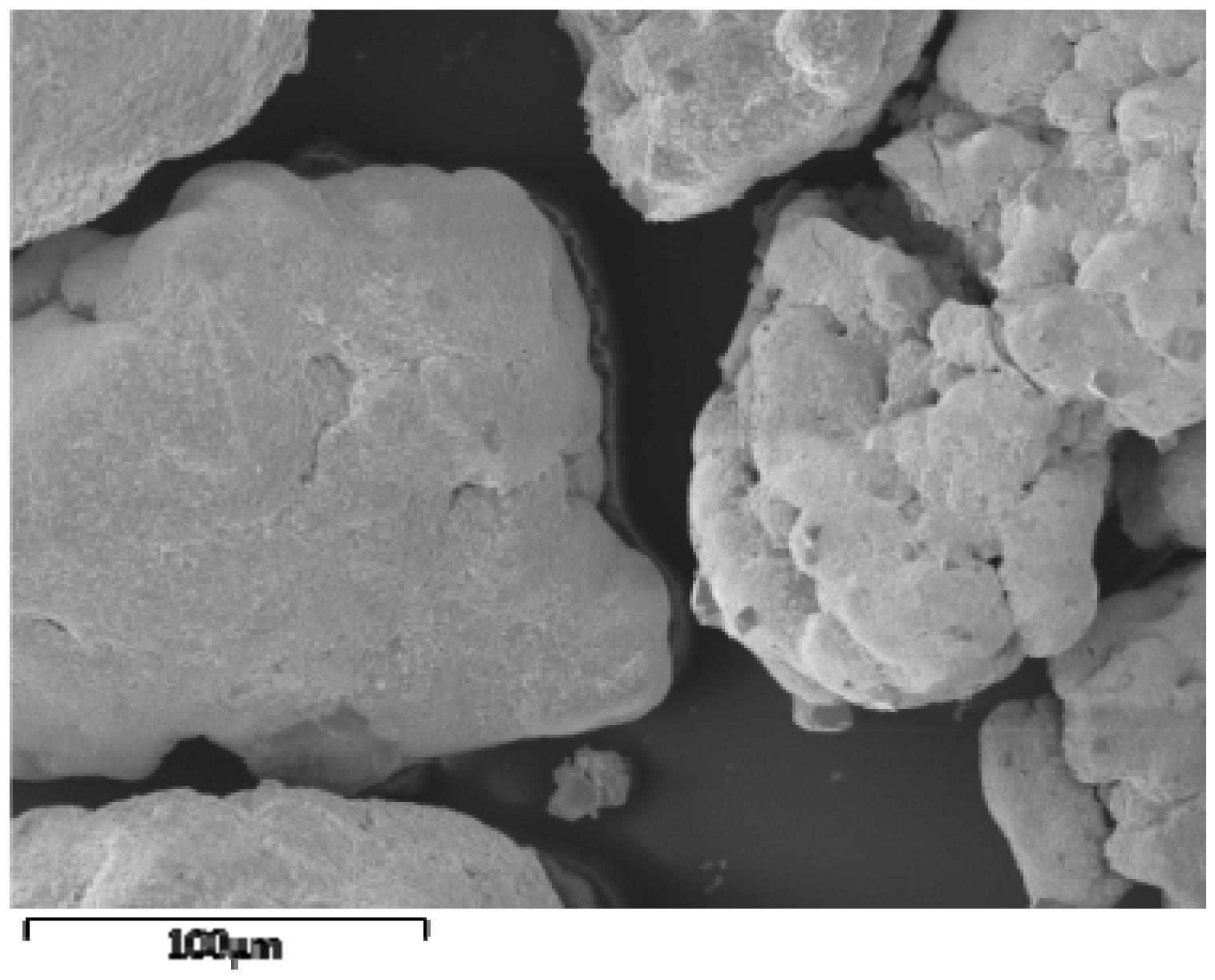
1.本发明涉及一种从酸性含砷溶液中还原脱除砷及制备金属砷的方法,属于有色金属冶金领域。
技术背景
2.砷是一种极其有害的毒性元素。生物体接触到少量含砷化合物即可发生慢性或急性中毒现象,产生诸如皮肤糜烂、呼吸粘膜炎、肝炎、肾病等症状,甚至直接死亡。研究表明,砷大量进入环境主要源于矿冶产业兴起,特别是铜、铅、锌、金、锡等有色冶炼过程,产生大量含砷废弃物。另一方面,砷的用途极其有限,这使得大量含砷废弃物得不到合理的处置,产生严重的环境污染问题和砷中毒事件。随着环保政策的日益严格,业界对含砷物料的无害化处置愈发紧迫。
3.当前,针对酸性含砷溶液中砷的脱除主要采用沉淀法和萃取法。由于萃取法仅能从溶液中分离砷,无法固化砷,因而,从砷安全处置的角度来看,沉淀法是溶液脱砷的主流方法。沉淀法大致分为钙盐沉淀法、铁盐沉淀法和硫化沉淀法。由于钙盐沉淀法需要在碱性条件下进行,加之沉淀产物砷钙渣环境稳定性较差,因而铁盐和硫化沉淀法应用更为普遍。铁盐沉淀法利用fe
3+
可与aso
43-反应生成难溶性砷酸铁的原理,通过向含砷溶液中补加铁盐来实现砷的沉淀分离。为了得到结晶良好的砷酸铁,通常需要在高温条件下进行砷的沉淀反应。硫化沉淀法以硫化钠、硫化铵等硫化物为沉淀剂,将砷转化为硫化砷沉淀。硫化沉淀过程简单,但该方法仅适合溶液成分较为简单的含砷溶液,对富含有有价金属的含砷溶液效果不佳。此外,对于酸性含砷溶液,采用硫化沉砷时,易于产生硫化氢有害气体,需多加防范。尽管铁盐和硫化沉淀法产物环境稳定性较好,但由于其反应条件较为苛刻,加之反应产物砷含量较低,沉砷渣量较大,难以满足当前废渣无害化和减量化的环保要求,因而开发高效脱砷、减量固砷的方法已成为酸性含砷溶液处理的发展趋势。
技术实现要素:4.针对现有处理酸性含砷溶液的方法存在过程复杂、产物环境稳定性不佳、产物含砷低、渣量大的不足,本发明提供了一种采用还原的方法来处理酸性含砷溶液,旨在通过还原的方法实现单质砷的制备,实现砷的深度脱除和减量固化。
5.为实现上述目的,本发明提出的一种从酸性含砷溶液中还原脱除砷及制备金属砷的方法,包括以下步骤:
6.向高压釜中依次加入酸性含砷溶液和活化剂,然后加入一定量的金属铁粉;然后密闭反应釜,开启搅拌,在大于85℃的温度下将砷还原为金属砷,其中,所述活化剂为过渡金属的可溶性盐;反应结束后,冷却过滤,所得滤渣即为金属砷产物,滤液为亚铁溶液。
7.优选地,所述酸性含砷溶液中硫酸与砷的摩尔浓度比为1.2-3.6:1。
8.优选地,所述酸性含砷溶液包括冶炼厂污酸溶液、含砷浸出液或含砷废液,酸度不超过350g/l。
9.优选地,所述过渡金属包括铜、镍、钴中的一种或多种。
10.优选地,所述活化剂的用量为溶液中砷质量的0.1-0.5%。
11.优选地,所述金属铁粉的平均粒度需大于74μm,小于300μm,且氧含量不高于0.25%。
12.优选地,所述金属铁粉的用量为砷质量的1.1-1.8倍。
13.优选地,所述金属铁粉的平均粒度越细,所需铁粉用量越多。
14.优选地,反应时间为40-90min。
15.本发明的技术构思如下:
16.本发明人经系统调研,单质砷是砷含量最高的含砷产物,因而以单质砷形式固化砷可以最大化的降低砷渣,从而实现渣的减量化;另一方面,单质砷是目前已知的化学性质最为稳定的含砷产物,因而以单质砷形式固化砷可以最大限度降低砷的危害。然而,单质砷制备较为困难,特别是从含砷溶液中制备单质砷尤为困难,且存在产生剧毒气体砷化氢的问题。为此,本发明人经过大量实验发现,在酸性含砷溶液中加入金属铁粉可以获得单质砷,但数量较少,砷主要以吸附形式脱除。经深入研究后,造成单质砷生成量较低的原因在于金属铁粉在含砷溶液中易于钝化,失去反应活性,从而抑制了砷还原的进行。为解决这一问题,我们开展了在反应体系中引入活化剂的研究,发现铜、镍、钴等过渡金属离子能够有效解决铁粉钝化问题,对铁粉还原制备单质砷反应有显著的强化作用。值得注意的是,在铁粉还原制备单质砷的过程中不会产生砷化氢。因此,在铁粉还原制备单质砷的反应体系中,通过引入铜、镍、钴等金属离子,可以强化金属铁的还原,从而实现砷深度脱除和减量固化。
17.本发明在高温酸性条件下,以金属铁粉为还原剂,将溶液中的砷还原为单质砷。为强化砷的还原,避免铁粉的钝化,在反应体系中引入铜、镍、钴等过渡金属离子,从而实现砷的深度脱除,并获得高砷含量的单质砷产物,为砷的资源化、减量化和无害化奠定基础。
18.本发明与现有技术相比较具有以下优势:
19.(1)本发明过程简单,无特殊装备要求,易于实现产业化。
20.(2)本发明原辅料消耗少,投入低,所得金属砷产物中砷含量大于99.2%,所得亚铁溶液中砷浓度低于1ppm。所得金属砷产物,既可以作为高纯砷生产原料,也可作为理想的固砷载体。
21.(3)本发明环境友好,反应过程无有害物质产出,不产生二次污染。
附图说明
22.图1为实施例1所得还原产物的sem图;
23.图2为实施例1所得还原产物的eds图;
24.图3为对比例1所得还原产物的sem图;
25.图4为对比例1所得还原产物的eds图。
具体实施方式
26.以下实施例旨在进一步说明本发明内容,而不是限制本发明权利要求保护的范围。
27.实施例1:
28.首先向高压釜中依次加入4.2l酸性含砷溶液(c
as
:21.6g/l;48g/l)和100ml硫酸铜溶液(c
cu
:3.0g/l;ph=3.2),搅拌均匀后,再加入132g金属铁粉(平均粒度127μm;氧含量0.11%)。然后密闭高压釜,搅拌加热至125℃,并保温反应50min,即可结束反应,过滤洗涤分别收集滤液和滤渣。取样分析结果表明,滤渣为砷含量超过99.5%的金属砷,滤液砷浓度不足1ppm,砷还原率高达99.9%以上。
29.对比例1:
30.首先向高压釜中依次加入4.2l酸性含砷溶液(c
as
:21.6g/l;48g/l),搅拌均匀后,再加入132g金属铁粉(平均粒度127μm;氧含量0.11%)。然后密闭高压釜,搅拌加热至125℃,并保温反应50min,即可结束反应,过滤洗涤分别收集滤液和滤渣。取样分析结果表明,滤渣为砷含量18.2%的砷铁渣,滤液砷浓度高达14.7g/l,砷还原率仅为34.96%以上。
31.对比例1与实施例1的区别在于:实施例1中加入了硫酸铜作为活化剂;而对比例1则没有使用活化剂,但实施例1中砷的还原率远高于对比例1,反应后液砷中浓度远低于对比例1,且所得还原渣砷含量明显高于对比例1。
32.图1为实施例1所得还原产物的sem图,图2为实施例1所得还原产物的eds图,图3为对比例1所得还原产物的sem图,图4为对比例1所得还原产物的eds图。
33.由图1和图2可以看出,所得产物颗粒呈规则形貌,粒径较为粗大,主要成分为砷和氧,未见铁的特征峰,由此推断,砷的还原的较为彻底,且所得产物为纯的金属砷。
34.由图3和图4可以看出,所得产物颗粒呈规则形貌,粒径分布较宽,主要成分为铁、砷和氧,由此推断,砷的还原不够彻底,产物中仍残留大量的金属铁,导致所得金属砷纯度不高。
35.实施例2:
36.首先向高压釜中依次加入4.4l酸性含砷溶液(c
as
:21.6g/l;48g/l)和100ml硫酸铜溶液(c
cu
:0.5g/l;ph=3.8),搅拌均匀后,再加入160g金属铁粉(平均粒度96μm;氧含量0.16%)。然后密闭高压釜,搅拌加热至160℃,并保温反应60min,即可结束反应,过滤洗涤分别收集滤液和滤渣。取样分析结果表明,滤渣为砷含量超过99.6%的金属砷,滤液砷浓度不足1ppm,砷还原率高达99.9%以上。
37.对比例2:
38.首先向高压釜中依次加入4.4l酸性含砷溶液(c
as
:21.6g/l;48g/l)和100ml硫酸铜溶液(c
cu
:0.5g/l;ph=3.8),搅拌均匀后,再加入160g金属铁粉(平均粒度26μm;氧含量1.28%)。然后密闭高压釜,搅拌加热至160℃,并保温反应60min,即可结束反应,过滤洗涤分别收集滤液和滤渣。取样分析结果表明,滤渣为砷含量11.5%砷铁渣,滤液砷浓度高达18.7g/l,砷还原率仅为7.6%。
39.对比例2与实施例2的区别在于:实施例2在还原过程中使用粒度较粗、氧含量较低的铁粉(96μm,0.16%),而对比例2则采用粒度较细、氧含量较高的铁粉(26μm,1.28%)作为还原剂,但两者效果相差较大,砷的还原率相差较大。铁粉粒度过细反而不利于砷的还原。
40.实施例3:
41.首先向高压釜中依次加入4.4l酸性含砷溶液(c
as
:21.6g/l;48g/l)和100ml硫酸铜溶液(c
cu
:1.2g/l;ph=3.5),搅拌均匀后,再加入140g金属铁粉(平均粒度215μm;氧含量0.07%)。然后密闭高压釜,搅拌加热至145℃,并保温反应75min,即可结束反应,过滤洗涤分别收集滤液和滤渣。取样分析结果表明,滤渣为砷含量超过99.6%的金属砷,滤液砷浓度不足1ppm,砷还原率高达99.9%以上。
42.对比例3:
43.首先向高压釜中依次加入4.4l酸性含砷溶液(c
as
:21.6g/l;48g/l)和100ml硫酸铜溶液(c
cu
:1.2g/l;ph=3.5),搅拌均匀后,再加入140g金属铁粉(平均粒度340μm;氧含量0.06%)。然后密闭高压釜,搅拌加热至145℃,并保温反应75min,即可结束反应,过滤洗涤分别收集滤液和滤渣。取样分析结果表明,滤渣为砷含量超过67.5%砷铁渣,滤液砷浓度为5.9g/l,砷还原率为71.8%。
44.对比例3与实施例3的区别在于:实施例3在还原过程中使用粒度相对较细的铁粉(平均粒度215μm;氧含量0.07%),而对比例3则采用粒度更粗大的铁粉(平均粒度340μm;氧含量0.06%)作为还原剂,但两者效果相差较大,砷的还原率相差较大。铁粉粒度过粗,活性较低,导致砷的还原率较低。
45.实施例4:
46.首先向高压釜中依次加入4.4l酸性含砷溶液(c
as
:21.6g/l;48g/l)和100ml氯化镍溶液(c
cu
:2.4g/l;ph=5.2),搅拌均匀后,再加入125g金属铁粉(平均粒度84μm;氧含量0.19%)。然后密闭高压釜,搅拌加热至150℃,并保温反应85min,即可结束反应,过滤洗涤分别收集滤液和滤渣。取样分析结果表明,滤渣为砷含量超过99.6%的金属砷,滤液砷浓度不足1ppm,砷还原率高达99.9%以上。
47.对比例4:
48.首先向高压釜中依次加入4.4l酸性含砷溶液(c
as
:21.6g/l;48g/l),150g naoh和100ml氯化镍溶液(c
ni
:2.4g/l;ph=5.2),搅拌均匀后,再加入125g金属铁粉(平均粒度84μm;氧含量0.19%)。然后密闭高压釜,搅拌加热至150℃,并保温反应85min,即可结束反应,过滤洗涤分别收集滤液和滤渣。取样分析结果表明,滤渣为砷含量21.4%的砷铁渣,滤液砷浓度为15.12g/l,砷还原/脱除率仅为28.4%。
49.对比例4与实施例4的区别在于:实施例4中未加碱调整酸度,且硫酸与砷的摩尔浓度比为1.7:1,而对比例4则在还原前先加碱调整酸度,调整后硫酸与砷的摩尔浓度比降至0.21:1。两者效果相差较大。
50.实施例5:
51.首先向高压釜中依次加入4.2l酸性含砷溶液(c
as
:13.8g/l;16g/l)、60ml浓硫酸(98%)和100ml氯化钴溶液(c
co
:1g/l;ph=5.4),搅拌均匀后,再加入96g金属铁粉(平均粒度107μm;氧含量0.13%)。然后密闭高压釜,搅拌加热至105℃,并保温反应70min,即可结束反应,过滤洗涤分别收集滤液和滤渣。取样分析结果表明,滤渣为砷含量超过99.4%的金属砷,滤液砷浓度不足1ppm,砷还原率高达99.9%以上。
52.实施例6:
53.首先向高压釜中依次加入4l酸性含砷溶液(c
as
:15.4g/l;128g/l)和100ml氯化镍溶液(c
ni
:2.8g/l;ph=5.2),搅拌均匀后,再加入108g金属铁粉(平均粒度96μm;氧含量0.16%)。然后密闭高压釜,搅拌加热至95℃,并保温反应75min,即可结束反应,过滤洗涤分别收集滤液和滤渣。取样分析结果表明,滤渣为砷含量超过99.7%的金属砷,滤液砷浓度不足1ppm,砷还原率高达99.9%以上。
54.实施例7:
55.首先向高压釜中依次加入4l酸性含砷溶液(c
as
:23.3g/l;62g/l)和100ml氯化铜溶液(c
cu
:2.0g/l;ph=3.8),搅拌均匀后,再加入136g金属铁粉(平均粒度84μm;氧含量0.21%)。然后密闭高压釜,搅拌加热至140℃,并保温反应55min,即可结束反应,过滤洗涤分别收集滤液和滤渣。取样分析结果表明,滤渣为砷含量超过99.5%的金属砷,滤液砷浓度不足1ppm,砷还原率高达99.9%以上。