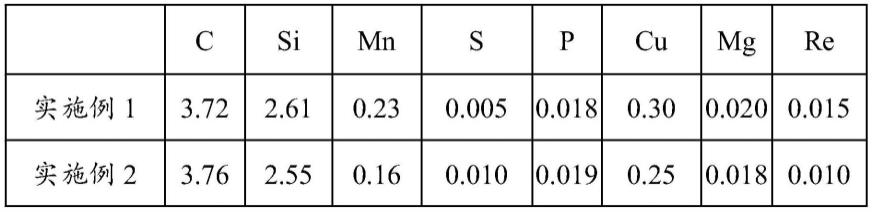
1.本发明涉及汽车发动机摇臂领域,特别涉及一种球墨铸铁摇臂及其制造方法和应用。
背景技术:2.摇臂是发动机配气机构的重要构件,其作用是将挺杆或凸轮轴的运动传递给气门,摇臂在载荷作用下将产生弯曲变形,进排气摇臂在工作过程中应具有足够的强度和刚度。对于中重型商用车柴油发动机,摇臂要承受较大的应力,而锻钢材料具有强度高、刚度大等特点,是大马力发动机摇臂的首选材料。然而,锻钢摇臂重量较重,加工余量较大,成本较高,难以满足汽车轻量化和降成本的要求。因此,在满足可靠性的前提下,采用合适的材料和工艺来降低摇臂的重量和生产成本是很有意义的。
3.目前,现有技术通常采用轻合金材料或铸造工艺来制造摇臂,来降低摇臂的重量或成本。采用轻合金材料可以明显降低摇臂重量,但其成本较高。采用铸造工艺成型性好,可以大大减小摇臂加工余量,加工性能好,降低摇臂成本,但铸造材料性能较差,难以保证零件可靠性和重量。目前,同时能降低锻钢摇臂重量和成本的技术方案鲜有报告。
4.中国专利文献cn110847996a公开一种发动机用轻质钛合金复合材料摇臂,该轻质钛合金复合材料摇臂重量较轻,抗拉强度≥1030mpa,屈服强度≥910mpa,延伸率≥8%,该摇臂力学性能虽然媲美锻钢摇臂,但其工艺复杂,成本较高,难以大规模应用。
5.球墨铸铁具有更好的耐磨性、低廉的成本、较好的工艺性和较低的密度等优点,采用铸铁摇臂替代锻钢摇臂可以降低材料成本、取消摇臂衬套、减小零件加工余量,来实现降成本的目的。但铸铁与锻钢材料相比,力学性能较低,难以保证零件重量和可靠性。譬如,中国专利文献cn 104775065 a公开的一种高强韧耐磨球铁摇臂及其制备方法,摇臂的材料化学组成按质量分数计,包括3.45-3.7%c,1.3-1.45%si,mn≤0.2%,0.15-0.25%cu,0.03-0.06%nb,s<0.04%,p<0.04%,余量为fe及不可避免的杂质。摇臂的制备方法包括熔炼、复合孕育、球化、多元微合金变质处理和热处理等步骤,该制备方法较复杂,虽然可以降低一定的成本,但与锻钢摇臂相比,摇臂的力学性能特别是疲劳性能有明显的下降,需提高零件的重量来提升疲劳性能,因而难以降低零件的重量。
技术实现要素:6.针对现有球墨铸铁摇臂难以在强度和韧性上媲美锻钢摇臂的问题,本发明通过严格控制化学成分、铸造工艺以及热处理工艺,制造出了抗拉强度和疲劳强度可媲美锻钢摇臂的球墨铸铁摇臂。
7.本发明是通过如下技术方案来实现的:
8.本发明提供的一种球墨铸铁摇臂的制造方法,包括:
9.铸造球墨铸铁摇臂铸件;所述球墨铸铁摇臂铸件包含如下化学成分:3.70wt.%~3.90wt.%c、2.55wt.%~2.90wt.%si、
10.0.15wt.%~0.35wt.%mn、p≤0.04wt.%、s≤0.02wt.%、0.015wt.%~0.04wt.%mg、0.20wt.%~0.35wt.%cu、0.01wt.%~0.03wt.%re,余量为fe和不可避免的杂质;
11.正火处理:将球墨铸铁摇臂铸件加热至830-860℃,保温70min-100min,风冷至400℃以下;
12.回火处理:将正火后的球墨铸铁摇臂铸件加热至540℃-560℃,保温60min-90min后空冷至室温。
13.在本发明提供的一些实施例中,风冷降温速度为30-70℃/min。
14.在本发明提供的一些实施例中,球墨铸铁摇臂铸件包含如下化学成分:
15.c:3.72wt.%~3.85wt.%;
16.si:2.55wt.%~2.90wt.%;
17.mn:0.16wt.%~0.35wt.%;
18.p≤0.025wt.%;
19.s≤0.010wt.%;
20.mg:0.018wt.%~0.022wt.%;
21.cu:0.25wt.%~0.35wt.%;
22.re:0.010wt.%~0.018wt.%;
23.余量为fe和不可避免的杂质。
24.在本发明提供的一些实施例中,所述铸造球墨铸铁摇臂铸件包括:
25.熔炼:使用中频炉进行铁液熔炼,将回炉料、生铁和废钢熔炼至熔融状态,根据化学成分检测结果加入增碳剂和合金调整铁液化学成分,控制出炉温度在1500℃-1520℃范围内,然后出炉;
26.球化处理:出炉时向球化包底部依次加入1.0wt.%-1.3wt.%的球化剂、0.25wt.%-0.35wt.%的包底孕育剂和铁;
27.浇注:将球化处理后的铁液在温度1400℃~1420℃时进行浇注,在浇注的同时加入随流孕育剂进行随流孕育,随流孕育剂占铁液的0.1wt.%~0.20wt.%。
28.在本发明提供的一些实施例中,所述球化剂采用稀土镁硅合金;所述稀土镁硅合金中,mg含量为6wt.%~8wt.%,re含量为2wt.%~4wt.%,ca含量为2wt.%~3.5wt.%,si含量为35wt.%~44wt.%,余量为铁和不可避免的杂质。
29.在本发明提供的一些实施例中,所述包底孕育剂为硅铝锆孕育剂;所述硅铝锆孕育剂中,si含量为62wt.%~69wt.%,al含量为3wt.%~5wt.%,zr含量为3wt.%~5wt.%,余量为铁和不可避免的杂质。
30.在本发明提供的一些实施例中,所述随流孕育剂为硅铋孕育剂,所述硅铋孕育剂中si含量为70wt.%~80wt.%,bi含量为2wt.%~3wt.%,余量为铁和不可避免杂质。
31.本发明还提供一种由上述球墨铸铁摇臂的制造方法制造而成的球墨铸铁摇臂,由上述球墨铸铁摇臂的制造方法制造而成的球墨铸铁摇臂的抗拉强度能达到852~941mpa,延伸率能达到6%~9%,硬度达到231~245hb,可与锻钢摇臂相媲美,且该球墨铸铁摇臂密度小于锻钢摇臂,降低了零件自重;此外,与锻钢摇臂相比,球墨铸铁摇臂加工余量小,降低了后续机械加工的难度和成本。
32.本发明还提供上述球墨铸铁摇臂作为中型柴油发动机进气摇臂、中型柴油发动机排气摇臂、重型柴油发动机进气摇臂中任意一种或几种的应用。上述球墨铸铁摇臂具有较高的抗拉强度和韧性,能满足中型柴油发动机进气摇臂、中型柴油发动机排气摇臂、重型柴油发动机进气摇臂对抗拉强度和韧性的要求,且上述球墨铸铁摇臂具有较好的耐磨性,可以取消摇臂衬套和磷化工艺。
33.与现有技术相比,本发明能够获得抗拉强度和疲劳强度与锻钢摇臂相媲美的球墨铸铁摇臂,相比锻钢摇臂,球墨铸铁摇臂密度小且加工余量小,因而降低了零件自重和后续机械加工成本。
具体实施方式
34.为使本发明实施例的目的、技术方案和优点更加清楚,下面将结合具体实施例对本发明的技术方案进行清楚、完整地描述,显然,所描述的实施例是本发明的一部分实施例,而不是全部的实施例。基于本发明中的实施例,本领域普通技术人员在没有做出创造性劳动的前提下所获得的所有其他实施例,都属于本发明保护的范围。
35.本发明提供的一种球墨铸铁摇臂的制造方法,包括:
36.铸造球墨铸铁摇臂铸件;所述球墨铸铁摇臂铸件包含如下化学成分:3.70wt.%~3.90wt.%c、2.55wt.%~2.90wt.%si、
37.0.15wt.%~0.35wt.%mn、p≤0.04wt.%、s≤0.02wt.%、0.015wt.%~0.04wt.%mg、0.20wt.%~0.35wt.%cu、0.01wt.%~0.03wt.%re,余量为fe和不可避免的杂质;
38.正火处理:将球墨铸铁摇臂铸件加热至830-860℃,保温70min-100min,风冷至400℃以下;
39.回火处理:将正火后的球墨铸铁摇臂铸件加热至540℃-560℃,保温60min-90min后空冷至室温。
40.本发明通过严格控制化学成分、铸造工艺和热处理工艺,除了能够获得抗拉强度和韧性与锻钢摇臂相媲美的球墨铸铁摇臂外,材料石墨细小圆整,石墨球数和珠光体含量较多,具有较好的耐磨性,可以取消摇臂衬套和磷化工艺。此外,相比锻钢摇臂,球墨铸铁摇臂密度小且加工余量小,因而降低了零件自重和后续机械加工成本。
41.在本发明提供的一些实施例中,球墨铸铁摇臂铸件包含如下化学成分:
42.c:3.72wt.%~3.85wt.%;
43.si:2.55wt.%~2.90wt.%;
44.mn:0.16wt.%~0.35wt.%;
45.p≤0.025wt.%;
46.s≤0.010wt.%;
47.mg:0.018wt.%~0.022wt.%;
48.cu:0.25wt.%~0.35wt.%;
49.re:0.010wt.%~0.018wt.%;
50.余量为fe和不可避免的杂质。
51.在本发明提供的一些实施例中,所述铸造球墨铸铁摇臂铸件包括:
52.熔炼:使用中频炉进行铁液熔炼,将回炉料、生铁和废钢熔炼至熔融状态,根据化学成分检测结果加入增碳剂和合金调整铁液化学成分,控制出炉温度在1500℃-1520℃范围内,然后出炉;
53.球化处理:出炉时向球化包底部依次加入1.0wt.%-1.3wt.%的球化剂、0.25wt.%-0.35wt.%的包底孕育剂和铁;
54.浇注:将球化处理后的铁液在温度1400℃~1420℃时进行浇注,在浇注的同时加入随流孕育剂进行随流孕育,随流孕育剂占铁液的0.1wt.%~0.20wt.%。
55.在本发明提供的一些实施例中,所述球化剂采用稀土镁硅合金;所述稀土镁硅合金中,mg含量为6wt.%~8wt.%,re含量为2wt.%~4wt.%,ca含量为2wt.%~3.5wt.%,si含量为35wt.%~44wt.%,余量为铁和不可避免的杂质。
56.在本发明提供的一些实施例中,所述包底孕育剂为硅铝锆孕育剂;所述硅铝锆孕育剂中,si含量为62wt.%~69wt.%,al含量为3wt.%~5wt.%,zr含量为3wt.%~5wt.%,余量为铁和不可避免的杂质。
57.在本发明提供的一些实施例中,所述随流孕育剂为硅铋孕育剂,所述硅铋孕育剂中si含量为70wt.%~80wt.%,bi含量为2wt.%~3wt.%,余量为铁和不可避免杂质。
58.本发明还提供一种由上述球墨铸铁摇臂的制造方法制造而成的球墨铸铁摇臂,由上述球墨铸铁摇臂的制造方法制造而成的球墨铸铁摇臂的抗拉强度能达到852~941mpa,延伸率能达到6%~9%,硬度达到231~245hb,可与锻钢摇臂相媲美,且该球墨铸铁摇臂密度小于锻钢摇臂,降低了零件自重;此外,与锻钢摇臂相比,球墨铸铁摇臂加工余量小,降低了后续机械加工的难度和成本。
59.本发明还提供上述球墨铸铁摇臂作为中型柴油发动机进气摇臂、中型柴油发动机排气摇臂、重型柴油发动机进气摇臂中任意一种或几种的应用。上述球墨铸铁摇臂具有较高的抗拉强度和韧性,能满足中型柴油发动机进气摇臂、中型柴油发动机排气摇臂、重型柴油发动机进气摇臂对抗拉强度和韧性的要求,且上述球墨铸铁摇臂具有较好的耐磨性,可以取消摇臂衬套和磷化工艺。
60.本发明中涉及到的化学元素在铸造球墨铸铁摇臂中起到的作用以及所要控制的含量范围如下:
61.c:c含量高,铸铁中析出的石墨球数多,促进石墨飘浮,力学性能下降;c含量低,增加铸件收缩倾向,降低材料铸造性能。为了保证力学性能和铸造工艺性能,本发明控制c含量的范围为3.70wt.%~3.90wt.%。
62.si:si是促进石墨化元素,随着si量增加,增加强度硬度,降低韧性,促进铁素体形成。si能提高共析转变温度,在热处理过程中可以加速珠光体和碳化物分解。本发明摇臂属于薄壁件,采用高si方案,其含量控制在2.55wt.%~2.9wt.%的范围内。
63.mn:mn促进珠光体形成,含量较多会增加白口倾向,容易偏析到晶界产生碳化物。本发明mn含量控制在0.15wt.%-0.35wt.%范围内。
64.s:与球化元素(主要为mg和re)都有很大亲和力。原铁液含s越多,消耗球化剂也越多,增加浮渣的产生,易导致球化衰退,严重影响球化效果,本发明中s含量限制在0.02wt.%以内。
65.mg、re:mg和re是球化元素,能够抑制片状石墨形成,含量低时会形成片状石墨,含
量较高会增加白口倾向和缩松倾向,并增加生产成本,本发明严格控制mg含量为0.015wt.%~0.04wt.%,re含量为0.01%~0.03%。
66.p:一般为有害元素,p元素过多会形成磷共晶,降低材料的韧性,使铸件易出现缩松和冷裂。本发明中p元素含量应控制在0.04wt.%内。
67.cu:cu在共晶转变时促进石墨化,减小或消除游离渗碳体。在共析过程中促进珠光体的形成,并改善组织与性能均匀性。cu含量加入过多,成本上升,延伸率下降。本发明cu的含量为0.20wt.%-0.35wt.%。
68.球化剂:本发明的球化剂采用稀土镁硅合金。球化剂中的mg能使石墨球圆整,但抗微量元素干扰能力差。re能够中和微量干扰元素的影响,但会促进铸件白口化和缩松倾向。ca的白口倾向相对于mg、re较弱,能延缓铁液与球化剂的反应剧烈程度。本发明将球化剂中mg的含量控制在6wt.%~8wt.%,re含量控制在2wt.%~4wt.%,ca含量控制在2wt.%~3.5wt.%,si含量控制在35wt.%~44wt.%。
69.球化处理:为了避免球化不良或球化过量,要控制好压包工艺和球化剂含量。压包过程中优先加入球化剂,随后加入压包孕育剂和铁板,可以避免球化剂过早或过晚反应。球化剂加入量也要严格控制,加入量偏多,易造成石墨异化、白口、缩孔缩松等倾向;加入量偏少,容易球化不良。本发明采用稀土镁硅球化剂加入量应控制在1.0wt.%~1.3wt.%范围内。
70.孕育剂:孕育剂的作用是消除球化元素mg和re引起的白口倾向,阻碍碳化物的形成,同时孕育剂还具有细化组织、改善性能和延缓球化衰退。本发明摇臂为中小薄壁零件,易形成碳化物,应采用强效孕育剂并避免加入含sb等促珠光体形成孕育剂。本发明采用压包孕育+随流孕育的孕育工艺。球化剂和孕育剂中的re、mg、bi、zr元素复合加入,在抑制碳化物生成的基础上,能够净化铁水,消除杂质元素的影响,增加石墨球数,细化石墨球,提高石墨圆整性,保证了零件的组织性能。本发明包底孕育剂为硅铝锆孕育剂,加入量为铁液的0.25wt.%-0.35wt.%,随流孕育剂为硅铋孕育剂,加入量为铁液的0.1wt.%-0.20wt.%。
71.热处理:在制备具有细小完整石墨球铸态铸件的基础上,通过部分奥氏体化热处理将部分基体转化为奥氏体,剩余铁素体弥散分布于奥氏体之间,冷却后获得细小的珠光体和弥散铁素体组织。与铸态零件相比,热处理后增加并细化了珠光体,又保留了部分铁素体,提高了零件强度硬度,并有一定的延伸性。零件化学成分和零件形状尺寸影响热处理工艺参数,进而影响零件的力学性能和疲劳性能。本发明摇臂零件壁厚较薄,选用高c、si和低cu方案来保证制备良好组织性能的铸态零件,si增加热处理温度,cu降低热处理时间,同时为保证热处理后的组织性能。本发明热处理正火温度830-860℃,保温70min-100min,回火温度540℃-560℃,保温60min-90min,保证零件的强度和韧性,降低热处理后残余应力,避免表面脱碳层对零件疲劳的影响,保证摇臂零件拥有良好的疲劳强度。
72.如无特殊说明,本发明以下实施例和对比例所采用的铸造原料中回炉料、生铁和废钢分别占20wt.%、60wt.%、20wt.%,且以下实施例和对比例均采用同一批次的稀土镁硅合金、硅铝锆孕育剂和硅铋孕育剂。
73.实施例1
74.本实施例提供的一种球墨铸铁摇臂的制造方法,包括如下步骤:
75.(1)铸造球墨铸铁摇臂铸件,使球墨铸铁摇臂铸件具有如下化学组成:c:
3.72wt.%,si:2.61wt.%,mn:0.23wt.%,p:0.018wt.%,s:0.005wt.%,mg:0.020wt.%,cu:0.30wt.%,re:0.015wt.%,余量为fe和不可避免的杂质;
76.(1.1)熔炼:使用中频炉进行铁液熔炼,将回炉料、生铁和废钢熔炼至熔融状态,根据化学成分检测结果加入增碳剂和合金以调整铁液的化学组成,控制出炉温度在1500℃-1520℃范围内,然后铁液出炉;
77.(1.2)球化处理:铁液出炉时,向球化包底部依次加入1.2wt.%的稀土镁硅合金作为球化剂、0.30wt.%的硅铝锆孕育剂作为包底孕育剂以及铁;所述稀土镁硅合金中,mg含量为6wt.%~8wt.%,re含量为2wt.%~4wt.%,ca含量为2wt.%~3.5wt.%,si含量为35wt.%~44wt.%,余量为铁和不可避免的杂质;所述硅铝锆孕育剂中,si含量为62wt.%~69wt.%,al含量为3wt.%~5wt.%,zr含量为3wt.%~5wt.%,余量为铁和不可避免的杂质;
78.(1.3)浇注:将球化处理后的铁液温度控制在1400℃~1420℃之间,进行浇注,在浇注的同时加入硅铋孕育剂作为随流孕育剂进行随流孕育,随流孕育剂占铁液的0.1wt.%~0.20wt.%;硅铋孕育剂中si含量为70wt.%~80wt.%,bi含量为2wt.%~3wt.%,余量为铁和不可避免杂质;
79.(2)正火处理:将球墨铸铁摇臂铸件加热至850℃,保温90min,以30℃/min~70℃/min的风冷降温速度风冷至380℃;
80.(3)回火处理:将正火后的球墨铸铁摇臂铸件加热至550℃,保温90min后空冷至室温;
81.(4)机加工:对回火处理后的产品进行喷丸处理和机加工。
82.实施例2
83.本实施例提供的一种球墨铸铁摇臂的制造方法,包括如下步骤:
84.(1)铸造球墨铸铁摇臂铸件,使球墨铸铁摇臂铸件具有如下化学组成:c:3.76wt.%,si:2.55wt.%,mn:0.16wt.%,p:0.019wt.%,s:0.010wt.%,mg:0.018wt.%,cu:0.25wt.%,re:0.010wt.%,余量为fe和不可避免的杂质;
85.(1.1)熔炼:使用中频炉进行铁液熔炼,将回炉料、生铁和废钢熔炼至熔融状态,根据化学成分检测结果加入增碳剂和合金以调整铁液的化学组成,控制出炉温度在1500℃-1520℃范围内,然后铁液出炉;
86.(1.2)球化处理:铁液出炉时,向球化包底部依次加入1.2wt.%的稀土镁硅合金作为球化剂、0.30wt.%的硅铝锆孕育剂作为包底孕育剂以及铁;所述稀土镁硅合金中,mg含量为6wt.%~8wt.%,re含量为2wt.%~4wt.%,ca含量为2wt.%~3.5wt.%,si含量为35wt.%~44wt.%,余量为铁和不可避免的杂质;所述硅铝锆孕育剂中,si含量为62wt.%~69wt.%,al含量为3wt.%~5wt.%,zr含量为3wt.%~5wt.%,余量为铁和不可避免的杂质;
87.(1.3)浇注:将球化处理后的铁液温度控制在1400℃~1420℃之间,进行浇注,在浇注的同时加入硅铋孕育剂作为随流孕育剂进行随流孕育,随流孕育剂占铁液的0.1wt.%~0.20wt.%;硅铋孕育剂中si含量为70wt.%~80wt.%,bi含量为2wt.%~3wt.%,余量为铁和不可避免杂质;
88.(2)正火处理:将球墨铸铁摇臂铸件加热至860℃,保温70min,以30℃/min~70℃/
min的风冷降温速度风冷至380℃;
89.(3)回火处理:将正火后的球墨铸铁摇臂铸件加热至550℃,保温90min后空冷至室温;
90.(4)机加工:对回火处理后的产品进行喷丸处理和机加工。
91.实施例3
92.本实施例提供的一种球墨铸铁摇臂的制造方法,包括如下步骤:
93.(1)铸造球墨铸铁摇臂铸件,使球墨铸铁摇臂铸件具有如下化学组成:c:3.85wt.%,si:2.89wt.%,mn:0.35wt.%,p:0.022wt.%,s:0.008wt.%,mg:0.022wt.%,cu:0.32wt.%,re:0.018wt.%,余量为fe和不可避免的杂质;
94.(1.1)熔炼:使用中频炉进行铁液熔炼,将回炉料、生铁和废钢熔炼至熔融状态,根据化学成分检测结果加入增碳剂和合金以调整铁液的化学组成,控制出炉温度在1500℃-1520℃范围内,然后铁液出炉;
95.(1.2)球化处理:铁液出炉时,向球化包底部依次加入1.2wt.%的稀土镁硅合金作为球化剂、0.30wt.%的硅铝锆孕育剂作为包底孕育剂以及铁;所述稀土镁硅合金中,mg含量为6wt.%~8wt.%,re含量为2wt.%~4wt.%,ca含量为2wt.%~3.5wt.%,si含量为35wt.%~44wt.%,余量为铁和不可避免的杂质;所述硅铝锆孕育剂中,si含量为62wt.%~69wt.%,al含量为3wt.%~5wt.%,zr含量为3wt.%~5wt.%,余量为铁和不可避免的杂质;
96.(1.3)浇注:将球化处理后的铁液温度控制在1400℃~1420℃之间,进行浇注,在浇注的同时加入硅铋孕育剂作为随流孕育剂进行随流孕育,随流孕育剂占铁液的0.1wt.%~0.20wt.%;硅铋孕育剂中si含量为70wt.%~80wt.%,bi含量为2wt.%~3wt.%,余量为铁和不可避免杂质;
97.(2)正火处理:将球墨铸铁摇臂铸件加热至830℃,保温100min,以30℃/min~70℃/min的风冷降温速度风冷至380℃;
98.(3)回火处理:将正火后的球墨铸铁摇臂铸件加热至550℃,保温90min后空冷至室温;
99.(4)机加工:对回火处理后的产品进行喷丸处理和机加工。
100.对比例1
101.本对比例提供的一种球墨铸铁摇臂的制造方法,包括如下步骤:
102.(1)铸造球墨铸铁摇臂铸件,使球墨铸铁摇臂铸件具有如下化学组成:c:3.83wt.%,si:2.10wt.%,mn:0.31wt.%,p:0.022wt.%,s:0.009wt.%,mg:0.025wt.%,cu:0.28wt.%,re:0.011wt.%,余量为fe和不可避免的杂质;
103.(1.1)熔炼:使用中频炉进行铁液熔炼,将回炉料、生铁和废钢熔炼至熔融状态,根据化学成分检测结果加入增碳剂和合金以调整铁液的化学组成,控制出炉温度在1500℃-1520℃范围内,然后铁液出炉;
104.(1.2)球化处理:铁液出炉时,向球化包底部依次加入1.2wt.%的稀土镁硅合金作为球化剂、0.30wt.%的硅铝锆孕育剂作为包底孕育剂以及铁;所述稀土镁硅合金中,mg含量为6wt.%~8wt.%,re含量为2wt.%~4wt.%,ca含量为2wt.%~3.5wt.%,si含量为35wt.%~44wt.%,余量为铁和不可避免的杂质;所述硅铝锆孕育剂中,si含量为62wt.%
~69wt.%,al含量为3wt.%~5wt.%,zr含量为3wt.%~5wt.%,余量为铁和不可避免的杂质。
105.(1.3)浇注:将球化处理后的铁液温度控制在1400℃~1420℃之间,进行浇注,在浇注的同时加入硅铋孕育剂作为随流孕育剂进行随流孕育,随流孕育剂占铁液的0.1wt.%~0.20wt.%;硅铋孕育剂中si含量为70wt.%~80wt.%,bi含量为2wt.%~3wt.%,余量为铁和不可避免杂质;
106.(2)正火处理:将球墨铸铁摇臂铸件加热至850℃,保温90min,以30℃/min~70℃/min的风冷降温速度风冷至380℃;
107.(3)回火处理:将正火后的球墨铸铁摇臂铸件加热至550℃,保温90min后空冷至室温;
108.(4)机加工:对回火处理后的产品进行喷丸处理和机加工。
109.对比例2
110.本对比例提供的一种球墨铸铁摇臂的制造方法,与实施例1相比,区别之处在于未进行正火处理和回火处理,球墨铸铁摇臂铸件铸造完成后直接进行机加工。
111.本对比例提供的一种球墨铸铁摇臂的制造方法,包括如下步骤:
112.(1)铸造球墨铸铁摇臂铸件,使球墨铸铁摇臂铸件具有如下化学组成:c:3.72wt.%,si:2.61wt.%,mn:0.23wt.%,p:0.018wt.%,s:0.005wt.%,mg:0.020wt.%,cu:0.30wt.%,re:0.015wt.%,余量为fe和不可避免的杂质;
113.(1.1)熔炼:使用中频炉进行铁液熔炼,将回炉料、生铁和废钢熔炼至熔融状态,根据化学成分检测结果加入增碳剂和合金以调整铁液的化学组成,控制出炉温度在1500℃-1520℃范围内,然后铁液出炉;
114.(1.2)球化处理:铁液出炉时,向球化包底部依次加入1.2wt.%的稀土镁硅合金作为球化剂、0.30wt.%的硅铝锆孕育剂作为包底孕育剂以及铁;所述稀土镁硅合金中,mg含量为6wt.%~8wt.%,re含量为2wt.%~4wt.%,ca含量为2wt.%~3.5wt.%,si含量为35wt.%~44wt.%,余量为铁和不可避免的杂质;所述硅铝锆孕育剂中,si含量为62wt.%~69wt.%,al含量为3wt.%~5wt.%,zr含量为3wt.%~5wt.%,余量为铁和不可避免的杂质;
115.(1.3)浇注:将球化处理后的铁液温度控制在1400℃~1420℃之间,进行浇注,在浇注的同时加入硅铋孕育剂作为随流孕育剂进行随流孕育,随流孕育剂占铁液的0.1wt.%~0.20wt.%;硅铋孕育剂中si含量为70wt.%~80wt.%,bi含量为2wt.%~3wt.%,余量为铁和不可避免杂质;
116.(2)机加工:对球墨铸铁摇臂铸件进行喷丸处理和机加工。
117.对比例3
118.本对比例提供的一种球墨铸铁摇臂的制造方法,与实施例1相比,区别之处在于球墨铸铁摇臂铸件正火处理后,直接空冷至室温。
119.本对比例提供的一种球墨铸铁摇臂的制造方法,包括如下步骤:
120.(1)铸造球墨铸铁摇臂铸件,使球墨铸铁摇臂铸件具有如下化学组成:c:3.72wt.%,si:2.61wt.%,mn:0.23wt.%,p:0.018wt.%,s:0.005wt.%,mg:0.020wt.%,cu:0.30wt.%,re:0.015wt.%,余量为fe和不可避免的杂质;
121.(1.1)熔炼:使用中频炉进行铁液熔炼,将回炉料、生铁和废钢熔炼至熔融状态,根据化学成分检测结果加入增碳剂和合金以调整铁液的化学组成,控制出炉温度在1500℃-1520℃范围内,然后铁液出炉;
122.(1.2)球化处理:铁液出炉时,向球化包底部依次加入1.2wt.%的稀土镁硅合金作为球化剂、0.30wt.%的硅铝锆孕育剂作为包底孕育剂以及铁;所述稀土镁硅合金中,mg含量为6wt.%~8wt.%,re含量为2wt.%~4wt.%,ca含量为2wt.%~3.5wt.%,si含量为35wt.%~44wt.%,余量为铁和不可避免的杂质;所述硅铝锆孕育剂中,si含量为62wt.%~69wt.%,al含量为3wt.%~5wt.%,zr含量为3wt.%~5wt.%,余量为铁和不可避免的杂质。
123.(1.3)浇注:将球化处理后的铁液温度控制在1400℃~1420℃之间,进行浇注,在浇注的同时加入硅铋孕育剂作为随流孕育剂进行随流孕育,随流孕育剂占铁液的0.1wt.%~0.20wt.%;硅铋孕育剂中si含量为70wt.%~80wt.%,bi含量为2wt.%~3wt.%,余量为铁和不可避免杂质;
124.(2)正火处理:将球墨铸铁摇臂铸件加热至850℃,保温90min,空冷至室温。
125.(3)回火处理:将正火后的球墨铸铁摇臂铸件加热至550℃,保温90min后空冷至室温;
126.(4)机加工:对正火处理后的产品进行喷丸处理和机加工。
127.对比例4
128.本对比例提供的一种球墨铸铁摇臂的制造方法,与实施例1相比,区别之处在于球墨铸铁摇臂铸件的正火处理时间为150min,测试发现所得摇臂样品表面脱碳层>400μm。
129.本实施例提供的一种球墨铸铁摇臂的制造方法,包括如下步骤:
130.(1)铸造球墨铸铁摇臂铸件,使球墨铸铁摇臂铸件具有如下化学组成:c:3.72wt.%,si:2.61wt.%,mn:0.23wt.%,p:0.018wt.%,s:0.005wt.%,mg:0.020wt.%,cu:0.30wt.%,re:0.015wt.%,余量为fe和不可避免的杂质;
131.(1.1)熔炼:使用中频炉进行铁液熔炼,将回炉料、生铁和废钢熔炼至熔融状态,根据化学成分检测结果加入增碳剂和合金以调整铁液的化学组成,控制出炉温度在1500℃-1520℃范围内,然后铁液出炉;
132.(1.2)球化处理:铁液出炉时,向球化包底部依次加入1.2wt.%的稀土镁硅合金作为球化剂、0.30wt.%的硅铝锆孕育剂作为包底孕育剂以及铁;所述稀土镁硅合金中,mg含量为6wt.%~8wt.%,re含量为2wt.%~4wt.%,ca含量为2wt.%~3.5wt.%,si含量为35wt.%~44wt.%,余量为铁和不可避免的杂质;所述硅铝锆孕育剂中,si含量为62wt.%~69wt.%,al含量为3wt.%~5wt.%,zr含量为3wt.%~5wt.%,余量为铁和不可避免的杂质;
133.(1.3)浇注:将球化处理后的铁液温度控制在1400℃~1420℃之间,进行浇注,在浇注的同时加入硅铋孕育剂作为随流孕育剂进行随流孕育,随流孕育剂占铁液的0.1wt.%~0.20wt.%;硅铋孕育剂中si含量为70wt.%~80wt.%,bi含量为2wt.%~3wt.%,余量为铁和不可避免杂质;
134.(2)正火处理:将球墨铸铁摇臂铸件加热至850℃,保温150min,以30℃/min~70℃/min的风冷降温速度风冷至380℃;
135.(3)回火处理:将正火后的球墨铸铁摇臂铸件加热至550℃,保温90min后空冷至室温;
136.(4)机加工:对回火处理后的产品进行喷丸处理和机加工。
137.对比例5
138.本对比例提供的一种球墨铸铁摇臂的制造方法,包括如下步骤:
139.(1)铸造球墨铸铁摇臂铸件,使球墨铸铁摇臂铸件具有如下化学组成:c:3.87wt.%,si:2.56wt.%,mn:0.27wt.%,p:0.015wt.%,s:0.007wt.%,mg:0.033wt.%,cu:0.34wt.%,re:0.026wt.%,余量为fe和不可避免的杂质;
140.(1.1)熔炼:使用中频炉进行铁液熔炼,将回炉料、生铁和废钢熔炼至熔融状态,根据化学成分检测结果加入增碳剂和合金以调整铁液的化学组成,控制出炉温度在1500℃-1520℃范围内,然后铁液出炉;
141.(1.2)球化处理:铁液出炉时,向球化包底部依次加入1.2wt.%的稀土镁硅合金作为球化剂、0.30wt.%的钡硅铁孕育剂作为包底孕育剂以及铁;所述稀土镁硅合金中,mg含量为6wt.%~8wt.%,re含量为2wt.%~4wt.%,ca含量为2wt.%~3.5wt.%,si含量为35wt.%~44wt.%,余量为铁和不可避免的杂质;所述钡硅铁孕育剂中,si含量为63wt.%~68wt.%,ba含量为4wt.%~6wt.%,ca含量为0.5wt.%~2.5wt.%,余量为铁和不可避免的杂质。
142.(1.3)浇注:将球化处理后的铁液温度控制在1400℃~1420℃之间,进行浇注,在浇注的同时加入硅铁孕育剂作为随流孕育剂进行随流孕育,随流孕育剂占铁液的0.1wt.%~0.20wt.%;硅铁孕育剂中si含量为70wt.%~80wt.%,al含量为0.5wt.%~2.0wt.%,ca的含量为0.5wt.%~2.0wt.%,余量为铁和不可避免杂质;
143.(2)正火处理:将球墨铸铁摇臂铸件加热至850℃,保温90min,以30℃/min~70℃/min的风冷降温速度风冷至380℃;
144.(3)回火处理:将正火后的球墨铸铁摇臂铸件加热至550℃,保温90min后空冷至室温;
145.(4)机加工:对回火处理后的产品进行喷丸处理和机加工。
146.表1各实施例和对比例提供的球墨铸铁摇臂的制造方法的区别
147.[0148][0149]
表2各实施例和对比例的制造工艺以及所得产品的性能对比
[0150][0151]
‑‑
表示未经该步骤处理。
[0152]
依据q/eqy-424-2003内燃机摇臂疲劳试验方法进行疲劳试验,摇臂受力状态模拟实际服役工况,要求保证施加在摇臂长臂上的载荷与摇臂调整螺栓轴线同轴,施加在短臂上的载荷与长臂载荷夹角为15.04
°
。试验过程按升降法进行控制,保持最小压载荷1kn不变,对摇臂施加循环压载荷,并取循环载荷中的最大压载荷(循环基础为107周次)表示疲劳载荷大小。
[0153]
表3摇臂样品的疲劳测试结果以及重量
[0154]
疲劳性能中值疲劳强度摇臂本体重量实施例1所得摇臂样品42.3kn0.38kg对比例2所得摇臂样品29.6kn0.38kg对比例4所得摇臂样品33.4kn0.38kg
锻钢摇臂44.2kn0.53kg
[0155]
注1:锻钢摇臂采用40cr材料,进行调质处理,摇臂轴孔装配粉冶铜基衬套,铸铁摇臂无衬套。
[0156]
注2:摇臂安全系数满足设计要求的最低疲劳强度为34.5kn。
[0157]
以上所述仅是本发明的具体实施方式,使本领域技术人员能够理解或实现本发明。对这些实施例的多种修改对本领域的技术人员来说将是显而易见的,本文中所定义的一般原理可以在不脱离本发明的精神或范围的情况下,在其它实施例中实现。因此,本发明将不会被限制于本文所示的这些实施例,而是要符合与本文所申请的原理和新颖特点相一致的最宽的范围。