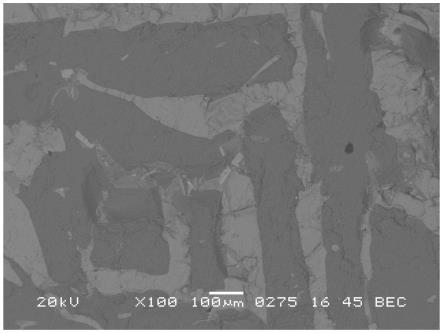
:
1.本发明涉及铸铁件生产熔炼工艺及制备技术领域,尤其是有韧性要求的铸件。具体涉及铸铁件生产使用的孕育剂和该系列孕育剂制备方法。
背景技术:2.铸造业是国家基础工业之一,其产品涉及军工、民用、航天、铁路、汽车、电力设备、基础建设、各种工农机械制造等。铸造件简称铸件,分为有色铸件和黑色铸件,黑色铸件又细分为铸铁件和铸钢件。
3.随着科学技术的不断进步,以及人们生活要求的提高,工业对铸铁件的要求也在不断提高。其中一个要求就是在保证甚至是提高铸件使用可靠性的基础上,要求铸件重量不断减轻,从而减轻整机的重量。以汽车铸件为例,一辆燃油汽车上的铸铁件的重量占据总重(质) 量的20-40%。减轻铸铁件的重量可以帮助减轻整车的重量,这样能减少汽车使用能耗,并提高行驶安全系数。新的能源政策下,新能源车的发展也如火如荼。不论是电动车(电池包提供能源)还是氢能源汽车,对汽车整车轻量化的要求也是近乎苛刻。在这样的大背景下,汽车铸铁件工作者也在不断摸索汽车用铸铁件的轻量化开发。
4.无独有偶,风电铸件的减重工作也是近年来铸造从业者重点关注的项目。由于风电安装时需要将十几吨甚至是几十吨的风电轮毂吊装到几十米至上百米的高空,工作难度和风险都是巨大的。在保证使用性能的同时,风电铸件的减重无疑是该问题的解决办法之一,同时为开发更高功率的风电整机提供了技术支持。
5.通过本发明的孕育剂及对应的使用方法,成功辅助汽车铸铁件和风电铸铁件提高性能,进而为其铸件减重提供了技术支持。
6.铸铁件通常含2%-4%的碳,常温下铸铁件中的碳大部分以不同形态的石墨形态出现。根据不同的石墨形态,铸铁件细分为球墨铸铁件、灰铸铁件、蠕墨铸铁件等等。铸铁件在生产过程中都需要用到孕育剂以及孕育工艺,来改善铸铁件中碳的存在形式、分布、尺寸、形态等,进而改变或者改善铸铁件的性能。这些性能包括但不仅限于机械性能、切削性能、固有频率、时效性能等。其中铸铁件使用方首要关注的是铸铁件的机械性能,主要包括抗材质的拉强度、屈服强度、延伸率、硬度和冲击强度(冲击功的吸收,包括常温冲击和低温冲击)。孕育剂在铸铁件生产成型过程中加入量通常在铁水总质量的0.05-1%。其加入量不大,但起的作用却十分关键。
7.铸铁件生产过程中,通过一定的孕育工艺,加入合适的孕育剂,可以达到以下诸多目的。1、有效的减少铸铁件白口(大块的fe3c组织,行业通常也称之为碳化物)生成,进而改善和保障铸铁件机械性能,降低铸铁件硬度,提高机加工性能。2、提高或者调整石墨析出量,同时可以改善石墨形态,减小铸铁件成型过程中的缩松倾向,提高材质致密度,进而提高产品的成品率和进一步提高性能;3、改善或者调整铸件基体组织,通常是珠光体(pearlite)和铁素体(ferrite)的比例,进而有针对性的调整铸铁件所需的性能;4、改善铸铁件材质的均匀性,包括基体组织和石墨的分布。通常由于铸铁件产品结构复杂、尺寸不
一,铸铁件性能均匀性和一致程度也是至关重要的。
8.铸铁行业使用的孕育剂通常为硅铁基合金。其中:硅(si)元素含量一般在质量百分比的 40%-80%,通常认为是溶剂元素(也是基体元素);含有不同成分含量的孕育元素,诸如ca、 al、ce、la、ba、sr、zr、bi、sb、mn等;含有c、sio2、灰分等杂质;fe为余量(也是主要的基体元素)。作为一种批量使用的工业添加剂,市场能关注到的孕育剂的质量标准只有简单个别元素的成分范围和粒度分布。因此,孕育剂生产厂家也就按照个别元素的成分范围和粒度分布,来简单匹配产品,这是当下的行业现状。
9.专利wo99/29911(cn1281513a)中谈到在含有la/ce以及金属氧化物的孕育剂的基础上,增加硫化物后对促进球墨铸铁中石墨球的生产有所提高。其中用氧化物、硫化物和含 ce硅铁合金物理混合。实际铸铁件生产过程中,硫元素(s)是铸铁件的五大基本元素之一,尤其是灰铁件,并不缺少。此外,铸铁件自然生产过程都是有氧环境,且铸铁件熔炼的原材料中的含氧组分也并不缺,例如废钢生铁的表层铁锈。所以额外加入硫和氧元素,略有蛇足之嫌。专利wo2018/004356(cn109477154a)中谈到硅铁合金中加入氧化铋(bi2o3)、氧化铁(fe2o3)和硫化亚铁(fes)物理混合后对铸件孕育的作用。此专利也是专注于硫化物和氧化物对孕育剂的改良作用。这些专利关注点都只是铸件金相中的石墨球数,仅是影响铸件性能的一个点。对于当下铸铁件性能要求的不断提高,已经难以满足。
技术实现要素:10.本发明设计开发了一种改善铸铁件韧性的孕育剂及该孕育剂的制备方法。通过设计的成分和特殊的合成方式,能改变孕育剂各化合相的组成方式和形态,从而提高孕育剂的孕育效果,提高孕育均匀性,降低孕育剂溶解所需温度,降低孕育剂熔化焓,提高孕育剂使用过程中的被溶解吸收的速度,也减少了孕育剂加入过程带来的缺陷风险。最终能降低部分铸件冶金缺陷的风险,提高铸件本身的性能。发明创造描述:
11.根据第一个方面,本发明涉及一种改善铸铁件韧性的孕育剂。其中所述孕育剂为粒状硅铁基合金,该合金包含重量百分比在40-80%之间的硅、0.5-3%之间的钙、0.5-6%之间的铝、 0-3%之间的氮,0-3%之间的硼,0-3%之间的锑,总量不超过2%质量的杂质(包括游离态的碳、灰分及其他氧化物),剩余质量量为铁。
12.本发明所述的孕育剂中的硅元素部分是以硅和铁的化合物形式存在,主要包括fesi相和fesi2相;硅元素的另外一部分是以单质硅的形式存在;
13.本发明所述的孕育剂中的氮元素部分是以铝和硼的氮化物的形式存在,另一部分固溶
14.本发明所述的孕育剂中的硼元素主要是以氮化铝和氮化硼复合化合物形式存在,附着于基体合金表面;
15.本发明所述的孕育剂基体合金中的铝元素部分是以和锑金属的金属间化合物形式存在,另一部分固溶于基体的铁硅相中。
16.验证发现,根据以上三点所生产出的孕育剂,相对于同元素组成但只是简单熔炼生成的孕育剂,铸铁件基体金相组成稳定(珠光体和铁素体比例),厚壁铸铁件碎块状石墨生成倾向小。
17.本发明所述的孕育剂基体中的孕育相在常温下和基体相融合更完全。其中,铝元素、钙元素、氮元素固溶于的合金基体相中;锑元素形成和铝元素、钙元素的金属间化合物,均匀分布于基体相之间。基体相是指硅单质相和硅铁化合相(主要包括fesi相和fesi2相)。
18.根据较佳实施方案,本发明所述的孕育剂中的各种相组织细化颗粒化,包括基体相和孕育相,形成类似“球墨铸铁金相”的各种相分布。相对于现有市面产品,本发明所诉孕育剂单位面积下形成的“晶粒”数提升一个数量级,相的分布也弥散、均匀,在微观下也呈类似球墨铸铁形态金相分布,如图2、3所示。其中,基体相全部为铁硅相,没有单质硅相存在;铁硅相fesi以大花瓣状、块状和类球状均匀分布,硅铁相fesi2包裹在其周围;部分孕育元素熔融于基体相中,例如部分的铝和钙;部分孕育剂相以化合相的形式分布于基体之间。例如锑、铝、钙。在100倍放大倍数下,在1mm2面积内,块状的“晶粒”颗数达到200个以上。
19.验证发现,在同条件的铸造使用条件下,根据以上所述所生产出的孕育剂,比同类硅铁基孕育剂,孕育效果更稳定,熔化/溶解速度更快,能耗更小,造渣倾向更小,孕育效率更高,球铁件同比情况下延伸率更高更稳定。换言之,铸造使用时限制条件更小,造成铸件夹渣缺的陷副作用倾向更低,达到同样铸件孕育要求时所需要的孕育剂加入量更低,铸铁件也就更有可能设计得更轻。
20.第二个方面涉及本发明的铸铁用孕育剂的生产制备方法。
21.步骤一,c系列添加剂制备:首选,混料初磨。选用高品位的氮化硼和氮化铝为原材料,按照一定的质量百分比均匀混合后,同时置于行星球磨机内,球磨罐充氮气保护。按照设计的转速和球磨时间,将两种材料混合物磨成均匀微粒。其次,烧结。将混合好的微粒装入模具压片,制成一定尺寸的圆片。然后将压制好的片状样品放入高温箱式炉中,直接放在坩埚盖子上错位叠放,按照一定的温度控制程序升温、控温、降温。最后,制粉。将烧结好的样块,用破碎机破碎成粉末,过筛。再用球磨机,按照一定的球磨工艺,制备成目标粒度的粉末,称之为c系列添加剂。
22.步骤二,制备孕育剂基材。首先,熔炼。选用高品位的硅铁、生铁、金属铝锭、金属锑锭和氮化物为原材料。先将硅铁、生铁按照一定比例置于中频炉内熔炼至1300℃左右(
±
20℃),呈液态金属液,静置扒去浮渣。然后按照一定的质量百分比加入氮化物、金属铝锭和/或锑锭,升温至1350-1400℃。其中氮化物选自工业尿素ch4n2o/co(nh2)2、碳酸氢铵nh4hco3、硫酸铵(nh4)2so4、硝酸铵nh4no3中的一种或几种。其次,冷却制粒。通过快速冷却设备使合金液冷却至固态(900℃以下),冷却速度大于50℃ /秒。再置于石墨容器中自然冷却至室温。最后破碎筛分至不同粒度规格的颗粒状孕育剂。
23.步骤三,孕育剂和添加剂合成。将步骤二制备好的孕育剂和步骤一制备好的添加剂c以一定的比例混合,加入粘结剂混合搅拌均匀,然后置于恒温干燥箱内干燥、烘烤,确保除去水分和结晶水。再破碎筛分至目标颗粒。
附图说明:
24.图1显示为比较例1的i1孕育剂锭块的平面扫描电镜(sem)金相图,使用背散射电子图像,放大100倍;
25.图2显示为实施例3的i7孕育剂的平面扫描电镜(sem)金相图,使用背散射电子图像,放大100倍;
26.图3显示为比较例3的i7孕育剂的平面扫描电镜(sem)高倍金相图,使用背散射电子图像,放大500倍;
27.图4显示为使用实施例4的i8孕育剂生产的qt700-10材质铸件的实际拉伸断口试棒的平面扫描电镜(sem)金相图,使用背散射电子图像,放大50倍;
28.图5显示为使用对比例4的i4孕育剂生产的qt400-18tl材质铸件的实际低温冲击断口的扫描电镜(sem)图,使用二次电子图像,放大50倍;
29.图6显示为使用实施例4的i8孕育剂生产的qt400-18tl材质铸件的实际低温冲击断口的扫描电镜(sem)图,使用二次电子图像,放大50倍;
具体实施方式:
30.比较例按照现有技术,直接购买市面上优质孕育剂作为对比例,分别是:比较例1,孕育剂编号i1,硅铁系孕育剂,产地中国宁夏,主要成分:73.8%si,2.7%al,1.53%ca,0.2-0.7mm和 10-70mm;比较例2,孕育剂编号i2,硅铝系孕育剂,产地加拿大,主要成分:74.6%si,3.97%al, 0.93%ca,0.2-0.7mm;比较例3,孕育剂编号i3,硅稀土系孕育剂,产地加拿大,主要成分:74.7%si,1.9%ce,0.2-0.7mm;比较例4,孕育剂编号i4,硅稀土+硫和氧的化合物孕育剂,产地挪威,主要成分:73.8%si,1.73%ce,0.76%ca,s/o《1.0%,0.2-0.7mm。各孕育剂情况如表1所示。
31.实施例1生产孕育剂首先,熔炼。选用高品位的硅铁(si%≥72%)、生铁(优质q12)、金属铝锭(al%≥99%) 和氮化物为原材料。先将硅铁、生铁按照一定比例置于中频炉内熔炼至1300℃左右(
±
20℃),呈液态金属液,静置扒去浮渣。然后按照一定的质量百分比加入氮化物和金属铝锭,升温至 1350-1400℃。其中氮化物选用工业尿素ch4n2o/co(nh2)2。其次,冷却制粒。通过快速冷却设备使合金液冷却至固态(900℃以下),冷却速度大于 50℃/秒。再置于石墨容器中自然冷却至室温。最后破碎筛分至0.2-0.7mm颗粒状孕育剂i5。实测成分:51.7%si,4.84%al,0.70%ca,0.47n%,具体信息如表1所示。表1.用于比对的孕育剂信息
对比产地孕育剂主要化学成分编号对比对比例1中国宁夏73.8%si,2.7%al,1.53%cai1市场产品对比例2加拿大74.6%si,3.97%al,0.93%cai2市场产品对比例3加拿大74.7%si,1.9%ce,0.76%cai3市场产品对比例4挪威73.8%si,1.73%ce,0.76%ca,s/o《1.0%i4市场产品实施例1中国51.7%si,4.84%al,0.70%ca,0.47n%i5本发明相关实施例2中国70.5%si,4.93%al,0.16%sb,0.52n%i6本发明相关
实施例3中国51.7%si,4.84%al,0.75%ca,0.23%b,1.01n%i7本发明相关实施例4中国70.5%si,4.93%al,0.17%sb,0.28%b,0.95n%i8本发明相关
32.实施例2生产孕育剂首先,熔炼。选用高品位的硅铁(si%≥72%)、金属铝锭(al%≥99%)、金属锑锭(sb%≥99%)和氮化物为原材料。先将硅铁置于中频炉内熔炼至1300℃左右(
±
20℃),呈液态金属液,静置扒去浮渣。然后按照一定的质量百分比加入氮化物、金属铝锭和锑锭,升温至 1350-1400℃。其中氮化物选用工业尿素ch4n2o/co(nh2)2。其次,冷却制粒。通过快速冷却设备使合金液冷却至固态(900℃以下),冷却速度大于50℃ /秒。再置于石墨容器中自然冷却至室温。最后破碎筛分至0.2-0.7mm颗粒状孕育剂i6。实测成分:70.5%si,4.93%al,0.16%sb,0.52n%,具体信息如表1所示。
33.实施例3生产孕育剂步骤一:制备添加剂c1。初磨。选用高品位的六方晶系氮化硼和氮化铝为原材料,按照质量比bn:aln=40:60均匀混合后,同时置于行星球磨机内,球磨罐充氮气保护。以400r/min的转速,48h的球磨时间进行球磨,将两种材料混合物磨成均匀微粒。期间每6小时开罐重置一遍粉末,确保材料没有粘黏于底部。封罐需要重新充氮气。烧结。将初磨混合好的微粒装入磨具压片,制成厚10mm,直径60mm尺寸的圆片。然后将压制好的片状样品放入高温箱式炉中,直接放在坩埚盖子上错位叠放。温度控制程序:升温速率:5℃/min(《1000℃),3℃/min/min(》1000℃),并在1300℃保温4h后降温,降温速率:3℃/min,降至800℃后随炉冷却。箱式炉充氮气保护。制粉。采用破碎机将烧结好的样品破碎成100微米颗粒粉末,(建议采用破碎机)200目过筛。将200目过筛颗粒粉末球磨成20微米以下,将粉末放入行星球磨机中,以400r/min的转速,24h的球磨时间进行球磨,500目过筛。得到c1添加剂。步骤二:制备合金颗粒:熔炼。选用高品位的硅铁(si%≥72%)、生铁(优质q12)、金属铝锭(al%≥99%)和氮化物为原材料。先将硅铁、生铁按照一定比例置于中频炉内熔炼至1300℃左右(
±
20℃),呈液态金属液,静置扒去浮渣。然后按照一定的质量百分比加入氮化物和金属铝锭,升温至 1350-1400℃。其中氮化物选用工业尿素ch4n2o/co(nh2)2。冷却制粒。通过快速冷却设备使合金液冷却至固态(900℃以下),冷却速度大于50℃/ 秒。再置于石墨容器中自然冷却至室温。最后破碎筛分至0.2-0.6mm颗粒状。实测成分:51.7%si, 4.84%al,0.70%ca,0.46n%,具体信息如表1所示。步骤三:熔炼合金颗粒和添加剂合成。将步骤二制备好的合金颗粒和步骤一制备好的添加剂c1混合,加入粘结剂混合搅拌均匀,然后置于恒温干燥箱内干燥、烘烤,确保除去水分和结晶水。再破碎筛分至0.2-0.7mm颗粒,得到孕育剂i7。
34.实施例4生产孕育剂
步骤一:制备添加剂c1。初磨。选用高品位的六方晶系氮化硼和氮化铝为原材料,按照质量比bn:aln=40:60均匀混合后,同时置于行星球磨机内,球磨罐充氮气保护。以400r/min的转速,48h的球磨时间进行球磨,将两种材料混合物磨成均匀微粒。期间每6小时开罐重置一遍粉末,确保材料没有粘黏于底部。封罐需要重新充氮气。烧结。将初磨混合好的微粒装入磨具压片,制成厚10mm,直径60mm尺寸的圆片。然后将压制好的片状样品放入高温箱式炉中,直接放在坩埚盖子上错位叠放。温度控制程序:升温速率:5℃/min(《1000℃),3℃/min/min(》1000℃),并在1300℃保温4h后降温,降温速率:3℃/min,降至800℃后随炉冷却。箱式炉充氮气保护。制粉。采用破碎机将烧结好的样品破碎成100微米颗粒粉末,(建议采用破碎机)200目过筛。将200目过筛颗粒粉末球磨成20微米以下,将粉末放入行星球磨机中,以400r/min的转速,24h的球磨时间进行球磨,500目过筛。得到c1添加剂。步骤二:制备合金颗粒:熔炼。选用高品位的硅铁(si%≥72%)、金属铝锭(al%≥99%)、金属锑锭(sb%≥99%) 和氮化物为原材料。先将硅铁置于中频炉内熔炼至1300℃左右(
±
20℃),呈液态金属液,静置扒去浮渣。然后按照一定的质量百分比加入氮化物、金属铝锭和锑锭,升温至1350-1400℃。其中氮化物选用工业尿素ch4n2o/co(nh2)2。冷却制粒。通过快速冷却设备使合金液冷却至固态(900℃以下),冷却速度大于50℃/ 秒。再置于石墨容器中自然冷却至室温。最后破碎筛分至0.2-0.6mm颗粒状。实测成分:70.5%si, 4.93%al,0.17%sb,0.28%b,0.95n%,具体信息如表1所示。步骤三:熔炼合金颗粒和添加剂合成。将步骤二制备好的合金颗粒和步骤一制备好的添加剂c1混合,加入粘结剂混合搅拌均匀,然后置于恒温干燥箱内干燥、烘烤,确保除去水分和结晶水。再破碎筛分至0.2-0.7mm颗粒,得到孕育剂i8。
35.实施例5孕育剂对比选取i1孕育剂和i7孕育剂的大颗粒合金,镶嵌成金相试块,并磨出一个观察平面。使用扫描电镜(sem)观察对比,使用的是扫描电镜的背散射电子光源的成分相,如图1、图2 和图3所示。图1中是i1孕育剂的金相,放大到100倍。深灰色相是单质硅相,浅灰色相是铁硅化合相,更浅色(条状)相是含ca/al的孕育元素化合相。图2中是i7孕育剂的金相,放大到100倍。灰色是富硅的fesi2相,亮灰色是fesi相,白亮色的是含锑、铝、钙的相。图3是i7孕育剂进一步放大到500倍的金相。是从图1-图3中可以明显看出两种孕育剂的金相区别。本发明所述的孕育剂中的各种相组织细化、颗粒化,包括基体相和孕育相,形成类似“球墨铸铁金相”的各种相分布。相对于现有市面产品,本发明所诉孕育剂单位面积里形成的“晶粒”数提升一个数量级,相的分布也弥散、均匀,在微观下也呈类似球墨铸铁形态金相分布。其中,基体相全部为铁硅相,相对于i1孕育剂,没有单质硅相存在;铁硅相fesi以大花瓣状、块状和类球状均匀分布,富硅的铁硅相fesi2包裹在其周围;部分孕育元素熔融于基体相中,包括部分的铝和钙;部分孕育剂相以化合相的形式分
布于基体之间。包括锑、铝、钙。在100倍放大倍数下,在1mm2面积内,组织中相的“晶粒”颗数达到200个以上。
36.实施例6孕育剂应用1选用实施例1至实施例4的孕育剂(i5~i8),以及对比例1和对比例2的孕育剂(i1、i2),总共6种孕育剂做实际应用的比对试验,观察石墨球数的变化。试验选取球墨铸铁铸件,是实际生产的铸件(牌号qt450-10),铸件上提前做好5mm和25mm两处标准的附铸试块。铁水重量1000kg,同一包铁水总共浇铸13箱。选取第5箱至第10箱,分别使用i1、i2、i5~i8孕育剂做最终随流孕育,孕育剂粒度均为0.2-0.7mm,加入量均为铁水重量的0.1%。试验其他条件相同,最后三模(箱)铸件浇铸时取样检测铸件最终成分,3.62%的c,2.59%的si, 0.22%的mn,0.035%的p,0.01%的s,0.037%的mg。实测结果如表2所示。表2.孕育剂在球墨铸铁上应用对比表从试验对比结果来看,本发明的孕育剂在5mm试块和25mm试块上的孕育表现均优异,比同类市场现有孕育剂表现更好,促进生产石墨球数量更多,石墨球的球化率更高。
37.实施例7孕育剂应用2选用实施例3的孕育剂(i7),和对比例3孕育剂(i3),做实际应用的比对试验。试验选取汽车球墨铸铁铸件,铸件生产厂商需要减轻铸件重量,要求铸件达到qt700-10要求,即要求抗拉强度要达到700mpa,同时延伸率要达到10%。在实际生产的铸件上做对比,取铸件两端上下砂箱两个附铸试块,取样位置铸件本体壁厚10mm。一包铁水重量1000kg,同一包铁水总共浇铸8箱。选取第4、5箱,分别使用i3、i7孕育剂做最终随流孕育,孕育剂粒度均为 0.2-0.7mm,加入量均为铁水重量的0.15%。试验其他条件相同,最后三模(箱)铸件浇铸时取样检测铸件最终成分,3.65%的c,2.65%的si,0.2%的mn,0.03%的p,0.01%的s,0.033%的mg,0.45%的cu及其他合金元素。实测结果如表3所示。表3.孕育剂在球墨铸铁上应用对比表从试验对比结果来看,本发明的孕育剂在高强度高延伸球铁件的性能表现优异,比同类市场现有孕育剂(加拿大产)表现更好。使用本发明孕育剂能够在不影响强度和硬度
的情况下,进一步提升材质的延伸率,性能也更稳定,铸铁件不同位置性能均匀性更好。同样的条件下,能够满足高强度高延伸球铁件的生产需求,减少铸件工艺上的苛刻性,进而可以减轻铸件重量同时达到同样的使用性能。
38.实施例8孕育剂应用3选用实施例4的孕育剂(i8),和对比例4孕育剂(i4),做实际应用的比对试验。试验选取机车球墨铸铁铸件(有低温冲击要求),铸件生产厂商要求达到qt400-18tl要求,实际抗拉强度要达到380mpa,延伸率要达到18%。同时“v”型试块-20℃低温冲击功最低要达到 12j(-40℃低温冲击作为参考值),低温冲击试块为铸件三个不同位置的附铸试块,取样位置铸件本体壁厚50mm。一炉铁水5吨,每包铁水重量约1000kg左右,选取第一包和第二包铁水,分别使用i4和i8孕育剂做随流孕育,粒度均为0.2-0.7mm,加入量均为铁水重量的0.15%,此外其他试验条件相同。如表4所示,是炉前炉后铁水成分。表4.孕育剂在球墨铸铁上应用对比表成分c%si%mn%p%s%mg%cr%ce%ti%炉前3.9001.0720.1330.0190.0150.0020.0370.0170.021第1包3.6062.0560.1490.0200.0100.0470.0380.0200.023第2包3.6291.9790.1460.0200.0110.0390.0380.0220.023每包铁水取一个y型试块做抗拉强度和延伸率测试;一包铁水浇铸3箱,选取首箱和尾箱的冲击试块做冲击性能,冲击试块做电镜观察。实测结果,常规机械性能金相全部合格,包括抗拉强度、硬度、延伸率、石墨球数、球化率以及珠光体含量(≤5%)。两种孕育剂性能差异主要体现在低温冲击性能和金相中的碎块状石墨两个方面,具体结果如表5所示。从试验对比结果来看,本发明的孕育剂在有低温冲击性能要求的铸件上表现优异,促进铸件金相碎块状石墨倾向小,低温冲击性能表现更优。对低温冲击断口进行扫描电镜分析观察,如图5和图6所示,分别是使用i4和i8孕育剂生产的低温铸件的-20℃的冲击断口。从断口可以看到,使用i8孕育剂生产的低温铸件,低温冲击断口断面以韧窝为主,石墨球数和韧窝数量较多,基本看不到准解理面。而使用i4孕育剂生产的低温铸件,低温冲击断口断面有明显的准解理面,有明显的碎块状石墨,韧窝数量和石墨球数也相对较少。表5.孕育剂在球墨铸铁上应用对比表