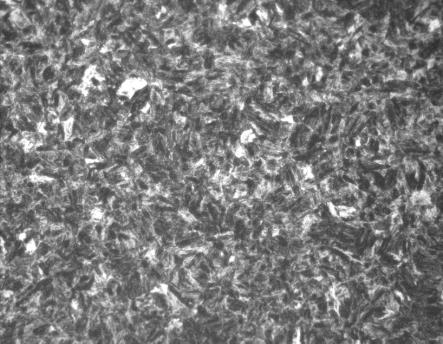
1.本发明属于连铸生产中厚板技术领域,具体涉及一种具有耐蚀耐磨性能的钢板及其制造方法。
背景技术:2.耐磨钢是在工程上应用比较广泛的一种特殊材料,由于其具有的良好的耐磨损性能,常被制成工程机械、矿山机械、煤矿机械、破碎机等机械零件,该类设备应用时其耐磨部件通常会与物料直接接触,从而产生磨损失效。而在耐磨部件接触的物料中,除了少部分干物料外,大部分物料处于湿润的腐蚀状态,从而给耐磨部件造成腐蚀损伤。严重时,耐磨部件会因腐蚀造成失效而使得制造的装备过早产生报废。此外,在耐磨部件在磨损过程中存在腐蚀时,腐蚀会加快磨损,磨损也会加快腐蚀,二者的叠加会进一步加速零部件的失效,从而造成严重的损失。在现有低合金耐磨钢板中,基本都只考虑了钢板的耐磨性能,而对于耐腐蚀性能却很少考虑,因此,需要研发一种能够承受腐蚀和磨损交叉作用的耐磨耐蚀合金钢。
3.对比文件1,专利“一种易焊接的具有耐蚀性能的nm360级耐磨钢板”(申请号:cn 104831191 a),此专利所生产的钢板虽然也具有耐蚀耐磨性能,但钢板的耐磨等级为nm360级别,-20冲击功仅为40j,不具有良好的低温冲击韧性,且文中也未提及钢板的不平度水平和耐大气腐蚀性能。
4.对比文件2,专利“一种具有耐蚀性的nm400级耐磨钢板的制备方法(申请号:cn 104818435 a),采用线淬火及在线回火工艺生产的一种种具有耐蚀性的nm400级耐磨钢板,钢板布氏硬度hbw≥370,抗拉强度≥1200mpa,-20冲击功仅为25j,不具有良好的低温冲击韧性,且文中也未提及钢板的不平度水平和耐大气腐蚀性能。
5.对比文件3,专利“具有优异低温韧性和焊接性能的耐腐蚀磨损钢板及其制备方法(申请号:cn 112267073 a,采用线淬火或离线淬火+回火,如采用离线淬火+回火生产周期较长,且成本相应增加,实施例中碳当量为0.54-0.59,碳当量较高,焊接性会较差,且文中也未提及钢板的不平度水平和耐大气腐蚀性能。
6.因此,需研发一种具有良好低温韧性、易焊接、板形良好的耐蚀耐磨钢板。
技术实现要素:7.本发明要解决的技术问题是提供一种具有耐蚀耐磨性能的钢板,同时本发明还提供了一种具有耐蚀耐磨性能的钢板的制造方法,通过合理成分、冶炼控制及轧制冷+热处理工艺配合,生产出一种具有良好低温韧性、易焊接、板形良好的耐蚀耐磨钢板。
8.为解决上述技术问题,本发明采取的技术方案是:一种具有耐蚀耐磨性能的钢板,所述钢板化学成分组成及其质量百分含量为:c:0.13-0.16%,si:0.20-0.40%,mn:0.9-1.10%,p≤0.012%,s≤0.003%,al:0.010-0.045%, cr:0.30-0.40%,mo:0.10-0.20%,ni:0.20-0.40,cu:0.10-0.30%,b:0.0015-0.0025,n≤
0.0040%,o≤0.0040%,h≤0.00015%,余量为fe和不可避免的杂质;钢板中碳当量cev≤0.45%,其中碳当量cev=c+mn/6+(cr+mo+v)/5+(ni+cu)/15;如上所述具有耐蚀耐磨性能的钢板,优选地,钢板中,按照化学成分以质量百分比计,还包括以下元素中的一种或几种:nb:0.00-0.020%,v:0.00-0.020%,ti:0.00-0.020%。
9.如上所述具有耐蚀耐磨性能的钢板,优选地,钢板中,板条马氏体组织的体积分数≥90%。
10.如上所述具有耐蚀耐磨性能的钢板,优选地,钢板的不平度≤5mm/m。
11.如上所述具有耐蚀耐磨性能的钢板,优选地,钢板的耐大气腐蚀指数为i,i=26.01(%cu)+3.88(%ni)+1.20(%cr)+1.49(%si)+17.28(%p)-7.29(%cu)(%ni)-9.10(% ni)(% p)-33.39(%cu)2,且i≥6.2。
12.如上所述具有耐蚀耐磨性能的钢板,优选地,钢板的钢板的抗拉强度为1250-1320mpa,180
°
弯曲实验d=4a合格,布氏硬度为405-412hbw,-40℃冲击功≥60j ,-60℃冲击功≥50j。
13.本发明还提供一种上述具有耐蚀耐磨性能的钢板的制造方法,包括如下步骤:1、冶炼:铁水预处理
→
转炉冶炼
→
lf炉处理
→
rh真空处理
→
连铸;将钢水经转炉、精炼炉脱磷脱硫,rh真空脱气严格控制气体的含量,其质量百分含量为:n≤0.0040%,o≤0.0040%,h≤0.00015%;连铸过程过热度控制为10-20℃,采用二冷电磁搅拌和凝固末端轻压下手段,铸坯浇铸过程中保持恒拉速,非金属夹杂a/b/c/d≤1.0级,a+b+c+d≤2.0级;2、加热:采用步进梁式加热炉,均热段温度控制在1160-1240℃,铸坯在加热炉内的总加热时间为260-320min,保证铸坯温度均匀;3、轧制及冷却:采用再结晶区+未再结晶区两阶段控轧工艺,粗轧开轧温度为≥1010℃,钢坯展宽完毕后纵轧最后两道次单道次压下率≥20%。精轧开轧温度860-920℃,终轧温度为810-850℃,保证精轧阶段累计压下率≥60%,轧制完成后进行空冷;4、热处理:淬火温度为890-910℃,升温速率3.0min/mm,在炉时间36-75min,淬火方式为水淬。
14.本发明的优点在于:1、通过合理的成分体系设计,通过最优的轧制及热处理工艺,提供一种具有耐蚀耐磨性能的钢板,钢板中的组织主要为板条马氏体,钢板的抗拉强度为1250-1320mpa,180
°
弯曲实验d=4a合格,布氏硬度为405-412hbw,-40℃冲击功≥60j ,-60℃冲击功≥50j;2、所生产的钢板碳当量cev≤0.45%,碳当量低,钢板具有良好的焊接性能;3、所生产的钢板除具有耐蚀耐磨性能外,还具有耐大气腐蚀性能,其中大气腐蚀指数为i≥6.2;4、所生产的耐蚀耐磨性能钢板厚度为12-25mm,钢板板形良好,不平度可达到≤5mm/m;5、所生产的耐蚀耐磨性能钢板淬火后无需回火,减少生产周期,降低生产成本。
附图说明
15.图1 实施例1一种具有耐蚀耐磨性能的钢板1/4典型微观组织。
具体实施方式
16.为了更好的解释本发明,以便于理解,下面结合附图,通过具体实施方式,对本发明作详细描述。
17.本发明实施例提供一种具有耐蚀耐磨性能的钢板,其化学成分按质量百分比计包括:c:0.13-0.16%,si:0.20-0.40%,mn:0.9-1.10%,p≤0.012%,s≤0.003%,al:0.010-0.045%, cr:0.30-0.40%,mo:0.10-0.20%,ni:0.20-0.40,cu:0.10-0.30%,b:0.0015-0.0025,n≤0.0040%,o≤0.0040%,h≤0.00015%,余量为fe和不可避免的杂质。
18.钢板中碳当量cev≤0.45%,其中,碳当量cev=c+mn/6+(cr+mo+v)/5+(cu+ni)/15。其中,cev代表钢板中的碳当量,c代表钢板中c元素的质量百分比,mn代表钢板中mn元素的质量百分比,cr代表钢板中cr元素的质量百分比,mo代表钢板中mo元素的质量百分比,v代表钢板中v元素的质量百分比,cu代表钢板中cu元素的质量百分比,ni代表钢板中ni元素的质量百分比。
19.钢板的耐大气腐蚀指数i≥6.2,其中,耐大气腐蚀指数为i=26.01(%cu)+3.88(%ni)+1.20(%cr)+1.49(%si)+17.28(%p)-7.29(%cu)(%ni)-9.10(% ni)(% p)-33.39(%cu)2,其中i代表钢板的耐大气腐蚀指数, cu代表钢板中cu元素的质量百分比,ni代表钢板中ni元素的质量百分比,cr代表钢板中cr元素的质量百分比,si代表钢板中si元素的质量百分比,p代表钢板中p元素的质量百分比。
20.该钢板中,各元素组分在本发明中的作用为:c:c元素是耐磨钢的主要构成元素之一,可以起到强烈的固溶强化作用,以提高钢的硬度、强度及耐磨性。需要合理控制耐磨钢中的c元素的含量,在获得高强度、高硬度的同时也保证钢板的韧性、焊接性能以及折弯成型性能。c元素的含量若低于0.10%,钢材的硬度、强度及耐磨性无法得到保证,若高于0.24%,则钢材的韧性和焊接性能会随之下降,因此,在本实施例中c元素的含量优选控制为0.13~0.16%之间。
21.si:si元素固溶在铁素体和奥氏体中,用于提高它们的硬度和强度。然而si含量过高会导致钢的韧性急剧下降,且钢板加入较多的si元素容易引起钢板表面容易产生氧化铁皮,不利于钢板表面质量的控制。si元素的含量若低于0.2%,钢材的硬度和强度不足,若高于0.40%,则钢材的韧性急剧下降,因此,在本实施例中si元素的含量优选控制在0.20~0.40%之间。
22.mn:mn元素能够强烈增加钢的淬透性,降低马氏体转变温度和钢的临界冷却速度。然而mn元素含量较高时,容易导致铸坯中出现偏析和裂纹,降低钢板的力学性能,偏析会对钢板腐蚀磨损起着强烈的不利作用。mn元素的含量若低于0.90%,则无法降低马氏体转变温度和钢的临界冷却速度,若高于1.10%,则容易导致铸坯中出现偏析和裂纹,降低钢板的力学性能,因此,本实施例中mn元素的含量优选控制在0.90-1.10%之间。
23.p:p元素在奥氏体中的溶解度很小,通常是和fe元素、mn元素等产生共晶磷化物,且在晶界析出。p元素容易引起材料的热裂,降低材料的机械性能并对钢板的耐磨性有一定的损害,严重时甚至会在工作中断裂,应尽量降低钢板中p元素的含量。因此,本实施例中p元素的含量优选控制在0.012%以下。
24.s:s元素容易与mn元素生成条状的mns夹杂,进入溶渣并被带入钢坯和后续钢板中,对钢板的塑韧性及耐腐蚀性产生不利影响。需要严格控制s元素含量。因此,在本实施例
中s元素的含量优选控制在0.003%以下。
25.al:al元素具有脱氧作用,可以有效去除钢种的氧,另外,al元素还是重要的晶粒细化元素,对提高钢板冲击韧性具有积极作用。但al元素过多会导致钢水的流动性变差,影响拉速甚至造成无法浇铸。因此,本实施例中al元素的含量优选控制在0.010-0.045%之间;cr:cr元素是可以显著提高耐磨钢的淬透性,降低钢板中马氏体的转变温度和临界冷却转变速度,同时,cr元素还在抗腐蚀方面有明显作用。在钢板的生产过程中,经淬火处理后,cr元素会大部分溶入耐磨钢的奥氏体中,提高了耐磨钢的稳定性、屈服强度和抗腐蚀性能,同时也加快了碳化物在冷却时的析出,但cr元素含量过高会降低了钢的延伸率及冲击韧性。因此,本实施例中,cr元素的含量优选控制为0.30-0.40%之间。
26.mo:mo元素可以提高钢淬透性,另外还可以进一步提高钢的强度和耐磨性,因此,本实施例中,mo元素的含量优选控制为0.10-0.20%之间。
27.ni:ni元素是形成和稳定奥氏体的主要合金元素,当cr和ni元素复合添加时,可以成倍的提高钢的淬透性,确保厚规格钢板内部获得马氏体组织,以保证钢板具有足够高的硬度,同时可提高钢板芯部和表面机械性能的一致性,另外ni元素还可以提高钢的低温韧性及耐腐蚀性能。因此,本实施例中,ni元素的含量优选控制为0.20-0.40%之间。
28.cu:cu元素的可以钢板的抗大气腐蚀性能,与p元素配合使用时效果更为显著。同时,添加cu元素还可以略微提高钢板的高温抗氧化性能,改善钢液的流动性。但cu元素添加量较高时,钢坯在连铸时表面容易产生裂纹,并且钢板在热加工时容易开裂。因此,在本实施例中cu元素的含量优选控制在0.10-0.30%之间。
29.b:微量的b元素可显著的提高钢板的淬透性,b元素吸附于奥氏体晶界上,能够降低晶间能量,抑制铁素体形成并强化晶界,从而提高钢的抗蠕变性能与持久强度。但b元素含量较高时,b元素与钢中残余氮、氧化合形成稳定的夹杂物,对钢板的性能有恶化作用。因此,本实施例中b元素含量优选控制在0.0015-0.0025%之间。
30.nb、v、ti:nb元素、v元素、ti元素是强碳化合物形成元素,在热轧时,碳化物的应变诱导析出,有助于细化形变奥氏体的相变产物,提高钢的强度和韧性。但nb、v、ti 元素的加入量过多,碳化物会迅速粗化长大,影响钢板的韧性。因此,本实施例处于微合金化影响的考虑,nb、v、ti可以选择性地添加一种或几种,其含量优选控制为:nb:0.00-0.02%,v:0.00-0.02%,ti:0.00-0.02%。
31.具体地,钢板中,按照化学成分以质量百分比计,还包含以下元素中的一种或几种:nb:0.00-0.02%,v:0.00-0.02%,ti:0.00-0.02%。
32.具体地,钢板中,板条马氏体组织的体积分数≥90%。
33.具体地,钢板的抗拉强度为1250-1320mpa,180
°
弯曲实验d=4a合格,布氏硬度为405-412hbw,-40℃冲击功≥60j ,-60℃冲击功≥50j。
34.具体地,钢板的不平度≤5mm/m。
35.本实施例通过合理的成分体系设计,通过最优的轧制及热处理工艺,提供了一种具有耐蚀耐磨性能的钢板,该钢板具有碳当量低、低温韧性优良、耐大气腐蚀等特征。此外,钢板的制备方法简单,包括冶炼、连铸、轧制、淬火工序等,可广泛应用于磨损过程中伴随腐蚀的工况环境的机械零部件制造。
36.实施例1
一种具有耐蚀耐磨性能的钢板厚度为12mm,钢板化学成分组成及其质量百分含量为:c:0.13%,si:0.40%,mn:1.10%,p:0.010%,s:0.002%,al:0.010%, cr:0.31%,mo:0.20%,ni:0.20%,cu:0.30%,b:0.0018%,nb:0.015%,ti:0.010%,n:0.0040%,o:0.0030%,h:0.00010%,余量为fe和不可避免的杂质,碳当量cev=0.45%,耐大气腐蚀指数i=6.26;钢板的生产步骤及工艺参数为:1、冶炼:铁水预处理
→
转炉冶炼
→
lf炉处理
→
rh真空处理
→
连铸;将钢水经转炉、精炼炉脱磷脱硫,rh真空脱气严格控制气体的含量,连铸过程过热度控制为12℃,采用二冷电磁搅拌和凝固末端轻压下手段,铸坯浇铸过程中保持恒拉速,非金属夹杂a类0.5级,b类0级,c类0级,d类1.0级。
37.2、加热:采用步进梁式加热炉,均热段温度控制在1160℃,铸坯在加热炉内的总加热时间为260min,保证铸坯温度均匀。
38.3、轧制及冷却:采用再结晶区+未再结晶区两阶段控轧工艺,粗轧开轧温度为1080℃,钢坯展宽完毕后纵轧最后两道次单道次压下率分别为22%、27%。精轧开轧温度900℃,终轧温度为840℃,精轧阶段累计压下率为80%,轧制完成后进行空冷。
39.4、热处理:淬火温度为890℃,升温速率3.0min/mm,在炉时间36(3*12)min,淬火方式为水淬;上述方法制备得到的钢板中,板条马氏体组织的体积分数为95%;钢板的拉伸强度为1310mpa,180
°
弯曲实验d=4a合格,硬度为412hbw,-40℃冲击功为72j ,-60℃冲击功为65j;钢板不平度为3mm/m。
40.如图1 为实施1所生产的一种具有耐蚀耐磨性能的钢板的金相照片,显微组织主要为板条马氏体,板条马氏体间存在少量粒状贝氏体或粒状渗碳体,板条内存在小尺寸断续的渗碳体组织,这种小尺寸断续分布的渗碳体对提高材料的塑性、韧性以及冷成形性能具有重要作用。
41.实施例2一种具有耐蚀耐磨性能的钢板厚度为16mm,钢板化学成分组成及其质量百分含量为:c:0.15%,si:0.30%,mn:0.9%,p:0.012%,s:0.002%,al:0.030%, cr:0.40%,mo:0.15%,ni:0.30%,cu:0.28%,b:0.0015%,nb:0.020%,n:0.0030%,o:0.0040%,h:0.00010%,余量为fe和不可避免的杂质,碳当量cev=0.45%,耐大气腐蚀指数i=6.32;钢板的生产步骤及工艺参数为:1、冶炼:铁水预处理
→
转炉冶炼
→
lf炉处理
→
rh真空处理
→
连铸;将钢水经转炉、精炼炉脱磷脱硫,rh真空脱气严格控制气体的含量,连铸过程过热度控制为10℃,采用二冷电磁搅拌和凝固末端轻压下手段,铸坯浇铸过程中保持恒拉速,非金属夹杂a类0.5级,b类0级,c类0级,d类0.5级。
42.2、加热:采用步进梁式加热炉,均热段温度控制在1190℃,铸坯在加热炉内的总加热时间为280min,保证铸坯温度均匀。
43.3、轧制及冷却:采用再结晶区+未再结晶区两阶段控轧工艺,粗轧开轧温度为1100℃,钢坯展宽完毕后纵轧最后两道次单道次压下率分别为20%、25%。精轧开轧温度920℃,终轧温度为850℃,精轧阶段累计压下率为76%,轧制完成后进行空冷。
44.4、热处理:淬火温度为900℃,升温速率3.0min/mm,在炉时间48(3*16)min,淬火方
式为水淬;上述方法制备得到的钢板中,板条马氏体组织的体积分数为94%;钢板的拉伸强度为1250mpa,180
°
弯曲实验d=4a合格,硬度为408hbw,-40℃冲击功为68j ,-60℃冲击功为60j;钢板不平度为5mm/m。
45.实施例3一种具有耐蚀耐磨性能的钢板厚度为20mm,钢板化学成分组成及其质量百分含量为:c:0.14%,si:0.20%,mn:0.9%,p:0.008%,s:0.003%,al:0.038%, cr:0.35%,mo:0.10%,ni:0.40%,cu:0.29%,b:0.0020%,nb:0.018%,ti:0.014%,n:0.0030%,o:0.0030%,h:0.00010%,余量为fe和不可避免的杂质,碳当量cev=0.43%,耐大气腐蚀指数i=6.27;钢板的生产步骤及工艺参数为:1、冶炼:铁水预处理
→
转炉冶炼
→
lf炉处理
→
rh真空处理
→
连铸;将钢水经转炉、精炼炉脱磷脱硫,rh真空脱气严格控制气体的含量,连铸过程过热度控制为20℃,采用二冷电磁搅拌和凝固末端轻压下手段,铸坯浇铸过程中保持恒拉速,非金属夹杂a类1.0级,b类0.5级,c类0级,d类0.5级。
46.2、加热:采用步进梁式加热炉,均热段温度控制在1200℃,铸坯在加热炉内的总加热时间为295min,保证铸坯温度均匀。
47.3、轧制及冷却:采用再结晶区+未再结晶区两阶段控轧工艺,粗轧开轧温度为1080℃,钢坯展宽完毕后纵轧最后两道次单道次压下率分别为21%、23%。精轧开轧温度890℃,终轧温度为840℃,精轧阶段累计压下率为72%,轧制完成后进行空冷。
48.4、热处理:淬火温度为900℃,升温速率3.0min/mm,在炉时间60(3*20)min,淬火方式为水淬;上述方法制备得到的钢板中,板条马氏体组织的体积分数为97%;钢板的拉伸强度为1320mpa,180
°
弯曲实验d=4a合格,硬度为411hbw,-40℃冲击功为75j ,-60℃冲击功为67j;钢板不平度为1mm/m。
49.实施例4一种具有耐蚀耐磨性能的钢板厚度为22mm,钢板化学成分组成及其质量百分含量为:c:0.16%,si:0.30%,mn:0.92%,p:0.009%,s:0.002%,al:0.045%, cr:0.30%,mo:0.12%,ni:0.39%,cu:0.28%,b:0.0019%,nb:0.016%,n:0.0030%,o:0.0020%,h:0.00012%,余量为fe和不可避免的杂质,碳当量cev=0.44%,耐大气腐蚀指数i=6.31;钢板的生产步骤及工艺参数为:1、冶炼:铁水预处理
→
转炉冶炼
→
lf炉处理
→
rh真空处理
→
连铸;将钢水经转炉、精炼炉脱磷脱硫,rh真空脱气严格控制气体的含量,连铸过程过热度控制为11℃,采用二冷电磁搅拌和凝固末端轻压下手段,铸坯浇铸过程中保持恒拉速,非金属夹杂a类0.5级,b类0级,c类0级,d类0级。
50.2、加热:采用步进梁式加热炉,均热段温度控制在1210℃,铸坯在加热炉内的总加热时间为305min,保证铸坯温度均匀。
51.3、轧制及冷却:采用再结晶区+未再结晶区两阶段控轧工艺,粗轧开轧温度为1010℃,钢坯展宽完毕后纵轧最后两道次单道次压下率分别为25%、26%。精轧开轧温度860℃,终轧温度为820℃,精轧阶段累计压下率为68%,轧制完成后进行空冷。
52.4、热处理:淬火温度为905℃,升温速率3.0min/mm,在炉时间66(3*22)min,淬火方式为水淬;上述方法制备得到的钢板中,板条马氏体组织的体积分数为90%;钢板的拉伸强度为1310mpa,180
°
弯曲实验d=4a合格,硬度为406hbw,-40℃冲击功为80j ,-60℃冲击功为65j;钢板不平度为1mm/m。
53.实施例5一种具有耐蚀耐磨性能的钢板厚度为25mm,钢板化学成分组成及其质量百分含量为:c:0.14%,si:0.40%,mn:0.91%,p:0.009%,s:0.001%,al:0.025%, cr:0.40%,mo:0.15%,ni:0.40%,cu:0.22%,b:0.0025%,nb:0.015%,ti:0.012%,n:0.0030%,o:0.0030%,h:0.00015%,余量为fe和不可避免的杂质,碳当量cev=0.44%,耐大气腐蚀指数i=6.22;钢板的生产步骤及工艺参数为:1、冶炼:铁水预处理
→
转炉冶炼
→
lf炉处理
→
rh真空处理
→
连铸;将钢水经转炉、精炼炉脱磷脱硫,rh真空脱气严格控制气体的含量,连铸过程过热度控制为13℃,采用二冷电磁搅拌和凝固末端轻压下手段,铸坯浇铸过程中保持恒拉速,非金属夹杂a类0级,b类0.5级,c类0级,d类0级。
54.2、加热:采用步进梁式加热炉,均热段温度控制在1240℃,铸坯在加热炉内的总加热时间为320min,保证铸坯温度均匀。
55.3、轧制及冷却:采用再结晶区+未再结晶区两阶段控轧工艺,粗轧开轧温度为1090℃,钢坯展宽完毕后纵轧最后两道次单道次压下率分别为24%、26%。精轧开轧温度880℃,终轧温度为810℃,精轧阶段累计压下率为60%,轧制完成后进行空冷。
56.4、热处理:淬火温度为910℃,升温速率3.0min/mm,在炉时间75(3*25)min,淬火方式为水淬;上述方法制备得到的钢板中,板条马氏体组织的体积分数为98%;钢板的拉伸强度为1300mpa,180
°
弯曲实验d=4a合格,硬度为405hbw,-40℃冲击功为60j ,-60℃冲击功为50j;钢板不平度为2mm/m。
57.对比例1一种具有耐蚀耐磨性能的钢板厚度为20mm,钢板化学成分组成及其质量百分含量为:c:0.18%,si:0.30%,mn:1.15%,p:0.013%,s:0.004%,al:0.020%, cr:0.43%,mo:0.3%,b:0.0020%,nb:0.020%,n:0.0050%,o:0.0030%,h:0.00020%,余量为fe和不可避免的杂质,碳当量cev=0.52%,耐大气腐蚀指数i=1.19;钢板的生产步骤及工艺参数为:1、冶炼:铁水预处理
→
转炉冶炼
→
lf炉处理
→
rh真空处理
→
连铸;将钢水经转炉、精炼炉脱磷脱硫,rh真空脱气严格控制气体的含量,连铸过程过热度控制为25℃,采用二冷电磁搅拌和凝固末端轻压下手段,铸坯浇铸过程中保持恒拉速,非金属夹杂a类1.5级,b类0.5级,c类1.0级,d类0级。
58.2、加热:采用步进梁式加热炉,均热段温度控制在1250℃,铸坯在加热炉内的总加热时间为240min,保证铸坯温度均匀。
59.3、轧制及冷却:采用再结晶区+未再结晶区两阶段控轧工艺,粗轧开轧温度为1000℃,钢坯展宽完毕后纵轧最后两道次单道次压下率分别为18%、19%。精轧开轧温度930℃,终
轧温度为860℃,精轧阶段累计压下率为50%,轧制完成后进行空冷。
60.4、热处理:淬火温度为920℃,升温速率2.0min/mm,在炉时间40min,淬火方式为水淬;上述方法制备得到的钢板中,板条马氏体组织的体积分数为92%;钢板的拉伸强度为1220mpa,180
°
弯曲实验d=4a开裂,硬度为383hbw,-40℃冲击功为35j ,-60℃冲击功为22j;钢板不平度为6mm/m。
61.腐蚀实验:腐蚀实验采用溶液悬挂浸泡的方式进行,用尼龙绳将试样悬挂浸泡在溶液中,水浴箱温度保持35℃,烧杯中放置浓度为0.1mol/l的na2so4溶液,用naoh调节ph至8.5,用保鲜膜密封烧杯口,浸泡时间为72小时,每隔24小时更换一次溶液。腐蚀试样加工成6mm
×
25mm
×
55mm的长方体,试样上部中间用钻头钻直径为φ2.5mm的小孔,用于悬挂。用砂纸将试样六个面逐级打磨至600#,在用丙酮和无水乙醇清洗并吹干后,称取试样的质量作为初始质量,并测量试样的长宽高尺寸,计算试样的表面积。腐蚀实验采用失重法测定试样的平均腐蚀速度。实验结束后用清洗液清除表面残留的腐蚀液及腐蚀产物,称量腐蚀后的试样重量,计算腐蚀速率:c.r.(mm/y)= 365(d)*24(h)*w*10/[s*72(h)*d];w:重量减少(g);s:表面积(cm2);d:密度(g/cm3)。
[0062]
磨损实验:磨损实验采用干砂/橡胶轮磨损测试。
[0063]
磨损试样加工成6mm
×
25mm
×
55mm的长方体,经超声波丙酮清洗后称重并记录磨损前重量。干砂/橡胶轮磨损试验的具体参数设定为施加载荷130n,橡胶轮的转速为200r/ min,石英砂的大小为40-70目,转数为3000r和6000r。每次磨损后的试样分别用丙酮超声波清洗,并用电子天平精确称重,记录磨损失重数据。序号钢板厚度(mm)布氏硬度(hbw)腐蚀速率(mm/年)磨损失重(g)实施例1124120.2070.835实施例2164080.2230.828实施例3204110.2110.812实施例4224060.2310.801实施例5254050.2380.792对比例1203830.3680.848
[0064]
综上,本发明的优点在于:1、通过合理的成分体系设计,通过最优的轧制及热处理工艺,提供一种具有耐蚀耐磨性能的钢板,钢板中的组织主要为板条马氏体,钢板的抗拉强度为1250-1320mpa,180
°
弯曲实验d=4a合格,布氏硬度为405-412hbw,-40℃冲击功≥60j ,-60℃冲击功≥50j;2、所生产的钢板碳当量cev≤0.45%,碳当量低,钢板具有良好的焊接性能;3、所生产的钢板除具有耐蚀耐磨性能外,还具有耐大气腐蚀性能,其中大气腐蚀指数为i≥6.2;4、所生产的耐蚀耐磨性能钢板厚度为12-25mm,钢板板形良好,不平度可达到≤5mm/m;5、所生产的耐蚀耐磨性能钢板淬火后无需回火,减少生产周期,降低生产成本。