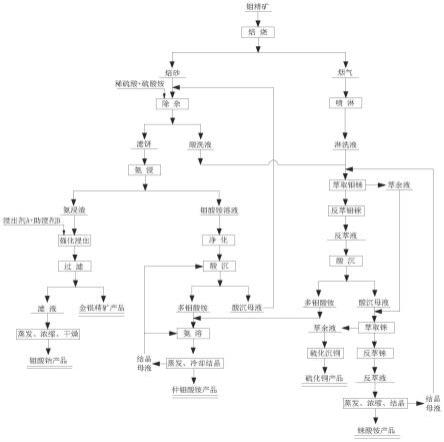
1.本发明属于冶金领域,尤其涉及一种从高铜钼精矿中综合回收稀贵金属的方法。
背景技术:2.铜钼矿经过混合浮选、铜钼分离系统后产出两种产品:铜精矿和钼精矿。铜精矿销售给铜冶炼厂,金银等贵金属均有按含量进行计价,其伴生的稀贵金属经过熔炼和电解后在阳极泥中富集,阳极泥再经过处理工艺回收各类稀贵金属。然而钼精矿销售时,金银等稀贵金属均无计价,其中的铼、金、银、铜均有较高的价值,但是传统的钼精矿冶炼处理工艺氨浸渣中钼含量高,达到约9%,稀贵金属回收率低、工艺流程长、成本高,而且废水中含有硝态氮不利于回收的利用,还会产生二次环境污染等问题。
技术实现要素:3.为解决上述现有技术中钼精矿焙烧处理后酸洗预处理液中钼含量高,氨浸渣钼含量高,工艺流程长、生产成本高、废水中含有硝态氮的问题,本发明提供了一种从高铜钼精矿中综合回收稀贵金属的方法。
4.本发明的技术方案:一种从高铜钼精矿中综合回收稀贵金属的方法,所述方法包括如下步骤:
5.(1)钼精矿焙烧,焙烧温度为500-700℃,焙烧后对烟气进行淋洗净化;
6.(2)酸洗除杂,调节酸液的ph为0.3-0.5,液固比为3:1-4:1;
7.(3)氨浸,采用氨水浸出,浸出时间60-90min;
8.(4)酸沉;酸沉时的温度为40-45℃,酸沉终点ph为1.5-2.5,得到多钼酸铵;酸沉母液返回步骤(2)中再次进行酸洗;
9.(5)采用氨水将步骤(4)得到的多钼酸铵进行溶解,按多钼酸铵:水:氨水=1:0.4:0.5的比例溶解,过滤,将过滤后的溶液进行煮沸蒸发浓缩,冷却结晶过滤后得到仲钼酸铵产品;
10.(6)钼的回收,酸洗液和烟气淋洗液中钼的回收,采用n235、仲辛醇、煤油有机混合相萃取钼;
11.(7)铼的回收,将步骤(6)中的酸沉过滤液和萃余液采用n235、仲辛醇、煤油有机混合相萃取铼;
12.(8)铜的回收,将步骤(7)中的铼萃余液通过硫化沉铜的方式进行回收。
13.所述步骤(1)中烟气进行淋洗净化前温度为300℃以上。
14.所述步骤(3)中氨浸液固比为4:1-5:1,温度为50-55℃,氨水用量为理论用量的1.2-1.3倍。
15.所述步骤(3)中在完成浸出后,调节溶液ph为8.0-8.5,以1g/100ml的比例加入活性炭,搅拌,过滤出活性炭,缓慢加入硫化铵,硫化铵的加入量为理论消耗量的2倍。
16.所述步骤(5)中结晶母液返回步骤(4)酸沉或步骤(5)多钼酸铵溶解的程序中回收
其中的钼。
17.所述步骤(2)采用稀硫酸进行酸浸除杂,在稀硫酸中加入100g/l的nh4so4,酸洗温度为80-90℃,酸洗时间90-120min。
18.所述步骤(6)的萃取过程中,萃取液n235、仲辛醇、煤油的体积比为2:1:7,萃取相比o:a=2:1,;以6mol/l氨水反萃,反萃相比o:a=1:2,反萃液加入硫酸酸化酸沉得到多钼酸铵,酸沉条件与步骤(4)相同,重复步骤(5)的操作,用以得到仲钼酸铵产品。
19.所述步骤(7)中萃取过程中,萃取液n235、仲辛醇、煤油的体积比为0.5:8:11.5,萃取相比o:a=2:1;以6mol/l氨水反萃,反萃相比o:a=1:2;反萃液在煮沸状态下蒸发浓缩至铼含量在15g/l以上,于-4℃冷却结晶得到铼酸铵产品;结晶母液返回步骤(6)中钼萃取的步骤中。
20.所述步骤(6)、步骤(7)萃取操作进行前调节有机相ph值为1。
21.所述步骤(5)完成后,进行氨浸渣强化浸出,氨浸渣采用浸出剂与助浸剂联合强化浸出,浸出温度80-100℃,浸出时间1.5-2.5小时,浸出剂浓度10-20g/l,用量为理论用量的1.2倍,助浸剂用量为浸出剂用量的10-20%,浸出液过滤、蒸发浓缩、冷却、离心、干燥后制得钼酸钠产品。
22.本发明的有益效果:
23.本发明通过钼精矿焙烧、酸洗除杂、氨浸、酸沉、溶解蒸发结晶、酸洗液和烟气淋洗液中钼的回收、采用n235、仲辛醇、煤油有机混合相萃取铼、通过硫化沉铜的方式,解决了钼精矿焙烧处理后酸洗预处理液中钼含量高,氨浸渣钼含量高,工艺流程长、生产成本高、废水中含有硝态氮的问题。
24.本发明通过多次循环利用酸沉母液、结晶母液、萃余液等操作废液,实现从含高铜钼精矿中综合回收铼、金、银等各种稀贵金属,综合回收率高,钼回收率95%以上,铼回收率70%以上,金、银、铜的回收率高达99%以上的效果。本发明中各个步骤全流程闭路循环,达到清洁生产要求,充分彻底的利用钼精矿资源,保障资源清洁环保经济地回收利用。
25.本发明方法通过针对含高铜钼精矿特点,采用稀硫酸除杂和硫酸铵抑制钼浸出、浸出剂与助浸剂联合强化氨浸渣的浸出,采用稀硫酸避免了银的浸出,使金银全部富集在氨浸渣中的方法,同时采用稀硫酸代替传统的硝酸,避免了硝态氮的环境污染和硝酸盐的累积,有利于资源的循环利用。
附图说明
26.图1为发明流程框图。
具体实施方式
27.为使本发明的目的、技术方案和优点更加清楚明了,下面具体实施例来描述本发明。但是应该理解,这些描述只是示例性的,而并非要限制本发明的范围。此外,在以下说明中,省略了对公知结构和技术的描述,以避免不必要地混淆本发明的概念。
28.本发明提供一种从高铜钼精矿中综合回收稀贵金属的方法,所述方法包括如下步骤:
29.(1)钼精矿焙烧,焙烧温度500-700℃,焙烧后对烟气进行淋洗净化;
30.(2)酸洗除杂,调节酸液的ph为0.3-0.5,液固比为3:1-4:1;
31.(3)氨浸,采用氨水浸出,浸出时间60-90min;
32.(4)酸沉;酸沉时的温度为40-45℃,酸沉终点ph为1.5-2.5,得到多钼酸铵;酸沉母液返回步骤(2)中再次进行酸洗;
33.(5)采用氨水将步骤(4)得到的多钼酸铵进行溶解,按多钼酸铵:水:氨水=1:0.4:0.5,的比例溶解,过滤,将过滤后的溶液进行煮沸蒸发浓缩,冷却结晶过滤后得到仲钼酸铵产品;
34.(6)钼的回收,酸洗液和烟气淋洗液中钼的回收,采用n235、仲辛醇、煤油有机混合相萃取钼;
35.(7)铼的回收,将步骤(6)中的酸沉过滤液与萃余液采用n235、仲辛醇、煤油有机混合相萃取铼;
36.(8)铜的回收,将步骤(7)中的铼萃余液通过硫化沉铜的方式进行回收。
37.所述步骤(1)中烟气进行淋洗净化前温度为300℃以上,使铼转化成七氧化二铼并以气态存在于高温烟气当中,从而提高铼到淋洗液中的回收率。
38.所述步骤(3)中氨浸液固比4:1-5:1,温度50-55℃,氨水用量为理论用量的1.2-1.3倍。该条件下钼的浸出率最优,浸出率达到96.5%。
39.所述步骤(3)中在完成浸出后,调节溶液ph为8.0-8.5,以1g/100ml的比例加入活性炭,搅拌,过滤出活性炭,缓慢加入硫化铵,硫化铵的加入量为理论消耗量的2倍。以该比例加入活性炭吸附杂质、净化溶液,再加入硫化铵除去大部分铜等杂质,该条件下溶液中杂质含量大幅降低,铜的去除率达到95%以上,为后续酸沉产出合格钼酸铵创造条件。
40.所述步骤(5)中结晶母液返回下批次步骤(4)酸沉或步骤(5)多钼酸铵溶解的程序中回收其中的钼。母液通过该工序循环返回,提高钼形成钼酸铵产品的直接回收率。
41.所述步骤(2)采用稀硫酸进行酸浸除杂,在稀硫酸中加入100g/l的nh4so4,酸洗温度为80-90℃,酸洗时间90-120min。在该条件下稀硫酸除杂,铜的去除率大于99.5%,铼的浸出率达到大于86.5%,铜浸出率比硝酸等其它的酸类高;同时用稀硫酸能避免银的浸出,使金银富集在浸出渣中,提高银的直接回收率,有利于金银的回收;加入nh4so4,由于同离子效益,可降低溶液中钼的含量,降低钼的浸出。
42.所述步骤(6)中萃取过程中,萃取液n235、仲辛醇、煤油的体积比为2:1:7,萃取相比o:a=2:1,;以6mol/l氨水反萃,反萃相比o:a=1:2,反萃液加入硫酸酸化酸沉得到多钼酸铵,酸沉条件与步骤(4)相同,重复步骤(5)的操作,用以得到仲钼酸铵产品。该条件下钼的萃取及反萃的回收率最高,同时反萃液酸沉后得到多钼酸铵沉淀,而其所含的铼留在溶液中进入下一步的萃取及反萃回收铼,达到钼铼高效分离回收。
43.所述步骤(7)中萃取过程中,萃取液n235、仲辛醇、煤油的体积比为0.5:8:11.5,萃取相比o:a=2:1;以6mol/l氨水反萃,反萃相比o:a=1:2;反萃液在煮沸状态下蒸发浓缩至铼含量在15g/l以上,于-4℃冷却结晶得到铼酸铵产品;结晶母液返回步骤(6)中钼萃取的步骤中。该条件下铼的萃取及反萃的回收率最高,也最有利于铼酸铵的结晶析出,结晶母液返回钼萃取及反萃工序能最大化回收并分离钼铼金属。
44.所述步骤(6)、步骤(7)萃取操作进行前调节有机相ph值为1。该ph条件下钼铼的萃取率最优。
45.所述步骤(5)完成后,进行氨浸渣强化浸出,氨浸渣采用浸出剂与助浸剂(如:氢氧化钠与磷酸钠)联合强化浸出,浸出温度80-100℃,浸出时间1.5-2.5小时,浸出剂浓度10-20g/l,用量为理论用量的1.2倍,助浸剂用量为浸出剂用量的10-20%,浸出液过滤、蒸发浓缩、冷却、离心、干燥后制得钼酸钠产品。加入浸出剂与助浸剂,在该工艺条件下,钼的浸出与回收率最高,达到99.16%,从而最大化的回收了钼金属。
46.本发明所述方法通过针对含高铜钼精矿特点,采用稀硫酸除杂和硫酸铵抑制钼浸出、浸出剂与助浸剂联合强化氨浸渣的浸出,采用稀硫酸避免了银的浸出,使金银全部富集在氨浸渣中的方法,同时采用稀硫酸代替传统的硝酸,避免了硝态氮的环境污染和硝酸盐的累积,有利于资源的循环利用。
47.实施例1
48.本发明提供一种从高铜钼精矿中综合回收稀贵金属的方法,钼精矿焙烧,钼精矿多元素成分分析如表1所示,该钼精矿焙烧温度650℃;硫化钼被氧化,同时伴生的铼转化成七氧化二铼并以气态存在于高温烟气当中,经过除尘后,对烟气进行淋洗净化,烟气淋洗前温度要保持在300℃以上,七氧化二铼几乎全部进入烟气淋洗液形成稀酸或称作污酸,对污酸进行铼回收,铼回收率达70%以上。
49.表1实施例1钼精矿多元素成分
[0050][0051]
酸洗除杂。采用稀硫酸进行酸浸除杂,ph在0.3,液固比3:1,在酸洗液中加入100g/l的nh4so4,由于同离子效应,可降低溶液中钼的含量,钼的浸出率只有1.44%,比不加抑制剂的情况下浸出率10.47%,低了9.03%,抑制效果显著。酸洗温度控制在90℃,酸洗时间120min。该工艺条件下,铜的去除率达到99.76%,铼的浸出率达到86.94%;而银不会浸出,保留在固相中富集,因此达到了让铜铼最大化浸出,而银不会浸出与金一起富集的效果。
[0052]
氨浸与氨浸液净化。氨浸液固比4:1,温度55℃,浸出时间90min,氨水用量为理论用量的1.2倍。在85℃,控制溶液ph=8.0,并加入少量活性炭1/100(g/100ml),搅拌30min,过滤出活性炭,缓慢加入硫化铵,加入量为铜理论消耗量的2倍,直至澄清后溶液无色透明。
[0053]
酸沉。酸沉时控制温度在45℃,缓慢加入硫酸并搅拌,控制酸沉终点ph在2.0,得到多钼酸铵。酸沉母液返回酸洗除杂2工序。
[0054]
溶解、蒸发、结晶。采用氨水将得到的多钼酸铵进行溶解,按多钼酸铵:水:氨水=1:0.4:0.5,于75℃溶解,溶液ph=6.8。过滤后液进行煮沸蒸发浓缩,冷却结晶过滤后得到仲钼酸铵产品,产品质量如表2所示,所得仲钼酸铵符合国家标准(msa-3)。结晶母液返回下批次多钼酸铵氨水溶解或酸沉工序循环回收其中的钼。钼的综合回收率达到95%以上。
[0055]
表2仲钼酸铵产品成分分析结果
[0056][0057]
氨浸渣强化浸出。氨浸渣采用氢氧化钠与磷酸钠联合强化浸出,浸出温度90℃,浸出时间2小时,氢氧化钠浓度10g/l,用量为理论用量的1.2倍,磷酸钠用量为氢氧化钠用量的15%。浸出液过滤、蒸发浓缩、冷却、离心、干燥后制得钼酸钠产品。钼在该强化浸出的条件下,回收率达到99.16%。同时金银富集在固态精矿中成为金精矿产品,金含量11.91g/t、银含量715.32g/t;金银的回收率达到99.86%,几乎没有损失。该精矿销售给黄金冶炼厂或铜冶炼厂回收金银。
[0058]
钼的回收。酸洗液和烟气淋洗液中钼的回收,采用体积比20%n235+10%仲辛醇+70%煤油有机相萃取钼,萃取前有机相先用ph=1的稀硫酸溶液酸化,萃取相比o:a=2:1,混合时间1min,澄清时间5min;以6mol/l氨水反萃,反萃相比o:a=1:2,混合时间1min,澄清时间5min。反萃液加入硫酸酸化酸沉得到多钼酸铵,酸沉条件如上述。多钼酸铵返回到上述步骤中,得到仲钼酸铵产品。
[0059]
将酸沉过滤后液和萃余液采用体积比2.5%n235+40%仲辛醇+57.5%煤油有机相萃取铼,萃取前有机相先用ph=1的盐酸溶液酸化,萃取相比o:a=2:1,混合时间1min,澄清时间5min;以6mol/l氨水反萃,反萃相比o:a=1:2,混合时间1min,澄清时间5min。反萃液在煮沸状态下蒸发浓缩至铼含量在15g/l以上,于-4℃冷却结晶得到铼酸铵产品,产品质量如表3所,所得铼酸铵符合国家标准产品;且综合回收率在70%以上。结晶母液返回钼萃取工序。
[0060]
表3铼酸铵产品成分分析结果
[0061][0062][0063]
铜的回收。铼萃余液中的铜,通过硫化沉铜进行回收。温度70℃,加入硫化钠量为铜理论量的1.2倍,搅拌沉淀2小时,过滤得到硫化铜精矿产品,铜的回收率达到99.96%,该硫化铜精矿销售给铜冶炼厂回收铜,滤液中和后达标外排。
[0064]
实施例2
[0065]
本发明提供一种从高铜钼精矿中综合回收稀贵金属的方法,钼精矿焙烧,该钼精矿焙烧温度500℃;硫化钼被氧化,同时伴生的铼转化成七氧化二铼并以气态存在于高温烟气当中,经过除尘后,对烟气进行淋洗净化,烟气淋洗前温度要保持在300℃以上,七氧化二铼几乎全部进入烟气淋洗液形成稀酸或称作污酸,对污酸进行铼回收,铼回收率达70%以上。
[0066]
酸洗除杂。采用稀硫酸进行酸浸除杂,ph在0.5,液固比4:1,在酸洗液中加入100g/l的nh4so4,由于同离子效应,可降低溶液中钼的含量,钼的浸出率只有1.52%,比不加抑制剂的情况下浸出率10.57%,低了9.05%,抑制效果显著。酸洗温度控制在95℃,酸洗时间125min。该工艺条件下,铜的去除率大于99.7%,铼的浸出率大于86.5%;而银不会浸出,保留在固相中富集,因此达到了让铜铼优化浸出,而银不会浸出与金一起富集的效果。
[0067]
氨浸与氨浸液净化。氨浸液的液固比5:1,温度50℃,浸出时间60min,氨水用量为理论用量的1.3倍。在85℃,控制溶液ph=8.0,并加入少量活性炭1/100(g/100ml),搅拌30min,过滤出活性炭,缓慢加入硫化铵,加入量为铜理论消耗量的2倍,直至澄清后溶液无色透明。
[0068]
酸沉。酸沉时控制温度在50℃,缓慢加入硫酸并搅拌,控制酸沉终点ph在2.5,得到多钼酸铵。酸沉母液返回酸洗除杂中。
[0069]
溶解、蒸发、结晶。采用氨水将得到的多钼酸铵进行溶解,按多钼酸铵:水:氨水=1:0.4:0.5的配比,于75℃溶解,溶液ph=6.8。过滤后液进行煮沸蒸发浓缩,冷却结晶过滤后得到仲钼酸铵产品。结晶母液返回下批次多钼酸铵氨水溶解或酸沉工序循环回收其中的钼。钼的综合回收率达到95%以上。
[0070]
氨浸渣强化浸出。氨浸渣采用浸出剂、助浸剂联合强化浸出,浸出温度80℃,浸出时间2.5小时,浸出剂浓度20g/l,用量为理论用量的1.2倍,助浸剂用量为浸出剂用量的15%。浸出液过滤、蒸发浓缩、冷却、离心、干燥后制得钼酸钠产品。氨浸渣在该强化浸出的条件下,钼回收率99.09%。同时金银富集在固态精矿中成为金精矿产品,金含量11.91g/t、银含量715.32g/t;金银的回收率99.92%,几乎没有损失。该精矿销售给黄金冶炼厂或铜冶炼厂回收金银。
[0071]
钼的回收。酸洗液和烟气淋洗液中钼的回收,采用体积比20%n235+10%仲辛醇+70%煤油有机相萃取钼,萃取前有机相先用ph=1的稀硫酸溶液酸化,萃取相比o:a=2:1,混合时间1min,澄清时间5min;以6mol/l氨水反萃,反萃相比o:a=1:2,混合时间1min,澄清时间5min。反萃液加入硫酸酸化酸沉得到多钼酸铵,酸沉条件如上述。多钼酸铵返回到上述步骤中,得到仲钼酸铵产品。
[0072]
将酸沉过滤后液与萃余液采用体积比2.5%n235+40%仲辛醇+57.5%煤油有机相萃取铼,萃取前有机相先用ph=1的盐酸溶液酸化,萃取相比o:a=2:1,混合时间1min,澄清时间5min;以6mol/l氨水反萃,反萃相比o:a=1:2,混合时间1min,澄清时间5min。反萃液在煮沸状态下蒸发浓缩至铼含量在15g/l以上,于-4℃冷却结晶得到铼酸铵产品,产品质量如表3所,所得铼酸铵符合国家标准产品;且铼的综合回收率在70%以上。结晶母液返回钼萃取工序。
[0073]
铜的回收。铼萃余液中的铜,通过硫化沉铜进行回收。温度70℃,加入硫化钠量为铜理论量的1.2倍,搅拌沉淀2小时,过滤得到硫化铜精矿产品,铜的回收率在99.9%以上,几乎没有损失,该硫化铜精矿销售给铜冶炼厂回收铜,滤液中和后达标外排。
[0074]
实施例3
[0075]
本发明提供一种从高铜钼精矿中综合回收稀贵金属的方法,钼精矿焙烧,该钼精矿焙烧温度700℃;硫化钼被氧化,同时伴生的铼转化成七氧化二铼并以气态存在于高温烟气当中,经过除尘后,对烟气进行淋洗净化,烟气淋洗前温度要保持在300℃以上,七氧化二
铼几乎全部进入烟气淋洗液形成稀酸或称作污酸,对污酸进行铼回收,铼回收率达70%以上。
[0076]
酸洗除杂。采用稀硫酸进行酸浸除杂,ph在0.3,液固比3:1,在酸洗液中加入100g/l的nh4so4,由于同离子效应,可降低溶液中钼的含量;钼的浸出率只有1.37%,比不加抑制剂的情况下浸出率10.45%,低了9.08%,抑制效果显著。酸洗温度控制在95℃,酸洗时间125min。该工艺条件下,铜的去除率达到99.83%,铼的浸出率87.26%;而银不会浸出,保留在固相中富集,因此达到了让铜铼优化浸出,而银不会浸出与金一起富集的效果。
[0077]
氨浸与氨浸液净化。氨浸液的液固比5:1,温度50℃,浸出时间60min,氨水用量为理论用量的1.3倍。在85℃,控制溶液ph=8.5,并加入少量活性炭1/100(g/100ml),搅拌30min,过滤出活性炭,缓慢加入硫化铵,加入量为铜理论消耗量的2倍,直至澄清后溶液无色透明。
[0078]
酸沉。酸沉时控制温度在50℃,缓慢加入硫酸并搅拌,控制酸沉终点ph在2.5,得到多钼酸铵。酸沉母液返回酸洗除杂中。
[0079]
溶解、蒸发、结晶。采用氨水将得到的多钼酸铵进行溶解,按多钼酸铵:水:氨水=1:0.4:0.5的配比,于75℃溶解,溶液ph=6.8。过滤后液进行煮沸蒸发浓缩,冷却结晶过滤后得到仲钼酸铵产品。结晶母液返回下批次多钼酸铵氨水溶解或酸沉工序循环回收其中的钼。钼的综合回收率达到95%以上。
[0080]
氨浸渣强化浸出。氨浸渣采用浸出剂、助浸剂联合强化浸出,浸出温度100℃,浸出时间2小时,浸出剂浓度18g/l,用量为理论用量的1.2倍,助浸剂用量为浸出剂用量的15%。浸出液过滤、蒸发浓缩、冷却、离心、干燥后制得钼酸钠产品。氨浸渣在该强化浸出的条件下,钼回收率99.26%。同时金银富集在固态精矿中成为金精矿产品,金含量11.91g/t、银含量715.32g/t;金银的回收率99.84%,几乎没有损失。该精矿销售给黄金冶炼厂或铜冶炼厂回收金银。
[0081]
钼的回收。酸洗液和烟气淋洗液中钼的回收,采用体积比20%n235+10%仲辛醇+70%煤油有机相萃取钼,萃取前有机相先用ph=1的稀硫酸溶液酸化,萃取相比o:a=2:1,混合时间1min,澄清时间5min;以6mol/l氨水反萃,反萃相比o:a=1:2,混合时间1min,澄清时间5min。反萃液加入硫酸酸化酸沉得到多钼酸铵,酸沉条件如上述。多钼酸铵返回到上述步骤中,得到仲钼酸铵产品。
[0082]
将酸沉过滤后液与萃余液采用体积比2.5%n235+40%仲辛醇+57.5%煤油有机相萃取铼,萃取前有机相先用ph=1的盐酸溶液酸化,萃取相比o:a=2:1,混合时间1min,澄清时间5min;以6mol/l氨水反萃,反萃相比o:a=1:2,混合时间1min,澄清时间5min。反萃液在煮沸状态下蒸发浓缩至铼含量在15g/l以上,于-4℃冷却结晶得到铼酸铵产品,产品质量如表3所,所得铼酸铵符合国家标准产品;且铼的综合回收率在70%以上。结晶母液返回钼萃取工序。
[0083]
铜的回收。铼萃余液中的铜,通过硫化沉铜进行回收。温度70℃,加入硫化钠量为铜理论量的1.2倍,搅拌沉淀2小时,过滤得到硫化铜精矿产品,铜的回收率在99.9%以上,几乎没有损失,该硫化铜精矿销售给铜冶炼厂回收铜,滤液中和后达标外排。
[0084]
本发明采用新型组合药剂抑制酸洗过程钼的浸出和强化氨浸渣钼的浸出,即:采用硫酸铵抑制钼的酸洗浸出,采用浸出剂和助浸剂强化氨浸渣中钼的浸出;并采用硫化法
替代萃取法回收铜的工艺,实现了钼、铼、金、银、铜等各类稀贵金属综合高效回收的目的,解决了钼精矿焙烧处理后酸洗预处理液中钼含量高,氨浸渣钼含量高,工艺流程长、生产成本高、废水中含有硝态氮的问题。
[0085]
本发明的具体保护范围不仅限以上解释说明,任何在本发明揭露的技术思路范围内,及根据本发明的技术方案加以简单地替换或改变,都应在本发明的保护范围之内。