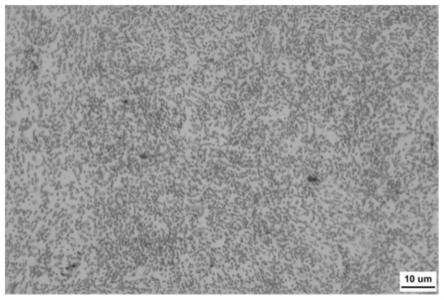
1.本发明属于金属热处理技术领域,具体涉及一种弹簧钢及其球化退火方法。
背景技术:2.弹簧钢是制造各种螺旋弹簧、板簧、扭簧等零件的原料,它广泛应用于国防、工农业及日常生活中的汽车、仪表、航空、航天、电器等领域,各种机械都离不开弹簧钢的使用。
3.弹簧钢必须具有良好的性能和质量才能满足制造弹簧的需要,比如较高的弹性极限、抗拉强度、硬度、塑性,在交变载荷下工作时能具有较高的疲劳极限和抗弹性减退能力。
4.弹簧钢一般采取轧制生产,但轧制后的材料存在组织不均匀、残余应力大、硬度高、塑性差等问题,不利于后续的加工,比如冷成型。冷成型技术用于制作高弹性极限的弹簧,对弹簧钢原始组织、碳化物球化率及硬度要求严格。采取现有的普通的球化退火工艺,球化率较低,不能满足冷成型的要求。
技术实现要素:5.针对上述问题,本技术的目的在于提供一种弹簧钢及其球化退火方法。
6.本技术提供的弹簧钢球化退火方法,具有加热速度快、球化时间短的特点,球化退火后弹簧钢的球化效果好,球化率高。
7.为实现上述目的,本技术采用以下技术方案:
8.本技术第一方面提供一种弹簧钢球化退火方法,包括以下步骤:
9.快速加热阶段:将热轧态弹簧钢装入热处理炉,并快速加热至两相区温度;
10.两相区保温阶段:所述弹簧钢在所述两相区温度进行保温;
11.第一冷却阶段:将所述弹簧钢快速降温至第一温度;
12.等温球化:将所述弹簧钢在所述第一温度进行等温球化;
13.第二冷却阶段:将所述等温球化处理后的弹簧钢随所述热处理炉缓冷至第二温度,然后出炉空冷。
14.在升温阶段,采取快速加热的方法,将弹簧钢加热至两相区。当温度达到两相区(ac1~ac3温度之间)时,珠光体中的铁素体先奥氏体化,沟槽处的碳元素由于能量密度较高,更易溶解到奥氏体基体中,在两相区保温过程中,片状碳化物逐渐断裂、溶解,留下弥散分布的未溶解粒状碳化物。此时将材料快速冷却到ar1温度以下,溶解的碳化物将以未溶解的粒状碳化物为核心进行非自发形核,形成球状碳化物组织。
15.在一些实施方案中,所述弹簧钢的成分以质量百分比计包括:c:0.56~0.64%,si:0.17~0.37%,mn:0.7~1.0%,p:≤0.025%,s:≤0.02%,cr:0.7~1.0%,ni:≤0.35%,cu≤0.25%,其余为基体fe和不可避免的杂质。
16.在一些实施方案中,所述快速加热的加热速度为120-160℃/h。采用快速加热,在提高加热效率的同时,减少表面烧损和脱碳层深度。
17.在一些实施方案中,所述两相区温度为740-760℃,所述两相区温度的保温时间为
96min~160min。
18.弹簧钢接近共析钢,两相区较窄,将温度控制在740-760℃,保温时间控制在96-160min,后续可以获得良好的球化效果;低于该温度或者保温时间时,片状碳化物溶解量过少,部分碳化物仍以片状存在,降低球化率;高于此温度或者保温时间时,碳化物溶解量过大,形核质点减少、球化率降低。
19.在一些实施方案中,所述热处理炉为连续式退火炉,所述连续式退火炉由加热区、保温区、快冷区、等温区、缓冷区五部分组成,所述加热区、所述保温区、所述快冷区、所述等温区、所述缓冷区对所述弹簧钢依次进行所述快速加热阶段、所述两相区保温阶段、所述第一冷却阶段、所述等温球化阶段、所述第二冷却阶段的处理。
20.在一些实施方案中,所述第一冷却阶段的冷却速度为20-30℃/h;
21.第一冷却阶段按此冷速冷却,可保留好未溶解的粒状碳化物,促进球化;冷速过快会增大过冷度,不利于球化;冷速过慢,则未溶解的粒状碳化物会进一步溶解,不利于球化。
22.所述第一冷却阶段在所述连续式退火炉的所述快冷区进行,冷却方式为开启风机冷却。
23.在一些实施方案中,所述第一温度为700-720℃,所述等温球化的等温时间为216min~360min。
24.等温球化的第一温度控制在此范围,球化效果最好,温度过高或者过低均会降低弹簧钢的球化率。同时需合理控制等温球化的等温时间,以免球化时间太短球化效果差,球化时间过长,造成碳化物聚集长大。
25.在一些实施方案中,所述第二温度为525-595℃。
26.第二温度过高,出炉空冷时,弹簧钢内外温差大,应力较大,易造成变形开裂,第二温度过低时,生产效果过低,影响辊速,导致连续化生产出现问题。
27.在一些实施方案中,所述缓冷为在所述缓冷区随炉冷却。
28.在一些实施方案中,所述热处理炉内采取氮气气氛保护,进炉布料高度120mm~180mm,辊道速度1.5~2.5m/h。
29.与氢气气氛相比,本技术采取氮气气氛保护,提高了生产的安全性。
30.本技术采取连续退火炉快速加热、等温球化退火,总加热时间约15h,并为连续式生产,大大缩短了退火时间,提高了退火效率;通入氮气保护后表面无明显烧损、材料无全脱碳层、总脱碳层深度可控制在0.3mm以内,减少了需要打磨的脱碳层深度。同时,本技术对等温球化后的冷却过程进行控制,避免产生较大的冷却应力,以提高冷加工性能。
31.本技术第二方面提供一种由上述弹簧钢球化退火方法制备的弹簧钢。
32.在一些实施方案中,由上述弹簧钢球化退火方法制备的弹簧钢球化率≥80%,硬度≤190hbw,晶粒度≥6级,表面无明显烧损、材料无全脱碳层、总脱碳层深度可控制在0.3mm以内。
33.与现有技术相比,本技术的有益效果是:
34.1)本技术采用连续式退火炉进行弹簧钢球化退火,通过将弹簧钢快速加热到ac1~ac3温度,得到不均匀奥氏体及大量未溶解的粒状碳化物,然后快速冷却到ar1温度以下,碳化物以未溶解质点非自发形核,离异共析形成球化碳化物,该技术具有加热速度快、球化时间短的特点。
35.2)本技术通过控制两相区的保温温度、保温时间,以及球化退火的等温温度及等温时间,所得弹簧钢球化率≥80%,硬度≤190hbw,晶粒度≥6级,表面无明显烧损、材料无全脱碳层、总脱碳层深度可控制在0.3mm以内,减少了需要打磨的脱碳层深度;本技术制备的弹簧钢满足冷成型用高弹性极限弹簧钢原料要求。
附图说明
36.图1为本技术一实施例制备的弹簧钢的球化显微组织图;
37.图2为本技术对比例1制备的弹簧钢的球化显微组织图。
具体实施方式
38.以下实施例对本技术的内容做进一步的详细说明,本技术的保护范围包含但不限于下述各实施例。实施例中未注明具体条件者,按照常规条件或制造商建议的条件进行。所用药品或仪器未注明生产厂商者,均为可以通过市购获得的常规产品。
39.本技术实施例的弹簧钢在球化退火前的状态为热轧棒材,直径范围φ20-φ80mm。热轧态的弹簧钢组织主要由片状珠光体和铁素体组成。
40.以下通过具体实施例对本发明进行详细说明,实施例中所用热轧后的弹簧钢棒材牌号为60crmn,执行标准gb/t1222-2016,各元素质量百分比如表1所示。
41.实施例1
42.该实施例中60crmn钢棒材的成分如表1所示。
43.表160crmn中各元素的质量百分比%(余量为fe和不可避免的杂质)
[0044][0045]
将热轧后的60crmn钢棒材装入连续退火炉,依次进行加热、保温、快冷、等温、缓冷、出炉,得到球化退火后的棒材,具体包括以下步骤:
[0046]
(1)布料:将热轧后的弹簧钢棒材放置在连续退火炉的传动辊道上,高度按照150mm进行布料,布料完成后按照设定好的辊速2m/h传动进入连续式退火炉中进行球化退火。
[0047]
(2)快速加热:以150℃/h的加热速度快速加热棒材至两相区温度750℃,并将弹簧钢在此温度保温120min;
[0048]
(3)快速冷却:将在两相区保温结束的弹簧钢送入连续退火炉的快速冷却区,开启风机将棒材由750℃以25℃/h的冷却速度快速冷却至710℃;
[0049]
(4)等温球化:将弹簧钢在710℃进行等温球化退火,等温时间300min;
[0050]
(5)炉内缓冷:将等温球化结束的弹簧钢在炉内缓冷至560℃。
[0051]
(6)出炉:将缓冷结束的弹簧钢棒材出炉。
[0052]
按设计的连续炉球化退火工艺生产9批60crmn,规格φ20~φ80mm,长度4-7m,球化率检测按sep-1520 1998-09执行,硬度检测按gbt231.1-2018执行,晶粒度检测按iso 643执行。
[0053]
表2为按照该实施例设计的连续炉球化退火工艺生产的60crmn的性能,由表2可知,60crmn弹簧钢碳化物球化率为85%~92%,硬度值为172hbw~181hbw,晶粒度7-8级,表面无明显烧损、材料无全脱碳层、总脱碳层深度可控制在0.3mm以内,满足要求。
[0054]
表2按照实施例1设计的连续炉球化退火工艺生产的60crmn的性能
[0055][0056][0057]
图1为采用本技术的球化退火工艺制备的60crmn弹簧钢的球化组织图,球化效果良好。
[0058]
实施例2
[0059]
本实施例中60crmn钢棒材的成分与实施例1中60crmn钢棒材的成分相同。
[0060]
本实施例提供的弹簧钢球化退火方法与实施例1中弹簧钢球化退火方法基本相同,不同之处在于,步骤(2)中快速加热的加热速度为120℃/h,具体包括以下步骤:
[0061]
(1)布料:将热轧后的弹簧钢棒材放置在连续退火炉的传动辊道上,高度按照150mm进行布料,布料完成后按照设定好的辊速2m/h传动进入连续式退火炉中进行球化退火。
[0062]
(2)快速加热:以120℃/h的加热速度快速加热棒材至两相区温度750℃,并将弹簧钢在此温度保温120min;
[0063]
(3)快速冷却:将在两相区保温结束的弹簧钢送入连续退火炉的快速冷却区,开启风机将棒材由750℃以25℃/h的冷却速度快速冷却至710℃;
[0064]
(4)等温球化:将弹簧钢在710℃进行等温球化退火,等温时间300min;
[0065]
(5)炉内缓冷:将等温球化结束的弹簧钢在炉内缓冷至560℃。
[0066]
(6)出炉:将缓冷结束的弹簧钢棒材出炉。
[0067]
按照本实施例设计的连续炉球化退火工艺生产60crmn,规格为φ20mm,对本实施例生产的60crmn的性能进行检测,结果如表3所示。
[0068]
实施例3
[0069]
本实施例中60crmn钢棒材的成分与实施例1中60crmn钢棒材的成分相同。
[0070]
本实施例提供的弹簧钢球化退火方法与实施例1中弹簧钢球化退火方法基本相同,不同之处在于,步骤(4)中等温时间为216min,具体包括以下步骤:
[0071]
(1)布料:将热轧后的弹簧钢棒材放置在连续退火炉的传动辊道上,高度按照150mm进行布料,布料完成后按照设定好的辊速2m/h传动进入连续式退火炉中进行球化退火。
[0072]
(2)快速加热:以150℃/h的加热速度快速加热棒材至两相区温度750℃,并将弹簧钢在此温度保温120min;
[0073]
(3)快速冷却:将在两相区保温结束的弹簧钢送入连续退火炉的快速冷却区,开启风机将棒材由750℃以25℃/h的冷却速度快速冷却至710℃;
[0074]
(4)等温球化:将弹簧钢在710℃进行等温球化退火,等温时间216min;
[0075]
(5)炉内缓冷:将等温球化结束的弹簧钢在炉内缓冷至560℃。
[0076]
(6)出炉:将缓冷结束的弹簧钢棒材出炉。
[0077]
按照本实施例设计的连续炉球化退火工艺生产60crmn,规格为φ60mm,对本实施例生产的60crmn的性能进行检测,结果如表3所示。
[0078]
表3按照实施例2~3设计的连续炉球化退火工艺生产的60crmn的性能
[0079][0080]
对比例1
[0081]
60crmn钢棒材的成分、退火前的状态、尺寸规格同实施例1,采用普通退火工艺。
[0082]
普通退火工艺具体步骤及工艺参数如下:
[0083]
(1)布料:将热轧后的弹簧钢棒材放置在连续退火炉的传动辊道上,高度按照150mm进行布料,布料完成后按照设定好的辊速2m/h传动进入连续式退火炉中进行球化退火。
[0084]
(2)快速加热:以150℃/h的加热速度快速加热棒材至两相区温度760℃。
[0085]
(3)保温:达到温度后,将弹簧钢在此温度保温650min。
[0086]
(4)炉内缓冷:将等温球化结束的弹簧钢在炉内缓冷至560℃。
[0087]
(5)出炉:将缓冷结束的弹簧钢棒材出炉。
[0088]
采用普通退火工艺,球化率仅50%左右,如图2所示,部分碳化物呈层片状或短棒状分布,硬度在210~230hbw,不能满足使用要求。
[0089]
对比例2
[0090]
该对比例中60crmn钢棒材的成分如表1所示,弹簧钢球化退火方法与实施例1基本相同,不同之处在于,步骤(2)中快速加热速度为60℃/h,具体包括以下步骤:
[0091]
(1)布料:将热轧后的弹簧钢棒材放置在连续退火炉的传动辊道上,高度按照150mm进行布料,布料完成后按照设定好的辊速2m/h传动进入连续式退火炉中进行球化退火。
[0092]
(2)快速加热:以60℃/h的加热速度快速加热棒材至两相区温度750℃,并将弹簧钢在此温度保温120min。
[0093]
(3)快速冷却:将在两相区保温结束的弹簧钢送入连续退火炉的快速冷却区,开启风机将棒材由750℃以25℃/h的冷却速度快速冷却至710℃。
[0094]
(4)等温球化:将弹簧钢在710℃进行等温球化退火,等温时间300min。
[0095]
(5)炉内缓冷:将等温球化结束的弹簧钢在炉内缓冷至560℃。
[0096]
(6)出炉:将缓冷结束的弹簧钢棒材出炉。
[0097]
按照该对比例设计的连续炉球化退火工艺生产60crmn,规格为φ30mm,对该对比例生产的60crmn的性能进行检测,结果如表4所示。由表4可知,脱碳层深度为0.38mm,显著地大于实施例1中规格为φ30mm的60crmn,不能满足使用要求。
[0098]
对比例3
[0099]
该对比例中60crmn钢棒材的成分如表1所示,弹簧钢球化退火方法与实施例1基本相同,不同之处在于,步骤(3)中快速冷却至680℃,具体包括以下步骤:
[0100]
(1)布料:将热轧后的弹簧钢棒材放置在连续退火炉的传动辊道上,高度按照150mm进行布料,布料完成后按照设定好的辊速2m/h传动进入连续式退火炉中进行球化退火。
[0101]
(2)快速加热:以150℃/h的加热速度快速加热棒材至两相区温度750℃,并将弹簧钢在此温度保温120min;
[0102]
(3)快速冷却:将在两相区保温结束的弹簧钢送入连续退火炉的快速冷却区,开启风机将棒材由750℃以25℃/h的冷却速度快速冷却至680℃;
[0103]
(4)等温球化:将弹簧钢在710℃进行等温球化退火,等温时间300min;
[0104]
(5)炉内缓冷:将等温球化结束的弹簧钢在炉内缓冷至560℃。
[0105]
(6)出炉:将缓冷结束的弹簧钢棒材出炉。
[0106]
按照该对比例设计的连续炉球化退火工艺生产60crmn,规格为φ30mm,对该对比例生产的60crmn的性能进行检测,结果如表4所示。由表4可知,球化率为68%和62%,显著地低于实施例1中规格为φ30mm的60crmn,硬度为195和197hbw,显著地高于实施例1中规格为φ30mm的60crmn,不能满足使用要求。
[0107]
对比例4
[0108]
该对比例中60crmn钢棒材的成分如表1所示,弹簧钢球化退火方法与实施例1基本相同,不同之处在于,步骤(3)中冷却速度为110℃/h,具体包括以下步骤:
[0109]
(1)布料:将热轧后的弹簧钢棒材放置在连续退火炉的传动辊道上,高度按照150mm进行布料,布料完成后按照设定好的辊速2m/h传动进入连续式退火炉中进行球化退火。
[0110]
(2)快速加热:以150℃/h的加热速度快速加热棒材至两相区温度750℃,并将弹簧钢在此温度保温120min。
[0111]
(3)快速冷却:将在两相区保温结束的弹簧钢送入连续退火炉的快速冷却区,开启风机将棒材由750℃以110℃/h的冷却速度快速冷却至710℃。
[0112]
(4)等温球化:将弹簧钢在710℃进行等温球化退火,等温时间300min。
[0113]
(5)炉内缓冷:将等温球化结束的弹簧钢在炉内缓冷至560℃。
[0114]
(6)出炉:将缓冷结束的弹簧钢棒材出炉。
[0115]
按照该对比例设计的连续炉球化退火工艺生产60crmn,规格为φ30mm,对该对比例生产的60crmn的性能进行检测,结果如表4所示。由表4可知,球化率为74%和72%,显著地低于实施例1中规格为φ30mm的60crmn,硬度为192和194hbw,显著地高于实施例1中规格为φ30mm的60crmn,不能满足使用要求。
[0116]
表4按照对比例2~4设计的连续炉球化退火工艺生产的60crmn的性能
[0117][0118]
以上所述仅为本发明的较佳实施例而已,并不用以限制本发明,凡在本发明的精神和原则之内所作的任何修改、等同替换和改进等,均应包含在本发明的保护范围之内。