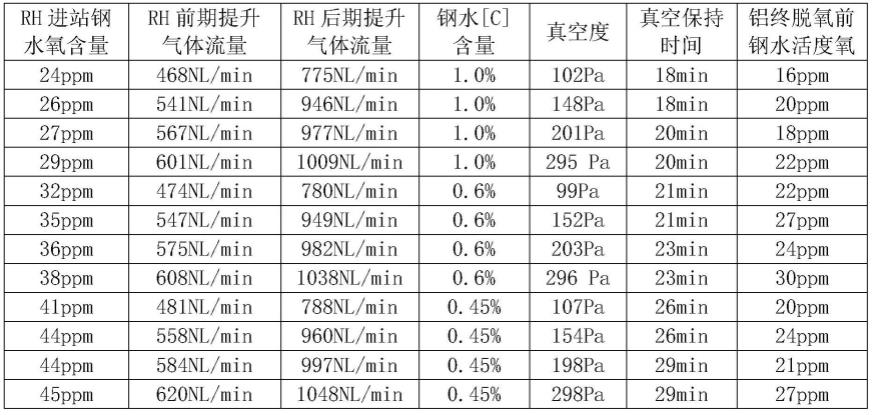
1.本发明属于炼钢领域,更具体地说,涉及一种高断裂韧性中高碳钢的生产方法。
背景技术:2.弹簧、轴承、轮轴等中高碳钢产品对钢材的抗疲劳性能要求很高,而钢材的断裂韧性是表征疲劳性能的重要参数。目前提高钢材断裂韧性主要有以下途径:第一种是优化钢种成分,利用ni、v、n等合金元素的强化作用;第二种是在轧制和热处理过程中进行细化和均匀化钢材的晶粒和组织;第三种是对钢中硬相夹杂物进行变性处理。其中第一种方法由于合金元素的添加,会一定程度上提高成本,第二种方法主要是提高钢材中基体本身的断裂韧性,并没有解决硬相夹杂物在钢基体中产生较强的应力集中问题,提高断裂韧性效果有限。因此解决钢中硬相夹杂物产生应力集中的问题,是目前提高钢材疲劳性能的一个重要方向。
3.中国专利申请号为:cn202010013701.4,公开日为:2020年5月19日的专利文献,为申请人曾申请过的一件名称为一种高断裂韧性的中高碳钢的专利,其生产工艺包括:1)初炼炉出钢采用碳粉、硅基合金、锰基合金粗脱氧;2)精炼过程采用无铝的脱氧材料还原钢包顶渣;3)采用碳脱氧工艺降低钢中活度氧至10-30ppm;4)浇铸前用铝基、钙基脱氧合金对钢水深脱氧。该方案中通过对钢中夹杂物的比例进行控制,配合上述生产工艺解决了钢中硬相夹杂物产生应力集中的问题,最终生产出了高断裂韧性的中高碳钢。但是,在实际生产中发现,采用常规方法控制钢中活度氧含量至10-30ppm时,由于需要控制的活度氧含量较低,整体控制过程并不稳定,且难以控制钢水中的碳氧平衡关系,影响最终制得的钢的性能。
4.众所周知,根据碳氧平衡反应常数:可计算出中高碳钢在常压时,[c]为0.45%平衡的[o]为44ppm,[c]为0.60%平衡的[o]为33ppm,[c]为1.0%平衡的[o]为20ppm。而在100pa真空下,[c]为0.45%平衡的[o]为0.04ppm,[c]为0.60%平衡的[o]为0.03ppm,[c]为1.0%平衡的[o]为0.02ppm。在lf精炼炉、真空炉有限的精炼时间内,钢水中的[c]和[o]无法达到平衡,则整个钢包内的钢水碳氧无法达到完全平衡,因此需要精确控制深脱氧前钢水中活度氧10-30ppm的范围。
[0005]
中国专利申请号为:cn201710220904.9,公开日为:2017年7月7日的专利文献,公开了一种超低碳钢的冶炼方法,其转炉吹炼后的出钢温度为1680℃-1700℃,然后向钢水中加入铝铁以使钢水初步脱氧,然后测温,并测定活度氧,根据测定的活度氧结果向钢水内喂入铝线微调活度氧,保证活度氧在550ppm-650ppm,满足条件后的钢水直接进入rh真空处理工序。该方案虽然在深脱氧前对钢水中的活度氧进行了控制,但是一方面该方案的活度氧在550ppm-650ppm,并不适用于10-30ppm的活度氧范围,另一方面其也没有解决碳氧平衡的问题。
技术实现要素:[0006]
1、要解决的问题
[0007]
针对现有的中高碳钢生产工艺中,难以在深脱氧前将钢水氧活度控制在10-30ppm的同时保证钢水中的碳氧平衡的问题,本发明提供一种高断裂韧性中高碳钢的生产方法,能够建立起钢水活度氧、真空度、真空保持时间三个维度的对应关系,精确控制深脱氧前钢水中活度氧10-30ppm的范围,保证钢水中的碳氧平衡关系,制备出高断裂韧性的中高碳钢。
[0008]
2、技术方案
[0009]
为解决上述问题,本发明采用如下的技术方案。
[0010]
一种高断裂韧性中高碳钢的生产方法,包括以下步骤:
[0011]
一、初炼炉出钢采用碳粉、硅基合金、锰基合金粗脱氧;
[0012]
二、精炼过程采用无铝的脱氧材料还原钢包顶渣;
[0013]
三、采用碳脱氧工艺降低钢中活度氧至10-30ppm;
[0014]
四、浇铸前用铝基、钙基脱氧合金对钢水深脱氧;
[0015]
所述步骤一中,出钢钢水中的碳含量为:0.4%-1.0%,活度氧含量为:20-50ppm;
[0016]
所述步骤二和步骤三中,当真空槽内真空度低于300pa时,每吨钢水的提升气体流量为:3.9~5.2nl/min;当真空槽内真空度高于300pa时,每吨钢水的提升气体流量为:6.3~8.8nl/min。
[0017]
作为技术方案的进一步改进,当真空槽内真空度低于300pa时,真空保持时间t=(ln(真空度)
×
a)/(ln([o])
×
ln([c]
×
b));
[0018]
其中,t的单位为min;真空度单位为pa;[o]为钢水中的活度氧含量,单位为ppm;[c]为钢水中的碳含量,单位为%;a和b为常数。
[0019]
作为技术方案的进一步改进,所述a的取值范围为24.1~25.8,a的大小与真空度的大小为正比关系;b的取值范围为8.9~11.2,b的大小与钢水中活度氧含量的大小为反比关系。
[0020]
作为技术方案的进一步改进,所述高断裂韧性中高碳钢包括以下质量百分比的化学成分:ca:<0.0004%,s:0.006%~0.015%,mn:0.6%~2.0%,余量为fe、c、si、p、n、als合金元素。
[0021]
作为技术方案的进一步改进,所述高断裂韧性中高碳钢中,mns和mns包裹氧化物夹杂的单位面积密度为10-40个/mm2。
[0022]
作为技术方案的进一步改进,所述高断裂韧性中高碳钢中,mns和mns包裹氧化物夹杂数量占总夹杂数量的比例≥95%。
[0023]
作为技术方案的进一步改进,所述高断裂韧性中高碳钢中,97%以上的mns和mns包裹氧化物夹杂的尺寸≤15μm。
[0024]
作为技术方案的进一步改进,所述高断裂韧性中高碳钢中,80%以上的mns和mns包裹氧化物夹杂的长/宽比在1-5范围内。
[0025]
作为技术方案的进一步改进,所述无铝的脱氧材料包括碳粉、电石、碳化硅、单质金属硅等。
[0026]
作为技术方案的进一步改进,浇铸采用连铸、模铸浇铸成钢锭。
[0027]
3、有益效果
[0028]
相比于现有技术,本发明一种高断裂韧性中高碳钢的生产方法,采用真空碳脱氧工艺,建立起独特的钢水活度氧、真空度、真空保持时间三个维度的对应关系模型,确保了
在用铝基、钙基脱氧合金对钢水终脱氧前,钢中活度氧为10-30ppm,控制了铝、钙深脱氧反应的热力学和动力学条件,实现微细氧化物夹杂在钢水中弥散、均匀分布,保证钢水中的碳氧平衡,从而生产出符合目标的高断裂韧性的中高碳钢。
具体实施方式
[0029]
下文对本发明的示例性实施例进行了详细描述。尽管这些示例性实施例被充分详细地描述以使得本领域技术人员能够实施本发明,但应当理解可实现其他实施例且可在不脱离本发明的精神和范围的情况下对本发明作各种改变。下文对本发明的实施例的更详细的描述并不用于限制所要求的本发明的范围,而仅仅为了进行举例说明且不限制对本发明的特点和特征的描述,以提出执行本发明的最佳方式,并足以使得本领域技术人员能够实施本发明。因此,本发明的范围仅由所附权利要求来限定。
[0030]
一种高断裂韧性中高碳钢的生产方法,采用rh精炼法,包括以下步骤:
[0031]
一、初炼炉出钢采用碳粉、硅基合金、锰基合金粗脱氧;
[0032]
二、精炼过程采用无铝的脱氧材料还原钢包顶渣;
[0033]
三、采用碳脱氧工艺降低钢中活度氧至10-30ppm;
[0034]
四、浇铸前用铝基、钙基脱氧合金对钢水深脱氧。
[0035]
其中,步骤一中,初炼炉采用转炉或电炉;步骤二中,无铝的脱氧材料包括碳粉、电石、碳化硅、单质金属硅等;步骤四中,浇铸采用连铸、模铸浇铸成钢锭。
[0036]
通过该工艺制备出的高断裂韧性中高碳钢,其化学成分以及质量百分比为:ca:<0.0004%,s:0.006%~0.015%,mn:0.6%~2.0%,余量为fe、c、si、p、n、als合金元素。
[0037]
同时,在该中高碳钢的制备过程中,通过控制钢中的钙含量,有效的减少钢材中的d类夹杂物,利用孔洞止裂原理,保证mns和mns包裹硬相夹杂物比例的同时,提高mns和mns包裹硬相夹杂物的绝对数量,使基体单位面积上mns和mns包裹氧化物夹杂数量合适,且控制软相夹杂物的尺寸和形状提高了止裂效果,进而提高了钢材的断裂韧性和疲劳性能,使钢材的断裂韧性kq值提高15%以上。
[0038]
具体的,该中高碳钢中,mns和mns包裹氧化物夹杂的单位面积密度为10-40个/mm2;mns和mns包裹氧化物夹杂数量占总夹杂数量的比例≥95%,其中,mns夹杂数量占总夹杂数量的比例≥70%;mns和mns包裹氧化物夹杂在材料的总夹杂的面积占比≥95%;97%以上的mns和mns包裹氧化物夹杂的尺寸≤15μm,80%以上的mns和mns包裹氧化物夹杂的长/宽比在1-5范围内。
[0039]
然而,在实际生产中,无论是对夹杂物的比例进行控制,还是对最终形成的高断裂韧性中高碳钢的性能进行控制,本生产方法的步骤三都是十分重要的,即需要在步骤四前,将钢水中的活度氧含量精确地控制在10-30ppm之间,从而确保最终生产出的中高碳钢的性能稳定性,且在精炼过程中需要保持钢水中的碳氧平衡。
[0040]
现有中高碳钢的生产工艺中,很少需要将活度氧控制在10-30ppm,且现有工艺大多采用向钢水中喂入铝线等简单的常规方式对活度氧进行控制,一般不会全面地考虑到真空槽内的真空度、真空保持时间以及钢水中的碳含量等多个因素,难以保证钢水中的碳氧平衡,因此,本技术上述生产方法的基础上,创新设计了以下方式解决这个问题。
[0041]
步骤一中,出钢钢水中的碳含量为:0.4%-1.0%,活度氧含量为:20-50ppm。
[0042]
步骤二和步骤三中,当真空槽内真空度低于300pa时,每吨钢水的提升气体流量为:3.9~5.2nl/min;当真空槽内真空度高于300pa时,每吨钢水的提升气体流量为:6.3~8.8nl/min。
[0043]
当真空槽内真空度低于300pa时,真空保持时间t=(ln(真空度)
×
a)/(ln([o])
×
ln([c]
×
b))。
[0044]
其中,t的单位为min;真空度单位为pa;[o]为钢水中的活度氧含量,单位为ppm;[c]为钢水中的碳含量,单位为%;a为常数,取值范围为24.1~25.8,a的大小与真空度的大小为正比关系,即在a的取值范围内,真空度越大a的取值越大;b为常数,取值范围为8.9~11.2,b的大小与钢水中活度氧含量的大小为反比关系,即在b的取值范围内,活度氧含量越大b的取值越小。
[0045]
通过上述措施,能够在有限的浇铸周期内,真空钢水无法达到碳氧平衡时,建立起钢水活度氧、真空度、真空保持时间三个维度的对应关系模型,确保了在用铝基、钙基脱氧合金对钢水终脱氧前,钢中活度氧为10-30ppm,控制了铝、钙深脱氧反应的热力学和动力学条件,实现微细氧化物夹杂在钢水中弥散、均匀分布,保证钢水中的碳氧平衡,从而生产出符合目标的高断裂韧性的中高碳钢。
[0046]
下面给出本技术在一次具体生产中的相关数据进一步说明。
[0047]
在某特钢厂120吨rh精炼炉上进行本技术方案的具体实施,生产钢种为满足本实施方式要求的中高碳钢,实施例具体试样过程参数及实验结果如下表所示。
[0048]
实施例实验过程及结果具体情况表
[0049][0050]
其中,rh前期指真空槽内真空度大于300pa的阶段,即开始抽真空时,真空度还没有下降到300pa以下的阶段,rh后期指真空槽内真空度小于300pa的阶段。
[0051]
由上表可得,通过本技术方案的实施,可以稳定的保证在用铝基、钙基脱氧合金对钢水终脱氧前,钢中活度氧为15-30ppm,控制了铝、钙深脱氧反应的热力学和动力学条件,实现微细氧化物夹杂在钢水中弥散、均匀分布和钢水中的碳氧平衡。
[0052]
本发明所述实例仅仅是对本发明的优选实施方式进行描述,并非对本发明构思和范围进行限定,在不脱离本发明设计思想的前提下,本领域工程技术人员对本发明的技术方案作出的各种变形和改进,均应落入本发明的保护范围。