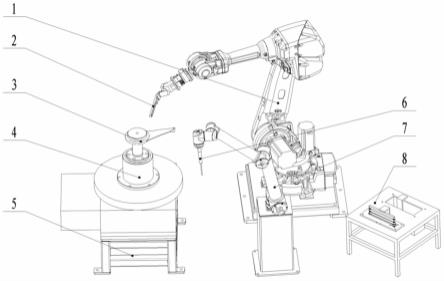
1.本发明涉及工业机器人自动磨抛加工技术领域,具体涉及一种针对复杂曲面的机器人自动磨抛加工装备与加工方法。
背景技术:2.在非规则复杂曲面零件加工领域,例如以航空发动机叶盘、叶片为典型代表的航空结构件,大量安装于航空发动机中,因其叶面结构复杂,性能要求高,加工难度大,因此针对复杂曲面的精密磨抛加工技术成为掣肘航空制造业发展的核心关键。
3.航空发动机叶盘、叶片的叶面形状自由不规则,结构灵活多样,表面特征多变,是典型的非规则复杂曲面,对加工过程的适应性和灵活性有着极高的要求。数控机床成本高、灵活性差,在柔顺性、适应性和运动空间等方面都具有较大局限性,不适用于此类非规则复杂曲面的精密加工过程。工业机器人虽自身具备传统自动化机床等所不具有的独特优势,如智能性和灵活性,但仍然缺乏针对复杂曲面的具有良好适应性的完整工艺方法。目前此类非规则复杂曲面表面的磨抛加工仍是工人手工进行,产品质量严重依赖于工人的经验和技术水平,表面一致性差,加工质量得不到保证,效率低、废品率高,与现代自动化生产的模式相矛盾。并且加工过程产生的噪声、粉尘等恶劣环境对工人的身体健康也有着极大地危害。
技术实现要素:4.针对现有技术存在的上述不足之处,本发明的目的在于提供一种针对复杂曲面的机器人自动磨抛加工装备与加工方法,能够实现多种类型复杂曲面的自动磨抛加工。以本发明的装备为加工工艺系统,采用零件特征识别,复杂曲面提取、磨抛轨迹生成、位置找正、运动规划及工件检测等,可以实现机器人自动磨抛复杂曲面,获得高质量,低成本的零件加工效果。
5.为实现上述目的,本发明所采用的技术方案如下:
6.一种针对复杂曲面的机器人自动磨抛加工装备,包括加工机器人、加工工具模块、待加工曲面、变位机、工作台、测量工具模块、测量机器人模块和砂带自动更换模块;其中:待加工曲面安装在变位机上,将变位机安装在工作台上,加工机器人与测量机器人并列安装于工作台一侧,砂带自动更换模块安装在加工机器人斜后方,加工工具模块安装于加工机器人末端执行器上;
7.所述加工工具模块包括磨抛加工部分和机器人端工具快换结构;磨抛加工部分包括砂带、气动砂带机、夹具、砂带机支撑台和工具端快换法兰,砂带安装于气动砂带机上,气动砂带机通过夹具与砂带机支撑台连接,砂带机支撑台、工具端快换法兰通过螺栓进行连接;机器人端工具快换结构包括顺序连接的机器人端快换法兰、力传感器和机器人末端执行器连接法兰,机器人末端执行器连接法兰与机器人末端执行器连接;通过机器人端快换法兰与工具端快换法兰,实现机器人自动更换磨抛工具;
8.所述力传感器用于实时测量磨抛过程中力的大小,作为反馈输入控制系统,实现闭环控制;测量工具模块包括雷尼绍测头,雷尼绍测头安装于测量机器人末端执行器上,通过测量机器人机械臂的移动,测量加工件的信息;
9.所述砂带自动更换模块包括砂带拆卸部分和砂带自动安装部分;其中:砂带拆卸部分包括第一l形砂带机限位板与废弃砂带收集槽;砂带自动安装部分包括备用砂带、同步齿形带、第二l形砂带机限位板、螺杆、固定板和驱动电机。
10.该加工装备还包括上位系统与机器人、测头、砂带更换电机之间的三线程异步通信系统;上位系统通过工业互联网与三大执行器件进行双向通信,下发工作指令,接受执行期间回传的传感数据、执行状态和位置信息并基于反馈信息做出下一步决策。
11.所述加工工具模块中,通过工具端快换法兰、机器人端快换法兰实现磨抛工具的快速更换;磨抛工具与夹具之间通过螺栓连接形成固定结构,并且磨抛工具与机器人末端法兰盘端面z轴成一钝角,便于伸入不规则的狭小空间结构中进行磨抛加工,以及避免机器人在工作中各关节轴处于奇异点;加工工具模块包含力传感器,能够实现加工过程的磨削力检测,为力控系统提供反馈,实现闭环控制,减少力控误差。
12.所述砂带自动更换模块由砂带拆卸部分和砂带自动安装部分组成;加工工具模块由机器人带动,运行至砂带拆卸装置位置,气动砂带机支撑臂上表面与第一l形砂带机限位板下表面平行,并使砂带机支撑臂末端突出卡扣抵住第一l形砂带机限位板,使得砂带机支撑臂弹簧收缩一段距离放松砂带,此时报废砂带在重力作用下自然落入废弃砂带收集箱内,完成砂带自动拆卸;
13.拆卸废弃砂带后将砂带机移动至砂带自动安装部分,使支撑臂上表面与第二l 形砂带机限位板下表面平行,并使砂带机支撑臂末端突出卡扣抵住第二l形砂带机限位板,使得砂带机支撑臂弹簧收缩一段距离便于安装新砂带,此时气动砂带机主动轮与支撑臂接触轮轴分别与砂带自动安装部分两个螺杆轴重合。此时启动驱动电机,在同步齿形带的作用下备用砂带开始上升,当备用砂带上升至指定位置时,驱动电机停止转动,机器人带动气动砂带机向后回撤一段距离,支撑臂弹簧回弹,实现砂带的预紧,砂带安装完成。
14.所述针对复杂曲面的机器人自动磨抛加工方法,包括:具有多方向性和几何特征自适应性的磨抛加工轨迹生成方法,通过对特征曲面的提取与离散化处理获取曲面几何特征,以去除分布的均匀程度为目标导向优化轨迹参数,基于叶盘表面几何特征规划加工路径,针对不同区域的几何特征调整轨迹形状参数和疏密程度,生成具有多方向性的摆线加工轨迹,并最终输出机器人可识别的轨迹程序文件。
15.该加工方法包含一种基于材料去除模型的动态运动规划方法,基于去除模型和目标去除反解preston方程,获取变化光顺平滑的适应局部几何特征的动态加工速度及加工力方案,获得随表面几何特征变力变速的磨抛加工控制策略,实现整体叶盘的磨抛加工。
16.本发明具有以下有益效果及优点:
17.1.本发明所提出磨抛加工方案能够代替技术工人进行磨抛作业,通过自动化,标准化,统一化的加工流程提升表面加工质量,有效保证加工质量的稳定性和一致性,同时降低加工成本及工人的劳动强度,提升复杂曲面工件的磨抛加工质量和效率。
18.2.本发明采用一种砂带自动更换装置,实现了砂带的自动更换,避免因砂带磨损产生磨抛效果的波动,保证了加工质量。砂带自动更换装置同时进一步提升了磨抛加工过
程中的自动化程度,节约人力成本,并为长时间、大批量、可持续的磨抛过程提供了可行性。
19.3.本发明采用一种具有多方向性和几何特征自适应性的磨抛加工轨迹生成方法进行离线轨迹规划,从而抑制加工表面条形纹理和规则残差高度的产生,减少过切或欠加工区域的产生,提高加工的表面质量,保障磨抛效果。同时此种离线轨迹生成算法能够使得本发明可适用于除整体叶盘外各种类型的复杂曲面磨抛加工,且都具有良好的磨抛加工效果,保证自动化加工过程的可行性和通用性。
20.4.本发明采用一种基于材料去除模型的动态运动规划方法,根据几何特征和目标去除调节机器人当前位姿下的目标力和速度,保证工件表面的去除均匀性和一致性,提高工件加工质量。
21.5.本发明采用雷尼绍测头实时检测工件位置,防止实际磨抛过程中工件放置偏差或加工轨迹偏移,有效补偿和调整加工刀具的位置和姿态精度,保证加工精度。同时还对磨抛加工完成的表面进行检测,以确保加工效果满足需求,保证工件的可用性和可靠性,提高加工过程的成品率。
附图说明
22.图1为本发明系统装置总体结构示意图。
23.图2为待加工曲面示意图。
24.图3为磨抛加工轨迹示意图。
25.图4为磨抛加工工具示意图示意图。
26.图5为测量工具示意图。
27.图6为系统通讯方案示意图。
28.图7为复杂曲面网格化示意图及其参数化结果示意图;其中:(a)复杂曲面网格化示意图;(b)参数化结果示意图。
29.图8为更换自动砂带装置整体示意图及砂带自动安装装置细节示意图;其中:(a)更换自动砂带装置整体示意图;(b)砂带自动安装装置细节示意图。
30.图9为磨抛加工过程示意图。
具体实施方式
31.为了进一步理解本发明,以下结合实例对本发明进行描述,但实例仅为对本发明的特点和优点做进一步阐述,而不是对本发明权利要求的限制。
32.本发明是为了实现机器人自动磨抛航空发动机整体叶盘,替代人工操作加工,增强整体叶盘加工可靠性和表面质量一致性,提升加工效果和加工效率,降低劳动强度和加工成本,满足日益增长的高精度整体叶盘制造需求。
33.如图1所示,本发明提供的针对复杂曲面的机器人自动磨抛加工装备,包括工业机器人为主要基体的用于自动磨抛复杂曲面的装备,本装备包括11个工作模块:加工机器人1、加工工具模块2(主要包括:气动砂带机22、夹具23、砂带机支撑台24、工具端快换法兰25、机器人端快换法兰26、力传感器27)、待加工曲面3、变位机4、工作台5、测量工具模块6、测量机器人7、砂带自动更换模块8,如图 1所示。图2为待加工曲面3,其形状不规则,表面曲率各处不等且变化大。
34.进行磨抛加工时,本发明采用一种叶片特征提取的方法,根据待加工复杂曲面的三维模型,对其进行特征提取并离散化处理。利用复杂曲面参数化的方法,对提取的复杂曲面按几何特征及精度要求进行轨迹规划,其轨迹规划结果如图3。根据机器人操作系统控制程序要求,生成机器人可识别的轨迹程序文件,将生成的轨迹程序文件导入机器人控制器。根据材料去除模型动态计算加工力与刀具进给速度,机器人控制器控制加工机器人1以设定参数带动磨抛加工工具2沿着输入加工轨迹运动,完成复杂曲面的磨抛加工。
35.本发明所提出的加工工具模块2如图4所示。该加工工具模块2包括气动砂带机22、夹具23、砂带机支撑台24、工具端快换法兰25、机器人端快换法兰26和力传感器27;其中:气动砂带机22为主要磨抛工具,砂带21安装于气动砂带机 22上,气动砂带机22驱动砂带21转动实现对工件的磨抛加工。气动砂带机22与夹具23之间通过螺栓连接形成固定结构。夹具23底面通过螺栓固定在砂带机支撑台24上,砂带机支撑台24与工具端快换法兰25之间通过螺栓固连,工具端快换法兰25用于磨抛工具的更换。气动砂带机22支撑臂与加工机器人1末端法兰盘端面z轴成一钝角,便于伸入不规则的狭小空间结构中进行磨抛加工,以及避免机器人在工作中各关节轴处于奇异点。以上各部分组成加工工具模块2,用以实现复杂曲面磨抛加工。
36.机器人端快换法兰26、力传感器27、机器人末端执行器连接法兰28顺序连接,机器人末端执行器连接法兰28与机器人末端执行器连接。以上各部分组成机器人端的工具快换结构,通过机器人端快换法兰26与工具端快换法兰25,实现机器人自动更换磨抛工具。力传感器27用于实时测量磨抛过程中磨抛力的大小,并将测得的磨抛接触力数值回传给控制系统,与预设的磨抛接触力比对,并进行补偿,从而实现恒力磨抛加工。
37.本发明所提出的测量工具模块6包括雷尼绍测头,如图5所示,通过连接件安装于测量机器人7末端执行器上。通过测量机器人7带动测量工具模块6移动,测量加工件的信息。磨抛加工过程中,加工机器人1运动精度低,变位机4也存在运动误差,引入测量工具可以用于识别并设定工件,进行工件位置测量并自动修正偏置值,替代手动测量设定误差过程完成位置找正,提高加工精度,减小加工误差,增强无人加工的可靠性及生产灵活性,降低废品率。同时用以检测工件表面质量并确认成品工件的尺寸,确认加工效果满足指标要求,保证加工零件可用性和可靠性。
38.本发明所提出的加工方案为保证磨抛加工过程中产生的粉末引起粉尘爆炸,采用常规除尘装置,在磨抛加工过程中对磨抛部位产生的粉末进行吸尘。除尘装置吸尘口安装在加工机器人1末端执行器上,通过导引管将吸尘口对准磨抛部位,在磨抛加工过程中达到吸尘的目的。为避免磨抛加工产生的热量影响磨抛加工质量,以及磨抛加工中产生的火花对工件表面造成灼烧,在磨抛加工过程中采用切削液对磨抛部位进行喷洒。切削液通过在机器人末端执行器上安装的喷嘴进行喷洒。
39.本发明所提出加工方案工具坐标系的标定(坐标系t),采用加工机器人1自身功能标定磨抛加工工具的坐标系,选择磨抛加工工具模块2上砂带机22前端支撑臂接触轮圆弧上表面中间点为对刀点进行工具坐标的标定。建立工具坐标系各轴方向:砂带机22上表面与待加工工件3中间轮盘上表面平行,工具坐标系原点为砂带机22的对刀点,磨抛工具坐标x轴、y轴方向根据离线轨迹规划程序的加工方向设定,z轴方向根据右手定则确定。
40.本发明所提出加工方案工件坐标系的标定(坐标系b),采用间接法在整体叶盘工
件上建立工件坐标系。首先在三维制图软件中选择待加工曲面3上的四个特征点,并记录其在工件坐标系中的坐标值。使用已测量工件坐标系的工具尖点依次接近四个特征点,并在机器人示教器中输入对应三维模型中的坐标值。在完成以上操作后,由机器人控制器计算所建立的工具坐标系相对于机器人底座坐标系的变换关系,从而完成工具坐标系的标定。
41.本发明所提出的机器人自动磨抛复杂曲面方案,包含一种砂带自动更换模块8,由砂带拆卸和砂带自动安装两部分组成,如图8所示。砂带拆卸部分包括第一l形砂带机限位板81和废弃砂带收集槽82。砂带自动安装部分由备用砂带84、同步齿形带85、第二l形砂带机限位板86、螺杆87、固定板88和驱动电机89组成,如图8(b)所示。第二l形砂带机限位板86通过螺栓连接在固定板88一侧,且第二 l形砂带机限位板86侧面与固定板88上表面垂直。固定板88下方安装有驱动电机 89。驱动电机89通过联轴器与螺杆87连接,在固定板88另一侧安装有同样的螺杆,两螺杆下方安装有配套同步带轮,通过同步齿形带85连接。当驱动电机89转动时,在同步齿形带85的作用下,可实现两螺杆的同步转动。两根螺杆之间安装有备用砂带84,备用砂带84可随着螺杆的转动实现上下移动。更换砂带时,机器人首先带动加工工具模块2移动到砂带拆卸装置位置,使砂带机22支撑臂上表面与第一l形砂带机限位板81上表面平行,并使砂带机支撑臂末端突出卡扣83抵住第一l形砂带机限位板81,使得砂带机支撑臂弹簧收缩一段距离放松砂带,此时报废砂带在重力作用下自然落入废弃砂带收集箱82内,完成砂带自动拆卸。拆卸废弃砂带后将砂带机22移动至砂带自动安装部分,使支撑臂上表面与第二l形砂带机限位板86上表面平行,并使砂带机支撑臂末端突出卡扣83抵住第二l形砂带机限位板86,使得砂带机支撑臂弹簧收缩一段距离便于安装新砂带,此时气动砂带机 22主动轮与支撑臂接触轮轴线分别与砂带自动安装部分两个螺杆轴轴线重合。此时启动驱动电机89,在同步齿形带85的作用下备用砂带84开始上升,当备用砂带 84上升至指定位置时,驱动电机89停止转动,加工机器人1带动气动砂带机22向后回撤一段距离,支撑臂弹簧回弹,实现砂带的预紧,砂带安装完成。
42.本发明的控制通讯方案包含三部分,工作线程如图6所示。分别为机器人控制器工作线程、测头工作线程、砂带更换电机工作线程,以实现四者之间的同步通讯连接,完成整体叶盘高精度机器人磨抛加工。上位系统通过工业互联网派发状态指令到每个工作线程,指导对应控制器下发控制指令。执行器件完成指令后反馈执行状态到上位系统,上位系统判断系统是否出现异常,计算测头检测结果与理想位置的偏差,从而生成偏差补偿或误差控制决策,实现控制闭环。其中机器人的动作指令需要机器人本体及机器人柔顺控制器配合控制实现,工业机器人本体与机器人柔顺控制器之间的通信采用高可靠性的tcp/ip(transmission control protocol/internetprotocol)通信协议,二者之间的通信实时性较高,采用数据流的方式进行通信,基于tcp/ip套接字与总控建立连接,底层使用握手信号来保证交互信息的完整性,同时建立独立的心跳连接,保证通信始终处于连接状态,保证指令下发的实时性和可靠性。套接字以字符串的形式发送指令数据支持数据打包和数据格式自定义,具有较好的自主性和适应性。机器人柔顺控制器ati力传感器27之间使用以太网进行通信,采用高速轻量的udp(user datagram protocol)协议,提供高达7000hz 的传输频率;机器人本体按照运动指令控制机器人末端加工刀具达到指定位姿,实现磨抛加工。
43.本发明包括一种具有多方向性和几何特征自适应性的磨抛加工轨迹生成方法,基于复杂曲面的局部特征,生成满足光顺、多方向的曲面加工轨迹。这种轨迹能够抑制表面条
形加工纹理的产生,保证表面各处的加工质量一致性。此轨迹生成需要对提取的曲面进行网格化,在网格曲面基础上进行路径的生成与规划。本发明首先通过delaunay三角网格划分获得均匀覆盖曲面的网格划分,方法包括但不限于网格前沿算法,具体为以加工表面的边界为网格的初始前沿,按三角网格单元的形状、尺度等要求向域内生成节点、连接单元,同时更新网格前沿,如此逐层向剖分域内推进,直至所有空间被剖分。此法最大的特征就是能够生成复杂形状的非结构网格,划分后的网格如图7(a)。delaunay三角网格划分可以最大程度上均匀三角网格分布,避免狭长三角形产生,对网格特征点的均匀分布有着巨大的意义。划分网格后提取其网格顶点作为特征信息点,并记录其对应几何特征信息,主要为当前点的位置、高度等。将三维曲面通过参数化获得复杂曲面的自由域平面展开图,具体为从三维曲面到平面的一个光滑双射。将三维曲面映射到二维图像,进行所需变换。方法包括但不限于基于arap(as-rigid-as-possible)的非固定边界的网格参数化方法等,具体为首先将三维表面用普通方法参数化到uv平面上,初始化第一个全局变换矩阵j。在local操作中,将每个三角形拆开作为一个独立的面,固定全局变换矩阵j求出当前全局变换下每个三角形可以处于的最佳局部变换l。global操作中,固定局部变换l,找到最适合目前局部变换的全局变换矩阵j。不断迭代local及 global操作,更新局部变换l和全局变换j,直到结果稳定。三维曲面于其参数化后二维曲面如图7(b)所示。参数化三维曲面之后结合原三维模型几何特征信息绘制平面轨迹导引线。具体为,使用参数化后的平面边界作为导引线初始位置,在导引线上平均分布多个点,将分布后的点向参数化后平面内侧进行偏置,其中偏置的走向和距离由该点位几何特征信息即该点在三维曲面上的曲率决定,偏置的走向为三维曲面上该点的高斯曲率方向,偏置的距离与三维曲面上该点的高斯曲率成正比,将导引线上所有点进行偏置后进行连线并将连线进行平滑处理即获得下一条导引线。按此方法重复直至导引线完全超出参数化后平面,将所有导引线首尾相以获得使三维曲面均匀去除的导引线。之后沿导引线绘制加工摆线,进一步提高轨迹多方向性并保证其光顺性,其中摆线半径为导引线偏置距离,摆线形状步长等由该点位几何特征即曲面在特征点处的曲率和弧长决定且随着曲面各处几何特征的变化而不断变化根据摆线形状参数和引导线生成在参数化平面的加工轨迹,将参数化平面的轨迹映射回三维空间曲面上,获得贴合曲面,包覆良好的磨抛加工轨迹。在此基础上通过优化算法微调轨迹形状参数,方法包括但不限于使用遗传算法对摆线形状参数进行优化分析。遗传算法是模拟自然界遗传机制和生物进化论而成的一种并行随机搜索最优化方法。遗传算法将“优胜劣汰,适者生存”的生物进化原理引入优化参数形成的编码串联群体中,按所选择的适应度函数并通过遗传中的复制、交叉及变异对个体进行筛选,使适适应度高的个体被保留下来,组成新的群体,新的群体既继承了上一代的信息,又优于上一代。这样周而复始,群体中个体适应度不断提高,直到满足一定的条件。具体为将摆线形状参数作为决策变量,将摆线参数转化为2进制数并首尾连接,表示群体中的个体基因型建立被加工后表面质量模型,用方差表示加工表面去除量分布的均匀程度,并将方差值最小作为个体适应度。由于方差的值域总是非负的并且优化目标是求函数的最小值,选个体适应度的倒数作为目标函数。随机生成个体的基因编码。对基因编码进行解码并计算其适应度。解码时按设定长度截断编码串再转化为对应十进制数即为摆线形状参数。个体以适应度为原则进行选择,适应度高的个体繁殖下一代数目多,适应度小的个体繁殖数目少。随后进行复制、交叉、变异的操作。复制操作可以通过随机方法来实现。首先产
生0~1之间均匀分布的随机数,若某串的复制概率为40%,则当产生的随机数在 0.40~1.0之间时,该串被复制,否则被淘汰。交叉的过程为:在匹配池中任选两个染色体,随机选择一点或多点交换点位置;交换双亲染色体交换点右边的部分,即可得到两个新的染色体数字串。变异运算用来模拟生物在自然的遗传环境中由于各种偶然因素引起的基因突变,它以很小的概率随机地改变遗传基因(表示染色体的符号串的某一位)的值,随机地将染色体的某一个基因由1变为0,或由0变为1。按上述方法进行迭代,直至最优个体适应度和群体适应度不再上升时,则算法迭代过程收敛,算法结束,寻得使表面加工后的平面质量最好的摆线形状参数并作为正式加工中的摆线形状参数。以此获得去除分布均匀、加工效果良好的磨抛轨迹。
44.本发明包括一种基于材料去除模型的动态运动规划方法,根据曲面几何特征动态规划机器人末端关节的运动及加工力。在同样的加工条件下,表面各处的几何特征差异会导致各处去除效果的差异,从而破坏加工表面质量的均匀性和一致性,从而影响加工质量和零件性能。遍历加工轨迹路径点,结合几何特征和默认参数下理论去除深度及接触面积半径,对照目标去除方法计算去除差值。基于材料去除模型,根据差值反解preston方程,获取不同位置适应局部几何特征的理想加工速度及加工力。根据加工轨迹顺序,将曲面各点速度和力拟合为光滑无突变的曲线,并按此变力变速的运动规划方案执行加工轨迹,完成基于几何特征自适应的复杂曲面磨抛加工。
45.应用发明本装备和方法的具体实施方式步骤包括:
46.1.将加工工具模块2安装在加工机器人1的第六轴末端法兰盘上,并与工作台定位块进行对刀定位,完成加工机器人1的基坐标与加工工具模块2的坐标标定,实现坐标标定统一。
47.2.将待加工曲面3安装到变位机4上,将变位机4安装在工作台5上,进行定位和夹紧。定位过程中以工作台上的定位块为参照物完成待加工曲面3的定位。把待加工曲面3的坐标与加工机器人1的基坐标进行统一标定,将待加工曲面3、磨抛加工工具2及测量工具模块6都统一到加工机器人1的基坐标上,完成工艺系统的坐标标定统一。
48.3.将待加工曲面3的三维模型导入轨迹离线生成软件,提取待加工曲面3的几何特征,离散化整体叶盘包含曲面。根据标定好的工件坐标系,设置工艺参数,计算基于几何特征自适应的多方向性加工轨迹。按步长进行轨迹离散化处理,生成加工轨迹。转换生成机器人系统可识别的轨迹程序文件,将规划好的轨迹程序文件导入机器人控制器。
49.4.将去除模型环境系数及其他参数导入主控,计算基于preston方程的材料去除模型。导入离线轨迹,设定目标去除,系统反解计算变力变速运动规划方案,生成控制策略。
50.5.测量工具模块6对待加工曲面3进行安装位置检测与找正,测量实际安装与理论安装位置误差,并将误差值返回主控,微调轨迹规划位姿,适应当前加工场景,保证磨抛加工精度。
51.6.机器人控制器驱动机器人按照规划好的磨抛加工轨迹带动磨抛加工工具2 完成进给运动。加工过程中磨抛加工工具2由加工机器人1带动,按照生成加工轨迹以设置的变力变速控制策略开始进行磨抛加工。
52.7.加工过程中,若砂带磨损,加工机器人1带动磨抛加工工具2到砂带自动更换模块8进行砂带自动更换。
53.8.整个磨抛加工过程如图9所示。