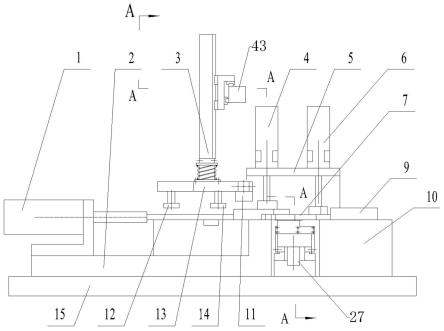
1.本发明涉及自动上料和夹紧技术,具体为一种组合件自动伸开定距、定位和夹紧装置。
背景技术:2.目前,组合部件的多个配合面加工通常采用先加工后组装方式,当相关精度要求较高时不易达到要求;或采用组装后加工,则多采用手动调整组合状态后再加工,没有完全实现自动化。如数显卡尺、游标卡尺加工,为提高量面精度,可采用尺框、尺身组合后再整体精磨;按常规方式是手动将组合部件的尺框、尺身拉开至适当的规定的位置尺寸,再进行安装、定位和夹紧,或采用半自动化将组合件拉开固定距离的工序单独进行,再通过中间转运工序进入精密磨削加工工序;如果将组合件状态调整工序和上料、加工等工序集成在一起实现全程自动化,将进一步提高生产自动化和效率。
3.与上述卡尺组合加工相类似的加工场合,同样也存在一样的问题。
技术实现要素:4.本发明的目的是针对现有技术中存在的不足,而提出一种组合件自动伸开定距、定位和夹紧装置。这种装置可实现组合件的自动准确定位、夹紧、定距,能实现整个加工过程的全自动化。
5.实现本发明目的的技术方案是:一种组合件自动伸开定距、定位和夹紧装置,包括间隔设在底板上的第一基座和第二基座,第一基座上设有带安装座的第一气缸,第一基座上设有用于安装第二气缸的缺口,其中第一气缸的活塞杆穿过安装座朝向第二基座,第二气缸的活塞杆方向与第一气缸活塞杆方向垂直;第二基座上设有定位块;第一基座和第二基座上方设有部分横跨第一基座和第二基座带弯折的支架,支架上间隔设有穿过支架的第一压紧气缸和第二压紧气缸,第一压紧气缸和第二压紧气缸的活塞杆均朝向底板;第一基座的上方设有夹持运动单元,第一基座和第二基座之间的底板上设有定距单元,夹持运动单元包括带x向滑动滑座的纵向梁架、带y向滑动滑座的横梁和可在横梁滑座上作z向运动的升降臂,其中横梁固定在纵向梁架的滑座上,纵向梁架通过支撑杆水平固定在底板的侧边;升降臂下端设有组合板,组合板的底面顺序间隔设有第一吸嘴、第二吸嘴和夹爪,第一吸嘴、第二吸嘴和夹爪的中垂线在同一直线上,第一吸嘴与第一气缸靠近,定距单元包括固定在底板上带弯折的支座,支座两侧边分别设有第一导轨和第二导轨,第一导轨和第二导轨的外侧分别设有第一压板和第二压板,第一导轨和第二导轨上横跨设有移动座,第一压板和第二压板后端头连接设有第三气缸,第三气缸的活塞杆与移动座连接;移动座的前端在纵向,即x向由里朝外依次设有梯形块和楔形定距块,其中梯形块的斜面与楔形定距块的斜面配合,楔形定距块上表面与第一压紧气缸和第二压紧气缸的活塞杆靠近;移动座上还设有垂直的与底板靠近的第四气缸,第四气缸的活塞杆与梯形块
固接,楔形定距块不与梯形块接触的两侧边分别设有带弯折的第一导向挡板和第二导向挡板,楔形定距块远离梯形块的侧面设有呈l状的限位角板,限位角板与楔形定距块之间设有第一弹簧,限位角板的底面与移动座之间设有一组第二弹簧,移动座上还设有用于限定限位角板的限位板,移动座上还设有盖板,定距单元前方设有用于加工组合件的加工组件,底板上设有带回转弹簧的回转挡板,支架上设有与回转挡板配合封闭的挡板,第一气缸、第二气缸、第三气缸、第四气缸、第一压紧气缸、第二压紧气缸、纵向梁架、横梁和升降臂、第一吸嘴、第二吸嘴和夹爪的运动均由控制台控制。
6.所述梯形块与楔形定距块两斜面的斜面角度不大于自锁角。
7.所述支座上还设有位于移动座下方的检测单元,用于检测移动座的位置状态。
8.将组合件放置在第一基座上时,第一气缸的活塞杆伸出后与组合件接触。
9.所述支座的安装位置依据组合件伸开的距离及位置确定,以确保组合件加工的准确性。
10.所述第二气缸的活塞杆与组合件的侧面接触,用于组合件的侧向定位。
11.所述升降臂与组合板之间设有弹性组件,避免在运动时与升降臂发生干涉。
12.工作原理:(1)组合件初始闭合状态时,在控制台的控制下,夹爪夹持组合件中的尺框部分、第一吸嘴和第二吸嘴负压吸住组合件的尺身部分,从而拾取组合件并移动放置至第一基座和第二基座的规定位置上;随后第一吸嘴和第二吸嘴负压解除,第一气缸的活塞杆顶出,带动组合件尺身相对尺框移动至定位块停止,实现拉出运动,进而第一气缸与第二气缸交替动作,第一气缸退回—第二气缸压紧—第一气缸压紧,完成组合件尺身定位;(2)接着,第三气缸动作,活塞杆顶出,推动移动座在第一导轨、第二导轨、第一导轨压板、第二导轨压板组成的组合导轨上运动至组合件的两个爪量面之间;向前移动过程中第四气缸缸体将回转挡板回转压下,随后第四气缸动作,活塞杆伸出,推动梯形块向上运动,利用楔形定距块的楔形并在第一导向挡板、第二导向挡板和第二弹簧的作用下,带动楔形定距块同时向上和向外侧伸出,直至第四气缸运动到位;(3)纵向梁架的滑座作x向运动,通过横梁和升降臂带动组合板连同第一吸嘴、第二吸嘴和夹爪推动组合件中的尺框适当移动靠向移动座,通过弹性位移使尺框量爪量面靠紧楔形定距块,实现尺框量爪量面和尺身量爪量面的准确定距;(4)组合件上方的第一压紧气缸、第二压紧气缸动作,第一压紧气缸和第二压紧气缸的活塞杆向下伸出,分别压紧组合件的尺框和尺身靠近需要加工处的部位,实现组合件在加工处附近区域的可靠压紧;(5)夹爪松开组合件,升降臂z向提升,横梁和纵向梁架部件继而作x、y向运动,带动组合板联合运动退出回到初始位置或下一工作位置,同时,第四气缸反向动作,其活塞杆带动梯形块向下运动,在第一弹簧和第二弹簧的作用下,楔形定距块在水平方向缩回,避免后续向下移动时与组合件零件摩擦;当梯形块下移碰到楔形定距块的下挡边后直接带动其下移,直到第四气缸反向运动到达下部限位,使楔形定距块在水平和垂向缩回到初始位置;接着第三气缸反向运动,其活塞杆带动移动座连同楔形定距块退回到初始位置,同时回转挡板自动弹回到初始竖直状态,贴紧挡板,形成封闭,阻挡切削液溅入;
(6)组合件伸开、定距、定位和夹紧,楔形定距块退出加工区域运动结束,可进入加工状态,由控制台控制加工组件通过加工运动对组合件的伸开开口部位进行加工;(7)加工结束后,第一压紧气缸、第二压紧气缸、第一气缸、第二气缸反向动作退回,松开组合件;纵向梁架滑座、横梁、升降臂联合作x、y、z向运动,通过组合板上的夹爪、第一吸嘴和第二吸嘴及负压转换,拾取组合件,转移至规定位置,完成下料,开始下一轮上料、伸开、定距、定位和夹紧、加工的循环;还可以根据另一种下料要求,在第一吸嘴和第二吸嘴转换为负压之前,先通过纵向梁架上的滑座作x运动,连同夹爪带动组合件相应的一个零件移动至与另一零件闭合,第一吸嘴和第二吸嘴再转换成负压吸住组合件,进行后续下料运动;(8)各个运动环节都通过检测单元以及各气缸内置感应元件进行位置和状态检测,控制台根据检测信号进行相应控制。
13.本技术方案可应用于自动化智能化加工系统中,具有以下功能特点:可实现组合部件两个零件的自动相对伸开至规定的准确距离,适应加工要求;可自动准确定位、夹紧;定距完成后定距部件可联动收缩和退回,避免与定距加工零件的摩擦。本装置与自动加工环节结合在一起,可实现包括组合件伸开定距环节的整个加工过程的全自动化。
14.这种装置可实现组合件的自动准确定位、夹紧、定距,能实现整个加工过程的全自动化。
附图说明
15.图1为实施例的结构示意图;图2为图1中的a-a处剖视图;图3为图1的俯视图;图4为图2中的b-b处剖视图;图5为图2中的c-c处剖视图;图6为图3中的d-d处剖视图;图7为图4中的e-e处剖视图;图8为实施例中组合件闭合状态示意图;图9为实施例中组合件伸开状态示意图。
16.图中,1、第一气缸; 2、第一基座 ;3、升降臂; 4、第一压紧气缸 ;5、支架;6、第二压紧气缸;7、组合件;9、定位块;10、第二基座;11、夹爪;12、第一吸嘴;13、组合板;14、第二吸嘴;15、底板;16、支座;17、第三气缸;18、移动座; 20、弹性组件;22、加工组件;23、检测单元;24、第二气缸;26、第一导轨;27、第四气缸;28、盖板;29、梯形块;30、楔形定距块;31、第一弹簧;32、限位角板;33、第二弹簧;34、限位板;35、第二导轨;36、第一导轨压板;37、第二导轨压板;38、第一导向挡板;39、第二导向挡板;40、回转挡板;41、挡板;42、纵向梁架;43、横梁。
具体实施方式
17.下面结合附图及具体实施例对本发明作进一步的详细描述,但不是对本发明的限定。
18.实施例:参照图1-图7,一种组合件自动伸开定距、定位和夹紧装置,包括间隔设在底板15上的第一基座2和第二基座10,第一基座2上设有带安装座的第一气缸1,第一基座2上设有用于安装第二气缸24的缺口,其中第一气缸1的活塞杆穿过安装座朝向第二基座10,第二气缸24的活塞杆与第一气缸1活塞杆方向垂直;第二基座10上设有定位块9,第一基座2和第二基座10上方设有部分横跨第一基座2和第二基座10带弯折的支架5,支架5上间隔设有穿过支架5的第一压紧气缸4和第二压紧气缸6,第一压紧气缸4和第二压紧气缸6的活塞杆均朝向底板15;第一基座2的上方设有夹持运动单元,第一基座2和第二基座10之间的底板15上设有定距单元,如图2所示,夹持运动单元包括带x向滑动滑座的纵向梁架42、带y向滑动滑座的横梁43和可在横梁滑座上作z向运动的升降臂3,其中横梁43固定在纵向梁架42的滑座上,纵向梁架42通过支撑杆水平固定在底板的侧边;升降臂3下端设有组合板13,组合板13的底面顺序间隔设有第一吸嘴12、第二吸嘴14和夹爪11,第一吸嘴12、第二吸嘴和夹爪11的中垂线在同一直线上,第一吸嘴12与第一气缸1靠近,如图2-图5所示,定距单元包括固定在底板15上带弯折的支座16,支座16两侧边分别设有第一导轨26和第二导轨35,第一导轨26和第二导轨35的外侧分别设有第一压板36和第二压板37,第一导轨26和第二导轨35上横跨设有移动座18,第一压板36和第二压板37后端头连接设有第三气缸17,第三气缸17的活塞杆与移动座18连接,移动座18的前端在纵向,即x向由里朝外依次设有梯形块29和楔形定距块30,其中梯形块29的斜面与楔形定距块30的斜面配合,楔形定距块30上表面与第一压紧气缸4和第二压紧气缸6的活塞杆靠近,移动座18上还设有垂直的与底板15靠近的第四气缸27,第四气缸27的活塞杆与梯形块29固接,楔形定距块30不与梯形块29接触的两侧边分别设有带弯折的第一导向挡板38和第二导向挡板39,楔形定距块30远离梯形块29的侧面设有呈l状的限位角板32,限位角板32与楔形定距块30之间设有第一弹簧31,限位角板32的底面与移动座18之间设有一组第二弹簧33,移动座18上还设有用于限定限位角板32的限位板34,移动座18上还设有盖板28,第一导向挡板38和第二导向挡板39对楔形定距块30的水平移动起到导向作用,如图2所示,定距单元前方设有用于加工组合件7的加工组件22,底板15上设有带回转弹簧的回转挡板40,支架5上设有与回转挡板40封闭的挡板41,回转挡板40为简单铰支板件机构,铰接处装有回转弹簧,当受作用力时,具有可向前回转并可自动回弹功能,回转挡板40与挡板41配合形成封闭区,避免加工切屑液溅入,第一气缸1、第二气缸24、第三气缸17、第四气缸27、第一压紧气缸4、第二压紧气缸6、纵向梁架42、横梁43和升降臂3、第一吸嘴12、第二吸嘴14和夹爪11的运动均由控制台控制。
19.如图4所示,所述梯形块29与楔形定距块30两斜面的斜面角度α不大于自锁角。
20.所述支座16上还设有位于移动座18下方的检测单元23,用于检测移动座18的位置状态。
21.将组合件7放置在第一基座2上时,第一气缸1的活塞杆伸出后与组合件7接触。
22.所述支座16的安装位置依据组合件7伸开的距离l及位置确定,以确保组合件7加工的准确性。
23.如图6所示,所述第二气缸24的活塞杆与组合件7的侧面接触,用于组合件7的侧向定位。
24.所述升降臂3与组合板13之间设有弹性组件20,避免在运动时与升降臂3发生干涉。
25.本例以游标卡尺作为组合件的示例,本例加工组件为砂轮。
26.工作原理:(1)组合件7初始闭合状态时,如图8所示,在控制台的控制下,夹爪11夹持组合件7中的尺框部分、第一吸嘴12和第二吸嘴14负压吸住组合件7的尺身部分,从而拾取组合件7并移动放置至第一基座2和第二基座10的规定位置上;随后第一吸嘴12和第二吸嘴14负压解除,第一气缸1的活塞杆顶出,带动组合件7尺身相对尺框移动至定位块9停止,实现拉出运动;进而第一气缸1与第二气缸24交替动作,第一气缸1退回—第二气缸24压紧—第一气缸1压紧,完成组合件7尺身定位;(2)接着,第三气缸17动作,活塞杆顶出,推动移动座18在第一导轨26和第二导轨35、第一导轨压板36、第二导轨压板37组成的组合导轨上运动至组合件7尺框和尺身的两个爪量面之间;向前移动过程中第四气缸27缸体将回转挡板40回转压下,随后第四气缸27动作,活塞杆伸出,推动梯形块29向上运动,利用楔形定距块30的楔形并在第一导向挡板38、第二导向挡板39和第二弹簧33的作用下,带动楔形定距块30同时向上和向外侧伸出,直至第四气缸27运动到位;(3)纵向梁架42的滑座作x向运动,通过横梁43和升降臂3带动组合板13连同第一吸嘴12、第二吸嘴14和夹爪11带动组合件7中的尺框适当移动靠向移动座18,通过弹性位移使尺框量爪量面靠紧楔形定距块30,实现尺框量爪量面和尺身量爪量面的准确定距;(4)组合件7上方的第一压紧气缸4、第二压紧气缸6动作,第一压紧气缸4和第二压紧气缸6的活塞杆向下伸出,分别压紧组合件7的尺框和尺身靠近需要加工处的部位,实现组合件7在加工处附近区域的可靠压紧;(5)夹爪11松开组合件7,升降臂3沿z向提升,横梁43和纵向梁架42部件继而作x、y向运动,带动组合板13联合运动退出回到初始位置或下一工作位置,同时,第四气缸27反向动作,其活塞杆带动梯形块29向下运动,在第一弹簧31和第二弹簧33的作用下,楔形定距块30在水平方向缩回,避免后续向下移动时与组合件7零件摩擦;当梯形块29下移碰到楔形定距块30的下挡边后直接带动其下移,直到第四气缸27反向运动到达下部限位,使楔形定距块30在水平和垂向缩回到初始位置;接着第三气缸17反向运动,其活塞杆带动移动座18连同楔形定距块30退回到初始位置,同时回转挡板40自动弹回到初始竖直状态,贴紧挡板41,形成封闭,阻挡切削液溅入;(6)组合件7伸开、定距、定位和夹紧,如图9所示,楔形定距块30退出加工区域运动结束,可进入加工状态,由控制台控制加工组件22通过加工运动对组合件7的伸开开口部位进行加工;(7)加工结束后,第一压紧气缸4、第二压紧气缸6、第一气缸1、第二气缸24反向动作退回,松开组合件7;纵向梁架42滑座、横梁43、升降臂3联合作x、y、z向运动,通过组合板13上的夹爪11、第一吸嘴12和第二吸嘴14及负压转换,拾取组合件7,转移至规定位置,完成下料,开始下一轮上料、伸开、定距、定位和夹紧、加工的循环;还可以根据另一种下料要求,
在第一吸嘴12和第二吸嘴14转换为负压之前,先通过纵向梁架42上的滑座作x运动,连同夹爪带动组合件7的尺框移动至与尺身闭合,第一吸嘴12和第二吸嘴14再转换成负压吸住组合件7,进行后续下料运动;(8)各个运动环节都通过检测单元23以及各气缸内置感应元件进行位置和状态检测,控制台根据检测信号进行相应控制。