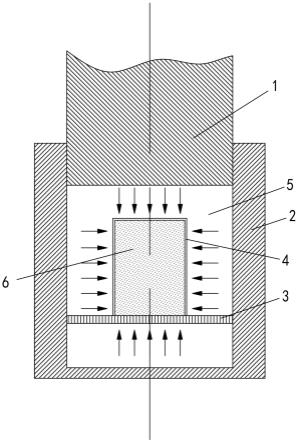
1.本发明涉及一种硬质合金/金属陶瓷制品的成型方法,该技术应用于制作硬质合金/金属陶瓷制品。
背景技术:2.粉末压制成型是利用外加压力将粉末成形所需形状的方法,粉末压制成形法是应用最普遍的成形方法,在粉末冶金和精细陶瓷等制品的生产中被广泛采用。但是压制成形过程中,由于颗粒间以及颗粒与模壁间存在的内、外摩擦引起压力损失使压坯各部位受力不均,因此压坯密度分布不均匀,最终导致制品尺寸收缩不均和性能不均。为了解决这个问题,陆续开发了双向压制、浮动压制、拉下式压制等压制方法,这些方法相对于单向压制虽然在密度均匀性上有所改善,但是由于在成型原理上无法解决产生密度差异的原因,因此无法从根本上解决粉末压制密度不均匀的现象。
3.冷等静压技术,作为一种全向压制成型技术,如图1所示,是在常温下,通常用橡胶或塑料作包套模具材料,以液体为压力介质,一般使用压力为100~630mpa,通过全向加压使粉体成型或使模压成型软坯密度均匀化,主要用于粉体材料成型,为进一步烧结提供坯体。作为一种成型工艺,与常规成型技术相比,等静压成型的制品密度高,一般要比单向和双向模压成型高5~l5%,压坯的密度均匀一致。在模压成型中,无论是单向、还是双向压制,都会出现压坯密度分布不均现象。这种密度的变化在压制复杂形状制品时,往往可达到10% 以上。冷等静压技术作为一种全向加压成型技术,虽然在成型坯件密度均匀性上有改善,但是该方法存在设备投资大(需专用特种设备)、效率低、容易污染坯体等缺点。
技术实现要素:4.本发明针对粉末压制成型容易出现密度不均匀的现象,冷等静压成型存在设备投资大、效率低、容易污染坯体的问题,开发一种粉末等静压成型方法。
5.为达到上述目的,本发明采用的结构技术方案是:一种粉末等静压成型方法,其特征在于,包括以下步骤:第一步,在橡胶制成的包套模内装入混合粉料或模压成型软坯,所述混合粉料是添加有1-4wt.%石蜡的硬质合金或金属陶瓷材料,所述模压成型软坯的材料也是添加有1-4wt.%石蜡的硬质合金或金属陶瓷材料;将装好的包套模放入真空箱中抽真空加热,加热温度为40-60℃,保温时间为20-60min;另一边,在金属模中装入软化点《70℃的树脂,将金属模加热到其内树脂完全软化;第二步,将第一步加热后的包套模放入金属模中,使包套模浸没于树脂中;第三步,采用压机驱动金属模的冲头,使冲头进入金属模的模腔中对树脂熔融液体施加20-100mpa压力,保压0-30s后卸压,取出包套模,割开包套模后即可得到成型压坯。
6.上述方案中,所述金属模外圈装有电加热圈,以电加热圈对金属模的加热。实际中也可以采用其他现有加热方式。
7.上述方案中,所述金属模由阴模、上冲以及带孔承料板构成,带孔承料板置于金属模的模腔内下部;所述第二步中包套模放置于带孔承料板上中心位置。
8.上述方案中,所述“树脂”可以采用萜烯树脂、石油树脂、酚醛树脂等各类软化点《70℃的树脂。
9.本发明方法的致密化机理与冷等静压工艺基本相同,两者之间的差异在于,采用本发明方法由于对带有成型剂的混合料进行加热使粉末颗粒重排与塑性变形进行得更加充分。因此,本发明方法在较低的压力下能获得更高、更均匀的压坯密度。本发明的低温低压致密化的贡献主要通过两个途径实现:首先,在低温下石蜡软化所产生的润滑作用能有效的降低颗粒之间的内摩擦使颗粒重排易于进行,便于获得紧密堆积结构;其次,石蜡润滑剂能大幅度降低粉末颗粒与模壁之间的摩擦,减小了施加的外压损失。低温等静压过程中颗粒之间的内摩擦与模壁摩擦的降低相对地提高了作用在粉末体上的有效压制压力,有利于压坯密度的提高。
10.本发明方法具有以下优势:(1)生产成本低:无需专用设备,设备投入低。
11.(2)压坯密度高:相同压制压力下,本发明专利工艺压制的压坯密度比传统方法高0.10~0.30g/cm3。
12.(3)压坯强度高:与传统模压工艺相比,采用本发明专利工艺制造的压坯强度可提高10%~40%,表面光洁度好。
13.(4)压制压力低:于获得相同密度的零件,本发明专利的压制压力至少降低40mpa,这都有利于提高设备寿命和制取形状复杂、面积大的产品。
14.(5)压坯密度分布均匀且烧结性能好:本发明专利工艺制取的坯件,密度均匀程度优于传统方法制取的零件。经过烧结后,烧结收缩率小,强度和韧性均高于传统工艺。
附图说明
15.图1为现有冷等静压技术的示意图;图2为本发明实施例一和实施例二中金属模压制状态的示意图。
16.图中:1、上冲;2、阴模;3、带孔承料板;4、包套模;5、树脂;6、混合粉料或模压成型软坯。
具体实施方式
17.下面结合附图及实施例对本发明作进一步描述:实施例一:一种粉末等静压成型方法,包括以下步骤:第一步,在包套模内按设计重量装入混合粉料,该混合粉料是添加有1-4 wt.%石蜡的硬质合金或金属陶瓷材料,具体本实施例中用的是含有2wt.%的56号石蜡的wc-co硬质合金混合料,即56号石蜡含量为2wt.%,而wc-co硬质合金混合料的含量为98 wt.%。而所述wc-co硬质合金混合料的具体配比是wc粒度0.8μm,含量为90wt.%;co粒度0.8μm,含量为10wt.%;在振实均匀后,将装好混合料的包套模放入真空干燥箱中抽真空加热,加热温度为40-60℃,保温时间为20-60min,在此最佳加热温度为60℃,保温时间为30min。
18.另一边,在一金属模中装入软化点《70℃的树脂,该树脂具体可采用萜烯树脂,树脂的装入量要保证融化后树脂熔融液体高度不小于包套模的高度,将金属模加热到其内树脂完全软化;具体是如图2所示,金属模外圈装有电加热圈,以电加热圈完成金属模加热。
19.所述金属模由阴模2、上冲1以及带孔承料板3构成,带孔承料板3置于金属模的模腔内下部,如图2所示。
20.第二步,将包套模放入金属模中,包套模没入金属模内树脂中,具体如图2所示,包套模4被置于金属模内带孔承料板3上中心位置,包套模4四周均是树脂5。
21.第三步,采用在普通四柱液压机驱动金属模的上冲1,使上冲1进入金属模的模腔中对树脂熔融液体施加压力20-100mpa,保压0-30s后卸压,取出包套模4,割开包套模4后即可得到成型压坯。
22.具体操作上,在第一步中的金属模一开始就可以先定位装夹于所述普通40吨四柱液压机的工作台上,后续对金属模的加热、橡腔包套模的放入均在压机工作台上完成,在第三步中直接以压机进行施力压制,如此操作较为方便。
23.采用本实施例方法压制的模压成型软坯生坯密度比传统方法高0.10g/cm3;压坯强度与传统模压工艺相比,可提高30%;烧结后硬坯尺寸精度比传统模压工艺提高20%。
24.实施例二:一种粉末等静压成型方法,包括以下步骤:第一步,将普通模压好的含2.5 wt.% 48号石蜡的圆柱形的金属陶瓷模压成型软坯用包套模包好,所述金属陶瓷模压成型软坯的材料具体配比是:ti(c,n)40-65%、ni粉22~32%、mo粉12~18%、wc粉5~8%;然后,放入真空干燥箱中抽真空加热,加热温度为50℃,保温时间为20min;同时,另一边在普通四柱液压机工作台上放置一副圆柱形的金属模,金属模外圈装有电加热圈,模具中加入一定量(融化后树脂熔融液体高度不小于橡胶软模具高度)的石油树脂(树脂软化点《60℃),将模具加热到60℃,待树脂完全软化。
25.第二步,将第一步包着模压成型软坯的包套模放入金属模的模腔中,包着模压成型软坯的包套模被浸没于石油树脂的熔融液体中;第三步,压机启动,上冲缓慢进入模腔中对熔融液体施加压力20-100mpa,保压5s后卸压,上冲复位,从熔融液体中取出包套模,割开包套模后即可得到成型压坯。
26.采用本实施例方法压制出的压坯生坯密度比传统方法高0.20g/cm3;压坯强度与传统模压工艺相比,可提高40%;烧结后硬坯尺寸精度比传统模压工艺提高30%。
27.上述实施例只为说明本发明的技术构思及特点,其目的在于让熟悉此项技术的人士能够了解本发明的内容并据以实施,并不能以此限制本发明的保护范围。凡根据本发明精神实质所作的等效变化或修饰,都应涵盖在本发明的保护范围之内。