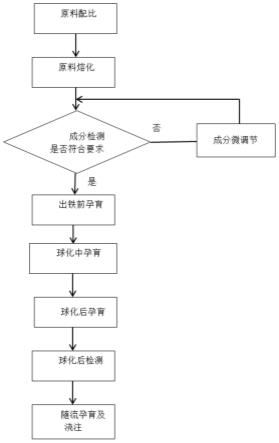
1.本发明涉及到一种铁铸件的铸造方法,具体涉及到一种大吨位的球墨铸铁铸件的制备方法。
背景技术:2.qt600-3基体组织是以珠光体为主的球墨铸铁,具有高强度高刚度、中等韧性和塑性,耐磨性及铸造工艺性能良好等特点,综合性能较高,广泛的应用于各种动机械曲轴、连杆、液压缸体、离合器片等零部件及机床铸件。目前铸造生产过程中,大型横梁壁厚从20-200mm间变化,采用灰铁制造工艺简便可行,但其力学性能较差、弹性模量较低且铸态变形量较大。采用球墨铸铁制造横梁,其力学性能会成倍的增加,弹性模量会翻倍,这带来的将是铸态下铸件自身变形量的减少和降低,大大提升了横梁自身的强度及刚度。
3.目前采用球铁进行大吨位横梁的生产制造,需要克服并解决壁厚差异带来的石墨数少、石墨数量不均衡、薄壁处渗碳体量超标,厚壁处珠光体含量不足,还要防止导轨厚大断面处的石墨畸变等难题。
技术实现要素:4.本发明的目的是针对现有技术存在的问题,提供一种球化均匀、球状石墨畸变少、薄壁处无渗碳体、厚壁处珠光体化完全且铸态下铸件变形量少、力学性能优于qt600-3的大吨位球墨铸铁铸件的制备方法。
5.为实现上述目的,本发明采用的技术方案是:制备方法包括以下步骤:
6.(1)原料配比:生铁45%-60%、废钢55%-40%、碳化硅0.6%-1.0%以及适量的增碳剂和适量的硅锰铁合金;
7.(2)原料熔化、成分检测:原料加入熔炼炉内,熔化成铁液后升温至1380℃~1420℃扒渣并取样,根据试样成分调整c、si含量,调整后的原铁液成分:c:3.9-3.95%;si:0.9-1.05%;mn:0.3-0.4%;p≤0.04%;s≤0.025%;
8.(3)铁液过热处理:将原铁液过热,过热温度1500℃~1540℃;
9.(4)出铁前孕育:(a)将1500℃~1540℃铁液倒入降温容器,完成后迅速转运至球化现场,转移过程中铁水温度降至1420-1450℃时将硅铁孕育块加入降温容器;(b)将降温容器转运至球化包处,测量铁水温度,在1400℃~1420℃将铁液倒入球化包进行球化;
10.(5)球化中孕育:在球化包的堤坝的一侧放入球化剂,所述球化剂上放入cu、sn、sb合金,再放入孕育块,最后用硅钢片填实球化剂、孕育块和合金之间的间隙;
11.(6)球化后孕育:在铁液倒入球化包过程中加入一定量的孕育块;
12.(7)球化后检测:对球化后的铁液成分进行检测;所述球墨铸铁的成分为:c:3.7-3.85%;si:1.9-2.2%;mn:0.3-0.4%;p≤0.04%;s≤0.025%;cu:0.3-0.4%;sn:0.02-0.04%;sb:≤0.015%;mg:0.035-0.06%,余量为fe;
13.(8)随流孕育及浇注:球化检测后将铁水包运至铸件浇杯口处并加入孕育块,
1330-1350℃完成浇注。
14.通过上述技术方案,在制备过程中,采用倒包球化、四次复合孕育块工艺,第一次孕育,采用硅孕育块处理工艺,能降低铁液中氧的活度,形成的脱氧产物sio2将会均匀分布在铁水中成为铁液氧化物的主要成分;中期球化包球化过程中生成的硫化物(mgs)、氧化物(mgo)会与第一次、第二次孕育块处理过程中形成大量的sio2结合形成具有双重结构核心的mgs
·
sio2,mgo
·
sio2,2mgo
·
sio2等斜方晶系复式硅酸盐,同时孕育剂中少量的si、ba、ca、al等元素对双重结构核心mgs
·
sio2,mgo
·
sio2,2mgo
·
sio2的表面成分进行催化、改变并激活,让其成为石墨有效析出的异质核心,依靠上述异质核心石墨大量生成并长大;随着球化和第三次、第四次孕育块不断的缓释深入的孕育会促使更多的异质核心及石墨生成,从而促使石墨球更多、更圆整、更均匀,保证球化等级不低于2级(球化率不低于90%);于此同时通过联合相应的cu、sn、sb合金作用,更可在共晶凝固时促使石墨以更圆整形式析出长大以及共析转变过程中稳定铸态下的珠光体含量。最终通过上述工艺,稳定获得球数多、球化均匀、球状石墨畸变少且铸态下铸件变形量少的大吨位球墨铸铁件。
15.作为对技术方案的进一步改进,为了延长孕育块的溶解时间,使孕育效果充分在铁液中发挥,有效降低铁液中氧、硫的活度。步骤(4)中,硅铁孕育块长度为30-200mm、厚度为20-50mm,加入量为0.1%-0.3%。
16.作为对技术方案的进一步改进,为了延长孕育块的溶解时间,使孕育剂在铁液中充分反应,能够有效去除铁液中的活性氧并彻底净化铁液,促使石墨的形成。步骤(5)中,使用长30-50mm、宽30-50mm、高20-30mm的含si、ba、ca、al的孕育块,加入量为0.4%-0.6%,最后球化剂、孕育块、合金之间的间隙用硅钢片填实。
17.作为对技术方案的进一步改进,为了延长第三次孕育块的溶解时间,使孕育剂在铁液中充分反应,促使石墨球更多、更圆整、更均匀。步骤(6)中,使用长30-50mm、宽30-50mm、高20-30mm的含si、ba、ca、al的孕育块,加入量为0.1%-0.3%,在铁液的五分之二倒入球化包之后加入。
18.作为对技术方案的进一步改进,为了促进充分球化,保证铸态下大吨位球铁石墨球的数量。步骤(8)中,使用长度为30-200mm、宽度为30-200mm、高为10-20mm孕育块,加入量0.1%-0.3%。
19.作为对技术方案的进一步改进,为了保证浇注铁液性能的稳定,进而保证铸件整体的力学性能,对制备过程的时间进行严格限定,优先地,从球化开始到浇注前的时间小于15分钟。
20.优先地,在步骤(6)中,当铁液的五分之二倒入球化包时加入孕育块。
21.作为对技术方案的进一步改进,为了延长孕育块的溶解时间,保证孕育剂在铁水中充分反应,保证孕育效果。在步骤(4、5、6、8)中,加入压实的孕育块。
22.优先地,所述孕育块采用振实封装后获得。
23.作为对技术方案的进一步改进,为了提高检测的准确性。在步骤(3)中,取铁液试样和炉前光谱试样,进行双重检测。
24.与现有技术相比,本发明的有益效果是:1、通过用倒包球化调节温度让温度可控、四次复合孕育块工艺,铸态下大吨位球铁石墨球的数量提高至150-200个/mm2,最终可以确保铸件球数多、球化均匀、不畸形且保证力学性能;2、采用压实的孕育块,由于压实的孕育
块的堆积密度比常规松散状态下的堆积密度大,传热速度比常规状态下的孕育剂的速度慢,因此能够实现孕育剂的缓释效果,延长孕育块的溶解时间,这可以让铁液充分的存在温度、浓度起伏区域,能够促进铁液的球化效果,从而保证孕育效果。
附图说明
25.图1为本发明实施例中制备方法的流程图;
26.图2为本发明实施例中横梁1#的40mm试块放大300倍的金相组织;其中,图(a)为腐蚀前的金相组织,图(b)为腐蚀后的金相组织;
27.图3为本发明实施例中横梁1#的70mm试块放大300倍的金相组织;其中,图(a)为腐蚀前的金相组织,图(b)为腐蚀后的金相组织;
28.图4为本发明实施例中横梁2#的40mm试块放大300倍的金相组织;其中,图(a)为腐蚀前的金相组织,图(b)为腐蚀后的金相组织;
29.图5为本发明实施例中横梁2#的70mm试块放大300倍的金相组织其中,图(a)为腐蚀前的金相组织,图(b)为腐蚀后的金相组织;
30.图6为本发明实施例中横梁的结构示意图。
具体实施方式
31.下面将结合本发明中的附图,对本发明的技术方案进行清楚、完整地描述,显然,所描述的实施例仅仅是本发明一部分实施例,而不是全部的实施例。基于本发明中的实施例,本领域普通技术人员在没有做出创造性劳动条件下所获得的所有其它实施例,都属于本发明保护的范围。
32.实施例一:
33.本实施例中的大吨位球墨铸铁铸件的制备方法包括以下步骤:第一步,原料配比:原料选择q10生铁45%~60%、优质废钢55%~40%、碳化硅0.6%~1.0%以及适量增碳剂和适量的硅锰铁合金。其中优质废钢可选用优质碳素废钢。
34.第二步,原料熔化:原料熔化前保炉膛内干净无渣,原料加入熔炼炉内,铁液熔化完成后升温至1380℃~1420℃扒渣取样,扒渣取样后,加入碳化硅,随后分批次加入增碳剂;调整铁液中成分至符合要求,再升温至1500℃~1540℃,铁液过热后出铁。根据表1中所需原铁水成分进行配料,通过改变生铁与废钢加入比例调整硅、锰等成分,通过增碳剂调整含碳量至要求成分,硅铁调整至合适范围。加料熔化时必须确保炉膛内干净无渣,增碳剂前期随炉料加入炉内,铁液熔化完成后升温至1380℃~1420℃时扒渣取样,扒渣取样用于铁水检测使用。扒渣取样后,碳化硅应在熔化的前中期加入,随着增碳剂一起分批分次多次加入。在铁水温度为1380℃~1420℃时,进行铁水成分检测;取热分析试样和炉前试样进行光谱检测,进行双重检测,微调整铁液的碳含量、硅含量、锰含量;根据试样成分调整c、si含量,调整后的原铁液成分:c:3.9-3.95%;si:0.9-1.05%;mn:0.3-0.4%;p≤0.04%;s≤0.025%。将调整后的铁液升温至1500℃~1540℃过热后出铁。在进行球化前,铁水的最终成分为表1中第3行的数值。
[0035][0036]
表1
[0037]
步骤三:将原铁液过热,过热温度为1500℃~1540℃;铁液过热后出铁。
[0038]
步骤四,出铁前孕育:第一步,将1500℃~1540℃铁液倒入特定快速降温容器,完成后迅速转运至球化现场,转移过程中铁水温度降至1420-1450℃时将多个硅铁孕育块加入降温容器;第二步,将降温容器转运至球化包处,测量铁水温度,在1400℃~1420℃将铁液倒入球化包进行球化。
[0039]
优选地,硅铁孕育块的尺寸为长30-200mm、宽30-200mm、高为20-50mm,加入量为0.1%-0.3%。采用大块状的硅铁孕育剂比传统采用小颗粒的孕育剂能够有效延缓孕育剂的溶解,延长溶解的时间,使孕育剂在铁水中能够充分反应,能够有效增加铁液形核表层物质sio2,降低铁液中氧的活度,形成的脱氧产物sio2会均匀分布在铁水中成为铁液氧化物的主要成分,与球化过程中的产物进行结合,促使石墨核心的形成。
[0040]
步骤五,球化中孕育:采用包底冲入法以及现场倒包球化,球化包使用球铁生产专用球化包,烘烤后使用在球化包的堤坝的一侧放入球化剂,所述球化剂上放入cu(铜)、sn(锡)、sb(锑)合金,再放入多个孕育块,最后用厚度为1mm的0.5%硅钢片填实球化剂、孕育块和合金之间的间隙。如表2所示,球化剂、孕育块的重要成分。
[0041][0042]
表2
[0043]
优选地,孕育块使用长30-50mm、宽30-50mm、高20-30mm的含si、ba、ca、al的孕育
块,加入量为0.4%-0.6%。大吨位球铁铸件采用块状的孕育剂比传统采用小颗粒的孕育剂能够有效延缓孕育剂的溶解,延长溶解的时间,使孕育剂在铁水中能够充分反应。此外,在投入孕育块后,铁液局部温度下降,孕育块溶度较高,进而促使铁液形成温度、浓度起伏区域,根据液态合金中元素浓度起伏理论,能够促进铁液的球化。
[0044]
其中,钡(ba)的硫化物生成自由能比mns的低,更应成为石墨形核的有效核心,含ba孕育剂能减小白口倾向,提高铸件的延伸率,况且钡具有很强的脱氧脱硫的能力,与氧、硫形成的氧化物、硫化物是有效成为石墨形核的核心,因而钡能有效提高石墨数量。铜(cu)能促进共晶阶段石墨化,降低奥氏体转变临界温度,细化并增加珠光体,结合铸件结构合理的加入量0.3-0.6%。锡强烈促进珠光体形成,结合铸件结构合理的加入量控制在0.05%以下;锑强烈促进形成珠光体,对球墨铸铁有使石墨球细化的作用,尤其对大断面球墨铸铁有效,结合铸件结构合理的加入量控制在0.015%以下。
[0045]
步骤六,球化中孕育:在铁液倒入球化包过程中投入三个孕育块,在铁水的五分之二倒入球化包时或以后投入孕育块,孕育块不断的缓释深入的孕育会促使更多的异质核心及石墨生成,从而促使石墨球更多、更圆整、更均匀;于此同时通过联合相应的cu、sn、sb合金作用,更可在共晶凝固时促使石墨以更圆整形式析出长大以及共析转变过程中稳定铸态下的珠光体含量。
[0046]
优先地,分别在铁液的五分之二、五分之三、五分之四分别向球化包投放孕育块;孕育块使用长30-50mm、宽30-50mm、高20-30mm的含si、ba、ca、al的孕育块,加入量为0.1%-0.3%。更优选地,为了减少投放量,可一次性投入个孕育块,满足三次分别投入的孕育块的量。大吨位球铁铸件采用大块状的孕育块比传统采用小颗粒的孕育剂能够有效延缓孕育剂的溶解,延长溶解的时间,使孕育剂在铁水中能够充分反应。此外,在投入孕育块后,铁液局部温度下降,孕育块溶度较高,进而促使局部铁液形成温度、浓度起伏区域,根据液态合金中元素浓度起伏理论,能够促进铁液的球化效果。中期球化包球化过程中生成的硫化物(mgs)、氧化物(mgo)会与第一次、第二次孕育处理过程中形成大量的sio2结合,形成具有双重结构核心的mgs
·
sio2,mgo
·
sio2,2mgo
·
sio2等斜方晶系复式硅酸盐,同时孕育剂中少量的si、ba、ca、al等元素对双重结构核心mgs
·
sio2,mgo
·
sio2,2mgo
·
sio2的表面成分进行催化、改变并激活,让其成为石墨有效析出的异质核心,依靠上述异质核心石墨大量生成并长大。随着球化反应以及第二次孕育剂的投入量,孕育剂溶解完全,无法再进行净化球化环境,为了能够进一步促使石墨异质核心的生成和长大。
[0047]
步骤七,球化后检测:对球化后的铁液进行扒渣、吹包,完成后取试样检测球化后铁水成分。如表1所示,球墨铸铁铁水的最终成分为:c:3.7-3.85%;si:2.0-2.2%;mn:0.3-0.4%;p≤0.04%;s≤0.025%;cu:0.3-0.4%;sn:0.02-0.04%;sb:≤0.015%;mg:0.035-0.06%,余量为fe。
[0048]
步骤八,随流孕育及浇注:球化检测后将铁水包运至铸件浇杯口处并加入孕育剂块,1330-1350℃完成浇注,使用长度为30-200mm、宽度为30-200mm、高为10-20mm孕育块,加入量0.1%-0.3%。随流的第四孕育能够使更多的异质核心及石墨生成,从而促使石墨球更多、更圆整、更均匀;促使石墨以更圆整形式析出长大以及共析转变过程中稳定铸态下的珠光体含量。为了充分球化,保证浇注铁液性能的稳定,进而保证铸件的力学性能,对制备过程的时间进行严格限定,优先地,从球化开始到浇注前的时间小于15分钟。
[0049]
最终通过上述工艺可以保证铸态下大吨位球铁的石墨球数、石墨圆整度和石墨球不产生畸变且铸态下的珠光体含量稳定等效果,从而有效保证大吨位球铁的力学性能。
[0050]
根据上述制造工艺方法,铸造完成的铸件横梁的试块的金相组织和力学性能如表3所示,具体的金相组织图如附图2-5所示。铸造完成后的横梁铸件本体试块的球化等级为2级(球化率不低于90%);40mm的附注试块的石墨球数200-250个/mm2,70mm的附注试块的石墨球数150-180个/mm
2,
,可见,通过本实施例的制造工艺的石墨球数得到了明显提高。试块的珠光体含量达到95%以上,铸件硬度达到了229hbw以上;力学性能的抗拉强度达到了617mpa以上,延伸率达到了3.0以上,均优于球墨铸铁的qt600-3的力学性能。
[0051][0052][0053]
表3
[0054]
表4中是本实施例中球铁横梁铸件与灰铁同种类型横梁的变形量对比。由表4可知,根据本发明的制造工艺制造的横梁的试块的弹性模量大约是灰铁横梁的弹性模量的2倍,但自身变形量大约是灰铁横梁的一半,而横梁的试块的抗拉强度是灰铁横梁的2倍以上由表4可知,本实施例中球墨铸铁铸件相比常规的灰铁铸件具有更少的变形量和更好更稳定的力学性能。
[0055][0056]
表4
[0057]
实施例二:
[0058]
为了延长孕育剂在铁液的中的溶解时间,增加反应时间,使孕育效果充分在铁液中发挥。同时也可以让铁液充分的存在温度、浓度起伏区域,能够促进铁液的球化效果,减少投放孕育剂对铁液的影响,保证孕育效果。孕育块采用直接在市场上购买压实后的孕育块,或者铸造厂家将购买的小颗粒或粉状的孕育剂经过压实或振实得到,且压实或振实后的孕育剂成块状,最后封装获得后投入实际生产用的孕育剂块。孕育剂块经压实后的振实密度比常规松散状态下小颗粒的孕育剂的大。通过对孕育剂块的进行压缩紧实,由于压实的孕育剂块的颗粒紧实,导热效率低,进而可有效推迟孕育剂的熔化时间,能够有效降低孕育块的传热效率,从而可以在球化包中倒入一定量的铁水后,孕育剂成块开始缓慢释放,保证孕育剂在铁水中充分反应,进而实现孕育剂的缓释效果,延长孕育剂块的溶解时间,进一步促进铁液的球化,保证孕育效果。
[0059]
尽管已经示出和描述了本发明的实施例,对于本领域的普通技术人员而言,可以理解在不脱离本发明的原理和精神的情况下可以对这些实施例进行多种变化、修改、替换和变型,本发明的范围由所附权利要求及其等同物限定。