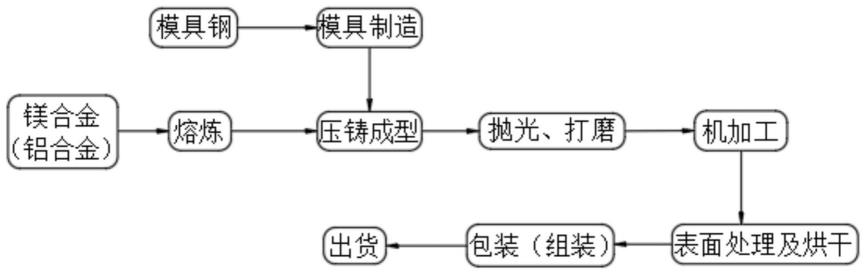
1.本发明涉及镁、铝合金压铸工艺方法技术领域,特别涉及一种镁合金、铝合金压铸工艺方法。
背景技术:2.目前镁、铝合金作为材料制造的产品越来越多,而镁、铝合金在制作产品中运用的方法为压铸法,压铸法具有生产效率高,尺寸精度高,批量生产成本低,压铸件的组织致密,抗拉强度和抗弯强度高的优点,但是,压铸件也有自身的缺陷,普通压铸件压铸速度较快,其内部热量散失慢,使其内应力增大,同时轻合金溶液内部可能存在气泡,使压铸件自身的韧性降低。
3.经检索,申请号为201310147616.7的中国专利,公开了一种轻合金的压铸方法,包括如下步骤:化料过程,将轻合金在连续融化保温炉内加热融化并搅拌除渣,然后利用除气机除气;压射过程,将融化后的原料在压铸料筒内加热压射并冷却成型形成铸件;退火过程,将铸件进行退火处理,空冷后得到成型产品。采用本发明的压铸工艺制备的压缩机密封盘退火处理后,由于在化料过程中进行了除气,内部没有气泡,退火后产品韧性也较好,但是在化料过程只是将轻合金放置在连续融化保温炉内加热融化,而在高温环境下,内部的轻合金很容易发生氧化,原料发生了改变,从而使后续生产出的成品中特性也随之改变。
4.因此,本发明提出了一种镁合金、铝合金压铸工艺方法。
技术实现要素:5.本发明的主要目的在于提供一种镁合金、铝合金压铸工艺方法,可以有效解决背景技术中的问题。
6.为实现上述目的,本发明采取的技术方案为:一种镁合金、铝合金压铸工艺方法,所述镁合金、铝合金压铸工艺流程具体如下:s1、选取高强度模具钢,根据需要制备需要进行压铸的合金工件的压铸成型模具;s2、外购符合要求的镁合金或铝合金原料,并将其投入压铸机自带的熔炉进行熔炼,得到熔融状态下的镁液或铝液;s3、将上述镁液或铝液通过压铸机压铸成型,并且镁液或铝液在压力下迅速冷却、结晶、凝固成型,得到成型铸件粗胚;s4、对成型铸件粗胚进行抛光打磨,使其表面光滑;s5,对抛光打磨后的成型铸件进行机加工,得到符合要求的高精度精密铸件;s6、对机加工后的铸件进行表面处理,防氧化,增加耐磨,加强表面硬度,处理完毕后进行包装出货,完成整个工艺。
7.优选的,在进行镁合金压铸时需要满足如下条件:1)将镁锭加热至150℃后方可加入;2)熔炼温度控制在660-680℃;3)熔炼和压铸过程中需要在浇铸炉内充入保护气体以防止镁液与空气接触发生氧化反应。
8.优选的,在浇铸炉内充入的保护气体为二氧化硫气体。
9.优选的,所述镁合金原料采用牌号为az91d、am60b、az81、am50a、am20、ae42、as41b中的任意一种。
10.优选的,在进行铝合金压铸时需要满足如下条件:1)进行熔炼前将符合标准要求的铝合金料、熔炼工具预热烘干,防止合金料、熔化工具表面吸附的湿气熔入铝液转化为氢气;2)回炉料添加比例不超过50%;3)熔炼温度控制在680-750℃;4)熔炼过程中利用熔剂对铝液进行精炼、除气、打渣、晶粒细化处理;5)压铸前炉内铝液进行保温,温度控制在640~680℃。
11.优选的,在进行铝合金浇筑的过程还包括对铝液进行炉前分析,取样检查断面晶粒组织及化学成份是否符合标准。
12.优选的,所述铝合金原料采用牌号为a380、380、a360、360、383、384、390、13、a13、43、218中的任意一种。
13.优选的,对成型铸件的表面处理包括清洗、钝化、喷油、喷粉、电泳、微弧氧化、化成和阳极氧化。
14.与现有技术相比,本发明具有如下有益效果:本发明通过将镁合金、铝合金锭通过熔解炉加热熔化,熔融的镁、铝液通过机械方式注入压铸机压室,然后通过压射冲头的高速运动,使镁、铝液在高压作用下高速充填模具型腔,镁、铝液在压力下迅速冷却、结晶、凝固成型。成型铸件经过各种表面处理和机械加工工艺后,成为各种不同结构及性能要求的镁合金、铝合金制品,其制品物理性能和功能都超过了行业标准和国内外同行业的同类产品水平,具有结构复杂、内部组织致密、力学性能优良、尺寸精度高、表面质量好等特点。
附图说明
15.图1为本发明的压铸工艺流程图。
具体实施方式
16.为使本发明实现的技术手段、创作特征、达成目的与功效易于明白了解,下面结合具体实施例,进一步阐述本发明。
17.实施例1本实施例具体说明镁合金的压铸工艺方法,具体如下:s1、选取高强度模具钢,根据需要制备需要进行压铸的合金工件的压铸成型模具;s2、外购符合要求的镁合金,将镁锭加热至150℃,并将其投入压铸机自带的熔炉进行熔炼,熔炼温度控制在660-680℃,得到熔融状态下的镁液;具体的,所述镁合金原料采用牌号为az91d、am60b、az81、am50a、am20、ae42、as41b中的任意一种;熔炼和压铸过程中需要在浇铸炉内充入保护气体以防止镁液与空气接触发生氧化反应。
18.s3、将上述镁液或铝液通过压铸机压铸成型,并且镁液或铝液在压力下迅速冷却、结晶、凝固成型,得到成型铸件粗胚;具体的,根据模具产品特征要求选择与之匹配的压铸机与压铸工艺,主要是调节控制压铸过程中的压力、速度、行程的变化,控制压射时间、冷却时间、储能时间及顶出时
间,通过对对铝液与模温的控制,选择性能优越的离型剂压铸出合格的产品;s4、对成型铸件粗胚进行抛光打磨,使其表面光滑;s5,对抛光打磨后的成型铸件进行机加工,得到符合要求的高精度精密铸件;主要是针对一些有高精度的装配要求,而模具成型无法满足的产品进行机械加工的一种工艺,如cnc车﹑铣等;s6、对机加工后的铸件进行表面处理,包括清洗、钝化、喷油、喷粉、电泳、微弧氧化、化成和阳极氧化等步骤,防氧化,增加耐磨,加强表面硬度,处理完毕后进行包装出货,完成整个工艺。
19.本实施例中,表面处理工艺是针对镁铝合金的特性,根据客户不同的要求,对工件进行清洁,防氧化,增加耐磨,加强表面硬度,也可以通过喷油,喷粉工艺遮盖压铸工件的一些表面缺陷,甚至达到客户对外观的多样化要求。
20.应当说明的是,本实施例中所述的保护气体为二氧化硫气体,其具体是由液态so2气化的,而液态so2是气体so2经压缩冷冻制取的,液态so2无色透明,有刺激酸臭味。液态so2于-10.09℃沸腾,-72℃冻结,一般用气化罐,其优点是可贮罐直接连接,便于使用,可减轻劳动强度,同时可显著减少so2放空所造成的浪费与污染。
21.实施例2本实施例主要对铝合金的压铸工艺进行详细说明。
22.具体的,铝合金的压铸工艺如下:s1、选取高强度模具钢,根据需要制备需要进行压铸的合金工件的压铸成型模具;s2、外购符合要求铝合金原料,并将其投入压铸机自带的熔炉进行熔炼,得到熔融状态下的镁液或铝液;所述铝合金原料采用牌号为a380、380、a360、360、383、384、390、13、a13、43、218中的任意一种。
23.s3、将上述镁液或铝液通过压铸机压铸成型,并且镁液或铝液在压力下迅速冷却、结晶、凝固成型,得到成型铸件粗胚;具体的,根据模具产品特征要求选择与之匹配的压铸机与压铸工艺,主要是调节控制压铸过程中的压力、速度、行程的变化,控制压射时间、冷却时间、储能时间及顶出时间,通过对对铝液与模温的控制,选择性能优越的离型剂压铸出合格的产品;s4、对成型铸件粗胚进行抛光打磨,使其表面光滑;s5,对抛光打磨后的成型铸件进行机加工,得到符合要求的高精度精密铸件;主要是针对一些有高精度的装配要求,而模具成型无法满足的产品进行机械加工的一种工艺,如cnc车﹑铣等;s6、对机加工后的铸件进行表面处理,包括清洗、钝化、喷油、喷粉、电泳、微弧氧化、化成和阳极氧化等步骤,防氧化,增加耐磨,加强表面硬度,处理完毕后进行包装出货,完成整个工艺。
24.本实施例中,表面处理工艺是针对镁铝合金的特性,根据客户不同的要求,对工件进行清洁,防氧化,增加耐磨,加强表面硬度,也可以通过喷油,喷粉工艺遮盖压铸工件的一些表面缺陷,甚至达到客户对外观的多样化要求。
25.应当说明的是,在进行铝合金压铸时需要满足如下条件:1)进行熔炼前将符合标准要求的铝合金料、熔炼工具预热烘干,防止合金料、熔化工具表面吸附的湿气熔入铝液转
化为氢气;2)回炉料添加比例不超过50%;3)熔炼温度控制在680-750℃;4)熔炼过程中利用熔剂对铝液进行精炼、除气、打渣、晶粒细化处理;5)压铸前炉内铝液进行保温,温度控制在640~680℃。
26.另外,需要说明的是,本发明通过采用规格型号为4500ton或3500ton的国产压铸机进行压铸,其主要是通过如下参数要求实现压铸:(1)自动给汤、自动喷雾、智能取件、输送全自动化作业;(2)慢压射速度在0~0.6m/s无级可调,且能实现匀速与加速运动;(3)快压射速度可达10m/s,能实现一级或多级高速段运动,控制精度可达2%;(4)建压时间最短小于30ms,慢、快压射转换时间小于20ms;(5)压射和增压终了时压力冲击峰值小于20%,具有压射终了制动减速功能;(6)压射比压于60~160mpa内无级可调;(7)一次压射后压力波动小于15%;(8)双回路模温控制系统精准控制模具温度。
27.在生产工艺上,依据iso/ts16949:2008、iso9001:2009质量体系及iso14001环境体系认证,采用qj 168-1985(镁合金铸件技术条件(中文))、qj 1635-1989(铸造镁合金熔炼规范(中文))、gb/t 15114-2009(铝合金压铸件)、ys/t 11-1991(铝及铝合金电阻熔炼炉 保温炉)、gb/t 1196-2008(重熔用铝锭)、iso 23079-2005(镁和镁合金、回炉料、要求、分类和验收)等标准,采用铝屑挤压成型回收系统、废镁重熔回收系统,配套相关环保设施,减少生产过程中的三废排放,以实现节约成本和环保的要求,达到清洁生产与循环经济的目标。
28.根据gb/t228-2002 金属材料室温拉伸试验方法,gb/t14452-93 金属弯曲力学性能试验方法(三点弯曲),gb/7314-87 金属压缩试验方法,产品砂孔标准astm-e505等方式对实施例1和实施例2中制备的产品进行物性功能测试,其测试结果分别如表1和表2。
29.表1:镁合金产品原材料物性功能指标
物性功能指标az91dam60baz81am50aam20ae42as41b实施例1极限抗拉强度a(mpa)230220220220185225215230屈服强度(mpa)16013036-108-128-106.012延伸率(%)36-8725747577575布氏硬度bhn7562140////140抗剪强度(mpa)140/707070//70疲劳强度(mpa)7070454545454545杨氏模量(gpa)4545
ꢀꢀꢀꢀꢀꢀ
表2:铝合金产品原材料物性功能指标商业标准a380360a360380383384390实施例2极限检验强度(mpa)320300320320310330320320屈服强度(mpa)160170170160150170250190延伸率(%)3.52.53.53.53.52.5《1.03.5布氏硬度bhn80757580758412080抗剪强度(mpa)190190180190/200/200疲劳强度c(mpa)140140140140145140140140
杨氏模量(gpa)7171717171//81通过上述的表1和表2可以看出,本发明所公开的一种镁合金、铝合金压铸工艺方法,其制备的合金铸件物理性能和功能都超过了行业标准和国内外同行业的同类产品水平,具有结构复杂、内部组织致密、力学性能优良﹑尺寸精度高、表面质量好等特点。
30.另外,需要说明的是,本发明公开的镁合金、铝合金压铸工艺方法在生产过程中,排放的废气主要有:1、打磨过程中产生的粉尘,主要是颗粒物; 2、熔镁、熔铝过程中产生的废气;3、有机废气;4、酸雾废气。
31.针对上述废气的处理方法为:1、加强自然进风、机械排风等方式,计划设置优良的通风系统,保证其工作温度及车间内的微量的有害气体符合国家卫生标准。
32.2、采用“旋风+布袋”干法除尘及湿法除尘,净化效率可达95%以上,能保证达标排放。
33.对于铝、镁合金废料的回收相关说明:对于镁﹑铝合金压铸过程中产生的不同废料,可通过不同的方式给于回收并加以再利用,既是对资源利用的需要,也是环境和成本上的需要。
34.铝合金一般废料如:水口﹑渣包﹑废品等可在做过一些清理工作后,直接与新料按一定比例添加,经过精炼、除气、打渣、细化等熔炼工艺后,必要时经过成份调整后获得符合国家或是国际标准的合金成份。当中需注意的是在回收过程中严格区分不同牌号的合金材料。对于打磨、机加后的铝屑回收公司采用的是铝屑挤压成型重熔回收系统,由于铝屑体积较小,如果直接在熔炼时添加,因其炉内表面温度高(达680℃以上),大部份铝屑会因高温而氧化成三氧化二铝,失去回收价值,且会影响原有材料的成份,并对后续压铸及产品质量带来一系列问题。铝屑挤压成型重熔回收系统是通过对零散的铝屑清理后,用特制的挤压设备将零散的铝屑挤压成块状,再投放烬内重熔,经精炼、除气、打渣、细化、检测后,变成铝锭循环使用。
35.镁合金废料回收分两种方式,一是通过重熔精炼装置进行回收,将废料清洁处理后投放炉内,通过精炼处理后镁液经两个静置室的三级过滤后进入浇注室再变成标准镁锭,所有过程是在密封并有保护气体的作用下进行。而对于高危废镁其主要工艺如下:将高危废镁经过清洁处理后投放坩锅内,将温度上升至镁合金沸点,形成蒸馏进入结晶器后结晶,一些杂质如硅﹑铁﹑铜等则以固态存于坩锅底,最后得到99.9%高纯度结晶镁。
36.以上显示和描述了本发明的基本原理和主要特征和本发明的优点。本行业的技术人员应该了解,本发明不受上述实施例的限制,上述实施例和说明书中描述的只是说明本发明的原理,在不脱离本发明精神和范围的前提下,本发明还会有各种变化和改进,这些变化和改进都落入要求保护的本发明范围内。本发明要求保护范围由所附的权利要求书及其等效物界定。