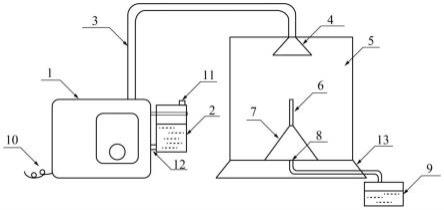
1.本发明涉及水玻璃型壳硬化技术领域。具体地说是一种水玻璃型壳硬化液滴反应装置及水玻璃型壳硬化工艺。
背景技术:2.由于水玻璃成本低廉、无毒等优点,在熔模铸造型壳生产中常被作为粘结剂而广泛应用。目前,水玻璃型壳的硬化采用浸入法,即将蜡模涂覆涂层后,浸入硬化剂溶液中一定时间,涂层中的粘结剂与硬化剂溶液发生化学反应而获得强度。由于单一涂层型壳强度低,故工业生产中采用多层涂层及耐火粉料构成具有一定厚度的型壳。而每一壳层必需浸入硬化剂溶液中硬化后才能获得相应的强度,达到其力学及工艺性能要求。然而,当同一型壳或多批次型壳多次浸入硬化剂溶液中时,制壳材料吸收大量溶剂水会造成硬化剂溶液浓度发生变化;部分制壳材料(比如粘结剂、耐火粉料等)的脱落会污染硬化剂溶液;这些都会造成硬化剂溶液的物理化学性质随使用频次发生明显改变,从而使得硬化得到的水玻璃型壳的性能和质量难以控制。此外,硬化溶液使用一定周期后,废液无法回用,排放量大,极易造成环境污染。
3.水玻璃型壳的常温强度增大,其焙烧强度、残留强度均有不同程度增大,但三者的增长幅度(速率)不同(这与高温条件下的相转变密切相关)。但只要常温强度、焙烧强度的增长速率超过残留强度的增长速率,在常温强度数值、焙烧强度数值要求一定的情况下,就可相对地降低残留强度。如某中型结构铸件生产中,要求型壳常温强度不小于10.0mpa、焙烧强度不小于7.0mpa、且残留强度不大于3.0mpa,则采用传统制壳工艺(浸入法硬化),通常常温强度和焙烧强度容易达到要求,但残留强度往往超标,如果采用减小厚度的办法降低残留强度则会导致常温强度和焙烧强度不符合要求,因此传统制壳工艺(浸入法硬化)很难同时兼顾“常温强度和焙烧强度”与残留强度同时符合要求。为了使得常温强度、焙烧强度满足要求,采用传统制壳工艺制备的型壳通常具有较大的厚度,型壳厚度大不仅增加固体废弃物的排放,而且散热性较差,不利于金属铸件的快速凝固,导致铸件晶粒组织不理想,从而不利于铸件性能的提高。此外,在实际铸造生产中,一些南方企业冬季无暖气的生产车间的气温一般在-5~10℃,此温度条件下,采用浸入法制备型壳时,如果硬化剂的浓度较低,则型壳硬化反应缓慢甚至无法硬化,因此需要用高浓度硬化剂溶液进行生产,但采用高浓度硬化剂溶液生产的型壳在浸入法硬化时硬化反应快导致严重开裂,制备的型壳通常焙烧强度极低,无法满足应用要求,导致废品率高。
技术实现要素:4.为此,本发明所要解决的技术问题在于提供一种低温环境适应性好的水玻璃型壳硬化液滴反应装置及水玻璃型壳硬化工艺,以解决浸入法硬化水玻璃型壳时高浓度硬化剂溶液生产型壳废品率高的问题,并解决在制壳过程中硬化剂溶液的有效浓度随使用次数的增加发生变化、硬化剂溶液易被制壳材料污染导致的水玻璃型壳的强度低、性能和质量难
以控制,以及硬化剂溶液利用率低、排放量大、造成环境污染严重的问题;同时本发明这种工艺能够有效提高水玻璃型壳的常温强度和焙烧强度,减小残留强度,使得型壳在较薄的厚度下即可满足“常温强度和焙烧强度”较高而“残留强度”较低的要求,实现型壳的“增强减薄”。
5.为解决上述技术问题,本发明提供如下技术方案:
6.一种水玻璃型壳硬化液滴反应装置,包括雾化器、储液罐、反应室和残液收集槽;所述储液罐的硬化剂溶液出口端通过供液管与所述雾化器的硬化剂溶液入口端流体导通,所述雾化器的硬化剂溶液雾化液滴出口端通过液滴输送管与所述反应室的硬化剂溶液雾化液滴入口端流体导通;所述反应室的硬化剂溶液残液出口端与所述残液收集槽的硬化剂溶液残液入口端流体导通;所述储液罐可以通过直接或间接形式与雾化器相连通。
7.上述水玻璃型壳硬化液滴反应装置,所述反应室内设置有液滴分布器和试样支架;所述试样支架固定安装在所述反应室内,蜡模试样安置在所述试样支架上;所述液滴分布器的硬化剂溶液雾化液滴入口端与所述液滴输送管的硬化剂溶液雾化液滴出口端流体导通,所述液滴分布器的硬化剂溶液雾化液滴出口端朝向所述蜡模试样;所述反应室的底壁上开设有残液排出孔,所述反应室通过所述残液排出孔与所述残液收集槽流体导通;本发明中的反应室为正方体、圆柱体或长方体,以及由正方体、圆柱体和长方体组合成的其它形状的反应室。
8.上述水玻璃型壳硬化液滴反应装置,所述液滴分布器呈喇叭口型,即所述液滴分布器的内径自其硬化剂溶液雾化液滴入口端至硬化剂溶液雾化液滴出口端逐渐增大。
9.上述水玻璃型壳硬化液滴反应装置,所述储液罐上开设有加液孔,所述雾化器通过供电电缆与电源电连接;所述硬化剂溶液经所述雾化器雾化后形成的雾滴的粒径为0.5~500μm,雾滴粒径越大,单位时间内与型壳表面的水玻璃涂料的接触面积增大,使得水玻璃膜的硬化速率加快,但当雾化粒径过大时,硬化速率过快,容易出现因水玻璃膜脱水收缩速率快而导致开裂,形成大尺寸裂纹,从而降低型壳强度,雾滴越小,硬化强度越高,但型壳硬化速率慢,需要硬化时间延长,导致生产率低;所述雾化器的硬化剂溶液雾化液滴出口端的雾化液滴流量为0.2~2.0l/min,所述雾化器的载气压力为0.2~1.5mpa;所述雾化器为利用高频、液力或射流原理驱动液体实现硬化剂溶液雾化的各类装置,比如雾化器为超声波雾化器、液体雾化器、喷淋器或文丘里射流器,也可以是可以实现雾化功能的其它形式的雾化器;液体雾化器可以使单液头雾化器,也可以是双液头雾化器,文丘里射流器是指利用文丘里原理制备的各种射流器。
10.上述水玻璃型壳硬化液滴反应装置,还包括反应室支架;所述反应室固定安装在所述反应室支架上。
11.一种水玻璃型壳硬化工艺,采用上述水玻璃型壳硬化液滴反应装置进行水玻璃型壳硬化,具体包括如下步骤:
12.步骤a:将硬化剂溶液灌装至所述储液罐中;采用水玻璃涂料对蜡模进行涂料涂挂并进行撒砂处理,撒砂处理完成后得到蜡模试样;将所述蜡模试样直接放置或悬挂于所述反应室中;硬化剂溶液可以是不饱和溶液、饱和溶液或过饱和溶液;本发明中,涂料涂挂和撒砂处理包括对面层、过渡层、加强层、背层及封浆层等各壳层构筑时使用的任意种类的涂料及耐火骨料;涂料涂挂形式为刷涂、浸涂、喷涂等方法施涂与蜡模或蜡模组表面;撒砂形
式为沸腾砂床、雨淋式撒砂机中撒砂或手工撒砂等;
13.步骤b:启动所述雾化器,所述雾化器通过所述供液管将所述储液罐中的所述硬化剂溶液泵入所述雾化器中进行雾化;
14.步骤c:所述硬化剂溶液经所述雾化器转化为硬化剂溶液雾化液滴,所述硬化剂溶液雾化液滴通过所述液滴输送管输送至所述反应室中,并与所述反应室内安置的所述蜡模试样表面的水玻璃涂层进行硬化反应,使所述蜡模试样表面的水玻璃涂层硬化为水玻璃型壳;反应后残留的硬化剂溶液雾化液滴沉积汇集至所述反应室底部,并流入所述残液收集槽中;硬化反应的时间可以根据水玻璃型壳的形状、尺寸、结构及层厚选择;硬化时间可通过雾化液滴发生器的启闭来控制;水玻璃型壳的硬化速率可通过雾化液滴流量(功率调节)及载气气体压力控制(压力阀调节)实现,载气气体可为空气或co2等气体;雾化液滴流量增大时,单位时间内,型壳表面雾化液滴沉积量多,型壳表面雾化液滴覆盖面积增大,硬化反应速率加快;载气压力增大时,雾化液滴沉积速率快,型壳表面雾化液滴沉积量多;高速运动的雾化液滴冲击型壳表面易于铺展,雾化液滴与型壳接触面积增大,硬化反应速率加快;但过快的反应速率会导致本发明雾化液滴硬化后生成的水玻璃型壳的性能逐渐接近传统浸入法硬化,优势减弱甚至消失;雾化液滴流量小及载气气体压力低时,有利于获得高的型壳性能,但型壳生产率较低。因此,适宜的雾化液滴流量为0.2~2.0l/min,载气压力范围为0.2~1.5mpa。
15.步骤d:取出具有水玻璃型壳的所述蜡模试样,重复步骤a至步骤c,在所述蜡模试样上完成所有型壳壳层的硬化得到具有水玻璃型壳壳层的蜡模,切断电源,从所述反应室中取出所述具有水玻璃型壳壳层的蜡模;可视情况重复步骤a至c,在蜡模或模组表面构筑多层相同或不同涂料、耐火骨料壳层组成的水玻璃型壳;
16.步骤e:将所述具有水玻璃型壳壳层的蜡模进行干燥,并采用热水浴法进行型壳脱蜡,脱蜡完成后得到水玻璃型壳;将水玻璃型壳置于电阻炉中焙烧并随炉冷却至室温,得到焙烧型水玻璃型壳。采用本发明的水玻璃型壳硬化液滴反应装置及工艺制得的型壳可以为单层/多层型壳或不同粘结剂形成的复合型壳。
17.上述水玻璃型壳硬化工艺,所述硬化剂溶液为一种或两种及两种以上的金属和/或非金属的盐溶液,或者所述硬化剂溶液为一种或两种及两种以上的有机酸和/或无机酸的溶液;所述硬化剂溶液经所述雾化器雾化后形成的雾滴的粒径为0.5~500μm,所述雾化器的硬化剂溶液雾化液滴出口端的雾化液滴流量为0.2~2.0l/min,所述雾化器的载气压力为0.2~1.5mpa。
18.上述水玻璃型壳硬化工艺,步骤c中,硬化反应的时间为6~18min;
19.步骤a中:所述硬化剂溶液为浓度为5~25wt%的氯化铵溶液;所述水玻璃涂料的配制方法为:将耐火料粉和水玻璃按照质量之比为1.2:1混合,然后加入润湿剂和消泡剂进行搅拌1h后再进行8h的静置处理,确保粘结剂与耐火粉料充分湿润;所述水玻璃涂料在使用前先搅拌20min然后静置5min后再使用;涂料涂挂及撒砂的方法为:将蜡模或蜡模组浸入所述水玻璃涂料中,静置30~50s;然后将涂挂水玻璃涂料的蜡模或蜡模组取出,并放入沸腾砂床或雨淋式撒砂机中进行撒砂处理,撒砂处理结束后,自然干燥50~60min,即得到所述蜡模试样;
20.步骤d中:再次配制所述水玻璃涂料:将耐火料粉和水玻璃按照质量之比为1.1:1
混合,然后连续搅拌至少4.0h后储存待用;所述水玻璃涂料在使用前先搅拌20min然后静置5min后再使用;涂料涂挂及撒砂的方法为:将已经构筑一层水玻璃型壳壳层的蜡模或蜡模组浸入所述水玻璃涂料中,静置30~50s;然后将涂挂水玻璃涂料的已经构筑一层水玻璃型壳壳层蜡模或蜡模组取出,并放入沸腾砂床和雨淋式撒砂机中进行撒砂处理,撒砂处理结束后,自然干燥40~50min,即得到所述蜡模试样,然后重复步骤b-c的操作方法使所述蜡模试样表面形成第二层水玻璃型壳;然后按照第二层水玻璃型壳的构筑方法在蜡模或蜡模组表面构筑第三层水玻璃型壳。
21.上述水玻璃型壳硬化工艺,步骤c中,硬化反应的时间为9min;所述硬化剂溶液为浓度为5wt%的氯化铵溶液;步骤a中,所述耐火料粉为270目的石英粉,撒砂处理时所用的砂石为50目和/或70目石英砂;步骤d中,所述耐火料粉由270目的石英粉和200目的莫来石粉按照质量之比7:3混合而成,撒砂处理时所用的砂石为20目和/或40目石英砂。
22.上述水玻璃型壳硬化工艺,步骤e中,干燥温度为5~30℃,干燥时间为12~24h;热水浴的温度为90~98℃,热水浴时间为10~15min;焙烧时,先以5℃/min的速率升温到750℃,然后保温2.0h,最后随炉冷却至室温。
23.本发明的技术方案取得了如下有益的技术效果:
24.1、本发明中的水玻璃型壳硬化液滴反应装置,采用雾化器将硬化剂溶液雾化,硬化剂溶液雾化后的液滴在空气流推动下输送、沉积至水玻璃型壳涂料的表面,同时逐步渗入水玻璃型壳涂层中,与水玻璃型壳涂层中的水玻璃发生化学反应而使型壳建立强度;由于在水玻璃型壳硬化过程中,硬化剂溶液始终保存在储液罐中不与水玻璃型壳接触,因此其浓度不会发生变化,且其物理化学性质稳定,使得在相同工艺参数下硬化得到的水玻璃型壳硬化特性具有较高的一致性。采用本发明的水玻璃型壳硬化液滴反应装置可以将硬化剂液滴输送到水玻璃型壳的面层、过渡层和封浆层等任何一个壳层,型壳硬化速率可通过液滴浓度及输送量(雾化时间)来控制;相比浸入法,采用该装置及工艺制备的水玻璃型壳强度得到了明显的提高,且同一工艺参数下制备的不同批次的水玻璃型壳性能稳定,硬化剂溶液消耗量也显著减少。
25.2、本发明中水玻璃型壳硬化工艺,能有效避免现有浸入法硬化水玻璃型壳工艺中存在的硬化剂溶液消耗量大、易污染、物理化学性质随使用频次变化、型壳硬化特性波动大、硬化剂废液排放大等问题,实现了硬化剂残液的近零排放;同时由于硬化剂性质稳定、硬化速率可控,能够提高水玻璃型壳的常温强度和焙烧强度,降低其残留强度等。同时,该工艺能够提高硬化剂溶液的利用率,减少废液的排放,有利于保护环境。采用本发明水玻璃型壳硬化液滴反应装置及方法硬化的水玻璃型壳,与传统浸入法相比,在一定硬化工艺条件下(硬化剂溶液浓度为5%~25%,硬化时间为6~18min),制备的水玻璃型壳常温强度峰值可提高47.01%,焙烧强度的峰值可提高42.58%;而残留强度峰值则可降低8.42%;此外,由于半封闭的液滴硬化工艺常温强度远高于浸入法制备的型壳,因此,在型壳强度满足要求的条件下,可适当减小型壳厚度,这将有利于进一步降低型壳的残留强度。本发明中获得型壳常温强度峰值为21.42mpa,其对应的焙烧强度及残留强度分别为8.22mpa和6.31mpa;残留强度与常温强度及焙烧强度之比率分别为29.46%和76.76%;而采用浸入法硬化的型壳常温强度峰值仅为14.57mpa,与其对应的焙烧强度及残留强度分别为6.52mpa和5.20mpa;残留强度与常温强度及焙烧强度之比率分别为35.69%和79.75%;说明采用本
发明制备的型壳其残留强度的增长速率低于常温强度、焙烧强度的增长速率,即较薄的壳层厚度条件下就能获得与浸入法相当的常温强度及焙烧强度,而型壳厚度减薄后其残留强度相应降低,有利于铸件凝固后脱壳。此外,型壳硬化过程中,液气两相流中硬化剂液滴含量低,其输送量可准确控制,硬化反应后残余废液少,利用率提高至96%以上。
26.3、本发明通过一种简单易行的水玻璃型壳硬化液滴反应器装置与方法制备熔模铸造用水玻璃型壳,每一壳层的在恒定浓度的硬化剂液滴作用下发生硬化,硬化剂不被污染,消耗量少,硬化反应过程易于控制,通过调控极少的工艺参数实现了水玻璃型壳性能的可控性;本发明的工艺可以在硬化剂溶液浓度较高的条件下制备得到具有较高常温强度和焙烧强度的型壳,能够在生产温度较低的生产环境中生产满足应用要求的型壳,降低低温生产环境中型壳的废品率。
27.4、采用本发明工艺制备的水玻璃型壳相对于传统浸入法制备的水玻璃型壳具有较高的常温强度和焙烧强度,以及相对较低的残留强度占比;这就使得在常温强度和焙烧强度要求一定时,可以采用本发明工艺,在适当降低水玻璃型壳的厚度的情况下制备得到较薄的水玻璃型壳,即采用较薄的水玻璃型壳壁厚(薄壳)就能达到足够的常温强度和焙烧强度要求;而薄壁水玻璃型壳不仅可以进一步降低残留强度,而且还可以减少固废的排放,且有利于金属的快速凝固、以及铸件性能的提高(由于薄壳散热能力强,冷却快速快,金属的晶粒细小,力学性能好),同时也有利于铸件凝固后型壳的脱壳。
附图说明
28.图1本发明实施例1水玻璃型壳硬化液滴反应装置的结构示意图;
29.图2本发明实施例2制备的焙烧型水玻璃型壳的焙烧强度柱状图(与浸入法对比);
30.图3本发明实施例2制备的水玻璃型壳的常温强度柱状图(与浸入法对比);
31.图4本发明实施例4制备的焙烧型水玻璃型壳的焙烧强度柱状图(与浸入法对比);
32.图5本发明实施例4制备的水玻璃型壳的常温强度柱状图(与浸入法对比);
33.图6本发明实施例6制备的焙烧型水玻璃型壳的焙烧强度柱状图(与浸入法对比);
34.图7本发明实施例6制备的水玻璃型壳的常温强度柱状图(与浸入法对比)。
35.图中附图标记表示为:1-雾化器;2-储液罐;3-液滴输送管;4-液滴分布器;5-反应室;6-蜡模试样;7-试样支架;8-残液排出孔;9-残液收集槽;10-供电电缆;11-加液孔;12-供液管;13-反应室支架。
具体实施方式
36.实施例1
37.本实施例中水玻璃型壳硬化液滴反应装置结构示意图如图1所示,包括雾化器1、储液罐2、液滴分布器4、反应室5、试样支架7、残液收集槽9和反应室支架13;试样支架7固定安装在反应室5内,蜡模试样6安置在试样支架7上;储液罐2的硬化剂溶液出口端通过供液管12与雾化器1的硬化剂溶液入口端流体导通,雾化器1的硬化剂溶液雾化液滴出口端通过液滴输送管3与位于反应室5内的液滴分布器4的硬化剂溶液雾化液滴入口端流体导通;液滴分布器4的硬化剂溶液雾化液滴出口端朝向蜡模试样6,液滴分布器4呈喇叭口型,即液滴分布器4的内径自其硬化剂溶液雾化液滴入口端至硬化剂溶液雾化液滴出口端逐渐增大
(在其它一些实施例中,液滴分布器4可以呈其它形状,如长方体形、圆盘型或直线型等);反应室5的硬化剂溶液残液出口端通过开设在反应室5底壁上的残液排出孔8与残液收集槽9的硬化剂溶液残液入口端流体导通。
38.储液罐2上开设有加液孔11,雾化器1通过供电电缆10与电源电连接;本实施例中的雾化器1为超声波雾化器,在其它一些实施例中也可以选择液体雾化器、喷淋器或文丘里射流器对本实施例中的超声波雾化器进行替换,液体雾化器可以使单液头雾化器,也可以是双液头雾化器,文丘里射流器是指利用文丘里原理制备的各种射流器;本实施例中的反应室为正方体,在其它一些实施例中也可以采用圆柱体、长方体以及由正方体、圆柱体和长方体组合成的其它形状的反应室。
39.实施例2
40.本实施例中,水玻璃型壳硬化工艺是采用实施例1的水玻璃型壳硬化液滴反应装置进行水玻璃型壳硬化的;蜡膜试样为采用射蜡机压射制备40
×
20
×
6mm的长方形凹槽蜡模,在凹槽蜡模表面施涂、撒砂构筑水玻璃型壳壳层,具体包括如下步骤:
41.步骤a:将硬化剂溶液灌装至储液罐中;采用水玻璃涂料对蜡模进行涂料涂挂并进行撒砂处理;撒砂处理完成后得到面层蜡模试样,将面层蜡模试样置于反应室中;
42.本步骤中,选择270目精制石英粉作为耐火粉料1.2kg,按粉液比(耐火粉料质量:水玻璃质量)1.2:1配制混合料,搅拌均匀后再分别加入润湿剂和消泡剂各1.0ml,连续搅拌1.0h后进行8.0h静置处理,得到面层水玻璃涂料,储存待用;使用前再次搅拌面层水玻璃涂料,搅拌时间为20min,然后静置5min后进行涂料涂挂;将压射成型的蜡模用清洗剂清洗并自然干燥后,将蜡模或蜡模组浸入制备的面层水玻璃涂料中,静置30~50s,然后将涂挂面层水玻璃涂料的蜡模取出,并放入沸腾砂床和雨淋式撒砂机中进行撒砂处理(50/70目石英砂)后,自然干燥50~60min得到面层蜡模试样。本步骤中所用的润湿剂、消泡剂和清洗剂均为本领域技术人员常用的试剂,本实例中不再赘述。本步骤所用的硬化剂溶液为浓度为5.0wt%的nh4cl溶液。
43.步骤b:启动雾化器,雾化器通过供液管将储液罐中的硬化剂溶液泵入雾化器中进行雾化;硬化剂溶液经雾化器雾化后形成的雾滴的粒径为0.5~500μm;所述雾化器的硬化剂溶液雾化液滴出口端的雾化液滴流量为1.0l/min,所述雾化器的载气压力为0.5mpa;
44.步骤c:硬化剂溶液经雾化器转化为硬化剂溶液雾化液滴,硬化剂溶液雾化液滴通过液滴输送管输送至反应室中,并与反应室内安置的面层蜡模试样表面的面层水玻璃涂层反应,反应时间为6~18min,使面层蜡模试样表面的面层水玻璃涂层硬化形成水玻璃型壳面层;反应后残留的硬化剂溶液雾化液滴沉积汇集至反应室底部,并流入残液收集槽中;
45.步骤d:取出具有水玻璃型壳的蜡模试样,重复步骤a至步骤c继续在蜡模试样上依次构筑水玻璃型壳过渡层和水玻璃型壳封浆层,待蜡模试样上完成所有型壳壳层的硬化,即得到具有水玻璃型壳壳层的蜡模,切断电源,从反应室中取出具有水玻璃型壳壳层的蜡模,即完成了水玻璃型壳的硬化;
46.本步骤中,水玻璃型壳过渡层的构筑方法为:将270目的石英粉与200目的莫来石粉按照质量比7:3配制成混合粉料,按粉液比(耐火粉料质量:水玻璃质量)1.1:1配制混合料,连续搅拌至少4.0h后储存待用,得到过渡层水玻璃涂料;使用前再次搅拌过渡层水玻璃涂料,搅拌时间为20min,然后静置5min再进行涂挂;将已构水玻璃型壳面层的蜡模或模组
浸入制备的过渡层水玻璃涂料中,静置30~50s,然后将涂挂过渡层水玻璃涂料的蜡模取出并放入雨淋式撒砂机中撒砂(20/40目石英砂)后,自然干燥40~50min,得到过渡层蜡模试样;然后将过渡层蜡模试样置于反应室中,采用步骤b-c的操作方法使蜡模试样表面形成水玻璃型壳过渡层;
47.本步骤中,水玻璃型壳封浆层的构筑方法以及使用的原料与上述水玻璃型壳过渡层的构筑方法完全相同,此处不再赘述。
48.步骤e:将上述具有水玻璃型壳壳层的蜡模在20℃条件下干燥12~24h,并采用热水浴法进行型壳脱蜡,即将上述具有水玻璃型壳壳层的蜡模试样浸入约95℃的热水中,水浴约10~15min后取出水玻璃型壳,脱蜡完成后得到水玻璃型壳;将水玻璃型壳置于xd-1400s箱式电阻炉中,以5℃/min的速率升温到750℃后保温2.0h,并随炉冷却至室温,即制备得到焙烧型水玻璃型壳;
49.采用传统浸入法制备水玻璃型壳和焙烧型水玻璃型壳,其制备方法与本实施例相比,除了水玻璃涂层的硬化反应为浸入法(即将蜡膜试样浸入硬化剂溶液中)之外,其它操作方法及工艺参数与本实施例完全一致,且用的试剂、涂料、原料配比等也完全相同。
50.将本实施例制备的水玻璃型壳和焙烧型水玻璃型壳分别与采用传统浸入法制备的水玻璃型壳和焙烧型水玻璃型壳进行对比;通过焙烧型水玻璃型壳的弯曲强度测试对比可以比较本实施例与传统浸入法两种不同硬化方法制备的水玻璃型壳的焙烧强度,结果见图2;通过水玻璃型壳的弯曲强度测试对比可以比较本实施例与传统浸入法两种不同硬化方法制备的水玻璃型壳的常温强度,结果见图3。
51.将本实施例传统浸入法工艺简称为“浸入法”,将本实施例的制备工艺简称为“雾化法”。两种工艺下不同硬化时间制备的水玻璃型壳其常温强度、焙烧强度和残留强度如表1所示。
52.表1
[0053][0054]
从表1可以看出,采用本实例的硬化工艺制备的水玻璃型壳,其焙烧强度在硬化时间为9min时达到最高,为9.7mpa,而采用传统侵入法工艺制备的水玻璃型壳,在硬化时间6~18min范围内其焙烧强度变化不大,均在6.38~6.71mpa之间;两种硬化工艺条件下,当硬化时间为6~15min时,传统浸入法工艺制备的水玻璃型壳的焙烧强度明显低于本实施例的硬化工艺制备的水玻璃型壳。
[0055]
同时,从表1中可以看出,采用本实例的硬化工艺制备的水玻璃型壳,其常温强度在硬化时间为6min时达到最高,为21.42mpa;而采用传统侵入法工艺制备的水玻璃型壳,其常温强度在硬化时间为12min时达到最高,为14.57mpa;两种硬化工艺条件下,当硬化时间在6~18min范围内时,其常温硬化强度均呈现先下降后增加然后再下降的趋势。
[0056]
与传统浸入法相比,本实施例制备的水玻璃型壳常温强度峰值提高了47.01%,焙烧强度峰值提高了44.56%,而水玻璃型壳到达常温强度峰值时,残留强度占比(残留强度/常温强度峰值)降低了6.23%;水玻璃型壳到达焙烧强度峰值时,残留强度占比(残留强度/焙烧强度峰值)降低了44.26%;硬化剂溶液的利用率提高至98.0%。
[0057]
实施例3
[0058]
本实施例中,水玻璃型壳硬化工艺也是采用实施例1的水玻璃型壳硬化液滴反应装置进行水玻璃型壳硬化的;除所使用的硬化剂溶液为浓度为10.0wt%的nh4cl溶液外,其他具体操作步骤、采用的试剂原料、工艺参数等与实施例2完全相同。
[0059]
采用传统的浸入法制备水玻璃型壳和焙烧型水玻璃型壳,其制备方法与本实施例相比,除了水玻璃涂层的硬化反应为浸入法(即将蜡膜试样浸入硬化剂溶液中)之外,其它操作方法及工艺参数与本实施例完全一致,且用的试剂、涂料、原料配比等也完全相同。
[0060]
将本实施例制备的水玻璃型壳和焙烧型水玻璃型壳分别与采用传统浸入法制备的水玻璃型壳和焙烧型水玻璃型壳进行对比;通过焙烧型水玻璃型壳的弯曲强度测试对比可以比较本实施例与传统浸入法两种不同硬化方法制备的水玻璃型壳的焙烧强度;通过水玻璃型壳的弯曲强度测试对比可以比较本实施例与传统浸入法两种不同硬化方法制备的水玻璃型壳的常温强度。
[0061]
将本实施例传统浸入法工艺简称为“浸入法”,将本实施例的制备工艺简称为“雾化法”。两种工艺下不同硬化时间制备的水玻璃型壳其常温强度、焙烧强度和残留强度如表2所示。
[0062]
表2
[0063][0064]
与传统浸入法相比,本实施例制备的水玻璃型壳常温强度峰值提高了27.33%,焙烧强度峰值提高了3.24%,而水玻璃型壳到达常温强度峰值时,残留强度占比(残留强度/常温强度峰值)降低了2.95%;水玻璃型壳到达焙烧强度峰值时,残留强度占比(残留强度/焙烧强度峰值)降低了8.25%;硬化剂溶液的利用率提高至97.5%。
[0065]
实施例4
[0066]
本实施例中,水玻璃型壳硬化工艺也是采用实施例1的水玻璃型壳硬化液滴反应装置进行水玻璃型壳硬化的;除所使用的硬化剂溶液为浓度为15.0wt%的nh4cl溶液外,其他具体操作步骤、采用的试剂原料、工艺参数等与实施例2完全相同。
[0067]
采用传统的浸入法制备水玻璃型壳和焙烧型水玻璃型壳,其制备方法与本实施例相比,除了水玻璃涂层的硬化反应为浸入法(即将蜡膜试样浸入硬化剂溶液中)之外,其它操作方法及工艺参数与本实施例完全一致,且用的试剂、涂料、原料配比等也完全相同。
[0068]
将本实施例制备的水玻璃型壳和焙烧型水玻璃型壳分别与采用传统浸入法制备的水玻璃型壳和焙烧型水玻璃型壳进行对比;通过焙烧型水玻璃型壳的弯曲强度测试对比可以比较本实施例与传统浸入法两种不同硬化方法制备的水玻璃型壳的焙烧强度,结果见图4;通过水玻璃型壳的弯曲强度测试对比可以比较本实施例与传统浸入法两种不同硬化方法制备的水玻璃型壳的常温强度,结果见图5。从图4和图5中可以看出,硬化剂浓度增大到15.0wt%时,两种硬化工艺条件下,硬化时间超过9min后,常温强度及焙烧后强度不再增加,甚至会逐渐降低。因此,硬化时间一般控制不超过9min。
[0069]
将本实施例传统浸入法工艺简称为“浸入法”,将本实施例的制备工艺简称为“雾化法”。两种工艺下不同硬化时间制备的水玻璃型壳其常温强度、焙烧强度和残留强度如表3所示。
[0070]
表3
[0071][0072][0073]
与传统浸入法相比,本实施例制备的水玻璃型壳常温强度峰值提高了26.23%,焙烧强度峰值提高了90.91%,而水玻璃型壳到达常温强度峰值时,残留强度占比(残留强度/常温强度峰值)降低了3.09%;水玻璃型壳到达焙烧强度峰值时,残留强度占比(残留强度/焙烧强度峰值)降低了6.45%;硬化剂溶液的利用率提高至96.0%。
[0074]
实施例5
[0075]
本实施例中,水玻璃型壳硬化工艺也是采用实施例1的水玻璃型壳硬化液滴反应装置进行水玻璃型壳硬化的;除所使用的硬化剂溶液为浓度为20.0wt%的nh4cl溶液外,其他具体操作步骤、采用的试剂原料、工艺参数等与实施例2完全相同。
[0076]
采用传统的浸入法制备水玻璃型壳和焙烧型水玻璃型壳,其制备方法与本实施例
相比,除了水玻璃涂层的硬化反应为浸入法(即将蜡膜试样浸入硬化剂溶液中)之外,其它操作方法及工艺参数与本实施例完全一致,且用的试剂、涂料、原料配比等也完全相同。
[0077]
将本实施例制备的水玻璃型壳和焙烧型水玻璃型壳分别与采用传统浸入法制备的水玻璃型壳和焙烧型水玻璃型壳进行对比;通过焙烧型水玻璃型壳的弯曲强度测试对比可以比较本实施例与传统浸入法两种不同硬化方法制备的水玻璃型壳的焙烧强度;通过水玻璃型壳的弯曲强度测试对比可以比较本实施例与传统浸入法两种不同硬化方法制备的水玻璃型壳的常温强度。
[0078]
将本实施例传统浸入法工艺简称为“浸入法”,将本实施例的制备工艺简称为“雾化法”。两种工艺下不同硬化时间制备的水玻璃型壳其常温强度、焙烧强度和残留强度如表4所示。
[0079]
表4
[0080][0081]
与传统浸入法相比,本实施例制备的水玻璃型壳常温强度峰值提高了69.60%,焙烧强度峰值提高了83.84%,而水玻璃型壳到达常温强度峰值时,残留强度占比(残留强度/常温强度峰值)升高了12.15%;水玻璃型壳到达焙烧强度峰值时,残留强度占比(残留强度/焙烧强度峰值)降低了4.93%;硬化剂溶液的利用率提高至96.3%。
[0082]
实施例6
[0083]
本实施例中,水玻璃型壳硬化工艺也是采用实施例1的水玻璃型壳硬化液滴反应装置进行水玻璃型壳硬化的;除所使用的硬化剂溶液为浓度为25.0wt%的nh4cl溶液外,其他具体操作步骤、采用的试剂原料、工艺参数等与实施例2完全相同。
[0084]
采用传统的浸入法制备水玻璃型壳和焙烧型水玻璃型壳,其制备方法与本实施例相比,除了水玻璃涂层的硬化反应为浸入法(即将蜡膜试样浸入硬化剂溶液中)之外,其它操作方法及工艺参数与本实施例完全一致,且用的试剂、涂料、原料配比等也完全相同。
[0085]
将本实施例制备的水玻璃型壳和焙烧型水玻璃型壳分别与采用传统浸入法制备的水玻璃型壳和焙烧型水玻璃型壳进行对比;通过焙烧型水玻璃型壳的弯曲强度测试对比可以比较本实施例与传统浸入法两种不同硬化方法制备的水玻璃型壳的焙烧强度,结果见图6;通过水玻璃型壳的弯曲强度测试对比可以比较本实施例与传统浸入法两种不同硬化方法制备的水玻璃型壳的常温强度,结果见图7。从图6和图7中可以看出,硬化剂浓度为25.0wt%、硬化时间不超过12min时,本实施例的型壳常温强度、焙烧强度均优于传统浸入
法制备的型壳。硬化时间超过12min后,本实施例的硬化方法所制备型壳的强度优势减弱。
[0086]
将本实施例传统浸入法工艺简称为“浸入法”,将本实施例的制备工艺简称为“雾化法”。两种工艺下不同硬化时间制备的水玻璃型壳其常温强度、焙烧强度和残留强度如表5所示。
[0087]
表5
[0088][0089]
对于精铸生产而言,型壳的性能首先必须满足常温、焙烧强度要求,在此前提下,才考虑残留强度是否足够低,只比较两种硬化工艺的残留强度是没有实际意义的。从表5中可以看出,当硬化剂浓度达到25.0wt%时,所有浸入法硬化型壳的焙烧强度均低于3.0mpa,已达不到一般型壳的焙烧强度要求(不低于3.0mpa),因此,这种硬化条件下获得的型壳尽管残留强度极低,但由于焙烧强度过低,在实际生产中仍无法应用。而采用雾化法时,即使硬化剂浓度达到25.0wt%的高浓度,也可以制备得到焙烧强度满足应用要求的型壳。
[0090]
与传统浸入法相比,本实施例制备的水玻璃型壳虽然到达常温强度峰值时,残留强度占比(残留强度/常温强度峰值)升高了10.95%,但水玻璃型壳常温强度峰值提高了67.04%,焙烧强度峰值提高了483.44%,水玻璃型壳到达焙烧强度峰值时,残留强度占比(残留强度/焙烧强度峰值)降低了74.03%;硬化剂溶液的利用率提高至97.0%。本实施例的结果说明,高的硬化剂溶液浓度条件下,传统浸入法制备的型壳焙烧强度损失远高于本发明的硬化工艺,特别是其焙烧强度均低于2.0mpa,已远不能满足工业生产要求。
[0091]
需要特别指出的是,在实际铸造生产中,低温环境下(一般《10℃)型壳硬化反应缓慢,制壳周期延长,生产率低,如南方企业冬季无暖气的生产条件下,生产车间气温一般在-5~10℃,硬化剂的浓度较低时,型壳无法硬化,必需采用高浓度硬化剂,而采用高浓度硬化剂溶液以浸入法生产型壳虽然可以加速硬化,但导致的后果是生产的型壳虽然具有较低的残留强度,但由于焙烧强度极低,也无法使用,导致废品率高。本实例进一步突显了本发明的优势,即使采用25.0wt%的高浓度溶液作硬化剂(接近20℃时的饱和浓度值27.11%),雾化法硬化型壳的强度性能仍能满足要求,即对于硬化剂溶液变化具有较强的低温环境适应性。
[0092]
显然,上述实施例仅仅是为清楚地说明所作的举例,而并非对实施方式的限定。对于所属领域的普通技术人员来说,在上述说明的基础上还可以做出其它不同形式的变化或变动。这里无需也无法对所有的实施方式予以穷举。而由此所引伸出的显而易见的变化或
变动仍处于本专利申请权利要求的保护范围之中。
[0093]
综上,利用本发明的水玻璃型壳硬化液滴反应装置可对水玻璃型壳以雾化液滴冲击方式进行硬化,进而实现水玻璃型壳的可控制备;与传统浸入法硬化过程相比,本发明的工艺中所用水玻璃型壳硬化液滴反应装置结构简单;且硬化剂种类、浓度、液滴输入量、载气能够根据实际需求选择;硬化反应速率、反应程度及每一壳层的性能均可方便调控。由于该装置储液罐中的硬化剂溶液始终不与型壳接触,不会被污染,其成分及物理化学性质稳定,雾化后得到的水玻璃型壳的硬化特性也保持不变;硬化剂溶液以雾化液滴的方式与型壳表面接触而发生硬化反应,故型壳硬化所消耗的硬化剂量少;能避免现有浸入法硬化水玻璃型壳工艺中存在的硬化剂溶液消耗量大、易污染、物理化学性质随使用频次变化、型壳硬化特性波动、硬化剂废液排放大等问题;由于硬化剂性质稳定、硬化速率可控,因此能够提高水玻璃型壳的常温强度和焙烧强度,降低残留强度;使得制备的水玻璃型壳性能远高于一般与传统浸入法型壳。同时,它能够提高硬化剂溶液的利用率,减少废液的排放,有利于保护环境。另外,本发明的工艺制备周期短,可在最短几分钟内完成型壳硬化,过程简单、快捷且便于操作;硬化过程在密闭反应器内进行,无挥发,操作环境良好;适用于包括钠、钾等各类水玻璃粘结剂和其他酸性液体硬化剂硬化的各类精密铸造型壳的可控制备,也能够为其他种类复合型壳的制备以胶凝材料的材料加工提供一种快速简便的快速硬化方法,普适性极高。