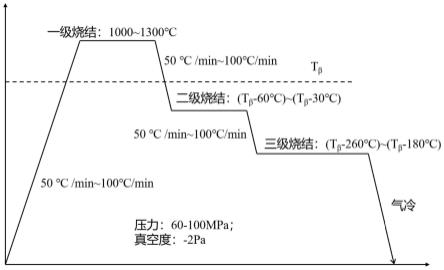
1.本技术涉及钛合金粉末冶金技术领域,具体涉及一种基于放电等离子体烧结的高强钛合金零件的多级烧结方法。
背景技术:2.高强钛合金具有比强度高、韧性好以及抗腐蚀性能优异等特点,是航空航天、船舶、化工行业重要的结构材料,广泛应用于各类承力和抗腐蚀部件。高强钛合金小型零部件通常采用锻造、轧制等方法成型,随后结合热处理、机加工等方法加工,整个过程周期长,且原材料利用率低,导致相关产品的成本高,极大限制了产品的推广与应用。
3.粉末冶金方法是制造小型钛合金零件的重要路径之一,直接将粉末直接烧结成型,有效降低了原材料损耗,进而降低加工成本。然而,传统的粉末冶金方法在制造钛合金零件时烧结时间长,使得烧结效率低,且杂质含量不可控,导致钛合金的强度和塑性不稳定。
4.放电等离子体烧结技术(sps)是近年来发展起来的一种新型烧结技术,通过在粉末之间产生脉冲电流,利用焦耳热和加压变形使得粉末烧结致密。该技术可以将金属粉末直接烧结成为零件毛坯,具有烧结速度快、加热均匀、烧结零件密度高、晶粒细小均匀、材料利用率高等优点。但是直接采用该放电等离子体烧结技术烧结成型的高强钛合金产品在显微镜下其晶界界面中无α相,导致产品的强度低和塑性差,不满足航空航天领域对产品强度和塑性的要求。
技术实现要素:5.本发明目的在于提供一种基于放电等离子体烧结的高强钛合金零件的多级烧结方法,该方法先对钛合金粉末进行球磨,再通过放电等离子体烧结技术在高真空中进行多级快速烧结,保证了钛合金零件塑性,同时提升了强度,使得制备的高强钛合金零件适用于航空航天领域。
6.为实现上述目的,本发明采用如下技术方案:
7.基于放电等离子体烧结的高强钛合金零件的多级烧结方法,包括如下步骤:
8.(1)选取高强度的钛合金粉末,并测定所述钛合金粉末的相转变点t
β
;
9.(2)球磨钛合金粉末,球料比为2:1~5:1,球磨转速为250r/min~300r/min,球磨时间240~360min;
10.(3)根据零件的重量称取球磨后钛合金粉末,并装入模具,然后将模具放入放电等离子体烧结炉膛内后抽真空;
11.(4)一级烧结,调节压力至60~100mpa,以升温速率为50~100℃/min升温至一级烧结温度,保温5~10min;一级烧结温度为1100~1350℃;
12.(5)二级烧结,保持压力,以降温速率为50~100℃/min降温至二级烧结温度,并保温10~20min;二级烧结温度为t
β-60℃~t
β-30℃;
13.(6)三级烧结,保持压力,以降温速率为30-50℃/min降温至三级烧结温度,保温30~60min;三级烧结温度为t
β-260℃~t
β-180℃;
14.(7)三级烧结后通入惰性气体快速冷却至室温,打开模具取出钛合金零件。
15.进一步地,步骤(1)中选取粒度为50~200μm、o含量≤0.1wt%、n含量≤0.01wt%、c含量≤0.01wt%的所述钛合金粉末。
16.进一步地,步骤(1)中采用采用金相法测试所述相转变点t
β
。
17.进一步地,步骤(1)中所述球磨采用采用碳化物球或钢球。
18.进一步地,步骤(3)中抽真空至-2pa。
19.进一步地,步骤(7)中所述钛合金零件的片层形α相组织宽度为0.5~1.5μm,长度为2~15μm。
20.本发明具有如下有益效果:
21.(1)对高强钛合金粉末进行球磨,使粉末充分变形和晶格细化,并在粉末内部产生大量的晶格畸变和位错,有利于在快速烧结过程中的α形核和均匀析出;
22.(2)一级高温快速保压烧结,可保证钛合金粉末充分致密且β晶粒不长大,有利于钛合金的力学性能和韧性匹配;一级烧结完成后快速冷却至二级烧结温度,类似一种原位锻造,使已经致密的钛合金粉末β晶界处的晶界α相析出,从而使晶界α相不连续,保证了钛合金的塑性;二级烧结完成后快速冷却至三级烧结温度,三级烧结则保证晶内α相充分析出,强化钛合金的β基体,提升了钛合金的强度;整个烧结过程速度快,原材料利用率高达到95%以上,无需后热处理,同时烧结的高强钛合金材料微观组织均匀,强度较高,力学性能优异;
23.(3)加工周期短,操作简单,成本低,适合大批量生产。
附图说明
24.图1为本发明烧结温度变化示意图。
25.图2为本发明球磨后的钛合金颗粒示意图。
26.图3为本发明烧结成型微观组织示意图。
27.图4为本发明对比实施例2的微观组织示意图。
具体实施方式
28.实施例1
29.本实施例提供的基于放电等离子体烧结的高强钛合金零件的多级烧结方法包括如下步骤:
30.(1)选取高强度的钛合金粉末,本实施例选取tc18钛合金粉末,tc18钛合金粉末形状为球形,tc18钛合金粉末的o含量0.1wt%,n含量为0.01wt%,c含量为0.01wt%,具体选用两种不同粒度的tc18钛合金粉末,分别为d50和d90,d50的粒度为108μm,d90的粒度为165μm;通过金相法测试用于制备tc18钛合金粉末棒材的相转变点t
β
(℃),t
β
=870℃。
31.(2)球磨钛合金粉末,本实施例采用行星式球磨机,该行星式球磨机内安装为碳化物球,球料比为2:1,球磨转速为250r/min,球磨时间360min,有利于烧结过程中的相析出,析出比较充分,如图2所示,球磨后球形的钛合金粉末产生变形且晶粒被细化。
32.(3)根据零件的重量称取球磨后钛合金粉末,并装入由石墨制造的模具,模具上下各塞入石墨压头一个,石墨压头用于调节压力,模具上插入控温热电偶,然后将模具放入放电等离子体烧结炉膛内后抽真空至-2pa。
33.(4)一级烧结,将钛合金粉末在加压条件下快速升温至高温烧结,升温前通过石墨压头调节压力至80mpa,并保压,然后采用升温速率为100℃/min升温至一级烧结温度1250℃,保温5min;一级烧结可使钛合金粉末致密,其致密度可达99.9%。
34.(5)二级烧结,一级烧结完成后在保持80mpa压力情况下,以降温速率为50℃/min降温至二级烧结温度830℃(t
β-40℃),并保温15min,二级烧结可析出不连续晶界α相,从而提高钛合金的塑形。
35.(6)三级烧结,二级烧结完成后继续保持80mpa的压力,以降温速率为40℃/min降温至三级烧结温度620℃(t
β-250℃),保温40min;三级烧结可析出细小片层α相,以提高钛合金的强度;本实施例的烧结温度变化如图1所示。
36.(7)烧结完成后,释放压力并断电,通入高纯氩气,并快速冷却至室温,最后打开模具取出钛合金零件,其微光晶界图如图3所示,从图中可知微观组织均匀且α相析出均匀,其片层形α相组织宽度为0.5~1.5μm,长度为2~15μm。
37.实施例2
38.本实施例提供的基于放电等离子体烧结的高强钛合金零件的多级烧结方法包括如下步骤:
39.(1)选取高强度的钛合金粉末,本实施例选取tb6钛合金粉末,tb6钛合金粉末形状为球形,tb6钛合金粉末的o含量0.1wt%,n含量为0.01wt%,c含量为0.01wt%,具体选用两种不同粒度的tb6钛合金粉末,分别为d50和d90,d50的粒度为85μm,d90的粒度为131μm;通过金相法测试用于制备tc18钛合金粉末棒材的相转变点t
β
(℃),t
β
=805℃。
40.(2)球磨钛合金粉末,本实施例采用行星式球磨机,该行星式球磨机内安装为钢球,球料比为3:1,球磨转速为280r/min,球磨时间240min。
41.(3)根据零件的重量称取球磨后钛合金粉末,并装入由石墨制造的模具,模具上下各塞入石墨压头一个,石墨压头用于调节压力,模具上插入控温热电偶,然后将模具放入放电等离子体烧结炉膛内后抽真空至-2pa。
42.(4)一级烧结,将钛合金粉末在加压条件下快速升温至高温烧结,升温前通过石墨压头调节压力至100mpa,并保压,然后采用升温速率为80℃/min升温至一级烧结温度1150℃,保温8min;一级烧结可使钛合金粉末致密,其致密度可达99.9%。
43.(5)二级烧结,一级烧结完成后在保持100mpa压力情况下,以降温速率为80℃/min降温至二级烧结温度770℃(t
β-35℃),并保温20min,二级烧结可析出不连续晶界α相,从而提高钛合金的塑形。
44.(6)三级烧结,二级烧结完成后继续保持100mpa的压力,以降温速率为40℃/min降温至三级烧结温度550℃(t
β-255℃),保温50min;三级烧结可析出细小片层α相,以提高钛合金的强度。
45.(7)烧结完成后,释放压力并断电,通入高纯氩气,并快速冷却至室温,最后打开模具取出钛合金零件。
46.对比实施例1
47.本实施例选用tc18钛合金粉末用传统的粉末冶金方法直接烧结成型。
48.对比实施例2
49.本实施例与实施例1基本相同,仅仅减少实施例1中球磨的步骤(2),本实施例制造的钛合金零件的晶界α相较为连续,塑性差,晶界α相析出不充分,导致相变不充分,从而使样品的强度低,如图4所示,微观组织里面晶界α析出不均匀的问题,以及连续的晶界α相。
50.对比实施例3
51.本实施例采用传统的放电等离子体烧结技术对tc18钛合金粉末,即一次温度直接烧结成型,即实施例1一次烧结后成型的零件。
52.对比实施例4
53.本实施例与实施例1基本相同,仅仅改变一级烧结温度,一级烧结温度问950℃,本实施例制造的钛合金零件不致密,组织间有大量的孔洞。
54.对实施例1、实施例2、对比实施例1、对比实施例2、对比实施例3和对比实施例4进行力学性能测试,其力学性能如表1所示。
55.表1力学性能
56.实施例抗拉强度mpa屈服强度mpa延伸率%实施例1-d501209117411.2实施例1-d901211118110.1实施例2-d50128012099.6实施例2-d90128412119.1对比实施例1-d509659018.1对比实施例2-d509709257.4对比实施例3-d509568968.1对比实施例4-d509719167.9
57.以上所述仅是本发明优选的实施方式,但本发明的保护范围并不局限于此,任何基于本发明所提供的技术方案和发明构思进行的改造和替换都应涵盖在本发明的保护范围内。