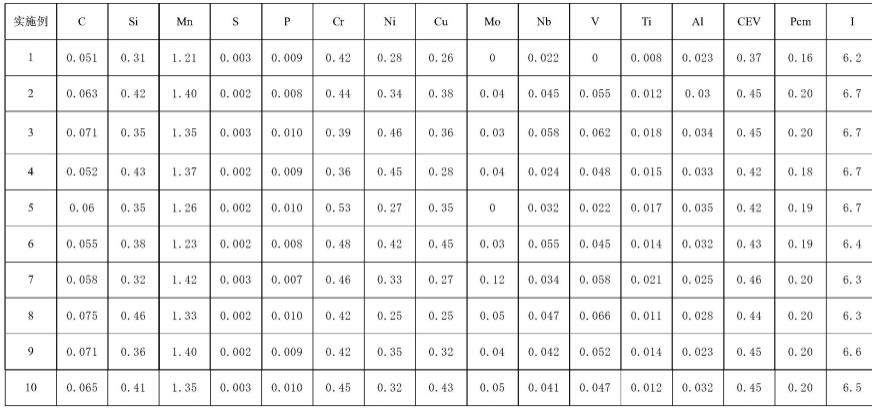
1.本发明涉及金属材料领域,尤其涉及一种低屈强比易焊接耐候桥梁钢及其制造方法。
背景技术:2.由于钢具有强度高、自重轻以及良好的塑性和韧性等优点,因此跨越江河湖海、深山峡谷的大跨度桥梁均采用钢桥。1990年以来,国外开展了一系列针对高性能钢在桥梁工程中的实用性及可靠性等方面研究,研究结果表明,高性能钢在低温韧性、抗脆断性、疲劳性以及持久强度等方面与普通钢材相比都有较大改善。
3.普通钢桥易生锈,严重影响其服役期内的安全性,因此钢桥防腐涂装十分重要,而桥梁制造与服役过程中的反复涂装成本巨大。数据表明,在钢桥40年的使用期间内,普通钢加三次反复涂装的费用己超过了裸露使用耐候钢桥费用的两倍。可见,使用无涂装耐候钢可大大降低桥梁全寿命成本,经济效益巨大,因此高性能耐候桥梁钢是国内外桥梁发展的趋势。
4.为保证桥梁结构的安全性和长寿命,钢板不仅需要具有一定的强度、塑性和韧性以外,还应该具有较小的屈强比和良好的z向性能,特殊环境服役下的桥梁钢还要求必须具有良好的耐候性能。随着桥梁钢结构日益增加,提高桥梁钢结构制造企业的焊接效率也是势在必行,这就要求桥梁钢具有优异的焊接性能。因此,研制兼具有较高的强韧性、低屈强比、耐候和良好焊接性能等综合技术特征的桥梁用钢成为新型绿色桥梁发展的亟需。
5.技术特征和指标的复杂性、多样性显著增加了高强韧低屈强比易焊接耐候桥梁钢的研发难度。首先,钢板强度的提高,使轧制变形抗力增大,道次变形率受到限制,使晶粒细化和控制难度倍增,而钢板厚度增加将导致厚度截面温度梯度增加、恶化厚度方向的冷却和组织均匀性;其次,钢板的低屈强比要求也会激化强度-韧性矛盾,进一步增加性能控制难度,同时桥梁钢需要具有良好的耐蚀性和焊接性能,需要进一步对成分进行优化设计。因此,如何使高强度桥梁钢兼具低屈强比、良好的耐候性能及焊接性能等综合技术特征是本发明要解决的关键问题。
6.目前,国内外对高强韧、耐候桥梁钢板有一些研究,经检索发现了部分专利和文献,但其所记载的内容与本发明的技术方案所述成分、生产方法、性能、产品类别等方面存在明显差异。
7.中国发明专利申请号cn 107385358 a公开了一种tmcp型屈服420mpa桥梁钢板及其生产方法,该发明专利申请钢板的化学成分组成及质量百分含量为:c:0.07~0.09%,si:0.25~0.50%,mn:1.40~1.60%,p《0.015%,s《0.005%,ni:0.15~0.25%,cr:0.10~0.20%,nb:0.020~0.030%,al:0.030~0.050%,v:0.030~0.040%,余量为fe和不可避免的杂质;生产方法包括冶炼、连铸、加热、轧制、冷却工序。该发明钢板化学成分采用低c,nb、v微合金化设计,辅以ni、cr等合金元素确保钢板强度、韧性匹配,钢板最大厚度可达到70mm。但该发明专利申请的缺点是钢板不具有耐候性能,不能满足桥梁钢裸露使用。
8.中国发明专利申请号cn 109797342 a公开了一种用于钢结构制作的高强度、高韧性、耐大气腐蚀钢板及其制造方法,元素成分wt%:c:0.03~0.10%,si:0.30~0.50%,mn:1.10~1.50%,p《0.010%,s《0.003%,cr:0.45~0.70%,cu:0.25~0.40%,ni:0.30~0.40%,alt:≥0.030%,ti:0.006~0.030%,v:0.040~0.080%,mo:0.02~0.08%,ca:0.0010~0.0030%,n:0.0020~0.0080%,b:0.0002~0.0030%,ce:0.001~0.010%,耐大气腐蚀指数i》6.5,cev《0.54,pcm《0.27,余量为fe和不可避免的杂质。该发明采用特定化学成分设计和钢板调制工艺获得具有贝氏体组织的高性能钢板,能够用于桥梁、高层建筑等钢结构制作。但该发明专利申请的缺点是钢板不具有较低的屈强比,安全性能不好,且添加ca、b、ce等稀有元素,冶炼困难,提高生产成本;碳当量过高,焊接性能较差。
9.中国发明专利申请号cn 102534384 a公开了一种无cr高性能耐候桥梁钢及其制备方法。该发明的无cr高性能耐候桥梁钢,其化学组成按质量百分比为:c:0.02~0.05%,si:0.20~0.30%,mn:0.6~1.00%,p≤0.02%,s≤0.010%,cu:0.20~0.40%,ni:0.30~0.80%,nb:0.04~0.07%,ti:0.005~0.015%,al≤0.02%,余量为fe及杂质。该发明的无cr高性能耐蚀桥梁钢具有良好的综合力学性能、焊接性能并且不含有毒性元素cr,同时具有优良的耐大气海洋腐蚀性。该发明桥梁钢添加了较多的ni合金,成本较高,且屈强比较高,不能满足桥梁安全性能。
10.日本发明专利申请号jp1992173920(a)公开了低屈服比厚高张力板,其含有较高的ni元素和b元素,成本较高,且耐候性能较差,不能满足相关桥梁工程要求。
11.综上所述,现有技术对低屈强比易焊接耐候桥梁钢的研究尚有不足,多数桥梁钢不具备低屈强比及耐候性能,不能满足相关工程应用要求。
技术实现要素:12.本发明目的是为了克服现有技术的缺陷,提供了一种低屈强比易焊接耐候桥梁钢及其制造方法。按照本发明钢的化学成分及生产工艺要求生产的产品具有高强韧性、高塑性、低屈强比、优异的耐候性、焊接性能以及抗层状撕裂性能。本发明采用的技术手段如下:
13.一种低屈强比易焊接耐候桥梁钢,其组分及质量百分比含量为:c:0.051%~0.080%、si:0.20%~0.50%、mn:1.20%~1.50%、p≤0.010%、s≤0.003%、cr:0.30%~0.60%、ni:0.20%~0.50%、cu:0.20%~0.50%、mo:0%~0.20%、nb:0.02%~0.06%、v:0%~0.070%、ti:0.005%~0.025%、al:0.010%~0.040%,余量为铁和不可避免的杂质,碳当量cev≤0.46%、焊接敏感性pcm≤0.20%,耐大气腐蚀指数i≥6.2。
14.进一步地,钢板最大厚度100mm,屈服强度≥345mpa,抗拉强度≥500mpa,断后伸长率≥22%,屈强比≤0.80,厚度方向z向断面收缩率≥60%,钢板母材的-40℃冲击功≥200j。
15.进一步地,预设的大气环境腐蚀下的周浸腐蚀试验168h厚度腐蚀速率为0.74~1.20g/m2.h。
16.进一步地,耐候性能是345mpa级普通桥梁钢的2倍以上。
17.进一步地,焊接热影响区-40℃冲击功≥100j。
18.为实现本发明的目的,本发明还公开了一种技术方案,即一种低屈强比易焊接耐候桥梁钢的生产方法,包括铁水预处理、转炉冶炼、炉外精炼、连铸、轧制、冷却、矫直、热处
理工艺步骤,其中的铁水预处理、转炉冶炼、炉外精炼的步骤可采用现有技术,本发明主要具体工艺步骤如下:
19.1)连铸工艺:连铸坯浇注过热度10~25℃,连铸坯厚度>6倍的成品钢板厚度;浇注过热度和连铸坯拉速的控制可以有效减少铸坯质量缺陷。
20.2)轧制工艺:
21.连铸坯加热工艺:连铸坯加热段温度1210~1250℃,均热段温度1190~1230℃,均热段时间不低于60min;加热工艺可以满足合金特别是nb、v元素的固溶,同时,防止奥氏体晶粒过分长大;加热时间可保证坯料温度均匀性。
22.轧制包括粗轧工艺和精轧工艺;
23.其中,粗轧工艺开轧温度为1070~1120℃,粗轧终轧温度为1020~1070℃,粗轧阶段的轧制温度和变形工艺使奥氏体晶粒再结晶并且抑制晶粒长大,粗轧阶段保证至少最后2个道次的每道次变形率大于15%且道次间隔不超过15s,粗轧阶段累计变形率≥50%,粗轧末段采用大压下和短间隔工艺可以降低生产桥梁用钢的设备负荷,利用多道次大压下率变形叠加效果,促进奥氏体发生再结晶,达到晶粒细化目标,适宜本发明耐候桥梁钢板的生产;增大连铸坯到成品钢板的压缩比可以有效控制晶粒尺寸,总压缩比≥6,所述总压缩比为连铸坯厚度与成品钢板厚度之比。
24.中间待温坯厚度2.5~3.5t,其中t为成品钢板厚度;精轧工艺开轧温度为830~900℃,精轧终轧温度为770~830℃;适宜的中间待温坯厚度和道次变形率既可以满足未再结晶区奥氏体变形和形变能的积累,又能保证在原铸坯厚度一定的情况下粗轧阶段获得足够的变形率,达到晶粒细化目的;低的精轧温度促进奥氏体形变能的积累和nb、v、ti的细小析出相的诱导析出,增加形核位置;精轧末期在相变点温度附近足够的变形有利于细小的铁素体生成,可以降低有效晶粒尺寸,明显提高低温韧性。
25.3)冷却工艺:轧后钢板进行加速水冷,轧制完成后钢板待温,开始水冷冷却温度680~740℃,返红温度400~600℃,冷却速度为10~25℃/s;随后,进行热矫直和空冷;控制钢板开始水冷温度可以改善冷却时钢板的应力过大,保证钢板板型,又可以使形成细小的先共析铁素体,钢板的晶粒尺寸更加均匀,进一步降低钢板屈强比;合适终冷温度可以促进贝氏体形成,细化m/a岛,提高钢板强度。
26.为了进一步保证钢板晶粒尺寸均匀,提高钢板塑韧性,还包括4)热处理工艺:对轧后钢板进行高温回火热处理,加热温度为580~690℃,总保温时间为2.5~4.5min/mm,出炉后空冷至室温。高温回火的目的一是消除钢板的残余应力,使钢板的性能更加均匀,有利于后续加工制造,二是通过两相区回火生成一部分铁素体组织,降低屈强比。三是进一步细化晶粒,提高钢板的塑性与低温冲击性。
27.进一步地,精轧过程中,单道次变形率不低于10%。
28.进一步地,精轧处理后,对轧制后钢板进行堆垛缓慢冷却,堆垛缓冷温度≥300℃,堆垛时间≥24h。
29.进一步地,钢板最终微观组织为铁素体+及珠光体、铁素体+珠光体+贝氏体、铁素体+贝氏体的复合组织中的其中一种,其中,铁素体体积百分含量在20%~70%。
30.本发明的各化学组分的选用原理及含量设计原因如下:
31.本发明c可以通过间隙固溶发挥强化作用,还可以与nb等合金元素作用形成细小
的碳化物析出,在轧制变形或奥氏体相变之前析出,阻碍晶粒长大,提高形核率,细化组织;同时,还可以阻碍位错移动,有效提高抗拉强度,降低屈强比,因此,c含量不宜过低;但是,c的增加对韧性不利,特别是对低温韧性有影响较大;而且,c的增加会恶化钢板的焊接性能。所以,c含量也不能过高,本发明认为c含量控制在0.051%~0.080%较为适宜。
32.si是钢中脱氧元素之一,si能改善钢的耐腐蚀性能,同时si具有较强的固溶强化作用,si在钢中可以增加残余奥氏体数量,降低钢板的屈强比。但过量的si将使贝氏体晶粒尺寸增大,恶化钢的韧性及焊接性能。因此本发明中si含量的控制在0.20%~0.50%较为适宜。
33.mn可有效提高强度和淬透性;降低奥氏体相变温度,抑制钢板加速冷却前的相变晶粒长大,发挥细化晶粒作用,提高钢板强度;但是,mn含量过高会容易抑制铁素体转变,影响钢的屈服强度,不利于降低屈强比,过高的mn含量会诱发偏析,恶化钢板组织均匀性和层状撕裂性能且不利于焊接,本发明认为将mn含量控制在1.20%~1.50%较为适宜。
34.p、s在本发明中为有害杂质元素,含量越低越好;其中,过高的p会导致组织偏析,对低温韧性有明显的不利影响,本发明将p控制在≤0.010%,s含量增加会促进夹杂物的生成和长大,恶化低温性能和厚度方向性能,因此,s≤0.003%。
35.cr是本发明中提高耐候性的主要元素,cr含量的提高有利于细化α-feooh,并且cr能置换α-feooh中的fe3
+
形成无定形的α-(fe1-xcrx)ooh。在钢板表面生成α-feooh和δ-feooh致密锈膜层,可以保护钢不再继续腐蚀,cr与cu复合添加,可以形成更加致密的锈层,耐候性显著提高。cr还具有较好的淬透性,在钢板轧制加速冷却的过程中能够提高钢板心部冷速,细化钢板心部组织,提高钢板的低温韧性和z向性能,但是cr含量过高会导致钢板热加工性劣化,所以将cr含量限定在0.30%~0.60%。
36.ni提高钢材强度效果不明显,但能保持良好的塑性、低温韧性以及耐腐蚀性能,同时在高温下具有防锈和耐热能力。当ni与cr、cu复合添加时,不仅可以明显改善低温韧性,还可以提高锈层的稳定性,显著提高耐腐蚀性能。通过ni、mn等奥氏体稳定化元素还可以在两相区热处理过程中获得适量、细小且稳定的逆转变奥氏体,有利于钢的塑性提高和屈强比降低。但ni含量过高,钢板表面易产生大量难以脱落的氧化铁皮,成本也增加,本发明认为将ni含量控制在0.20%~0.50%较为适宜。
37.cu能改善钢的淬透性,可以明显提高厚钢板的心部强度,也是重要的提高耐候性的元素,在厚钢板缓慢冷却过程中,适量cu通过自回火可析出ε-cu,提高钢板强度。cu含量过高时,会降低钢板的表面质量和塑性。本发明认为将cu含量控制在0.20%~0.50%较为适宜。
38.mo可以起到稳定锈层的作用,能够有效提高钢板的腐蚀性能,特别是在含有氯化物的环境中,可显著提高耐点蚀和缝隙腐蚀的能力,而且,mo有助于轧制时奥氏体晶粒的细化,同时提高钢板高温回火稳定性,mo含量过高时,会降低钢板的焊接性能;此外,mo为贵重元素,导致钢的成本大幅度上升。因此,在本钢种中将mo含量限定在0%~0.20%。
39.本发明中nb的作用包括(1)固溶强化;(2)在轧制过程中和加速冷却前的析出,钉扎晶界,促进形核,有效细化晶粒,从而提高强度和改善韧性;(3)降低奥氏体相变温度,能够细化晶粒;在高温过程中析出的nbc粒子或与v、mo复合析出第二相,能够提高钢的高温强度。但是,nb含量过高会恶化焊缝和热影响区韧性,还会增加成本,本发明认为将nb含量控
制在0.02%~0.06%较为适宜。
40.由于v具有较低的全固溶温度,均热时基本全部固溶,轧制过程中固溶的v能有效提高淬透性和提高再结晶温度,在快速水冷过程中v可以形成细小的碳氮化物析出,显著提高钢板强度。在高温回火的过程中,固溶的v的碳氮化物也会析出,保证钢板高温回火强度。v还兼具固溶强化和降低屈强比作用,当v含量过高时,虽然显著提高强度,但恶化低温韧性和焊接性能。本发明认为将v含量控制在0.%~0.070%较为适宜。
41.ti可以发挥固n效果,形成以tin为主的析出相,能抑制高温条件下奥氏体的晶粒长大,也可以改善焊后热影响区韧性,在焊接过程中,tin粒子阻止热影响粗晶区晶粒长大,提高焊接接头低温韧性。另外ti由于较低的固溶度,易在奥氏体到铁素体的转变过程中以相间析出的形式出现,提高高温强度。但过多的ti会降低钢的韧性,本发明认为将ti含量控制在0.005%~0.0025%较为适宜。
42.al是强脱氧元素,还可与n结合形成aln,能够起到细化晶粒作用,提高低温冲击韧性,降低钢的脆性转变温度。al还具有抗氧化性和抗腐蚀性能,al与cr、si合用,可显著提高钢的高温不起皮性能和耐高温腐蚀的能力,但是al含量过高对焊接性不利,本发明认为al含量控制0.010%~0.040%为宜。
43.碳当量(cev)和焊接裂纹敏感性指数(pcrn)可预测钢材冷裂纹倾向的大小,数值越小,说明钢材在焊接时产生裂纹的倾向就越小,钢材的焊接性能越好。其计算公式为:碳当量%(cev%)=c+mn/6+(cr+mo+v)/5+(ni+cu)/15,焊接裂纹敏感性指数%(pcm%)=c+si/30+mn/20+cu/20+ni/60+cr/20+mo/15+v/10+5b。本发明cev≤0.46%,pcm≤0.20,具有优异的焊接性能。
44.i值为耐大气腐蚀指数,其计算公式为:
45.i=26.01(%cu)+3.88(%ni)+1.20(%cr)+1.49(%si)+17.28(%p)-7.29(%cu)(%ni)-9.10(%ni)(%p)-33.39(%cu)2,当i值≥6.0时,可以认为该钢种为耐蚀钢,当其正常地暴露在空气中时,该钢可以裸钢(不涂漆)使用。本发明钢板的i值≥6.20,具有良好的耐大气腐蚀性能。
46.本发明具有以下优点:
47.1、本发明成分通过低c和低mn设计改善材料韧性,利用nb、v、ti元素抑制奥氏体晶粒长大并在奥氏体转变过程中的促进形核作用来细化晶粒,控制钢板厚度心部组织,提高组织均匀性;通过ni、cu、cr、mo元素增加固溶强化效果提高钢板的低温韧性及耐候性能;配以相应的生产工艺解决了桥梁用钢高强度、低屈强比、耐候及焊接性能等技术指标的匹配难题。
48.2、本发明没有添加稀土元素,降低了部分合金成本,并进一步提高钢板的塑韧性。
49.3、本发明cev及pcm较低,i值较高,具有优异的焊接性能和耐候性能。
50.4、本发明的冶炼、连铸工艺方案改善了铸坯质量,从而提高了钢板的低温韧性及z向性能。
51.5、本发明采用高温回火热处理工艺,最终获得了由铁素体+珠光体、铁素体+贝氏体、铁素体+珠光体+贝氏体其中一种组成的复相组织。适当的控制“软、硬”相含量配比可以使强度和塑性、韧性达到最佳配合,实现提高强度并降低屈强比的目的,从而得到良好的抗震性能。
52.6、本发明为控轧控冷以及一次热处理的制造方法,工序简单。
53.7、本发明所述一种低屈强比易焊接耐候桥梁钢板最大厚度100mm,屈服强度≥345mpa,抗拉强度≥500mpa,断后伸长率≥22%,屈强比≤0.80,厚度方向z向性能≥60%,-40℃冲击功≥200j,耐候性能是普通345mpa级桥梁钢的2倍以上,焊接热影响区-40℃冲击功≥100j。满足低温条件下桥梁钢的抗震、耐候、焊接性能需求。
附图说明
54.为了更清楚地说明本发明实施例或现有技术中的技术方案,下面将对实施例或现有技术描述中所需要使用的附图做以简单地介绍,显而易见地,下面描述中的附图是本发明的一些实施例,对于本领域普通技术人员来讲,在不付出创造性劳动性的前提下,还可以根据这些附图获得其他的附图。
55.图1为本发明实施例1的金相组织图。
56.图2为本发明实施例4的金相组织图。
57.图3为本发明实施例7的金相组织图。
具体实施方式
58.为使本发明实施例的目的、技术方案和优点更加清楚,下面将结合本发明实施例中的附图,对本发明实施例中的技术方案进行清楚、完整地描述,显然,所描述的实施例是本发明一部分实施例,而不是全部的实施例。基于本发明中的实施例,本领域普通技术人员在没有做出创造性劳动前提下所获得的所有其他实施例,都属于本发明保护的范围。
59.本发明实施例的化学成分见表1;相应实施例的冶炼连铸及板坯加热工艺见表2;相应实施例的粗轧工艺见表3;相应实施例的精轧工艺见表4;相应实施例的冷却和热处理制度见表5;相应实施例的性能和微观组织比例见表6;相应实施例的腐蚀速率见表7,其中,实施例1、4、7的金相图分别如图1~3所示。
60.表1本发明实施例的化学成分wt%
[0061][0062]
表2本发明实施例的连铸及铸坯加热工艺
[0063]
实施例浇注过热度,℃加热段温度/℃均热温度/℃均热段时间/min
11812201197692211228120778320123112098242212301217765191245121078621124012127372312291216758201233121180921123811989210221243122895
[0064]
表3本发明实施例的粗轧工艺
[0065][0066]
表4本发明实施例的精轧工艺
[0067][0068]
表5本发明实施例的冷却和热处理工艺
[0069][0070]
本发明经过表1的化学成分和表2~5的生产工艺,冶炼并轧制了10种实施例,本发明冶炼并轧制的10种实施例的性能如表6所示。
[0071]
表6本发明实施例的性能和微观组织比例
[0072][0073]
本发明耐候性能通过周浸腐蚀试验168h后的质量损失评定,具体腐蚀试验试验溶液:0.01mol/l nahso3;补充溶液:0.02mol/l nahso3;试验温度:45
±
2℃;相对湿度:70
±
5%;周浸轮转速:1圈/60分钟,得到的结论如表7所示。
[0074]
表7本发明实施例的腐蚀速率
[0075]
[0076][0077]
本发明一种低屈强比易焊接耐候桥梁钢及其制造方法,成分设计通过低c和低mn改善材料韧性和焊接性能,利用nb、ti、v元素抑制奥氏体晶粒长大并在奥氏体转变过程中的促进形核作用来细化晶粒,控制钢板厚度心部组织,提高组织均匀性;同时,针对高强度特点利用nb抑制奥氏体再结晶的作用,提高轧制温度,有效降低轧制抗力,也有利于增大轧制道次变形率;通过ni元素增加固溶强化效果并利用ni元素提高低温韧性;利用cr、cu、mo改善钢板的的淬透性、提高固溶强化作用、并且可以提高钢板的耐候性能,配以相应的冶炼、加热、轧制、冷却、热处理等生产工艺获得高强度、低屈强比、良好的耐候、焊接性等综合性能及理想的微观组织。
[0078]
最后应说明的是:以上各实施例仅用以说明本发明的技术方案,而非对其限制;尽管参照前述各实施例对本发明进行了详细的说明,本领域的普通技术人员应当理解:其依然可以对前述各实施例所记载的技术方案进行修改,或者对其中部分或者全部技术特征进行等同替换;而这些修改或者替换,并不使相应技术方案的本质脱离本发明各实施例技术方案的范围。