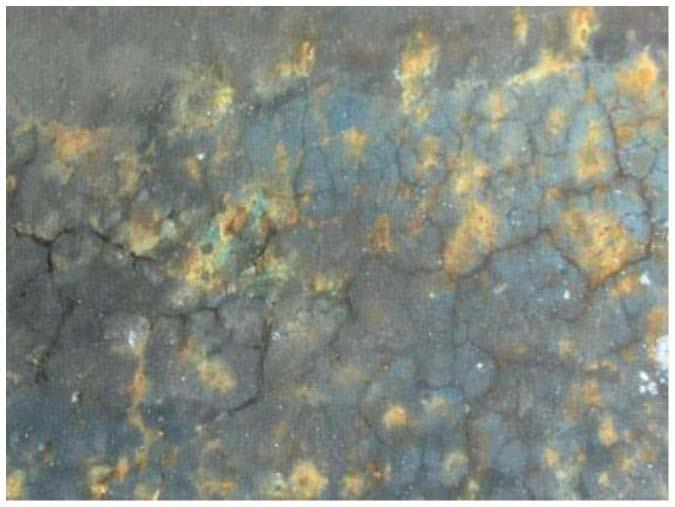
1.本发明属于冶金技术领域,涉及型钢导板制备技术,尤其是一种高强高韧耐磨抗疲劳型钢导板的制备方法及应用。
背景技术:2.型钢轧机入口导板在轧机运行时,钢坯对导板产生巨大的接触应力并产生剪切粘着磨损。同时,由于高温钢坯的热传导和摩擦热的产生,使导板的工作表面温度急剧升高,工作一段时间后形成氧化疲劳层,随着疲劳层的逐渐脱落,又成为硬质磨粒,使导板表面产生沟槽。在高温下导板的组织将发生瞬时相变,致使硬度下降,加剧了工作表面的磨损失效。国外仍普遍使用高铬镍合金钢制作导板,国内型钢厂家购入的进口轧机图纸上都会自带高铬镍合金钢导板的成分和相应的技术要求,但成本高,寿命短,不适合我国组合式型钢导板的推广。
3.近些年型钢正向着高牌号高品质(高强减量化)的方向发展,耐低温钢、高强钢、耐腐蚀钢、耐高温钢、耐磨钢使用量逐年增加,这些钢材均对型钢热工具提出了更苛刻的要求,造成导板在使用过程中提前出现磨损、结瘤、粘钢、疲劳裂纹导致轧件进孔型时容易出现卡钢、咬入困难的情况,使用过程中出现初期网状裂纹及磨损失效,造成早期报废。
技术实现要素:4.本发明的目的在于克服现有技术的不足之处,根据型钢导板失效原因,通过成分设计、变质处理、特殊处理及热处理工艺优化,提供一种高强高韧耐磨抗疲劳型钢导板的制备方法,通过改性高合金钢导板的化学成分及利用该成分的稀土变质处理和热处理方法,进而达到改善型钢导板性能、提高使用寿命的目的。
5.本发明解决其技术问题是采取以下技术方案实现的:
6.一种高强高韧耐磨抗疲劳型钢导板的制备方法,包括如下方法步骤:
7.⑴
熔化钢铁基料
8.选工业废钢作为钢铁基料进行熔化,优选含硅锰钒合金的钢铁基料,包括以下重量百分比wt%计的各化学元素:c:0.12-0.20%,si0.30-0.65%,mn0.5-1.7%,v0.02-0.05%,p《0.35%,s《0.35%,加入以重量份数计的上述基料600-700份后进行高温熔化。
9.⑵
插铝脱氧处理并添加合金
10.当熔化基料温度达到1550-1620℃时,投入以重量份数计的纯铝锭0.5-1.7份,该添加量为纯铝锭总加入量的50%,然后添加合金,该合金包括:增碳剂碳粉、锰铁、硅铁、钼铁、铬铁、钒铁和纯镍,合金加入量以重量份数计分别为:
11.增碳剂碳粉7-15份,
12.97%的锰铁1-8份,
13.含硅量为75%的硅铁5-7份,
14.含钼量为59%的钼铁8-12份,
15.含量为100%铬铁190-211份,
16.含钒量为80%的钒铁13-40份,
17.100%的纯镍60-80份;
18.上述增碳剂碳粉分次加入,加入方式如下:当熔化基料温度达到1550-1620℃时,先将1/3的增碳剂碳粉加入熔化的钢铁基料液中,随后合金依次全部加入熔化的基料后,再将1/3的增碳剂碳粉加入钢包中,冲入少量钢水搅拌,熔化后回冲炉内钢液增碳,最后将剩余1/3的增碳剂碳粉再次加入钢包中,冲入少量钢水搅拌,熔化后回冲炉内钢液再次增碳,然后打渣加合金。
19.增碳剂碳粉如果一次加入会引起冒烟严重,烧损量大,碳粉容易团聚引起碳偏析。如果分三个阶段不同工位加入可以保证碳的收得率,降低碳粉的烧损,使碳成分均匀不偏析。
20.⑵
合金出钢变质处理
21.当合金液温度达到1500℃-1550℃时出炉,然后钢水浇注冲入钢包,浇注前将剩余50%的铝锭0.5-1.7份加入,同时加入稀土变质剂金属钪,该稀土变质剂金属钪的添加重量份数为0.1-0.4份,为总稀土变质剂金属钪添加量的50%,充分搅拌后,扒去钢液表面熔渣,静置5-10分钟后进行砂箱浇注。
22.上述稀土变质剂金属钪具体添加方法为:提前破碎成8-12mm小块,按钢水重量的50%置于钢包底部,用包内冲入法对钢水进行变质处理,当钢水冲入包内1/2时投入剩下50%稀土变质剂金属钪,使得稀土变质剂金属钪的收得率在70-80%。
23.稀土变质处理可以使大块状的网状一次碳化物产生颈缩、球化,防止粗大碳化物在恶劣的工作环境下割裂基体产生早期裂纹;油冷细化晶粒,可以达到细化过饱和奥氏体和一次网状碳化物的效果;高温时效处理从过饱和的奥氏体中析出细小弥散的二次碳化物,保证了基体的耐磨性和韧性的良好匹配。
24.本发明实施例中在蔡司光学显微镜下对20个视野直接观察,并采用图像分析测试放大100倍晶粒个数,经过稀土钪作为变质剂后,变质后单位面积的晶粒个数平均由120个提高至180个。稀土sc为表面活性元素,易富聚在结晶前沿阻止晶粒长大,使铸态晶粒细化,稀土sc元素沿晶界富聚,抑制了奥氏体晶粒的长大,使晶粒进一部细化。变质前碳化物以连续网状分布于晶界,变质后碳化物由连续网状变为不连续网状和颗粒状,稀土之所以能改变碳化物的形态,是因为凝固过程中,稀土能富集在这些高熔点复合碳化物周围阻止碳化物沿晶界长大,使碳化物细化。
25.变质处理后力学性能提高是因为稀土变质剂有脱氧去硫去气净化钢液的作用,它与钢液中的硫、氧形成高熔点第二类球状或块状复合硫化物夹杂,消除了沿晶界聚集分布的第二类硫化物夹杂对性能的危害,此外稀土元素有净化晶界和强化晶界的作用,从而使导板的抗热疲劳性能得以提高。碳化物形态及分布,也是影响型钢导板力学性能的另一重要因素,未变质处理的碳化物在晶界呈网状分布;变质处理后碳化物主要以断续网状颗粒分布晶内或晶界,消除了粗大网状碳化物的危害,使其性能得以提高。
26.变质处理包括:采用分批次加入钢液,稀土变质剂高温时容易烧损,具体操作为钢包内提前加入50%的稀土变质剂sc;当钢水冲入钢包内1/2时投入另外50%的稀土变质剂,所述稀土变质剂的加入量为钢液的0.03-0.06wt%,收得率约70%。
27.稀土合金变质后的铸造组织中的一次碳化物网要比未变质的铸造组织中的一次碳化物网细而薄,大块状的碳化物细碎化明显。
28.⑷
砂箱浇注
29.浇注温度为1390-1420℃,经过搅拌均匀后浇入已经烘干的砂箱中,铸件进一步进行快冷处理及时效处理。
30.⑸
快冷处理
31.当铸件在砂箱中形成外壳并逐渐变为火红色时,迅速脱模后投入油槽中进行快冷处理,为避免开裂及变形,并快速通过不稳定的奥氏体区,油淬至450℃-550℃成暗红色时,迅速将导板提出油面,导板表面沾带的油会首先冒出白色的烟,随后发生着火现象,导板就在这种着火燃烧的油淬条件下继续冷却,待油燃尽后,导板空冷至50℃-80℃后进行时效处理。
32.⑹
时效处理
33.空冷处理后的导板放入热处理炉中630-680℃下保温10-15小时出炉空冷,完成高温时效处理,得到成品。
34.快冷+时效处理后的过饱和奥氏体晶粒细化,一次碳化物网细小显著,晶粒尺寸较之铸态组织细化大约5倍,二次碳化物成球状分布在奥氏体基体上。
35.同样,本发明实施例中在蔡司光学显微镜下对20个视野直接观察,并采用图像分析测试放大500倍晶粒个数,快冷处理后晶粒个数平均由24个提高至100个,晶粒细化明显。铸态快冷过程抑制了奥氏体晶粒长大,一次碳化物沿未长大的奥氏体晶界析出形成细小的网及颗粒,而时效处理温度既保证了奥氏体晶粒不再继续长大,又可以析出二次球化的碳化物,因此快冷+时效处理后一次碳化物网保持铸态的细化程度,同时从过饱和的奥氏体中析出二次球状碳化物。在热处理过程中,由于稀土sc在晶界富集,降低了晶界能,也使得碳化物难以在晶界继续析出和长大。因此,快冷+时效处理改善了碳化物的形态,使其变成不连续的断网状一次碳化物和细小的二次碳化物。晶粒细化是使冲击韧性提高的同时还能增加强度的最有效手段,晶粒细化可增加耐磨性及抗疲劳性,是材料综合性能得以提高的最佳方式。
36.经过上述方法制备的型钢导板成品包含以重量百分比wt%计的以下各元素:c0.8-1.6%,si0.7-1.1%,mn1.2-1.7%,cr19-21%,ni6-8%,mo0.5-0.7%,v1-3%,al0.1-0.3%,sc0.02-0.05%,p《0.04%,s《0.04%,其余为fe和少量微量杂质。
37.本发明的优点及有益效果:
38.1、本发明专利申请制备方法最终获得成品化学成分(重量百分比wt%)为:c0.8-1.6,si0.7-1.1,mn1.2-1.7,p《0.04,s《0.04,cr19-21,ni6-8,mo0.5-0.7,v1-3,al0.1-0.3,sc0.02-0.05,其余为fe和无法检测的微量杂质,对比高铬镍合金钢,其成分设计为较低的碳、铬、镍含量,适中的锰、钒、钼和稀土合金含量,变质剂为稀土钪。较低的碳含量可以提高冲击韧性;较低碳、铬含量可减少大块状碳化物数量及碳化物网厚度;适当降低镍含量可防止结瘤及粘钢,并可以降低制造成本;通过添加钒合金、稀土合金及热处理补给强度及硬度损失。
39.2、本发明专利申请中稀土变质处理明显改善了铸造组织,稀土合金变质后铸造组织中的一次碳化物网颈缩断网,碳化物网厚度减薄,大快状的一次碳化物碎化成小块状及
颗粒状。当sc质量分数为0.02%时,合金钢中一次碳化物无论是尺寸还是形态均发生了变化,当sc质量分数增加到0.05%时,合金钢的一次碳化物显著细化,sc质量分数达到0.06%时,合金钢中一次碳化物尺寸和形态并没有进一步改变,稀土合金变质剂加入量在一定范围内可有效改善一次碳化物形貌。
40.3、本发明申请中增加了特殊处理工艺,即指高温铸态试样直接油冷,去掉了铸态试样冷却至室温再回炉正火的工序,既显著细化了晶粒又缩短了热处理周期。铸件在油中淬冷呈暗红色时,取出中断冷却,在500℃以下附着于铸件上的淬火油燃烧,铸件处于油燃烧中冷却,且燃烧后产生了导热性小的残留物质包裹铸件,所以冷却是极为缓慢的。这样,不仅获得了高的淬火硬度,而且淬火应力较小,晶粒细化非常明显,一次碳化物网细化约5倍,晶粒细化是同时提高强度和韧性最有效的手段。
41.4、本发明申请中高温时效处理的目的是达到过饱和奥氏体分解析出二次碳化物,并使得二次碳化物成细小弥散的球状分布于奥氏体基体上,改变了原有正火条状碳化物形态,增加了基体材料的耐磨性及硬度。上述热处理工艺取消了正火工艺,只需进行一次高温时效处理,既节约能源降低成本,又简便易行,高温处理时效还可确保导板不变形、不开裂。
42.5、本发明申请成品高合金铸钢导板在线材轧机及h型钢轧机上进行考核轧制,导板平均使用寿命是300h,平均轧钢量845t,原高铬镍合金钢导板平均使用寿命180h,平均轧钢量586吨,原高铬铸铁导板的平均使用寿命是90h,平均轧钢量209吨,使用寿命提高了30%-70%。即本专利申请制备的导板显著提高轧机作业率,解决了轧制高钢级型材中过早出现断裂、磨损失效、龟裂及粘钢问题,避免了早期报废,提高了使用寿命。
附图说明
43.图1为失效型钢导板的宏观表面裂纹形态图;
44.图2为未变质处理铸态组织中一次网状碳化物形态图(呈大块状);
45.图3为稀土变质处理后铸态组织中一次网状碳化物形态图(碎化断网);
46.图4为铸坯表面成暗红色投入油中快冷后的组织状态图;
47.图5为快冷+高温时效组织状态图;
48.图6为一次碳化物显微硬度图;
49.图7为过饱和奥氏体显微硬度图;
50.图8为本专利申请与现有成品样磨损量对比图;
51.图9为热处理工艺示意图。
具体实施方式
52.下面通过具体实施例对本发明作进一步详述,以下实施例只是描述性的,不是限定性的,不能以此限定本发明的保护范围。
53.本发明专利申请人首先对失效的型钢导板进行分析,主要问题是导板的组织结构不合理,原有的组织不再适应高牌号型钢的轧制使用。高铬镍合金钢以及高铬铸铁在强度、硬度、冲击功和耐磨性方面均无法达到最佳平衡,失效型钢导板的宏观裂纹如图1所示,组织中大块状的一次碳化物连成网状,这种组织的使用性能非常恶劣。
54.控制碳化物类型、数量、形貌、分布和尺寸是改善导板性能的有效手段,因此型钢
导板的热疲劳抗力主要取决于碳化物形态。稀土变质剂处理不仅细化大块状的一次状碳化物,并可有效促使一次碳化物断网,通过热处理可提高强度和韧性,同时改善二次碳化物形态,可增加其耐磨性,进而显著提高导板的使用寿命。
55.现有的稀土变质剂多为镧铈及其合金,鲜有关于稀土钪作为变质剂的公开文献记载。本专利申请主要公开了一种高合金钢成分,以及通过钪稀土铝合金对其变质处理后,进一步采用特殊处理及热处理制备型钢导板的工艺方法。
56.本发明申请的技术方案是从材质组分和热处理工艺两方面对型钢导板的制备方法进行改进,适用于高牌号型钢轧制,达到强度、硬度、冲击功和耐磨性几个方面的合理匹配,同时通过改善导板的碳化物形貌以提高其使用寿命。
57.本发明申请的技术方案为较低的碳、铬、镍含量,适中的锰、钒、钼,稀土含量,高温奥氏体的铸坯油冷后进行高温时效处理,变质剂为稀土钪。较低的碳含量可以提高冲击韧性;较低碳、铬含量可减少大块状碳化物数量;适当降低镍含量可防止结瘤及粘钢,并可以降低制造成本;通过添加钒合金、稀土合金及热处理补给强度及硬度损失;通过变质处理及热处理获得稳定性好的一次碳化物和二次碳化物。
58.稀土变质处理可以使大块状的网状一次碳化物产生颈缩、球化,防止粗大碳化物在恶劣的工作环境下割裂基体产生早期裂纹;油冷细化晶粒,可以达到细化过饱和奥氏体和一次网状碳化物的效果;高温时效处理从过饱和的奥氏体中析出细小弥散的二次碳化物,保证了基体的耐磨性和韧性的良好匹配,所述合金型钢包括以下制备步骤:
59.首先熔化钢铁基料(工业废钢),首选含硅锰钒合金的钢铁基料(如低合金高强度含钒钢),其化学成分(重量百分比wt%)为:c:0.12-0.20,si0.30-0.65,mn0.5-1.7,p《0.35,s《0.35,v0.02-0.05,加入基料625-713kg。当温度达到1550-1620℃时,首先插铝脱氧,投入纯铝锭0.59-1.65kg(总加入量的一半),然后添加合金,依次为增碳剂、锰铁、硅铁、钼铁、铬铁、钒铁和镍板,合金加入量为:碳粉(增碳剂)7.2-14.8kg,含硅量为75%的硅铁5.82-7.0kg,97%的纯锰1-7.63kg,含钼量为59%的钼铁8.47-11.86kg,含量为100%铬铁190-210.8kg,含钒量为80%的钒铁13.15-39.47kg,100%的纯镍60-80kg。增碳剂加入高温钢液会引起喷溅,并且加入时间过早,附着在炉底、炉壁的增碳剂不易熔入钢液,加入时间过迟则失去了增碳的时机,造成熔炼、升温时间的延迟。
60.加入方法上,当熔化基料温度达到1550-1620℃时,先将1/3的增碳剂加入熔化的钢铁基料液中,随后合金依次全部加入熔化的基料后,再将1/3的增碳剂加入钢包中,冲入少量钢水搅拌,熔化后回冲炉内钢液增碳,最后将剩余1/3的增碳剂再次加入钢包中,冲入少量钢水搅拌,熔化后回冲炉内钢液再次增碳,然后打渣加合金。
61.合金混合熔化完全后出钢,即合金液温度达到1500℃-1550℃出炉。然后钢水浇注冲入钢包,浇注前将剩余的铝锭0.59-1.65kg(总加入量的一半)和变质剂金属钪0.15-0.35kg(总加入量的一半)提前破碎成10mm左右的小块,按所述钢水重量的一半置于钢包底部,用包内冲入法对钢水进行变质处理,当钢水冲入包内1/2时投入另外50%的稀土变质剂,前后两次稀土变质剂不同时期的加入可保证稀土收得率在70%左右,铝锭的熔点远低于稀土变质剂,小块状的铝锭将钢水剩余的游离氧结合形成氧化物并上浮,高洁净度的钢水可充分发挥稀土变质剂的作用和保证稀土收得率。
62.充分搅拌后,扒去钢液表面熔渣,静置合适的时间(5-10分钟)后进行砂箱浇注,浇
注温度为1390-1420℃,经过搅拌均匀后浇入已经烘干的砂箱中。所述铸件进一步进行快冷处理及时效处理,当铸件在砂箱中形成外壳并逐渐变为火红色时,迅速脱模后投入油槽中进行快冷处理,为避免开裂及变形,并快速通过不稳定的奥氏体区,油淬至450℃-550℃左右成暗红色时,迅速将导板提出油面,导板表面沾带的油会首先冒出白色的烟,随后发生着火现象,导板就在这种着火燃烧的油淬条件下继续冷却,待油燃尽后,导板空冷至50℃-80℃后放入热处理炉中630-680℃下保温10-15小时出炉空冷,完成高温时效处理,得到成品。
63.采用1吨中频炉冶炼,其钢水的化学成分(重量百分比wt%)为:c0.8-1.6,si0.7-1.1,mn1.2-1.7,cr19-21,ni6-8,mo0.5-0.7,p《0.04,s《0.04,v1-3,al0.1-0.3,sc0.02-0.05,其余为fe和无法检测的少量微量杂质。
64.碳:c是影响高合金铸钢硬度和韧性的主要元素,随着c含量的增加组织中碳化物数量多,则导板的硬度高、耐磨性好,但韧性下降,因此c含量以0.8%-1.6%为宜。
65.硅:si在高温下能形成致密的氧化膜提高抗氧化性,但si含量过高将导致基体脆性增大,因此si含量控制在0.7%-1.1%为宜。
66.锰:mn能去硫、提高淬透性、强化基体,但mn含量过高时,晶粒有粗化的倾向,并增加导板的高温脆性敏感性,因此mn含量宜控制在1.2%-1.7%。
67.铬:溶入基体中的cr增加钢的淬透性和抗氧化性,形成碳化物的cr增加耐磨性和抗粘钢性能。但cr含量过高基体会转变成铁素体反而使耐磨性急剧下降,因此cr含量以19%-21%为宜。
68.镍:ni提高钢的淬透性及冲击韧性,ni具有良好的耐腐蚀特性。ni价格高,且加入量过高会造成型钢导板粘钢,因此含量控制在6%-8%。
69.钼:mo是提高钢的热强性、回火稳定性和淬透性元素,mo元素会降低钢的热脆倾向,但增加成本,因此将mo含量控制在0.5%-0.7%。
70.变质剂:稀土变质剂中的sc元素既是一种稀土元素,又是一种3d型过渡元素,sc原子序数为21,与大原子半径的镧铈核外四层电子不同,稀土sc元素核外为三层电子,在稀土元素家族中属于小原子半径,强过冷元素,非碳化物形成元素,凝固过程中通过溶质元素再分配而富集在碳化物结晶前沿的液体中,细化奥氏体,其变质处理既具有稀土镧铈的细化铸造组织中的一次碳化物网的效果,又有别于稀土镧铈元素,可与多种合金形成金属间化合物及固溶体。
71.本专利申请通过添加稀土金属钪作为制备热敏特殊合金钢的变质元素,可以获得高的硬度和良好的强韧性,共晶碳化物颈缩断网,分布均匀,其形态有利于降低摩擦系数,提高导板抗氧化性及抗粘钢能力。随着稀土sc加入量的增多,导板的变质效果并未呈线性增加,质量分数为0.02%-0.05%的sc可以明显提高型钢导板的高温力学性能、组织稳定性及使用寿命,可避免长期高温工作时易产生的脆化现象。
72.变质处理包括:采用分批次加入钢液,稀土变质剂高温时容易烧损,具体操作为钢包内提前加入50%的稀土变质剂sc;当钢水冲入钢包内1/2时投入另外50%的稀土变质剂,所述稀土变质剂的加入量为钢液的0.03-0.06wt%,收得率约70%。
73.快冷处理及时效处理:当砂箱中的铸件逐渐由火红色变为暗红色时迅速脱模,投入油槽中进行快冷处理,为避免开裂及变形,并快速通过不稳定的奥氏体区,油淬至450℃-550℃左右迅速将导板提出油面,导板表面沾带的油会首先冒出白色的烟,随后发生着火现
象,导板就在这种着火燃烧的油淬条件下继续冷却,待油燃尽后,导板空冷至50℃-80℃后,再放入热处理炉中,随炉加热至630-680℃下保温10-15小时出炉空冷,完成高温时效处理,得到成品。
74.分别将未稀土变质的铸态试样(图2)、稀土变质的铸态试样(图3)和快冷+时效处理的成品试样(图5)加工成硬度及耐磨性试样测试比对。采用王水腐蚀试样磨面,对比奥氏体晶粒、碳化物网及碳化物形态。结果表明,稀土合金变质后的铸造组织中的一次碳化物网要比未变质的铸造组织中的一次碳化物网细而薄,大块状的碳化物细碎化明显;快冷+时效处理后的过饱和奥氏体晶粒细化,一次碳化物网细小显著,晶粒尺寸较之铸态组织细化大约5倍,二次碳化物成球状分布在奥氏体基体上。
75.实施例1
76.采用1吨中频炉冶炼,其钢水的化学成分(重量百分比wt%)为:c0.8,si0.7,mn1.4,p0.035,s0.030,cr20,ni6,mo0.5,v1.2,al0.19,sc0.29,其余为fe和无法检测的微量杂质。
77.首先熔化钢铁基料(工业废钢),首选含硅锰钒合金的钢铁基料,其化学成分(重量百分比wt%)为:c0.20,si0.65,mn1.7,p0.03,s0.03,v0.05,加入生铁714kg。当温度达到1558℃时,首先插铝脱氧,投入纯铝锭1.64kg(总加入量的一半),然后按照钢水所述化学成分的质量配比添加合金,依次为增碳剂、锰铁、硅铁、钼铁、铬铁、钒铁和镍板,合金加入量为:碳粉(增碳剂)15.0kg,含硅量为75%的硅铁7.0kg,97%的纯锰7.63kg,含钼量为59%的钼铁8.5kg,含量为100%铬铁200.0kg,含钒量为80%的钒铁16.0kg,100%的纯镍60kg。增碳剂加入高温钢液会引起喷溅,并且加入时间过早,附着在炉底、炉壁的增碳剂不易熔入钢液,加入时间过迟则失去了增碳的时机,造成熔炼、升温时间的延迟。加入方法上,增碳剂采取分批加入,先将1/3的增碳剂加入钢液,再将1/3的增碳剂放入钢包,冲入少量钢水搅拌,熔化后回冲炉内钢液增碳,共操作2次,然后打渣加合金。合金混合熔化后出钢,合金液温度达到1500℃℃出炉。然后钢水浇注冲入钢包,浇注前将剩余的铝锭1.64kg(总加入量的一半)和变质剂金属钪0.35kg(总加入量的一半)提前破碎成10mm左右的小块,按所述钢水重量的一半置于钢包底部,用包内冲入法对钢水进行变质处理,当钢水冲入包内1/2时投入另外50%的稀土变质剂,前后两次稀土变质剂不同时期的加入保证了稀土收得率在75%,铝锭的熔点远低于稀土变质剂,小块状的铝锭将钢水剩余的游离氧结合形成氧化物并上浮,高洁净度的钢水可充分发挥稀土变质剂的作用和保证稀土收得率。充分搅拌后,扒去钢液表面熔渣,静置5分钟后,进行砂箱浇注,浇注温度为1400℃,经过搅拌均匀后浇入已经烘干的砂箱中。当铸件在砂箱中形成外壳并逐渐变为火红色时,迅速脱模后投入油槽中进行快冷处理,为避免开裂及变形,并快速通过不稳定的奥氏体区,油淬至450℃左右成暗红色时,迅速将导板提出油面,导板表面沾带的油会首先冒出白色的烟,随后发生着火现象,导板就在这种着火燃烧的油淬条件下继续冷却,待油燃尽后,导板空冷至60℃后再放入热处理炉中650℃下保温12小时出炉空冷,完成高温时效处理,得到成品。该制造方法下的高合金铸钢导板在线材轧机上进行考核轧制,使用寿命为270h,轧钢量806t。
78.实施例2
79.采用1吨中频炉冶炼,其钢水的化学成分(重量百分比wt%)为:c1.5,si1.0,mn1.55,p0.035,s0.030,cr21,ni8,mo0.65,v2.5,al0.25,sc0.04,其余为fe和无法检测的
微量杂质。
80.首先熔化钢铁基料(工业废钢),首选含硅锰钒合金的钢铁基料,其化学成分(重量百分比wt%)为:c:0.13,si0.35,mn0.7,p0.35,s0.35,v0.021,加入生铁640kg。当温度达到1610℃时,首先插铝脱氧,投入纯铝锭1.35kg(总加入量的一半),然后按照钢水所述化学成分的质量配比添加合金,依次为增碳剂、锰铁、硅铁、钼铁、铬铁、钒铁和镍板,合金加入量为:碳粉(增碳剂)13.8kg,含硅量为75%的硅铁7.0kg,97%的纯锰7.0kg,含钼量为59%的钼铁10.0kg,含量为100%铬铁211kg,含钒量为80%的钒铁32.8kg,100%的纯镍80kg。增碳剂加入高温钢液会引起喷溅,并且加入时间过早,附着在炉底、炉壁的增碳剂不易熔入钢液,加入时间过迟则失去了增碳的时机,造成熔炼、升温时间的延迟。加入方法上,增碳剂采取分批加入,先将1/3的增碳剂加入钢液,再将1/3的增碳剂放入钢包,冲入少量钢水搅拌,熔化后回冲炉内钢液增碳,共操作2次,然后打渣加合金。合金混合熔化后出钢,合金液温度达到1510℃出炉。然后钢水浇注冲入钢包,浇注前将剩余的铝锭1.35kg(总加入量的一半)和变质剂金属0.30kg(总加入量的一半)提前破碎成10mm左右的小块,按所述钢水重量的一半置于钢包底部,用包内冲入法对钢水进行变质处理,当钢水冲入包内1/2时投入另外50%的稀土变质剂,前后两次稀土变质剂不同时期的加入保证了稀土收得率在68%,铝锭的熔点远低于稀土变质剂,小块状的铝锭将钢水剩余的游离氧结合形成氧化物并上浮,高洁净度的钢水可充分发挥稀土变质剂的作用和保证稀土收得率。充分搅拌后,扒去钢液表面熔渣,静置7分钟后,进行砂箱浇注,浇注温度为1390℃,经过搅拌均匀后浇入已经烘干的砂箱中。当铸件在砂箱中形成外壳并逐渐变为火红色时,迅速脱模后投入油槽中进行快冷处理,为避免开裂及变形,并快速通过不稳定的奥氏体区,油淬至550℃左右成暗红色时,迅速将导板提出油面,导板表面沾带的油会首先冒出白色的烟,随后发生着火现象,导板就在这种着火燃烧的油淬条件下继续冷却,待油燃尽后,导板空冷至80℃后再放入热处理炉中680℃下保温10小时出炉空冷,完成高温时效处理,得到成品。该制造方法下的高合金铸钢导板在h型钢轧机上进行考核轧制,使用寿命为312h,轧钢量883t。
81.实施例3
82.采用1吨中频炉冶炼,其钢水的化学成分(重量百分比wt%)为:c1.2,si0.9,mn1.4,p0.035,s0.030,cr20,ni7,mo0.6,v1.8,al0.17,sc0.35,其余为fe和无法检测的微量杂质。
83.首先熔化钢铁基料(工业废钢),首选含硅锰钒合金的钢铁基料,其化学成分(重量百分比wt%)为:c:0.13,si0.35,mn0.7,p0.30,s0.30,v0.021,加入生铁670.0kg。
84.当温度达到1600℃时,首先插铝脱氧,投入纯铝锭1.0kg(总加入量的一半),然后按照钢水所述化学成分的质量配比添加合金,依次为增碳剂、锰铁、硅铁、钼铁、铬铁、钒铁和镍板,合金加入量为:碳粉(增碳剂)11.5kg,含硅量为75%的硅铁6.0kg,97%的纯锰4.0kg,含钼量为59%的钼铁10.0kg,含量为100%铬铁200.0kg,含钒量为80%的钒铁20.0kg,100%的纯镍70kg。增碳剂加入高温钢液会引起喷溅,并且加入时间过早,附着在炉底、炉壁的增碳剂不易熔入钢液,加入时间过迟则失去了增碳的时机,造成熔炼、升温时间的延迟。加入方法上,增碳剂采取分批加入,先将1/3的增碳剂加入钢液,再将1/3的增碳剂放入钢包,冲入少量钢水搅拌,熔化后回冲炉内钢液增碳,共操作2次,然后打渣加合金。合金混合熔化后出钢,合金液温度达到1500℃℃出炉。然后钢水浇注冲入钢包,浇注前将剩余
的铝锭1.0kg(总加入量的一半)和变质剂金属钪0.25kg(总加入量的一半)提前破碎成10mm左右的小块,按所述钢水重量的一半置于钢包底部,用包内冲入法对钢水进行变质处理,当钢水冲入包内1/2时投入另外50%的稀土变质剂,前后两次稀土变质剂不同时期的加入保证了稀土收得率在73%,铝锭的熔点远低于稀土变质剂,小块状的铝锭将钢水剩余的游离氧结合形成氧化物并上浮,高洁净度的钢水可充分发挥稀土变质剂的作用和保证稀土收得率。充分搅拌后,扒去钢液表面熔渣,静置6分钟后,进行砂箱浇注,浇注温度为1410℃,经过搅拌均匀后浇入已经烘干的砂箱中。当铸件在砂箱中形成外壳并逐渐变为火红色时,迅速脱模后投入油槽中进行快冷处理,为避免开裂及变形,并快速通过不稳定的奥氏体区,油淬至510℃左右成暗红色时,迅速将导板提出油面,导板表面沾带的油会首先冒出白色的烟,随后发生着火现象,导板就在这种着火燃烧的油淬条件下继续冷却,待油燃尽后,导板空冷至60℃后再放入热处理炉中650℃下保温12小时出炉空冷,完成高温时效处理,得到成品。该制造方法下的高合金铸钢导板在h型钢轧机上进行考核轧制,使用寿命为350h,轧钢量962t。
85.尽管为说明目的公开了本发明的实施例,但是本领域的技术人员可以理解:在不脱离本发明及所附权利要求的精神和范围内,各种替换、变化和修改都是可能的,因此,本发明的范围不局限于实施例所公开的内容。