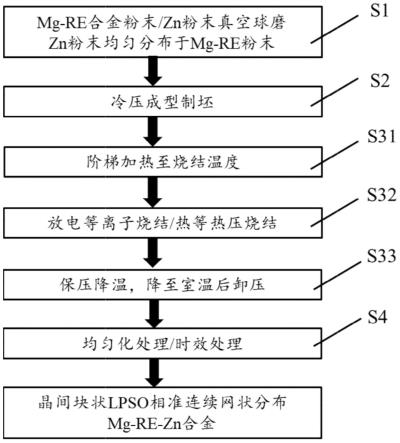
具有晶间块状lpso相准连续网状分布的mg-re-zn合金制备方法
技术领域
1.本发明涉及稀土镁合金制备技术领域,特别涉及一种具有晶间块状lpso相准连续网状分布的mg-re-zn合金制备方法。
背景技术:2.稀土镁合金因其具有较低的密度、较高的比强度、良好的耐热性能和耐腐蚀性能,近年来在航空航天领域以及轨道交通领域得到广泛的应用。稀土镁合金优异的力学性能主要来源于晶内层片状lpso相以及晶间块状lpso相,通过调控晶间块状lpso(长周期有序堆垛结构,long period-stacking ordered phase)相分布能够有效地进一步改善稀土镁合金的室温和高温力学性能。
3.传统制备稀土镁合金的方法主要通过铸锭冶金方法。铸锭冶金方法容易产生宏观偏析以及疏松、疏孔等缺陷,粉末冶金工艺则具有降低能源消耗、节省材料、性能优异、产品精度高且稳定性好等一系列优点,最大限度地减少合金成分偏聚,消除粗大、不均匀的合金组织。放点等离子烧结和热等静压烧结方法是目前最为常用的粉末冶金工艺。
技术实现要素:4.针对现有技术存在的问题,本发明提供一种具有晶间块状lpso相准连续网状分布的mg-re-zn合金制备方法,主要通过放电等离子烧结或热等静压烧结等技术对附着有zn粉末的mg-re合金粉末的冷压坯料进行烧结,并采用阶梯加热路径对模具升温,使mg-re合金粉末颗粒周围的稀土元素与zn元素进行反应生成准连续网状分布的晶间块状lpso相;最后通过热处理,得到力学性能优异的mg-re-zn合金,从而避免了传统铸造过程制备mg-re-zn合金晶间lpso相分布难以调控以及元素偏析等缺陷,制备的mg-re-zn合金晶间块状lpso相分布均匀、结构致密,提高了制备效率。
5.本发明提供了一种具有晶间块状lpso相准连续网状分布的mg-re-zn合金制备方法,具体实施步骤如下:
6.s1、将mg-re合金粉末和zn粉末进行球磨混粉;
7.s2、对附着有zn粉末的mg-re合金粉末进行冷压制坯并获得冷压坯料;
8.s3、对冷压坯料进行放电等离子烧结或热等静压烧结:
9.s31、将步骤s2得到的冷压坯料置于放电等离子烧结或热等静压烧结的模具中,并在模具中施加30~50mpa的压力;
10.s32、采用阶梯加热路径将位于模具中的冷压坯料加热到400~500℃的烧结温度,设定烧结压力为180~200mpa,烧结时间为15min;
11.s33、烧结过程结束后逐渐降温,在降温过程中需保持180~200mpa的压力,在冷压坯料和模具的温度完全降至室温后进行卸压,制备得到晶间块状lpso相呈准连续网状分布的mg-re-zn合金;
12.s4、对步骤s3得到的晶间块状lpso相准连续网状分布的mg-re-zn合金进行热处理;
13.s41、将晶间块状lpso相准连续网状分布的mg-re-zn合金置于热处理炉中进行均匀化处理,热处理设置480~520℃/10~16h;
14.s42、将均匀化处理后的烧结坯料置于时效炉中进行时效处理,时效处理设置为180~220℃/48~82h,得到最终的晶间块状lpso相分布的mg-re-zn合金。
15.可优选的是,所述步骤s1的具体过程如下:
16.s11、按一定的球料质量比将mg-re合金粉末和zn粉末进行混合,并将其置于球磨罐中,同时将球磨罐进行抽真空;
17.s12、将球磨罐置于行星式球磨机上,并设定行星式球磨机的相关参数,使zn粉末均匀附着在mg-re合金粉末颗粒的表面。
18.可优选的是,所述步骤s2的具体过程如下:
19.s21、将附着有zn粉末的mg-re合金粉末置于冷压模具中;
20.s22、采用压力机对附着有zn粉末的mg-re合金粉末进行冷压,所述冷压的压力为120~150mpa,保压时间为5~10min,得到附着有zn粉末的mg-re合金的冷压坯料。
21.可优选的是,在所述步骤s1中,所述mg-re合金粉末和所述zn合金粉末的球料质量比为5:1~7:1,所述mg-re合金粉末颗粒的直径为20~50μm,所述zn合金颗粒的直径为2~5μm。
22.可优选的是,在所述步骤s3中,所述放电等离子烧结或热等静压烧结均在真空下烧结;所述阶梯加热路径是升温阶段一直保持30~50mpa的压力,先以30~35℃/s的升温速率升温至250~300℃,保温时间为3~5min,随后继续以50~60℃/s的升温速率升温至400~500℃。
23.可优选的是,在所述步骤s3中,所述放电等离子烧结或热等静压烧结均在真空下烧结。
24.可优选的是,所述mg-re合金为mg-gd(-y)合金、mg-nd(-y)合金、mg-ce(-y)合金或者mg-la(-y)合金之一。
25.本发明与现有技术相比,具有如下优点:
26.1.本发明采用的放电等离子烧结和热等静压烧结技术属于近净成形技术,提高了制备效率,不需要600℃及以上的高温控制,避免了传统铸造成形过程中产生的高能耗和高污染。
27.2.本发明不需要将mg-re合金粉末以及zn粉末加热至熔融状态,避免了合金液态熔融条件下操作以及组织调控困难等缺陷。
28.3.本发明制备的mg-re-zn系合金中呈准连续网状分布的晶间块状lpso相通过原位反应生成,避免了传统铸造过程制备mg-re-zn合金晶间lpso相分布难以调控以及元素偏析等缺陷,制备的mg-re-zn合金晶间块状lpso相分布均匀、结构致密。
附图说明
29.图1为本发明具有晶间块状lpso相准连续网状分布的mg-re-zn合金制备方法的流程图;
30.图2为本发明具有晶间块状lpso相准连续网状分布的mg-re-zn合金制备方法中烧结反应的示意图;
31.图3为采用本发明具有晶间块状lpso相准连续网状分布的mg-re-zn合金制备方法中制备的mg-re-zn合金内部呈准连续网状分布的晶间块状lpso相图;
32.图4为采用本发明具有晶间块状lpso相准连续网状分布的mg-re-zn合金制备方法中制备的呈准连续网状分布的晶间块状lpso相的电子扫描形貌。
具体实施方式
33.为详尽本发明之技术内容、所达成目的及功效,以下将结合说明书附图进行详细说明。
34.具有晶间块状lpso相准连续网状分布的mg-re-zn合金制备方法,先将mg-re合金粉末和zn粉末进行球磨混粉和冷压制坯,在利用放电等离子烧结或热等静压烧结等方法,在mg-re合金粉末颗粒表面,稀土元素与锌元素原位反应生成准连续网状分布的晶间块状lpso相,制备室温力学性能和高温力学性能优异的晶间块状lpso相呈准连续网状分布的mg-re-zn合金。
35.其中准连续网状分布的含义为:re元素与zn元素在α-mg晶粒晶界处生成块状lpso相且贯穿于相邻晶粒之间,块状lpso相分布在α-mg晶粒周围,能够起到有效的强化效果,但α-mg基体之间相互联通,塑性变形过程中α-mg基体的变形协调能力能够有效改善mg-re-zn系合金的塑性,相比于如图1和图2所示,具体实施步骤如下:
36.s1、将mg-re合金粉末和zn粉末进行真空球磨混粉。
37.s2、对附着有zn粉末的mg-re合金粉末进行冷压制坯。
38.s3、对冷压坯料进行放电等离子烧结或热等静压烧结。
39.s4、对步骤s3得到的晶间块状lpso相分布的mg-re-zn合金进行热处理。
40.在本发明的一个优选实施例中,mg-re合金为mg-gd(-y)合金、mg-nd(-y)合金、mg-ce(-y)合金或者mg-la(-y)合金之一。
41.进一步的,步骤s1中真空球磨混粉的方法包括:
42.s11、按一定的球料质量比将mg-re合金粉末和zn粉末进行混合,并将其置于球磨罐中,同时将球磨罐进行抽真空。
43.s12、将球磨罐置于行星式球磨机上,并设定行星式球磨机的相关参数,使zn粉末均匀附着在mg-re合金粉末颗粒的表面。
44.具体而言,mg-re合金粉末和zn合金粉末的球料质量比为5:1~7:1,mg-re合金粉末颗粒的直径为20~50μm,zn合金颗粒的直径为2~5μm。
45.进一步的,步骤s2中冷压制坯的具体过程如下:
46.s21、将附着有zn粉末的mg-re合金粉末置于冷压模具中。
47.s22、采用压力机对附着有zn粉末的mg-re合金粉末进行冷压,冷压的压力为120~150mpa,保压时间为5~10min,得到附着有zn粉末的mg-re合金的冷压坯料。
48.进一步的,步骤s3中放电等离子烧结或热等静压烧结的具体过程如下:
49.s31、将步骤s2得到的冷压坯料置于放电等离子烧结或热等静压烧结的模具中,并在模具中施加30~50mpa压力。
50.s32、采用阶梯加热路径将位于模具中的冷压坯料加热到400~500℃的烧结温度,设定烧结压力为180~200mpa,烧结时间为15min,得到晶间块状lpso相分布的mg-re-zn合金。
51.s33、烧结过程结束后逐渐降温,在降温过程中需保持180~200mpa的压力,在冷压坯料和模具的温度完全降至室温后进行卸压,制备得到晶间块状lpso相呈准连续网状分布的mg-re-zn合金。
52.在本发明的一个优选实施例中,放电等离子烧结或热等静压烧结均在真空下烧结。阶梯加热路径是升温阶段一直保持30~50mpa的压力,先以30~35℃/s的升温速率升温至250~300℃,保温时间为3~5min,随后继续以50~60℃/s的升温速率升温至400~500℃。
53.优选地,通过步骤s3得到的mg-re-zn合金的晶间块状lpso相分布呈准连续网状分布。
54.进一步的,步骤s4中热处理方法包括:
55.s41、将晶间块状lpso相准连续网状分布的mg-re-zn合金置于热处理炉中进行均匀化处理,热处理制度为480~520℃/10~16h。
56.s42、将均匀化处理后的烧结坯料置于时效炉中进行时效处理,时效处理制度为180~220℃/48~82h,得到最终的晶间块状lpso相分布的mg-re-zn合金。
57.以下结合实施例对本发明一种具有晶间块状lpso相准连续网状分布的mg-re-zn合金制备方法做进一步描述:
58.具体实施例一:
59.s1、将mg-gd合金粉末和zn粉末进行真空球磨混粉。
60.s11、筛选粒径为30μm的mg-gd合金粉末颗粒和粒径为2μm的zn粉末颗粒,按照mg-gd合金粉末与zn粉末7:1的球料比进行混粉,置于内径60mm,外径100mm,高度60mm的球磨罐中进行抽真空至-0.09mpa。
61.s12、将球磨罐置于行星式球磨机上进行球磨,球磨时间50min,球磨转速为300rpm,球磨结束后zn粉末在mg-gd合金粉末表面,表面覆盖度为95%。
62.s2、对附着有zn粉末的mg-gd合金粉末进行冷压制坯。
63.s21、将经过球磨之后的附着有zn粉末的mg-gd合金粉末置于内径为60mm、外径为100mm和高为50mm的冷压模具中。
64.s22、采用压力机对附着有zn粉末的mg-gd合金粉末进行冷压,冷压的压力为150mpa,保压时间为10min,得到附着有zn粉末的mg-gd合金的冷压坯料。
65.s3、对冷压坯料进行放电等离子烧结或热等静压烧结。
66.s31、将步骤s2得到的冷压坯料置于放电等离子烧结模具中,放电等离子烧结模具为内径60mm、外径90mm和高70mm的圆柱体,并在模具中施加50mpa的压力,最后将坯料和放电等离子烧结模具置于放电等离子烧结炉中。
67.s32、采用阶梯加热路径将位于模具中的冷压坯料加热到400℃的烧结温度,先以20℃/s的升温速率升温至250℃,保温时间为3min,随后继续以40℃/s的升温速率升温至400℃,烧结压力为150mpa,烧结时间为8min,获得晶间块状lpso相准连续网状分布的mg-gd-zn合金。
68.s33、烧结过程结束后逐渐降温,在降温过程中需保持180mpa的压力,在冷压坯料和模具的温度完全降至室温后进行卸压,制备得到晶间块状lpso相呈准连续网状分布的mg-gd-zn合金。
69.s4、对步骤s3得到的晶间块状lpso相分布的mg-gd-zn合金进行热处理。
70.s41、将晶间块状lpso相准连续网状分布的mg-gd-zn合金置于热处理炉中进行均匀化处理,热处理制度为500℃/14h,将粉末烧结界面处聚集的稀土元素均匀化。
71.s42、将均匀化处理后的烧结坯料置于时效炉中进行时效处理,时效处理制度为200℃/56h,得到最终的晶间块状lpso相分布的mg-gd-zn合金,如图3和图4所示。
72.从图3和图4中可以观察到,经过球磨混粉以及放电等离子烧结之后的mg-gd-zn合金中晶间块状lpso相呈准连续网状分布,进而说明通过本发明方法能够制备晶间块状lpso相呈准连续网状分布的mg-gd-zn合金。
73.具体实施例二:
74.s1、将mg-gd-y-zr合金粉末和zn粉末进行真空球磨混粉。
75.s11、筛选粒径为40μm的mg-gd-y-zr合金粉末颗粒和粒径为5μm的zn粉末颗粒,按照mg-gd-y-zr合金粉末与zn粉末5:1的球料比进行混粉,置于内径50mm,外径90mm,高度50mm的球磨罐中进行抽真空至-0.09mpa。
76.s12、将球磨罐置于行星式球磨机上进行球磨,球磨时间30min,球磨转速为500rpm,球磨结束后zn粉末在mg-gd-y-zr合金粉末表面,表面覆盖度为90%。
77.s2、对附着有zn粉末的mg-gd-y-zr合金粉末进行冷压制坯。
78.s21、将经过球磨之后的附着有zn粉末的mg-gd-y-zr合金粉末置于内径为80mm、外径为120mm和高为60mm的冷压模具中。
79.s22、采用压力机对附着有zn粉末的mg-gd-y-zr合金粉末进行冷压,冷压的压力为120~150mpa,保压时间为5~10min,得到附着有zn粉末的mg-gd-y合金的冷压坯料。
80.s3、对冷压坯料进行放电等离子烧结或热等静压烧结。
81.s31、将步骤s2得到的冷压坯料置于放电等离子烧结模具中,放电等离子烧结模具为内径80mm、外径130mm和高80mm的圆柱体,并在模具中施加40mpa的压力,最后将坯料和放电等离子烧结模具置于放电等离子烧结炉中。
82.s32、采用阶梯加热路径将位于模具中的冷压坯料加热到500℃的烧结温度,先以35℃/s的升温速率升温至300℃,保温时间为5min,随后继续以50℃/s的升温速率升温至500℃,烧结压力为200mpa,烧结时间为10min,获得晶间块状lpso相准连续网状分布的mg-gd-y-zn-zr合金。
83.s33、烧结过程结束后逐渐降温,在降温过程中需保持200mpa的压力,在冷压坯料和模具的温度完全降至室温后进行卸压,制备得到晶间块状lpso相呈准连续网状分布的mg-gd-y-zn-zr合金。
84.s4、对步骤s3得到的晶间块状lpso相分布的mg-gd-y-zn-zr合金进行热处理。
85.s41、将晶间块状lpso相准连续网状分布的mg-gd-y-zn-zr合金置于热处理炉中进行均匀化处理,热处理制度为520℃/12h,将粉末烧结界面处聚集的稀土元素均匀化。
86.s42、将均匀化处理后的烧结坯料置于时效炉中进行时效处理,时效处理制度为220℃/52h,得到最终的晶间块状lpso相分布的mg-gd-y-zn-zr合金。
87.具体实施例三:
88.目前mg-gd-y-zn-zr合金采用传统的铸造方式制备,主要包括金属加热熔炼,浇筑,凝固冷却过程,其加热熔融过程需要高温以及高压且耗能较大,且产生的废气对环境的污染较大,难以实现精确的温度控制,通过传统铸造方法制备的合金容易在凝固冷却过程出现元素偏析以及疏松和疏孔等缺陷,且难以实现晶间块状lpso相分布的调控。
89.采用本发明的工艺方法制备mg-gd-y-zn-zr合金的过程中控温精确,具体过程见具体实施例二,本工艺方法不需要将合金加热至超过600℃的高温且制备时间缩短,效率较高,可以通过真空球磨混粉过程参数以及烧结参数实现晶间块状lpso相准连续网状分布调控,其准连续网状分布的晶间块状lpso相能够显著强化合金的室温/高温强度以及延伸率,制备的合金元素以及组织分布均匀且几乎不存在组织缺陷。
90.以上所述的实施例仅是对本发明的优选实施方式进行描述,并非对本发明的范围进行限定,在不脱离本发明设计精神的前提下,本领域普通技术人员对本发明的技术方案做出的各种变形和改进,均应落入本发明权利要求书确定的保护范围内。