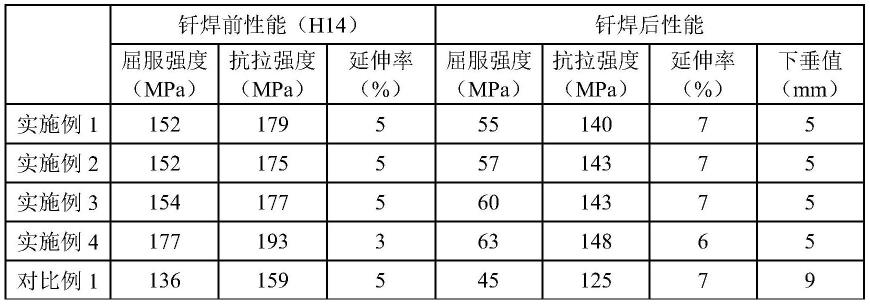
1.本发明属于铝合金材料技术领域,具体涉及一种高强自钎焊铝合金材料及其制备方法。
背景技术:2.铝合金由于其较高的比强度、优异的传热性能、丰富的储量和较低的成本等特点,在热交换器领域得到了广泛的应用,热交换器的全铝化已成为发展的必然趋势。钎焊铝热交换器,例如散热器、冷凝器、蒸发器等,通常用于汽车发动机冷却系统或空气调节系统以及工业冷却系统。
3.为实现翅片和基板(或管料)的钎焊,翅片或基板(管料)中的一种需要采用复合材料,即在al-mn铝合金的一侧或两侧通过轧制复合包覆一层用作钎料的al-si合金。轧制复合生产工艺相对复杂、流程长,材料成材率较低,生产成本较高。而且,铝热交换器的轻薄化发展要求材料不断减薄,材料的减薄给复合轧制包覆率的控制带了很大的困难和挑战。
4.传统的可控气氛钎焊技术大都采用钎剂去除母材和钎料表面的氧化膜,促进钎料的润湿铺展,从而实现大气环境下的钎焊。铝热交换器的轻薄化、小型化使得钎剂涂覆和清除更为困难,涂覆不良会影响钎焊效果和产品的使用性能,严重时造成钎焊报废。同时,材料的减薄和热交换器高效化对材料的耐腐蚀性提出了更高的要求,钎剂残留会影响产品的清洁度,降低材料的耐腐蚀性能。
5.专利zl201380076617.5、zl201410667590.3、cn201780023251.3公开了在使用钎剂条件下,单层具有加热接合功能的铝合金材及其制造方法。上述技术公开的si、fe、zn、cu等元素含量范围很宽,在si、fe等元素较高含量时,合金的熔点会降低至接近常用钎焊温度,而使这类合金钎焊后易出现完全熔蚀风险,丧失承力要求。
6.专利cn201910124774.8公开了一种无焊层钎焊用铝合金散热材料及其制备方法。该技术公开的si元素含量也过宽,较高的si含量易使合金钎焊出现完全坍塌的风险,且该合金mg:≤0.05wt%,主要适用于有钎剂的气体保护焊领域。
7.专利cn202011108161.4公开了一种自钎焊铝合金箔材及其制造方法。该技术公开的si含量为2.1-2.3wt%,si含量偏低,钎焊时形成用于钎焊接合的液相偏少,不利于保证结合强度。
技术实现要素:8.针对现有技术的不足,本发明提供一种高强自钎焊铝合金材料及其制备方法,本发明制备的铝合金材料不需包覆钎料层,在钎焊温度下未涂覆钎剂的单层合金形成有部分液相起到接合作用,该铝合金材料具有良好的拉伸性能、抗下垂性能和高温力学性能,可用于加工成翅片、基板或管料制造热交换器。
9.本发明采用以下技术方案:
10.一种高强自钎焊铝合金材料,其特征在于:所述铝合金材料的组分及其质量百分
含量为:si:2.5%~3.0%、mn+fe:1.3%~1.9%、mg:0.3%~0.6%、zr+er:0.3%~0.6%、bi:0.1%~0.15%、余量为al和不可避免的杂质;其中,mn与fe的质量比大于等于2,er与zr的质量比为2~3。
11.根据上述的高强自钎焊铝合金材料,其特征在于:所述铝合金材料的组分还包括zn、ti中的一种或两种,其中,zn的质量百分含量小于等于2%,ti的质量百分含量小于等于0.1%。
12.一种基于上述的高强自钎焊铝合金材料的制备方法,其特征在于:所述制备方法包括以下步骤:
13.(1)将所述铝合金材料制备成铝合金带坯;
14.(2)对铝合金带坯进行一次冷轧,得到铝合金带材;
15.(3)将铝合金带材以5℃/s~100℃/s的加热速率升温到350℃~500℃保温5s~180s,再以5℃/s~200℃/s的冷却速率冷却到100℃以下,进行二次冷轧后再以30℃/h~70℃/h的加热速率升温至300℃~480℃保温0.5h~10h,得到热处理后的铝合金带材;
16.(4)或者将铝合金带材以30℃/h~70℃/h的加热速率升温到300℃~480℃保温0.5h~10h,进行二次冷轧后以5℃/s~100℃/s的加热速率升温到350℃~500℃保温5s~180s,再以5℃/s~200℃/s的冷却速率冷却到100℃以下,得到热处理后的铝合金带材;
17.(5)对步骤(3)或步骤(4)得到的热处理后的铝合金带材进行冷轧,获得成品材料。
18.根据上述的高强自钎焊铝合金材料的制备方法,其特征在于:步骤(2)中对铝合金带坯进行一次冷轧的总加工率控制在70%~90%,步骤(5)中对热处理后的铝合金带材进行冷轧的总加工率控制在15%~35%。
19.根据上述的高强自钎焊铝合金材料的制备方法,其特征在于:步骤(3)中将铝合金带材以5℃/s~100℃/s的加热速率升温到350℃~500℃保温5s~180s,再以5℃/s~200℃/s的冷却速率冷却到100℃以下,进行二次冷轧的总加工率控制在50%~96%。
20.根据上述的高强自钎焊铝合金材料的制备方法,其特征在于:步骤(4)中将铝合金带材以30℃/h~70℃/h的加热速率升温到300℃~480℃保温0.5h~10h,进行二次冷轧的总加工率控制在50%~95%。
21.根据上述的高强自钎焊铝合金材料的制备方法,其特征在于:步骤(1)中将所述铝合金材料制备成铝合金带坯的制备方式为双辊连续铸轧方式、双带连铸连轧方式、半连铸加热轧方式中的一种。
22.根据上述的高强自钎焊铝合金材料的制备方法,其特征在于:步骤(1)中将所述铝合金材料制备成铝合金带坯的制备方式为双辊连续铸轧方式时,铸轧温度为680℃~730℃,铸造速度为500mm/min~1500mm/min,板坯厚度为2mm~10mm。
23.与现有技术相比,本发明的技术方案具有以下有益效果:
24.(1)本发明通过er、zr的复合添加,在退火过程中形成细小均匀分布的al3(erzr)核壳结构复合相,起到弥散强化作用,强化钎焊材料的强度;并有利于钎焊过程中形成粗大的长条状晶粒组织,减少熔蚀的扩散通道,提高钎焊抗下垂性能;同时添加bi元素增加si液相对铝材表面的润湿性,改善焊接性能。
25.(2)本发明采用快速加热、高温短时+中高温长时保温二次热处理组合工艺,可以最大程度地减少合金中的粗大化合物,同时保证有更多的细小弥散相存在,以提高合金的
钎焊前后拉伸性能和钎焊抗下垂性能。
26.(3)本发明铝合金材料的al3(erzr)核壳结构复合相能够强化钎焊材料的强度,减薄材料厚度,有利于轻量化;同时具有较高的热稳定性,有利于提高热交换器的工作温度;同时本发明通过添加mg元素,实现无钎剂的钎焊,保护环境,及通过组合热处理工艺促进焊后屈服强度;相比现有技术可以使焊后屈服强度提高10mpa以上。
具体实施方式
27.本发明的一种高强自钎焊铝合金材料,组分及其质量百分含量为:si:2.5%~3.0%、mn+fe:1.3%~1.9%、mg:0.3%~0.6%、zr+er:0.3%~0.6%、bi:0.1%~0.15%、余量为al和不可避免的杂质;其中,mn与fe的质量比大于等于2,er与zr的质量比为2~3。铝合金材料的组分还包括zn、ti中的一种或两种,其中,zn的质量百分含量小于等于2%,ti的质量百分含量小于等于0.1%。
28.本发明的高强自钎焊铝合金材料,是以si、fe、mn、mg、er、zr、bi等元素在特定含量范围内,余量由al和不可避免的杂质组成的。
29.(1)si:2.5~3.0wt%
30.本发明的高强自钎焊铝合金材料中si的质量百分含量为2.5%~3.0%。si能在合金中形成一定数量的低熔点共晶si相,可在钎焊温度下熔化形成液相,起到接合的作用,而无需包覆钎料层。si含量<2.5wt%,在610℃以下温度钎焊时,形成的液相不足,造成接合系数偏低,需要使用更高的钎焊温度,如此会带来其他不利影响。si含量>3wt%,会造成合金熔点严重降低,在610℃钎焊时,合金存在部分熔化风险,导致合金强度严重降低或坍塌,需要对钎焊温度控制要求提高,不利于操作。
31.(2)mn+fe:1.3~1.9wt%且mn/fe≥2
32.本发明的高强自钎焊铝合金材料中mn+fe的质量百分含量为1.3%~1.9%且mn与fe的质量比大于等于2。合金中加入mn、fe元素,保证铝合金板具有较高的强度、延伸率;同时控制mn+fe含量以及mn/fe比,一是调控mn、fe与si形成的化合物数量,降低对共晶si形成数量的不利影响,二是防止形成粗大的含fe相,避免对成形、拉伸性能的不利影响。
33.(3)mg:0.3~0.6%,bi:0.1~0.15%
34.本发明的高强自钎焊铝合金材料中mg的质量百分含量为0.3%~0.6%,bi的质量百分含量为0.1%~0.15%。通过添加mg元素,利用钎焊过程中mg的氧化、蒸发,破除铝材表面的氧化膜,促使合金内的si液相可流动到材料表面外部用于接合,达到无钎剂钎焊目的;同时添加bi元素增加si液相对铝材表面的润湿性,促进si液相的流动性来改善焊接性能。元素含量偏低,达不到上述效果;元素含量偏高,对进一步提高效果作用有限,并会带来成本增加。
35.(4)zr+er:0.3~0.6%且er/zr:2~3
36.本发明的高强自钎焊铝合金材料中zr+er的质量百分含量为0.3~0.6%,er与zr的质量比为2~3。通过er、zr的复合添加,可在退火过程中形成细小均匀分布的弥散相,钉轧晶界,起到弥散强化作用;同时可阻碍再结晶,有利于钎焊过程中形成粗大的长条状晶粒组织,减少熔蚀的扩散通道,提高钎焊抗下垂性能;al(erzr)复合相具有较高的热稳定性,保证合金较高温度下的强度,有利于提高热交换器的工作温度。
37.本发明基于高强自钎焊铝合金材料的制备方法,包括以下步骤:
38.(1)将所述铝合金材料制备成铝合金带坯;将铝合金材料制备成铝合金带坯的制备方式为双辊连续铸轧方式、双带连铸连轧方式、半连铸加热轧方式中的一种。将铝合金材料制备成铝合金带坯的制备方式为双辊连续铸轧方式时,铸轧温度为680℃~730℃,铸造速度为500mm/min~1500mm/min,板坯厚度为2mm~10mm。
39.(2)对铝合金带坯进行一次冷轧,得到铝合金带材;对铝合金带坯进行一次冷轧的总加工率控制在70%~90%
40.(3)将铝合金带材以5℃/s~100℃/s的加热速率升温到350℃~500℃保温5s~180s,再以5℃/s~200℃/s的冷却速率冷却到100℃以下,进行二次冷轧后再以30℃/h~70℃/h的加热速率升温至300℃~480℃保温0.5h~10h,得到热处理后的铝合金带材;进行二次冷轧的总加工率控制在50%~96%。
41.(4)或者将铝合金带材以30℃/h~70℃/h的加热速率升温到300℃~480℃保温0.5h~10h,进行二次冷轧后以5℃/s~100℃/s的加热速率升温到350℃~500℃保温5s~180s,再以5℃/s~200℃/s的冷却速率冷却到100℃以下,得到热处理后的铝合金带材;进行二次冷轧的总加工率控制在50%~95%。
42.(5)对步骤(3)或步骤(4)得到的热处理后的铝合金带材进行冷轧,获得成品材料。对热处理后的铝合金带材进行冷轧的总加工率控制在15%~35%。
43.对本发明高强自钎焊铝合金材料的制备方法进行说明如下:
44.(1)一次冷轧
45.总加工率控制在70%~90%,可以促进粗大化合物的破碎,利于提高合金延性,同时可促使共晶硅相分布更均匀,有助于后续钎焊液相均匀分布。
46.(2)退火
47.以30℃/h~70℃/h的速率升温至300℃~480℃并保温0.5h~10h,可以促使alerzr、almnsi弥散相的析出,提高合金的拉伸性能、抗下垂性能和耐热性能。
48.以5℃/s~100℃/s的加热速率升温到350℃~500℃保温5s~180s,然后以5℃/s~200℃/s的速度冷却到100℃以下,可以促进mg2si的回溶,提高mg元素的固溶,有利于合金的强度、钎焊,同时控制弥散相的长大,使钎焊时成形尺寸合适的晶粒,调控合适的晶界数量,保证钎焊过程中有足够的si液相能沿晶界扩散到表面进行接合。
49.(4)最终冷轧
50.总加工率控制在15%~35%,调控变形储能,结合第二相分布控制,利于钎焊时形成拉长且尺寸合适的晶粒,保证钎焊性能和抗下垂性能。
51.下面结合具体实施例对本发明的技术方案作进一步详细说明,此处所描述的具体实施例仅用于解释本发明,但不作为对本发明技术方案的限定。
52.实施例1-4、对比例1所采用的铝合金材料的组分及其质量百分含量见表1。
53.表1铝合金材料成分及其质量百分含量(wt%)
[0054] femnsimgbizner+zral实施例10.21.12.50.30.11.50.3余量实施例20.41.52.70.40.151.50.5余量实施例30.21.13.00.50.11.50.4余量
实施例40.31.33.00.60.100.5余量对比例10.21.12.50.30.11.50余量
[0055]
实施例1
[0056]
对表1中实施例1所给的合金成分的6mm厚度带坯进行一次冷轧到0.6mm(总加工率为90%),冷轧结束后进行一次退火:以30℃/h的速率升温至450℃并保温0.5h;退火后带材二次冷轧到0.15mm厚度后进行第二次退火:以15℃/s的加热速率升温到350℃保温60s,然后以不低于20℃/s的速度冷却到100℃以下;对退火带材进行最终冷轧至0.1mm,加工率为33.3%。实施例1所得产品的性能见表2。
[0057]
实施例2
[0058]
对表1中实施例2所给的合金成分的6mm厚度带坯进行一次冷轧到1.8mm(总加工率为70%),冷轧结束后进行一次退火:以100℃/s的加热速率升温到500℃保温5s,然后以不低于20℃/s的速度冷却到100℃以下;退火后带材二次冷轧到0.118mm厚度后进行第二次退火:以70℃/h的速率升温至300℃并保温3h;对退火带材进行最终冷轧至0.1mm,加工率为15%。实施例2所得产品的性能见表2。
[0059]
实施例3
[0060]
对表1中实施例3所给的合金成分的6mm厚度带坯进行一次冷轧到1.8mm(总加工率为70%),冷轧结束后进行一次退火:以55℃/s的加热速率升温到400℃保温30s,然后以不低于20℃/s的速度冷却到100℃以下;退火后带材二次冷轧到0.134mm厚度后进行第二次退火:以50℃/h的速率升温至400℃并保温1.5h;对退火带材进行最终冷轧至0.1mm,加工率为25%。实施例3所得产品的性能见表2。
[0061]
实施例4
[0062]
对表1中实施例4所给的合金成分的6mm厚度带坯进行一次冷轧到1.2mm(总加工率为80%),冷轧结束后进行一次退火:以50℃/s的加热速率升温到450℃保温20s,然后以不低于20℃/s的速度冷却到100℃以下;退火后带材二次冷轧到0.143mm厚度后进行第二次退火:以60℃/h的速率升温至380℃并保温2.5h;对退火带材进行最终冷轧至0.1mm,加工率为20%。实施例4所得产品的性能见表2。
[0063]
对比例1
[0064]
对表1中对比例1所给的合金成分的6mm厚度带坯进行一次冷轧到0.6mm(总加工率为90%),冷轧结束后进行一次退火:以30℃/h的速率升温至450℃并保温0.5h;退火后带材二次冷轧到0.15mm厚度后进行第二次退火:以15℃/s的加热速率升温到350℃保温60s,然后以不低于20℃/s的速度冷却到100℃以下;对退火带材进行最终冷轧至0.1mm,加工率为33.3%。对比例1所得产品的性能见表2。
[0065]
表2合金性能
[0066][0067]
以上实施例1-4制备出合金的性能如表2所列,相比对比例1(现有技术),实施例1-4合金钎焊后具有高的强度(焊后屈服强度≥55mpa),良好的抗下垂性能(610℃保温15min,下垂值≤8mm),钎焊后晶粒长轴达到1mm以上;进一步加工成翅片可与板料、管料在不使用钎剂钎焊条件下实现良好的接合。
[0068]
以上实施例仅用于说明本发明的技术方案而非对其进行限制,所属领域的普通技术人员应当理解,参照上述实施例可以对本发明的具体实施方式进行修改或者等同替换,这些未脱离本发明精神和范围的任何修改或者等同替换均在本发明的权利要求保护范围之内。