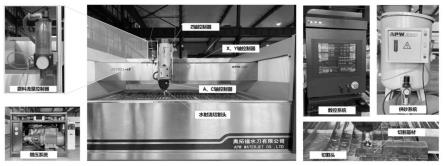
1.本发明涉及一种基于高压磨料水射流的钢轨修复工艺,属于先进制造与自动化技术领域。
背景技术:2.铁路是国民经济“大动脉”,在我国经济社会发展中的地位和作用至关重要。钢轨作为铁路的核心部件,其服役时在复杂的交变载荷和轮轨摩擦作用下产生一系列病害,严重威胁列车运行安全。随着我国经济发展对线路运能日益提升的迫切需要,钢轨修复与维护已经成为铁路运行安全性与稳定性的关键。高压磨料水射流技术具有加工柔性高、质量好、成本低、热影响小以及安全环保等优点,是当前唯一的冷态特种加工技术。因此,将高压磨料水射流技术应用于钢轨修复,有助于提升钢轨修复效率、保证加工质量,利于提升列车运行平稳性、降低噪声,还可发挥水射流装备最大性能,节省水射流装备能耗与更换新轨的开支,填补高压磨料水射流修复钢轨方面的空白,对推动我国铁路交通的进一步发展具有重要意义。
技术实现要素:3.本发明针对高压磨料水射流对钢轨材料切割过程效率低、切割质量不稳定等问题,通过单因素实验探究主要工艺参数对实验结果影响规律;基于田口法进行正交试验,考虑切割深度与切割质量对实验结果进行信噪比分析,获得高压磨料水射流切割钢轨材料过程最优工艺参数组合;基于以上进行钢轨轨顶面修复实验,验证面向钢轨修复的高压磨料水射流最优工艺参数组合的有效性以及高压磨料水射流修复钢轨工艺的可行性;构建高压磨料水射流切割钢轨材料切割深度与表面粗糙度预测模型并验证其有效性及实用性。
4.本发明的一种基于高压磨料水射流的钢轨修复工艺包括如下步骤:
5.s1:搭建高压磨料水射流切割钢轨材料实验台;
6.s2:以60n钢轨为例,应用线切割设备在60n钢轨顶面10mm处进行缓慢走丝切割,将钢轨制备成400mm*70mm*22mm的长方体块,并用黄油包裹储存防止其表面氧化;
7.s3:确定影响水射流最大切割深度以及切割质量的主要工艺参数为射流压力、靶距、进给速度、磨料流量;
8.s4:确定工艺参数取值范围;
9.s5:探究高压磨料水射流射流压力对最大切割深度的影响规律,射流压力分别取240mpa,260mpa,280mpa,300mpa,320mpa,340mpa;靶距取4mm;喷嘴横移速度取135mm/min;磨料流量取381.7g/min进行实验;
10.s6:探究高压磨料水射流靶距对最大切割深度的影响规律,射流压力取330mpa;靶距分别取2mm,3mm,4mm,5mm,6mm,7mm;喷嘴横移速度取135mm/min;磨料流量取381.7g/min进行实验;
11.s7:探究高压磨料水射流喷嘴横移速度对最大切割深度的影响规律,射流压力取
330mpa;靶距选取4mm;喷嘴横移速度分别取120mm/min,130mm/min,140mm/min,150mm/min,160mm/min,170mm/min;磨料流量取381.7g/min进行实验;
12.s8:探究高压磨料水射流磨料流量对最大切割深度的影响规律,射流压力取330mpa;靶距取4mm;喷嘴横移速度取135mm/min;磨料流量分别取242.9g/min,277.6g/min,312.3g/min,347g/min,381.7g/min,416.4g/min进行实验;
13.s9:探究高压磨料水射流射流压力对切割侧壁表面粗糙度的影响规律,射流压力分别取240mpa,260mpa,280mpa,300mpa,320mpa,340mpa;靶距取4mm;喷嘴横移速度取135mm/min;磨料流量取381.7g/min进行实验;
14.s10:探究高压磨料水射流靶距对切割侧壁表面粗糙度的影响规律,射流压力取330mpa;靶距分别取2mm,3mm,4mm,5mm,6mm,7mm;喷嘴横移速度取135mm/min;磨料流量取381.7g/min进行实验;
15.s11:探究高压磨料水射流横移速度对切割侧壁表面粗糙度的影响规律,射流压力取330mpa;靶距选取4mm;喷嘴横移速度分别取120mm/min,130mm/min,140mm/min,150mm/min,160mm/min,170mm/min;磨料流量取381.7g/min进行实验;
16.s12:探究高压磨料水射流磨料流量对切割侧壁表面粗糙度的影响规律,射流压力取330mpa;靶距取4mm;喷嘴横移速度取135mm/min;磨料流量分别取242.9g/min,277.6g/min,312.3g/min,347g/min,381.7g/min,416.4g/min进行实验;
17.s13:设计正交实验探究高压磨料水射流主要工艺参数(射流压力、靶距、进给速度、磨料流量)的最优组合;
18.s14:选用最优工艺参数组合进行基于高压磨料水射流的钢轨表面修复实验,为了方便观测实验结果选取水射流喷嘴进给距离为80mm;
19.s15:分析修复后钢轨表面的宏/围观形貌;
20.本发明的有益效果是:本发明为钢轨修复工艺提供新方法,有效解决了打磨与铣磨为主的传统修复方式带来的烧伤、切削力大引发的钢轨烧伤、刀具磨损等问题,明晰高压磨料水射流切割钢轨材料过程中工艺参数与材料去除效率和修复质量之间的映射关系,揭示材料去除机制;优化高压水射流切割钢轨材料过程工艺参数,提高水射流切割钢轨材料的效率与质量;验证基于高压磨料水射流的钢轨修复工艺可行性,旨在实现基于高压磨料水射流的钢轨仿形包络切割修复。
附图说明
21.图1为本发明高压磨料水射流切割钢轨材料实验台。
22.图2为本发明射流压力对最大切割深度影响曲线。
23.图3为本发明靶距对最大切割深度影响曲线。
24.图4为本发明横移速度对最大切割深度影响曲线。
25.图5为本发明磨料流量对最大切割深度影响曲线。
26.图6为本发明射流压力对表面粗糙度影响曲线。
27.图7为本发明靶距对表面粗糙度影响曲线。
28.图8为本发明横移速度对表面粗糙度影响曲线。
29.图9为本发明磨料流量对表面粗糙度影响曲线。
30.图10(1)-10(4)为本发明切割深度信噪比响应曲线,其中图10(1)为射流压力对切割深度信噪比响应曲线,图10(2)为靶距对切割深度信噪比响应曲线,图10(3)为横移速度对切割深度信噪比响应曲线,图10(4)为磨料流量对切割深度信噪比响应曲线。
31.图11(1)-11(4)为本发明粗糙度信噪比响应曲线,其中图11(1)为射流压力对粗糙度信噪比响应曲线,图11(2)为靶距对粗糙度信噪比响应曲线,图11(3)为进给速度对粗糙度信噪比响应曲线,图11(4)为磨料流量对粗糙度信噪比响应曲线。
32.图12(1)和12(2)为本发明磨料水射流钢轨修复过程,其中图12(1)为a修复中,图12(2)为b修复后。
33.图13(1)和13(2)为本发明修复效果,其中图13(1)为a修复前,图13(2)为b修复后。
34.图14为本发明磨料水射流修复深度示意图。
35.图15(1)和15(2)为本发明钢轨修复后表面微观形貌,其中图15(1)为a粗糙切削区,图15(2)为b平滑切削区。
36.图16(1)和16(2)为本发明钢轨修复后表面微观3d形貌,其中图16(1)为a粗糙切削区,图16(2)为b平滑切削区。
具体实施方式
37.下面结合附图及实施例,对本发明进行进一步详细说明,但应当理解实施例用以解释本发明,并不用于限制本发明。
38.本发明开发一种基于高压磨料水射流的钢轨修复工艺。图1为本发明高压磨料水射流切割钢轨材料实验台。图2为本发明射流压力对最大切割深度影响曲线。图3为本发明靶距对最大切割深度影响曲线。图4为本发明横移速度对最大切割深度影响曲线。图5为本发明磨料流量对最大切割深度影响曲线。图6为本发明射流压力对表面粗糙度影响曲线。图7为本发明靶距对表面粗糙度影响曲线。图8为本发明横移速度对表面粗糙度影响曲线。图9为本发明磨料流量对表面粗糙度影响曲线。图10(1)-10(4)为本发明切割深度信噪比响应曲线,其中图10(1)为射流压力对切割深度信噪比响应曲线,图10(2)为靶距对切割深度信噪比响应曲线,图10(3)为横移速度对切割深度信噪比响应曲线,图10(4)为磨料流量对切割深度信噪比响应曲线。图11(1)-11(4)为本发明粗糙度信噪比响应曲线,其中图11(1)为射流压力对粗糙度信噪比响应曲线,图11(2)为靶距对粗糙度信噪比响应曲线,图11(3)为进给速度对粗糙度信噪比响应曲线,图11(4)为磨料流量对粗糙度信噪比响应曲线。图12(1)和12(2)为本发明磨料水射流钢轨修复过程,其中图12(1)为a修复中,图12(2)为b修复后。图13(1)和13(2)为本发明修复效果,其中图13(1)为a修复前,图13(2)为b修复后。图14为本发明磨料水射流修复深度示意图。图15(1)和15(2)为本发明钢轨修复后表面微观形貌,其中图15(1)为a粗糙切削区,图15(2)为b平滑切削区。图16(1)和16(2)为本发明钢轨修复后表面微观3d形貌,其中图16(1)为a粗糙切削区,图16(2)为b平滑切削区。
39.本发明的整体技术方案为一种基于高压磨料水射流的钢轨修复工艺,包括如下步骤:
40.s1:搭建如图1所示的高压磨料水射流切割钢轨材料实验台;
41.s2:以60n钢轨为例,应用线切割设备在60n钢轨顶面10mm处进行缓慢走丝切割,将钢轨制备成400mm*70mm*22mm的长方体块,并用黄油包裹储存防止其表面氧化;
42.s3:确定影响水射流最大切割深度以及切割质量的主要工艺参数为射流压力、靶距、进给速度、磨料流量;
43.s4:确定工艺参数取值范围;
44.s5:探究高压磨料水射流射流压力对最大切割深度的影响规律,射流压力分别取240mpa,260mpa,280mpa,300mpa,320mpa,340mpa;靶距取4mm;喷嘴横移速度取135mm/min;磨料流量取381.7g/min进行实验,结果如图2所示。
45.射流压力在240mpa~320mpa时,被加工工件的最大切割深度随射流压力的增加而变大,且在240mpa~300mpa时,被加工工件的最大切割深度与射流压力之间的关系近似呈线性关系。射流压力为240mpa时,被加工工件最大切割深度值最小,射流压力为320mpa时,被加工工件最大切割深度值最大。射流压力在320mpa~340mpa时,被加工工件的最大切割深度随射流压力的增加而减小;
46.s6:探究高压磨料水射流靶距对最大切割深度的影响规律,射流压力取330mpa;靶距分别取2mm,3mm,4mm,5mm,6mm,7mm;喷嘴横移速度取135mm/min;磨料流量取381.7g/min进行实验,结果如图3所示。
47.靶距在2mm~3mm时,被加工工件的最大切割深度随靶距的增大而增大。靶距为3mm时,被加工工件的最大切割深度值达到最大,最大切割深度值为19.22mm。靶距在3mm~7mm时,被加工工件的最大切割深度随靶距的增大而减小,随着靶距的不断增大,被加工工件的最大切割深度减小的速度也逐渐增大;
48.s7:探究高压磨料水射流喷嘴横移速度对最大切割深度的影响规律,射流压力取330mpa;靶距选取4mm;喷嘴横移速度分别取120mm/min,130mm/min,140mm/min,150mm/min,160mm/min,170mm/min;磨料流量取381.7g/min进行实验,结果如图4所示。
49.磨料水射流喷嘴横移速度在120mm/min~170mm/min范围内,被加工工件的最大切割深度随横移速度的增加而增大。横移速度为170mm/min时,被加工工件的最大切割深度值最小,最小切割深度值为16.6mm,横移速度为120mm/min时,被加工工件的最大切割深度值最大,最大切割深度值为21mm。在120mm/min~150mm/min时最大切割深度与横移速度之间近似呈线性关系,在150mm/min~170mm/min时最大切割深度随横移速度减小速度逐渐下降;
50.s8:探究高压磨料水射流磨料流量对最大切割深度的影响规律,射流压力取330mpa;靶距取4mm;喷嘴横移速度取135mm/min;磨料流量分别取242.9g/min,277.6g/min,312.3g/min,347g/min,381.7g/min,416.4g/min进行实验,实验结果如图5所示。
51.磨料流量在242.9g/min~416.4g/min范围内,被加工工件的最大切割深度随磨料流量的增加而增大。磨料流量为242.9g/min时,被加工工件的最大切割深度值最小,最大切割深度值为16.06mm,磨料流量为416.4g/min时,被加工工件的最大切割深度值达到最大,最大切割深度值为19.62mm。在312.3g/min~416.4g/min范围内,最大切割深度值随磨料流量增加的趋势较312.3g/min之前减缓;
52.s9:探究高压磨料水射流射流压力对切割侧壁表面粗糙度的影响规律,射流压力分别取240mpa,260mpa,280mpa,300mpa,320mpa,340mpa;靶距取4mm;喷嘴横移速度取135mm/min;磨料流量取381.7g/min进行实验,实验结果如图6所示。
53.射流压力在240mpa~340mpa范围时,随着射流压力的增大,钢轨材料切割侧壁表
面粗糙度相应的减小。射流压力为240mpa时,钢轨材料切割侧壁表面粗糙度最大,粗糙度值为5.453μm,射流压力为340mpa时,钢轨材料切割侧壁表面粗糙度最小,粗糙度值为3.948μm;
54.s10:探究高压磨料水射流靶距对切割侧壁表面粗糙度的影响规律,射流压力取330mpa;靶距分别取2mm,3mm,4mm,5mm,6mm,7mm;喷嘴横移速度取135mm/min;磨料流量取381.7g/min进行实验,实验结果如图7所示。
55.靶距在2mm~7mm范围时,随着靶距的增大,钢轨材料切割侧壁表面粗糙度相应的变大。靶距为2mm时,钢轨材料切割侧壁表面粗糙度最小,粗糙度值为3.876μm,靶距为7mm时,钢轨材料切割侧壁表面粗糙度最大,粗糙度值为6.148μm。靶距在5mm~7mm时钢轨材料切割侧壁表面粗糙度随着靶距的增加粗糙度值增加得更快;
56.s11:探究高压磨料水射流横移速度对切割侧壁表面粗糙度的影响规律,射流压力取330mpa;靶距选取4mm;喷嘴横移速度分别取120mm/min,130mm/min,140mm/min,150mm/min,160mm/min,170mm/min;磨料流量取381.7g/min进行实验,实验结果如图8所示。
57.横移速度在120mm/min~170mm/min时,随着横移速度的增大,钢轨材料切割侧壁表面粗糙度相应的变大。横移速度在120mm/min时,钢轨材料切割侧壁表面粗糙度最小,粗糙度值为3.691μm,横移速度在170mm/min时,钢轨材料切割侧壁表面粗糙度最大,粗糙度值为6.17μm。横移速度在160mm/min~170mm/min时钢轨材料切割侧壁表面粗糙度变大趋势较140mm/min~160mm/min时更慢;
58.s12:探究高压磨料水射流磨料流量对切割侧壁表面粗糙度的影响规律,射流压力取330mpa;靶距取4mm;喷嘴横移速度取135mm/min;磨料流量分别取242.9g/min,277.6g/min,312.3g/min,347g/min,381.7g/min,416.4g/min进行实验,实验结果如图9所示。
59.随着磨料流量的增大,磨料流量在242.9g/min~416.4g/min时,钢轨材料切割侧壁表面粗糙度相应的变小。磨料流量在416.4g/min时,钢轨材料切割侧壁表面粗糙度最小,粗糙度值为3.353μm,磨料流量在242.9g/min时,钢轨材料切割侧壁表面粗糙度最大,粗糙度值为6.583μm;
60.s13:涉及如表1所示的正交实验,其结果如表2所示。
61.表1正交实验参数
[0062][0063]
表2正交实验及其结果
[0064][0065]
对实验结果进行信噪比分析,其中望小特性、望大特性以及望目特性信噪比函数分别为:
[0066][0067][0068][0069]
其中:iy为样本数据;y为样本数据的平均值;2ys为样本数据的方差;n为测量次数。分析信噪比函数以及实验目标可知,基于高压磨料水射流的钢轨材料修复过程的实验结果分析中,最大切割深度应为望大特性,切割侧壁表面粗糙度应为望小特性,因此对基于高压磨料水射流的钢轨材料修复过程最大切割深度目标以及切割侧壁表面粗糙度目标分别采用望大特性和望小特性进行分析,分析结果见表3以及表4:
[0070]
表3切割深度信噪比分析表
[0071][0072]
表4粗糙度信噪比分析表
[0073][0074]
为了得到各参数组合的信噪比均值,对各参数组合的极差进行排秩。不同工艺参数各个水平下的切割深度信噪比均值与粗糙度信噪比均值分别见表5以及表6,信噪比响应图见图10(1)-10(4)以及图11(1)-11(4)。
[0075]
表5切割深度信噪比均值表
[0076][0077]
表6粗糙度信噪比均值表
[0078][0079]
表3表明高压磨料水射流对钢轨材料切割过程中,影响切割效率的四个工艺参数,极差由大到小依次为射流压力》磨料流量》喷嘴横移速度》靶距,射流压力对最大切割深度影响最大,其次是磨料流量,靶距对最大切割深度影响最小。表4表明高压磨料水射流对钢轨材料切割过程中,影响粗糙度的四个工艺参数,极差由大到小依次为喷嘴横移速度》磨料流量》靶距》射流压力,喷嘴横移速度对粗糙度影响最大,其次是磨料流量,射流压力对粗糙度影响最小。
[0080]
由切割深度信噪比响应曲线可以看出,当射流压力为360mpa时,切割深度的平均信噪比达到最大。当靶距为3mm时,切割深度的平均信噪比达到最大。当进给速度为120mm/min时,切割深度的平均信噪比达到最大。当磨料流量为416.4g/min时,切割深度的平均信噪比达到最大。由粗糙度信噪比响应曲线可以看出,当射流压力为360mpa时,粗糙度的平均信噪比达到最大。当靶距为3mm时,粗糙度的平均信噪比达到最大。当进给速度为120mm/min时,粗糙度的平均信噪比达到最大。当磨料流量为416.4g/min时,粗糙度的平均信噪比达到最大。因此,面向效率与质量的高压磨料水射流对钢轨材料切割最优工艺参数组合为:射流压力360mpa;靶距3mm;进给速度120mm/min;磨料流量416.4g/min;
[0081]
s14:选用最优工艺参数组合进行基于高压磨料水射流的钢轨表面修复实验,为了方便观测实验结果选取水射流喷嘴进给距离为80mm,图12(1)和12(2)分别展示了钢轨水射流修复中和修复后的状态;
[0082]
s15:分析修复后钢轨表面的宏/微观形貌。图13(1)和13(2)分别展示了修复后钢轨表面的形貌特征。钢轨修复表面上半部加工质量较好,无裂纹,其表面粗糙度为2.648μm,满足钢轨修复后表面粗糙度小于6μm的要求。
[0083]
由图14可看出高压磨料水射流修复钢轨轨顶面单次加工余量为1.5mm,高于钢轨铣磨车单次走刀加工余量,远超钢轨打磨车单次加工余量,以上均满足《高速铁路钢轨打磨管理办法》钢轨修复要求。
[0084]
图15(1)和15(2)所示的微观形貌表明,修复后的钢轨表面无较为明显裂纹,无烧伤情况,下部粗糙切削区微观损伤与上部平滑切削区微观损伤都表现出较长犁削沟痕伴随着较短的冲蚀变形坑。图15(1)表明下部粗糙切削区微观形貌表现出了明显的划痕损伤。图16(1)和16(2)所示的微观3d形貌图表明粗糙切削区沿射流横移方向条纹高度存在明显变化,即对应着图15(1)中的划痕损伤,由图16(2)可以看出,钢轨修复后平滑切削区微观3d形貌较好,表面沿射流横移方向条纹高度变化呈一定规律。
[0085]
经以上实验验证,高压磨料水射流修复钢轨是完全可行的。同时基于上述分析,再次验证了所得到高压磨料水射流切割钢轨材料最优工艺参数组合即:射流压力360mpa、喷嘴与被修复钢轨表面距离3mm、喷嘴进给速度120mm/min、磨料流量416.4g/min,可获得较高的切割深度与切割质量,其修复质量可满足钢轨修复需求。
[0086]
以上所述为本发明的优选实施例,并不用于限制本发明,本发明所属领域的技术人员依然可以对上述技术方案进行修改,或者对其中部分技术特征进行等同替换。凡在本发明的精神和原则之内,所作的任何修改、等同替换、改进等,均应包括在本发明的保护范围之内。