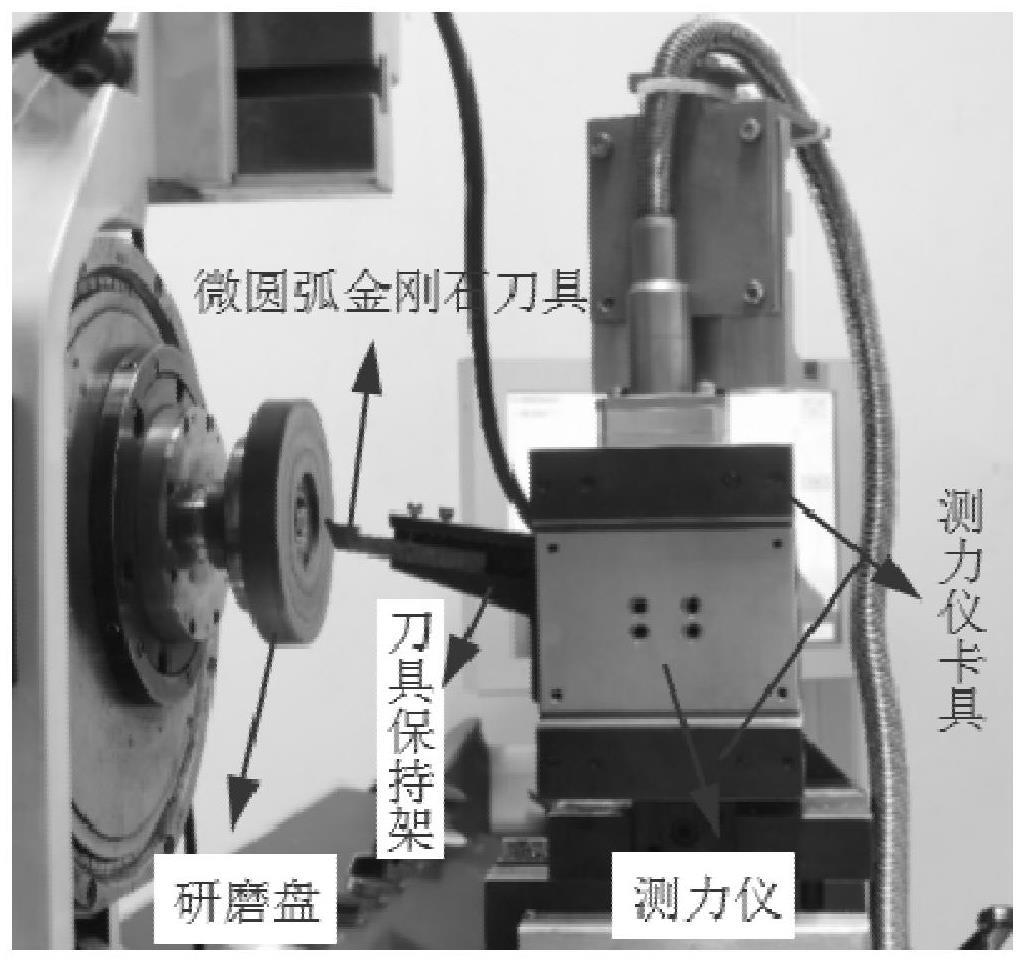
1.本发明属于光学加工技术领域,涉及一种适合于制造刀尖圆弧半径50~100μm高精度微圆弧金刚石刀具的机械刃磨工艺,应用于微特征光学零件的超精密切削加工。
背景技术:2.由于金刚石的硬度极高,是自然界最硬的物质之一,并且经过仔细研磨抛光后可以获得极其锋利的刃口,因此被认为是制作超精密切削加工刀具的理想材料。也是由于金刚石的高硬度,其高质量机械加工十分困难。经过大量学者和工程技术人员几十年的攻关研究,大圆弧刃和直线刃金刚石刀具的机械刃磨技术已逐步趋于成熟。
3.但是,工业上对先进光学系统的成像质量要求越来越高,并且要求光学系统进一步集成化和小型化,这对光学微透镜、曲面反射镜、衍射透镜等高端光学元件的精度提出了更高的要求。而加工高精度的微光学元件,不仅需要金刚石刀具的特征尺寸小,还需要金刚石刀具的制造精度比被加工元件精度高半个数量级及以上。其中,典型的刀具之一就是刀尖圆弧半径50~100μm的高精度微圆弧金刚石刀具,并且这类刀具在3c产业中也具有广泛的应用场景,如智能手机、平板电脑的摄像头透镜模具的超精密加工和计算机机械硬盘读数头的超精密加工等。这些超精密元件均对加工表面质量和面型精度的要求极高,为满足加工要求必须采用更高精度的微圆弧金刚石刀具,目前工业上要求刀刃圆弧波纹度优于50nm/100
°
圆弧包角、锋利度要求优于30nm、放大4000倍无肉眼可见崩刃缺陷。
4.金刚石晶体具有极高的脆性,并且很容易解理,加之金刚石晶体的各向异性,致使高精度微圆弧金刚石刀具的机械刃磨制备极其困难。另外,由于微圆弧金刚石刀具的特征尺寸很小、强度很弱,机械刃磨过程中对磨削力非常敏感,如果磨削力大小控制不当或者波动过大,很容易导致切削刃崩碎甚至折断而报废。这些微圆弧金刚石刀具机械刃磨过程中的新难题,用传统大圆弧刃金刚石刀具和直线刃金刚石刀具的刃磨方法很难解决。
5.为了实现刀尖圆弧半径50~100μm光学加工用高精度微圆弧金刚石刀具的国产化,打破国外技术垄断,需要深入研究每个工艺参数对该类微圆弧金刚石刀具机械刃磨质量的影响,精确掌握刀刃圆弧波纹度、锋利度和微观缺陷的变化规律,探索微圆弧金刚石刀具刀刃圆弧波纹度、锋利度和微观缺陷的控制方法,优化机械刃磨工艺参数以实现该类高精度微圆弧金刚石刀具的加工。
技术实现要素:6.为了加工刀刃圆弧波纹度优于50nm/100
°
圆弧包角、切削刃口钝圆半径优于30nm、刀尖圆弧半径50~100μm、放大4000倍无肉眼可见崩刃的一类微圆弧金刚石刀具,本发明提供了一种近无崩刃微圆弧金刚石刀具的力控制机械刃磨工艺。本发明主要从控制微圆弧金刚石刀具机械研磨的磨削力大小和各向异性入手,进而抑制刀尖崩碎、折断和金刚石晶体材料去除率的各向异性,结合前期积累的高精度大圆弧金刚石刀具机械刃磨工艺经验,对该类微圆弧金刚石刀具进行机械刃磨加工。通过大量的微圆弧金刚石刀具机械刃磨工艺实
验,详细分析了金刚石磨料粒度、研磨盘基体材料、研磨压力、研磨盘转速、往复运动行程、往复运动频率、摆轴摆动速度、磨削力大小等对该类微圆弧金刚石刀具刀刃圆弧波纹度、锋利度和微观缺陷的影响规律,并建立优选的微圆弧金刚石刀具机械刃磨工艺,为打破国外的技术壁垒、提高我国光学加工用微圆弧金刚石刀具的加工水平,迈出了探究性的一步。
7.本发明的目的是通过以下技术方案实现的:
8.一种近无崩刃微圆弧金刚石刀具的力控制机械刃磨工艺,包括如下步骤:
9.步骤一:选择规整的八面体天然金刚石晶体作为刀头材料,用激光切割机沿金刚石{100}晶面切开;选择与金刚石晶体热膨胀系数相近的硬质合金作为刀柄材料,并按刀头设计参数加工成合适的形状;
10.步骤二:用金刚石平磨机把步骤一切开的金刚石晶体沿{100}晶面研磨成厚度为1~1.5mm的薄片,并保证上下研磨表面的平整度,方便后续精磨前刀面;
11.步骤三:用酒精清洗步骤一的刀柄和步骤二的金刚石片,以去除二者表面的污染物;然后,按前、后刀面均为{100}晶面进行定向,在刀柄和金刚石片之间加入银铜钛焊料并将其固定在刀柄之上;最后,把固定有金刚石片和焊料的刀柄置于真空焊接炉内进行钎焊,高温融化后的焊料将金刚石片与刀柄牢固的焊接在一起;
12.步骤四:用激光切割机对步骤三焊好的金刚石片进行粗成型加工,按设计好的刀尖角把金刚石片的前端加工成v型刀头,刀头侧边要伸出刀柄边缘0.2mm以上,方便后续研磨加工;
13.步骤五:用金刚石平磨机对步骤四粗成型加工完成的刀具前刀面进行精磨加工,一是保证前刀面与刀柄底面平行,二是去除步骤二残留的研磨痕迹以减小前刀面粗糙度;
14.步骤六:用卡具把kistler 9119aa2型测力仪固定在pg3b行星型钻石刀具研磨机的刀架上,再把刀具固定保持架安装在测力仪上,最后把步骤五完成前刀面研磨的金刚石刀具毛坯固定在刀具保持架上;
15.步骤七:恒温控制pg3b行星型钻石刀具研磨机周围环境条件为25℃,恒温精度
±
0.5℃;在主轴冷却水循环系统正常工作情况下,空载运行研磨机半小时以上,使其性能达到稳定状态;
16.步骤八:把研磨机摆轴摆到左(或右)侧1/2刀尖角对应角度位置并锁定,调节主轴箱的左右位置,使金刚石刀具侧面与砂轮盘的接触点位置偏离主轴中心15mm;用800#青铜基砂轮盘粗磨刀头的侧刀面,粗磨工艺参数为:开启砂轮盘往复运动(往复运动行程30mm、运动频率0.25hz),主轴转速3600rpm,研磨压力19.6n,此工序粗磨左(或右)侧面直到在研磨机自带光学监测系统下观察该侧刃为一条光滑的直线为止;然后,把摆轴摆到右(或左)侧1/2刀尖角对应角度位置,采用相同的粗磨工艺参数,粗磨右(或左)侧刀面直到该侧刃也为一条光滑的直线并与另一侧刃相交于一点为止;
17.步骤九:用3000#青铜基砂轮盘替换800#砂轮盘,把摆轴锁定在90
°
位置,借助研磨机的光学监测系统进行对刀操作,使此时的v型刀头关于监测系统坐标系的y轴左右对称,打开光学监测系统的辅助测量功能并设置大于刀尖圆弧设计半径10μm的辅助圆,调节刀架上的微调装置,使v型刀头的两侧刃与辅助圆相切,对刀完成后锁紧刀架的微调装置;设置研磨工艺参数为:金刚石刀具侧面与砂轮盘的接触点位置偏离主轴中心15mm,开启砂轮盘往复运动(往复运动行程30mm、运动频率0.25hz),主轴转速3600rpm,研磨压力14.7n;先研
磨刀尖位置,把v型刀头研磨成梯形刀头,直到梯形短边距辅助圆5μm时停止研磨,再把摆轴置于左(右)侧60
°
位置研磨梯形刀头短边的左(右)顶点直到砂轮距辅助圆5μm停止研磨,最后把摆轴置于右(左)侧60
°
位置研磨梯形刀头短边的右(左)顶点直到砂轮距辅助圆5μm停止研磨;打开摆轴连续运转功能,并设置摆动速度10
°
/s,左右两侧驻留时间各1s,对刀头进行粗磨圆弧操作,直到刀头圆弧与辅助圆弧重合停止研磨;
18.步骤十:用研磨机自带的滚磨卡具替换带有金刚石刀具和测力仪传感器的刀架,用铸铁研磨盘替换3000#砂轮盘,把摆轴摆到90
°
位置,用单点金刚石笔对铸铁研磨盘在位修整,修整工艺参数设置为:金刚石笔与砂轮盘的接触点位置偏离主轴中心15mm,开启砂轮盘往复运动(往复运动行程30mm、运动频率0.08hz),主轴转速3600rpm,研磨压力9.8n;粗修整单次修整深度2μm,共5次,精修整单次修整深度1μm,共3次;在位修整完成后,采用激光位移传感器对研磨盘端面全跳动进行在位检测,如果研磨盘全盘面跳动小于2μm,结束修整,否则重复精修整步骤直到全盘面跳动小于2μm;
19.步骤十一:在铸铁研磨盘表面均匀涂覆w0.5的金刚石研磨膏,接着用研磨块在研磨盘表面手工预研15~20分钟后刮除研磨盘表面多余研磨膏,使研磨颗粒均匀镶嵌于铸铁研磨盘表面的孔隙内;
20.步骤十二:用带有金刚石刀具和测力仪传感器的刀架替换滚磨卡具,借助光学监测系统把刀架复位至步骤九的位置并锁紧;
21.步骤十三:用信号传输线缆连接测力仪传感器与数据采集系统,完成仪器参数设置,并预热半小时以上,在光学监测系统下设置辅助圆半径为刀尖圆弧半径的设计值;
22.步骤十四:用铸铁研磨盘对微圆弧金刚石刀具半精磨,工艺参数设置为:金刚石刀具刀尖与研磨盘接触点位置偏离主轴中心35mm,研磨盘附加往复运动(行程2mm、频率0.1hz),主轴转速3600rpm,摆轴摆速2
°
/s,研磨压力14.7n,左右两侧驻留时间各1s;用进给旋钮进给刀架,当刀具接近研磨盘时,改用微进给系统进给,实时关注光学监测系统屏幕,并结合研磨机自带的声音监测系统判断刀具与研磨盘的接触状态,当声音监测系统发出沙沙的研磨声时停止进给,并把此时的位置设置为零位;
23.步骤十五:设置测力仪测量参数并开始磨削力测量,用微进给系统继续进给刀架,同时关注磨削力的实时测量结果,当磨削力稳定在700
±
50mn附近时,停止进给,并把摆轴摆动速度设置为10
°
/s,开始半精磨,待声音监测系统无沙沙声音发出,重复步骤十四和步骤十五的操作,直到研磨去除量达到8μm;
24.步骤十六:采用步骤十四的刃磨工艺参数和步骤十五的磨削力监测方法,用微进给系统进给刀架,当磨削力达到并稳定在360
±
30mn附近时停止进给,开始精磨,待声音监测系统无沙沙声音发出,重复本步骤操作,直到研磨去除量达到2μm;
25.步骤十七:从刀具固定保持架卸下刃磨完成的微圆弧金刚石刀具,用酒精清洗刀头去除表面污物;先在1000
×
光学显微镜下观察,在切削刃无肉眼可见崩刃的情况下,进一步在4000
×
扫描电子显微镜(sem)下观察也无肉眼可见崩刃的情况下,再采用金刚石刀具半径波幅测量仪测量刀刃圆弧波纹度,若测量结果优于50nm/100
°
圆弧包角,最后用原子力显微镜(afm)在2μm
×
2μm的范围内检测切削刃形貌并测量切削刃口钝圆半径,如果无微观崩刃且切削刃口钝圆半径小于30nm,则认为该刀具刃磨质量合格;如果以上任一测量结果不满足要求则认为该刀具刃磨质量不合格,需要重复步骤十六重新刃磨,直到每项指标都
符合要求为止;
26.步骤十八:对于步骤十七检测质量合格的微圆弧金刚石刀具装盒保护,贴标签标示刀具几何参数和刃磨精度参数。
27.相比于现有技术,本发明具有如下优点:
28.1、本发明提供了一种适用于制造刀尖圆弧半径50~100μm的光学加工用高精度微圆弧金刚石刀具的机械刃磨工艺,基于磨削力大小控制和各向异性抑制的工艺思想,综合分析刃磨过程中的磨料粒度、研磨盘基体材料、研磨压力、研磨盘转速、往复运动行程、往复运动频率、摆轴摆动速度、磨削力大小等对该类微圆弧金刚石刀具刀刃圆弧波纹度、锋利度和微观缺陷的影响规律,优选工艺参数,即采用800#青铜基砂轮盘初步研磨刀具的两侧面,快速去除激光烧蚀影响层,再用3000#青铜基砂轮盘粗磨刀具的两侧面和刀尖圆弧,去除侧边800#砂轮盘研磨产生的崩口并预成型,最后用铸铁研磨盘精密研磨刀尖和侧面,完成高精度微圆弧金刚石刀具的机械刃磨加工。
29.2、本发明通过控制微圆弧金刚石刀具机械研磨的磨削力大小及各向异性进而抑制刀尖崩碎、折断和金刚石晶体材料去除率各向异性大小,即先在不产生明显崩刃的前提下通过适当增大磨削力来获得较大的材料去除率达到多于材料快速去除的目的,再通过减小磨削力来抑制其各向异性程度以获得均匀的材料去除率,达到提高刃磨精度和刃磨质量的目的。
30.3、本发明不仅加工效率高,而且消除了传统刃磨工艺对修磨操作人员经验手法的依赖性,本发明凭借刃磨机床的高精度即可在刃磨机上完成高精度微圆弧金刚石刀具的机械刃磨,最终获得刀刃圆弧波纹度优于50nm/100
°
圆弧包角、切削刃口钝圆半径优于30nm、刀尖圆弧半径50~100μm、放大4000倍无肉眼可见崩刃的一类光学加工用高精度微圆弧金刚石刀具。
附图说明
31.图1是用于加工高精度微圆弧金刚石刀具的pg3b行星型钻石刀具研磨机及测力仪传感器和刀具安装的实物照片;
32.图2是刀具毛坯准备流程图,a)八面体金刚石原石,b)沿{100}晶面切开的金刚石,c)硬质合金刀柄,d)金刚石钎焊,e)精磨前刀面;
33.图3是专门设计的用于测力仪传感器与pg3b研磨机连接的卡具和刀具固定保持架,a)装配图,b)爆炸图,图中:1、刀架本体,2、固定件1,3、刀具固定保持架,4、紧固螺栓1,5、紧固螺栓2,6、紧固螺栓3,7、金刚石刀具,8、紧固螺栓4,9、垫片,10、固定件2,11、测力仪;
34.图4是对刀操作示意图,a)左右对刀示意图,b)前后对刀示意图,c)刀头粗磨后的示意图,d)刀头半精磨前对刀的示意图;
35.图5是微圆弧金刚石刀具机械研磨时的磨削力测量结果,a)半精磨时的磨削力,b)精磨时的磨削力;
36.图6是加工完成的刀尖形貌及检测结果,a)1000
×
光学显微镜观察,b)4000
×
sem观察,c)刀刃圆弧波纹度,d)afm检测的切削刃形貌,e)切削刃钝圆半径。
具体实施方式
37.下面结合附图对本发明的技术方案作进一步的说明,但并不局限于此,凡是对本发明技术方案进行修改或者等同替换,而不脱离本发明技术方案的精神和范围,均应涵盖在本发明的保护范围中。
38.本发明提供了一种近无崩刃微圆弧金刚石刀具的力控制机械刃磨工艺,基于对磨削力大小和各向异性控制的思想来抑制刀尖崩碎、折断和金刚石晶体机械研磨材料去除率各向异性,综合分析刃磨过程中的磨料粒度、研磨盘基体材料、研磨压力、研磨盘转速、往复运动行程、往复运动频率、摆轴摆动速度、磨削力大小等对微圆弧金刚石刀具刀刃圆弧波纹度、锋利度和微观缺陷的影响规律,建立优选后的微圆弧金刚石刀具机械刃磨工艺,以此获得刀刃圆弧波纹度优于50nm/100
°
圆弧包角、切削刃口钝圆半径优于30nm、刀尖圆弧半径50~100μm、放大4000倍无肉眼可见崩刃的一类光学加工用微圆弧金刚石刀具。具体实现步骤如下:
39.步骤一:选择规整的八面体天然金刚石晶体作为刀头材料,如图2a)所示,并用激光切割机沿金刚石{100}晶面切开,如图2b)所示;选择与金刚石晶体热膨胀系数相近的硬质合金作为刀柄材料,这种材料可以有效降低后续焊接表面的残余应力,并按刀头设计参数加工成合适的形状,如图2c)所示。
40.步骤二:用金刚石平磨机把步骤一切开的金刚石晶体沿{100}晶面研磨成厚度为1~1.5mm的薄片,并保证上下研磨表面的平整度,方便步骤五精磨前刀面。
41.步骤三:用酒精清洗步骤一的刀柄和步骤二的金刚石片,以去除二者表面的污染物;然后,按前、后刀面均为{100}晶面进行定向,在刀柄和金刚石片之间加入银铜钛焊料并将其固定在刀柄之上;最后,把固定有金刚石片和焊料的刀柄置于真空焊接炉内进行钎焊,高温融化后的焊料将金刚石片与刀柄牢固的焊接在一起,如图2d)所示。
42.步骤四:用激光切割机对步骤三焊好的金刚石片进行粗成型加工,按设计好的刀尖角把金刚石片的前端加工成v型刀头,刀头侧边要伸出刀柄边缘0.2mm以上,方便后续研磨加工。
43.步骤五:用金刚石平磨机对步骤四成型粗加工完成的刀具前刀面进行精磨加工,一是保证前刀面与刀柄底面平行,二是去除步骤二残留的研磨痕迹以减小前刀面粗糙度,如图2e)所示。
44.步骤六:先用卡具把kistler 9119aa2型测力仪固定在pg3b行星型钻石刀具研磨机的刀架上,再把刀具固定保持架安装在测力仪上,最后把步骤五完成前刀面研磨的金刚石刀具毛坯固定在刀具保持架上,如图1和3所示。
45.本步骤中,利用专门设计的卡具和刀具保持架把kistler测力仪传感器固定在pg3b行星型钻石刀具研磨机上,实现了金刚石刀具机械刃磨的磨削力实时监测。
46.本步骤中,如图3所示,所述卡具包括固定件1和固定件2;所述固定件1和固定件2分别设置在测力仪的两侧;所述固定件1和固定件2的数量均为两个,分别设置在测力仪的上下端;所述固定件1、测力仪和固定件2通过紧固螺栓3固连在一起;所述固定件1通过紧固螺栓2与刀架本体固连在一起;所述刀具固定保持架包括刀具固定保持架本体和由刀具固定保持架本体侧部向外延伸的刀具安装槽,金刚石刀具通过紧固螺栓4安装在刀具安装槽内;所述刀具固定保持架本体位于两个固定件1之间且通过紧固螺栓1与测力仪固连在一
起。
47.步骤七:恒温控制pg3b行星型钻石刀具研磨机周围环境条件为25℃,恒温精度
±
0.5℃;在主轴冷却水循环系统正常工作情况下,空载运行研磨机半小时以上,使其性能达到稳定状态。
48.步骤八:把研磨机摆轴摆到左(或右)侧1/2刀尖角对应角度位置并锁定,调节主轴箱的左右位置,使金刚石刀具侧面与砂轮盘的接触点位置偏离主轴中心15mm。用800#青铜基砂轮盘粗磨刀头的侧刀面,粗磨工艺参数为:开启砂轮盘往复运动(往复运动行程30mm、运动频率0.25hz),主轴转速3600rpm,研磨压力19.6n。此工序粗磨左(或右)侧面直到在研磨机自带光学监测系统下观察该侧刃为一条光滑的直线为止。然后,把摆轴摆到右(或左)侧1/2刀尖角对应角度位置,采用相同的工艺参数,粗磨右(或左)侧刀面直到该侧刃也为一条光滑的直线并与另一侧刃相交于一点为止。
49.步骤九:用3000#青铜基砂轮盘替换800#砂轮盘。把摆轴锁定在90
°
位置,借助研磨机的光学监测系统进行对刀操作,使此时的v型刀头关于监测系统坐标系的y轴左右对称,如图4a)所示,打开光学监测系统的辅助测量功能并设置大于刀尖圆弧设计半径10μm的辅助圆,调节刀架上的微调装置,使v型刀头的两侧刃与辅助圆相切,如图4b)所示,对刀完成后锁紧刀架的微调装置。设置研磨工艺参数为:金刚石刀具侧面与砂轮盘的接触点位置偏离主轴中心15mm,开启砂轮盘往复运动(往复运动行程30mm、运动频率0.25hz),主轴转速3600rpm,研磨压力14.7n。先研磨刀尖位置,把v型刀头研磨成梯形刀头,直到梯形短边距辅助圆5μm时停止研磨,再把摆轴置于左(右)侧60
°
位置研磨梯形刀头短边的左(右)顶点直到砂轮距辅助圆5μm停止研磨,最后把摆轴置于右(左)侧60
°
位置研磨梯形刀头短边的右(左)顶点直到砂轮距辅助圆5μm停止研磨。打开摆轴连续运转功能,并设置摆动速度10
°
/s,左右两侧驻留时间各1s,对刀头进行粗磨圆弧操作,直到刀头圆弧与辅助圆弧重合停止研磨,如图4c)所示。
50.步骤十:用研磨机自带的滚磨卡具替换带有金刚石刀具和测力仪传感器的刀架,用铸铁研磨盘替换3000#砂轮盘,把摆轴摆到90
°
位置,用单点金刚石笔对铸铁研磨盘在位修整,修整工艺参数设置为:金刚石笔与砂轮盘的接触点位置偏离主轴中心15mm,开启砂轮盘往复运动(往复运动行程30mm、运动频率0.08hz),主轴转速3600rpm,研磨压力9.8n。粗修整单次修整深度2μm,共5次,精修整单次修整深度1μm,共3次。在位修整完成后,采用激光位移传感器对研磨盘端面全跳动进行在位检测,如果研磨盘全盘面跳动小于2μm,结束修整,否则重复精修步骤直到全盘面跳动小于2μm。
51.步骤十一:在铸铁研磨盘表面均匀涂覆w0.5的金刚石研磨膏,接着用研磨块在研磨盘表面手工预研15~20分钟后刮除研磨盘表面多余研磨膏,使研磨颗粒均匀镶嵌于铸铁研磨盘表面的孔隙内。
52.步骤十二:用带有金刚石刀具和测力仪传感器的刀架替换滚磨卡具,借助光学监测系统把刀架复位至步骤九的位置并锁紧。
53.步骤十三:用信号传输线缆连接测力仪传感器与数据采集系统,完成仪器参数设置,并预热半小时以上。在光学监测系统下设置辅助圆半径为刀尖圆弧半径的设计值,如图4d)所示。
54.步骤十四:用铸铁研磨盘对微圆弧金刚石刀具半精磨,工艺参数设置为:金刚石刀
具刀尖与研磨盘接触点位置偏离主轴中心35mm,研磨盘附加往复运动(行程2mm、频率0.1hz),主轴转速3600rpm,摆轴摆速2
°
/s,研磨压力14.7n,左右两侧驻留时间各1s。用进给旋钮进给刀架,当刀具接近研磨盘时,改用微进给系统进给,实时关注光学监测系统屏幕,并结合研磨机自带的声音监测系统判断刀具与研磨盘的接触状态,当声音监测系统发出沙沙的研磨声时停止进给,并把此时的位置设置为零位。
55.步骤十五:设置测力仪测量参数并开始磨削力测量,用微进给系统继续进给刀架,同时关注磨削力的实时测量结果,当磨削力稳定在700
±
50mn附近时,如图5a)所示,停止进给,并把摆轴摆动速度设置为10
°
/s,开始半精磨,待声音监测系统无沙沙声音发出,重复步骤十四和步骤十五的操作,直到研磨去除量达到8μm。
56.本步骤中,把半精磨的磨削力控制在700
±
50mn范围内是抑制刀尖崩刃缺陷和刀尖折断的核心工艺措施。
57.步骤十六:采用步骤十四的刃磨工艺参数和步骤十五的磨削力监测方法,用微进给系统进给刀架,当磨削力达到并稳定在360
±
30mn附近时,如图5b)所示,停止进给,开始精磨,待声音监测系统无沙沙声音发出,重复本步骤操作,直到研磨去除量达到2μm。
58.本步骤中,把精磨的磨削力控制在360
±
30mn范围内是抑制金刚石晶体材料去除率各向异性,保证微圆弧金刚石刀具刃磨精度和切削刃口钝圆半径(又称锋利度)的核心工艺措施。
59.步骤十七:从刀具固定保持架卸下刃磨完成的微圆弧金刚石刀具,用酒精清洗刀头去除表面污物。先在1000
×
光学显微镜下观察,在切削刃无肉眼可见崩刃的情况下,如图6a)所示,进一步在4000
×
扫描电子显微镜(sem)下观察也无肉眼可见崩刃的情况下,如图7b)所示,再采用金刚石刀具半径波幅测量仪测量刀刃圆弧波纹度,若测量结果优于50nm/100
°
圆弧包角,如图6c)所示,最后用原子力显微镜(afm)在2μm
×
2μm的范围内检测切削刃形貌并测量切削刃口钝圆半径,如果无微观崩刃且切削刃口钝圆半径小于30nm,如图6d)所示,则认为该刀具刃磨质量合格。如果以上任一测量结果不满足要求则认为该刀具刃磨质量不合格,需要重复步骤十六重新刃磨,直到每项指标都符合要求为止。
60.步骤十八:对于步骤十七检测质量合格的微圆弧金刚石刀具装盒保护,贴标签标示刀具几何参数和刃磨精度参数。