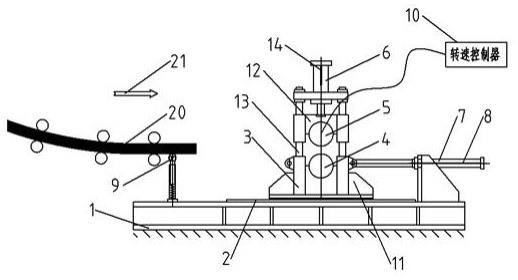
1.本发明属于冶金过程控制技术领域;尤其涉及一种自适应控制铸轧速度的连铸大压下装置和方法。
背景技术:2.在连铸生产过程中,高温液态钢水经过结晶器一次冷却区、垂直区、弯曲区、弧形区、矫直区、水平区等连续冷却形成带有一定厚度液芯的铸坯,最终完全凝固。连铸坯在正常凝固后,铸坯的致密度低,在后序的轧制过程中需要大压缩比才能解决致密度一致的问题。为解决此问题,许多冶金工作者利用连铸坯芯部温度高,外部温度低,铸坯外硬内软,少量的压下即可容易穿透铸坯芯部的特性,在高温的连铸坯表面施加一定压下量,从而使中心组织更加致密均匀,提高铸坯致密度。
3.但是,连铸坯表面在压下的过程中,由于其截面面积发生变化,其铸坯运动的速度也发生变化,以往的压下装置其辊子转速是根据检测前置铸坯速度和压下量,通过体积秒流量相等原理来逼近,但是在生产实践中无法完全做到体积秒流量相等,使前置铸坯速度和压下装置中的铸坯的速度不匹配,造成滞坯、堆钢、损坏设备等生产事故。
技术实现要素:4.本发明的目的是提供了一种自适应控制铸轧速度的连铸大压下装置和方法。
5.本发明是通过以下技术方案实现的:本发明涉及一种自适应控制铸轧速度的连铸大压下装置,包括:装置本体、基座1、滑轨2、速度控制器10、铸坯拉速检测部件、移位部件;滑轨2设置在基座1上,且与装置本体滑动连接;速度控制器10、移位部件分别与装置本体连接。
6.优选地,所述装置本体包括:机架3、支撑辊4、固定框架11、压下辊5、压下液压缸6、升降框架12;升降框架12套设在连接杆13上,压下液压缸6设置在所述装置本体的顶端。
7.优选地,所述支撑辊4设置在所述固定框架11上。
8.优选地,所述升降框架12设有压下辊5、直线位置传感器14;其中,压下辊5由电机减速机驱动。
9.优选地,所述装置本体的机架3沿着滑轨2移动。
10.优选地,所述移位部件包括:平衡液压缸7、位移传感器8,位移传感器8设置在平衡液压7上。
11.优选地,所述铸坯拉速检测部件为铸坯拉速检测轮9,铸坯拉速检测轮9设置在所述基座1上。
12.优选地,所述速度控制器包括:基本参数模块15、铸坯拉坯速度检测模块16、位移
检测模块17、逻辑判断和计算模块18、速度执行系统19。
13.本发明还涉及前述的自适应控制铸轧速度的连铸大压下装置的运作方法,包括以下步骤:当铸坯到达铸坯拉速检测轮9时,铸坯拉坯速度检测模块16获得铸坯20的速度并传入到逻辑判断和计算模块18,其判段和计算过程如下:步骤1,根据铸坯20的速度计算大压下装置内铸坯的理论速度v;步骤2,通过位移检测模块17判断大压下机架是否偏离原点;步骤3,若大压下机架3没有偏离原点,则把速度v发送到速度执行系统19;步骤4,若大压下机架3偏离原点,则判断大压下机架是否沿拉坯方向21移动;步骤5,若大压下机架3是沿拉坯方向21移动,则大压下装置内铸坯20的匹配线速度v=v-δv,并发送到速度执行系统19;步骤6,若大压下机架3是沿拉坯方向21的反移动,则大压下装置内铸坯20的匹配线速度v=v+δv,并发送到速度执行系统19;步骤7,重复步骤2。
14.本技术针对以往的压下装置在生产过程中,其铸轧速度是根据检测前置铸坯速度和压下辊压下量,通过体积秒流量相等原理来逼近,但是在生产实践中无法完全做到体积秒流量相等,使前置铸坯速度和压下装置中的铸坯的速度不匹配,造成滞坯、堆钢、损坏设备。
15.本发明具有以下优点:(1)本发明所涉及的自适应控制铸轧速度的连铸大压下装置为自适应移动结构,可以沿着滑轨移动,使大压下装置的铸轧速度随着铸坯拉速及铸坯拉速的变化自适应调整,从而自动匹配拉坯速度,并使大压下装置始终自动向原点逼近,解决了以往的大压下装置与铸坯速度难以快速响应匹配,造成滞坯、堆钢、损坏设备等生产事故的问题。(2)本发明所述的自适应控制铸轧速度的连铸大压下装置的铸轧速度控制系统独立,不与连铸机的控制系统相连。
附图说明
16.图1是本发明所涉及的自适应控制铸轧速度的连铸大压下装置结构示意图;图2为自适应铸轧速度控制系统控制逻辑示意图;其中,1为基座;2为滑轨;3为机架;4为支撑辊;5为压下辊;6为压下液压缸; 7为平衡液压缸;8为位移传感器;9为铸坯拉速检测轮;10为速度控制器;11为固定框架;12为升降框架;13为连接杆;14为直线位置传感器;15为基本参数模块;16为铸坯拉坯速度检测模块;17为位移检测模块;18为逻辑判断和计算模块;19为速度执行系统;20为铸坯;21为拉坯方向。
17.具体实施方式
18.下面结合具体实施例对本发明进行详细说明。应当指出的是,以下的实施实例只是对本发明的进一步说明,但本发明的保护范围并不限于以下实施例。
实施例
19.本实施例一种自适应控制铸轧速度的连铸大压下装置,见图1所示,包括:装置本体、基座1、滑轨2、速度控制器10、铸坯拉速检测部件、移位部件;滑轨2设置在基座1上,且与装置本体滑动连接;速度控制器10、移位部件分别与装置本体连接。
20.进一步地,所述装置本体包括:机架3、支撑辊4、固定框架11、压下辊5、压下液压缸6、升降框架12;升降框架12套设在连接杆13上,压下液压缸6设置在所述装置本体的顶端。
21.进一步地,所述支撑辊4设置在所述固定框架11上。
22.进一步地,所述升降框架12设有压下辊5、直线位置传感器14;其中,压下辊5由电机减速机驱动。
23.进一步地,所述装置本体的机架3沿着滑轨2移动。
24.进一步地,所述移位部件包括:平衡液压缸7、位移传感器8,位移传感器8设置在平衡液压7上。
25.进一步地,所述铸坯拉速检测部件为铸坯拉速检测轮9,铸坯拉速检测轮9设置在所述基座1上。
26.进一步地,所述速度控制器包括:基本参数模块15、铸坯拉坯速度检测模块16、位移检测模块17、逻辑判断和计算模块18、速度执行系统19。
27.所述连铸坯凝固末端自适应控制铸轧速度的大压下装置,设置在连铸坯凝固末端后面。
28.本实施例还涉及前述的自适应控制铸轧速度的连铸大压下装置的运作方法,包括以下步骤:见图2所示,在生产过程中,当铸坯20到达前置铸坯拉速检测轮9时,铸坯拉坯速度检测模块16获得铸坯的线速度为2.3m/min,并传入到逻辑判断和计算模块18,在铸坯20进入压下机架3前,铸坯20的线速度为2.3m/min;铸坯20进入压下机架3,压下液压缸6驱动压下辊5对铸坯20压下18mm,铸坯厚度方向变薄,理论山需要大于2.3m/min的线速度来匹配前置铸坯,因此铸坯推着压下机架3沿着拉坯方向移动;位移检测模块17检测到压下机架3偏离原点,并且判断压下机架是沿拉坯方向21移动,计算出压下装置辊的匹配线速度2.3m/min,并发送到速度执行系统19;压下机架3向原点逼近,并且重复上述步骤。
29.本发明针对以往的压下装置在生产过程中存在以下不足:其铸轧速度是根据检测前置铸坯速度和压下辊压下量,通过体积秒流量相等原理来逼近,在生产实践中无法完全做到体积秒流量相等,使前置铸坯速度和压下装置中的铸坯的速度不匹配,造成滞坯、堆钢、损坏设备等现象,研发一种连铸坯凝固末端自适应控制铸轧速度的大压下装置,从而解决上述技术问题。
30.本发明具有以下优点:(1)本发明所涉及的一种自适应控制铸轧速度的连铸大压下装置和方法,本发明
所涉及的大压下装置为自适应移动结构,可以沿着滑轨移动,使大压下装置的铸轧速度随着铸坯拉速及铸坯拉速的变化自适应调整,从而自动匹配拉坯速度,并使大压下装置始终自动向原点逼近,解决了以往的大压下装置与铸坯速度难以快速响应匹配,造成滞坯、堆钢、损坏设备等生产事故的问题。(2)本发明所述的一种自适应控制铸轧速度的连铸大压下装置和方法,其大压下装置的铸轧速度控制系统独立,不与连铸机的控制系统相连。
31.以上对本发明的具体实施例进行了描述。需要理解的是,本发明并不局限于上述特定实施方式,本领域技术人员可以在权利要求的范围内做出各种变形或修改,这并不影响本发明的实质。