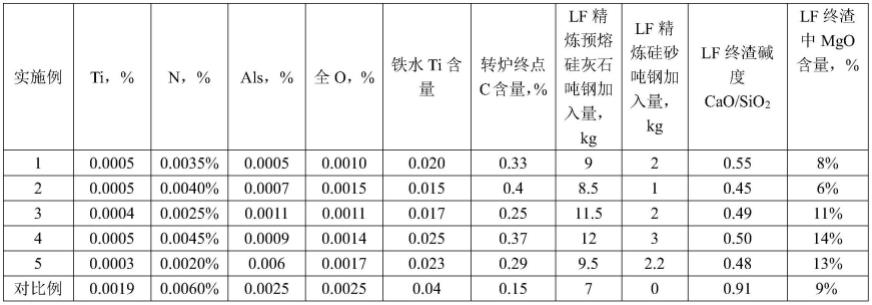
1.本发明涉及炼钢技术领域,尤其涉及一种高强度高疲劳寿命汽车悬架簧和气门弹簧钢盘条的夹杂物控制方法。
背景技术:2.夹杂物是汽车悬架簧和气门弹簧钢等钢种的重要技术指标。夹杂物级别、尺寸和数量、分布等指标控制水平的高低直接影响悬架簧和气门簧等弹簧的疲劳寿命。汽车弹簧钢未来的发展方向为高强化(高应力、减重)合高疲劳寿命,这将对夹杂物提出更加苛刻的要求。弹簧钢中的夹杂物主要为tin夹杂物和氧化物(硫化孟夹杂物由于是变形夹杂物,尺寸较小一般对疲劳寿命无害)。tin夹杂物不变形,只能通过降低其尺寸来降低其危害,降低tin夹杂物尺寸只能通过降低钢中ti和n含量同时降低其偏析是必然选择。降低氧化物夹杂物的尺寸和危害,有两种工艺路线:一种是尽可能降低钢中的全氧含量,一种是使氧化物夹杂物塑性化,配合高的压缩比,但往往钢中的氧含量不会太低。
3.控制弹簧钢盘条中大尺寸硬质夹杂物的生产方法cn 201810973722.3。该发明公开了一种控制弹簧钢盘条中大尺寸硬质夹杂物的生产方法,其包括转炉冶炼、lf精炼、连铸和加热开坯工序;所述转炉冶炼工序:转炉出钢脱氧合金化过程中,采取先碳脱氧后锰硅复合脱氧,锰硅复合脱氧时加入的合金中mn含量与si含量的重量比≥5.0;所述lf精炼工序:采用预熔精炼合成渣造渣,目标碱度w(cao)/w(sio2)为0.8~1.2,渣中w(al2o3)≤3%、w(mno)+w(mgo)≤10%,其余占比≤5%。采用本方法生产的弹簧钢热轧盘条,盘条横截面上氧化物夹杂直径得到有效减小;盘条经拉拔、热处理、喷丸后,弹簧钢丝的旋转弯曲疲劳寿命达到1
×
107次以上,加工成的高强度汽车悬架簧疲劳寿命达到1
×
106以上。上述专利存在的问题和缺点是lf精炼渣碱度控制的偏高,钢水中al含量偏高,氧化物夹杂物塑性化效果不好。lf精炼过程中顶渣侵蚀渣线部位的耐材严重,并且钢水中的氧含量较高。没有对钢中的tin夹杂物提出具体的控制方法。
技术实现要素:4.本发明提供了一种高强度高疲劳弹簧钢盘条夹杂物控制方法,目的是使氧化物夹杂物在低氧条件下具有良好的变形性能,同时细化弹簧钢盘条中tin夹杂物和氧化物夹杂物的尺寸,解决汽车悬架簧和气门簧等钢种对高强化和高疲劳寿命的要求。同时降低精炼渣对钢包渣线部位耐材的侵蚀厚度,提高寿命、降低成本。
5.为了达到上述目的,本发明采用以下技术方案实现:
6.一种高强度高疲劳弹簧钢盘条夹杂物控制方法,包括如下方法:
7.1)转炉冶炼铁水温度≥1300℃,铁水ti含量≤0.03wt%;转炉采用全铁水冶炼或加入少量优质不含al、ti的优质废钢。采用高碳工艺,高拉碳出钢,转炉冶炼终点c含量大于0.2wt%,氧含量小于0.025wt%,转炉终点温度在1600℃以上。
8.2)转炉出钢时采用硅铁、中碳锰铁和低碳铬铁进行脱氧合金化,各合金中al含量
小于0.02wt%,ti含量小于0.01wt%。转炉出钢后采用无al无ti的钢包罐,防止钢水增al和增ti。
9.3)转炉出钢后进行扒渣,扒渣后渣层厚度小于80mm;或者采用转炉留钢操作,避免下渣,防止钢水回ti、回al;出钢后预先按吨钢加入2kg~4kg预熔硅灰石。
10.4)lf精炼过程中加入预熔硅灰石(碱度cao/sio2=0.6-0.8,al2o3含量小于3%)造渣,吨钢加入量8kg~12kg;按吨钢加入1kg~3kg石英砂或硅砂进一步降低预熔硅灰石的碱度,从而降低钢水中的al含量,使氧化物夹杂物塑性化;加入一定量的mgo,作用是降低钢包渣线部位侵蚀,同时保证钢水在低氧含量(10-20ppm)实现氧化物夹杂物的低熔点塑性化。另外,顶渣中加入mgo更容易实现氧化物夹杂物的低熔点塑性化;炉渣造好后精炼时间不小于30分钟,精炼过程温度控制在1520~1600℃之间;lf终渣碱度控制cao/sio2=0.4~0.6,al2o3含量小于5wt%,mgo含量在5wt%~15wt%,mno和feo含量均小于2wt%,tio2含量小于1wt%。
11.5)lf精炼过程中的成分微调也采用硅铁、中碳锰铁和低碳铬铁,并且合金中al含量小于0.02wt%,ti含量小于0.01wt%。
12.6)vd真空脱气保压时间大于15min,破空后弱吹氩搅拌30分钟以上。
13.7)采取上述技术措施实现氧化物夹杂物的塑性化和细化tin夹杂物尺寸,最终钢水中的o含量在10-20ppm,al含量在5-15ppm。ti含量在5ppm以下,n控制在50ppm以下。
14.8)采用大方坯连铸,断面尺寸为(250~300)mm
×
(350~400)mm;全程保护浇注,钢水过热度小于20℃,拉速小于等于0.7m/min;连铸大方坯连轧开坯成断面尺寸为(150~200)mm
×
(150~200)mm连轧坯。
15.9)连铸坯在加热炉内的加热温度控制在1200℃以上,保温时间3小时以上。
16.10)连轧坯轧制盘条前在加热炉的加热温度控制在1050~1200℃,吐丝温度850~910℃,盘条索氏体相变温度650~710℃;
17.11)盘条规格为5.5~18mm。
18.本发明中之所以在lf加预熔硅灰石基础上再加入硅砂或石英砂降低碱度(cao/sio2,下同),就是因为不加预熔硅灰石时钢中复合氧化物夹杂物中的氧化铝含量因钢水中al含量太高而导致复合夹杂物中的氧化铝较高而没有进入图1中低熔点塑性区(1400℃液相线包围区域,该区域夹杂物为可变形夹杂物)。钢中al含量高的原因是本发明钢种55sicr弹簧钢中si、mn和cr合金含量很高(与帘线钢相比),在转炉合金化过程中硅铁l、中碳锰铁和低碳铬铁合金中的残铝带入钢中的al含量太高,在lf精炼阶段由于顶渣成分不合适不能降低钢中al含量,从而导致钢中氧化物夹杂物中的氧化铝含量偏高而没有进入低熔点塑性区(图1)。经过热力学计算和试验研究表明:在lf精炼过程中进一步降低顶渣碱度可以降低钢中al含量,从而使氧化物夹杂物成分进入低熔点塑性区,进而导致夹杂物尺寸进一步得到细化;本发明中lf顶渣中加入mgo之所以更容易使夹杂物低熔点塑性化的原因为mgo的加入会使sio
2-cao-al2o3系低熔点塑性区(见图2-图9,粗实线包围区域,即1400℃液相线包围区域)的面积变大。低熔点区域面积越大复合夹杂物成分越容易落在低熔点塑性区。由图9可以,mgo含量为15%时低熔点区域面积越大,这也正是本发明中lf顶渣中控制mgo含量的上限为15%的原因。20%和25%mgo时sio
2-cao-al2o3系低熔点塑性区的面积虽然也和15%mgo时低熔点区域所占面积差不多,但考虑成本因素,上限定为15%mgo;通过在现场做工业
试验发现在lf精炼过程中向顶渣中加入mgo以后钢包渣线部位的侵蚀变轻,原因可能是钢包渣线部位材质为镁碳砖,lf渣中存在一定量的氧化镁以后抑制了钢包渣线部位的侵蚀;图10为1600℃时55sicr弹簧钢液与sio
2-al2o
3-cao系夹杂物平衡时的等[o]线(热力学计算结果),可以看出氧含量最低为28-40ppm时钢中氧化物夹杂物才能进入低熔点塑性区域,氧含量较高。热力学计算和试验表明lf顶渣中加入一定量的氧化镁以后,由于mgo为碱性氧化物,相当于增加了lf顶渣的碱度和扩大了低熔点塑性区,因此,氧化物夹杂物落在低熔点区域的氧含量会降低,从工业大生产数据来看,氧含量在10-20ppm的范围内。
[0019]
本发明采用了一种全新的技术方案,即在热力学计算和试验基础上,主要通过全新的lf精炼顶渣成分设计,在钢液溶解氧含量较低的情况下实现氧化物夹杂物为低熔点塑性夹杂物,从而在相同压缩比的条件下细化了氧化物夹杂物的尺寸,同时也会降低精炼渣对钢包渣线部位耐材的侵蚀厚度,提高寿命、降低成本。通过控制铁水ti含量、使用低ti合金、专用钢包罐等办法降低钢中ti含量的办法使tin夹杂物尺寸进一步细化。同时配合适当的转炉冶炼、精炼、连铸、连轧、盘条轧制工艺,有效细化了弹簧钢盘条夹杂物的尺寸。最终通过细化夹杂物的尺寸提高了高强度55sicr汽车悬架簧和气门簧钢种的高疲劳寿命。
[0020]
与现有技术相比,本发明的有益效果是:
[0021]
本发明方法实施后弹簧钢盘条中tin夹杂尺寸小于5微米,氧化物夹杂物尺寸小于10微米,氧化物夹杂物长宽比大于3,为塑性夹杂物。同时保证钢水在低氧含量(10-20ppm)和不至于在很低的al含量(2-5ppm)条件下(钢水中al控制很低会增加炼钢成本,控制起来也比较困难)实现氧化物夹杂物的低熔点塑性化。另外,顶渣中加入mgo更容易实现氧化物夹杂物的低熔点塑性化;同时降低精炼渣对钢包渣线部位耐材的侵蚀厚度,提高寿命、降低成本。盘条制成汽车悬架弹簧钢丝强度级别达到2000mpa级,疲劳寿命达到100万次以上,盘条制成汽车气门簧钢丝强度级别达到2100mpa级,疲劳寿命达到一亿次以上。
附图说明
[0022]
图1是55sicr弹簧钢中氧化物夹杂物成分中在相图中的分布;
[0023]
图2是5%mgo含量的cao-al2o
3-sio
2-mgo系相图低熔点区域液相线投影图;
[0024]
图3是10%mgo含量的cao-al2o
3-sio
2-mgo系相图低熔点区域液相线投影图;
[0025]
图4是15%mgo含量的cao-al2o
3-sio
2-mgo系相图低熔点区域液相线投影图;
[0026]
图5是20%mgo含量的cao-al2o
3-sio
2-mgo系相图低熔点区域液相线投影图;
[0027]
图6是25%mgo含量的cao-al2o
3-sio
2-mgo系相图低熔点区域液相线投影图;
[0028]
图7是30%mgo含量的cao-al2o
3-sio
2-mgo系相图低熔点区域液相线投影图;
[0029]
图8是sio
2-cao-al2o3系相图低熔点区域液相线投影图;
[0030]
图9是低熔点区面积随mgo含量的变化曲线图;
[0031]
图10是1600℃时55sicr弹簧钢液与sio
2-al2o
3-cao系夹杂物平衡时的等[o]线图。
具体实施方式
[0032]
为了使本发明的目的、技术方案及优点更加清楚明白,以下结合实施例,对本发明进行进一步详细说明。应当理解,此处所描述的具体实施例仅仅用以解释本发明,并不用于限定本发明。
[0033]
一种高强度高疲劳弹簧钢盘条夹杂物控制方法,包括如下方法:
[0034]
转炉冶炼铁水温度≥1300℃,铁水ti含量≤0.03wt%;转炉采用全铁水冶炼或加入少量优质不含al、ti的优质废钢。采用高碳工艺,高拉碳出钢,转炉冶炼终点c含量大于0.2wt%,氧含量小于0.025wt%,转炉终点温度在1600℃以上;
[0035]
转炉出钢时采用硅铁、中碳锰铁和低碳铬铁进行脱氧合金化,各合金中al含量小于0.02wt%,ti含量小于0.01wt%。转炉出钢后采用无al无ti的钢包罐,防止钢水增al和增ti;
[0036]
转炉出钢后进行扒渣,扒渣后渣层厚度小于80mm;或者采用转炉留钢操作,避免下渣,防止钢水回ti、回al;出钢后预先按吨钢加入2kg~4kg预熔硅灰石;
[0037]
lf精炼过程中加入预熔硅灰石(碱度cao/sio2=0.6-0.8,al2o3含量小于3%)造渣,吨钢加入量8kg~12kg;按吨钢加入1kg~3kg石英砂或硅砂进一步降低预熔硅灰石的碱度,从而降低钢水中的al含量,使氧化物夹杂物塑性化;加入一定量的mgo,作用是降低钢包渣线部位侵蚀,同时保证钢水在低氧含量(10-20ppm)实现氧化物夹杂物的低熔点塑性化。另外,顶渣中加入mgo更容易实现氧化物夹杂物的低熔点塑性化;炉渣造好后精炼时间不小于30分钟,精炼过程温度控制在1520~1600℃之间;lf终渣碱度控制cao/sio2=0.4~0.6,al2o3含量小于5wt%,mgo含量在5wt%~15wt%,mno和feo含量均小于2wt%,tio2含量小于1wt%;
[0038]
lf精炼过程中的成分微调也采用硅铁、中碳锰铁和低碳铬铁,并且合金中al含量小于0.02wt%,ti含量小于0.01wt%;
[0039]
vd真空脱气保压时间大于15min,破空后弱吹氩搅拌30分钟以上。
[0040]
采取上述技术措施实现氧化物夹杂物的塑性化和细化tin夹杂物尺寸,钢水中的o含量在10-20ppm,al含量在5-15ppm。ti含量在5ppm以下,n控制在50ppm以下。
[0041]
采用大方坯连铸,断面尺寸为280mm
×
380mm;全程保护浇注,钢水过热度小于20℃,拉速小于等于0.7m/min;连铸大方坯连轧开坯成断面尺寸为160mm
×
160mm,长度为10.6m-11m连轧坯。
[0042]
连铸坯在加热炉内的加热温度控制在1200℃以上,保温时间3小时以上。
[0043]
连轧坯轧制盘条前在加热炉的加热温度控制在1050~1200℃,吐丝温度850~910℃,盘条索氏体相变温度650~710℃;
[0044]
盘条规格为5.5~18mm。
[0045]
实施例钢种为55sicr,实施例工艺参数见表1,实施例产品性能见表2。由表1和表2可以看出,实施例中55sicr弹簧钢盘条中夹杂物尺寸和变形性能及疲劳寿命明显优于对比例,并且钢丝的强度也高于对比例。
[0046]
表1 实施例和对比例工艺参数
[0047][0048]
表1 实施例和对比例工艺参数(续)
[0049][0050]
表2 实施例和对比例夹杂物尺寸和产品性能
[0051][0052]