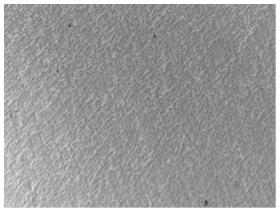
1.本发明属于合金制造领域,涉及一种铜铁合金,尤其涉及一种铁骨架的铜铁合金及其制备方法。
背景技术:2.高强度高导电铜合金作为具有优良综合性能和力学性能的功能结构材料,具有较高的强度和良好的塑性及优良的导电性能,是制备电阻焊电极、缝焊滚轮、焊矩喷嘴、电气工程开关触桥、集成电路引线框架、高速铁路列车架空导线芯等器件的优良材料。从铜合金强化和电传导机制方面分析,铜合金的高强度和高导电性高之间存在着矛盾,使铜合金得到强化后,其导电率必然出现某一程度的下降,且强度提高得多,随之合金的电阻增加得多,导电率下降得也多。这一矛盾贯穿于高强度高导电性铜合金研究与开发的始终。
3.cu-fe合金是其中成本最低的一种合金系,已有不少学者进行了研究。但由于铁在铜中有较高的溶解度,铁合金整体性能。铜铁合金若铁含量不同、制备方式不同,则其组织结构也存在差异,其产品性能也不相同。目前业界制备铜铁合金的方法有真空感应熔炼、粉末冶金固相烧结法等,这些方法有的成本较高,有的无法实现量产,有的在性能上存在缺陷,比如真空感应熔炼法由于fe在铜中固溶度低,很容易造成偏析,无法制备更高强度和铁含量铜铁合金,并且由于cu基体中固溶fe,形成杂质造成电子散射影响导电性能。
4.粉末冶金固相烧结法作为一种铜铁原位合金制备方法,相比熔铸法等传统方法,最大优势在于可以限制fe在cu基体的溶解度,并且获得近似于cu-cr、cu-nb等相近的综合性能。但是固相烧结所得到的产品致密度差(铜原子并不能完全充满骨架),结合性差(固相烧结金属结合形式主要为烧结颈,因此强度无法与金属键结合形式强度相比),加工性差(由于结合形式特殊,塑性较差,组织结构很难改变)。
技术实现要素:5.为解决现有技术中存在的技术问题,本发明提供一种铁骨架的铜铁合金及其制备方法,所述制备方法解决了传统工艺存在的铜铁合金偏析问题,制备得到的铜铁合金致密度高,具有优异的导电性能、机械强度、耐磨性以及硬度。
6.为达到上述技术效果,本发明采用以下技术方案:
7.本发明目的之一在于提供一种铁骨架的铜铁合金的制备方法,所述制备方法包括:
8.将铁粉末与造孔剂混合后进行压制和预烧结,得到铁骨架;
9.将铜材置于所述铁骨架表面进行烧结,完成渗铜,得到所述铜铁合金。
10.本发明中,通过粉末冶金液相烧结的方法,将铜熔渗进入铁骨架中,铁粉颗粒之间形成烧结颈部,铜则在烧坯中形成网状结构,该方法制备得到的铜铁合金,有着更好的导电性,并且由于抑制了第三相生成,铜和铁各自的优点特性都得以保留。
11.作为本发明优选的技术方案,所述铁骨架的制备方法包括:
12.对铁粉进行还原处理后,与所述造孔剂混合,得到原料粉末;
13.将所述原料粉末依次进行压制以及预烧结处理,得到所述铁骨架。
14.作为本发明优选的技术方案,所述铁粉的平均粒度为10~30μm,如12μm、15μm、18μm、20μm、22μm、25μm或28μm等,但并不仅限于所列举的数值,该数值范围内其他未列举的数值同样适用。
15.优选地,所述还原处理在氢气气氛或真空条件下进行。
16.优选地,所述还原处理的温度为600~1000℃,如650℃、700℃、750℃、800℃、850℃、900℃或950℃等,但并不仅限于所列举的数值,该数值范围内其他未列举的数值同样适用。
17.优选地,所述还原处理的时间为2~4h,如2.2h、2.5h、2.8h、3h、3.2h、3.5h或3.8h等,但并不仅限于所列举的数值,该数值范围内其他未列举的数值同样适用。
18.作为本发明优选的技术方案,所述混合过程中,所述造孔剂至少分2次加入,如3次、4次、5次或6次等,但并不仅限于所列举的数值,该数值范围内其他未列举的数值同样适用。
19.优选地,所述造孔剂包括汽油和/或石蜡油。
20.优选地,所述混合的时间不低于6h,如6.5h、7h、7.5h、8h、8.5h、9h、9.5h或10h等,但并不仅限于所列举的数值,该数值范围内其他未列举的数值同样适用。
21.本发明中,混合的方法可以是将铁粉与部分造孔剂混合后,加入立式混合器中,搅拌30~60min后,再将剩余的造孔剂分批次加入,每批次间间隔1~3h,且每批次可以等量或不等量加入。
22.本发明中,可以通过控制造孔剂加入量,来调控铁骨架内部的蜂窝状结构的体积,即可通过制造孔剂加入量来调控铁骨架的密度,从而限定铜的渗入量,以达到调控铁铜合金中铁铜质量比的目的,从而调控铁铜合金的性能。因此,本发明对铁铜合金的比例以及造孔剂的加入量未做具体限定。
23.作为本发明优选的技术方案,所述压制前对所述原料粉末进行吹晾搅拌。
24.优选地,所述吹晾搅拌的时间为2~4h,如2.2h、2.5h、2.8h、3h、3.2h、3.5h或3.8h等,但并不仅限于所列举的数值,该数值范围内其他未列举的数值同样适用。
25.作为本发明优选的技术方案,所述压制包括钢模压制和/或静压压制。
26.本发明中,可以通过调控压制的压力来调控铁骨架的密度,从而限定铜的渗入量,以达到调控铁铜合金中铁铜质量比的目的。因此,本发明对压制的具体压力未做限定。同时,本发明还可同时调控压制压力以及造孔剂的加入量,来对铁骨架的内部多孔结构进行调控,以达到调控铁铜合金的性能的目的。
27.作为本发明优选的技术方案,所述预烧结为依次进行的一段预烧结和二段预烧结。
28.优选地,所述一段预烧结在氢气气氛或真空条件下进行。
29.优选地,所述一段预烧结的温度为300~500℃,如320℃、350℃、380℃、400℃、420℃、450℃或480℃等,但并不仅限于所列举的数值,该数值范围内其他未列举的数值同样适用。
30.优选地,所述一段预烧结的时间为3~6h,如3.5h、4h、4.5h、5h或5.5h等,但并不仅
限于所列举的数值,该数值范围内其他未列举的数值同样适用。
31.优选地,所述二段预烧结在氢气气氛下进行。
32.优选地,所述二段预烧结的温度为1050~1200℃,如1060℃、1070℃、1080℃、1090℃、1100℃、1110℃、1120℃、1130℃、1140℃、1150℃、1160℃、1170℃、1180℃或1190℃等,但并不仅限于所列举的数值,该数值范围内其他未列举的数值同样适用。
33.优选地,所述二段预烧结的时间为3~4h,如3.1h、3.2h、3.3h、3.4h、3.5h、3.6h、3.7h、3.8h或3.9h等,但并不仅限于所列举的数值,该数值范围内其他未列举的数值同样适用。
34.作为本发明优选的技术方案,所述烧结的温度为1100~1200℃,如1110℃、1120℃、1130℃、1140℃、1150℃、1160℃、1170℃、1180℃或1190℃等,但并不仅限于所列举的数值,该数值范围内其他未列举的数值同样适用。
35.优选地,所述烧结的时间为2~4h,如2.2h、2.5h、2.8h、3h、3.2h、3.5h或3.8h等,但并不仅限于所列举的数值,该数值范围内其他未列举的数值同样适用。
36.作为本发明优选的技术方案,所述铁骨架的铜铁合金的制备方法包括:
37.对铁粉在氢气气氛或真空条件下于600~1000℃进行还原处理2~4h后,与造孔剂混合;所述混合过程中,所述造孔剂至少分2次加入,所述混合的时间不低于6h,得到原料粉末;
38.对所述原料粉末进行吹晾搅拌2~4h,将所述原料粉末进行钢模压制和/或静压压制;
39.压制后进行预烧结处理,所述预烧结为依次进行的一段预烧结和二段预烧结;所述一段预烧结在氢气气氛或真空条件下进行,温度为300~500℃,时间为3~6h;所述二段预烧结在氢气气氛下进行,温度为1050~1200℃,时间为3~4h,得到所述铁骨架;
40.将铜材置于所述铁骨架表面进行烧结,所述烧结的温度为1100~1200℃,时间为2~4h,完成渗铜,得到所述铜铁合金。
41.本发明目的之二在于提供一种铁骨架的铜铁合金,所述铜铁合金由目的之一所述的制备方法制备得到。
42.与现有技术相比,本发明至少具有以下有益效果:
43.(1)本发明提供的铁骨架的铜铁合金的制备方法通过粉末冶金骨架烧结法制备铜铁合金,可以制备更高铁含量的高强度铜铁合金;而传统熔铸等方法,铜和铁熔点相差较大,铁密度相对铜低,因此容易出现铁相偏析,尽管目前有一些方法能改善传统熔铸工艺缺陷,如高温熔炼添加微量元素以减少铁元素液相分离;或采用精炼除气搅拌+半连铸+热轧制备铜铁合金带材;如低频电子搅拌+真空熔炼,但以上方法仅适用于fe含量较低、小规格样品试制;
44.(2)本发明提供的铁骨架的铜铁合金的制备方法有利于抑制第三相的生成,解决铜铁合金偏析问题,得到的铜铁合金组织均匀,并且由于铁含量高,拥有更优异的导电能力和强度、耐磨性、硬度等特性。
附图说明
45.图1为本发明制备得到的铜铁合金的金相图。
46.下面对本发明进一步详细说明。但下述的实例仅仅是本发明的简易例子,并不代表或限制本发明的权利保护范围,本发明的保护范围以权利要求书为准。
具体实施方式
47.为更好地说明本发明,便于理解本发明的技术方案,本发明的典型但非限制性的实施例如下:
48.实施例1
49.本实施例提供一种铁骨架的铜铁合金的制备方法,所述制备方法包括:
50.对500g铁粉在氢气气氛下于600℃进行还原处理4h后,与2g石蜡油混合,搅拌30min后,再分3次加入石蜡油,每次加入2g,每次间隔3h,得到原料粉末;
51.对所述原料粉末进行吹晾搅拌2h,将所述原料粉末进行静压压制,压坯的密度为5.7g/cm3;
52.压制后进行预烧结处理,所述预烧结为依次进行的一段预烧结和二段预烧结;所述一段预烧结在氢气气氛下进行,温度为300℃,时间为6h;所述二段预烧结在氢气气氛下进行,温度为1050℃,时间为4h,得到所述铁骨架;
53.将250g铜材置于所述铁骨架表面进行烧结,所述烧结的温度为1100℃,时间为4h,完成渗铜,得到所述铜铁合金。
54.实施例2
55.本实施例提供一种铁骨架的铜铁合金的制备方法,所述制备方法包括:
56.对1000g铁粉在氢气气氛下于1000℃进行还原处理2h后,与16g石蜡油混合,搅拌60min后,再分4次加入石蜡油,每次加入4g,每次间隔1h,得到原料粉末;
57.对所述原料粉末进行吹晾搅拌4h,将所述原料粉末进行静压压制,压坯的密度为;
58.压制后进行预烧结处理,所述预烧结为依次进行的一段预烧结和二段预烧结;所述一段预烧结在氢气气氛下进行,温度为500℃,时间为4h;所述二段预烧结在氢气气氛下进行,温度为1200℃,时间为3h,得到所述铁骨架;
59.将500g铜材置于所述铁骨架表面进行烧结,所述烧结的温度为1200℃,时间为4h,完成渗铜,得到所述铜铁合金。
60.实施例3
61.本实施例提供一种铁骨架的铜铁合金的制备方法,所述制备方法包括:
62.对1000g铁粉在氢气气氛下于700℃进行还原处理3.5h后,与16g石蜡油混合,搅拌40min后,再分4次加入石蜡油,每次加入8g,每次间隔2h,得到原料粉末;
63.对所述原料粉末进行吹晾搅拌3h,将所述原料粉末进行等静压压制,压制的压力为200mpa;
64.压制后进行预烧结处理,所述预烧结为依次进行的一段预烧结和二段预烧结;所述一段预烧结在氢气气氛下进行,温度为350℃,时间为5h;所述二段预烧结在氢气气氛下进行,温度为1100℃,时间为4h,得到所述铁骨架;
65.将360g铜材置于所述铁骨架表面进行烧结,所述烧结的温度为1150℃,时间为3h,完成渗铜,得到所述铜铁合金。
66.实施例4
67.对800g铁粉在氢气气氛下于900℃进行还原处理2.5h后,与8g石蜡油混合,搅拌45min后,再分4次加入石蜡油,每次加入8g,每次间隔2h,得到原料粉末;
68.对所述原料粉末进行吹晾搅拌3h,将所述原料粉末进行等静压压制,压制的压力为200mpa;
69.压制后进行预烧结处理,所述预烧结为依次进行的一段预烧结和二段预烧结;所述一段预烧结在氢气气氛下进行,温度为450℃,时间为4h;所述二段预烧结在氢气气氛下进行,温度为1100℃,时间为3.5h,得到所述铁骨架;
70.将240g铜材置于所述铁骨架表面进行烧结,所述烧结的温度为1150℃,时间为3.5h,完成渗铜,得到所述铜铁合金。
71.实施例5
72.对500g铁粉在氢气气氛下于800℃进行还原处理3h后,与8g石蜡油混合,搅拌45min后,再分4次加入石蜡油,每次加入2g,每次间隔2h,得到原料粉末;
73.对所述原料粉末进行吹晾搅拌3h,将所述原料粉末进行静压压制,压制的压力为150mpa;
74.压制后进行预烧结处理,所述预烧结为依次进行的一段预烧结和二段预烧结;所述一段预烧结在氢气气氛下进行,温度为400℃,时间为4.5h;所述二段预烧结在氢气气氛下进行,温度为1150℃,时间为3.5h,得到所述铁骨架;
75.将600g铜材置于所述铁骨架表面进行烧结,所述烧结的温度为1150℃,时间为3.5h,完成渗铜,得到所述铜铁合金。
76.实施例6
77.本实施例除了铁粉与8g石蜡油混合,搅拌45min后,再分4次加入石蜡油,每次加入4g,每次间隔2h,得到原料粉末;以及铜材的用量为360g,外其余条件均与实施例5相同。
78.实施例7
79.本实施例除了压制的压力为200mpa,铜材的用量为240g,外其余条件均与实施例5相同。
80.对比例1
81.本对比例将与实施例5等量的铁粉以及铜粉混合,进行粉末冶金制备得到铜铁合金。具体的条件为:
82.称取500g铁粉与600g铜粉,与5ml溶剂油混合,搅拌30min后,分3次加入溶剂油,每次间隔2h,每次加入2ml,得到原料粉末。
83.对所述原料粉末吹晾搅拌3h,然后利用钢模压制成型,压制压力为150mpa;
84.压制后进行烧结处理,温度1100℃,时间为6h,得到所述铜铁合金材料。
85.对比例2
86.本对比例将与实施例5等量的铁材以及铜材,通过熔铸法制备得到铜铁合金。具体的条件为:
87.将600g铜与500g铁放置在石墨模具中,加热到1400℃后烧结6h,得到所述材料。
88.对实施例1-7以及对比例1和2制备得到的铜铁合金的性能进行测试,其结果如表1所示。
89.密度的测试方法为排水法计算密度。
90.成分的测试方法为使用多功能射线检测仪检测。
91.硬度的测试方法为布氏硬度计测试铜铁合金样块。
92.表1
[0093] 密度/g/cm3硬度成分(fe含量)%实施例18.1614378.05实施例28.2113581.2实施例38.2313082.11实施例48.0915586.4实施例58.4012770.3实施例68.3012469.5实施例78.1015677.8对比例18.0217886.2对比例28.8011570.2
[0094]
与实施例5相比对比例1与对比例2,因为其产生了偏析,对比例1铁含量偏高,对比例2铜含量偏高,因此其硬度、密度均不符合要求,铁含量过多密度会偏低,硬度会偏高,但是电学性能会偏低,而铜含量过高密度会偏高,硬度偏低,物理性能较差。
[0095]
申请人声明,本发明通过上述实施例来说明本发明的详细结构特征,但本发明并不局限于上述详细结构特征,即不意味着本发明必须依赖上述详细结构特征才能实施。所属技术领域的技术人员应该明了,对本发明的任何改进,对本发明所选用部件的等效替换以及辅助部件的增加、具体方式的选择等,均落在本发明的保护范围和公开范围之内。
[0096]
以上详细描述了本发明的优选实施方式,但是,本发明并不限于上述实施方式中的具体细节,在本发明的技术构思范围内,可以对本发明的技术方案进行多种简单变型,这些简单变型均属于本发明的保护范围。
[0097]
另外需要说明的是,在上述具体实施方式中所描述的各个具体技术特征,在不矛盾的情况下,可以通过任何合适的方式进行组合,为了避免不必要的重复,本发明对各种可能的组合方式不再另行说明。
[0098]
此外,本发明的各种不同的实施方式之间也可以进行任意组合,只要其不违背本发明的思想,其同样应当视为本发明所公开的内容。