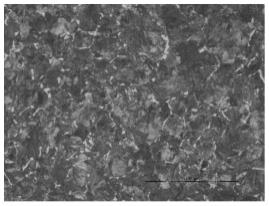
1.本发明属于车轮钢领域,涉及铁道矿山及铁道货运用高碳高韧性重载车轮的制造领域,具体为一种高碳高韧性重载车轮钢及车轮生产方法。
背景技术:2.近年来,随着世界经济的发展,铁路货运量以惊人的速度增加,铁路运输不断向高速、重载方向发展,重载铁路运输因其运输能力大、运输效率高、成本低已被国际世界公认为铁路货运发展主要方向之一。特别是矿石、煤炭等大宗货物的运输任务主要是由铁路来完成,铁路运输对经济所做的贡献是不可磨灭的。市场研究机构fitch solutions的最新报告强调,全球2021-2025年的铁矿石产量平均增长2.4%,而此前五年为-2.0%。美国、澳大利亚、加拿大、巴西、南非、俄罗斯、中国等多个国家推行铁道货运重载运输极大地提高了铁路劳动生产率,重载运输取得的效益已由各国的实际运输业绩所证实。目前,世界各国争相借助于高新技术,以增加重载列车牵引重量。国际上重载车轮的运用大概占铁路车轮总需求的三分之一。
3.重载铁路运输的迅速发展,使得车轮的需求量越来越多。然而,由于列车重量增大,长度增加,车辆轴重增大,列车运行中的牵引力及制动力加大,导致货物及车辆设备损坏增多、线路变形以及养护维修工作量增大、轮轨磨耗加剧等,已成为重载铁路运输中的突出问题。车轮在运行过程中不但承受着货车的自重与载重,而且还与钢轨、闸瓦及环境介质都有着非常复杂的关系,承受着极其复杂的应力和踏面制动所产生的热负荷。车轮服役寿命明显缩短、损伤发生率显著提高,严重威胁了行车安全及工作人员的生命安全,铁路车辆使用费用的三分之一都用在了轮对的修理和技术维护上。据美国和澳大利亚统计,重载运输中15%~2o%的运营成本耗费于轮轨磨损。美国和俄罗斯的数据表明,若轮对负荷提高lot,轮轨磨耗将增加6~18倍。轴重的增加势必会对铁路车轮造成一定的负面影响,迫使车轮在极端条件下服役,这就对重载车轮的特性提出了更高的要求。
4.目前,国内货车车轮材质主要有tb/t 2817标准中的cl60(ii号钢)、cl65 (iii号钢)、cl70(iv号钢),但均未规定轮辋断裂韧性。国外货车车轮材质主要有欧标en13262中的er6、er7、er8、ers8、er9五种材质,但轮辋抗拉强度不能超过1050mpa。美标aar m-107/m-208中的aar-b、aar-c、aar-d三种材质,但未规定冲击性能。
5.现有技术中,2015年8月12日公开的公开号为cn 104831158 a的一种车轮钢,其用途以及热处理方法的专利,其成分为:c 0.68-0.77%、si≤1.00%、 mn≤1.20%、p≤0.025%、s≤0.025%,其余为fe和不可避免的杂质元素。用于制造铁路货车车轮。热处理方法包括如下步骤:(1)车轮随炉升温至850~ 870℃;(2)保温;(3)轮辋喷水冷却;(4)在辐板中部温度降至730℃以下时,对辐板部位进行风冷;(5)空冷;(6)加热,回火,保温。采用上述成分及工艺制造的车轮抗拉强度在926mpa~956mpa,可以用于高碳车轮制造,不足之处是抗拉强度不超过1000mpa,不能满足铁道矿山及铁道货运用高碳高韧性重载车轮的要求。
6.2017年10月13日公开的公开号为cn 107245649 a的一种高强高塑性重载铁路货
车车轮用钢及其生产方法的专利,其化学成分重量百分比为:c 0.67
‑ꢀ
0.77%、si 0.50-0.70%、mn 0.70-0.8%、v 0.05-0.15%、n 50-150ppm、 als≤0.025%、p≤0.015%、s≤0.015%,其余为fe和不可避免的杂质元素。采用上述成分及与之相对应的工艺制造的车轮,强韧性良好,可用于重载车轮制造,但不足之处是其强度略低,踏面下30mm处硬度平均值最高338hbw,不适合大轴重工况下服役。
7.2014年4月23日公开的公开号为cn 103741033 a的一种提高塑性的铁路货车用高碳车轮钢及其车轮制备方法的专利,化学成分重量百分比为:c0.70~ 0.75%、si0.70~1.00%、mn0.60~0.90%、0《cr≤0.35%、als0.010~0.030%、p ≤0.020%、s≤0.040%,其余为fe和不可避免的杂质元素,热处理工序为:轧制、粗加工后的车轮随炉升温至850-880℃后保温,总加热时间为2.5-3.0h,出炉空冷至室温;再将车轮随炉升温至840-860℃后保温,总加热时间为 2.5-3.0h,出炉喷水冷却450s;然后放入490-510℃炉中,保温4.5-5.5h后,出炉空冷至室温,获得良好的综合性能。不足之处在于相比常规淬火工艺,增加了一道升温
→
空冷的正火工序,增加了温室气体排放。
技术实现要素:8.本发明的目的在于提供一种高碳高韧性重载车轮钢,通过添加v、n元素,可以与c形成碳化物、氮化物及碳氮化物,碳化物、氮化物及碳氮化物的析出能够起到阻止奥氏体晶粒长大及析出强化的作用,从而能够获得满足要求的车轮钢组织和性能;添加ni元素,可以获得更加优良的车轮组织及提高晶粒度级别,从而提高车轮的机械性能。
9.本发明还有一个目的在于提供一种车轮生产方法,利用上述高碳高韧性重载车轮钢生产车轮,采用淬火前快速加热的热处理工艺,获得理想的细珠光体+ 铁素体组织,不仅轮辋机械性能水平更高,能够显著提高车轮强度,有效增强了重载服役条件下车轮耐磨性能,而且提高车轮韧性,增强了车轮抗断裂能力。
10.本发明具体技术方案如下:
11.一种高碳高韧性重载车轮钢,包括以下质量百分比成分:
12.c 0.71-0.75%、si 0.30-0.35%、mn 0.82-0.90%、p≤0.015%、s0.006-0.015%、v 0.05-0.10%、cr 0.22-0.27%、ni 0.20-0.27%、n0.0060-0.0100%,其余为fe和不可避免的杂质元素。
13.优选地,本发明提供的一种高碳高韧性重载车轮钢,包括以下质量百分比成分:
14.c 0.71-0.73%、si 0.30-0.35%、mn 0.85-0.90%、p≤0.010%、s 0.006-0.012%、 v 0.05-0.10%、cr 0.22-0.27%、ni 0.20-0.27%、n 0.0060-0.0090%,其余为 fe和不可避免的杂质元素。
15.高碳高韧性重载车轮钢的成分满足公式: 410<930-[570
×
%c]-[80
×
%mn]-[20
×
%si]-[50
×
%cr]-[30
×
%ni]-[20
×
%v] <460;
[0016]
该公式基于aar m-107/m-208《碳素钢车轮规范》成分设计,但aar标准中仅需公式值>390,而本发明提高了公式下限,并且规定了上限,一方面是充分考虑到塑韧性,不能一味追求强度,另一方面是合金元素/微合金元素含量不能过低,要能够满足30-45t轴重铁道货运车辆服役要求。
[0017]
本发明提供的一种车轮生产方法,采用高碳高韧性重载车轮钢生产,具体生产方
法包括电炉冶炼连铸工序、切锭轧制工序、热处理工序,所述热处理工序具体为:先将车轮加热至500-550℃,保温5-15min,再快速加热至淬火温度,保温,轮辋喷水冷却后,回火处理。
[0018]
将车轮加热至500-550℃,加热速率为20-25℃/min;
[0019]
所述快速加热至淬火温度,加热速率为30-35℃/min;
[0020]
所述淬火温度是820-880℃;在淬火温度下保温时间为30-40min;
[0021]
所述轮辋喷水冷却,使轮辋内部金属以2℃/s~5℃/s的冷却速度加速冷却到400-500℃即停止喷水。
[0022]
所述回火处理是指:在470-500℃回火处理4.0-5.0小时。
[0023]
本发明生产的车轮,车轮踏面组织为铁素体+珠光体,踏面下10mm处晶粒度11-12级;踏面下10mm处析出v(c,n)中v含量占总v含量的比例为43-53%,充分发挥了v元素的析出强化和细晶强化作用,提高了车轮常规力学性能;车轮珠光体片层间距为115-130μm,片层间距细小即意味着车轮强度较高,对重载服役工况有利;
[0024]
车轮轮辋抗拉强度rm≥1185mpa、屈服强度rp
0.2
≥800mpa、延伸率a≥16%、断面收缩率z≥43%;常温冲击u5≥10j,-60℃冲击u
5,2
≥50j;断裂韧性≥ 49mpa
·m1/2
;常温下磨损率≤3.1
×
10-6
g/m;-60℃磨损率≤4.5
×
10-6
g/m;车轮磨耗限处硬度为336-345hbw,磨耗限处硬度极差≤4hbw。
[0025]
适用于30-45t轴重运行速度120km/h的铁道货运车辆。
[0026]
本发明设计思路及达到的效果如下:
[0027]
到目前为止,国内外货运/客运车轮用钢均为铁素体+珠光体组织的中、高碳碳素钢,具备这种组织的车轮在硬度水平相当时,具有最好的耐磨性,因此,本发明的车轮用钢具有铁素体+珠光体组织状态。
[0028]
c元素的主要作用是保证车轮钢获得高硬度、高强度及高耐磨性,但其含量过高将降低车轮的冲击韧性和塑性。世界范围内不同地区、不同标准车轮钢均为亚共析钢,因此本发明将c的范围确定为0.71-0.75%之间。
[0029]
si是铁素体形成元素。si既可以以固溶强化的方式提高铁素体的强度,又可以抑制高碳珠光体钢中析出网状碳化物。si是一个对铁素体进行置换固溶强化非常有效的元素,作用仅次于磷,但同时在一定程度上降低钢的韧度和塑性。一般都将si限制一定范围内。因此本发明将si的范围确定为0.30-0.35%。
[0030]
mn元素可以改变钢在凝固时所形成的氧化物的性质和形状。同时它与s有较大的亲合力,可以避免在晶界上形成低熔点的硫化物fes,而以具有一定塑性的mns存在,从而消除硫的有害影响,改善钢的热加工性能。mn具有固溶强化作用,从而提高铁素体和奥氏体的强度和硬度,虽然其固溶强化效果不及碳、磷和硅,但其对钢的延展性几乎没有影响。在铁素体-珠光体型钢中mn是唯一可使屈服强度增加又使冷脆转变温度变化最小的合金元素。mn/s比超过150,虽然能够提高车轮钢的塑性和韧性,但会增加过热敏感性和回火脆性倾向。因此本发明将mn含量的范围确定为0.82-0.90%,s含量的范围确定为0.006-0.015%。
[0031]
p元素是铁素体稳定化元素。p溶于铁素体,虽然能提高车轮钢的强度和硬度,但最大的害处是偏析严重,增加回火脆性,显著降低钢的塑性和韧性,导致车轮易在加工时脆裂。因此,本发明将p的含量控制在≤0.015%。
[0032]
v作为强碳化物形成元素,能够促使钢中细小弥散的碳化物、氮化物、碳氮化物的形成,并且碳氮化物具有较高的热稳定性,能够起到较好的钉扎作用,有效阻止位错的运动,提高车轮钢在制动等温度较高时服役的强度。v元素与c、 n元素结合形成的化合物,对钢的晶粒细化和沉淀强化均有贡献。晶粒细化是唯一能同时提高钢的屈服强度和韧性(降低韧-脆转变温度)的强韧化机制。但v 含量过高时,会导致车轮钢奥氏体晶粒粗大,降低车轮钢综合力学性能。因此,本发明将v的含量设定为0.05-0.10%。
[0033]
n原子在钢中主要是以间隙原子的形式占据奥氏体点阵的八面体间隙位置,能够起到明显的固溶强化作用;同时,n在奥氏体中能够增加自由电子的浓度,导致面心立方晶格点阵中电子能增加,提高原子间金属键的结合力,从而提高了组织的稳定性和材料的强度。但n元素含量过高对车轮钢塑韧性不利,因此本发明将n的含量设定为0.0060-0.0100%。
[0034]
cr是碳化物形成元素。cr在铁内扩散移动比较缓慢,同时cr也降低碳的扩散速率,cr含量增加,使等温曲线向右移动,延长相变孕育期,降低临界冷却速率,提高淬透性。同时,在调质过程中,cr元素的存在可以增强钢的回火稳定性。另外,cr元素可以与c形成碳化物洗出,增强钢的强度和耐磨性。但 cr元素含量较高时,会导致碳化物粗化,降低钢的伸长率和断面收缩率。因此,本发明将cr的含量控制在0.22-0.27%。
[0035]
ni作为强烈的形成奥氏体和扩大奥氏体相区的元素。ni可以使c曲线右移, ni提高γ
→
α相变形核功,提高γ、α两相自由能差而降低临界转变温度。ni 可以降低钢中各元素的扩散速率,而延缓奥氏体分解转变,从而提高钢的淬透性。ni可以显著增强车轮钢的抗疲劳性,并且可提高车轮钢的低温韧性。一定量的ni元素可以通过强化铁素体,细化珠光体,进而来增强车轮钢的强度,同时还能保证车轮钢的塑韧性但是ni元素含量过高会降低c、n元素在钢基体中的溶解度,从而降低车轮钢的力学性能。因此,本发明将ni的含量控制在 0.20-0.27%。
[0036]
本发明淬火加热过程中先将车轮以20-25℃/min速度加热至500-550℃,然后快速加热至淬火温度并保温,保温完成后进行淬火。本发明采用的快速加热热处理包括快速加热+淬火+回火工艺。本发明采用快速加热热处理工序为:首先将车轮以20-25℃/min的速度加热至500-550℃,保温5-15min。这一加热阶段温度最高不能超过550℃,这是因为冷态车轮在550℃以下尚未进入塑性状态,若快速加热至较高温度,车轮本身产生加热裂纹的风险增加,容易造成质量损失。而后使车轮以30-35℃/min的速度加热至820-880℃,保温30-40min。这一加热阶段可以进行快速加热,这是因为500℃以上快速加热时不存在产生加热裂纹的可能性,而且对奥氏体的晶粒结构产生有利影响。实验表明,对车轮钢进行快速连续加热,可以使奥氏体形成温度升高,从而使奧氏体形核速度和长大速度之比增大,有利于获得细晶粒奥氏体,并且晶粒大小非常均匀;通过后续淬火可以得到具有较细片层间距的p+f微观结构;保温的目的是车轮整体温度均匀性,保温结束后出炉,快速加热热处理工艺的淬火加热总时间为80-110min,与常规加热工艺时间2.5-3.0h相比,加热总时间缩短至少22%以上,轮辋喷水冷却,使轮辋内部金属以2℃/s~5℃/s的冷却速度加速冷却到500℃以下,然后在470-500℃温度范围内回火处理4.0-5.0小时。
[0037]
本发明提供一种铁道矿山及铁道货运用高碳高韧性重载车轮钢及有效提高车轮强度及韧性的车轮生产方法。本发明车轮相比传统aar-c车轮钢,不仅轮辋机械性能水平更
高,能够显著提高车轮强度,有效增强了重载服役条件下车轮耐磨性能,而且提高车轮韧性,增强了服役条件下车轮抗断裂能力,车轮设计安全冗余更大,为将来重载条件下强度及韧性要求更高的铁道矿山及铁道货运用车轮研发做技术储备。
附图说明
[0038]
图1热处理工艺示意图
[0039]
图2实施例1轮辋组织;
[0040]
图3实施例2轮辋组织;
[0041]
图4实施例3轮辋组织;
[0042]
图5对比例1轮辋组织;
[0043]
图6对比例2轮辋组织;
[0044]
图7对比例3轮辋组织;
[0045]
图8对比例4轮辋组织;
[0046]
图9对比例5轮辋组织;
[0047]
图10实施例及对比例车轮车轮踏面下10mm处晶粒度对比;
[0048]
图11实施例及对比例车轮踏面下10mm处析出v(c,n)中v含量占总v含量百分比对比;
[0049]
图12实施例及对比例车轮珠光体片层间距对比;
[0050]
图13实施例1轮辋硬度;5个点的测试硬度分别为338hbw、339hbw、336hbw、 336hbw、337hbw;
[0051]
图14实施例2轮辋硬度;5个点的测试硬度分别为343hbw、342hbw、342hbw、 341hbw、345hbw;
[0052]
图15实施例3轮辋硬度;5个点的测试硬度分别为340hbw、339hbw、340hbw、 342hbw、341hbw;
[0053]
图16对比例1轮辋硬度;5个点的测试硬度分别为329hbw、330hbw、332hbw、 336hbw、332hbw;
[0054]
图17对比例2轮辋硬度;5个点的测试硬度分别为335hbw、331hbw、332hbw、 334hbw、337hbw;
[0055]
图18对比例3轮辋硬度;5个点的测试硬度分别为339hbw、330hbw、333hbw、 331hbw、330hbw;
[0056]
图19对比例4轮辋硬度;5个点的测试硬度分别为332hbw、329hbw、333hbw、 332hbw、339hbw;
[0057]
图20对比例5轮辋硬度;5个点的测试硬度分别为331hbw、336hbw、338hbw、 338hbw、337hbw;
[0058]
图21实施例及对比例车轮磨耗限处硬度极差对比。
具体实施方式
[0059]
下面结合附图及实施例对本发明做详细的说明。
[0060]
实施例及对比例高碳高韧性重载车轮钢的化学成分质量分数如表1所示,表1没有
显示的余量为fe和不可避免的杂质。实施例级对比例均采用电炉冶炼经lf+rh精炼真空脱气后直接连铸成φ380mm的圆坯,经切锭、轧制后形成直径为980mm的车轮。
[0061]
表1实施例及对比例车轮化学成分(质量百分比%)
[0062][0063]
实施例1
[0064]
一种车轮生产方法,采用高碳高韧性重载车轮钢生产:将化学成分如表1 实施例1的钢水经过电炉炼钢工序、lf炉精炼工序、rh真空处理工序、圆坯连铸工序、切锭热轧工序、热处理工序、加工、成品检测工序而形成。所述的热处理工序为:首先将车轮以20℃/min的速度加热至520℃(冷态车轮在550℃以下尚未进入塑性状态,若快速加热,存在产生加热裂纹的风险,造成质量损失),在520℃温度下保温8min,再以30℃/min的速度加热至850
±
10℃(500℃以上进行快速加热,不存在出现加热裂纹的可能性),在850
±
10℃温度下保温 30min(快速加热可对奥氏体的晶粒结构产生影响。实验表明,对车轮钢进行快速连续加热,可以使奥氏体形成温度升高,从而使奧氏体形核速度和长大速度之比增大,有利于获得细晶粒奥氏体,并且晶粒大小非常均匀;通过后续淬火可以得到具有较细片层间距的p+f微观结构;保温的目的是车轮整体温度均匀性),保温结束后出炉(快速加热热处理工艺的淬火加热总时间为74min,与常规加热工艺时间2.5h相比,加热总时间缩短50%以上),轮辋喷水冷却,使轮辋内部金属以2℃/s~5℃/s的冷却速度加速冷却到500℃以下,然后在480
±
10℃回火处理4.5小时。
[0065]
如图2、5、8-12所示,本实施例制备的车轮轮辋金相组织与对比例1、对比例4、对比例5车轮组织均为细珠光体+少量铁素体,但本实施例中车轮组织更加细小均匀,晶粒度级别更高,珠光体片层间距更小,起钉扎作用的v含量占比更高。如图13、16、19-21所示,本实施例制备的车轮磨耗限处硬度明显高于对比例,而且磨耗限处硬度极差明显低于对比例。本实施例车轮机械性能如表2所示,由表2可以看出实施例1拉伸性能、冲击性能及断裂韧性均优于对比例1、对比例4、对比例5车轮。
[0066]
在微机控制滚动接触疲劳试验台上进行常温及低温滚动磨损对比试验,低温滚动磨损试验是在试验台上加装低温环境系统(由制冷机组、pid调控系统两部分构成,并通过低温腔体连接)。滚动磨损试验试样为40mm的盘形试样,均取自对比例和本实施例车轮轮辋相同部位处,试验结果见表3所示。由表3可知,实施例1车轮常温、-60℃低温磨损性能明显优于对比例1、对比例4、对比例5车轮。
[0067]
由此可见,实施例1在强度、硬度以及冲击性能比对比例1、对比例4、对比例5车轮优良的前提下,车轮磨耗限处硬度极差明显缩小,常温、-60℃低温耐磨性明显提高。
[0068]
实施例2
[0069]
一种车轮生产方法,采用高碳高韧性重载车轮钢生产:将化学成分如表1 实施例2的钢水经过电炉炼钢工序、lf炉精炼工序、rh真空处理工序、圆坯连铸工序、切锭热轧工序、热处理工序、加工、成品检测工序而形成。所述的热处理工序为:首先将车轮以23℃/min的速度加热至530℃(冷态车轮在550℃以下尚未进入塑性状态,若快速加热,存在产生加热裂纹的风险,从而造成质量损失),在530℃温度下保温5min,再以32℃/min的速度加热至870
±
10℃ (500℃以上进行快速加热,不存在出现加热裂纹的可能性),在870
±
10℃温度下保温35min(快速加热可对奥氏体的晶粒结构产生影响。实验表明,对车轮钢进行快速连续加热,可以使奥氏体形成温度升高,从而使奧氏体形核速度和长大速度之比增大,有利于获得细晶粒奥氏体,并且晶粒大小非常均匀;通过后续淬火可以得到具有较细片层间距的p+f微观结构;保温的目的是车轮整体温度均匀性),保温结束后出炉(快速加热热处理工艺的淬火加热总时间为74min,与常规加热工艺时间2.8h相比,加热总时间缩短50%以上),轮辋喷水冷却,使轮辋内部金属以2℃/s~5℃/s的冷却速度加速冷却到500℃以下,然后在490
±ꢀ
10℃回火处理4.0小时。
[0070]
如图3、6、8-12所示,本实施例制备的车轮轮辋金相组织与对比例2、对比例4、对比例5车轮组织均为细珠光体+少量铁素体,但本实施例中车轮组织更加细小均匀,晶粒度级别更高,珠光体片层间距更小,起钉扎作用的v含量占比更高。如图14、17、19-21所示,本实施例制备的车轮磨耗限处硬度明显高于对比例,而且磨耗限处硬度极差明显低于对比例。本实施例车轮机械性能如表2所示,由表2可以看出实施例2拉伸性能、冲击性能及断裂韧性均优于对比例2、对比例4、对比例5车轮。
[0071]
在微机控制滚动接触疲劳试验台上进行常温及低温滚动磨损对比试验,低温滚动磨损试验是在试验台上加装低温环境系统(由制冷机组、pid调控系统两部分构成,并通过低温腔体连接)。滚动磨损试验试样为40mm的盘形试样,均取自对比例和本实施例车轮轮辋相同部位处,试验结果见表3所示。由表3可知,实施例2车轮常温、-60℃低温磨损性能明显优于对比例2、对比例4、对比例5车轮。
[0072]
由此可见,实施例2在强度、硬度以及冲击性能比对比例2、对比例4、对比例5车轮优良的前提下,车轮磨耗限处硬度极差明显缩小,常温、-60℃低温耐磨性明显提高。
[0073]
实施例3
[0074]
一种车轮生产方法,采用高碳高韧性重载车轮钢生产:将化学成分如表1 实施例3的钢水经过电炉炼钢工序、lf炉精炼工序、rh真空处理工序、圆坯连铸工序、切锭热轧工序、热处理工序、加工、成品检测工序而形成。所述的热处理工序为:首先将车轮以25℃/min的速度加热至540℃(冷态车轮在550℃以下尚未进入塑性状态,若快速加热,存在产生加热裂纹的风险,从而造成质量损失),在540℃温度下保温10min,再以30℃/min的速度加热至830
±
10℃ (500℃以上进行快速加热,不存在出现加热裂纹的可能性),在830
±
10℃温度下保温30min(快速加热可对奥氏体的晶粒结构产生影响。实验表明,对车轮钢进行快速连续加热,可以使奥氏体形成温度升高,从而使奧氏体形核速度和长大速度之比增大,有利于获得细晶粒奥氏体,并且晶粒大小非常均匀;通过后续淬火可以得到具有较细片层间距的p+f微观结构;保温的目的是车轮整体温度均匀性),保温结束后出炉(快速加热热处理工艺的淬火加热总时间为71min,与常规加热工艺时间2.5h相比,加热总时间缩短50%以上),轮辋喷水冷却,使轮辋内部金属以2℃/s~5℃/s的冷却速度加速冷却到500℃以下,然后在490
±ꢀ
10℃回火处理4.0小时。
[0075]
如图4、7-12所示,本实施例制备的车轮轮辋金相组织与对比例3、对比例 4、对比例5车轮组织均为细珠光体+少量铁素体,但本实施例中车轮组织更加细小均匀,晶粒度级别更高,珠光体片层间距更小,起钉扎作用的v含量占比更高。如图15、18-21所示,本实施例制备的车轮磨耗限处硬度明显高于对比例,而且磨耗限处硬度极差明显低于对比例。本实施例车轮机械性能如表2所示,由表2可以看出实施例3拉伸性能、冲击性能及断裂韧性均优于对比例2、对比例4、对比例5车轮。
[0076]
在微机控制滚动接触疲劳试验台上进行常温及低温滚动磨损对比试验,低温滚动磨损试验是在试验台上加装低温环境系统(由制冷机组、pid调控系统两部分构成,并通过低温腔体连接)。滚动磨损试验试样为40mm的盘形试样,均取自对比例和本实施例车轮轮辋相同部位处,试验结果见表3所示。由表3可知,实施例3车轮常温、-60℃低温磨损性能明显优于对比例2、对比例4、对比例5车轮。
[0077]
由此可见,实施例3与在强度、硬度以及冲击性能比对比例2、对比例4、对比例5车轮优良的前提下,车轮磨耗限处硬度极差明显缩小,常温、-60℃低温耐磨性明显提高,发明取得了预期效果。
[0078]
对比例1:
[0079]
对比例1车轮与实施例1车轮为同一炉号,成分完全一致。其他生产工序一致,仅在热处理工序的淬火加热阶段存在不同。对比例1车轮随炉升温至850
ꢀ±
10℃后保温,总加热时间2.5h,而后轮辋喷水冷却,然后在480
±
10℃回火处理4.5小时。
[0080]
对比例2:
[0081]
对比例2车轮与实施例2车轮为同一炉号,成分完全一致。其他生产工序一致,仅在热处理工序的淬火加热阶段存在不同。对比例2车轮随炉升温至870
ꢀ±
10℃后保温,总加热时间2.8h,而后轮辋喷水冷却,然后在490
±
10℃回火处理4.0小时。
[0082]
对比例3:
[0083]
对比例3车轮与实施例3车轮为同一炉号,成分完全一致。其他生产工序一致,仅在热处理工序的淬火加热阶段存在不同。对比例3车轮随炉升温至830
ꢀ±
10℃后保温,总加热时间2.5h,而后轮辋喷水冷却,然后在490
±
10℃回火处理4.0小时。
[0084]
对比例4:
[0085]
对比例4车轮成分见表1,为传统aar-c成分设计车轮钢。其他生产工序同实施例1一致,仅在热处理工序的淬火加热阶段存在不同。对比例4车轮随炉升温至850
±
10℃后保温,总加热时间3.0h,而后轮辋喷水冷却,然后在480
ꢀ±
10℃回火处理4.2小时。
[0086]
对比例5:
[0087]
对比例5车轮成分与对比例4车轮一致,为传统aar-c成分设计车轮钢。其他生产工序同实施例1一致,仅在热处理工序的淬火加热阶段存在不同。所述的热处理工序为:首先以25℃/min的速度加热至520℃保温10min,再以33℃ /min的速度加热至850
±
10℃保温38min(总加热时间为79min)出炉,轮辋喷水冷却,在480
±
10℃回火处理4.2小时。
[0088]
表2实施例及对比例车轮常规机械性能
[0089][0090][0091]
表3实施例及对比例车轮磨损性能
[0092][0093]
综上,本发明车轮相比传统aar-c车轮钢及传统热处理工艺生产的车轮,不仅轮辋机械性能水平更高,能够显著提高车轮强度,有效增强了重载服役条件下车轮耐磨性能,而且提高车轮韧性,增强了服役条件下车轮抗断裂能力,车轮设计安全冗余更大。