ti-al-si合金。
36.优选熔炼炼前先将废弃脱硝催化剂和造渣剂高温焙烧;以便去除其中的水分及有机杂质,提高炉料的单位热效应。优选焙烧时间为5小时,以便达到更好的结晶水取出效率。
37.优选混合原料质量组分为:废弃脱硝催化剂20~30份,还原剂10~30份,造渣剂40~50份,以便提高废弃脱硝催化剂中有价金属的回收效率。
38.优选还原剂的粒径≤100目,可以提高反应的速度和产率;优选还原剂的纯度≥99%,可以提高反应的速率且减少杂质含量。
39.本发明选用的方法为铝热还原法,al为主要还原剂,ca作为脱氧剂加入,提高合金纯度,降低氧含量。
40.本发明提供了一种回收废弃脱硝催化剂的冶金钛渣,包括如下质量含量的组分,如表1。
41.表1废弃脱硝催化剂的成分
[0042][0043]
本发明选用了五元渣系,可以增加冶炼过程中渣的流动性,并且增加传质效率,分离废弃脱硝催化剂中的有害元素,降低合金中的有害元素,提高合金纯度。
[0044]
在本发明中,解决的技术问题是提供一种低熔点低密度高效回收废弃脱硝催化剂中的有价金属的渣相,直接一步制备ti-al-si合金。
[0045]
实施例1
[0046]
一种废弃脱硝催化剂直接制备ti-al-si合金的方法,废弃脱硝催化剂的组成如表2所示。
[0047]
表2
[0048]
[0049]
具体步骤包括:
[0050]
1)将废弃脱硝催化剂除灰,清洗,球磨过筛得到100目以下的原料;
[0051]
2)将废弃脱硝催化剂50g、caco320g、naco320g、na3alf614g、mgf214g与33g还原剂铝钙合金混匀;
[0052]
3)将步骤2)中的原料混合后压制,压样机压力为200mpa,然后放入坩埚中;
[0053]
4)将装有原料的坩埚,放入硅钼炉中加热至1550℃,保温30min;
[0054]
5)待冶炼结束后,样品随炉冷却,起锭除渣得到ti-al-si合金。
[0055]
如图2所示,本实施例所得合金的x射线衍射(xrd)分析图谱。由图2可知,其中tial、al5ti2、al
3v0.3
t
0.6
和ti5si3等合金相被检测到,说明废弃脱硝催化剂中的有价元素被有效回收。其中,w元素因为含量较少,不易被xrd检测。
[0056]
参见图3,为本实施例所得合金的扫描电镜(sem)和x射线能谱分析(eds)面扫图。由图3可知,合金主要相为tial合金和tisi合金组成,从eds面扫图中可以看出,sem图谱中颜色较亮的部分主要为tisi合金,其余部分主要为tial合金,且该合金氧含量较低,这与xrd检测结果相符。
[0057]
经电感耦合等离子体(icp)检测,钛的收得率约为98%,硅的收得率约为98%,w的回收率约为97%,v的回收率约为97%。
[0058]
实施例2
[0059]
一种废弃脱硝催化剂直接制备ti-al-si合金的方法,废弃脱硝催化剂的组成如表3所示,
[0060]
表3
[0061][0062]
具体步骤包括:
[0063]
1)将废弃脱硝催化剂除灰,清洗,球磨过筛得到100目以下的原料;
[0064]
2)将废弃脱硝催化剂100g、caco340g、naco340g、na3alf630g、mgf230g与70g还原剂铝钙合金混匀;
[0065]
3)将步骤2)中的原料混合后压制,压样机压力为400mpa,然后放入坩埚中;
[0066]
4)将装有原料的坩埚,放入硅钼炉中加热至1700℃,保温30min;
[0067]
5)待冶炼结束后,样品随炉冷却,起锭除渣得到ti-al-si合金。
[0068]
经电感耦合等离子体(icp)检测,钛的收得率约为97%,硅的收得率约为95%,w的回收率约为98%,v的回收率约为97%。
[0069]
综上,本发明所提供的废弃脱硝催化剂的直接回收方法通过一步法实现了废弃脱硝催化剂的资源回收利用,制备工艺简单,便于控制。并且,熔炼后钛的回收率可达98%,硅的收得率可达98%,w的收得率可达98%,v的收得率可达97%,取得了意想不到的效果。
[0070]
最后需要说明的是,以上实施例仅用以说明本发明的技术方案而非限制技术方案,本领域的普通技术人员应当理解,那些对本发明的技术方案进行修改或者等同替换,而
不脱离本技术方案的宗旨和范围,均应涵盖在本发明的权利要求范围当中。