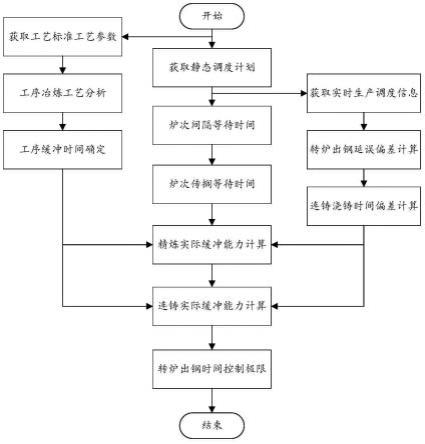
1.本发明涉及炼钢-连铸过程的生产计划与调度技术领域,特别涉及一种基于转炉出钢延迟程度判断的炼钢-连铸过程调度方法。
背景技术:2.钢铁工业作为国家经济社会发展的重要基础性支柱产业,其发展水平是一个国家综合国力的重要体现。近几年,钢铁工业向着绿色低碳方向转型升级成为必然的发展要求。作为典型的流程制造业,钢铁制造流程的高效智能管控可以有效帮助钢铁企业节能降耗、减少碳排放,是钢铁工业实现绿色低碳与智能化发展的关键技术。
3.炼钢-连铸区段作为钢铁制造流程的核心区段,覆盖了铁水预处理、转炉/ 电炉炼钢、炉外精炼、连铸等多个工序,包含大量装备以及众多生产工艺,是一个高温条件下包含气-液-固多相复杂物理化学反应的准连续/间歇生产过程,这导致了炼钢-连铸区段的生产调度极为复杂。该区段的生产调度是一个具备多约束性和不确定性特征的多目标组合优化问题,且由于炼钢-连铸过程的生产工艺复杂、工序/设备繁多、物流交叉频繁,其调度过程必然发生不确定性事件(例如出钢延迟、钢水温度不符合生产要求等),因此,静态调度计划并不能完全适用于生产现场的实时调度。同时,由于连铸连浇,其对钢水供应节奏、温度等都有严格要求,所以,炼钢-连铸区段的生产调度具备很强的实时性要求,在发生不确定性事件后,调度计划应能够进行快速调整以应对各种突发情况并保证调度计划的优异性。在炼钢厂实际生产过程中,利用工序缓冲能力调整前后工序生产节奏以保证生产连续性是现场调度人员的重要手段。因此,如何准确量化炼钢-连铸调度过程的动态缓冲能力,获得转炉冶炼时间控制极限对现场调度人员判断当前生产运行状况、及时进行准确调度调整、保障炼钢厂动态有序-协同连续运行具有极为重要的现实意义。
4.国内外学者对于炼钢-连铸调度过程的量化评价问题进行了研究,但相关研究报道还较少。针对该问题,文献“基于仿真的炼钢车间生产调度优化技术研究,重庆大学,2007”阐述了平均设备利用率、平均等待队列、平均等待时间、计划完成时间、连浇实现率等五项炼钢厂生产调度优化的指标。文献“quantitative evaluation of multi-process collaborative operation insteelmaking-continuous casting section,int.j.min.met.mater.,2020,8(28): 1353-1366”公开了一种多工序协同运行水平量化评价模型,其综合考虑了工序作业周期、连浇炉数、系统产能、炉-机对应关系及生产调度影响因素等,实现了对多工序协同运行水平的量化评价。文献“特殊钢厂炉机匹配研究,北京科技大学学报,2013,35(1):126-133”提出了炉
→
机匹配度、工序当量周期等参数,用于评价炼钢-连铸区段的炉-机匹配模式和工序间生产运行节奏的协调性。
5.上述相关研究所建立的评价指标或是针对炼钢厂生产调度模型的性能进行评价,或是基于炼钢厂物质流的基本运行参数对炼钢厂生产运行水平进行评价,两者反应的均是对炼钢厂已有生产运行结果的评价,可用于后续生产调度模型的优化与炼钢厂车间布局的改造。
6.炼钢-连铸过程具备很强的实时性与突发性,因此,生产过程中需进行频繁的调度调整以适应各种变化来实现生产运行的稳定、高效性,上述评价指标对生产现场实时调度的指导性有限,目前尚缺少可供现场调度人员参考,并用于实时判断当前生产运行状态以便及时准确进行动态调整的调度指标。
技术实现要素:7.针对上述炼钢-连铸调度过程存在的问题,本发明提供了一种基于转炉出钢延迟程度判断的炼钢-连铸过程调度方法,其目的在于通过分析转炉炉次发生不同程度出钢延迟的条件下,后续转炉炉次冶炼时间控制极限的定量化表达,为现场实际调度过程提供实时参考指标,解决炼钢-连铸调度问题。
8.为解决上述技术问题,本发明提供了如下技术方案:
9.一种基于转炉出钢延迟程度判断的炼钢-连铸过程调度方法,包括:
10.获取炼钢厂各工序的标准工艺参数;
11.获取当前炼钢-连铸过程各炉次静态调度计划数据和各炉次的实时调度数据;
12.确定缓冲方式,计算不同缓冲方式下转炉冶炼时间控制极限;其中,所述缓冲方式包括:只考虑精炼工序缓冲以及同时考虑精炼工序与连铸工序双重缓冲;在只考虑精炼工序缓冲时,所述转炉冶炼时间控制极限根据精炼工序的实际缓冲时间计算;在同时考虑精炼工序与连铸工序双重缓冲时,所述转炉冶炼时间控制极限根据精炼工序的实际缓冲时间与连铸工序的实际缓冲时间计算;
13.基于转炉实际冶炼周期与转炉冶炼时间控制极限的关系调整工序参数。
14.进一步地,所述标准工艺参数包括:转炉标准冶炼周期、lf精炼炉标准软吹时间、lf精炼炉标准最小软吹时间、连铸机标准浇注时间、初始计划拉速、最小计划拉速,以及各工序之间钢水传搁过程的必要传搁时间。
15.进一步地,所述静态调度计划数据包括:转炉计划开始冶炼时刻、转炉计划完成冶炼时刻、lf精炼炉计划通电开始时刻、lf精炼炉计划软吹完成时刻、连铸机计划开始浇注时刻,以及连铸机计划完成浇注时刻;
16.所述实时调度数据包括:钢水质量、转炉实际开始冶炼时刻、转炉实际完成冶炼时刻、连铸机实际开始浇注时刻和连铸机实际完成浇注时刻。
17.进一步地,所述精炼工序的实际缓冲时间的计算过程包括:
18.根据静态调度计划,当前转炉炉次与后一炉次的间隔时间δτ1为:
[0019][0020]
当前转炉炉次在转炉到lf精炼炉之间的传搁等待时间δτ2为:
[0021][0022]
当前转炉炉次在lf精炼炉软吹位到连铸机之间的传搁等待时间δτ3为:
[0023][0024]
前一炉次对当前转炉炉次的转炉开始时间的影响δτ4为:
[0025]v1,c
表示初始计划拉速,表示最小计划拉速。
[0038]
进一步地,在同时考虑精炼工序与连铸工序双重缓冲时,所述转炉冶炼时间控制极限的计算公式为:
[0039][0040]
其中,表示同时考虑精炼工序与连铸工序双重缓冲时的转炉冶炼时间控制极限,表示转炉标准冶炼周期,表示当前转炉炉次的精炼过程实际缓冲时间,表示当前转炉炉次的连铸工序的实际缓冲时间。
[0041]
进一步地,在同时考虑精炼工序与连铸工序双重缓冲时,所述基于转炉实际冶炼周期与转炉冶炼时间控制极限的关系调整工序参数,包括:
[0042]
当第i-1炉次转炉冶炼结束时刻发生延误,取消第i炉次转炉冶炼前等待时间,即第i-1炉次转炉冶炼完成后即刻开始第i炉次的转炉冶炼;
[0043]
当转炉实际冶炼周期小于/等于时,缩短当前精炼炉次lf精炼软吹时长,或当转炉实际冶炼周期大于且小于/等于时,缩短当前精炼炉次lf精炼软吹时长,同时延长当前浇注炉次的浇注时间;
[0044]
其中,所述第i-1炉次为冶炼结束时刻发生延误的首炉次。
[0045]
进一步地,所述基于转炉实际冶炼周期与转炉冶炼时间控制极限的关系调整工序参数,还包括:当转炉实际冶炼周期大于时,采用预设的动态调度模型对当前实际调度问题进行重新求解,获取新的排产计划。
[0046]
本发明提供的技术方案带来的有益效果至少包括:
[0047]
本发明提供的基于转炉出钢延迟程度判断的炼钢-连铸过程调度方法,通过对转炉冶炼时间控制范围的计算,可得出明确的时间控制范围,明确转炉冶炼时间的控制极限。当发生不同程度出钢延迟时,可根据实际延迟时间迅速判断当前炼钢厂生产运行中精炼工序与连铸工序所需进行的调整,可用于指导现场实际调度,适用于生产过程复杂的实时调度过程。
附图说明
[0048]
为了更清楚地说明本发明实施例中的技术方案,下面将对实施例描述中所需要使用的附图作简单地介绍,显而易见地,下面描述中的附图仅仅是本发明的一些实施例,对于本领域普通技术人员来讲,在不付出创造性劳动的前提下,还可以根据这些附图获得其他的附图。
[0049]
图1是本发明实施例提供的基于转炉出钢延迟程度判断的炼钢-连铸过程调度方法的执行流程示意图。
具体实施方式
[0050]
为使本发明的目的、技术方案和优点更加清楚,下面将结合附图对本发明实施方
式作进一步地详细描述。
[0051]
第一实施例
[0052]
本实施例以某炼钢厂生产q355b钢种、工艺路径为转炉-lf精炼炉-连铸机、铸坯断面规格为370mm
×
750mm,铸坯米重为0.9737t/m,连铸机流数为3为例,对本发明的基于转炉出钢延迟程度判断的炼钢-连铸过程调度方法进行详细说明。如图1所示,该基于转炉出钢延迟程度判断的炼钢-连铸过程调度方法包括:
[0053]
步骤1:获取各工序生产q355b钢时的标准工艺参数,包括:转炉标准冶炼周期lf精炼炉标准软吹时间lf精炼炉标准最小软吹时间连铸机标准浇注时间初始计划拉速v
1,c
、最小计划拉速各工序之间钢水传搁过程的必要传搁时间其中,i为炉次数,j和j’为工序数,j=1、j’=1 均表示转炉工序,j=2、j’=2均表示lf精炼通电工序,j=3、j’=3均表示精炼软吹工序,j=4、j’=4均表示连铸工序;具体数据如表1和表2所示:
[0054]
表1标准工艺参数
[0055][0056]
表2各工序间传搁过程的必要传搁时间表
[0057][0058]
步骤2:获取当前炼钢-连铸过程各炉次静态调度计划数据以及当前炼钢-连铸过程各炉次的实时调度数据;其中,各炉次静态调度计划数据包括:转炉计划开始冶炼时刻转炉计划完成冶炼时刻lf精炼炉计划通电开始时刻lf精炼炉计划软吹完成时刻连铸机计划开始浇注时刻连铸机计划完成浇注时刻具体如表3所示:
[0059]
表3炼钢-连铸过程静态计划数据表
[0060][0061][0062]
实时调度数据包括:钢水质量gi、转炉实际开始冶炼时刻转炉实际完成冶炼
时刻连铸机实际开始浇注时刻连铸机实际完成浇注时刻如表4所示,其中,第1炉次转炉实际开始冶炼时刻与该炉次转炉计划开始冶炼时刻相同,从表4中可以看出,第2炉次转炉冶炼结束时刻与静态计划相比发生5min延迟。此时,计算第3炉次的转炉冶炼时间控制极限,并根据第3炉次的实际转炉冶炼时间进行相应调控。
[0063]
表4炼钢-连铸过程实时调度数据表
[0064][0065]
步骤3:计算转炉当前冶炼炉次(即第3炉次)精炼工序的实际缓冲时间;根据静态调度计划,转炉第3炉次与后一炉次(即第4炉次)间隔时间为:
[0066][0067]
第3炉次在转炉到lf精炼炉之间的钢水传搁等待时间为:
[0068][0069]
第3炉次在lf精炼炉软吹位到连铸机之间的钢水传搁等待时间为:
[0070][0071]
转炉上一炉次(即第2炉次)对当前转炉炉次(即第3炉次)转炉开始时间的影响为:
[0072][0073]
则第3炉次的lf精炼过程实际缓冲时间为:
[0074][0075]
步骤4:计算转炉当前冶炼炉次(即第3炉次)连铸工序的实际缓冲时间;
[0076]
当第3炉次开始转炉冶炼时,连铸工序的实际缓冲时间为:
[0077][0078]
步骤5:根据lf精炼工序的实际缓冲时间与连铸工序的实际缓冲时间,得到不同缓冲方式下转炉冶炼时间控制极限,具体如下:
[0079]
1)第3炉次只考虑lf精炼工序缓冲条件下,该炉次对应的转炉冶炼时间控制极限为:
[0080]
[0081]
2)第3炉次同时考虑精炼工序与连铸工序双重缓冲条件下,该炉次对应的转炉冶炼时间控制极限为:
[0082][0083]
步骤6:基于第3炉次转炉冶炼周期与转炉冶炼时间控制极限的关系调整工序参数,对于转炉工序的调整:取消第3炉次的转炉冶炼前等待时间,即第2 炉次转炉工序完成后立即开始第3炉次转炉工序;对于精炼和连铸工序的调整,如前所述本实施例的转炉实际冶炼周期为45min大于/等于且小于/等于此时需要同时考虑第3炉次精炼和未浇注炉次(本实施例为第2炉次未浇注)连铸工序进行缓冲,即缩短第3炉次lf精炼软吹时长至7min,加快 lf精炼出钢,并降低第2炉次连铸拉速至0.99m/min,延长2min浇铸时间。通过上述的工序调整即保障了连铸工序第3炉次的钢水供应,同理基于上述调整方式继续对后续受影响导致冶炼开始时刻发生延迟的第4、第5炉次进行调整,直至第6炉次即可实现转炉开始时刻与计划开始时刻保持一致,随即停止调整。
[0084]
需要说明的是,在炼钢-连铸调度过程中,转炉出钢延迟会对后续工序与炉次产生不同程度影响进而连铸连浇,根据研究与现场经验总结,炼钢-连铸过程具有多种缓冲手段,如利用调度计划中炉次之间存在的间隔等待时间进行缓冲、通过压缩精炼工序软吹时长进行缓冲以及通过降低连铸拉速延长浇铸时间进行缓冲等。其中精炼工序因其自身工艺特点,软吹时间可进行一定程度的缩减,因此该工序通常被作为主要的缓冲手段。在利用其进行缓冲时,首先要考虑其由于自身工艺要求所带来的常规缓冲能力,其次需要综合考虑转炉已出钢炉次的出钢延迟对精炼时间的影响以及已浇铸炉次因钢水重量波动导致浇铸时间变化对精炼时间的影响,最后得出如前所述的缓冲时间。
[0085]
第二实施例
[0086]
本实施例以某炼钢厂生产q355b钢种、工艺路径为转炉-lf精炼炉-连铸机、铸坯断面规格为370mm
×
750mm,铸坯米重为0.9737t/m,连铸机流数为3为例,对本发明的基于转炉出钢延迟程度判断的炼钢-连铸过程调度方法进行详细说明。如图1所示,该基于转炉出钢延迟程度判断的炼钢-连铸过程调度方法包括:
[0087]
步骤1:获取各工序生产q355b钢时的标准工艺参数,包括:转炉标准冶炼周期lf精炼炉标准软吹时间lf精炼炉标准最小软吹时间连铸机标准浇注时间初始计划拉速v
1,c
、最小计划拉速各工序之间钢水传搁过程的必要传搁时间具体数据如表5和表6所示:
[0088]
表5标准工艺参数
[0089][0090]
表6各工序间传搁过程的必要传搁时间表
[0091][0092]
步骤2:获取当前炼钢-连铸过程各炉次静态调度计划数据以及当前炼钢-连铸过程各炉次的实时调度数据;其中,各炉次静态调度计划数据包括:转炉计划开始冶炼时刻转炉计划完成冶炼时刻lf精炼炉计划通电开始时刻lf精炼炉计划软吹完成时刻连铸机计划开始浇注时刻连铸机计划完成浇注时刻如表7所示:
[0093]
表7炼钢-连铸过程静态计划数据表
[0094][0095][0096]
各炉次的实时调度数据包括:钢水质量gi、转炉实际开始冶炼时刻转炉实际完成冶炼时刻连铸机实际开始浇注时刻连铸机实际完成浇注时刻如表8所示,其中第1炉次转炉实际开始冶炼时刻与该炉次转炉计划开始冶炼时刻相同,从表8中可以看出,第2炉转炉出钢发生延迟,冶炼周期为 45min,同时,第3炉也同样发生转炉出钢延迟,冶炼周期为45min。此时,已进行相关调控(如实施例1),即第3炉次lf精炼软吹时长缩短至7min,并降低连铸工序第2炉次的计划拉速至0.99m/min。此时,需计算第4炉次的转炉冶炼时间控制极限,并根据第4炉的实际转炉冶炼时间进行相应调控。
[0097]
表8炼钢-连铸过程实时调度数据表
[0098][0099]
步骤3:计算转炉当前冶炼炉次(即第4炉次)精炼工序的实际缓冲时间;根据静态调度计划,转炉第4炉次与后一炉次(即第5炉次)间隔时间为:
[0100][0101]
第4炉次在转炉到lf精炼炉之间的钢水传搁等待时间为:
[0102][0103]
第4炉次在lf精炼炉软吹位到连铸机之间的钢水传搁等待时间为:
[0104][0105]
转炉上一炉次(即第3炉次)对当前转炉炉次(即第4炉次)转炉开始时间的影响为:
[0106][0107]
则第4炉次的精炼过程实际缓冲时间为:
[0108][0109]
步骤4:根据lf精炼工序的实际缓冲时间,得到转炉冶炼时间控制极限为:
[0110][0111]
步骤5:基于第4炉次转炉冶炼周期与转炉冶炼时间控制极限的关系调整工序参数,对于转炉工序的调整:取消第4炉次的转炉冶炼前等待时间,即第3 炉次转炉工序完成后立即开始第4炉次转炉工序;对于精炼和连铸工序的调整,如前所述本实施例的转炉实际冶炼周期为40min小于/等于此时对于第 4炉次,仅需要考虑lf精炼工序进行缓冲,即缩短该炉次lf精炼软吹时长至 8min,加快lf精炼出钢。通过上述的工序调整即保障了连铸工序第4炉次的钢水供应,同理基于上述调整方式对后续受影响导致冶炼开始时刻发生延迟的第5 炉次进行调整,直至第6炉次即可实现转炉开始时刻与计划开始时刻保持一致,随即停止调整。
[0112]
第三实施例
[0113]
本实施例以某炼钢厂生产q235b钢种、工艺路径为转炉-lf精炼炉-连铸机、铸坯断面规格为390mm
×
1024mm,铸坯米重为1.291t/m,连铸机流数为3为例,对本发明的基于转炉出钢延迟程度判断的炼钢-连铸过程调度方法进行详细说明。如图1所示,该基于转炉出钢延迟程度判断的炼钢-连铸过程调度方法包括:
[0114]
步骤1:获取各工序生产q235b钢时的标准工艺参数,包括:转炉标准冶炼周期lf精炼炉标准软吹时间lf精炼炉标准最小软吹时间连铸机标准浇注时间初始计划拉速v
1,c
、最小计划拉速各工序之间钢水传搁过程的必要传搁时间具体数据如表9和表10所示:
[0115]
表9标准工艺参数
[0116][0117]
表10各工序间传搁过程的必要传搁时间表
[0118][0119]
步骤2:获取当前炼钢-连铸过程各炉次静态调度计划数据以及当前炼钢-连铸过程各炉次的实时调度数据;其中,各炉次静态调度计划数据包括:转炉计划开始冶炼时刻转炉计划完成冶炼时刻lf精炼炉计划通电开始时刻lf精炼炉计划软吹完成时刻连铸机计划开始浇注时刻连铸机计划完成浇注时刻如表11所示:
[0120]
表11炼钢-连铸过程静态计划数据表
[0121][0122]
各炉次的实时调度数据包括:钢水质量gi、转炉实际开始冶炼时刻转炉实际完成冶炼时刻连铸机实际开始浇注时刻连铸机实际完成浇注时刻如表12所示,其中第1炉次转炉实际开始时刻与该炉次转炉计划开始时刻相同,计算第2炉次的转炉冶炼时间控制极限,并根据第2炉的实际转炉冶炼时间进行相应调控。
[0123]
表12炼钢-连铸过程实时调度数据表
[0124][0125]
步骤3:计算转炉当前冶炼炉次(即第2炉次)精炼工序的实际缓冲时间;根据静态调度计划,转炉第2炉次与后一炉次(即第3炉次)间隔时间为:
[0126][0127]
第2炉次在转炉到lf精炼炉之间的钢水传搁等待时间为:
[0128][0129]
第2炉次在lf精炼炉软吹位到连铸机之间的钢水传搁等待时间为:
[0130][0131]
转炉上一炉次(即第1炉次)对当前转炉炉次(即第2炉次)转炉开始时间的影响为:
[0132][0133]
则第3炉次的lf精炼过程实际缓冲时间为:
[0134][0135]
步骤4:根据lf精炼工序的实际缓冲时间,得到转炉冶炼时间控制极限为:
[0136][0137]
步骤5:基于第2炉次转炉冶炼周期与转炉冶炼时间控制极限的关系调整工序参数,第2炉次转炉冶炼开始时刻未发生延误,实际冶炼周期为46min小于/ 等于对于精炼和连铸工序的调整,如前所述本实施例中,对于第2炉次,仅需要考虑精炼工序进行缓冲,即缩短该炉次lf精炼软吹时长至10min,加快lf精炼出钢,通过上述的工序调整即保障了连铸工序第2炉次的钢水供应。
[0138]
此外,需要说明的是,本发明可提供为方法、装置或计算机程序产品。因此,本发明实施例可采用完全硬件实施例、完全软件实施例或结合软件和硬件方面的实施例的形式。而且,本发明实施例可采用在一个或多个其中包含有计算机可用程序代码的计算机可用存储介质上实施的计算机程序产品的形式。
[0139]
本发明实施例是参照根据本发明实施例的方法、终端设备(系统)、和计算机程序产品的流程图和/或方框图来描述的。应理解可由计算机程序指令实现流程图和/或方框图中的每一流程和/或方框、以及流程图和/或方框图中的流程和/或方框的结合。可提供这些计算机程序指令到通用计算机、嵌入式处理机或其他可编程数据处理终端设备的处理器以产生一个机器,使得通过计算机或其他可编程数据处理终端设备的处理器执行的指令产生用于实现在流程图一个流程或多个流程和/或方框图一个方框或多个方框中指定的功能的装置。
[0140]
这些计算机程序指令也可存储在能引导计算机或其他可编程数据处理终端设备以特定方式工作的计算机可读存储器中,使得存储在该计算机可读存储器中的指令产生包括指令装置的制造品,该指令装置实现在流程图一个流程或多个流程和/或方框图一个方框或多个方框中指定的功能。这些计算机程序指令也可装载到计算机或其他可编程数据处理终端设备上,使得在计算机或其他可编程终端设备上执行一系列操作步骤以产生计算机实现的处理,从而在计算机或其他可编程终端设备上执行的指令提供用于实现在流程图一个流程或多个流程和/或方框图一个方框或多个方框中指定的功能的步骤。
[0141]
还需要说明的是,在本文中,术语“包括”、“包含”或者其任何其他变体意在涵盖非
排他性的包含,从而使得包括一系列要素的过程、方法、物品或者终端设备不仅包括那些要素,而且还包括没有明确列出的其他要素,或者是还包括为这种过程、方法、物品或者终端设备所固有的要素。在没有更多限制的情况下,由语句“包括一个
……”
限定的要素,并不排除在包括所述要素的过程、方法、物品或者终端设备中还存在另外的相同要素。
[0142]
最后需要说明的是,以上所述是本发明可选实施方式,应当指出,尽管已描述了本发明可选实施例,但对于本技术领域的技术人员来说,一旦得知了本发明的基本创造性概念,在不脱离本发明所述原理的前提下,还可以做出若干改进和润饰,这些改进和润饰也应视为本发明的保护范围。所以,所附权利要求意欲解释为包括优选实施例以及落入本发明实施例范围的所有变更和修改。