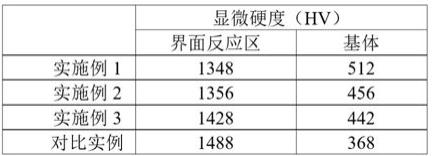
1.本发明涉及一种稀土附着碳化钨颗粒增强铁基表层复合材料的制备方法,属于复合材料制备领域。
背景技术:2.随着现代经济和工业的高速发展,对于材料的服役性能提出了更加严苛的要求,特别是在耐磨材料领域,由于单一的金属以及简单的金属合金材料已经很难适配现代工业要求。耐磨材料在现代生活和工业生产中起到了不可或缺的作用,比如街头随处可见的球墨铸铁井盖、大型破碎机的衬板以及工业生产所用的磨球等等。根据我国最新的统计数据因磨损消耗,造成材料的损失量是相当巨大的,而且这个数字还在与日俱增。因此成功研发性能优异的耐磨材料是科研工作者刻不容缓的任务。在矿山、建材、机械、冶金等邻域在广泛应用的激冷激热工况,不仅需要材料具有良好的耐磨性能,而且还需具备耐高温和抗冲击等性能。现在使用的耐热钢具有抗疲劳性能,但是在激冷激热条件下其耐磨性差影响了服役寿命,而且生产成本高也限制了其发展。因此结构、组织和性能可调控的陶瓷颗粒增强钢铁基复合材料成为了新的研究热点。颗粒增强金属基复合材料不仅具备金属基体良好的塑性和可成形性,而且还具有增强颗粒高强度、高硬度、高模量等特点。更重要的是其还具有耐磨性、耐蚀性、易于制备等优良特点。碳化钨颗粒与钢铁基体的润湿角几乎为零,因此其能够良好的冶金结合,形成良好的界面,这也极大的增强了其耐磨性。
3.中国发明专利(cn113106313a)发明一种稀土掺杂wc颗粒增强钢基复合材料的制备方法,属于钢基复合材料制备的技术领域。其制备方法是:把石蜡和碳化钨颗粒放在烧杯中水浴加热,使石蜡包裹在碳化钨表面,再与稀土球磨混粉。把表面附着有稀土的wc颗粒与钢粉混合,用粉末压片机压实后,在真空管式炉中烧结成型。稀土的附着提高了钢粉与陶瓷颗粒的润湿性,改善了复合界面的性能;但是此工艺烧结出的复合材料出现较多的微孔等缺陷,特别是碳化钨颗粒团聚分布的时候缺陷更加明显。
4.因此,本发明对于上述粉末冶金制备过程中致密性不好,容易出现孔洞等缺陷。通过碳化钨增强颗粒与不同粒度纯铁粉混合,并且加入稀土和合金元素的粉末,提高了基体和增强颗粒的润湿性以及复合界面的结合性。通过改变复合材料的结构,采用复合层、基材层、复合层的三层结构,基材层的加入减少了复合层在烧结过程致密性不好的比例,从而提高复合材料整体的致密性,并且在一定程度上节约了成本。
技术实现要素:5.本发明提供一种稀土附着碳化钨颗粒增强铁基表层复合材料的制备方法。采用细晶纯铁作为基材层;复合层由增强体、粗晶纯铁粉末、金属粉末构成,其中增强体是表面附着有稀土的碳化钨颗粒与细晶纯铁的混合粉末,先制备复合层:先把稀土包裹在碳化钨颗粒的表面,再把表面附着有稀土的碳化钨与细晶纯铁球磨混粉制得增强体粉末,最后再把增强体粉末、粗晶纯铁与金属粉末球磨得到复合层;其次再按照一定的质量分数依次按照
复合层-基材层-复合层铺入模具中,用粉末压片机压实后,放入真空管式炉中烧结成型。
6.本发明所述方法具体步骤如下:(1)将碳化钨、粘结剂、稀土粉末加入酒精以后进行湿法球磨,真空干燥条件下脱去粘结剂和酒精,筛去没有附着上的稀土粉末;其中,碳化钨的质量百分比为98.8%~99.4%,稀土粉末的质量百分比为0.6-1.2%。
7.(2)把表面附着有稀土元素的碳化钨颗粒与细晶纯铁球磨混粉,得到增强体粉末;增强体粉末中表面附着稀土的碳化钨质量分数为40%-60%,细晶纯铁的质量分数为40%-60%。细晶纯铁颗粒的粒径与所用球型铸造碳化钨颗粒的粒径接近两者能够均匀混合,而且不容易发生偏析和偏聚。
8.(3)把增强体粉末、粗晶纯铁粉末、金属粉末球磨混粉,得到复合层粉末;复合层粉末中,增强体的质量分数为50%-60%,金属粉末的质量分数为5%-10%,其余的为粗晶纯铁粉末。粗晶纯铁与增强体粉末能够发生冶金反应,使得碳化钨颗粒周围的界面结合强度提高。
9.(4)将复合层粉末、基材细晶纯铁粉、复合层粉末依次层铺,基材层位于两个复合层中间,用粉末压片机压实,得到预制坯,把预制坯放在真空管式炉中烧结成形,两个复合层粉末的质量分数相同,质量分数均为20%-40%,基材层的质量分数为20%-60%。
10.优选的,本发明所述碳化钨为60-80目的球型铸造碳化钨,细晶纯铁为60-100目,粗晶纯铁为40-60目。球型铸造碳化钨颗粒不容易产生应力集中(造成孔洞、裂纹等缺陷)。
11.优选的,本发明所述金属粉末为co、w、ni、cr中的一种或多种,其粒径10-60um。
12.优选的,本发明所述稀土粉末为nd、y、la粉末中的一种或多种按任意比例混合,稀土粉末粒径为50-75um。
13.优选的,本发明步骤(1)中粘结剂为水玻璃,加入量为碳化钨颗粒和稀土粉末总质量的1%。
14.优选的,本发明步骤(1)的球磨工艺为:正转60min-停转20min-反转60min-停转20min-正传60min-停转20min为一个周期,循环3个周期;转速为300-400r/min;正转后反转使得粉末充分混合,停转是为了防止长时间连续混粉球磨罐内温度升高。
15.优选的,本发明所述步骤(2)和(3)中的球磨工艺均为:正转60min-停转20min-反转60min,转速为200 r/min。
16.优选的,本发明所述步骤(1)中在70℃保温5-6h,去除酒精,在140℃保温11-12h,去除水玻璃。
17.优选的,本发明步骤(4)中压制的压力为550mpa,保压12-18min。
18.优选的,本发明步骤(3)中烧结过程中烧结温度为1350-1450℃,保温时间为60-80min,具体的升温过程为:室温至500℃,速率为≤5℃/min;500℃至800℃,速率为≤10℃/min;800℃至1000℃,速率为≤5℃/min;1000℃至1350℃,速率为≤3℃/min;1350℃至1450℃,速率为≤2℃/min,最后随炉冷却到室温。温度梯度升高使得复合材料每一层都充分的反应。
19.本发明的另一目的在于提供所述方法制备得到的稀土附着碳化钨颗粒增强铁基表层复合材料。
20.本发明的友益效果为:(1)本发明通过稀土元素的加入,改善了基体材料与碳化钨增强颗粒之间的润湿
性,细化了基体材料的晶粒,净化了晶界;稀土的加入扩大了基体与碳化钨的界面,改善两者的结合性能,从而提高了复合材料的力学性能。
21.(2)本发明附着有稀土的碳化钨颗粒先与粗晶纯铁粉混合后再与细晶纯铁粉混合,能够充分发挥各组元之间的多功能响应,以及不同组元间的协同和耦合效应。细晶纯铁颗粒的粒径与所用球型铸造碳化钨颗粒的粒径接近两者能够均匀混合,而且不容易发生偏析和偏聚。粗晶纯铁与增强体粉末能够发生冶金反应,使得碳化钨颗粒周围的界面结合强度提高,从而使得复合层的力学性能提高。
22.(3)本发明加入合金元素可以调控复合材料的组织和界面,并且可以促进碳化钨与基体之间的冶金结合,从而提高了复合材料的力学性能。
23.(4)本发明采用复合层-基材层-复合层三层结构,通过加入细晶纯铁基材层,可以降低存在致密性缺陷的复合层的比例,从而使得复合材料整体的致密性提高;而且此结构使得复合材料在具有表面耐磨的条件下,复合材料整体还具有良好的断裂韧性,使得该复合材料在冶金、机械等严苛的激冷极热条件下具有良好的应用前景。
附图说明
24.图1为本发明所述稀土附着碳化钨颗粒增强铁基表层复合材料的结构示意图;图2为未加稀土和合金元素复合层复合界面的扫描图;图3为实施例1附着稀土nd和加入合金元素cr的扫描图;图4为实施例1附着稀土nd和加入合金元素cr的线扫图;图5碳化钨附着稀土的sem图。
具体实施方式
25.下面列举具体实施方式,对本发明作进一步说明,但本发明的保护范围并不限于所述内容。
26.实施例1一种稀土附着碳化钨颗粒增强铁基表层复合材料的制备方法如下:(1)将60目球型铸造碳化钨颗粒、粘结剂、稀土nd粉末放入球磨罐中,并且加入酒精,抽真空通氩气后,球磨12h;其中粘接剂为水玻璃;其中球磨工艺为:正转60min-停转20min-反转60min-停转20min-正传60min-停转20min为一个周期,循环3个周期;转速为300r/min;在原料中,碳化钨的质量百分比为99.4%,稀土粉末的质量百分比为0.6%;水玻璃加入量为碳化钨颗粒和稀土粉末总质量的1%。
27.(2)然后取出在真空干燥箱中脱去酒精和水玻璃,在70℃保温5h,去除酒精,在140℃保温12h,去除水玻璃,并且筛去没有附着上的稀土粉末。
28.(3)把表面附着有稀土元素的碳化钨颗粒与60目的细晶纯铁球磨混粉,球磨时间为2h,得到增强体粉末;其中,增强体粉末中表面附着稀土碳化钨的质量分数为40%,其余的为细晶纯铁;球磨工艺为:正转60min-停转20min-反转60min,转速为200 r/min。
29.(4)把增强体粉末、40目粗晶纯铁、cr金属粉末球磨混粉,时间为2h,得到复合层粉末;其中复合层粉末中增强体的质量分数为50%,cr金属粉末的质量分数为5%,其余的为基体;球磨工艺同步骤(3)。
30.(5)预制压制:将制得的复合层粉末、基材60目细晶纯铁粉、复合层粉末依次层铺,基材层位于两个复合层中间,用粉末压片机压实;压力为550mpa,保压12min;其中复合层的质量分数均为20%,基材层的质量分数为60%,复合层的质量分数均为20%。
31.(6)把预制坯放在真空管式炉中烧结成形,烧结温度为1350℃,保温时间为60min,其中烧结过程为:室温至500℃,速率为5℃/min;500℃至800℃,速率为10℃/min;800℃至1000℃,速率为5℃/min;1000℃至1350℃,速率为3℃/min,最后随炉冷却到室温。
32.本实例制备的碳化钨颗粒增强铁基复合材料,经过观察三层截面的金相,用image-pro统计孔隙率,发现其孔隙率比整体构型的碳化钨铁基复合材料降低了50%,同时延展率从1%提高到了5%。
33.实施例2一种稀土附着碳化钨颗粒增强铁基表层复合材料的制备方法,具体包括以下步骤:(1)将70目球型铸造碳化钨颗粒、粘结剂、稀土y粉末放入球磨罐中,并且加入酒精,抽真空通氩气后,球磨10.5h;其中粘接剂为水玻璃;其中球磨工艺为:正转60min-停转10min-反转60min-停转10min-正传60min-停转10min为一个周期,循环3个周期;转速为350r/min;在原料中,碳化钨的质量百分比为99%,稀土粉末的质量百分比为1%;水玻璃加入量为碳化钨颗粒和稀土粉末总质量的1%。
34.(2)然后取出在真空干燥箱中脱去酒精和水玻璃,在70℃保温6h,去除酒精,在140℃保温12h,去除水玻璃,并且筛去没有附着上的稀土粉末;(3)把表面附着有稀土元素的碳化钨颗粒与80目的细晶纯铁球磨混粉,球磨时间为2h,得到增强体粉末;其中,增强体粉末中表面附着稀土碳化钨的质量分数为50%,其余的为细晶纯铁。球磨工艺为:正转60min-停转20min-反转60min,转速为250 r/min。
35.(4)把增强体粉末、50目粗晶纯铁、co和w的金属粉末球磨混粉,时间为2h,得到复合层粉末;其中复合层粉末中增强体的质量分数为55%,co、w金属粉末的质量分数为7.5%,其余的为基体,球磨工艺同步骤(3)。
36.(5)预制压制:将制得的复合层粉末、基材80目细晶纯铁粉、复合层粉末依次层铺,基材层位于两个复合层中间,用粉末压片机压实。压力为550mpa,保压12min;其中复合层的质量分数均为30%,基材层的质量分数为40%,复合层的质量分数均为30%。
37.(6)把预制坯放在真空管式炉中烧结成形,烧结温度为1400℃,保温时间为70min,其中烧结过程为:室温至500℃,速率为4℃/min;500℃至800℃,速率为8℃/min;800℃至1000℃,速率为3℃/min;1000℃至1350℃,速率为2℃/min,1350℃至1400℃,速率为2℃/min最后随炉冷却到室温。
38.作为对比制备了整体构型的碳化钨铁基复合材料,具体制备方法为:与实施例2的区别在于,将70目球型铸造碳化钨颗粒直接与80目的细晶纯铁球磨混粉,球磨时间为2h,球磨工艺为:正转60min-停转20min-反转60min,转速为250 r/min。然后预制压制,压力为550mpa,保压12min。最后把预制坯放在真空管式炉中烧结成形,烧结温度为1400℃,保温时间为60min,烧结工艺同实施例2。
39.本实例制备的碳化钨颗粒增强铁基复合材料,经过观察三层截面的金相,用image-pro统计孔隙率,发现其孔隙率比整体构型的碳化钨铁基复合材料降低了30%,同时
延展率从1%提高到了5%。
40.实施例3一种稀土附着碳化钨颗粒增强铁基表层复合材料的制备方法,具体包括以下步骤:(1)将80目球型铸造碳化钨颗粒、粘结剂、稀土la粉末放入球磨罐中,并且加入酒精,抽真空通氩气后,球磨9h;其中粘接剂为水玻璃;其中球磨工艺为:正转60min-停转5min-反转60min-停转5min-正传60min-停转5min为一个周期,循环3个周期;转速为400r/min;在原料中,碳化钨的质量百分比为98.8%,稀土粉末的质量百分比为1.2%;水玻璃加入量为碳化钨颗粒和稀土粉末总质量的1%。
41.(2)然后取出在真空干燥箱中脱去酒精和水玻璃,在70℃保温6h,去除酒精,在140℃保温11h,去除水玻璃,并且筛去没有附着上的稀土粉末;(3)把表面附着有稀土元素的碳化钨颗粒与100目的细晶纯铁球磨混粉,球磨时间为2h,得到增强体粉末。其中,增强体粉末中表面附着稀土碳化钨的质量分数为60%,其余的为细晶纯铁;球磨工艺为:正转60min-停转20min-反转60min,转速为300 r/min。
42.(4)把增强体粉末、60目粗晶纯铁、ni金属粉末球磨混粉,时间为2h,得到复合层粉末;增强体的质量分数为60%,ni金属粉末的质量分数为10%,其余的为基体,球磨工艺同步骤(3)。
43.(5)预制压制:将制得的复合层粉末、基材100目细晶纯铁粉、复合层粉末依次层铺,基材层位于两个复合层中间,用粉末压片机压实。压力为550mpa,保压12min;其中复合层的质量分数均为40%,基材层的质量分数为20%,复合层的质量分数均为40%。
44.(6)把预制坯放在真空管式炉中烧结成形,烧结温度为1450℃,保温时间为80min,其中烧结过程为:室温至500℃,速率为3℃/min;500℃至800℃,速率为6℃/min;800℃至1000℃,速率为3℃/min;1000℃至1350℃,速率为2℃/min;1350℃至1450℃,速率为1℃/min,最后随炉冷却到室温。
45.作为对比制备了整体构型的碳化钨铁基复合材料,具体制备方法为:与实施例3的区别在于,将80目球型铸造碳化钨颗粒直接与100目的细晶纯铁球磨混粉,球磨时间为2h,球磨工艺为:正转60min-停转20min-反转60min,转速为300r/min。然后预制压制,压力为550mpa,保压12min。最后把预制坯放在真空管式炉中烧结成形,烧结温度为1450℃,保温时间为60min,烧结工艺同实施例3。
46.本实例制备的碳化钨颗粒增强铁基复合材料,经过观察三层截面的金相,用image-pro统计孔隙率,发现其孔隙率比整体构型的碳化钨铁基复合材料降低了20%,同时延展率从1%提高到了5%。
47.对比实例与实施例1的区别在于,将60目球型铸造碳化钨颗粒直接与60目的细晶纯铁球磨混粉,球磨时间为2h,球磨工艺为:正转60min-停转20min-反转60min,转速为200 r/min。然后预制压制,压力为550mpa,保压12min。最后把预制坯放在真空管式炉中烧结成形,烧结温度为1350℃,保温时间为60min,烧结工艺同实施例1。
48.表1为复合层界面反应区和基体的显微硬度。
49.图2与图3对比,随着稀土和金属元素的加入复合层碳化钨与基体界面的宽度变宽;从表1可得,随着稀土的加入复合层基体的硬度升高从368hv升高到了442、456、512hv,界面反应区的硬度略有降低从1488hv降低到了1428、1356、1348hv,但其两者差值降低从1120hv降低到了986、900、836hv,复合层整体的耐磨性随之提高。