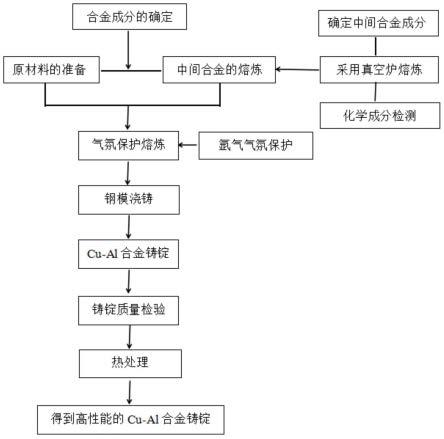
1.本发明涉及铜合金制造技术领域,具体是涉及一种性能优异的铸造铜合金的制备方法。
背景技术:2.随着轨道交通业的快速发展,隧道掘进机等相关设备需求日趋增长,铜合金被广泛应用于航空航天、海洋工程、机械工程等高应力条件工作下的结构零件、耐磨件及耐腐蚀件等,是现代工业中不可或缺的一种重要的合金材料。
3.cu-al合金是一种固溶强化、形变强化和析出强化相结合的合金,可通过控制变形及热处理工艺来控制析出相的相貌、大小和分布,以获得强度与塑性的综合平衡。国内外开展了大量复杂cu-al合金的相关研究工作,国外对铸造cu-al合金的耐腐蚀、耐摩擦等性能研究较深入,国内的研究仅集中在耐腐蚀性能方面,针对铸态cu-al合金的工艺、组织和性能的研究很少。
4.本发明采用气氛保护熔炼+中间合金+微合金化的方法,配合适当的热处理工艺,制备出高强度、高塑性、耐磨、耐腐蚀的cu-al合金材料。
技术实现要素:5.为解决上述技术问题,本发明提供了一种性能优异的铸造铜合金的制备方法。
6.本发明的技术方案是:一种性能优异的铸造铜合金的制备方法,包括以下步骤:
7.s1、配料
8.按照质量百分比称取原料:al 8%-13%、fe 2%-5%、ni 4%-8%、mn 0.2%-2%、si 0.1%-0.5%、b 0.1%-0.5%,余量为cu;
9.s2、装炉及抽真空
10.将称取的al放入熔炼炉的坩埚内,其余所述原料放入二次加料室,开始对熔炼炉内抽真空,待熔炼炉内真空压力至р≤0.08mpa时,继续抽真空,待熔炼炉内真空度≤20pa时,向熔炼炉内充入氩气,开始真空熔炼;
11.s3、熔炼
12.开始真空熔炼时,先升温熔化全部的al,随后通过所述二次加料室将其余所述原料加入,调整熔炼炉的加热功率至70-90kw,保持8-10min,然后提升加热功率至150-170kw,保持8-10min,再提升加热功率至190-210kw,使熔炼炉内原料全部熔化,在加热功率190-210kw下精炼25-30min,得到熔融金属液;
13.s4、浇铸
14.将步骤s3所得熔融金属液静置降温后,开始浇铸,浇铸完成后,停止加热并在熔炼炉内冷却40min出炉,得到铸锭,随后将铸锭放入热处理炉进行热处理。采用上述方法制作出的cu-al合金,由于采用了气氛保护熔炼,熔炼过程不与空气接触,能获得气体含量极少的合金,且有效地消除了非金属夹杂,获得的合金组织致密、成分均匀、气孔、夹杂较少,并
且添通过添加fe、ni、mn、si、b合金元素改善合金性能,微量的mn、si、b元素,可对铜液进行微合金化处理,提升了合金强度及塑性。
15.进一步地,所述fe、mn元素以中间合金cufe50、cumn37的形式加入,使用中间合金可以降低熔炼温度,减少合金元素烧损。
16.进一步地,所述中间合金cufe50、cumn37的制备方法为:
17.1)按照质量百分比秤取cufe50中间合金原料:cu 50%、fe 50%;按照质量百分比秤取cumn37中间合金原料:cu 63%、mn 37%,
18.2)将cufe50中间合金原料或cumn37中间合金原料装入熔炼炉的坩埚内,开始对熔炼炉内抽真空,
19.3)当熔炼炉内真空度达到р≤10pa时,开始真空熔炼,调整熔炼炉的加热功率至20
±
2kw,保持8min,提升加热功率至40
±
2kw,保持10min,再提升加热功率至50
±
2kw,保持10min,然后提升加热功率至65kw保持,直至坩埚内中间合金原料全部熔化后,降低加热功率至20kw,打开氩气阀门,向熔炼炉内充入氩气,
20.4)调整熔炼炉的加热功率至60kw,精炼5min,然后使用石墨坩埚开始快速浇铸,浇铸时间≤30s,浇铸完成冷却20min后出炉,使用上述方法制得的cufe50、cumn37中间合金元素分布均匀,不易产生偏析,且由于制备过程中不与空气接触,金属不易发生氧化。
21.进一步地,步骤s2以及步骤3中所述充入氩气的方法为:直至熔炼炉内真空压力达到-0.08mpa时,停止充入氩气,充入氩气可保证熔炼炉内压力,避免熔炼炉内原料高温氧化。
22.进一步地,步骤s3在放入al之后的具体操作为:使熔炼炉内温度保持在680-720℃,直至al全部熔化后加入精炼剂,静置15-20min,加入精炼剂之后可有效去除氧化铝杂质,且能减少铝和铜的烧损。
23.进一步地,所述精炼剂按质量份数计包括:kcl:40-43份、nacl:34-37份、na2tif6:8-10份、na3alf6:5-8份、c2cl6:2-4份、稀土:0.5-1份,上述组份中kcl和nacl对al2o3、夹杂物和氧化膜有很强的浸润能力,na3alf6可溶解al2o3,na2tif6中的ti元素可以作为变质剂改善铜合金的性能,且能提高al2o3溶解度,c2cl6可提高精炼效果,细化晶粒,稀土可吸附熔体中的杂质氢,达到除气体的同时减少氧化物,且可使al2o3夹杂尺寸变小,细化铸锭晶粒。
24.进一步地,步骤s4开始浇铸前,先调整设备功率至100kw,然后再采用专用钢模进行浇铸,调整功率可保证合适的浇铸温度,提高铜液的流动性,使铜液更好的成型,选用专用钢模可避免浇铸过程中产生偏析和缩孔。
25.进一步地,步骤s4浇铸时浇铸速度为先慢、再适当加快,最后再减慢,整个浇铸时间为1min,浇注过程先慢,后快的过程可保证铜液凝固过程有效补缩,形成致密组织。
26.作为本发明的一种可选技术方案,步骤s4所述热处理方法为:将铸锭在550-650℃温度下,保温4h,随炉冷却,上述热处理方法可调整铸锭组织,细化晶粒。
27.作为本发明的另一种可选技术方案,步骤s4所述热处理方法为:
28.1)在550-650℃温度下,保温4h,
29.2)向铸锭表面喷洒-20℃的低温氮气,使铸锭表面温度降低100-120℃,停止喷洒低温氮气,使铸锭表面温度回升50-70℃,
30.3)继续向铸锭表面喷洒-20℃的低温氮气,重复步骤2),直至铸锭表面温度≤350
℃,停止喷洒低温氮气,随炉冷却,上述热处理方法通过使铸锭小幅度快速降温,能使晶粒迅速成型,再使温度略微回升的方式,可以很好的消除铸锭内部的残余应力,调整铸锭内部组织,消除组织缺陷。
31.本发明的有益效果是:
32.(1)本发明通过采用气氛保护熔炼,由于熔炼过程不与空气接触,能获得气体含量极少的合金,能有效地消除非金属夹杂,获得组织致密、成分均匀、气孔、夹杂较少的合金。
33.(2)本发明通过添加fe、ni、mn、si、b合金元素改善合金性能,合金元素加入方式采用cufe50、cumn37中间合金的形式,可降低熔炼温度,减少合金元素烧损;添加微量的mn、si、b元素,对铜液进行微合金化处理,可加强细晶强化,提升铜合金强度及塑性。
34.(3)本发明通过对熔化的al加入精炼剂,减少了氧化物夹杂,精炼剂还可调整最后得到的铸锭的内部组织,细化晶粒,提高铸锭的综合性能,且本发明采用低温氮气对铸锭进行小幅度快速降温,再使温度略微回升的方式对铸锭进行热处理,很好的消除了铸锭内部的残余应力,并调整了铸锭内部组织,消除组织缺陷。
附图说明
35.图1是本发明铸造铜合金制备流程图。
36.图2是本发明实施例1铸造铜合金金相图。
37.图3是本发明实施例4铸造铜合金金相图。
38.图4是本发明实施例5铸造铜合金金相图。
39.图5是本发明实施例6铸造铜合金金相图。
具体实施方式
40.下面结合具体实施方式来对本发明进行更进一步详细的说明,以更好地体现本发明的优势。
41.实施例1
42.如图1所示,本发明实施例公开了一种性能优异的铸造铜合金的制备方法,包括以下步骤:
43.s1、配料
44.按照质量百分比称取原料:al 9.6%、fe 4.2%、ni 4.5%、mn 1.8%、si 0.1%、b 0.1%,余量为cu;
45.s2、装炉及抽真空
46.将称取的al放入熔炼炉的坩埚内,其余原料放入二次加料室,开启机械泵,打开低真空挡板阀对熔炼炉内抽真空,待炉内真空压力р达到0.08mpa时,开启罗茨泵,继续抽真空,待熔炼炉内真空度为20pa时,向熔炼炉内充入氩气,直至真空压力达到-0.08mpa时,停止充入氩气,开始真空熔炼;
47.s3、熔炼
48.开始真空熔炼时,先升温熔化全部的al,随后通过二次加料室将其余原料加入,调整熔炼炉的加热功率至80kw,保持10min,然后提升加热功率至160kw,保持10min,再提升加热功率至200kw,使熔炼炉内金属全部熔化,在加热功率200kw下精炼25min,得到熔融金属
液;
49.s4、浇铸
50.将步骤s3所得熔融金属液静置降温后,先调整熔炼炉加热功率至100kw,采用专用钢模开始浇铸,浇铸速度为15kg/min,、再调整至30kg/min,最后再减慢为15kg/min,整个浇铸时间为1min,浇铸完成后,停止加热并在熔炼炉内冷却40min出炉,得到铸锭,随后将铸锭放入热处理炉中,在650℃温度下,保温4h,随炉冷却。
51.实施例2
52.本实施例与实施例1基本相同,不同之处在于,fe、mn元素以中间合金cufe50、cumn37的形式加入,且cufe50、cumn37中间合金的制备方法为:
53.1)按照质量百分比秤取cufe50中间合金原料:cu 50%、fe 50%;按照质量百分比秤取cumn37中间合金原料:cu 63%、mn 37%,
54.2)将cufe50中间合金原料或cumn37中间合金原料装入熔炼炉的坩埚内,开启机械泵,打开低真空挡板阀对熔炼炉内抽真空,待熔炼炉内真空压力р达到0.08mpa以下时,开启罗茨泵,继续抽真空,
55.3)当熔炼炉内真空度р达到10pa时,开始真空熔炼,调整熔炼炉加热功率至20kw,保持8min,提升加热功率至40kw,保持10min,提升加热功率至50kw,保持10min,提升加热功率至65kw保持,直至坩埚内中间合金原料全部熔化后,降低加热功率至20kw,打开氩气阀门,向熔炼炉内充入氩气,直至熔炼炉内真空压力达到-0.08mpa时,停止充入氩气。
56.4)调整熔炼炉加热功率至60kw,精炼5min,然后使用石墨坩埚开始快速浇铸,浇铸时间30s,浇铸完成冷却20min后出炉。
57.实施例3
58.本实施例与实施例1基本相同,不同之处在于,步骤s3在放入al之后的具体操作为:使熔炼炉内温度保持在700℃,直至al全部熔化后加入精炼剂,静置15min,加入精炼剂的组份按质量份数计包括:kcl:42份、nacl:36份、na2tif6:9份、na3alf6:8份、c2cl6:4份、稀土:1份。
59.实施例4
60.本实施例与实施例1基本相同,不同之处在于,步骤s1中称取的原料质量百分比不同,具体为:al 9.8%、fe 4.4%、ni 5.2%、mn 1.5%、si 0.1%、b 0.1%,余量为cu。
61.实施例5
62.本实施例与实施例1基本相同,不同之处在于,步骤s1中称取的原料质量百分比不同,具体为:al 10.5%、fe 4.5%、ni 4.7%、mn 0.3%、si 0.1%、b 0.1%,余量为cu。
63.实施例6
64.本实施例与实施例1基本相同,不同之处在于,步骤s1称取的原料质量百分比不同,具体为:al 11.2%、fe 4.0%、ni 6.0%、mn 0.5%、si 0.1%、b 0.1%,余量为cu。
65.实施例7
66.本实施例与实施例1基本相同,不同之处在于,步骤s1称取的原料质量百分比不同,具体为:al 8%、fe 2%、ni 4%、mn 0.2%、si 0.1%、b 0.1%,余量为cu。
67.实施例8
68.本实施例与实施例1基本相同,不同之处在于,步骤s1称取的原料质量百分比不
同,具体为:al 13%、fe 5%、ni 8%、mn 2%、si 0.5%、b 0.5%,余量为cu。
69.实施例9
70.本实施例与实施例1基本相同,不同之处在于,步骤s3开始真空熔炼时熔炼炉的加热功率不同,具体为:调整熔炼炉的加热功率至70kw,保持10min,然后提升加热功率至150kw,保持10min,再提升加热功率至190kw,使熔炼炉内金属全部熔化,在加热功率190kw下精炼25min。
71.实施例10
72.本实施例与实施例1基本相同,不同之处在于,步骤s3开始真空熔炼时熔炼炉的加热功率不同,具体为:调整熔炼炉的加热功率至90kw,保持10min,然后提升加热功率至170kw,保持10min,再提升加热功率至210kw,使熔炼炉内金属全部熔化,在加热功率210kw下精炼25min。
73.实施例11
74.本实施例与实施例3基本相同,不同之处在于加入的精炼剂各组份质量份数不同,具体为:kcl:42份、nacl:36份、na2tif6:8份、na3alf6:8份、c2cl6:4份、稀土:1份。
75.实施例12
76.本实施例与实施例3基本相同,不同之处在于加入的精炼剂各组份质量百分比不同,具体为:kcl:42份、nacl:36份、na2tif6:10份、na3alf6:8份、c2cl6:4份、稀土:1份。
77.实施例13
78.本实施例与实施例1基本相同,不同之处在于,步骤s4具体的热处理方法为:
79.1)在650℃温度下,保温4h,
80.2)向铸锭表面喷洒-20℃的低温氮气,使铸锭表面温度降低110℃,停止喷洒低温氮气,使铸锭表面温度回升60℃,
81.3)继续向铸锭表面喷洒-20℃的低温氮气,重复步骤2),直至铸锭表面温度≤350℃,停止喷洒低温氮气,随炉冷却。
82.实施例14
83.本实施例与实施例13基本相同,不同之处在于,热处理的步骤2)使铸锭表面降低的温度为100℃。
84.实施例15
85.本实施例与实施例13基本相同,不同之处在于,热处理的步骤2)使铸锭表面降低的温度为120℃。
86.实施例16
87.本实施例与实施例13基本相同,不同之处在于,热处理的步骤2)使铸锭表面回升的温度为50℃。
88.实施例17
89.本实施例与实施例13基本相同,不同之处在于,热处理的步骤2)使铸锭表面回升的温度为70℃。
90.实施例18
91.本实施例与实施例13基本相同,不同之处在于,热处理的步骤3)直至铸锭表面温度≤300℃,停止喷洒低温氮气,随炉冷却。
92.实施例19
93.本实施例与实施例13基本相同,不同之处在于,热处理的步骤3)直至铸锭表面温度≤380℃,停止喷洒低温氮气,随炉冷却。
94.实验例
95.针对各实施例所制备的铸造铜合金,分别测试其硬度、抗拉强度、屈服强度、延伸率,具体探究如下:
96.1、探究不同的原料质量百分比对所制备的铸造铜合金性能的影响:
97.以实施例1、4、5、6、7、8作为实验对比得到的试样性能测试数据如下表1所示:
98.表1不同的原料质量百分比制备得到的试样性能测试数据
99.组别硬度(hb)抗拉强度(mpa)屈服强度(mpa)延伸率(%)实施例119469030817.0实施例419569031516.0实施例519370332318.0实施例619670131016.5实施例718368230716.0实施例819567329815.0
100.由表1数据可知使用不同质量百分比的原料制备的铸造铜合金的性能也有不同变化,使用者可根据实际使用的性能需求选择不同质量百分比的原料。
101.如图2、3、4、5所示,通过本发明制备方法得到的铸造铜合金材料的材料相组成为(α+γ2)共析相+β相+k相,k相弥散分布于整个材料之中,且通过本发明的方法制备的铸造铜合金材料组织致密、无气孔、夹杂等铸造缺陷。
102.2、探究熔炼炉加热功率对所制备的铸造铜合金性能的影响
103.以实施例1、9、10作为实验对比,结果如下表2所示:
104.表2不同的熔炼炉加热功率制备得到的试样性能测试数据
105.组别硬度(hb)抗拉强度(mpa)屈服强度(mpa)延伸率(%)实施例119469030817.0实施例918568330216.0实施例1019068730616.5
106.由上述表2数据可看出,不同的熔炼炉加热功率对制备的铸造铜合金的硬度、抗拉强度、屈服强度、延伸率均有一定影响,且实施例1所选加热功率相对更优。
107.3、探究中间合金加入对铸造铜合金性能的影响
108.以实施例1、2作为实验对比,结果如下表3所示:
109.表3实施例1、2制备得到的试样性能测试数据
110.组别硬度(hb)抗拉强度(mpa)屈服强度(mpa)延伸率(%)实施例119469030817.0实施例219271231618.5
111.由上述表3数据可看出,以中间合金cufe50、cumn37形式加入fe、mn元素制备得到的铸造铜合金综合性能更优。
112.4、探究不同精炼剂对所制备的铸造铜合金性能的影响
113.以实施例1、3、11、12作为实验对比,同时以实施例3的配组为基准,去除na2tif6,配比制成对比例1的精炼剂,还采用市售的精炼剂取代实施例3中使用的精炼剂作为对比例2,结果如下表4所示:
114.表4不同精炼剂制备得到的试样性能测试数据
115.组别硬度(hb)抗拉强度(mpa)屈服强度(mpa)延伸率(%)实施例119469030817.0实施例320571531919.0实施例1120069631018.0实施例1220170231518.5对比例119669331417.5对比例219469231217.5
116.通过实施例1和实施例3对比可以看出在铝完全熔化后加入精炼剂所制备的铸造铜合金硬度、抗拉强度、屈服强度、延伸率等性能均有提升;
117.通过实施例3和对比例1可以看出精炼剂中加入了na2tif6得到的铸造铜合金综合性能得到了提高;
118.通过实施例3和对比例2可以看出,实施例3采用的精炼剂对于本发明铸造铜合金的性能提升效果更好;
119.通过实施例3、11、12对比可以看出精炼剂中na2tif6的质量份数不同,对所制备的铸造铜合金综合性能也有影响,其中实施例3使用的精炼剂配比制备的铸造铜合金性能更优。
120.5、探究不同热处理参数对所制备的铸造铜合金性能的影响
121.以实施例1、13、14、15、16、17、18、19作为实验对比,同时在实施例13基础上还分别使用-10℃和-30℃的低温氮气与实施例13做了两组对比例,分别计做对比例3、对比例4;以实施例13为基础,不采用低温氮气对铸锭降温,而是通过控制热处理炉的参数来使铸锭降温,作为对比例5;以实施例13为基础,采用低温氮气直接通入热处理炉内,低温氮气不直接作用于铸锭而使铸锭降温,作为对比例6,结果如下表5所示:
122.表5不同氮气温度制备得到的试样性能测试数据
123.[0124][0125]
通过实施例1和实施例13可以看出,实施例13的热处理方式制备的铸造铜合金的性能更好。
[0126]
通过实施例13、14、15可以看出,热处理时使铸锭表面降低不同的温度对制备的铸造铜合金性能会产生不同的影响,且实施例13选择的降低温度更优;
[0127]
通过实施例13、16、17可以看出热处理时使铸锭表面回升不同的温度对制备的铸造铜合金性能会产生不同的影响,且实施例13选择的回升温度更优;
[0128]
通过实施例13、18、19可以看出停止喷洒低温氮气时铸锭表面温度对制备的铸造铜合金性能会产生影响,实施例19与实施例13相比,实施例13中选择的温度更优,实施例18与实施例13相比,铜合金性能变化幅度不大,从经济角度考虑,实施例13选择的温度更优;
[0129]
通过实施例13、对比例3、对比例4可以看出,使用不同温度的低温氮气进行热处理对制备的铜合金性能会产生影响,且使用-20℃的低温氮气进行热处理对本发明铸造铜合金的性能提升效果更优;
[0130]
通过实施例13和对比例5可以看出,实施例13采用低温氮气对铸锭进行降温的方式可提高制备的铸造铜合金性能;
[0131]
通过实施例13和对比例6可以看出,实施例13制备的铸造铜合金性能优于对比例6,低温氮气直接作用于铸锭表面的热处理方式更优。