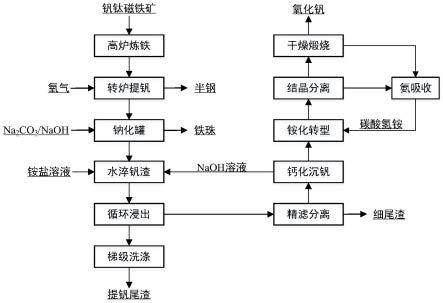
1.本发明涉及钒冶金化工领域,具体涉及一种短流程钒渣浸出方法。
背景技术:2.钒是重要的战略资源,具有优异的强度、延展性、耐热性,能显著改善钢的性能,是生产高强度钢不可缺少的重要元素,广泛用于钢铁、化工、航空航天、军工、电子技术、钒电池储能、环保等重要领域,被称为现代工业的味精。
3.传统钒钛磁铁矿高炉炼铁-转炉吹钒-钠(钙)化焙烧提钒工艺存在的问题为转炉吹钒工序和钠(钙)化焙烧工序一般不在同一个厂区内,转炉吹钒得到的1300-1400℃的高温钒渣冷却到常温后,再运送至钠(钙)化焙烧厂区,经过破碎
→
球磨
→
混配料
→
钠(钙)化焙烧(800-1000℃)提钒,转炉高温钒渣的物理热没有得到有效利用,钠化焙烧工序还要再进行升温,能耗较大。
4.cn102086487b公开了一种节能减排的钒渣处理方法,包括以下步骤:将与铁水分离后的1200℃以上的高温液态钒渣置于渣罐中;然后,根据钒渣品位向渣罐中加入钠化合物,然后用水冷超音速或亚音速氧枪向渣罐中供氧,造成强氧化性气氛,同时能起到搅拌作用,促使钒渣中快速生成水溶性钒酸钠,把得到的含有水溶性钒酸钠的渣处理得到v2o5。该方法缩短了工艺流程,且节约了能耗,但该方法存在钒酸钠溶液沉钒后废水处理难或处理成本高的问题。
技术实现要素:5.针对现有技术的不足之处,本发明提供了一种节能绿色的短流程钒渣浸出新工艺,本发明利用转炉直接对钒渣进行充分氧化,省去传统提钒工艺常温钒渣钠化焙烧流程,工艺流程简单,生产能耗大幅度降低;通过水淬法制备多孔钒渣,再利用多级反应罐进行提钒,各级泵输送的溶液均为过滤后的溶液,渣量非常少,对泵的磨损小;钠化沉钒后的naoh溶液返回冲渣系统,结晶分离母液返回铵化沉钒工序,无废水产生。
6.为达此目的,本发明采用的技术方案如图1所示,包括钒钛磁铁矿在高炉炼铁完成后,在转炉提钒终点将半钢倒入半钢罐后,在转炉内通过优化供氧方式,最大限度的将钒渣中的低价钒转化为五价钒;然后将熔融钒渣倒入钠化罐中,加入碳酸钠或氢氧化钠进行钠化,将残留的铁珠逐渐在罐底沉降,然后采用水淬法将高温钒渣粒化得到多孔钒渣,再经过循环浸出,底部浆液进行精滤分离得到钒酸钠滤液和细尾渣;钒酸钠溶液可通过酸性铵盐沉钒得到多钒酸铵或通过钙化沉钒-铵化转型得到偏钒酸铵,钙化沉钒后的naoh溶液返回冲渣系统,通过结晶分离、干燥煅烧可以得到氧化钒,结晶分离和干燥煅烧过程中的氨可以回收后转变为碳酸氢铵循环利用;料斗中的虑上物经梯级洗涤、过滤分离过程得到提钒尾渣。本发明利用转炉直接对钒渣进行充分氧化,省去传统提钒工艺常温钒渣钠化焙烧流程,工艺流程简单,生产能耗大幅度降低;通过水淬法制备多孔钒渣,再利用循环浸出进行提钒、多级洗涤罐进行尾渣洗涤,各级泵输送的流体均为过滤后的溶液,渣量非常少,对泵的
磨损小;钙化沉钒后的naoh溶液返回冲渣系统,结晶分离母液返回铵化沉钒工序,无废水产生。
7.具体可以包括以下步骤:
8.步骤(1),在转炉提钒终点,提起氧枪停止吹氧,将半钢倒入半钢罐,再通过优化转炉内供氧方式,最大限度的将钒渣中的低价钒转化为五价钒;
9.步骤(2),将氧化后的熔融钒渣倒入钠化罐内,然后向其中加入na2co3或naoh进行钒渣钠化,同时在钠化罐设置氧枪吹氧,起到搅拌和氧化作用,在搅拌作用下,钒渣中残留的铁珠逐渐在罐底沉降;
10.步骤(3),待钒渣和钠盐混合均匀后,打开右侧排料口,排出钒渣,然后通过冲渣液的冲击、粒化得到多孔钒渣,并排入到浸出罐中,待钠化罐中的钒渣全部排出后停止通氧;
11.步骤(4),浸出罐中设有可以上下移动的料斗,料斗外部为篮状结构,内衬滤布,冲渣液经过滤布流至反应罐底部,然后被冲渣泵抽出作为冲渣液循环使用;待浸出罐底部浆液的钒浓度达到一定值后,即可对底部浆液进行精滤分离得到钒酸钠滤液和细尾渣;
12.步骤(5),将料斗逐级放入到洗涤罐中进行梯级洗涤,洗涤完成后,将料斗提升至液面以上,待水沥干后,送入下一级洗涤罐。例如,当梯级洗涤的级数为3级时如图2所示。
13.本发明步骤(1)中所述供氧方式为在转炉设置顶枪和侧枪,侧枪在钒渣倒入钠化罐之前始终保持吹氧状态,氧气通入量为200-500m3/min;将顶枪枪位降到最低枪位,距转炉底部0.6-1m处,氧气通入量为300-1500m3/min,通氧时间为1-4min,顶枪吹氧完成后提枪,转炉前后倾动1-5次,倾动角度范围为45-100
°
,倾动过程中保持侧枪吹氧,倾动时间为2-4min,吹氧目的是提高钒渣中的低价钒转化为五价钒的转化率。
14.本发明步骤(2)中na2co3或naoh的加入量为6-20kg/t钒渣,优选为naoh。
15.本发明步骤(2)中所述钠化罐结构为底部有一定斜度,钠化罐底部与水平面夹角为10-30
°
,便于铁珠在一侧沉积。
16.本发明步骤(2)中所述钠化罐氧气通入量为100-500m3/min。
17.本发明步骤(3)中通过调整冲渣液压力和流量,使得多孔钒渣的粒度为2-20mm。
18.本发明步骤(3)中冲渣过程中产生的水蒸气收集后用于尾渣洗涤。
19.本发明步骤(4)中所述滤布过滤精度为5-100um。
20.本发明步骤(4)中所述循环浸出反应时间为60-180min,液渣质量比0.7-1.2,浸出液中naoh浓度为20-45%,浸出温度80-120℃。
21.本发明步骤(4)中浸出罐底部浆液的钒浓度达到25-40g/l后,即可对浆液进行精滤分离。
22.本发明步骤(5)中所述梯级洗涤的级数为n级,n=2-5。
23.本发明步骤(5)中所述梯级洗涤是指n级的洗涤后液作为(n-1)级的洗涤液。具体操作为将n级洗涤罐底部的洗涤后液泵入(n-1)级洗涤罐顶部,对(n-1)级料斗中的钒渣进行喷淋;最后一级的洗涤液为清水,最后一级清水加入量为冲渣液蒸发量与尾渣带走水量之和;各级洗涤温度为70-95℃。
24.本发明步骤(5)中经最后一级洗涤后,将料斗提至洗涤罐液面以上,静置一段时间,待水沥干后,直接将尾渣排入尾渣库。
25.本发明步骤(4)、(5)中为保证浸出罐内浸出效果和洗涤罐内洗涤效果,浸出罐和
洗涤罐上的料斗可上下移动,起到搅拌作用,移动频率为1-60次/h,各级洗涤时间为60-180min。
26.与现有技术相比,本发明至少具有以下有益效果:
27.(1)利用转炉直接对钒渣进行充分氧化,省去传统提钒工艺常温钒渣钠化焙烧流程,工艺流程简单,生产能耗大幅度降低。
28.(2)通过水淬法制备多孔钒渣,再利用循环浸出进行提钒、多级洗涤进行尾渣洗涤,各级泵输送的流体均为过滤后的溶液,渣量非常少,对泵的磨损小。
29.(3)钙化沉钒后的naoh溶液返回冲渣系统,结晶分离母液返回铵化沉钒工序,无废水产生。
附图说明
30.图1示出了本发明短流程钒渣浸出方法流程示意图。
31.图2示出了梯级洗涤示意图。
具体实施方式
32.为便于理解本发明,本发明列举实施例如下。本领域技术人员应该明了,所述实施例仅仅是帮助理解本发明,不应视为对本发明的具体限制。
33.实施例1
34.(1)在转炉提钒终点,提起氧枪停止吹氧,将半钢倒入半钢罐后,开启侧枪向转炉内通氧,氧气通入量为500m3/min;然后将顶枪枪位降到转炉最低枪位,距转炉底部0.6m处,氧气通入量为1500m3/min,通氧时间为1.5min;完成后提起顶枪,转炉前后倾动3次,倾动角度范围为100
°
,倾动过程中保持侧枪吹氧,倾动时间为3min。
35.(2)氧化工序完成后,将15吨熔融钒渣倒入钠化罐内,并加入180kg naoh,向钠化罐内通氧,氧气通入量为500m3/min,使钒渣和钠盐充分混合,并进一步氧化钒渣;钒渣和钠盐混合过程中,铁珠在钠化罐底部沉降。
36.(3)待钒渣和钠盐混合均匀后,打开右侧排料口,排出钒渣,然后通过冲渣液的冲击、粒化得到多孔钒渣,并排入到浸出罐中,通过调整冲渣液压力和流量,得到多孔钒渣的粒度为2-10mm。
37.(4)浸出罐中设有可以上下移动的料斗,料斗外部为篮状结构,内衬滤布,滤布过滤精度为100um,冲渣液经过滤布流至浸出罐底部,然后通过冲渣泵抽走仍作为冲渣液循环使用,循环浸出时间为180min,浸出液中naoh浓度为35%,液渣质量比为1.2,浸出温度120℃。
38.(5)设置四级洗涤罐,将料斗逐级放入到洗涤罐中进行梯级洗涤,各级洗涤时间为180min,料斗上下移动频率为30次/h,洗涤完成后,将料斗提升至液面以上,待水沥干后,送入下一级洗涤罐,最后一级经洗涤、沥干后直接将尾渣排入尾渣库,最后一级洗涤水量为6吨。
39.经检测:本实施例钒浸出率88.93%。
40.实施例2
41.(1)在转炉提钒终点,提起氧枪停止吹氧,将半钢倒入半钢罐后,开启侧枪向转炉
内通氧,氧气通入量为400m3/min;然后将顶枪枪位降到转炉最低枪位,距转炉底部0.6m处,氧气通入量为1200m3/min,通氧时间为1.5min;完成后提起顶枪,转炉前后倾动4次,倾动角度范围为90
°
,倾动过程中保持侧枪吹氧,倾动时间为2min。
42.(2)氧化工序完成后,将15吨熔融钒渣倒入钠化罐内,并加入100kg na2co3,向钠化罐中通氧,氧气通入量为300m3/min,使钒渣和钠盐充分混合,并进一步氧化钒渣;钒渣和钠盐混合过程中,铁珠在钠化罐底部沉降。
43.(3)待钒渣和钠盐混合均匀后,打开右侧排料口,排出钒渣,然后通过冲渣液的冲击、粒化得到多孔钒渣,并排入到浸出罐中,通过调整冲渣液压力和流量,得到多孔钒渣的粒度为5-15mm。
44.(4)浸出罐中设有可以上下移动的料斗,料斗外部为篮状结构,内衬滤布,滤布过滤精度为10um,冲渣液经过滤布流至浸出罐底部,然后通过一级泵抽走仍作为冲渣液循环使用,循环浸出时间为120min,浸出液中naoh浓度为30%,渣液质量比为1:1,浸出温度90℃。
45.(5)设置三级洗涤罐,将料斗逐级放入到洗涤罐中进行梯级洗涤,各级洗涤时间为120min,料斗上下移动频率为20次/h,洗涤完成后,将料斗提升至液面以上,待水沥干后,送入下一级洗涤罐,最后一级经洗涤、沥干后直接将尾渣排入尾渣库。洗涤水量6.4吨。
46.经检测:本实施例钒浸出率87.32%。
47.实施例3
48.(1)在转炉提钒终点,提起氧枪停止吹氧,将半钢倒入半钢罐后,开启侧枪向转炉内通氧,氧气通入量为300m3/min;然后将顶枪枪位降到转炉最低枪位,距转炉底部0.8m处,氧气通入量为1000m3/min,通氧时间为3min;完成后提起顶枪,转炉前后倾动2次,倾动角度范围为70
°
,倾动过程中保持侧枪吹氧,倾动时间为2min。
49.(2)氧化工序完成后,将15吨熔融钒渣倒入钠化罐内,并加入130kg na2co3,向钠化罐内通氧,氧气通入量为200m3/min,使钒渣和钠盐充分混合,并进一步氧化钒渣;钒渣和钠盐混合过程中,铁珠在钠化罐底部沉降。
50.(3)待钒渣和钠盐混合均匀后,打开右侧排料口,排出钒渣,然后通过冲渣液的冲击、粒化得到多孔钒渣,并排入到浸出罐中,通过调整冲渣液压力和流量,得到多孔钒渣的粒度为2-15mm。
51.(4)浸出罐中设有可以上下移动的料斗,料斗外部为篮状结构,内衬滤布,滤布过滤精度为20um,冲渣液经过滤布流至浸出罐底部,然后通过一级泵抽走仍作为冲渣液循环使用,循环浸出时间为90min,浸出液中naoh浓度25%,液渣质量比为0.7,浸出温度80℃。
52.(5)设置三级洗涤罐,将料斗逐级放入到洗涤罐中进行梯级洗涤,各级洗涤时间为90min,料斗上下移动频率为30次/h,洗涤完成后,将料斗提升至液面以上,待水沥干后,送入下一级洗涤罐,最后一级经洗涤、沥干后将尾渣排入尾渣库。最后一级洗涤水量7.1吨。
53.经检测:本实施例钒浸出率86.75%。
54.实施例4
55.(1)在转炉提钒终点,提起氧枪停止吹氧,将半钢倒入半钢罐后,开启侧枪向转炉内通氧,氧气通入量为200m3/min;然后将顶枪枪位降到转炉最低枪位,距转炉底部1m处,氧气通入量为800m3/min,通氧时间为3min;完成后提起顶枪,转炉前后倾动1次,倾动角度范
围为45
°
,倾动过程中保持侧枪吹氧,倾动时间为1min。
56.(2)氧化工序完成后,将15吨熔融钒渣倒入钠化罐内,并加入90kg naoh,向钠化罐内通氧,氧气通入量为100m3/min,使钒渣和钠盐充分混合,并进一步氧化钒渣;钒渣和钠盐混合过程中,铁珠在钠化罐底部沉降。
57.(3)待钒渣和钠盐混合均匀后,打开右侧排料口,排出钒渣,然后通过冲渣液的冲击、粒化得到多孔钒渣,并排入到浸出罐中,通过调整冲渣液压力和流量,得到多孔钒渣的粒度为5-20mm。
58.(4)浸出罐中设有可以上下移动的料斗,料斗外部为篮状结构,内衬滤布,滤布过滤精度为50um,冲渣液经过滤布流至浸出罐底部,然后通过一级泵抽走仍作为冲渣液循环使用,循环浸出时间为60min,浸出液中naoh浓度为20%,液渣质量比为1.1,浸出温度90℃。
59.(5)设置三级洗涤罐,将料斗逐级放入到洗涤罐中进行梯级洗涤,各级洗涤时间为60min,料斗上下移动频率为30次/h,洗涤完成后,将料斗提升至液面以上,待水沥干后,送入下一级洗涤罐,最后一级经洗涤、沥干后直接将尾渣排入尾渣库。最后一级洗涤水量6.2吨。
60.经检测:本实施例钒浸出率85.25%。
61.实施例5
62.(1)在转炉提钒终点,提起氧枪停止吹氧,将半钢倒入半钢罐后,开启侧枪向转炉内通氧,氧气通入量为400m3/min;然后将顶枪枪位降到转炉最低枪位,距转炉底部0.6m处,氧气通入量为1200m3/min,通氧时间为3min;完成后提起顶枪,转炉前后倾动3次,倾动角度范围为100
°
,倾动过程中保持侧枪吹氧,倾动时间为4min。
63.(2)氧化工序完成后,将15吨熔融钒渣倒入钠化罐内,并加入120kg naoh,向钠化罐内通入氧气,氧气通入量为200m3/min,使钒渣和钠盐充分混合,并进一步氧化钒渣;钒渣和钠盐混合过程中,铁珠在钠化罐底部沉降。
64.(3)待钒渣和钠盐混合均匀后,打开右侧排料口,排出钒渣,然后通过冲渣液的冲击、粒化得到多孔钒渣,并排入到浸出罐中,通过调整冲渣液压力和流量,得到多孔钒渣的粒度为2-20mm。
65.(4)浸出罐中设有可以上下移动的料斗,料斗外部为篮状结构,内衬滤布,滤布过滤精度为10um,冲渣液经过滤布流至浸出罐底部,然后通过一级泵抽出仍作为冲渣液循环使用,循环浸出时间为60min,液渣质量比为0.9,浸出液中naoh浓度为30%,浸出温度120℃。
66.(5)设置二级洗涤罐,将料斗逐级放入到洗涤罐中进行梯级洗涤,各级洗涤时间为60min,料斗上下移动频率为20次/h,洗涤完成后,将料斗提升至液面以上,待水沥干后,送入下一级洗涤罐,最后一级经洗涤、沥干后直接将尾渣排入尾渣库。最后一级洗涤水量为6.6吨。
67.经检测:本实施例钒浸出率85.74%。
68.在循环浸出过程中,液渣质量比与使用量平衡关系如表1所示。
69.表1系统用水量平衡计算
[0070][0071][0072]
申请人声明,本发明通过上述实施例来说明本发明的详细方法,但本发明并不局限于上述详细方法,即不意味着本发明必须依赖上述详细方法才能实施。所属技术领域的技术人员应该明了,对本发明的任何改进,对本发明产品各原料的等效替换及辅助成分的添加、具体方式的选择等,均落在本发明的保护范围和公开范围之内。