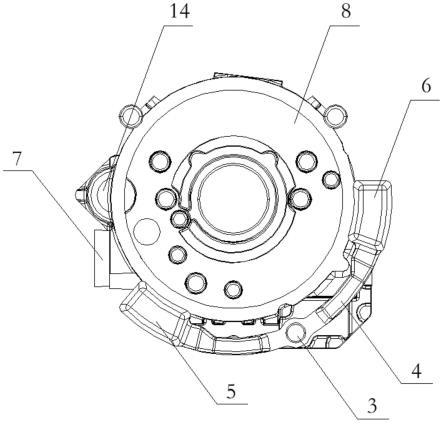
1.本发明涉及铸造技术领域,特别是涉及一种预防汽车发动机球铁飞轮壳铸件气缩孔的铸造工艺及铸造模具。
背景技术:2.由于环保和节能的需要,汽车的轻量化已经成为世界汽车发展的潮流。随着汽车质量的降低,汽车燃料的消耗也会随之降低,且汽车轮胎以及制动系统承受的压力也会降低。
3.传统的汽车发动机飞轮壳主要以灰铁ht250材质为主,随着汽车轻量化的整体要求,主机厂对发动机飞轮壳的材质进行了调整,将灰铁ht250逐步调整为球铁qt450-12。由于产品材质调整,产品强度大幅提高,因此产品壁厚就可大幅下降,铸件重量也随之降低,为汽车整体的节本降耗奠定了基础。
4.由于灰铁和球铁的铁液充型凝固属性是不同的,灰铁为层状凝固,收缩率相对小,而球铁为糊状凝固,不利于补缩,且球铁的收缩率大,这就导致球铁产品在几何热节处易出现气缩孔缺陷。
技术实现要素:5.本发明所要解决的技术问题是,克服现有技术的缺点,提供一种预防汽车发动机球铁飞轮壳铸件气缩孔的铸造工艺及铸造模具。
6.为了解决以上技术问题,本发明的技术方案如下:一种预防汽车发动机球铁飞轮壳铸件气缩孔的铸造模具,包括外型上型板模、外型底型板模和浇注系统,所述外型上型板模与所述外型底型板模通过砂箱和湿型砂载体对接形成型腔,所述浇注系统与所述型腔连通,所述型腔内设置有用于放置覆膜砂芯的第一放置腔,所述浇注系统包括直浇道、与直浇道连通的横浇道以及连通在横浇道上的第一补缩冒口和第二补缩冒口,所述第一补缩冒口和所述第二补缩冒口与铸件相邻的几何热节之间的弧心角为25度,且所述第一补缩冒口和所述第二补缩冒口与铸件马达孔之间的弧心角大于相邻的几何热节与铸件马达孔之间的弧心角。
7.作为本发明所述预防汽车发动机球铁飞轮壳铸件气缩孔的铸造模具的一种优选方案,其中:所述覆膜砂芯上开设有用于放置冷铁的第二放置腔。
8.作为本发明所述预防汽车发动机球铁飞轮壳铸件气缩孔的铸造模具的一种优选方案,其中:所述冷铁位于铸件几何热节对应的铸件面处。
9.作为本发明所述预防汽车发动机球铁飞轮壳铸件气缩孔的铸造模具的一种优选方案,其中:所述冷铁的形状与相邻几何热节的铸件面形状相适配。
10.作为本发明所述预防汽车发动机球铁飞轮壳铸件气缩孔的铸造模具的一种优选方案,其中:所述冷铁与相邻几何热节之间的接触面面积大于相邻几何热节面积的80%。
11.作为本发明所述预防汽车发动机球铁飞轮壳铸件气缩孔的铸造模具的一种优选方案,其中:还包括用于制作所述覆膜砂芯的热芯盒组件,所述热芯盒组件包括相对设置的热芯盒定模和热芯盒动模,所述热芯盒定模与所述热芯盒动模对接形成用于制作覆膜砂芯的型腔。
12.本发明还公开了一种预防汽车发动机球铁飞轮壳铸件气缩孔的铸造工艺,包括,以飞轮壳上平面为分型面,制作外型上型板模、外型底型板模以及配套的砂箱;根据飞轮壳铸件的形状制造热芯盒组件,并通过热芯盒组件制作所需的覆膜砂芯;将砂箱设置于外型上型板模上,加入潮模砂,震实压紧,脱开外型上型板模,砂箱和潮模砂形成上型腔;将砂箱设置于外型底型板模上,加入潮模砂,震实压紧,脱开外型底型板模,砂箱和潮模砂形成下型腔;将制作好的冷铁放置在覆膜砂芯的第二放置腔中,将覆膜砂芯放置在潮模砂下型腔的第一放置腔内,然后将上型腔与下型腔采用定位长销对接后卡紧,形成型腔;将铁液通过浇注系统浇注进型腔内,浇注结束后冷却,然后用震动落砂将铸件与型砂分离,得到铸件。
13.作为本发明所述预防汽车发动机球铁飞轮壳铸件气缩孔的铸造工艺的一种优选方案,其中:浇注结束后的冷却时间为30~60min。
14.作为本发明所述预防汽车发动机球铁飞轮壳铸件气缩孔的铸造工艺的一种优选方案,其中:浇注时间为18~22s。
15.本发明的有益效果是:(1)本发明在铸件的几何热节处设置补缩冒口,有效避免了浇注系统补缩冒口颈充型时对热节进行预热,即预防间接形成接触热节,且补缩冒口在铸件充型凝固过程中可对铸型内铁液液态收缩和第一次体收缩进行瞬时补给,有效避免了铸件内部形成气缩孔缺陷。
16.(2)本发明在铸件的几何热节处设置有冷铁,将易形成缩孔缩松缺陷的热节点外移,使其逼近补缩冒口的作用范围,从而在浇注成型过程辅助消除球铁飞轮壳铸件气缩孔缺陷。
17.(3)本发明通过设计冷铁的合理厚度,保证厚实热节处与薄壁处金属液同时冷却,使球铁飞轮壳金属液充型时铸件壁薄与壁厚处达到同时均衡凝固,从而获得整体组织致密均匀的优质铸件。
附图说明
18.为了更清楚地说明本发明实施例的技术方案,下面将对实施例描述中所需要使用的附图作简单地介绍,显而易见地,下面描述中的附图仅仅是本发明的一些实施例,对于本领域普通技术人员来讲,在不付出创造性劳动性的前提下,还可以根据这些附图获得其它的附图。
19.图1为本发明提供的预防汽车发动机球铁飞轮壳铸件气缩孔的铸造模具中外型上型板模的结构示意图;
图2为本发明提供的预防汽车发动机球铁飞轮壳铸件气缩孔的铸造模具中外型底型板模的结构示意图;图3为本发明提供的预防汽车发动机球铁飞轮壳铸件气缩孔的铸造模具中覆膜砂芯组合的结构示意图;图4为本发明提供的预防汽车发动机球铁飞轮壳铸件气缩孔的铸造模具中浇注系统与铸件的模拟工艺图;图5为传统铸造模具中浇注系统与铸件的模拟工艺图;图6为本发明提供的预防汽车发动机球铁飞轮壳铸件气缩孔的铸造模具铸造出的铸件的结构示意图;图7为本发明提供的预防汽车发动机球铁飞轮壳铸件气缩孔的铸造工艺的流程示意图;其中:1、外型上型板模;2、外型底型板模;3、直浇道;4、横浇道;5、第一补缩冒口;6、第二补缩冒口;7、冷铁;8、铸件;9、第一补砂芯;10、第二补砂芯;11、第三补砂芯;12、第四补砂芯;13、内腔大圆芯;14、马达孔。
具体实施方式
20.为使本发明的内容更容易被清楚地理解,下面根据具体实施方式并结合附图,对本发明作出进一步详细的说明。
21.图1~图4为本技术实施例提供的预防汽车发动机球铁飞轮壳铸件气缩孔的铸造模具的结构示意图。该铸造模具包括外型上型板模1、外型底型板模2和浇注系统。
22.具体的,参见图1和图2,外型上型板模1和外型底型板模2上分别开设有与铸件8相匹配的外型上模型块和外型底模型块。外型上型板模1与外型底型板模2对接后,外型上模型块与外型底模型块对接,在外型上型板模1与外型底型板模2之间形成型腔。
23.在型腔内设置有用于放置覆膜砂芯的第一放置腔。其中,覆膜砂芯由热芯盒组件制成。热芯盒组件包括热芯盒定模和热芯盒动模。热芯盒定模与热芯盒动模之间形成与覆膜砂芯形状相适配的型腔。在本实施例中,根据飞轮壳铸件8的侧面根据铸造成型需要,设计有三组热芯盒组件,分别为第一热芯盒组件、第二热芯盒组件以及第三热芯盒组件。第一热芯盒组件可制造出第一补砂芯9和第三补砂芯11,第二热芯盒组件可制造出第二补砂芯10和第四补砂芯12。第三热芯盒可制造出覆膜砂内腔大圆芯13。四个补砂芯按照图3的顺序组合,形成飞轮壳铸件8的侧面形状。覆膜砂内腔大圆芯13按照设计要求,即图3,下落至规定位置,形成铸件8的内腔。
24.较佳的,在第二补砂芯10和第四补砂芯12上开设有第二放置腔,可放置冷铁7。
25.浇注系统与模腔连通。浇注系统具体包括直浇道3、与直浇道3连通的横浇道4以及分别连通在横浇道4上的第一补缩冒口5和第二补缩冒口6。参见图4,横浇道4呈圆弧状,且其形状与铸件8的侧面形状相适配。在横浇道4上开设有直浇口3,铁液可通过直浇口3进入横浇道4内。第一补缩冒口5和第二补缩冒口6均与横浇道4连通。其中,第一补缩冒口5和第二补缩冒口6均位于铸件8的几何热节附近处。
26.传统的铸造模具中,补缩冒口直接位于几何热节的上部,在浇注时,金属液流长时间对几何热节处预热,导致该铸件8几何热节金属液充型后凝固时间更加延长,加之球铁为
糊状凝固,补缩冒口根部壁厚只有5-7mm,充型完成后,根部在几何热节凝固之前基本凝固,导致补缩通道堵塞,热节处气体无法外溢,同时几何热节处金属液凝固形成体收缩,也由于补缩通道堵塞浇冒口系统无法对铸件8热节进行金属液补偿,导致热节处形成气缩孔缺陷。而本实施例中,第一补缩冒口5与铸件8上相邻的几何热节之间的弧心角为25度,第二补缩冒口6与铸件8上相邻的几何热节之间的弧心角也为25度,且第一补缩冒口5与铸件8马达孔14之间的弧心角大于与第一补缩冒口5相邻的几何热节与铸件8马达孔14之间的弧心角,第二补缩冒口6与铸件8马达孔14之间的弧心角大于与第二补缩冒口6相邻的几何热节与铸件7马达孔14之间的弧心角。图5为原铸造工艺中浇注系统与铸件8的位置示意图,通过对比可知,本实施例提供的铸造模具中的两个补缩冒口和整体浇注系统是通过将传统铸造模具的补缩冒口位置和整体浇注系统以飞轮壳中心孔轴为参照点(离开马达孔14的方向)逆时针旋转25度得到,这样调整后有效避免了浇注系统补缩冒口颈充型时对热节进行预热,即预防间接形成接触热节。
27.需要说明的是,上述设计充分利用了金属充型模拟软件找出该类结构球铁铸件8铁液充型补缩的合理位置,在铸件8充型凝固过程中浇冒口系统可对铸型内铁液液态收缩和第一次体收缩进行瞬时补给。充型结束球铁石墨膨胀时热冒口的冒口颈封闭,利用铁液石墨膨胀来形成自补缩。该工艺系统设计最大限度的满足铁液充型凝固过程中运用浇冒口工艺系统对汽车球铁飞轮壳体内部热节的铁液补充和飞轮壳壳体铸件8凝固过程中石墨膨胀时冒口筋形成自封闭,利用石墨膨胀压力对铸件8的热节部分进行补缩,为预防铸件8形成气缩孔缺陷做好基础预防。
28.另外,本实施例中,在铸件8易形成气缩孔缺陷的两个对称的几何热节部位设计了随形的对应冷铁7,且该热节处的冷铁7设计在第二补砂芯10和第四补砂芯12上,即冷铁7放置在第二补砂芯10和第四补砂芯12上的第二放置腔内。冷铁7没有补偿收缩作用,但冷铁7有转移铸件8的几何热节之作用。放置冷铁7的目的是将易形成缩孔缩松缺陷热节点外移使其逼近冒口的作用范围,利用冷铁7在浇注成型过程中辅助消除球铁飞轮壳铸件8气缩孔缺陷。
29.需要说明的是,冷铁7要与铸件8几何热节部位形状的相吻合,这样可保证足够接触面,从而保证冷却效果。其中,冷铁7与相邻几何热节之间的接触面面积为相邻几何热节面积的80%以上。同时,冷铁7的厚度提前设定,即通过模拟软件模拟保证厚实热节处与薄壁处金属液同时冷却。在本实施例中,设计该铸件冷铁的厚度为30~35mm,使球铁飞轮壳金属液充型时铸件8壁薄与壁厚处达到同时均衡凝固,从而获得整体组织致密均匀的优质铸件8。
30.图7为本技术实施例提供的预防汽车发动机球铁飞轮壳铸件气缩孔的铸造工艺的流程示意图。该铸造工艺包括步骤s101~步骤s106,具体步骤说明如下:步骤s101:以飞轮壳上平面为分型面,制作外型上型板模1、外型底型板模2以及配套的砂箱。
31.步骤s102:根据飞轮壳铸件的形状制造热芯盒组件,并通过热芯盒组件制作所需的覆膜砂芯。
32.步骤s103:将砂箱设置于外型上型板模1上,加入潮模砂,震实压紧,脱开外型上型板模1,砂箱和潮模砂形成上型腔。
33.步骤s104:将砂箱设置于外型底型板模2上,加入潮模砂,震实压紧,脱开外型底型板模2,砂箱和潮模砂形成下型腔。
34.步骤s105:将制作好的冷铁放置在覆膜砂芯的第二放置腔中,将覆膜砂芯放置在潮模砂下型腔的第一放置腔内,并按照图3所示的顺序排布,然后将上型腔与下型腔采用定位长销对接后卡紧,形成型腔。
35.具体的,在冷铁7放置在在第二补砂芯10和第四补砂芯12上的第二放置腔内。第二补砂芯10和第四补砂芯12放置在型腔内后,冷铁7位于铸件8的几何热节部位。
36.步骤s106:将铁液通过浇注系统浇注进型腔内,浇注结束后冷却,然后用震动落砂将铸件8与型砂分离,得到铸件8。
37.具体的,在进行浇注时,浇注的时间控制在18~22s,保证浇注过程中铁液整体的温度符合浇注要求。在浇注结束后,冷却45~60min,保证铸件8冷却完毕。
38.通过上述铸造工艺生产出的铸件8经过电镜检查和试压验证解剖查看,不管在铸件8较厚实部位还是铸件8的其他部位均没有发现有气缩孔缺陷现象。通过若干次的工艺验证,证明了上述铸造工艺有效解决了铸件8气缩孔缺陷,且该工艺不会因铁液化学成分的波动再出现气缩孔、缩松导致的铸造缺陷现象。
39.除上述实施例外,本发明还可以有其他实施方式;凡采用等同替换或等效变换形成的技术方案,均落在本发明要求的保护范围。