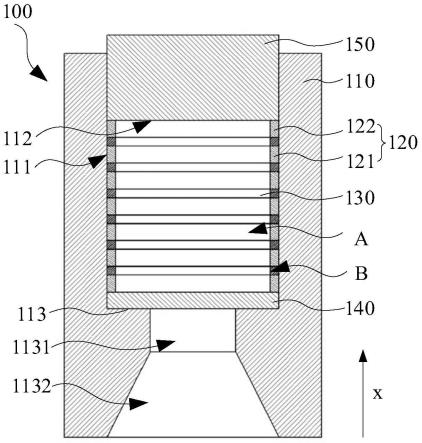
1.本技术涉及半导体材料制备技术领域,特别是涉及模具装置。
背景技术:2.为提升半导体封装材料的导热性能,金刚石由于其高导热率,在复合材料中具有广阔应用前景。然而,由于金刚石硬度极高,复合材料的制备难度大且成本高。
技术实现要素:3.基于此,提供一种能够提升复合材料制备容易程度的模具装置,以解决复合材料制备困难且成本高的问题。
4.一种模具装置,用于将第一基材制备形成复合材料,包括:
5.容具,具有容纳腔和沿第一方向开设的第一开口,第一开口与容纳腔相连通;
6.定位组件,设于容纳腔内;定位组件内限定形成有沿第一方向延伸的定位腔,定位腔与第一开口相连通,以使第一基材能够经由第一开口而进入定位腔内;以及
7.至少两个金属网,沿第一方向彼此间隔设置,且借助于定位组件定位于定位腔内;
8.其中,相邻的金属网之间形成用于夹持第一基材以制备复合材料的夹持空间。
9.在其中一个实施例中,定位组件包括沿第一方向交替且间隔布置的第一定位件和第二定位件;
10.第一定位件和第二定位件上沿第一方向开设有定位孔,全部定位孔共同限定形成定位腔;
11.相邻的第一定位件和第二定位件之间形成用于限位一金属网的限位空间。
12.在其中一个实施例中,定位组件还包括定位结构;
13.定位结构配合于相邻的第一定位件和第二定位件之间,以形成限位空间。
14.在其中一个实施例中,定位结构包括凸出结构;
15.凸出结构设于第一定位件朝向第二定位件的一侧;和/或凸出结构设于第二定位件朝向第一定位件的一侧;
16.相邻的第一定位件和第二定位件借助于凸出结构彼此相间隔,以形成限位空间。
17.在其中一个实施例中,定位结构包括凸出结构和凹陷结构;
18.凸出结构与凹陷结构的至少其中之一设于第一定位件朝向相邻的第二定位件的一侧,凸出结构与凹陷结构的至少其中另一设于第二定位件朝向相邻的第一定位件的一侧;
19.相邻的第一定位件和第二定位件能够借助于至少部分凸出结构形成间隔,和/或能够借助至少部分相配合的凸出结构与凹陷结构形成间隔,以形成限位空间。
20.在其中一个实施例中,凸出结构与凹陷结构的其中之一设于第一定位件朝向相邻的第二定位件的一侧,凸出结构与凹陷结构的其中另一设于第二定位件朝向相邻的第一定位件的一侧;
21.相邻的第一定位件和第二定位件能够借助于至少部分凸出结构形成间隔,和/或能够借助至少部分相配合的凸出结构与凹陷结构形成间隔,以形成限位空间。
22.在其中一个实施例中,第一定位件朝向相邻的第二定位件的一侧设有凸出结构和凹陷结构;
23.第二定位件朝向相邻的第一定位件的一侧设有凸出结构和凹陷结构;
24.相邻的第一定位件和第二定位件能够借助于至少部分凸出结构形成间隔,和/或能够借助至少部分相配合的凸出结构与凹陷结构形成间隔,以形成限位空间。
25.在其中一个实施例中,金属网上设有配合部;
26.配合部能够与定位结构相互配合,以使金属网限位于第一定位件和第二定位件之间。
27.在其中一个实施例中,容具远离第一开口的一端具有台阶部;
28.台阶部构造为能够用于支撑定位组件。
29.在其中一个实施例中,台阶部上设有第一通道;
30.第一通道的径向尺寸小于第一开口的径向尺寸。
31.上述模具装置,在容具的容纳腔内,通过由定位组件所限定的定位腔对金属网和第一基材进行定位,使得相邻两个金属网能够在制备过程中可靠夹持第一基材,从而避免了直接对第一基材中硬度较大的金刚石进行加工,进而降低了制备困难程度和制备成本。
附图说明
32.图1为本技术一实施例的模具装置的结构示意图;
33.图2为本技术一实施例的容具的结构示意图;
34.图3为本技术一实施例的金属网的结构示意图;
35.图4为本技术一实施例的第一定位件的结构示意图;
36.图5为本技术一实施例的第二定位件的结构示意图;
37.图6为本技术一实施例的承托件的结构示意图;
38.图7为本技术一实施例的压头的结构示意图。
39.附图标记说明:
40.100、模具装置;110、容具;111、容纳腔;112、第一开口;113、台阶部;1131、第一通道;1132、第二通道;120、定位组件;121、第一定位件;1211、凸出结构;122、第二定位件;1221、凹陷结构;a、定位腔;a、定位孔;130、金属网;131、配合部;b、限位空间;140、承托件;150、压头。
具体实施方式
41.为使本技术的上述目的、特征和优点能够更加明显易懂,下面结合附图对本技术的具体实施方式做详细的说明。在下面的描述中阐述了很多具体细节以便于充分理解本技术。但是本技术能够以很多不同于在此描述的其它方式来实施,本领域技术人员可以在不违背本技术内涵的情况下做类似改进,因此本技术不受下面公开的具体实施例的限制。
42.在本技术的描述中,需要理解的是,术语“中心”、“纵向”、“横向”、“长度”、“宽度”、“厚度”、“上”、“下”、“前”、“后”、“左”、“右”、“竖直”、“水平”、“顶”、“底”、“内”、“外”、“顺时
针”、“逆时针”、“轴向”、“径向”、“周向”等指示的方位或位置关系为基于附图所示的方位或位置关系,仅是为了便于描述本技术和简化描述,而不是指示或暗示所指的装置或元件必须具有特定的方位、以特定的方位构造和操作,因此不能理解为对本技术的限制。
43.此外,术语“第一”、“第二”仅用于描述目的,而不能理解为指示或暗示相对重要性或者隐含指明所指示的技术特征的数量。由此,限定有“第一”、“第二”的特征可以明示或者隐含地包括至少一个该特征。在本技术的描述中,“多个”的含义是至少两个,例如两个,三个等,除非另有明确具体的限定。
44.在本技术中,除非另有明确的规定和限定,术语“安装”、“相连”、“连接”、“固定”等术语应做广义理解,例如,可以是固定连接,也可以是可拆卸连接,或成一体;可以是机械连接,也可以是电连接;可以是直接相连,也可以通过中间媒介间接相连,可以是两个元件内部的连通或两个元件的相互作用关系,除非另有明确的限定。对于本领域的普通技术人员而言,可以根据具体情况理解上述术语在本技术中的具体含义。
45.在本技术中,除非另有明确的规定和限定,第一特征在第二特征“上”或“下”可以是第一和第二特征直接接触,或第一和第二特征通过中间媒介间接接触。而且,第一特征在第二特征“之上”、“上方”和“上面”可是第一特征在第二特征正上方或斜上方,或仅仅表示第一特征水平高度高于第二特征。第一特征在第二特征“之下”、“下方”和“下面”可以是第一特征在第二特征正下方或斜下方,或仅仅表示第一特征水平高度小于第二特征。
46.需要说明的是,当元件被称为“固定于”或“设置于”另一个元件,它可以直接在另一个元件上或者也可以存在居中的元件。当一个元件被认为是“连接”另一个元件,它可以是直接连接到另一个元件或者可能同时存在居中元件。本文所使用的术语“垂直的”、“水平的”、“上”、“下”、“左”、“右”以及类似的表述只是为了说明的目的,并不表示是唯一的实施方式。
47.此外,附图并不是1:1的比例绘制,并且各元件的相对尺寸在附图中仅以示例地绘制,而不一定按照真实比例绘制。
48.为了便于理解本技术的技术方案,在详细展开说明之前,首先对现有半导体器件用于封装的复合材料进行阐述。
49.半导体封装常用的热沉材料是一种具有高热导率、低热膨胀系数等特性的散热封装材料,其为芯片起着固定支撑、散发热量的作用,为芯片提供了稳定工作的环境。常用的热沉材料包括钨铜合金、钼铜合金、铝碳化硅、覆铜陶瓷板等,但这些材料热导率普遍相对较低,已不能满足电子元器件日益增长的散热需求。
50.金刚石导热率可达2000w/mk,是良好的散热封装材料,而金刚石同时还具有高硬度的特性,导致其极难加工,整块的金刚石制备困难,成本高昂。因此,通常将金刚石颗粒与金属材料制备得到复合材料,并通过设计金刚石颗粒所占的体积分数,调控复合材料的热膨胀系数需求,从而与碳化硅、氮化镓等半导体材料相匹配,且具有较高热导率,能够更好地满足芯片的散热需求。
51.为便于描述,附图仅示出了与本技术实施例相关的结构。
52.图1示出了本技术一实施例中的模具装置100的结构示意图,图2示出了本技术一实施例中的容具110的结构示意图;图3示出了本技术一实施例中的金属网130的结构示意图。
53.参阅图1,并结合图2、图3,本技术一实施例提供了的模具装置100,用于将第一基材制备形成复合材料,包括容具110、定位组件120和至少两个金属网130。容具110具有容纳腔111和沿第一方向开设的第一开口112,第一开口112与容纳腔111相连通。定位组件120设于容纳腔111内,定位组件120内限定形成有沿第一方向延伸的定位腔a,定位腔a与第一开口112相连通,以使第一基材能够经由第一开口112进入定位腔a内。至少两个金属网130沿第一方向彼此间隔设置,且借助于定位组件120定位于定位腔a内。其中,相邻的金属网130之间形成用于夹持第一基材以制备复合材料的夹持空间。
54.上述模具装置100,在容具110的容纳腔111内,通过由定位组件120所限定的定位腔a对金属网130和第一基材进行定位,使得相邻两个金属网130能够在制备过程中可靠夹持第一基材,从而避免了直接对第一基材中硬度较大的金刚石进行加工,进而降低了在将第一基材加工制备得到复合材料的过程中的制备困难程度和制备成本。
55.需要说明的是,本技术中的模具装置100可应用于熔渗工艺、粉末冶金工艺、搅拌铸造工艺、烧结工艺等制备工艺中,其中,烧结工艺包括但不限于是放电等离子烧结、热压烧结工艺、高压烧结工艺等。本技术以熔渗工艺作为示例。熔渗工艺是将金属加热至液体状态,在无压或者压力辅助下渗入金刚石颗粒中,最后凝固成复合材料。
56.结合本技术中的模具装置100,第一基材包括金刚石,金属网130具有多个网孔,网孔的孔径大于金刚石的粒径。如此,能够确保金刚石被限制于两个金属网130之间,避免金属网130的孔径过大,导致金刚石无法夹持在两层金属网130之间。尤其是在制备多层复合材料时,通过金属网130对金刚石进行拦截,能够避免模具装置100中更上层的金刚石会穿过金属网130掉落至更下层,以免制备得到的多层复合材料难以保持每层复合材料的均匀一致性。而金属网130限位于第一定位件121和第二定位件122之间,能够在复合材料的制备过程中,限制金刚石颗粒及金属网130在金属溶液中的浮动。除此之外,金属网130还能够保证金刚石颗粒铺展的均一性,从而提升所制备得到的复合材料的厚度均匀一致性。
57.进一步地,模具装置100用于将第一基材和第二基材制备形成复合材料。第二基材以第一基材为中心,对称设于两个金属网130的相背的一侧。具体到一些实施方式中,第二基材为金属块。如此,在制备过程中,金属块变形,由金属网130的网孔进入并包覆于金刚石外部,再经由冷却凝固后得到复合材料。
[0058]“变形”是指金属在加热过程中会发生形变。此处需要说明的是,物体因温度改变而发生的膨胀现象被称为“热膨胀”。通常是指外压强不变的情况下,物质在温度升高时,其体积随之增大。在升温过程中,金属发生熔融,熔融是熔化过程中的固液共存状态,此时无论固相金属或是液相金属,均发生“变形”,也即其体积增大,而在模具装置100的容具110内,受限于容具110的内壁、金属自身重力以及其他压力,金属变形会经由金属网130的网孔进入,也即是填充于金刚石与金属网130的缝隙之间,实现对金刚石的包覆。也即是,制备得到的金刚石“镶嵌”于复合材料内部。
[0059]
在一些实施例中,第一基材还包括金属粉。如此,借助于金属粉能够进一步地确保对金刚石的包覆效果。具体地,金属粉与第二基材的金属块的材料相同。如此,能够进一步提升复合材料的结合强度,而且能够易于控制金属的熔点,确保金属在熔渗过程中能够可靠熔化至包覆金刚石。示例性地,金属粉及金属块的材料包括铜、银、铝、镍中的至少一种。上述金属材料导热性较好,最终制备形成的复合材料导热率更高,更能适用于半导体散热
领域。
[0060]
需要说明的是,本技术提供的模具装置100,既可以仅制备一层复合材料,也可以通过在模具装置100中借助于多个金属块及多个金属网130,同时制备多层的复合材料。借助于第二基材金属块,制备得到的复合材料沿第一方向的两侧为金属层。在将冷却的多层复合材料及模具装置100从加热炉中取出后,通过对多层的复合材料在金属层处进行切割,即可形成单层的复合材料。切割方法示例性地,可以为线切割、激光切割、金刚石刀具切割、水刀切割等,在此不作限制。
[0061]
其中,经过本技术提供的模具装置100制备得到的多层复合材料,每层之间借助于金属层结合在一起,故而在对其进行切割时,不会存在金刚石和金属网130的阻碍,因此降低了加工难度,提高了成品率。而且,预留的金属层也易于后续的表面镀覆和封装等的加工步骤。而且,正是由于复合材料在第一方向上的两侧为金属层,降低了研磨抛光的难度,复合材料的表面平整度和粗糙度也得到了极大改善。
[0062]
图4示出了本技术一实施例中的第一定位件121的结构示意图;图5示出了本技术一实施例中的第二定位件122的结构示意图。
[0063]
参阅图4、图5,并结合图1,在一些实施例中,定位组件120包括沿第一方向交替且间隔布置的第一定位件121和第二定位件122。第一定位件121和第二定位件122上沿第一方向开设有定位孔a,全部定位孔a共同限定形成定位腔a,相邻的第一定位件121和第二定位件122之间形成用于限位一金属网130的限位空间b。由于相邻的两个金属网130限定了所能够容纳的第一基材的量,也即借助于相邻的两个金属网130限定了所能制备得到的复合材料的尺寸,如此,借助于交替间隔布置的第一定位件121和第二定位件122,能够对金属网130进行支撑及限位,从而避免在制备过程中金属网130在容具110中发生移位,进而确保了在同时制备多层复合材料时,每层复合材料的结构尺寸保持一致。需要说明的是,为满足不同复合材料的厚度需求,第一定位件121与第二定位件122在第一方向上的尺寸可进行根据需求进行调节,在此不作限制。
[0064]
请继续结合图4和图5所示,在一些实施例中,定位组件120还包括定位结构,定位结构配合于相邻的第一定位件121和第二定位件122之间,以形成限位空间b。如此,能够借助于第一定位件121和第二定位件122之间的定位结构,形成用于限位金属网130的限位空间b。具体到一些实施方式中,定位结构包括凸出结构1211,凸出结构1211设于第一定位件121朝向第二定位件122的一侧。相邻的第一定位件121和第二定位件122借助于凸出结构1211彼此相间隔,以形成限位空间b。如此,通过第一定位件121上的凸出结构1211与第二定位件122朝向第一定位件121的表面配合作用,从而可靠地将金属网130夹持在第一定位件121和第二定位件122之间。
[0065]
具体到又一些实施方式中,凸出结构1211设于第二定位件122朝向第一定位件121的一侧。如此,通过第二定位件122上的凸出结构1211与第一定位件121朝向第二定位件122的表面配合作用,从而可靠地将金属网130夹持在第一定位件121和第二定位件122之间。具体到再一些实施方式中,凸出结构1211还可以同时设于第一定位件121朝向第二定位件122的一侧,以及第二定位件122朝向第一定位件121的一侧。
[0066]
在一些实施例中,定位结构包括凸出结构1211和凹陷结构1221,凸出结构1211与凹陷结构1221的至少其中之一设于第一定位件121朝向相邻的第二定位件122的一侧,凸出
结构1211与凹陷结构1221的至少其中另一设于第二定位件122朝向相邻的第一定位件121的一侧。需要说明的是,凸出结构1211与凹陷结构1221的“至少”其中之一,也即为第一定位件121及第二定位件122上既可以设有凸出结构1211,也可以设有凹陷结构1221,还可以同时设有凸出结构1211和凹陷结构1221。在装配时,第一定位件121与第二定位件122借助于彼此的凸出结构1211和凹陷结构1221相互配合,从而限制第一定位件121与第二定位件122之间的移动,进而确保对金属网130的限位效果。
[0067]
在一些实施方式中,相邻的第一定位件121和第二定位件122能够借助于至少部分凸出结构1211形成间隔。如此,结合后述一些实施例,借助于凸出结构1211朝向第二定位件122的表面,与第二定位件122朝向第一定位件121的表面相抵,能够实现对金属网130的可靠限位。
[0068]
在又一些实施方式中,相邻的第一定位件121和第二定位件122能够借助至少部分相配合的凸出结构1211与凹陷结构1221形成间隔,以形成限位空间b。如此,通过凸出结构1211和凹陷结构1221之间的配合,能够进一步地减小第一定位件121和第二定位件122之间的间距,从而使得金属网130能够被限制在更小的空间内,进一步地减小金属网130的可移动范围。而且,借助于凹陷结构1221的凹陷更为稳靠地限制第一定位件121相对第二定位件122的移动,进而使得对金属网130的限位更为可靠。在本技术的实施方式中,金属网130在第一方向上的两个表面分别与第一定位件121和第二定位件122相贴合,也即夹持于第一定位件121和第二定位件122之间。
[0069]
具体到一些实施例中,凸出结构1211与凹陷结构1221的其中之一设于第一定位件121朝向相邻的第二定位件122的一侧,凸出结构1211与凹陷结构1221的其中另一设于第二定位件122朝向相邻的第一定位件121的一侧。可以理解地,在本实施例中,第一定位件121或第二定位件122上,有且仅有凸出结构1211或是凹陷结构1221的其中之一。
[0070]
具体至一些实施方式中,相邻的第一定位件121和第二定位件122能够借助于至少部分凸出结构1211形成间隔。如此,能够借助于凸起结构1211形成的间隔对金属网130进行限位。具体至另一些实施方式中,相邻的第一定位件121和第二定位件122能够借助至少部分相配合的凸出结构1211与凹陷结构1221形成间隔,以形成限位空间b。如此,借助于凸起结构1211和凹陷结构1221的配合,能够进一步地减小间隔的距离,从而缩小金属网130的可移动空间。
[0071]
具体到又一些实施例中,第一定位件121朝向相邻的第二定位件122的一侧设有凸出结构1211和凹陷结构1221。第二定位件122朝向相邻的第一定位件121的一侧设有凸出结构1211和凹陷结构1221。相邻的第一定位件121和第二定位件122能够借助于至少部分凸出结构1211形成间隔,和/或能够借助至少部分相配合的凸出结构1211与凹陷结构1221形成间隔,以形成限位空间b。可以理解地,在本实施例中,第一定位件121或第二定位件122上,既设有凸出结构1211,又设有凹陷结构1221。
[0072]
进一步地,第一定位件121朝向第二定位件122的一侧设有多个凸出结构1211,多个凸出结构1211沿第一定位件121的周向彼此间隔设置。第二定位件122朝向第一定位件121的一侧设有多个凹陷结构1221,多个凹陷结构1221沿第二定位件122的周向彼此间隔设置。其中,多个凸出结构1211与多个凹陷结构1221一一对应且相互配合。如此,借助于多个凸出结构1211和多个凹陷结构1221之间的配合,能够从多个位置限制第一定位件121和第
二定位件122之间的相互移动,以进一步地确保金属网130的可靠限位。
[0073]
更进一步地,第一定位件121朝向第二定位件122的一侧设有四个凸出结构1211,第二定位件122朝向第一定位件121的一侧设有四个凹陷结构1221。在如图4示出的实施例中,第一定位件121在第一方向上的两侧均设有凸出结构1211。如此,在第一定位件121与第二定位件122交错设置时,能够保证当第一定位件121位于两个第二定位件122之间时,能够依靠两侧的凸出结构1211同时与两个第二定位件122上的凹陷结构1221相配合,从而实现更为稳靠的定位。
[0074]
在一些实施例中,凸出结构1211的外廓形状与凹陷结构1221的內廓形状相适配。如此,能够确保凸出结构1211与凹陷结构1221可靠配合。具体至如图4和图5示出的实施例中,凸出结构1211在与第一方向相垂直的平面上的正投影呈圆形,凹陷结构1221在与第一方向相垂直的平面上的正投影呈圆形。可以理解地,凸出结构1211呈圆柱体结构。如此,能够提升凸出结构1211与凹陷结构1221的加工的容易程度。当然,凸出结构1211与凹陷结构1221也可以为其他形状,在此不作限制。
[0075]
在其他实施例中,定位结构也可以为其他结构形式。例如,第一定位件121朝向第二定位件122的一侧具有在第一方向上凸起的弧形段,第二定位件122朝向第一定位件121的一侧具有在第一方向上凹陷的弧形段。如此,第一定位件121和第二定位件122借助于弧形段彼此相配合,也可限制第一定位件121与第二定位件122之间的相互运动。弧形段既可以是连续的弧形段,以形成类似于“波浪”状结构,也可以是彼此间隔的弧形段,只要能够实现第一定位件121与第二定位件122之间的相互配合即可。
[0076]
请再次参阅图3,在一些实施例中,金属网130上设有配合部131,配合部131能够与定位结构相互配合,以使金属网130限位于第一定位件121和第二定位件122之间。如此,通过金属网130上的配合部131与定位结构配合,能够确保金属网130与定位结构相贴合。具体到一些实施方式中,配合部131为配合孔。结合前述一些实施例,第一定位件121上设有凸出结构1211,第二定位件122上设有凹陷结构1221,金属网130夹持在第一定位件121和第二定位件122之间,也即是凸出结构1211穿过配合孔伸入凹陷结构1221,从而确保金属网130能够被第一定位件121和第二定位件122可靠定位。进一步地,金属网130上设有多个配合部131,多个配合部131沿周向彼此间隔设置。如此,能够易于金属网130从多个位置限位于第一定位件121和第二定位件122之间。具体至如图3示出的实施方式中,金属网130上开设有四个配合孔。
[0077]
图6示出了本技术一实施例中的承托件140的结构示意图。
[0078]
参阅图6,并结合图1和图2所示,在一些实施例中,容具110远离第一开口112的一端具有台阶部113,台阶部113被构造为能够用于支撑定位组件120。如此,借助于台阶部113能够为定位组件120提供支撑平台,从而沿第一方向支撑定位组件120。可以理解地,第一定位件121与第二定位件122彼此交替地沿第一方向设置在台阶部113上。具体到一些实施方式中,模具装置100还包括承托件140,承托件140与定位组件120依次沿第一方向设于台阶部113上。在制备复合材料的过程中,承托件140能够承托第一基材,以确保制备工艺的可靠进行。尤其是在压力熔渗的工艺中,承托件140能够提供更为稳靠的支撑作用。示例性地,承托件140可以为垫片。
[0079]
在一些实施例中,台阶部113上设有第一通道1131,第一通道1131的径向尺寸小于
第一开口112的径向尺寸。如此,结合前述一些实施例,通过第一通道1131能够使得制备过程中的废液更为容易地排出,而避免堆积在容具110的容纳腔111的底部,致使制备得到的底层的复合材料结构与上层的复合材料结构相异。结合前述一些实施例,需要说明的是,金属溶液可通过承托件140与容具110的容纳腔111的腔壁之间的缝隙流出,也即是承托件140并不会影响废液的排出。
[0080]
在一些实施例中,台阶部113上还设有与第一通道1131相连通的第二通道1132,第二通道1132的径向尺寸沿背离第一开口112的方向逐渐增大。如此,借助于第二通道1132能够与外部容器进行配合,外部容器示例性地,可以为废液容器。当然,在其他一些实施方式中,也可以不采用台阶部113与承托件140的配合方式,而在容具110的底部设置一个或多个出液口以使废液排出,在此不作限制。
[0081]
图7示出了本技术一实施例中的压头150的结构示意图。
[0082]
参阅图7,并结合图1,在一些实施例中,模具装置100还包括压头150,压头150沿第一方向位于容纳腔111内靠近第一开口112的一端。其中,压头150用于辅助压力熔渗。如此,借助于压头150能够更为容易地向容具110内的第一基材和第二基材施加压力。具体地,压头150可以但不限于是圆柱体、长方体、圆台等形状,在此不作限制。
[0083]
本技术实施例提供的模具装置100,在容具110的容纳腔111内,通过由定位组件120所限定的定位腔a对金属网130和第一基材进行定位,使得相邻两个金属网130能够在制备过程中可靠夹持第一基材,从而避免了直接对第一基材中硬度较大的金刚石进行加工,进而降低了在将第一基材加工制备得到复合材料的过程中的制备困难程度和制备成本。借助于定位组件120中交替间隔布置的第一定位件121和第二定位件122,能够对金属网130进行支撑及限位,从而避免在制备过程中金属网130在容具110中发生移位,进而确保了在同时制备多层复合材料时,每层复合材料的结构尺寸保持一致。而且,经过本技术提供的模具装置100制备得到的多层复合材料,每层之间借助于金属层结合在一起,故而在对其进行切割时,不会存在金刚石和金属网130的阻碍,因此降低了研磨抛光的难度,复合材料的表面平整度和粗糙度也得到了极大改善。
[0084]
以上所述实施例的各技术特征可以进行任意的组合,为使描述简洁,未对上述实施例中的各个技术特征所有可能的组合都进行描述,然而,只要这些技术特征的组合不存在矛盾,都应当认为是本说明书记载的范围。
[0085]
以上所述实施例仅表达了本技术的几种实施方式,其描述较为具体和详细,但并不能因此而理解为对申请专利范围的限制。应当指出的是,对于本领域的普通技术人员来说,在不脱离本技术构思的前提下,还可以做出若干变形和改进,这些都属于本技术的保护范围。因此,本技术专利的保护范围应以所附权利要求为准。