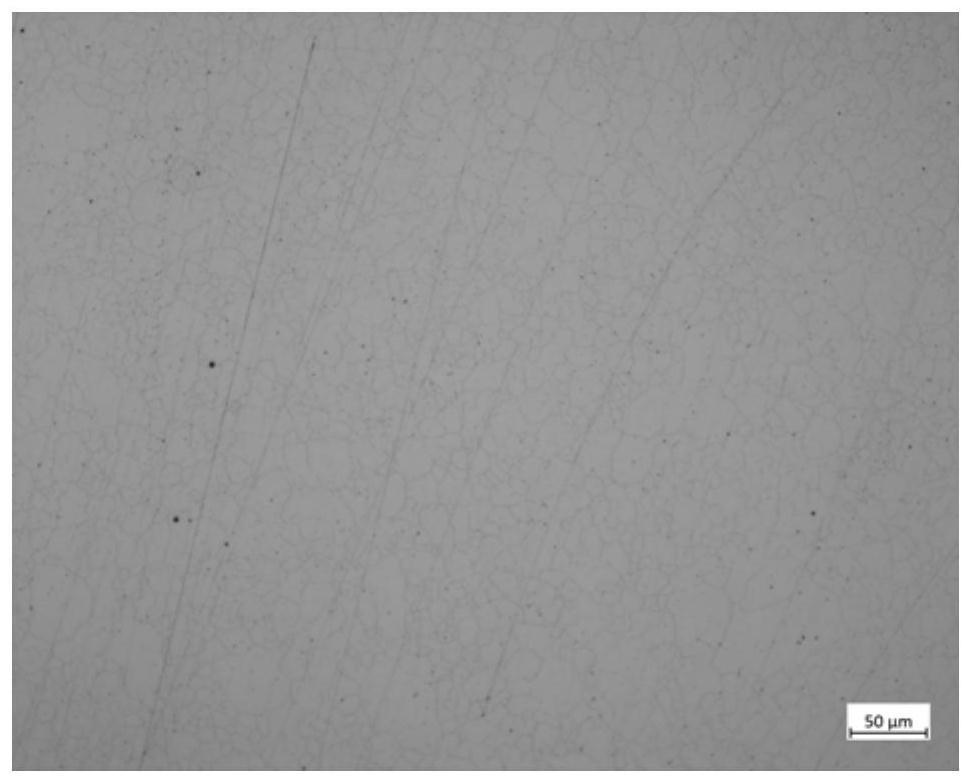
nb-ti微合金化耐高温渗碳高扭矩输出齿轮钢及其制造方法和高温渗碳处理方法
技术领域
1.本发明属于轮钢领域,具体涉及nb-ti微合金化耐高温渗碳高扭矩输出齿轮钢及其制造方法和高温渗碳处理方法,适用于制造高扭矩汽车变速输出齿轮用钢。
背景技术:2.新能源汽车以其低污染、高效能等特点而成为未来汽车行业发展的重点方向。与传统燃油车相比,减/差速器齿轮转速高、瞬时扭矩大是制约新能源汽车发展的重要瓶颈,也是亟需解决的重点难题。
3.通常齿轮钢增加扭矩的技术包括提高合金含量,增加淬透性提高马氏体含量来提高扭矩;另一种技术方案是添加微合金化元素,如nb、v来细化晶粒,提高扭矩,但这些技术方案带来的成本的增加,使得这些技术方案在推广时遇到巨大的阻力。
4.目前常用的新能源齿轮钢材料为17crnimo6齿轮钢,其淬透性控制范围j9: 37~47hrc,j15:34~46hrc,j25:31~43hrc。但是随着高输出扭矩的需求,现有的齿轮钢材料性能剩余量已不足,无法满足未来新能源汽车设计需要。
5.20cr2ni4性能虽然优于17crnimo6,但是合金成本太高,材料推广难度大,仅被少量应用。因此,有必要开发一种具有高淬透性、高输出扭矩、优异的强韧性能的低成本齿轮材料,以满足汽车行业对低成本高输出扭矩高性能齿轮钢的需求。常规的渗碳工艺存在着工艺周期长,能源消耗、劳动强度大等问题,严重影响了生产效率,成为齿轮制造过程中的瓶颈。为解决上述问题,开展高温渗碳工艺研究是身份必要的,当渗碳温度提高到1050℃时,渗碳扩散系数提高 7倍,渗碳时间可由原来的7小时缩短为2-3小时,显著的提高了渗碳工艺事假,提高生产效率。然而,提高渗碳温度势必会带来混晶等渗碳缺陷,导致零件不合格。
6.中国专利,公布号为cn108866439a,公开日为2018年11月23日的发明专利公开了一种nb、ti复合微合金化高温真空渗碳重载齿轮用钢,通过复合微合金化设计,提高了渗碳温度,细化了晶粒,但对淬透性并没有严格要求,尚无法满足低成本高输出扭矩高性能齿轮钢的需求。
7.中国专利,公布号为cn 104109816a,公布日为2014年10月22日的发明专利公布了一种高淬透性crnimo系齿轮钢,该发明通过提高cr、ni等元素在较高范围,有效的提高的材料的淬透性,淬透性可达到j9:40-46hrc,j15: 39-44hrc,j25:38-44hrc;并通过al和n的含量控制保证了渗碳过程中奥氏体晶粒不发生明显长大,提高渗碳合金钢的抗疲劳性能和综合力学性能。虽然淬透性得到了进一步提高,但ni、mo含量极高,还添加v、nb等贵金属,成本大幅度增加,尚无法满足低成本高输出扭矩高性能齿轮钢的需求。
8.中国专利,公布号为cn107604253a,公布日为2018年1月19日的发明专利公布了一种高淬透性mn-cr系列渗碳钢,该发明通过提高c、mn、cr等元素在较高范围,含b有效的提高的材料的淬透性,淬透性可达到j9:40-46hrc, j15:34-40hrc,j25:30.5-33.5hrc;并通过
al和n的含量控制保证了渗碳过程中奥氏体晶粒不发生明显长大。虽然淬透性得到了进一步提高,尚无法满足低成本高输出扭矩高性能齿轮钢的需求。
9.目前crnimo系齿轮钢具有良好的强韧性,并且对crnimo系齿轮钢的开发中有了一定的技术积累,但目前无法做到提高淬透性、高输出扭矩,性能与20cr2ni4相当但成本大幅度降低的需求。因此迫切需要开发新的技术手段,提高淬透性、强韧性、高输出扭矩并且低成本的高性能齿轮钢,用来满足汽车行业的不断发展。
技术实现要素:10.本发明的目的在于提供nb-ti微合金化耐高温渗碳高扭矩输出齿轮钢及其制造方法,通过配方设计和匹配的制造方法,获得低成本高扭矩输出齿轮用钢,其末端淬透性可以满足j9:45~49hrc,j15:43~48hrc,j25:40~44hrc。
11.本发明还有一个目的在于提供nb-ti微合金化耐高温渗碳高扭矩输出齿轮钢的高温渗碳处理方法,经980~1050℃高温渗碳后,材料的奥氏体晶粒度≥8.0 级,扭转疲劳强度≥600mpa。
12.本发明具体技术方案如下:
13.本发明提供的一种nb-ti微合金化耐高温渗碳高扭矩输出齿轮钢,包括以下质量百分比成分:c:0.18-0.24%,si:0.17-0.37%,mn:0.80-1.20%,cr:
14.1.50-1.80%,mo:0.30-0.50%,ni:1.20-1.40%,nb:0.020~0.050%, ti:0.020~0.060%,al:0.030-0.040%,p:≤0.010%,s:≤0.020%,t.o:≤10ppm, [n]:0.0090-0.0120ppm,其余为fe和不可避免的杂质元素。
[0015]
所述的nb-ti微合金化耐高温渗碳高扭矩输出齿轮钢的成分还满足: 0.01%≤alf=al-1.52
×
[n]≤0.030%,2.5≤al/[n]≤5;2.5≤al/[n]≤5保证奥氏体aln第二相能够析出足够的量保证晶粒度细小均匀,过多的al容易引起 aln分布不均匀,引起混晶;自由alf能够大幅度提高淬透性,但过高反而降低淬透性,其中[n]的系数重新进行了拟合修订,自由alf提高淬透性的临界值为 0.01%~0.030%,过低作用不大,过高反而降低淬透性。
[0016]
本发明提供的一种nb-ti微合金化耐高温渗碳高扭矩输出齿轮用钢的制造方法,包括以下工艺流程:
[0017]
冶炼-lf精炼-rh真空处理-连铸-精整成材。
[0018]
所述冶炼是指电弧炉冶炼;
[0019]
钢在精炼过程中充分脱氧,氧含量低于10ppm,并在真空处理前期加入铝线进行调al,保证符合自由铝的控制,严禁在真空处理后期对al进行大幅度调整,这样既可以保证铝的含量,也能防止钢中夹杂物过多。
[0020]
所述精整成材包括加热、轧制和缓冷。
[0021]
所述加热为:钢坯在加热炉的均热温度控制在1250~1280℃、预热、加热和均热总时间控制8.0h-12.0h。
[0022]
所述轧制,控制开轧温度1200~1230℃、终轧温度880-900℃。
[0023]
所述缓冷具体为:轧后经过冷床冷却至600-650℃入坑缓冷,缓冷时间≥24h,出坑后进行修磨扒皮,确保表面无脱碳、零缺陷。
[0024]
齿轮钢的加工工艺:在1250~1280℃高温加热时,al和n都固溶在奥氏体中,在随
后的缓冷阶段,会在奥氏体晶界上或者晶界周围富集。随后,尽管在淬火时的加热过程中,发生aln的析出和残余的固溶al的扩散,但原来粗大的奥氏体晶界附近偏析的al在点阵中移动,很难大量移动到新生成的奥氏体晶界的周围,固溶al量相对减少,造成晶粒附近的固溶al量达不到足够提高淬透性的必要含量。因此,富集在枝晶间隙处自由铝,经过轧制后,自由铝在原奥氏体晶界处富集,且不会随着热处理后晶界变化而变化。
[0025]
本发明提供的一种采用本发明齿轮钢生产的耐高温高扭矩输出齿轮的高温渗碳处理方法,具体渗碳方法流程为:正火-高温渗碳后降温油淬-低温回火。
[0026]
具体为:齿轮材料先经过930-950℃正火处理,正火保温时间1
±
0.5h,然后在980-1050℃进行渗碳处理,渗碳时间6-8h,渗碳后温度降低至810-830℃保温30-40min后进行油冷淬火,淬火油温度为120-200℃,淬火后进行 160-180℃低温回火,回火时间不小于2h。
[0027]
本发明设计构思如下:
[0028]
c:c是钢中最基本有效的强化元素,是影响淬透性最有效的元素,并且成本较低,为了保证齿轮钢有足够的强度和足够的淬透性,需要提高c含量,并且c含量的提高有助于提高心部基体硬度,使得基体中马氏体板条中的碳含量增加,并且心部碳含量的提高有助于提高心部残余奥氏体的含量,残余奥氏体可以增加基体的协调变形能力,使得高扭矩的作用下协调变形,不易萌生裂纹,且马氏体硬度的提高远大于残余奥氏体提高带来的硬度降低,心部硬度的提高能够增加静扭强度,所以碳含量不低于0.18,但过高的碳含量对韧性损伤较大,对于crnimo系齿轮钢碳含量不应高于0.24%。故确定碳含量在0.18~0.24%
[0029]
si:si是脱氧剂,同时通过固溶强化提高钢的强硬度,也可以提高齿轮钢的淬透性,si的含量不能低于0.17%,但过量的硅使c的活性增加,促进钢在轧制和热处理过程中的脱碳和石墨化倾向使得渗碳层易氧化,并且在渗碳过程中尤其是高温渗碳过程中,较多的si会导致材料出现内氧化,故si的含量不能高于0.17%。si含量控制在0.17%-0.37%。
[0030]
mn:mn可以扩大奥氏体相区,并且稳定奥氏体组织,提高钢的淬透性,但是mn可溶于铁素体,提高钢中铁素体和奥氏体的硬度和强度,同时mn可以提高奥氏体组织的稳定性,显著提高钢的淬透性。但过量的mn会降低钢的塑性,钢在热轧时韧性变坏。mn含量控制在0.80-1.20%。
[0031]
cr:cr可提高钢的淬透性及强度,cr在钢种和碳结合,形成碳化物,由于齿轮钢淬火后低温回火,并无大块的碳化物析出,均以细小的碳化物析出,析出的碳化物在马氏体板条间富集,抑制板条在应力下移动,马氏体中的位错可以缠结,提高强度和抗疲劳性能,故cr含量不低于1.50%,但与此同时,过高的cr会形成碳化物膜影响渗碳效果,降低渗碳层性能,故cr的含量不能高于 1.80%。cr含量控制在1.50-1.80%。
[0032]
mo:mo能明显提高钢的淬透性,防止回火脆性及过热倾向。此外,本发明中mo元素与cr元素的合理配合可使淬透性和回火抗力得到明显提高,并且mo 能细化晶粒。而mo含量过低则上述作用有限,mo含量过高,促进晶界铁素体薄膜的形成,不利于钢的热塑性,增加钢的再热裂纹倾向,且成本较高。因此,控制mo含量为0.30~0.50%。
[0033]
ni:ni能有效提高钢的心部韧性,降低韧脆转变温度,提高低温冲击性能,具有提高钢材料疲劳强度的效果,ni在本项目中另一个作用是提高层错能,位错跨过势垒提高,提高抗扭转性能,而ni成本较高,且ni含量过高会降低热加工后的切削性。故ni含量控制在1.20~1.40%以内。
[0034]
al:al是有效的脱氧剂,且能形成aln细化晶粒,al含量低于0.030%时,作用不明显,高于0.040%时易形成粗大的夹杂物,恶化钢的性能。因此需要特殊在炼钢过程中al的加入时机加以调整,保证al含量应控制在0.030-0.040%。
[0035]
nb:nb是有效的细化晶粒微合金化元素,能够与钢中的c、n元素形成碳氮化物钉轧晶界抑制奥氏体晶粒长大,含量过少细化晶粒不明显,同时固溶的nb 含量能够提高淬透性,使得心部硬度提高,静扭强度增加,所以含量应高于 0.025%,但是过高的nb含量容易导致nb的夹杂物过大,影响疲劳性能,所以应保证nb含量应控制在0.020~0.050%。
[0036]
ti:ti与c、o、n都有极强的亲和力,其与c、n结合析出的tin、tic相有效的阻碍奥氏体晶粒度长大,起到细化晶粒的作用。ti同样可以提高材料的屈服点。同时钢中加入一定量的ti,ar3温度降低非常明显,从而提高试验料的淬透性,尤其ti含量达到0.030%以上,效果越发明显。在渗碳淬火过程中由于含ti碳化物的存在,使得基体中碳含量的降低从而导致奥氏体不稳定,这有利于降低材料表面渗碳层的残余奥实体含量,提高材料表面硬度,从而提高接触疲劳性能和扭转疲劳性能。含ti碳化物的析出做为阻碍位错运动的质点,同样能够提高材料的屈服强度。另外,含ti析出相在高温条件下不容易溶解,使得高温渗碳条件下材料奥氏体晶粒度不容易长大。因此ti含量控制在 0.020~0.060%,并适当降低n的含量。
[0037]
p和s:硫容易在钢中与锰形成mns夹杂,使钢产生热脆,但是添加少量的 s,在不影响产品性能的同时,会明显改善齿轮钢的切削性能,而mns同时具有细化晶粒的效果;p是具有强烈偏析倾向的元素,增加钢的冷脆,降低塑性,对产品组织和性能的均匀性有害。控制p≤0.010%,s:≤0.020%。
[0038]
t.o:t.o在钢中形成氧化物夹杂,较高的氧含量在渗碳尤其是高温渗碳条件下会引起材料的内氧化,降低材料的性能。因此控制t.o≤10ppm。
[0039]
[n]:能与ti、b和al等形成化合物,细化晶粒,合理的al/[n]对晶粒细化明显作用,而过高的[n]会形成气泡等连铸缺陷。同时,钢中形成的细小的tin 颗粒能够有效地阻碍奥氏体在高温条件下长大。但是,tin属于脆性夹杂,较多的tin不利于钢的疲劳性能。因此,[n]含量应控制在90-120ppm。
[0040]
与现有技术相比,本发明提供的nb-ti微合金化耐高温渗碳高扭矩输出齿轮用钢,通过提高碳含量增加及提高淬透性增加心部硬度,提高淬透性,其末端淬透性可以满足j9:45~49hrc,j15:43~48hrc,j25:40~44hrc,通过高温渗碳处理大幅度缩短渗碳时间,提高热处理效率,扭转疲劳强度≥600mpa,经 980~1050℃高温渗碳后材料的奥氏体晶粒度≥8.0级。按gb/t 225进行末端淬透性性能检验,本发明钢末端淬透性j9、j15及j25控制与cinimo系相比得到了大幅度提高,成本比20cr2ni4大幅度降低。
附图说明
[0041]
图1为实施例1渗碳后的晶粒图;
[0042]
图2为实施例2渗碳后的晶粒图;
[0043]
图3为实施例3渗碳后的晶粒图;
[0044]
图4为对比例1渗碳后的晶粒图;
[0045]
图5为对比例2渗碳后的晶粒图。
具体实施方式
[0046]
本发明采用特定成分的齿轮钢,共生产5炉本发明钢,并采用电弧炉冶炼
‑ꢀ
精炼-真空处理-连铸-轧制(精整),钢在精炼过程中充分脱氧,氧含量低于 10ppm,并在真空处理前期加入铝线进行调al,保证符合自由铝的控制,严禁在真空处理后期对al进行大幅度调整,这样既可以保证铝的含量,也能防止钢中夹杂物过多;钢坯在加热炉的均热温度控制在1250~1280℃、预热、加热和均热总时间控制8.0h-12.0h,开轧温度:1200-1230℃,终轧温度880-900℃,轧后经过冷床冷却至600-650℃入坑缓冷,缓冷时间≥24h。按照gb/t 3077中的要求生产2炉18crnimo7-6钢作为对比钢,并采用与对比钢相同的冶炼与轧制工艺,各实施例和对比例的具体配方和生产工艺参数如表1、表2所示。
[0047]
各实施例和对比例的成分见表1,表1没有显示的余量为fe和不可避免的杂质,生产工艺参数见表2。
[0048]
表1本发明实施例和对比例化学成分(单位:[n]、t.o为ppm,其它为wt%)
[0049][0050][0051]
表2实施例和对比例轧钢生产工艺参数
[0052][0053]
表3为本发明实施例末端淬透性值,由表3能够看出,本发明实施例1~5 所述齿轮钢淬透性控制j9、j15、j25值均在高扭矩汽车变速器输出齿轮用钢要求的范围内,与对比例相比淬透性相当。
[0054]
表3本发明实施例末端淬透性值(hrc)
[0055][0056][0057]
各实施例和对比例生产的齿轮材料先经过930-950℃正火处理,正火保温时间1h,然后在980-1050℃进行渗碳处理,渗碳时间6-8h,渗碳后温度降低至 810-830℃保温30-40min后进行油冷淬火,淬火油温度为120-200℃,淬火后进行160-180℃低温回火,回火时间不小于2h。具体参数如表4。
[0058]
表5为本发明实施例经过高温渗碳处理后,进行奥氏体晶粒度级晶粒尺寸检验,由表5能够看出,本发明实施例1~5所述齿轮钢经过高温渗碳后,晶粒度均在8.0级以上,并且不混晶。
[0059]
表4本发明实施例渗碳工艺
[0060][0061]
表5本发明实施例高温渗碳后晶粒度级晶粒尺寸
[0062][0063][0064]
通过实施例和对比例可以得到,只有在本发明配方和工艺条件下生产,才能达到本技术的效果,不仅淬透性提高,高温渗碳后晶粒≥8.0级且不混晶,扭转疲劳强度≥600mpa。