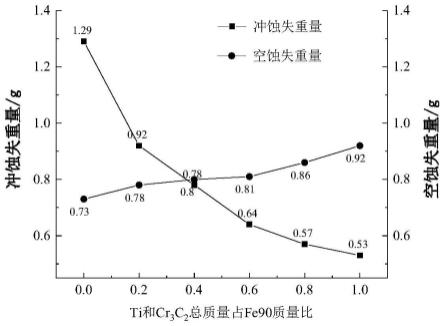
1.本发明属于机械磨蚀防护领域,涉及水力机械磨蚀防护,进一步涉及水力机械过流部件高抗冲蚀-空蚀-腐蚀涂层。
背景技术:2.对于运行于多泥沙河流的水力机械,由于受到空蚀、泥沙冲蚀的联合破坏,造成故障率升高、运行效率降低、使用寿命缩短,维护成本增加等问题。此外,长期的水下运行工况往往还会伴随着腐蚀问题的产生,这会进一步加剧水力机械过流部件的破坏。
3.为解决此类问题,尽管人们进行了诸多尝试,也取得了一系列成果。如在过流部件表面涂覆抗空蚀性能优异的聚氨酯高分子涂层,或采用热喷涂技术制备wc陶瓷涂层等,此类技术在一定程度上减缓了过流部件的破坏,有效提高了水力机械的使用寿命。然而,由于聚氨酯高分子类涂层的抗划伤性能差,抗冲蚀性能不佳,且涂层与基体的粘结力弱,只有20mpa左右,在服役过程易脱落失效;wc陶瓷涂层虽然有着良好的抗冲蚀性能,但抗空蚀能力表现不佳。
4.激光熔覆技术在增强金属基体硬度等性能方面已得到一定应用。例如公告号为cn108103502b的中国发明专利以基础金属粉末和硬质颗粒粉末(tin、tic、ticn、wc、sin、sic等)为激光熔覆粉末马氏体不锈钢刀剪进行激光熔覆处理,来对局部硬度进行改善处理。在不锈钢粉末中添加碳化物、氮化物等陶瓷硬质相作为熔覆粉末,通过各相间的优势互补,可以获得更优异的综合性能。
5.然而,此类方式也会存在一些弊端。首先,由于陶瓷相与金属基体的物理与化学性质存在差异,受制备工艺以及增强相类型等因素的制约,界面区易形成热力学不平衡体系,使得材料的韧性下降,恶化其抗空蚀性能。此外,陶瓷相的引入稀释了原有不锈钢涂层中耐蚀性元素的比例,导致涂层耐蚀性的下降。总之,水力机械过流部件受空蚀、冲蚀和腐蚀耦合破坏的影响,这种耦合破坏形式对激光熔覆技术提出了更高的要求。
技术实现要素:6.本发明的目的是提供一种高抗冲蚀-空蚀-腐蚀涂层,在提高涂层抗冲蚀的基础上而不降低涂层的抗空蚀性和耐腐蚀性,克服水力机械由于长期在水环境中工作,受空蚀、冲蚀和腐蚀耦合破坏的影响。
7.为了以上目的,本发明所采用的技术方案是:
8.一种高抗冲蚀-空蚀-腐蚀涂层,所述高抗冲蚀-空蚀-腐蚀涂层为fe90、ti粉和cr3c2通过激光熔覆形成的激光熔覆涂层;所述ti粉和cr3c2的总质量为fe90质量的20~100%,ti粉和cr3c2在所述激光熔覆过程中原位生成tic硬质相。
9.本发明的高抗冲蚀-空蚀-腐蚀涂层,cr3c2作为原位自生反应中的c源,和ti粉反应生成tic硬质相的同时,还可以向涂层中补充耐蚀性元素cr,所得涂层兼具抗冲蚀-空蚀-腐蚀的效果,提高水力机械过流部件的使用寿命。
10.优选地,ti粉和cr3c2的质量比为0.5~0.55。
11.优选地,fe90由以下质量分数的组分组成:c:0.13~0.16wt%,cr:12~14wt%,si:1.2~1.4wt%,b:1.55~1.65wt%;余量为铁。
12.所述激光熔覆包括以下步骤:
13.(1)将fe90粉末、ti粉和cr3c2粉末球磨混合,得到熔覆粉末;
14.(2)基体前处理后,在保护气氛下进行激光熔覆。
15.在激光高温作用下ti粉和cr3c2反应生成tic硬质颗粒而形成的原位自生涂层;原料来源广、制备工艺简单,对水力机械的改造成本低,适合大规模工业化推广应用。
16.优选地,步骤(1)中,fe90粉末的粒径为15~100μm,cr3c2粉末的粒径为15~100μm,ti粉的粒径为15~100μm。
17.优选地,步骤(1)中,球磨混合后在100~120℃下干燥0.5~3.0h。经烘干处理后的熔覆粉末能增加流动性,从而进一步改善送粉效果和激光熔覆效果。
18.优选地,步骤(2)中,激光熔覆工艺参数为:激光功率1.6~2.4kw,扫描速度3.6~4.8m/min,送粉速度30~40g/min,搭接率50%,熔覆层数2~5层。熔覆过程采用氩气保护,采用以上优选熔覆工艺参数,可以获得无气孔、裂纹等缺陷的复合涂层,涂层与基体之间呈冶金结合。
19.优选地,步骤(2)中,所述基体为水力机械过流部件,所述前处理包括去除表面油污和氧化皮。采用光纤激光器在经过前处理的水力机械过流部件表面熔覆,能够进一步优化激光熔覆层与基体的结合效果,保证激光熔覆层的抗冲蚀-空蚀-腐蚀功能更好实现。
附图说明
20.图1为本发明实施例1分散均匀后的熔覆粉末显微形貌;
21.图2为本发明制备抗冲蚀-空蚀-腐蚀涂层中相应步骤的处理视图,其中,(a)为待熔覆样品,(b)为样品表面处理后效果,表面处理需完全清除油污和氧化皮直至露出金属光泽表面,避免激光的加热下在界面处产生恶化涂层性能的杂质;(c)为激光熔覆后效果,(ti+cr3c2)的含量依次为20%,40%,60%,80%和100%;
22.图3为本发明实施例1熔覆涂层截面显微组织结构图;
23.图4为本发明中不同ti+cr3c2添加量的涂层冲蚀、空蚀失重量结果;
24.图5为本发明中不同ti+cr3c2添加量的涂层电化学曲线。
具体实施方式
25.针对水力机械长期在水环境中工作,受空蚀、冲蚀和腐蚀耦合破坏的影响,本发明提出了一种高抗冲蚀-空蚀-腐蚀涂层,其属于一种激光熔覆原位自生涂层。
26.上述高抗冲蚀-空蚀-腐蚀涂层的制备方法,包括以下步骤:
27.步骤一:熔覆粉末的制备,以fe90半马氏体不锈钢粉末作为基础粉末,添加预定比例的ti粉和cr3c2,在真空球磨机中机械混合均匀并通过干燥箱中烘干水分后待用;
28.步骤二:基面处理,使用角磨机或喷砂机对待熔覆基面进行处理,除去表面油污和氧化铁皮;
29.步骤三:激光熔覆,采用高速激光熔覆系统,在氩气保护氛围下,以同轴送粉的方
式将步骤一中的粉末进行熔覆即得。
30.进一步地,步骤一中真空球磨机球磨时间为20~60min,干燥箱干燥温度为100~120℃,干燥时间为0.5~3.0h。优选地,干燥温度为110~120℃,干燥时间为1.0~2.0h。
31.进一步地,步骤二中氩气保护的氩气流量为10~20l/min。
32.进一步地,步骤三中激光熔覆工艺参数如下:
33.激光功率1.6~2.4kw,扫描速度3.6~4.8m/min,送粉速度30~40g/min,搭接率50%,熔覆层数4~5层。
34.利用上述方法制备的高抗冲蚀-空蚀-腐蚀涂层,具有以下优点:
35.(1)由于涂层采用原位自生方法制备,即通过ti元素和cr3c2在高温下反应直接合成tic增强相,基体与增强相之间的相容性更好,具有高韧性,因此抗空蚀性能优异,而弥散分布的细小tic相,则能起到强化基体的作用,如当ti粉和cr3c2的总加入量质量百分比为fe90粉末的60%时,涂层的冲蚀失重量为0.64g,远小于纯fe90涂层的1.29克,因此tic硬质相的生成能够显著提高涂层的抗冲蚀性。
36.(2)cr3c2作为原位自生反应中的c源,和ti粉反应生成tic硬质相的同时,还可以向涂层中补充耐蚀性元素cr,有助于提高涂层的耐腐蚀性。
37.下面结合具体实施例对本发明的实施过程进行详细说明。以下实施例中,如无特殊说明,实施例所涉及的原料均为市售常规商品。其中,fe90粉末粒度为15~100μm,成分质量百分数为:c:0.13~0.16wt%,cr:12~14wt%,si:1.2~1.4wt%,b:1.55~1.65wt%;余量为铁。
38.ti粉粒度为15~100μm,纯度不小于99.9%。
39.cr3c2粉末粒度为15~100μm,纯度不小于99.9%。
40.一、本发明的高抗冲蚀-空蚀-腐蚀涂层的具体实施例
41.实施例1
42.本实施例的高抗冲蚀-空蚀-腐蚀涂层,由包括以下步骤的方法制得:
43.(1)将fe90粉、ti粉和cr3c2粉以质量百分比为fe90:ti:cr3c2=15:1:2的比例称取,放入真空球磨机中进行研磨1h,得到混合粉末。将混合粉末放入真空干燥箱中进行烘干处理以增加粉末的流动性,烘干温度110℃,烘干时间为2h。
44.(2)对待熔覆的45钢基体面进行处理,清除表面油污、氧化皮等,直至露出金属光泽表面。
45.(3)将配制完成的粉末放入送粉器,采用光纤式高速激光熔覆系统,在氩气保护氛围下,氩气流量20l/min,采取同轴送粉的方式进行激光熔覆。激光功率为1600w,扫描速度4.8m/min,搭接率50%,送粉速度40g/min,熔覆层数为4层,得到高抗冲蚀-空蚀-腐蚀涂层。
46.本实施例的高抗冲蚀-空蚀-腐蚀涂层,其为fe90、ti粉和cr3c2通过激光熔覆形成的激光熔覆涂层;ti粉和cr3c2的总质量为fe90质量的20%,cr3c2、ti的质量比为0.5。ti粉和cr3c2在所述激光熔覆过程中原位生成tic硬质相。
47.实施例2
48.本实施例的高抗冲蚀-空蚀-腐蚀涂层,由包括以下步骤的方法制得:
49.(1)将fe90粉、ti粉和cr3c2粉以质量百分比为fe90:ti:cr3c2=15:2:4的比例称取,放入真空球磨机中进行研磨1h,充分混合均匀后放入真空干燥箱中进行烘干处理以增
加粉末的流动性,烘干温度110℃,烘干时间为2h。
50.(2)对待熔覆的45钢基体表面进行处理,清除表面油污、氧化皮等,直至露出金属光泽表面。
51.(3)将配制完成的粉末放入送粉器,采用光纤式高速激光熔覆系统,在氩气保护氛围下,氩气流量20l/min,采取同轴送粉的方式进行激光熔覆。激光功率为2400w,扫描速度3.6m/min,搭接率50%,送粉速度36g/min,熔覆层数为4层,得到高抗冲蚀-空蚀-腐蚀涂层。
52.本实施例的高抗冲蚀-空蚀-腐蚀涂层,其为fe90、ti粉和cr3c2通过激光熔覆形成的激光熔覆涂层;ti粉和cr3c2的总质量为fe90质量的40%,ti粉和cr3c2的质量比为0.5。ti粉和cr3c2在所述激光熔覆过程中原位生成tic硬质相。
53.实施例3
54.本实施例的高抗冲蚀-空蚀-腐蚀涂层,由包括以下步骤的方法制得:
55.(1)将fe90粉、ti粉和cr3c2粉以质量百分比为fe90:ti:cr3c2=5:1:2的比例称取,放入真空球磨机中进行研磨1h,充分混合均匀后放入真空干燥箱中进行烘干处理以增加粉末的流动性,烘干温度110℃,烘干时间为2h。
56.(2)对待熔覆的45钢基体表面进行处理,清除表面油污、氧化皮等,直至露出金属光泽表面。
57.(3)将配制完成的粉末放入送粉器,采用光纤式高速激光熔覆系统,在氩气保护氛围下,氩气流量14l/min,采取同轴送粉的方式进行激光熔覆。激光功率为1600w,扫描速度4.2m/min,搭接率50%,送粉速度30g/min,熔覆层数为5层,得到高抗冲蚀-空蚀-腐蚀涂层。
58.本实施例的高抗冲蚀-空蚀-腐蚀涂层,其为fe90、ti粉和cr3c2通过激光熔覆形成的激光熔覆涂层;ti粉和cr3c2的总质量为fe90质量的60%,ti粉和cr3c2的质量比为0.5。ti粉和cr3c2在所述激光熔覆过程中原位生成tic硬质相。
59.实施例4
60.本实施例的高抗冲蚀-空蚀-腐蚀涂层,由包括以下步骤的方法制得:
61.(1)将fe90粉、ti和cr3c2粉以质量百分比为fe90:ti:cr3c2=15:4:8的比例称取,放入真空球磨机中进行研磨1h,充分混合均匀后放入真空干燥箱中进行烘干处理以增加粉末的流动性,烘干温度110℃,烘干时间为2h。
62.(2)对待熔覆的45钢基体表面进行处理,清除表面油污、氧化皮等,直至露出金属光泽表面。
63.(3)将配制完成的粉末放入送粉器,采用光纤式高速激光熔覆系统,在氩气保护氛围下,氩气流量15l/min,采取同轴送粉的方式进行激光熔覆。激光功率为2200w,扫描速度4.2m/min,搭接率50%,送粉速度40g/min,熔覆层数为4层,得到高抗冲蚀-空蚀-腐蚀涂层。
64.本实施例的高抗冲蚀-空蚀-腐蚀涂层,其为fe90、ti粉和cr3c2通过激光熔覆形成的激光熔覆涂层;ti粉和cr3c2的总质量为fe90质量的80%,ti粉和cr3c2的质量比为0.5。ti粉和cr3c2在所述激光熔覆过程中原位生成tic硬质相。
65.实施例5
66.本实施例的高抗冲蚀-空蚀-腐蚀涂层,由包括以下步骤的方法制得:
67.(1)将fe90粉、ti粉和cr3c2粉以质量百分比为fe90:ti:cr3c2=3:1:2的比例称取,放入真空球磨机中进行研磨1h,充分混合均匀后放入真空干燥箱中进行烘干处理以增加粉
末的流动性,烘干温度110℃,烘干时间为2h。
68.(2)对待熔覆的45钢基体表面进行处理,清除表面油污、氧化皮,直至露出金属光泽表面。
69.(3)将配制完成的粉末放入送粉器,采用光纤式高速激光熔覆系统,在氩气保护氛围下,氩气流量20l/min,采取同轴送粉的方式进行激光熔覆。激光功率为1600w,扫描速度4.8m/min,搭接率50%,送粉速度40g/min,熔覆层数为4层,得到高抗冲蚀-空蚀-腐蚀涂层。
70.本实施例的高抗冲蚀-空蚀-腐蚀涂层,其为fe90、ti粉和cr3c2通过激光熔覆形成的激光熔覆涂层;ti粉和cr3c2的总质量为fe90质量的100%,ti粉和cr3c2的质量比为0.5。ti粉和cr3c2在所述激光熔覆过程中原位生成tic硬质相。
71.二、对比例
72.对比例1
73.本对比例的激光熔覆涂层,制备过程如下:
74.(1)将纯fe90粉末放入真空干燥箱中进行烘干处理以增加粉末的流动性,烘干温度110℃,烘干时间为1h。
75.(2)对待熔覆的基体表面进行处理,清除表面油污、氧化皮等,直至露出金属光泽表面。
76.(3)将配制完成的粉末放入送粉器,采用光纤式高速激光熔覆系统,在氩气保护氛围下,氩气流量15l/min,采取同轴送粉的方式进行激光熔覆。激光功率为2000w,扫描速度4.2m/min,搭接率50%,送粉速度35g/min,熔覆层数为4层,得到高抗冲蚀-空蚀-腐蚀涂层。
77.对比例2~5
78.对比例2~5的激光熔覆涂层,选择fe90粉、ti粉和c粉,分别以质量百分比为fe90:ti:c=(60:4:1)、(30:4:1)、(20:4:1)、(15:4:1)、(12:4:1)的比例按实施例1的制备方法制备激光熔覆涂涂层。
79.三、实验例
80.实验例1熔覆过程分析
81.本实验例对实施例的高抗冲蚀-空蚀-腐蚀涂层的相关制备过程进行说明。
82.图1显示了经过真空球磨机充分混合均匀后的熔覆粉末的显微形貌,3种粉末机械混合均匀,粒径均在20~100μm之间。
83.图2显示了熔覆前后的样品形貌变化,其中,(a)为待熔覆样品,(b)为样品表面处理后效果,表面处理需完全清除油污和氧化皮直至露出金属光泽表面,避免激光的加热下在界面处产生恶化涂层性能的杂质;(c)为激光熔覆后效果,(ti+cr3c2)的含量由左向右、由上向下依次为20%,40%,60%,80%和100%。可以看到,6种熔覆涂层总体质量良好,无裂纹、气孔和夹杂等缺陷。可以看到,6种熔覆涂层总体质量良好,无裂纹、气孔和夹杂等缺陷。
84.将实施例1制得的样品用切割机将样品沿垂直熔覆方向切开,依次用400目、800目、1200目和2000目砂纸打磨截面、抛光、腐蚀(腐蚀液选择质量分数4%硝酸+96%无水乙醇),然后用金相显微镜观察样品的截面形态,见附图3,其中左下方为熔覆涂层,左上方为基体。可见涂层与基体结合良好,为冶金结合。
85.实验例2冲蚀和空蚀实验
86.将本发明实施例1~5和对比例1所获得的激光熔覆涂层进行冲蚀和空蚀性能测
试。冲蚀仪器采用高速加沙射流冲磨仪,试验条件为含沙量:200kg/m3,流速:30m/s,冲磨角度:90
°
,冲磨时间:10min;空蚀实验仪器为xoqs-2500系列智能温控超声波材料气蚀试验机,试验条件为:功率1200w,超声频率:20khz,超声时间:72h。冲蚀和空蚀实验结果见附图4。
87.由图4可以看到,纯fe90熔覆涂层的冲蚀失重量为1.29g,空蚀失重量为0.73g,加入ti粉和cr3c2后,冲蚀失重量迅速下降,空蚀失重量略有上升。即本发明涂层在不严重影响fe90涂层抗空蚀性的前提下,能显著改善涂层的抗冲蚀性能。
88.实验例3抗腐蚀实验
89.腐蚀试验仪器选择cs350电化学工作站,ag/agcl(饱和kcl)为参比电极,铂网为辅助电极。腐蚀介质为1mol/l的nacl溶液。测得的电化学曲线如附图5所示。
90.由图可知,不同试样测得的极化曲线形状基本相似,说明其发生的腐蚀反应的过程基本相同,由图还可以得到涂层的自腐蚀电位,随着ti粉和cr3c2添加量的提高,自腐蚀电位均略有增加,表明耐腐蚀性有所提高。
91.针对对比例1~5的激光熔覆涂涂层,采用以上实验条件,对涂层的耐蚀性进行测试,采用tafel曲线外推法求得自腐蚀电流密度和自腐蚀电位,并与实施例1~5的涂层自腐蚀电位进行比较,结果如表1所示。
92.表1各涂层的自腐蚀电位和自腐蚀电流密度
[0093][0094][0095]
由表1可知,各对比例得到的自腐蚀电位均低于实施例,自腐蚀电流密度均高于实施例,显示了对比例的激光熔覆涂涂层的耐腐蚀性差于实施例。