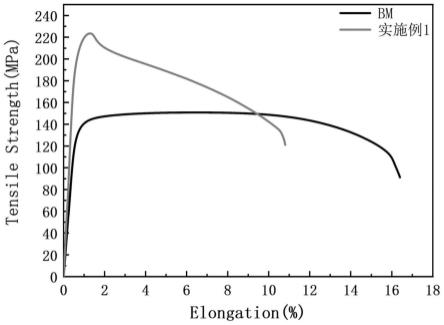
1.本发明涉及超细晶纯金属制备技术领域,尤其涉及一种纯金属低角度晶界强化的处理工艺。
背景技术:2.经济型纯铝是一种广泛使用的形变强化型金属材料。但是,形变强化会使纯铝的塑性和韧性恶化。为了实现良好的强韧性匹配,减小晶粒尺寸是唯一有效的途径。为此,工业中常用冷大塑性变形和低温退火处理来获得超细晶和纳米晶纯铝组织。目前已报道的大塑性变形方法有等通道挤压、高压扭转、重度冷轧、累积叠轧、多向锻造等。虽然这些方法可以获得超细晶、纳米晶纯铝,但是过度塑性变形不仅改变了初始材料尺寸,并且最终产品厚度或体积都很小,限制了其实际工业应用。
3.搅拌摩擦加工具有高应变速率、大应变特点的强热变形方法,通过动态再结晶机制实现晶粒细化,同时不改变材料的初始形状和尺寸。由于纯铝是一种高层错能材料,缺少元素偏聚和第二相粒子对晶界的钉扎作用,导致其在搅拌摩擦加工的热变形过程中极易发生动态回复和再结晶晶粒长大,因此难以得到晶粒尺寸小于1μm的超细晶组织。同时,完全再结晶的晶粒之间晶体学取向多以高角度晶界(相邻晶粒之间的晶体学取向差大于15
°
)为主,这种高角度晶界很容易迁移而使晶粒发生长大,导致强度和组织热稳定性降低。例如,专利cn109735731a提出了一种基于搅拌摩擦加工制备超细晶铝合金的方法。该方法采用了预先连续挤压和多道次搅拌摩擦加工的方式,同时又配合在线冷却来防止晶粒长大。该种方法工艺复杂,加工周期相对较长。更重要的是所采用的加工参数使得热输入较高,等效应变小,由于完全再结晶转变使得组织中高角度晶界比例高,而低角度晶界(相邻晶粒之间的晶体学取向差小于15
°
)比例很低;此外,尽管采用了在线冷却措施来抑制再结晶晶粒长大,但是外部冷却受热传导速率限制,很难获得小于1μm的晶粒尺寸,结果是被加工纯铝的强度和热稳定性均不高。
技术实现要素:4.针对上述背景技术中存在的问题,本发明提供一种纯金属低角度晶界强化的处理工艺。
5.为实现上述目的,本发明采取的技术方案为:
6.本发明提供一种纯金属低角度晶界强化的处理工艺,包括如下步骤:
7.将冷轧纯金属板材进行搅拌摩擦加工;其中,所述搅拌摩擦加工的转速为1000~2500rpm,所述搅拌摩擦加工的行进速度为3000~7000mm/min。
8.在某些具体的实施方式中,所述搅拌摩擦加工的转速为1000rpm、1500rpm、2000rpm、2500rpm或它们之间的任意转速。
9.在某些具体的实施方式中,所述搅拌摩擦加工的行进速度为3000mm/min、4000mm/min、5000mm/min、6000mm/min、7000mm/min或它们之间的任意转速。
10.在本发明的技术方案中,所述低角度晶界为相邻晶粒之间的晶体学取向差小于等于5~15
°
,例如为6
°
、8
°
、10
°
、12
°
或14
°
。
11.作为优选地实施方式,所述冷轧纯金属板材的冷轧度为30~80%,例如为40%、50%、60%、70%或80%。
12.作为优选地实施方式,所述冷轧纯金属板材的厚度为1~3mm,过高或过低均不利于获得低角度晶界的组织。
13.作为优选地实施方式,所述搅拌摩擦加工采用通用型搅拌摩擦加工设备;
14.优选地,所述搅拌摩擦加工中,搅拌头的倾角为1~2.5
°
;
15.优选地,所述搅拌摩擦加工中,轴肩的下压量为0.1~0.15mm。
16.作为优选地实施方式,所述通用型搅拌摩擦加工设备的搅拌头上的搅拌针长为0.9~2.9mm。
17.作为优选地实施方式,所述通用型搅拌摩擦加工设备的搅拌头上的搅拌针的根部直径为3~4mm;
18.优选地,所述通用型搅拌摩擦加工设备的搅拌头上的搅拌针的端部直径为2.7~3.7mm。
19.作为优选地实施方式,所述通用型搅拌摩擦加工设备的搅拌头的轴肩直径为8~12mm。
20.在某些具体的实施方式中,所述处理工艺还包括搅拌摩擦加工后的冷却,所述冷却为空冷或水冷。
21.作为优选地实施方式,所述纯金属为高层错能纯金属,优选为纯铝、纯铜或纯铁。
22.在本发明的技术方案中,经过上述纯金属低角度晶界强化的处理工艺后的纯铝为超细晶纯铝,上述方法不仅适用于纯铝,也适用于其它高层错能纯金属,如纯铜、纯铁等。
23.上述技术方案具有如下优点或者有益效果:
24.本发明通过采用高转速和超高行进速度下对纯金属板材进行搅拌摩擦加工,显著降低加工区热输入,同时有效地提高加工区的等效应变,在室温下就可快速在组织中获得10~30%比例低角度晶界和块状超细晶纯铝,得到的超细晶纯铝的粒径可达到0.5~1μm,这是现有技术中采用低转速以及低行进速度下的搅拌摩擦加工无法实现的效果。本发明通过上述处理工艺得到的纯铝,其较高比例的低角度晶界带来的强化效果,使得加工区组织不仅具有良好的强韧性匹配,使屈服强度和组织热稳定性显著提升,还具有好的组织热稳定性,具有潜在的工业应用价值。
附图说明
25.图1为本发明实施例1-2中搅拌摩擦加工设备的结构示意图。
26.图2为本发明实施例1-2中搅拌摩擦加工处理的过程示意图。
27.图3为本发明实施例1中搅拌摩擦加工处理后的纯铝的tem明场组织形貌和晶粒大小统计图。
28.图4为本发明实施例2中搅拌摩擦加工处理后的纯铝的tem明场组织形貌和晶粒大小统计图。
29.图5为本发明实施例1中搅拌摩擦加工处理后的纯铝的ipf图和晶界分布统计图。
30.图6为本发明实施例2中搅拌摩擦加工处理后的纯铝的ipf图和晶界分布统计图。
31.图7为本发明实施例1中搅拌摩擦加工处理后的纯铝的拉伸性能图。
32.图8为本发明实施例2中搅拌摩擦加工处理后的纯铝的拉伸性能图。
33.图9为本发明实施例1中搅拌摩擦加工处理后的纯铝的组织热稳定性曲线。
具体实施方式
34.下述实施例仅仅是本发明的一部分实施例,而不是全部的实施例。因此,以下提供的本发明实施例中的详细描述并非旨在限制要求保护的本发明的范围,而是仅仅表示本发明的选定实施例。基于本发明的实施例,本领域技术人员在没有作出创造性劳动的前提下所获得的所有其他实施例,都属于本发明的保护范围。
35.在本发明中,若非特指,所有的设备和原料等均可从市场购得或是本行业常用的。下述实施例中的方法,如无特别说明,均为本领域的常规方法。
36.下述实施例中,实施例1-2中采用的搅拌摩擦加工处理设备为通用型搅拌摩擦加工设备,结构图如图1所示,图中,1为搅拌头的卡持端,2为搅拌头的轴肩,3为搅拌针(a为搅拌针的根部,b为搅拌针的端部)。
37.实施例1:
38.本实施例中,待处理的母材选用3mm厚的60%冷轧纯铝板,去除表面氧化膜后固定在通用型搅拌摩擦加工设备工作台上,选用的常规搅拌头为:搅拌针根部直径4mm,端部直径3.7mm,针长2mm,轴肩直径10mm,加工过程如图2所示(图2中,4为加工区,5为待加工板材,θ为搅拌头的倾角),搅拌头的倾角保持2.5
°
,下压量0.1mm。
39.本实施例中,搅拌摩擦加工工艺参数为:搅拌头旋转速度1200r/min,行进速度6000mm/min,搅拌摩擦加工处理完成后,自然冷却。
40.通过tem技术和ebsd技术对该参数下的加工区试样进行观察,得到tem明场组织形貌和晶粒大小统计图(见图3),ipf图和晶界分布统计图(见图5),从图中可以看出,1200r/min-6000mm/min的处理参数,得到了平均晶粒尺寸0.58μm,低角度晶界占比30.74%的超细晶纯铝组织。经过拉伸性能测试,如图7所示,可以看出采用本发明提供的方法制得超细晶纯铝拉伸强度表现优异(图7中,bm为完全退火态组织)。
41.对超细晶纯铝组织进行热稳定性研究:将上述参数下得到的加工区试样分别在100℃、150℃、200℃、250℃、300℃下保温15min或45min后,对其平均硬度进行统计,如图9所示(其中,横坐标“nz”为未进行热处理的初始状态;横坐标“100-45”表示100℃下保温45min,其余同理),从图中可以看出采用本发明提供的方法制得的超细晶纯铝在250℃时仍保持了良好的热稳定性,这是由于本发明提供的方法制得的试样中存在着较高比例的低角晶界所致。
42.实施例2
43.本实施例中,待处理的母材选用3mm厚的60%冷轧纯铝板,去除表面氧化膜后固定在通用型搅拌摩擦加工设备工作台上,选用的常规搅拌头与实施例1一致,为:搅拌针根部直径4mm,端部直径3.7mm,针长2mm,轴肩直径10mm,加工过程中的搅拌头倾角和下压量与实施例1一致。
44.本实施例中,搅拌摩擦加工工艺参数为:搅拌头旋转速度为1500r/min,行进速度
为6000mm/min,搅拌摩擦加工处理完成后,在室温下自然冷却。
45.通过tem技术和ebsd技术对该参数下的加工区试样进行观察,得到tem明场组织形貌和晶粒大小统计图(见图4),ipf图和晶界分布统计图(见图6),从图中可以看出,1500r/min-6000mm/min的处理,得到了平均晶粒尺寸0.75μm,低角度晶界占比12.53%的超细晶纯铝组织。
46.经过拉伸性能测试,如图8所示(图8中,bm为完全退火态组织),可以看出采用本发明提供的方法制得超细晶纯铝拉伸强度表现优异。
47.对比例1
48.本发明还对3mm厚的60%冷轧纯铝板用与实施例1-2相同的通用型搅拌摩擦加工设备进行了其它旋转速度-行进速度参数组合的搅拌摩擦工艺处理,通过实验证明,转速在1000~2500rpm范围以外和行进速度在3000~7000mm/min以外的参数组合的处理,均不能获得完整致密的加工区形貌,例如,低转速-高行进速度处理下,不能成形,有沟槽缺陷;而低转速-低行进速度和高转速-低行进速度下处理过程中,会出现粘刀现象,不能成形。
49.以上所述仅是本发明的优选实施方式,应当指出:对于本技术领域的普通技术人员来说,在不脱离本发明原理的前提下,还可以做出若干改进和润饰,这些改进和润饰也应视为本发明的保护范围。