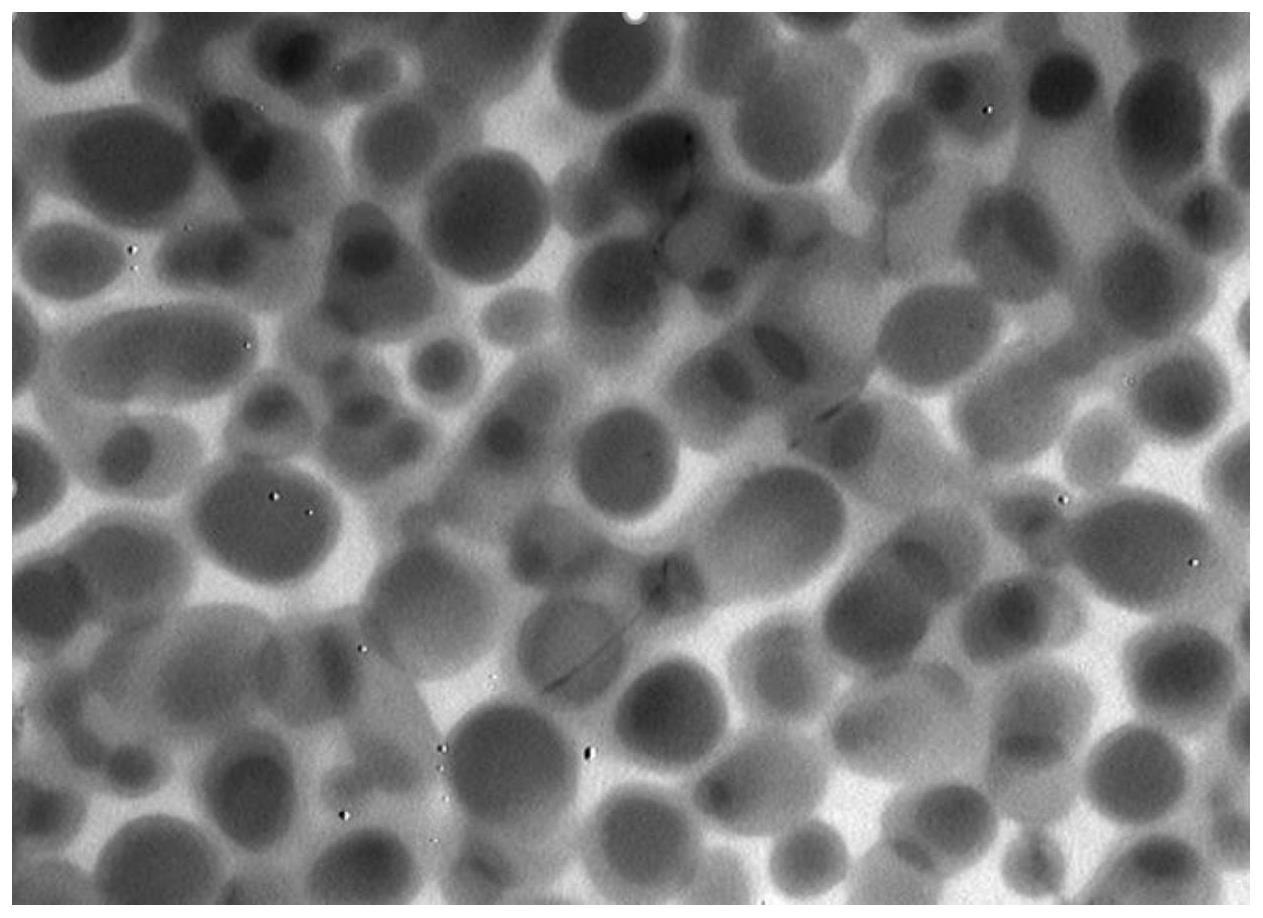
1.本发明涉及氢能工业管道用材设计技术领域,具体而言,尤其涉及一种氢能专用管道合金、管道及管道的制备方法。
背景技术:2.氢能是当下备受关注的清洁能源,目前已有多种制氢、提纯氢技术,在民用和工业领域氢气应用十分广泛,是新世纪重要的二次能源,氢能开发和利用是我国能源转型的重要方向之一。由于氢极易渗入临氢材料中,造成氢致塑性损失,即氢脆,随着氢气压力,浓度的提高,对材料氢脆抗性也做出了更高的要求。成熟的储氢运技术利用压力容器和高压管道以高压气态氢形式进行存储与运输,但是要想和天然气一样大规模普及,甚至如西气东输一样远距离运输,面临的困难之一就是金属制容器和管道的氢脆问题。
3.随着氢气普及利用,输氢管道广泛应用于加氢站、燃料电池汽车、工业厂区等场景。输氢管径的直径有大有小,输送压力范围也很大,低的到0.1mpa,大的100mpa;使用量差距也非常大。氢运输管道也有它的特点,新建的氢气管道它应该满足相匹配环境中的抗氢等级。
4.管道与氢气长期接触,氢会侵入到管道材料内部,导致金属材料出现损减、裂纹扩张速度加快和断裂韧性的下降。现有技术中输送纯氢气所采用的常规天然气管道不具备抗氢损能力。
技术实现要素:5.根据上述提出现有技术中输送纯氢气所采用的常规天然气管道不具备抗氢损能力的技术问题,而提供一种氢能专用管道合金、管道及管道的制备方法,利用纳米级γ
ˊ
强化相作为钢中的氢的捕获位点来吸附非扩散性氢,抑制氢脆。
6.本发明采用的技术手段如下:
7.一种氢能专用管道合金,包括的元素及相应的质量百分比为:
8.c:0.02~0.04%,si:小于0.3%,mn:小于0.5%,p:小于0.003%,s:小于0.005%,cr:16~21%,al:1.2~2%,ti:1~2%,v:0.08~0.3,nb:0.06~0.3,b:0.0015~0.0028,n:小于0.0005%,ni:25~33%,mo:1~3%,cu:2~4.5%,且满足ti+al小于4%,ti/al≈0.6~1.0,v+nb≤0.6%,余量为fe及不可避免的杂质。
9.进一步地,所述合金的屈服强度为620~680mpa,抗拉强度为1080~1280mpa,断后伸长率为38~45%;在200℃,0.1mpa,72h或300℃,0.1mpa,48h条件下充氢后,断后伸长率为36~42%,氢致塑性损失小于8%,氢含量为5~20ppm。
10.进一步地,用于高压储氢容器或高压氢气输送用无缝管。
11.本发明还提供了一种氢能专用管道,采用如权利要求1所述的合金,所述管道包括由ni、al、ti构成的平均粒径小于100nm的γ
ˊ
强化相。
12.进一步地,所述γ
ˊ
强化相的平均粒径为20~80nm。
13.进一步地,所述管道用于30~90mpa高压纯氢环境中储氢容器承高压结构材料或者换热器、调节阀非管道用材。
14.本发明还提供了一种氢能专用管道的制备方法,具体包括以下步骤:
15.s1:根据合金成分包括的元素及相应的质量百分比进行配料并熔炼得到钢锭,钢锭进行均匀化处理;
16.s2:均匀化后的钢锭经过开坯锻造成棒材,经过再次均匀化后水冷或者直接移送致挤压机穿孔作为原始坯料;
17.s3:将原始坯料依次经过穿孔、挤压、酸洗、冷轧、轿直、热处理、酸洗和精整,得到具有小于100nm的强化相的氢能专用管道成品;其中,所述热处理为所述热处理为670℃~850℃回火处理。
18.进一步地,所述回火处理温度为840℃。
19.较现有技术相比,本发明具有以下优点:
20.本发明提供的氢能专用管道合金、管道及管道的制备方法,制得的管道抗氢等级高,在高压临氢环境中具有良好的综合性能,可保证高压临氢环境中的强度使用要求,安全等级高,可以避免爆炸,泄露等安全事故。
21.基于上述理由本发明可在氢能工业管道领域广泛推广。
附图说明
22.为了更清楚地说明本发明实施例或现有技术中的技术方案,下面将对实施例或现有技术描述中所需要使用的附图做以简单地介绍,显而易见地,下面描述中的附图是本发明的一些实施例,对于本领域普通技术人员来讲,在不付出创造性劳动性的前提下,还可以根据这些附图获得其他的附图。
23.图1为本发明所述管道中的纳米级γ
ˊ
强化相。
具体实施方式
24.为使本发明实施例的目的、技术方案和优点更加清楚,下面将结合本发明实施例中的附图,对本发明实施例中的技术方案进行清楚、完整地描述,显然,所描述的实施例仅仅是本发明一部分实施例,而不是全部的实施例。以下对至少一个示例性实施例的描述实际上仅仅是说明性的,决不作为对本发明及其应用或使用的任何限制。基于本发明中的实施例,本领域普通技术人员在没有做出创造性劳动前提下所获得的所有其他实施例,都属于本发明保护的范围。
25.本发明提供了一种氢能专用管道合金,包括的元素及相应的质量百分比为:
26.c:0.02~0.04%,si:小于0.3%,mn:小于0.5%,p:小于0.003%,s:小于0.005%,cr:16~21%,al:1.2~2%,ti:1~2%,v:0.08~0.3,nb:0.06~0.3,b:0.0015~0.0028,n:小于0.0005%,ni:25~33%,mo:1~3%,cu:2~4.5%,且满足ti+al小于4%,ti/al≈0.6~1.0,v+nb≤0.6%,余量为fe及不可避免的杂质。
27.进一步地,所述合金的屈服强度为620~680mpa,抗拉强度为1080~1280mpa,断后伸长率为38~45%;在充氢前后,材料强度基本无变化,氢致塑性损失小于8%,充氢后断裂面不出现脆性断裂特征。
28.将本发明提供的合金加工成光滑圆板状拉伸试样,试样表面粗糙度小于0.7,利用高压气相热充氢技术,氢通过吸附、溶解、扩散进入拉伸试样中,通过改变氢压、充氢温度和充氢时间来实现试样中氢含量的控制,充氢环境为高纯氢(99.99%)氛围;
29.采用200℃,0.1mpa,72h或300℃,0.1mpa,48h的充氢参数对试样进行充氢,充氢后试样中氢含量采用氧氮氢分析仪测定,经过测定氢含量达到5~20ppm,然后进行力学性能测试,力学性能测试测试采用恒应变速率控制变形,变形速率控制在0.001mm/min;经过测试,本发明提供的合金具有较好的抗氢性能等级,在充氢设备中氢元素含量不会随着充氢时间,温度,压力上升而线性上升,氢含量达到饱和后,将不继续溶氢于基体中;充氢后,断后伸长率为36~42%,氢致塑性损失小于8%;
30.综上所述,本发明提供的合金相较于普通固溶强化抗氢奥氏体不锈钢具有更高的强度与相对较少的氢致塑性损失能力,综合性能良好。
31.进一步地,用于高压储氢容器或高压氢气输送用无缝管。
32.进一步地,所述合金能够用于30mpa、45mpa、60mpa、70mpa级别,以纯氢为动力的氢燃料电池运输工具的加氢站或者储氢容器承高压结构。
33.本发明提供的氢能专用管道合金设计的工艺原理如下:
34.(1)c是奥氏体形成元素,在本发明中,c能显著提高合金的强度,在特定的热处理工艺制度下析出m
23
c6,mx等相可以提高合金的整体强度,但在cr合金化(16~28%)的铁-镍基合金中,在650~850℃温度范围内,m
23
c6,mx等相的析出会造成晶间贫cr,此时,晶间腐蚀敏感性增加,氢致诱发的沿晶裂纹扩展速率会大幅提高,氢致塑性损失较大,因此本发明控制c含量不大于0.04%;
35.(2)al和ti为铁素体形成元素,是高温合金中主要的强化相γ
ˊ
形成元素,一般al和ti占比越高,其部件的服役温度也可大幅提高,合金中al和ti含量达到10%,其γ
ˊ
含量可达到30vol.%,广泛应用于大型涡轮盘锻件,本发明利用纳米级γ
ˊ
强化相作为钢中的氢的捕获位点来形成非扩散性氢,从而抑制扩散性氢导致的脆化,本发明控制al和ti总含量小于3%;
36.(3)cr元素是不锈钢中最重要的耐蚀元素,cr是铁素体形成元素,在奥氏钢中添加量一般为16-21%,具有良好的耐酸性腐蚀能力,在酸洗过程中表明形成纳米级的cr2o3是耐蚀性能的保证,因此,本发明控制cr含量在18wt.%;
37.(4)ni的主要作用是稳定奥氏体相,提高不锈钢的低温韧性,与此同时,ni元素还能提高钝化膜的强度,提高抗晶间腐蚀能力,ni作为γ
ˊ
相的形成基体,在铁镍基合金中含量一般为25-35%;
38.(6)cu是奥氏体化元素,可以改善合金的冷加工性能,切削性能,提高表面钝化膜稳定性,提高合金的耐蚀性能,由其在医疗行业中的抗菌性能,本发明cu含量控制在2~4.5%;
39.(7)v、nb是铁素体形成元素,在熔炼过程中易与n和溶体中的c接触形成第二相粒子nb(c,n),熔炼过程控制粒子的分散性,在凝固过程中可以有效的钉扎晶界,得到细晶组织;在热处理过程中,首先沿晶界进析出的vxcy,nbc的第二相也可以进一步提高合金的整体强度,本发明v,nb含量控制在0.6%以下。
40.(8)mo是铁素体形成元素,在cr-ni奥氏体不锈钢中,304与316的区别在于,316添
加了1~2wt.%mo,mo是晶界强化元素,能显著提高与晶界强化的相关性能,特别是耐腐蚀性能,耐腐蚀性能中抗晶间腐蚀性能更为优异,尤其是抗氢脆性能,本发明mo含量控制在1~3%之间;
41.(9)b是铁素体形成元素,b的添加能够强烈抑制第二相在晶界处析出,避免了晶间富cr倾向,能够显著提高耐晶间腐蚀性能,尤其是抗氢脆性能。
42.本发明还提供了一种氢能专用管道,采用如权利要求1所述的合金,所述管道包括由ni、al、ti构成的平均粒径小于100nm的γ
ˊ
强化相。
43.进一步地,所述γ
ˊ
强化相的平均粒径为20~80nm。
44.优选地,所述γ
ˊ
强化相的平均粒径为50~80nm。
45.进一步地,所述管道用于30~90mpa高压纯氢环境中储氢容器承高压结构材料或者换热器、调节阀非管道用材。
46.本发明还提供了一种氢能专用管道的制备方法,具体包括以下步骤:
47.s1:根据合金成分包括的元素及相应的质量百分比进行配料并熔炼得到3~6吨钢锭,钢锭进行均匀化处理;
48.s2:均匀化后的钢锭经过开坯锻造成直径30mm的棒材,经过1100~1150℃再次均匀化后水冷或者直接移送致挤压机穿孔作为原始坯料;
49.s3:将原始坯料依次经过穿孔、挤压、酸洗、冷轧、轿直、热处理、酸洗和精整,得到具有小于100nm的强化相的氢能专用管道成品;其中,所述热处理为670℃~850℃回火处理,通过回火处理,纳米级γ
ˊ
强化相在晶内均匀析出,γ
ˊ
强化相在晶内均匀析出,回火工艺是必须的,如果不将回火温度设为γ
ˊ
强化相析出敏感温度区间,则无法制备希望的微细析出物;纳米级γ
ˊ
强化相平均粒径小于50~80nm时,析出物与母相的界面面积小,点阵错配度低,捕获氢的效果较好,纳米级γ
ˊ
强化相的平均粒径超过100nm时,与母相的界面间隙较大,表面致密性降低,此情况下捕获氢的效果也降低。
50.进一步地,步骤s1中均匀化处理的参数为1200℃
×
12h。
51.进一步地,回火处理的温度为840℃。
52.进一步地,所述热处理为在真空条件或在惰性气体保护气氛下的热处理。
53.进一步地,步骤s1中熔炼采用的方法为真空感应、真空自耗或电渣重熔。
54.采用本发明提供的合金制备得到的高压氢能专用管道,在慢应变速度拉伸试验中,高压充氢后的拉伸不会较大气中的拉伸大幅降低,能够作为城市氢燃料运载工具加氢站用高压氢用管道。
55.进一步地,根据不同壁厚设计,本发明提供的所述管道输氢压力可以达到80mpa。
56.实施例1
57.本实施例所述合金包括的元素及相应的质量百分比为:c:0.02%,si:小于0.3%,mn:小于0.5%,p:小于0.003%,s:小于0.005%,cr:16%,al:2%,ti:2%,v:0.08%,nb:0.06%,b:0.0015%,n:小于0.0005%,ni:25%,mo;1%,cu:2%,余量为fe及不可避免的杂质。
58.进一步地,本实施例所述合金的屈服强度为680mpa,抗拉强度为1280mpa,断后伸长率为38%。
59.进一步地,本实施例所述合金在200℃,0.1mpa,72h或300℃,0.1mpa,48h条件下进
行充氢试验后,断后伸长率为36%,氢致塑性损失小于8%,氢含量为6ppm。
60.实施例2
61.本实施例所述合金包括的元素及相应的质量百分比为:c:0.04%,si:小于0.3%,mn:小于0.5%,p:小于0.003%,s:小于0.005%,cr:21%,al:1.2%,ti:1%,v:0.3%,nb:0.3%,b:0.0028%,n:小于0.0005%,ni:33%,mo:3%,cu:4.5%,余量为fe及不可避免的杂质。
62.进一步地,本实施例所述合金的屈服强度为620mpa,抗拉强度为1192mpa,断后伸长率为45%。
63.进一步地,本实施例所述合金在200℃,0.1mpa,72h或300℃,0.1mpa,48h条件下进行充氢试验后,断后伸长率为42%,氢致塑性损失小于8%,氢含量为5ppm。
64.实施例3
65.本实施例所述合金包括的元素及相应的质量百分比为:c:0.03%,si:小于0.3%,mn:小于0.5%,p:小于0.003%,s:小于0.005%,cr:19%,al:1.4%,ti:1.5%,v:0.21%,nb:0.15%,b:0.0022%,n:小于0.0005%,ni:31%,mo:2%,cu:3.3%,余量为fe及不可避免的杂质。
66.进一步地,本实施例所述合金的屈服强度为680mpa,抗拉强度为1080mpa,断后伸长率为44%。
67.进一步地,本实施例所述合金在200℃,0.1mpa,72h或300℃,0.1mpa,48h条件下进行充氢试验后,断后伸长率为42%,氢致塑性损失小于8%,氢含量为9ppm。
68.最后应说明的是:以上各实施例仅用以说明本发明的技术方案,而非对其限制;尽管参照前述各实施例对本发明进行了详细的说明,本领域的普通技术人员应当理解:其依然可以对前述各实施例所记载的技术方案进行修改,或者对其中部分或者全部技术特征进行等同替换;而这些修改或者替换,并不使相应技术方案的本质脱离本发明各实施例技术方案的范围。