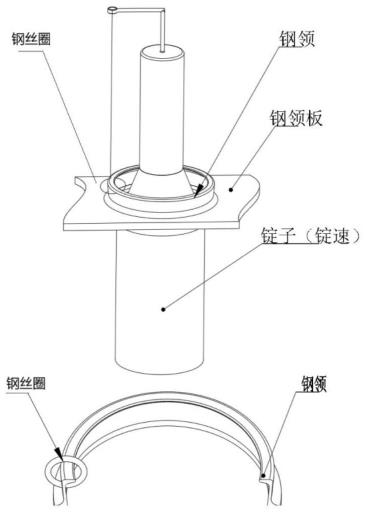
ag/ws
2-dlc涂层及其制备方法
技术领域
1.本发明属于钢领表面涂层技术领域,具体涉及一种ag/ws
2-dlc(类金刚石)涂层,本发明还涉及一种ag/ws
2-dlc涂层的制备方法。
背景技术:2.纺织业是我国经济的传统支柱产业和民生产业,而纺纱又是纺织产业链的第一道工序,其作用不可替代。目前,环锭纺纱仍然占据我国纺纱行业的主导地位,有数据表明,我国各类环锭纺纱机数量多达10万台,稳居世界第一位。环锭纺纱机的“环”就是钢领的别称,钢领是对纱线进行加捻以及卷绕流程的重要器件之一,其使用性能和使用寿命直接影响纺纱机的最高锭速。钢领的服役寿命短暂与其恶劣的工况环境以及磨损情况都是密不可分的。在实际生产中,钢领与运动部件钢丝圈组成了一对摩擦副,其结构如图1所示。钢丝圈的高速运转导致钢领长期处于高温、高压的工况条件,加之较高湿度的空气环境,如何有效降低钢领的磨损成为当前亟待解决的问题。
3.当前钢领表面涂层技术我国与国外仍存在巨大差距,研究新型硬质涂层使其能够满足钢领在实际生产中的需求是纺织企业在发展高速纺纱技术中的必经之路。涂层的强韧化设计一直是新型硬质涂层应用的关键技术,利用两种组元或者多种组元依次交替叠加在一起制备成多层涂层材料被认为是突破强度与韧性“倒置关系”、提高涂层综合性能的有效途径之一。
技术实现要素:4.本发明的目的在于提供一种ag/ws
2-dlc涂层,解决了现有钢领磨损导致的服役寿命低的问题。
5.本发明的另一目的在于提供一种ag/ws
2-dlc涂层的制备方法。
6.本发明所采用的第一种技术方案是:ag/ws
2-dlc涂层,包括交替沉积于钢领基材表面的ag层和ws
2-dlc层,每个ag层和ws
2-dlc层的厚度均为200~500nm。
7.本发明第一种技术方案的特点还在于,
8.ws
2-dlc层由ws2粒子和石墨粒子掺杂组成。
9.本发明所采用的第二种技术方案是:ag/ws
2-dlc涂层的制备方法,包括以下步骤:
10.步骤1、将钢领基材装夹在非平衡磁控溅射离子镀设备的样品台中部,再将设备的炉腔体抽真空;
11.步骤2、向炉腔体内通入氩气,调节偏压对基材表面进行溅射清洗;
12.步骤3、在样品台两侧相对靶位上放置ag靶材,设定轰击时间使得溅射出的ag粒子在基材表面沉积一层厚度200~500nm的ag层;
13.步骤4、将ag靶材更换为ws2靶材,并在样品台两侧另外两个相对靶位上放置石墨靶材,再次抽真空,设定轰击时间使得溅射出的ws2粒子和c粒子在软质层表面沉积一层厚度200~500nm的ws
2-dlc层;
14.步骤5、重复步骤3和步骤4依次交替沉积ag层和ws
2-dlc层,再炉冷、空冷即得。
15.本发明第二种技术方案的特点还在于,
16.步骤1和步骤4中抽真空至真空度为4.0~5.0
×
10-4
pa。
17.步骤2中通入氩气后的气压为0.5~0.8pa。
18.步骤3和步骤4中设定轰击时间为20~40min。
19.步骤3和步骤4的沉积过程中保持偏压为-80v,样品台的旋转速度保持在10rpm。
20.步骤5中的炉冷温度为40℃以下。
21.本发明的有益效果是:本发明的ag/ws
2-dlc涂层及其制备方法,利用物理气相沉积技术设计和制备ag/ws
2-dlc涂层,实现了软硬交替分布的涂层可控构筑,为改善或解决纺纱技术快速发展的瓶颈问题奠定了坚实的基础,为关键技术的推广和应用拓宽了适用领域。
附图说明
22.图1是现有钢领摩擦配副的结构示意图;
23.图2是本发明的ag/ws
2-dlc涂层的结构示意图;
24.图3是本发明的ag/ws
2-dlc涂层的制备方法采用的物理气相沉积设备示意图。
具体实施方式
25.下面结合附图以及具体实施方式对本发明进行详细说明。
26.本发明提供了一种ag/ws
2-dlc涂层,如图2所示,首先在钢领基材表面沉积ag层,在此基础上,再沉积硬质ws
2-dlc层,实现软质层和硬质层交替沉积。
27.本发明还提供了一种ag/ws
2-dlc涂层的制备方法,首先引入材料的基体、含ws2、石墨和ag的靶材,其次采用物理气相沉积的方法在钢领基材上交替沉积ag层和ws
2-dlc层,最后结合得到软硬质层交替的多层复合涂层。具体操作如下:
28.第一步、采用英国teer公司生产的闭合场非平衡磁控溅射离子镀(cfubmsip)设备。该设备采用udp-650型非平衡磁控溅射系统如图3所示,将清洗好的钢领基材装夹在旋转样品台中部,把炉腔体内的真空度抽至4.0~5.0
×
10-4
pa,在室温下真空系统中进行后续操作;
29.第二步、样品在沉积薄膜之前须进行氩离子溅射清洗以去除基材表面的氧化层和吸附的杂质。通入ar气使ar气气压为0.5~0.8pa,调节偏压对基材表面进行溅射清洗;
30.第三步、在样品台两侧相对靶位上放置ag靶材,设定轰击时间为20~40min,使得溅射出的ag粒子在基材表面沉积一层厚度200~500nm的ag层作为软质层。沉积过程中保持偏压为-80v,样品台的旋转速度保持在10rpm;
31.第四步、打开炉腔体将ag靶材更换为ws2靶材,并在样品台两侧另外两个相对靶位上放置石墨靶材,再次在室温下将炉腔体内的真空度抽至4.0~5.0
×
10-4
pa,开始溅射沉积。设定轰击时间为20~40min,使得溅射出的ws2粒子和c粒子在软质层表面沉积一层厚度200~500nm的ws
2-dlc层作为硬质层,沉积过程中保持偏压为-80v,样品台的旋转速度保持在10rpm;
32.第五步、采用第三步和第四步的方式依次交替沉积ag层和ws
2-dlc层,一层ag层和
一层ws
2-dlc层为一组,共沉积三组,之后炉冷至40℃以下,再空冷即得多层复合涂层。
33.通过上述方式,本发明的ag/ws
2-dlc涂层及其制备方法,利用物理气相沉积技术设计和制备ag/ws
2-dlc涂层,实现了软硬交替分布的涂层可控构筑,解决了现有钢领磨损导致的服役寿命低的问题,为改善或解决纺纱技术快速发展的瓶颈问题奠定了坚实的基础,为关键技术的推广和应用拓宽了适用领域。
34.实施例1
35.将清洗好的钢领基材装夹在旋转样品台中部,把炉腔体内的真空度抽至4.0
×
10-4
pa,在室温下真空系统中进行后续操作;通入ar气使气压为0.5pa,调节偏压对基材表面进行溅射清洗;在样品台两侧相对靶位上放置ag靶材,设定轰击时间为20min,使得溅射出的ag粒子在基材表面沉积一层厚度200nm的ag层作为软质层,沉积过程中保持偏压为-80v,样品台的旋转速度保持在10rpm;打开炉腔体将ag靶材更换为ws2靶材,并在样品台两侧另外两个相对靶位上放置石墨靶材,再次在室温下将炉腔体内的真空度抽至4.0
×
10-4
pa,开始溅射沉积,设定轰击时间为20min,使得溅射出的ws2粒子和c粒子在软质层表面沉积一层厚度200nm的ws
2-dlc层作为硬质层,沉积过程中保持偏压为-80v,样品台的旋转速度保持在10rpm;依次交替沉积ag层和ws
2-dlc层,一层ag层和一层ws
2-dlc层为一组,共沉积三组,之后炉冷至40℃,再空冷即得多层复合涂层。
36.实施例2
37.将清洗好的钢领基材装夹在旋转样品台中部,把炉腔体内的真空度抽至4.5
×
10-4
pa,在室温下真空系统中进行后续操作;通入ar气使气压为0.6pa,调节偏压对基材表面进行溅射清洗;在样品台两侧相对靶位上放置ag靶材,设定轰击时间为30min,使得溅射出的ag粒子在基材表面沉积一层厚度350nm的ag层作为软质层,沉积过程中保持偏压为-80v,样品台的旋转速度保持在10rpm;打开炉腔体将ag靶材更换为ws2靶材,并在样品台两侧另外两个相对靶位上放置石墨靶材,再次在室温下将炉腔体内的真空度抽至4.5
×
10-4
pa,开始溅射沉积,设定轰击时间为30min,使得溅射出的ws2粒子和c粒子在软质层表面沉积一层厚度350nm的ws
2-dlc层作为硬质层,沉积过程中保持偏压为-80v,样品台的旋转速度保持在10rpm;依次交替沉积ag层和ws
2-dlc层,一层ag层和一层ws
2-dlc层为一组,共沉积三组,之后炉冷至38℃,再空冷即得多层复合涂层。
38.实施例3
39.将清洗好的钢领基材装夹在旋转样品台中部,把炉腔体内的真空度抽至5.0
×
10-4
pa,在室温下真空系统中进行后续操作;通入ar气使气压为0.8pa,调节偏压对基材表面进行溅射清洗;在样品台两侧相对靶位上放置ag靶材,设定轰击时间为40min,使得溅射出的ag粒子在基材表面沉积一层厚度500nm的ag层作为软质层,沉积过程中保持偏压为-80v,样品台的旋转速度保持在10rpm;打开炉腔体将ag靶材更换为ws2靶材,并在样品台两侧另外两个相对靶位上放置石墨靶材,再次在室温下将炉腔体内的真空度抽至5.0
×
10-4
pa,开始溅射沉积,设定轰击时间为40min,使得溅射出的ws2粒子和c粒子在软质层表面沉积一层厚度500nm的ws
2-dlc层作为硬质层,沉积过程中保持偏压为-80v,样品台的旋转速度保持在10rpm;依次交替沉积ag层和ws
2-dlc层,一层ag层和一层ws
2-dlc层为一组,共沉积三组,之后炉冷至35℃,再空冷即得多层复合涂层。