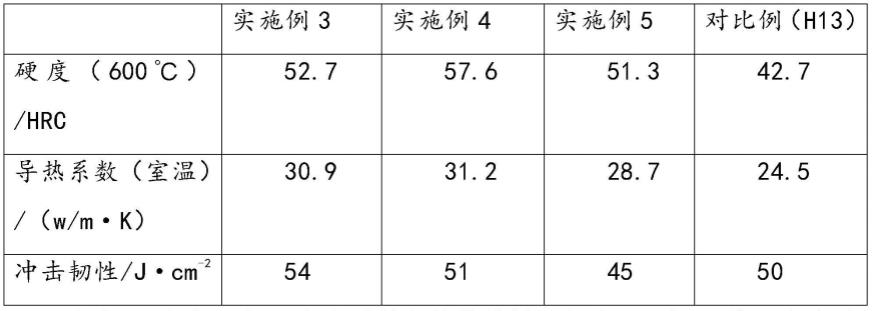
0.8。
16.进一步地,成核助剂在钢液中的用量质量百分比为1.27-1.52%。
17.进一步地,锻造的锻造比为7-10。
18.本发明的有益效果:
19.1.本发明在模具钢的基材中添加一种成核助剂,其以纳米级的碳粉、氮化硼和钽粉制成,通过硅烷偶联剂处理提高分散性,避免团聚,使得成核助剂可以均匀地分散在钢液中,成核助剂一方面可提供更多晶核,在出钢前加入可促进晶粒细化,另一方面,钽和碳在高温下形成碳化钽,其对铁基体的结晶有强烈促进作用,此外碳化钽与氮化硼均有较强的导热能力,从微观角度上看,提高碳化钽与氮化硼周围的冷却速度,进一步细化晶粒,从而使得本发明制备的模具钢具有良好的强韧性。
20.2.本发明通过降低模具钢配合料中的碳含量,配合成核助剂形成的高导热强化相共同提高导热性,通过采用较高的钼含量提高淬透性,以弥补低含碳量和高钨含量带来的淬透性差问题,同时配合料中的硅含量较低,降低配合料中碳在熔炼过程中石墨化,在出钢前添加的成核助剂补充模具钢中的碳含量,碳主要以碳化钽和氮化硼形成的强化相形成存在,并且熔炼时间较短,石墨化程度低,对模具钢的强韧性无太大影响,在保证强度的前提下提高模具钢的导热性。
具体实施方式
21.下面将结合本发明实施例,对本发明实施例中的技术方案进行清楚、完整地描述,显然,所描述的实施例仅仅是本发明一部分实施例,而不是全部的实施例。基于本发明中的实施例,本领域普通技术人员在没有作出创造性劳动前提下所获得的所有其它实施例,都属于本发明保护的范围。
22.实施例1
23.本实施例制备成核助剂,具体实施过程如下:
24.步骤a1:配置体积分数为40%的乙醇水溶液,并将乙醇水溶液倒入超声分散机的水槽中,得到分散体系;
25.步骤a2:取纳米碳粉、纳米氮化硼和纳米钽粉(钠还原钽粉)按照重量比为1:2.2:0.8混合后倒入分散体系中,在28khz下超声分散20min,之后静置10h;
26.步骤a3:向静置后的水槽中加入硅烷偶联剂kh550,再于28khz下超声分散20min,超声分散后对分散液先离心再蒸干,去除分散液,得到成核助剂。
27.实施例2
28.步骤a1:配置体积分数为40%的乙醇水溶液,并将乙醇水溶液倒入超声分散机的水槽中,得到分散体系;
29.步骤a2:取纳米碳粉、纳米氮化硼和纳米钽粉(钠还原钽粉)按照重量比为1:2.5:0.7混合后倒入分散体系中,在28khz下超声分散20min,之后静置10h;
30.步骤a3:向静置后的水槽中加入硅烷偶联剂kh550,再于28khz下超声分散20min,超声分散后对分散液先离心再蒸干,去除分散液,得到成核助剂。
31.实施例3
32.本实施例制备高导热高热强热作模具钢,具体实施过程如下:
33.步骤s1:按照以下成分进行配料:
34.c:0.32%;
35.w:1.2%;
36.mo:3.6%;
37.v:0.08%;
38.mn:0.1%;
39.cr:0.18%;
40.si:0.04%;
41.余量为fe以及不可避免的杂质;
42.将以上成分的配合料投加到真空熔炼炉中升温至1450℃熔炼成钢液,出钢前采用吹粉机向熔炼炉中吹入配合料质量1.27%的实施例1制备的成核助剂,控制出钢温度为1550℃,浇铸温度为1490℃,将钢液浇铸到模具中,得到电极棒;
43.步骤s2:将电极棒安装在电渣重熔炉的自耗电极上,电渣重熔炉中的渣系按照重量百分比计包括:氟化钙52%、氧化镁8%、氧化铝30%和氧化钙10%,重熔参数设置为:熔炼填充比为0.52,熔速为450kg/h,将电极棒重熔并制成钢坯;
44.步骤s3:将钢坯加热至1220
±
10℃后保温30min进行均质处理,之后将均质处理后的钢坯使用液压机自由锻造,控制锻造比为7,终锻温度为920℃,再水淬冷却至室温,得到淬火件;
45.步骤s4:将淬火件升温至480℃保温4h,之后采用淬火油进行油冷至室温,得到模具钢。
46.实施例4
47.本实施例制备高导热高热强热作模具钢,具体实施过程如下:
48.步骤s1:按照以下成分进行配料:
49.c:0.36%;
50.w:1.35%;
51.mo:3.92%;
52.v:1.08%;
53.mn:0.06%;
54.cr:0.18%;
55.si:0.02%;
56.余量为fe以及不可避免的杂质;
57.将以上成分的配合料投加到真空熔炼炉中升温至1462℃熔炼成钢液,出钢前采用吹粉机向熔炼炉中吹入配合料质量1.35%的实施例2制备的成核助剂,控制出钢温度为1550℃,浇铸温度为1520℃,将钢液浇铸到模具中,得到电极棒;
58.步骤s2:将电极棒安装在电渣重熔炉的自耗电极上,电渣重熔炉中的渣系按照重量百分比计包括:氟化钙52%、氧化镁8%、氧化铝30%和氧化钙10%,重熔参数设置为:熔炼填充比为0.52,熔速为450kg/h,将电极棒重熔并制成钢坯;
59.步骤s3:将钢坯加热至1220
±
10℃后保温35min进行均质处理,之后将均质处理后的钢坯使用液压机自由锻造,控制锻造比为8,终锻温度为960℃,再水淬冷却至室温,得到
淬火件;
60.步骤s4:将淬火件升温至500℃保温4h,之后采用淬火油进行油冷至室温,得到模具钢。
61.实施例5
62.本实施例制备高导热高热强热作模具钢,具体实施过程如下:
63.步骤s1:按照以下成分进行配料:
64.c:0.38%;
65.w:1.6%;
66.mo:4.2%;
67.v:1.4%;
68.mn:0.06%;
69.cr:0.15%;
70.si:0.02%;
71.余量为fe以及不可避免的杂质;
72.将以上成分的配合料投加到真空熔炼炉中升温至1462℃熔炼成钢液,出钢前采用吹粉机向熔炼炉中吹入配合料质量1.52%的实施例2制备的成核助剂,控制出钢温度为1560℃,浇铸温度为1520℃,将钢液浇铸到模具中,得到电极棒;
73.步骤s2:将电极棒安装在电渣重熔炉的自耗电极上,电渣重熔炉中的渣系按照重量百分比计包括:氟化钙52%、氧化镁8%、氧化铝30%和氧化钙10%,重熔参数设置为:熔炼填充比为0.52,熔速为450kg/h,将电极棒重熔并制成钢坯;
74.步骤s3:将钢坯加热至1220
±
10℃后保温35min进行均质处理,之后将均质处理后的钢坯使用液压机自由锻造,控制锻造比为10,终锻温度为1000℃,再水淬冷却至室温,得到淬火件;
75.步骤s4:将淬火件升温至530℃保温4h,之后采用淬火油进行油冷至室温,得到模具钢。
76.对实施例3-实施例5制备的模具钢制成试样进行测试,同时取市售h13热作模具钢作为对比例进行测试,具体测试方法如下:
77.高温硬度:将试样在600℃下保温12h,趁热采用洛氏硬度计检测表面硬度;
78.导热系数:室温下采用激光导热系数测试仪检测导热系数;
79.韧性:参照gb/t229-1994标准,在室温下进行v型冲击韧性测试;
80.具体测试数据如表1所示:
81.表1
[0082][0083]
由表1数据可知,本发明制备的热作模具钢在600℃下的硬度达到51.3-57.6hrc,具有良好的高温强度,室温下导热系数达到28.7-31.2w/m
·
k,具有优异的导热性能,夏氏v型冲击韧性达到45-54j/cm2,综上,本发明制备的模具钢具有优异的强韧性及导热性,可应用于热作模具钢。
[0084]
在说明书的描述中,参考术语“一个实施例”、“示例”、“具体示例”等的描述意指结合该实施例或示例描述的具体特征、结构、材料或者特点包含于本发明的至少一个实施例或示例中。在本说明书中,对上述术语的示意性表述不一定指的是相同的实施例或示例。而且,描述的具体特征、结构、材料或者特点可以在任何的一个或多个实施例或示例中以合适的方式结合。
[0085]
以上内容仅仅是对本发明所作的举例和说明,所属本技术领域的技术人员对所描述的具体实施例做各种各样的修改或补充或采用类似的方式替代,只要不偏离发明或者超越本权利要求书所定义的范围,均应属于本发明的保护范围。