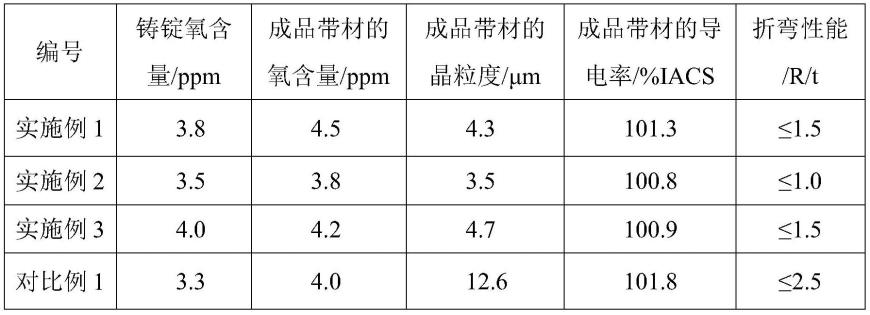
1.本发明属于铜合金技术领域,具体涉及一种无氧铜铸锭的制备方法及无氧铜带材的制备方法。
背景技术:2.无氧铜带具备极好的导电导热性能,焊接无氢裂现象,在5g、新能源汽车、新基建等领域应用广泛。高端无氧铜(氧含量在5ppm以下的tu00无氧铜)主要依赖进口,进口量在1万吨左右。国外制备tu00无氧铜主要采用高纯电解板和真空炉的方法进行制备,国内基本上无法稳定生产高端无氧铜。
3.如公开号为cn110343870a(申请号为201910680185.8)的中国发明专利申请《一种无氧铜熔铸生产方法》,其中公开了一种采用敞开式工频感应电炉生产大规格无氧铜锭(铸锭面积可达200000mm2)的方法,主要是在熔炼时通过石墨管吹气以及外加磁场的作用进行除气、造渣,降低熔体中的氧含量,通过此方法制备的氧含量在8~15ppm,但仍不满足高端无氧铜带的要求。另外,如公开号为cn113414359a(申请号为202110661944.3)的中国发明专利申请《一种水平连铸制备无氧铜的方法》,其中公开了采用底吹装置(底部吹气装置)底吹混合气体水平连铸制备tu00的无氧铜,从水平连铸的熔炼炉铜水到保温炉的过程是以潜液转流的方式进行,不接触空气,其次结晶器是安装在保温炉炉壁上,铜水直接进入结晶器,也不接触空气,因此整个熔炼铸造过程铜水流转过程密闭,氧化较少,因设备自身的原因,水平连铸制备无氧铜对于氧含量易控制,但由于受水平连铸设备的限制,铸坯厚度一般不超过20mm,无法进行热轧,只能采用一次冷轧和一次退火的方式制备成品,成品厚度一般在0.3mm以上,且由于是冷轧,所以晶粒不能完全破碎,再结晶后组织不均匀,折弯性能较差,无法满足电器行业折弯性能要求。
技术实现要素:4.本发明所要解决的第一个技术问题是提供一种采用敞开式半连铸炉制备无氧铜铸锭的制备方法。
5.本发明解决第一个技术问题所采用的技术方案为:一种无氧铜铸锭的制备方法,其特征在于,包括以下制备步骤:
6.1)熔炼:将配备的原料送入熔炼炉熔化,熔化速率为3~6t/h,熔化过程中采用煅烧木炭进行覆盖,熔炼炉温度控制在1190~1210℃,铜液通过安装有过滤器的溜槽转炉至保温炉,铜水液位高出泡沫陶瓷过滤器上表面15~25cm,过滤器的数量为两个,沿熔炼炉到保温炉的方向间隔设置,靠近熔炼炉出口处的过滤器的孔隙率在10~20ppi,靠近保温炉进口处的过滤器的孔隙率在20~40ppi,转炉后,保温炉的温度控制在1160~1180℃;
7.2)保温除气:转炉后,保温炉加料口补加煅烧木炭,覆盖厚度不低于20cm,同时补加铜磷中间合金;通过预埋在保温炉底部的吹气装置向铜液吹混合气体,所述混合气体的体积含量组成为40~60%的n2或/和ar,余量为co,每吨铜水的吹气量不低于200l;混合气
体压力为0.4~0.8mpa,吹气结束后加入铜钙中间合金;
8.3)半连铸:打开石墨塞棒,铜液通过三通管浇入结晶器中,冷却后拉出铸锭;铸造速度为60~80mm/min,混合气体的压力每隔0.5h下降0.04~0.07mpa。
9.熔炼炉温度控制在1190~1210℃,此时在保持铜水流动性良好的同时不至于过度氧化,另外铜水液位高出泡沫陶瓷过滤器上表面15~25cm,高于15cm是为了保持足够的静压力,保证铜液能够从过滤器流出而不至于堵塞在过滤器中,不高于25cm是为了保证铜液流出速度平缓,不会形成湍流,湍流会导致吸气,氧含量上升;转炉后,保温炉的温度控制在1160-1180℃,保证铜水流动性良好的同时使得氧化物(主要是氧化亚铜)随着底吹气体上浮;
10.过滤器用于过滤原料熔化过程中的氧化物夹渣,靠近熔炼炉处的过滤器的孔隙率在10~20ppi,先过滤熔炼炉内较大的氧化物颗粒,同时温度下降不超过10℃;靠近保温炉处的过滤器的孔隙率在20~40ppi,进一步过滤转炉过程中的氧化物夹渣。
11.为避免铸造过程中铜水与空气接触,作为优选,所述步骤3)中,铸造前先用氩气吹扫结晶器,然后在结晶器底部铺撒一层石墨颗粒,石墨颗粒厚度2~5mm,当铜水进入结晶器后,三通管位于铜水液面以下2~7cm,三通管的流量控制在8~16l/min。
12.作为优选,所述步骤2)中,铜磷中间合金中磷质量含量为12~15%,加入量不高于熔体总重的0.003%。p能够吸收铜液中的氧,并形成杂质上浮,进一步降低o含量,但加入量不能过高,否则无氧铜的导电率严重下降。
13.作为优选,所述步骤2)中,铜钙中间合金中钙质量含量为30~50%,加入量为熔体总重的0.002~0.006%。首先钙元素能够吸收熔体中的杂质元素,尤其是氧元素,净化熔体;其次能够作为形核核心,细化铸坯组织,由于组织具有遗传性,后续加工后的毛坯组织晶粒也更为细小,折弯性能也大大提高。
14.作为优选,所述步骤1)中,原料的质量百分比组成为10~20%的t2紫铜回料,余量为铜含量为99.9wt%以上的电解板。
15.作为优选,所述步骤3)中,铸锭的氧含量控制在5ppm以下。
16.本发明所要解决的第二个技术问题是提供一种无氧铜带材的制备方法。
17.本发明解决第二个技术问题所采用的技术方案为:一种无氧铜带材的制备方法,其特征在于:工艺流程包括:采用上述的无氧铜铸锭的制备方法制备
→
热轧
→
粗轧
→
精轧
→
退火
→
冷轧;所述热轧温度为700~750℃,热轧加工率在95%以上。
18.作为优选,所述粗轧的加工率控制在80%以上,所述精轧的加工率控制在50%以上,所述冷轧加工率控制25~35%。
19.作为优选,所述退火采用气垫炉退火,温度为650~720℃,速度为30~50m/min。
20.与现有技术相比,本发明的优点在于:
21.敞开式半连铸紫铜的生产过程中,熔炼炉是完全敞开熔炼,熔化后的铜水也是通过敞开的溜槽转入保温炉中,保温炉的铜水通过三通石墨浇管浇入结晶器中,浇注过程中铜水暴露在空气中,氧含量控制难度高。
22.另外由于加料和熔沟的搅拌作用,导致熔炼炉铜液吸氧严重,而且每次转炉后,剩余铜液完全暴露在空气中,粘附在熔炼炉炉壁上,通过在溜槽前后设置不同的孔隙率过滤器,有效过滤熔化炉熔化过程中以及转炉过程中生成的大量的微米级以上的氧化物夹渣,
并通过液面高度控制,稳定从熔炼炉到保温炉的熔体的流速,防止造成湍流导致的吸氧。另外在铸造时,控制底吹混合气体的压力,以一定数值下降,控制防止液面下降后,液体静压力下降而导致吹气压力过高,造成液面翻滚吸气,同时保证底吹气体始终形成微米级气泡,带动氧化物上浮,降低铸坯氧含量。
23.制备了氧含量低于5ppm以下的大规格铸锭,单根铸锭总重在10吨左右,后续通过热轧等工艺,制备出的成品带材的晶粒度在0.005mm以下厚度在0.1-0.3mm的细晶薄带,成品导电率在100%iacs以上,氧含量在4ppm以下,坏方向上r/t满足1.5以下折弯无开裂。
具体实施方式
24.以下结合实施例对本发明作进一步详细描述。
25.实施例1制备成品规格为630mm(宽)*0.2mm(厚)的无氧铜带材,包括以下制备步骤:
26.1)熔炼:将配备的原料送入熔炼炉熔化,原料的质量百分比组成为15%的t2紫铜回料,余量为铜含量为99.9wt%以上的电解板。
27.熔化速率为5t/h,熔化过程中采用煅烧木炭进行覆盖,木炭粒径控制在1~5cm,木炭在800℃下煅烧4h以上,覆盖厚度不小于30cm;熔炼炉温度控制在1190~1210℃,铜液通过安装有过滤器的溜槽转炉至保温炉,转炉温度为1200℃,铜水液位高出泡沫陶瓷过滤器上表面20cm,过滤器的数量为两个,沿熔炼炉到保温炉的方向间隔设置,靠近熔炼炉出口处的过滤器的孔隙率在15ppi,靠近保温炉进口处的过滤器的孔隙率在30ppi,转炉后,保温炉的温度控制在1160~1180℃;每次转炉量在20吨,转炉过程中溜槽加入混合覆盖剂,覆盖剂为1:1:1混合的木炭、石墨鳞片与冰晶石,覆盖剂的覆盖厚度10cm以上;
28.2)保温除气:转炉后,保温炉加料口补加煅烧木炭,覆盖厚度不低于20cm,同时补加铜磷中间合金,铜磷中间合金中磷质量含量为14%,加入量为熔体总重的0.002%;同时通过预埋在保温炉底部的吹气装置向铜液吹混合气体,混合气体的体积含量组成为40%的n2,余量为co,每吨铜水的吹气量250l;混合气体压力为0.5~0.6mpa,吹气结束后加入铜钙中间合金,铜钙中间合金中钙质量含量为50%,加入量为熔体总重的0.003%。
29.3)半连铸:铸造前先用氩气吹扫结晶器,然后在结晶器底部铺撒一层石墨颗粒,石墨颗粒厚度2mm,打开石墨塞棒,当铜水进入结晶器后,三通管位于铜水液面以下2~5cm,三通管的流量控制在10l/min,铜液通过三通管浇入结晶器中,冷却后拉出铸锭;铸造速度为70mm/min,混合气体的压力每隔0.5h下降0.04mpa,铸锭规格650mm*300mm。
30.4)热轧:热轧温度为730℃,热轧后铸坯规格为630mm*12mm;
31.5)铣面:单面铣面深度0.6mm;
32.6)粗轧:粗轧规格为630mm*1.5mm;
33.7)精轧:精轧规格为630mm*0.8mm;
34.8)退火:采用气垫炉退火,温度为720℃,速度为40m/min;
35.9)冷轧至成品规格,成品规格为630mm*0.2mm。
36.实施例2制备成品规格为630mm(宽)*0.15mm(厚)的无氧铜带材,包括以下制备步骤:
37.1)熔炼:将配备的原料送入熔炼炉熔化,原料的质量百分比组成为10%的t2紫铜
回料,余量为铜含量为99.9wt%以上的电解板。
38.熔化速率为6t/h,熔化过程中采用煅烧木炭进行覆盖,木炭粒径控制在1~5cm,木炭在700℃下煅烧4h以上,覆盖厚度不小于30cm;熔炼炉温度控制在1190~1210℃,铜液通过安装有过滤器的溜槽转炉至保温炉,转炉温度为1200℃,铜水液位高出泡沫陶瓷过滤器上表面20cm,过滤器的数量为两个,沿熔炼炉到保温炉的方向间隔设置,靠近熔炼炉出口处的过滤器的孔隙率在10ppi,靠近保温炉进口处的过滤器的孔隙率在20ppi,转炉后,保温炉的温度控制在1160~1180℃;每次转炉量在20吨,转炉过程中加入混合覆盖剂溜槽,覆盖剂为1:1:1混合的木炭、石墨鳞片与冰晶石,覆盖剂的覆盖厚度10cm以上;
39.2)保温除气:转炉后,保温炉加料口补加煅烧木炭,覆盖厚度不低于20cm,同时补加铜磷中间合金,铜磷中间合金中磷质量含量为14%,加入量为熔体总重的0.002%;同时通过预埋在保温炉底部的吹气装置向铜液吹混合气体,混合气体的体积含量组成为50%的n2,余量为co,每吨铜水的吹气量300l;混合气体压力为0.4~0.5mpa,吹气结束后加入铜钙中间合金,铜钙中间合金中钙质量含量为30%,加入量为熔体总重的0.004%。
40.3)半连铸:铸造前先用氩气吹扫结晶器,然后在结晶器底部铺撒一层石墨颗粒,石墨颗粒厚度2mm,打开石墨塞棒,当铜水进入结晶器后,三通管位于铜水液面以下2~5cm,三通管的流量控制在15l/min,铜液通过三通管浇入结晶器中,冷却后拉出铸锭;铸造速度为65mm/min,混合气体的压力每隔0.5h下降0.04mpa,铸锭规格650mm*300mm。
41.4)热轧:热轧温度为740℃,热轧后铸坯规格为630mm*10mm;
42.5)铣面:单面铣面深度0.6mm;
43.6)粗轧:粗轧规格为630mm*1.2mm;
44.7)精轧:精轧规格为630mm*0.6mm;
45.8)退火:采用气垫炉退火,温度为720℃,速度为38m/min;
46.9)冷轧至成品规格,成品规格为630mm*0.15mm。
47.实施例3制备成品规格为630mm(宽)*0.3mm(厚)的无氧铜带材,包括以下制备步骤:
48.1)熔炼:将配备的原料送入熔炼炉熔化,原料的质量百分比组成为10%的t2紫铜回料,余量为铜含量为99.9wt%以上的电解板。
49.熔化速率为6t/h,熔化过程中采用煅烧木炭进行覆盖,木炭粒径控制在1~5cm,木炭在700℃下煅烧4h以上,覆盖厚度不小于30cm;熔炼炉温度控制在1190~1210℃,铜液通过安装有过滤器的溜槽转炉至保温炉,转炉温度为1200℃,铜水液位高出泡沫陶瓷过滤器上表面20cm,过滤器的数量为两个,沿熔炼炉到保温炉的方向间隔设置,靠近熔炼炉出口处的过滤器的孔隙率在20ppi,靠近保温炉进口处的过滤器的孔隙率在40ppi,转炉后,保温炉的温度控制在1160~1180℃;每次转炉量在20吨,转炉过程中加入混合覆盖剂溜槽,覆盖剂为1:1:1混合的木炭、石墨鳞片与冰晶石,覆盖剂的覆盖厚度10cm以上;
50.2)保温除气:转炉后,保温炉加料口补加煅烧木炭,覆盖厚度不低于20cm,同时补加铜磷中间合金,铜磷中间合金中磷质量含量为14%,加入量为熔体总重的0.0015%;同时通过预埋在保温炉底部的吹气装置向铜液吹混合气体,混合气体的体积含量组成为60%的n2,余量为co,每吨铜水的吹气量250l;混合气体压力为0.4~0.5mpa,吹气结束后加入铜钙中间合金,铜钙中间合金中钙质量含量为40%,加入量为熔体总重的0.005%。
51.3)半连铸:铸造前先用氩气吹扫结晶器,然后在结晶器底部铺撒一层石墨颗粒,石墨颗粒厚度2mm,打开石墨塞棒,当铜水进入结晶器后,三通管位于铜水液面以下2~5cm,三通管的流量控制在10l/min,铜液通过三通管浇入结晶器中,冷却后拉出铸锭;铸造速度为70mm/min,混合气体的压力每隔0.5h下降0.05mpa,铸锭规格650mm*300mm。
52.4)热轧:热轧温度为700℃,热轧后铸坯规格为630mm*10mm;
53.5)铣面:单面铣面深度0.6mm;
54.6)粗轧:粗轧规格为630mm*1.5mm;
55.7)精轧:精轧规格为630mm*0.7mm;
56.8)退火:采用气垫炉退火,温度为720℃,速度为35m/min;
57.9)冷轧至成品规格,成品规格为630mm*0.3mm。
58.对比例为水平连铸tu00无氧铜带,成品规格为630mm(宽)*0.3mm(厚)。
59.对得到的实施例、对比例进行以下检测:
60.含氧量检测:经红外吸收法测量氧,采用gb/t 5121.8-2008铜及铜合金化学分析方法第8部分:氧含量的测定方法进行测试;
61.晶粒度检测方法:铜及铜合金平均晶粒度测试方法ys/t 347-2004中的截距法。
62.成品导电率测试方法:金属材料电阻测试方法gb/t 351。
63.坏方向(垂直于轧制方向)折弯性能测试方法:金属材料弯曲试验方法gb/t 232-2010。
64.表1本发明实施例、对比例的测试结果
65.