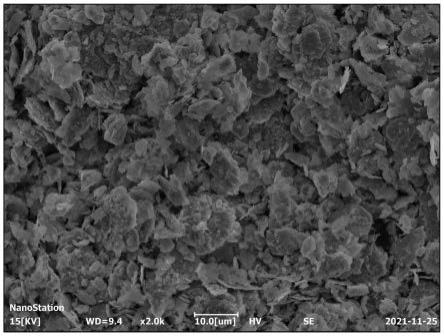
1.本发明属于复合吸波材料技术领域,具体涉及一种具有吸波性能的高熵合金/石墨烯复合材料及其制备方法。
背景技术:2.电子工业的迅猛发展,电磁污染也成为继大气污染、水污染、噪声污染之后的第四大污染。电磁波污染不仅干扰电子设备的正常运行,更会损害人类的身心健康。吸波材料是一种通过吸收接收到的电磁波能量,以减少电磁波干扰的材料,可使人们及设备免收电磁波的伤害。不管是为了保护环境,保护人类健康,还是保障信息安全和国防安全,研究和改进吸波材料,不断完善和提高吸波性能都势在必行。
3.目前,传统的吸波材料厚度较厚且阻抗匹配不佳,导致吸收强度小,直接影响了装备性能。高熵合金作为一种新型材料,具有各方面优良的性能,尤其是电磁波吸收性能方面。高熵合金通过调节各元素比例制备出所需的力学、物理化学特性的合金。高熵合金以其独特的结构性能特点,补充现有合金体系,扩展了人们对于多元相图中间区域的理解,并在理论上丰富了经典物理冶金学的认知。随着高熵合金研究的深入,高熵合金复合材料的提出使吸波材料在成分的选择上有了更大的空间。高熵合金与碳物质的复合,磁损耗与电损耗相结合的成分设计,能够为吸波材料提供更多的电磁损耗途径,有效提高吸波性能。
4.因此需要提供一种具有吸波性能的高熵合金/石墨烯复合材料及其制备方法使其适用于吸波领域,有效提高吸波性能。
技术实现要素:5.本发明所要解决的技术问题在于针对上述现有技术的不足,提供一种具有吸波性能的高熵合金/石墨烯复合材料。该高熵合金/石墨烯复合材料含有fe和ni铁磁性元素,增强了磁损耗能力和吸波能力,al、cr元素提高抗高温氧化能力的同时可以增强合金的耐腐蚀性,添加石墨烯提高了阻抗匹配和衰减特性,磁损耗主要由高熵合金贡献,介电损耗主要由石墨烯贡献,多种电磁波损耗机制协同作用,阻抗匹配良好,最大程度的吸收电磁波,达到提高反射损耗的效果。
6.为解决上述技术问题,本发明采用的技术方案是:具有吸波性能的高熵合金/石墨烯复合材料,其特征在于,所述复合材料的分子式为(fenicral
0.2
)
x
@cy,其中x和y分别为高熵合金fenicral
0.2
和石墨烯c的质量分数,且92<x<98,x+y=100。
7.本发明的高熵合金/石墨烯复合材料含有fe和ni铁磁性元素,增强了高熵合金/石墨烯复合材料的磁损耗能力,提高高熵合金/石墨烯复合材料的吸波能力,同时al、cr元素提高高熵合金/石墨烯复合材料的抗高温氧化能力的同时可以增强合金的耐腐蚀性,本发明中的高熵合金/石墨烯复合材料中的石墨烯有自润滑作用,添加石墨烯提高了阻抗匹配和衰减特性,使得入射的电磁波尽可能多地进入到高熵合金/石墨烯复合材料内部,在表面实现最小的反射,多种损耗机制的协同作用强烈衰减电磁波的能量,即电磁损耗增加,最大
程度的吸收电磁波,石墨烯加入到高熵合金中能提高合金的延展性,使复合材料弥散均匀的分散在高熵合金基体上,获得较薄的层片状,对于高熵合金/石墨烯复合材料,磁损耗主要由高熵合金贡献,介电损耗主要由石墨烯贡献,多种电磁波损耗机制协同作用,阻抗匹配良好,最大程度的吸收电磁波,达到提高反射损耗的效果。
8.上述的一种具有吸波性能的高熵合金/石墨烯复合材料,其特征在于,所述复合材料的分子式为(fenicral
0.2
)
x
@cy,其中x和y分别为高熵合金fenicral
0.2
和石墨烯c的质量分数,且92<x<94,x+y=100。本发明通过控制高熵合金/石墨烯复合材料中两者的比例,使高熵合金/石墨烯复合材料具有最优的吸波性能。
9.另外,本发明还提供了一种制备具有吸波性能的高熵合金/石墨烯复合材料的方法,其特征在于,该方法包括以下步骤:
10.步骤一、将铝粉、铬粉、铁粉、镍粉和石墨烯粉进行混合研磨,得到混合料;
11.步骤二、将步骤一中得到的混合料进行烘干,得到烘干混合料;
12.步骤三、将步骤二中得到的烘干混合料、无水乙醇和不锈钢磨球加入到经无水乙醇净化后的不锈钢球磨罐中进行搅拌,然后将不锈钢球磨罐进行封装后往复抽真空、充氩气数次,得到内部为真空状态的密封不锈钢球磨罐;
13.步骤四、将步骤三中得到的密封不锈钢球磨罐转移到高速球磨机上进行球磨,在不锈钢球磨罐中得到粉料;
14.步骤五、将步骤四中得到的粉料进行干燥处理,得到具有吸波性能的高熵合金/石墨烯复合材料;
15.步骤六、将步骤五中得到的高熵合金/石墨烯复合材料进行筛分,得到呈现多尺度不规则片状的高熵合金/石墨烯复合粉状材料。
16.上述的方法,其特征在于,步骤一中所述铝粉的质量纯度大于99.9%,粒度小于5μm,所述铬粉的质量纯度大于99.9%,粒度小于10μm,所述铁粉的质量纯度大于99.9%,粒度小于10μm,所述镍粉的质量纯度大于99.9%,粒度小于50μm,所述石墨烯粉的质量纯度大于99.9%,粒度小于20μm。本发明通过对原料纯度和粒径进行限定,防止杂质等不确定因素对材料性能的影响,保证球磨过程中合金粉末的均匀性。
17.上述的方法,其特征在于,步骤一中所述混合研磨采用玛瑙研钵进行,所述混合研磨中多次加入质量纯度大于99.95%的无水乙醇。本发明中由于石墨烯密度小,通过多次加入无水乙醇避免在研磨过程中石墨烯的质量减少而造成成分偏差,并且抑制粉末的团聚和粘壁,降低粉末的表面活性。
18.上述的方法,其特征在于,步骤三中所述真空状态的密封不锈钢球磨罐内部的真空度小于0.1pa。本发明通过控制密封不锈钢球磨罐内部的真空度,因为球磨过程中球磨罐内温度会升高,导致内部压强增大,如果在球磨之初不抽真空,在球磨过程中内部压强过大会使球磨罐的盖子顶开造成空气进入,会导致样品氧化,抽真空后,由于环境气压大于罐体内压强,大气压的作用使球磨罐一直处于真空密封状态,避免空气进入氧化粉料。
19.上述的方法,其特征在于,步骤四中所述球磨的参数为:球磨机的转速为300r/min~400r/min,球磨时间为60h~90h,球料比为15:1~20:1;所述粉料的粒径小于50μm。本发明通过限定球磨条件,保证了磨球对各原料粉末的机械合金化作用,避免了磨球撞击力过大造成球磨罐受损产生严重的铁屑污染,影响高熵合金吸波材料的成分含量;控制粉料的
粒径,是为了获得粒径较小的复合材料粉体。
20.上述的方法,其特征在于,步骤二、五中所述烘干的过程为:在真空干燥箱中,以真空度不大于0.1pa的条件下加热至60℃~80℃后保温24h以上,所述烘干的过程中向真空干燥箱中通入氩气,并保持氩气流速大于0.1l/min。本发明中步骤二的干燥是为了步骤五中加入的乙醇与粉料的质量比是一致的,为了工艺的统一,真空度不大于0.1pa跟上述球磨罐抽真空一样,加热至60℃~80℃保温24h以上的目的是为了乙醇完全挥发,通入氩气并保持氩气流速为0.1l/min是为了防止残存的空气氧化样品。
21.本发明与现有技术相比具有以下优点:
22.1、本发明的高熵合金/石墨烯复合材料含有fe和ni铁磁性元素,增强了磁损耗能力和吸波能力,al、cr元素提高抗高温氧化能力的同时可以增强合金的耐腐蚀性,添加石墨烯提高了阻抗匹配和衰减特性,使得入射的电磁波尽可能多地进入到高熵合金/石墨烯复合材料内部,在表面实现最小的反射,多种损耗机制的协同作用强烈衰减电磁波的能量,即电磁损耗增加,最大程度的吸收电磁波,还能提高合金的延展性,使复合材料弥散均匀的分散在高熵合金基体上,获得较薄的层片状,磁损耗主要由高熵合金贡献,介电损耗主要由石墨烯贡献,多种电磁波损耗机制协同作用,阻抗匹配良好,最大程度的吸收电磁波,达到提高反射损耗的效果。
23.2、本发明通过利用机械合金化法制备高熵合金/石墨烯复合材料,使高熵合金与石墨烯进行复合,并在球磨过程中多次加入无水乙醇避免在研磨过程中石墨烯的质量减少而造成成分偏差,并且抑制粉末的团聚和粘壁,降低粉末的表面活性,制备同时拥有磁损耗和电损耗的高熵合金/石墨烯复合材料,从而提高其吸波性能。
24.3、本发明制备高熵合金/石墨烯复合材料的方法存在多重极化,包括空间电荷极化,偶极极化,表面极化和界面极化,兼具磁损耗与电损耗,达到既降低材料厚度也可以实现优异吸波性能的目的,制备的高熵合金/石墨烯复合材料呈现多尺度特点,具有宽频高效电磁吸波性能,可广泛应用于各种民用、军事电磁波吸波领域。
25.4、本发明制备的高熵合金/石墨烯复合材料,最大反射损耗值为-42.5db,小于-10db的有效吸波频宽最高达4.9ghz,衰减常数随频率的增大而增大,吸波性能遵循四分之一波长原理,适应与复杂严苛的军事作战环境以及应对电磁污染的日趋泛滥。
26.下面通过附图和实施例对本发明的技术方案作进一步的详细描述。
附图说明
27.图1为本发明实施例1制备的高熵合金/石墨烯复合材料的形貌图。
28.图2是本发明实施例2制备的高熵合金/石墨烯复合材料的吸波性能曲线。
29.图3是本发明实施例3制备的高熵合金/石墨烯复合材料的吸波性能曲线。
具体实施方式
30.实施例1
31.本实施例包括以下步骤:
32.步骤一、将铝粉、铬粉、铁粉、镍粉和石墨烯粉进行混合研磨,得到混合料;所述铝粉的质量纯度大于99.9%,粒度小于5μm,所述铬粉的质量纯度大于99.9%,粒度小于10μm,
所述铁粉的质量纯度大于99.9%,粒度小于10μm,所述镍粉的质量纯度大于99.9%,粒度小于50μm,所述石墨烯粉的质量纯度大于99.9%,粒度小于20μm;所述混合研磨采用玛瑙研钵进行,所述混合研磨中多次加入质量纯度大于99.95%的无水乙醇;
33.步骤二、将步骤一中得到的混合料进行烘干,得到烘干混合料;所述烘干的过程为:在真空干燥箱中,以真空度不大于0.1pa的条件下加热至70℃后保温24h以上,所述烘干的过程中向真空干燥箱中通入氩气,并保持氩气流速大于0.1l/min;
34.步骤三、将步骤二中得到的30g烘干混合料、20ml无水乙醇和600g不锈钢磨球加入到经无水乙醇净化后的不锈钢球磨罐中进行搅拌,然后将不锈钢球磨罐进行封装后往复抽真空、充氩气数次,得到内部为真空状态的密封不锈钢球磨罐;所述真空状态的密封不锈钢球磨罐内部的真空度小于0.1pa;
35.步骤四、将步骤三中得到的密封不锈钢球磨罐转移到高速球磨机上进行球磨,在不锈钢球磨罐中得到粉料;所述球磨的参数为:球磨机的转速为400r/min,球磨时间为60h;所述粉料的粒径小于50μm;
36.步骤五、将步骤四中得到的粉料进行干燥处理,得到具有吸波性能的高熵合金/石墨烯复合材料;所述烘干的过程为:在真空干燥箱中,以真空度不大于0.1pa的条件下加热至80℃后保温24h以上,所述烘干的过程中向真空干燥箱中通入氩气,并保持氩气流速大于0.1l/min;
37.步骤六、将步骤五中得到的高熵合金/石墨烯复合材料进行筛分,得到高熵合金/石墨烯复合材料。
38.经检测,本实施例制备的高熵合金/石墨烯复合材料的分子式为(fenicral
0.2
)
97.5
@c
2.5
,该高熵合金/石墨烯复合材料在厚度为2.5mm时最大反射损耗值为-37.6db,小于-10db的有效吸波频宽2.6ghz,衰减常数随频率的增大而增大,吸波性能遵循四分之一波长原理。
39.图1为本实施例制备的高熵合金/石墨烯复合材料的形貌图,从图1中可以看出,制备的高熵合金/石墨烯复合材料呈现多尺度不规则的片状结构。
40.实施例2
41.本实施例包括以下步骤:
42.步骤一、将铝粉、铬粉、铁粉、镍粉和石墨烯粉进行混合研磨,得到总重为30g的混合料;所述铝粉的质量纯度大于99.9%,粒度小于5μm,所述铬粉的质量纯度大于99.9%,粒度小于10μm,所述铁粉的质量纯度大于99.9%,粒度小于10μm,所述镍粉的质量纯度大于99.9%,粒度小于50μm,所述石墨烯粉的质量纯度大于99.9%,粒度小于20μm;所述混合研磨采用玛瑙研钵进行,所述混合研磨中多次加入质量纯度大于99.95%的无水乙醇;
43.步骤二、将步骤一中得到的混合料进行烘干,得到烘干混合料;所述烘干的过程为:在真空干燥箱中,以真空度不大于0.1pa的条件下加热至60℃后保温24h以上,所述烘干的过程中向真空干燥箱中通入氩气,并保持氩气流速大于0.1l/min;
44.步骤三、将步骤二中得到的40g烘干混合料、20ml无水乙醇和600g不锈钢磨球加入到经无水乙醇净化后的不锈钢球磨罐中进行搅拌,然后将不锈钢球磨罐进行封装后往复抽真空、充氩气数次,得到内部为真空状态的密封不锈钢球磨罐;所述真空状态的密封不锈钢球磨罐内部的真空度小于0.1pa;
45.步骤四、将步骤三中得到的密封不锈钢球磨罐转移到高速球磨机上进行球磨,在不锈钢球磨罐中得到粉料;所述球磨的参数为:球磨机的转速为350r/min,球磨时间为80h;所述粉料的粒径小于50μm;
46.步骤五、将步骤四中得到的粉料进行干燥处理,得到具有吸波性能的高熵合金/石墨烯复合材料;所述烘干的过程为:在真空干燥箱中,以真空度不大于0.1pa的条件下加热至60℃后保温24h以上,所述烘干的过程中向真空干燥箱中通入氩气,并保持氩气流速大于0.1l/min;
47.步骤六、将步骤五中得到的高熵合金/石墨烯复合材料进行筛分,得到高熵合金/石墨烯复合材料。
48.经检测,本实施例制备的高熵合金/石墨烯复合材料的分子式为(fenicral
0.2
)
96
@c4,呈现多尺度不规则的片状结构,该高熵合金/石墨烯复合材料在厚度为2.5mm时最大反射损耗值为-42.5db,小于-10db的有效吸波频宽2.7ghz,衰减常数随频率的增大而增大,吸波性能遵循四分之一波长原理。
49.图2是本实施例制备的高熵合金/石墨烯复合材料的吸波性能曲线,从图2中可以看出,不同曲线代表采用不同厚度的高熵合金/石墨烯复合材料进行吸波测试,可以看出反射损耗随吸波层厚度增加先增大后降低,在厚度为2.5mm时达到最大值,最大的反射损耗值为-42.5db,即此时吸波性能最好。
50.实施例3
51.本实施例包括以下步骤:
52.步骤一、将铝粉、铬粉、铁粉、镍粉和石墨烯粉进行混合研磨,得到总重为30g的混合料;所述铝粉的质量纯度大于99.9%,粒度小于5μm,所述铬粉的质量纯度大于99.9%,粒度小于10μm,所述铁粉的质量纯度大于99.9%,粒度小于10μm,所述镍粉的质量纯度大于99.9%,粒度小于50μm,所述石墨烯粉的质量纯度大于99.9%,粒度小于20μm;所述混合研磨采用玛瑙研钵进行,所述混合研磨中多次加入质量纯度大于99.95%的无水乙醇;
53.步骤二、将步骤一中得到的混合料进行烘干,得到烘干混合料;所述烘干的过程为:在真空干燥箱中,以真空度不大于0.1pa的条件下加热至80℃后保温24h以上,所述烘干的过程中向真空干燥箱中通入氩气,并保持氩气流速大于0.1l/min;
54.步骤三、将步骤二中得到的35g烘干混合料、20ml无水乙醇和600g不锈钢磨球加入到经无水乙醇净化后的不锈钢球磨罐中进行搅拌,然后将不锈钢球磨罐进行封装后往复抽真空、充氩气数次,得到内部为真空状态的密封不锈钢球磨罐;所述真空状态的密封不锈钢球磨罐内部的真空度小于0.1pa;
55.步骤四、将步骤三中得到的密封不锈钢球磨罐转移到高速球磨机上进行球磨,在不锈钢球磨罐中得到粉料;所述球磨的参数为:球磨机的转速为400r/min,球磨时间为60h;所述粉料的粒径小于50μm;
56.步骤五、将步骤四中得到的粉料进行干燥处理,得到具有吸波性能的高熵合金/石墨烯复合材料;所述烘干的过程为:在真空干燥箱中,以真空度不大于0.1pa的条件下加热至70℃后保温24h以上,所述烘干的过程中向真空干燥箱中通入氩气,并保持氩气流速大于0.1l/min;
57.步骤六、将步骤五中得到的高熵合金/石墨烯复合材料进行筛分,得到高熵合金/
石墨烯复合材料。
58.经检测,本实施例制备的高熵合金/石墨烯复合材料的分子式为(fenicral
0.2
)
94
@c6,呈现多尺度不规则的片状结构,该高熵合金/石墨烯复合材料在厚度为2mm时最大反射损耗值为-37.3db,小于-10db的有效吸波频宽4.9ghz,衰减常数随频率的增大而增大,吸波性能遵循四分之一波长原理。
59.图3是本实施例制备的高熵合金/石墨烯复合材料的吸波性能曲线,从图3中可以看出,不同曲线代表采用不同厚度的高熵合金/石墨烯复合材料进行吸波测试,可以看出反射损耗随吸波层厚度增加先增大后降低,在厚度为2mm时达到最大值,最大的反射损耗值为-37.3db,即此时吸波性能最好。
60.实施例4
61.本实施例包括以下步骤:
62.步骤一、将铝粉、铬粉、铁粉、镍粉和石墨烯粉进行混合研磨,得到总重为30g的混合料;所述铝粉的质量纯度大于99.9%,粒度小于5μm,所述铬粉的质量纯度大于99.9%,粒度小于10μm,所述铁粉的质量纯度大于99.9%,粒度小于10μm,所述镍粉的质量纯度大于99.9%,粒度小于50μm,所述石墨烯粉的质量纯度大于99.9%,粒度小于20μm;所述混合研磨采用玛瑙研钵进行,所述混合研磨中多次加入质量纯度大于99.95%的无水乙醇;
63.步骤二、将步骤一中得到的混合料进行烘干,得到烘干混合料;所述烘干的过程为:在真空干燥箱中,以真空度不大于0.1pa的条件下加热至70℃后保温24h以上,所述烘干的过程中向真空干燥箱中通入氩气,并保持氩气流速大于0.1l/min;
64.步骤三、将步骤二中得到的30g烘干混合料、20ml无水乙醇和600g不锈钢磨球加入到经无水乙醇净化后的不锈钢球磨罐中进行搅拌,然后将不锈钢球磨罐进行封装后往复抽真空、充氩气数次,得到内部为真空状态的密封不锈钢球磨罐;所述真空状态的密封不锈钢球磨罐内部的真空度小于0.1pa;
65.步骤四、将步骤三中得到的密封不锈钢球磨罐转移到高速球磨机上进行球磨,在不锈钢球磨罐中得到粉料;所述球磨的参数为:球磨机的转速为300r/min,球磨时间为90h;所述粉料的粒径小于50μm;
66.步骤五、将步骤四中得到的粉料进行干燥处理,得到具有吸波性能的高熵合金/石墨烯复合材料;所述烘干的过程为:在真空干燥箱中,以真空度不大于0.1pa的条件下加热至70℃后保温24h以上,所述烘干的过程中向真空干燥箱中通入氩气,并保持氩气流速大于0.1l/min;
67.步骤六、将步骤五中得到的高熵合金/石墨烯复合材料进行筛分,得到呈现多尺度不规则片状的高熵合金/石墨烯复合粉状材料。
68.经检测,本实施例制备的高熵合金/石墨烯复合材料的分子式为(fenicral
0.2
)
92
@c8,呈现多尺度不规则的片状结构,该成高熵合金/石墨烯复合材料在厚度为2.5mm时最大反射损耗值为-35.5db,小于-10db的有效吸波频宽2.8ghz,衰减常数随频率的增大而增大,吸波性能遵循四分之一波长原理。
69.将本发明实施例1~4制备的高熵合金/石墨烯复合材料进行饱和磁化强度ms和矫顽力hc测试,得到的结果如表1所示,从表1可以看出,本发明制备的高熵合金/石墨烯复合材料的饱和磁化强度ms最高可达0.196emu/g,矫顽力hc最高仅为87.70oe。
70.表1
[0071][0072]
以上所述,仅是本发明的较佳实施例,并非对本发明作任何限制。凡是根据发明技术实质对以上实施例所作的任何简单修改、变更以及等效变化,均仍属于本发明技术方案的保护范围内。