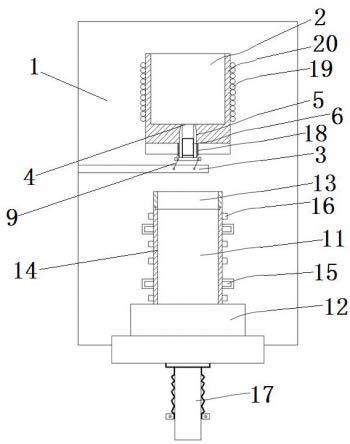
1.本发明属于集成电路用高纯金属熔炼与铸造技术领域,具体涉及一种高纯铜及铜合金铸锭的制备装置及方法。
背景技术:2.高纯金属溅射靶材广泛应用于信息存储、集成电路、平面显示、太阳能电池等产业,主要通过磁控溅射技术获得各种薄膜功能材料。目前,按照化学成分可将溅射靶材分为:纯金属靶材,如铝、铜、钛、钽、钴等;合金靶材,如铝铜、铝硅、铜磷、铜铝、铜锰、钨钛、镍铂、镍钴、镍钒等。依据摩尔定律,芯片制造工艺持续进步,不断迭代更新。随着芯片制程与制造技术的发展,对各种材料的性能也提出了越来越高的要求。作为集成电路芯片互连线材料,90nm及以上制程采用铝及铝合金材料,90-45nm制程采用高纯铜材料,45-7nm制程以超高纯铜铝、铜锰合金材料为主,在7nm以下制程则采用高纯钴作为互连材料。因此,高纯铜及铜合金溅射靶材的重要性日益显现。
3.如前所述,超高纯铜合金靶材是45nm及以下制程集成电路互连用关键支撑材料。纯铜具有更低的电阻率和更高的导热性,且具有比al高两个数量级的抗电迁移能力。将铜作为优良的互连材料不仅可以降低延迟,提高运算效率,而且还可以保证集成电路的可靠性。另外,向高纯铜中添加al、mn等微量合金元素,利用微合金化形成自发扩散阻挡层或者界面阻挡层可以进一步减小线宽。因此,高纯铜及铜合金溅射靶材是未来市场竞争的主要方向。
4.高纯铜及铜合金铸锭的制备是高纯铜及铜合金溅射靶材制造的基础。从现阶段取得的成果看,高纯铜及铜合金铸锭的品质是产品开发的重要环节,作为靶材生产的上游,其质量优劣直接影响靶材使用性能和客户满意程度。高纯铜及合金铸锭的制备方法通常是在真空感应炉中进行熔炼,并采用倾转坩埚静模铸造的方法获得目标尺寸的铸锭,其特征在于纯度高、周期短、成本低。然而,在现有设备条件下的实际生产过程中,所获得的铸锭往往存在较多的内部冶金缺陷,缺陷的种类主要包括气孔、疏松、夹杂、裂纹等,缺陷的产生主要是由于传统熔炼与铸造设备及工艺方法的局限性。因此,开发新型高纯金属的熔炼与铸造设备及工艺方法,提升高纯金属铸锭质量,对于高纯铜及铜合金溅射靶材行业降本增效、提升产品质量稳定性具有重要的现实意义。
技术实现要素:5.针对上述已有技术存在的不足,本发明提供一种高纯铜及铜合金铸锭的制备装置及方法。
6.本发明是通过以下技术方案实现的。
7.一种高纯铜及铜合金铸锭的制备装置,其特征在于,所述装置包括:熔炼炉腔,以及自上而下设置在熔炼炉腔内的熔炼装置、铸造装置;所述熔炼装置包括坩埚、流嘴组件、可移动式托盘,所述流嘴组件插装在所述坩埚底部开设的出料口中,所述可移动式托盘设
置在所述坩埚出料口的下面;所述铸造装置包括铸模、底托,所述铸模的上端开口与所述坩埚出料口正对,所述铸模设置在底托上。
8.进一步地,所述流嘴组件包括外导管、以及可拆卸的套装在外导管中的内管,所述外导管的外壁与所述坩埚出料口的内壁固定套接;所述外导管的下部外设有感应线圈。
9.进一步地,所述外导管为锥形管,所述内管为中空圆柱形管。
10.进一步地,所述可移动式托盘包括上托盘、下托杆,所述上托盘与下托杆的一端杆体之间通过四连杆机构连接,所述下托杆的另一端与设置在熔炼炉腔外部的电动推杆连接。
11.进一步地,所述铸模为水冷铜模具,包括上下开口的圆筒型壳体,所述圆筒型壳体为通过卡箍连接的两个相对设置的半圆形板组成,所述圆筒型壳体的外壁设有循环冷却水管路。
12.进一步地,所述铸模的顶部设有冒口。
13.进一步地,所述底托为水冷铜托,包括上下封闭的中空圆筒,所述中空圆筒的底部设有进水口,侧壁上部设有出水口,所述底托设置在熔炼炉腔的底部,所述底托的底部与设置在熔炼炉腔外的伺服电机连接。
14.进一步地,所述坩埚为电磁感应加热式坩埚。
15.一种采用上述装置制备高纯铜及铜合金铸锭的方法,其特征在于,所述方法包括:(1)将可移动式托盘置于坩埚出料口的下端,将出料口封住;(2)将高纯铜原料置于坩埚中经一次熔化、冷却、二次熔化、精炼,其中,当制备铜合金铸锭时,将合金原料在二次熔化过程中加入,然后得到高纯铜或铜合金熔体;(3)移动可移动式托盘脱离坩埚出料口,高纯铜或铜合金熔体经流嘴组件进入到铸模中,冷却后获得高纯铜或铜合金铸锭。
16.进一步地,所述步骤(2)一次熔化:抽真空至真空度≤1
×
10-2
pa,加热温度1200~1300℃,加热时间30~60min;冷却时间1h;二次熔化:加热温度1200~1300℃,加热时间15~30min;精炼:温度1300~1350℃,向炉膛内充入氩气,至炉内压力为-0.09~-0.05mpa。
17.进一步地,所述步骤(3)通过伺服电机带动底托沿水平方向往复式旋转。
18.采用本发明制备的高纯铜或铜合金铸锭的纯度为≥99.9999%(6n),甚至可以达到≥99.99995%(6n5)或者≥99.99999%(7n),氧含量≤1ppm、碳含量≤1ppm、氮含量≤1ppm,合金成分波动<5%,直径为φ200~φ400 mm,铸锭组织中无气孔、疏松、夹杂等冶金缺陷。
19.本发明的有益技术效果:(1)本发明采用坩埚底部漏铸实现铸造,坩埚中的金属熔体通过底部流嘴组件,注入下方铸模中,因此浮于坩埚中金属熔体液面顶层的氧化物或夹杂等最后流入铸模,集中分布于铸锭顶部,从而可在后序锯切缩孔时将其一并去除,降低了氧化物夹杂等进入铸锭组织内部造成缺陷的风险;(2)本发明提供的铸模为水冷铜铸模、底托为水冷铜底托,熔体进入铸模后,在轴向和径向均备有循环水冷却,更易于获得表面质量优良、晶粒细小的高纯金属铸锭,可有效提高成材率,同时铸锭表面光滑,更易于脱模,可大大延长铸模的使用寿命,同时在循环水的强冷却速率下,铸锭出炉时间大为缩短,生产效率获得显著提升;(3)铸造过程开启伺服电机,带动底托可沿水平方向做左右往复式震动,使合金熔
体成分均匀,成分波动<5%,细化晶粒尺寸,提高金属熔体填充能力减少疏松、气孔等冶金缺陷;(4)熔炼方式采用真空感应熔炼,在熔炼过程中通过降温,可以保证气体充分逸出,有利于获得高洁净度、低气体含量的金属熔体;(5)本发明的整个装置结构紧凑简单、熔炼与铸造工艺简便可靠,有助于消除或减少铸锭组织中的气孔、疏松、夹杂等冶金缺陷,有效提高铸锭产品的良率和成材率,显著提升生产效率。
附图说明
20.图1为本发明实施例中装置的结构示意图。
21.图2为本发明部分结构示意图。
22.图3为本发明实施例中方法的工艺流程图。
23.图4为本发明实施例中高纯铜铸锭的内部冶金缺陷c扫图。
24.图5为本发明实施例中高纯铜铝合金铸锭的内部冶金缺陷c扫图。
25.图6为本发明实施例中高纯铜锰合金铸锭的内部冶金缺陷c扫图。
具体实施方式
26.下面结合附图和具体实施方式对本发明进行详细说明。
27.如图1-2所示,一种高纯铜及铜合金铸锭的制备装置,包括:熔炼炉腔1,以及自上而下设置在熔炼炉腔内的熔炼装置、铸造装置;熔炼炉腔1为真空熔炼腔室,真空度在10-3
pa-10-1
pa范围内;熔炼装置包括坩埚2、流嘴组件、可移动式托盘3;坩埚2为电磁感应加热式坩埚,包括圆筒形坩埚,坩埚2外壁与电磁感应线圈20之间衬以绝缘隔热层19,绝缘隔热层19靠近电磁感应线圈20的一面为起绝缘作用的云母板,靠近坩埚2的一面为起隔热、保温作用的石棉板或硅酸铝毡等,位于熔炼炉腔1的内上部,通过支架支撑,用于盛放金属熔体,利用电磁感应加热原理,使坩埚2内的固态金属熔体成液态金属熔体;流嘴组件插装在坩埚2底部开设的出料口4中,具体地,流嘴组件包括外导管5、以及可拆卸的套装在外导管5中的内管6,外导管5的外壁与坩埚出料口4的内壁固定套接,外导管5为上下端开放的中空的锥形管,具体可以为石墨导管,内管6为上下端开放的中空圆柱形管,内管6能够紧密的并且可拆卸地插装在外导管5内下部中,在外导管5的下部外设有感应线圈18,用于对内管6中的熔体加热;可移动式托盘3设置在坩埚出料口4的下面,可移动式托盘3包括上托盘7、下托杆8,上托盘7与下托杆8的一端杆体之间通过四连杆机构9连接,具体地,四连杆机构9包括前后两组连杆,每组包括两根连杆,连杆的上下两端均设有连接孔,连杆的上端与上托盘7通过销轴连接、下端与下托杆8的端杆体通过销轴连接,下托杆8的另一端与设置在熔炼炉腔外部的电动推杆10连接;铸造装置包括铸模11、底托12,铸模11的上端开口与坩埚出料口正对,铸模11设置在底托12的上面,铸模11的顶部设有冒口13,在熔体全部由坩埚2转入铸模11后起到保温补缩的作用,从而减小铸锭的缩孔深度,提升铸锭成材率;具体地,铸模11为水冷铜模具,具体可以为紫铜材质,包括上下开口的圆筒型壳体14,顶部开口作为浇口,圆筒型壳体14可以为
通过上下两个卡箍15连接的两个相对设置的半圆形板组成,通过卡箍15防止作业过程中铸模11分开产生漏液,导致铸锭不能成型或几何尺寸异常,圆筒型壳体14的外壁设有循环冷却水管路16,具体可以为金属波纹管,用于加速铸锭冷却,提高生产效率。
28.进一步地,底托12为水冷铜托,具体可以为紫铜材质,包括上下封闭的中空圆筒,中空圆筒的底部设有进水口,侧壁上部设有出水口,用于与循环冷却水管路连接,底托12设置在熔炼炉腔1的底部,上部位于熔炼炉腔1内,底部与设置在熔炼炉腔外的伺服电机17连接。底托用于提高铸锭底部冷却速率。
29.实施例1如图3所示,一种采用上述装置制备高纯铜铸锭的方法,包括:(1)通过电动推杆10带动可移动式托盘3移动至坩埚出料口4的下端,将出料口4封住;(2)将高纯铜原料按一定堆叠顺序置于坩埚2中,关闭熔炼炉腔1开设的炉门,对炉内抽真空至真空度≤1
×
10-2
pa,开启与电磁感应加热式坩埚2连接的加热电源对原料加热进行一次熔化,当电流流经感应线圈时,利用电磁感应加热的原理使坩埚2中的金属固体熔化,至原料完全熔化成液态熔体后停止加热,加热温度从室温到1300℃,加热时间60min;关闭电源使熔体自然降温冷却1h,溶于金属熔体中的氮、氧、碳以及其他蒸汽压较熔炼金属高的杂质元素充分逸出,从而达到除气、除杂、净化熔体的目的;再次开启电源加热,进行二次熔化,加热温度1300℃,加热时间15min,提升温度至1350℃精炼铜熔体,同时向炉膛内充入氩气,至炉内压力-0.09~-0.05mpa进一步除气除杂,提高铸锭的表面质量;对于金属熔体温度的监控主要有两个位置,其一为坩埚2的温度:将测温保护管固定在坩埚外壁上,利用热电偶实时监测坩埚温度;其次为外导管5的温度:将测温保护管插在外导管5外壁,利用铠装钨铼热电偶实时监测和控制外导管5内感应加热的温度;(3)熔炼完成后,进入到浇铸阶段,在浇铸之前,对外导管5外的感应线圈18通电,使进入到流嘴组件中的冷凝的金属熔体加热熔化,移动可移动式托盘3脱离坩埚出料口4,上述制备好的高纯铜熔体经流嘴组件进入到铸模11中充型,通过伺服电机17带动底托12沿水平方向往复式旋转,获得晶粒细小、冶金缺陷少的内部组织,经过循环冷却水的作用下熔体冷凝后获得高纯铜铸锭。
30.在整个铸造过程中,铸模11和底托12设有的循环冷却水管路即金属波纹管内的冷却循环水始终处于运行状态,使铸模11内熔体在轴向和径向上均可实现快速冷却,既可保证铸锭的表面质量和内部微观组织,又可避免金属熔体凝固时外壁与铸模11内壁的粘连,利于延长铸模的使用寿命,此外还可缩短出炉时间,极大地提高生产效率。采用紫铜材质铸模可避免浇铸过程中,金属熔体与铸模材料发生反应,使铸锭表面产生杂质而被污染,降低铸锭质量。
31.通过本发明的实施例,可获得尺寸为φ400
×
700mm、纯度≥99.99999%(7n),氧含量≤1ppm、碳含量≤1ppm、氮含量≤1ppm,内部洁净无缺陷的高纯铜铸锭。图4为本发明实施例的高纯铜铸锭的内部冶金缺陷c扫图。表1为本发明实施例的高纯铜铸锭的纯度检测结果。
32.表1 高纯铜铸锭的纯度检测结果
实施例2如图3所示,一种采用上述装置制备高纯铜铝铸锭的方法,包括:(1)通过电动推杆10带动可移动式托盘3移动至坩埚出料口4的下端,将出料口4封住;(2)将高纯铜原料按一定堆叠顺序置于坩埚2中,关闭熔炼炉腔1开设的炉门,对炉内抽真空至真空度≤1
×
10-2
pa,开启与电磁感应加热式坩埚2连接的加热电源对原料加热进行一次熔化,当电流流经感应线圈时,利用电磁感应加热的原理使坩埚2中的金属固体熔化,至原料完全熔化成液态熔体后停止加热,加热温度从室温到1250℃,加热时间45min;关
闭电源使熔体自然降温冷却1h,溶于金属熔体中的氮、氧、碳以及其他蒸汽压较熔炼金属高的杂质元素充分逸出,从而达到除气、除杂、净化熔体的目的;再次开启电源加热,进行二次熔化,加热温度1250℃,加热时间20min,将合金原料高纯铝加入,然后得到高纯铜铝合金熔体;提升温度至1320℃精炼铜铝合金熔体,同时向炉膛内充入氩气,至炉内压力为-0.09~-0.05mpa进一步除气除杂,提高铸锭的表面质量;对于金属熔体温度的监控主要有两个位置,其一为坩埚2的温度:将测温保护管固定在坩埚2外壁上,利用热电偶实时监测坩埚2温度;其次为外导管5的温度:将测温保护管插在外导管5外壁,利用铠装钨铼热电偶实时监测和控制外导管5内感应加热的温度;(3)熔炼完成后,进入到浇铸阶段,在浇铸之前,对外导管5外的感应线圈18通电,使进入到流嘴组件中的冷凝的金属熔体加热熔化,移动可移动式托盘3脱离坩埚出料口4,上述制备好的高纯铜铝合金熔体经流嘴组件进入到铸模11中充型,通过伺服电机17带动底托12沿水平方向往复式旋转,使合金熔体成分均匀,获得晶粒细小、冶金缺陷少的内部组织,经过循环冷却水的作用下熔体冷凝后获得高纯铜铝合金铸锭。
33.在整个铸造过程中,铸模11和底托12设置的循环冷却水管路即金属波纹管内的冷却循环水始终处于运行状态,使铸模11内熔体在轴向和径向上均可实现快速冷却,既可保证铸锭的表面质量和内部微观组织,又可避免金属熔体凝固时外壁与铸模11内壁的粘连,利于延长铸模的使用寿命,此外还可缩短出炉时间,极大地提高生产效率。采用紫铜材质铸模可避免浇铸过程中,金属熔体与铸模材料发生反应,使铸锭表面产生杂质而被污染,降低铸锭质量。
34.通过本发明的实施例,可获得尺寸为φ300
×
700mm、纯度≥99.99995%(6n5),氧含量≤1ppm、碳含量≤1ppm、氮含量≤1ppm,al合金成分波动<5%,内部洁净无缺陷的高纯铜铝合金铸锭。图5为本发明实施例的高纯铜铝合金铸锭的内部冶金缺陷c扫图。表2为本发明实施例的高纯铜铝合金铸锭的纯度检测结果。
35.表2 高纯铜铝合金铸锭的纯度检测结果
ꢀ
实施例3如图3所示,一种采用上述装置制备高纯铜锰铸锭的方法,包括:(1)通过电动推杆10带动可移动式托盘3移动至坩埚出料口4的下端,将出料口4封住;(2)将高纯铜原料按一定堆叠顺序置于坩埚2中,关闭熔炼炉腔1开设的炉门,对炉内抽真空至真空度≤1
×
10-2
pa,开启与电磁感应加热式坩埚2连接的加热电源对原料加热进行一次熔化,当电流流经感应线圈时,利用电磁感应加热的原理使坩埚2中的金属固体熔化,至原料完全熔化成液态熔体后停止加热,加热温度从室温到1200℃,加热时间30min;关
闭电源使熔体自然降温冷却1 h,溶于金属熔体中的氮、氧、碳以及其他蒸汽压较熔炼金属高的杂质元素充分逸出,从而达到除气、除杂、净化熔体的目的;再次开启电源加热,进行二次熔化,加热温度1200℃,加热时间30min,将合金原料高纯锰加入,然后得到高纯铜锰合金熔体;提升温度至1300℃精炼铜锰合金熔体,同时向炉膛内充入氩气,至炉内压力为-0.09~-0.05mpa进一步除气除杂,提高铸锭的表面质量;对于金属熔体温度的监控主要有两个位置,其一为坩埚2的温度:将测温保护管固定在坩埚2外壁上,利用热电偶实时监测坩埚温度;其次为外导管5的温度:将测温保护管插在外导管5外壁,利用铠装钨铼热电偶实时监测和控制外导管5内感应加热的温度;(3)熔炼完成后,进入到浇铸阶段,在浇铸之前,对外导管5外的感应线圈18通电,使进入到流嘴组件中的冷凝的金属熔体加热熔化,移动可移动式托盘3脱离坩埚出料口4,上述制备好的高纯铜锰合金熔体经流嘴组件进入到铸模11中充型,通过伺服电机17带动底托12沿水平方向往复式旋转,使合金熔体成分均匀,获得晶粒细小、冶金缺陷少的内部组织,经过循环冷却水的作用下熔体冷凝后获得高纯铜锰合金铸锭。
36.在整个铸造过程中,铸模11和底托12设有的循环冷却水管路即金属波纹管内的冷却循环水始终处于运行状态,使铸模11内熔体在轴向和径向上均可实现快速冷却,既可保证铸锭的表面质量和内部微观组织,又可避免金属熔体凝固时外壁与铸模11内壁的粘连,利于延长铸模的使用寿命,此外还可缩短出炉时间,极大地提高生产效率。采用紫铜材质铸模可避免浇铸过程中,金属熔体与铸模材料发生反应,使铸锭表面产生杂质而被污染,降低铸锭质量。
37.通过本发明的实施例,可获得尺寸为φ200
×
700mm、纯度≥99.9999%(6n),氧含量≤1ppm、碳含量≤1ppm、氮含量≤1ppm,mn合金成分波动<5%,内部洁净无缺陷的高纯铜锰合金铸锭。图6为本发明实施例的高纯铜锰合金铸锭的内部冶金缺陷c扫图。表3为本发明实施例的高纯铜锰合金铸锭的纯度检测结果。
38.表3 高纯铜锰合金铸锭的纯度检测结果
相比传统熔炼工艺,本发明坩埚2内部的液态金属材料由于受到电磁力的作用,可实现充分搅拌,在浇铸时金属熔体的成分更加均匀。同时在熔炼过程中,可通过控制真空度以及加热功率,调整熔炼温度,使金属熔体中的氮、氧、碳以及其他蒸汽压较熔炼金属高的杂质元素充分逸出,从而达到除气、除杂、净化熔体的目的。相比传统铸造工艺,本发明采用坩埚2底部漏铸,坩埚2中的金属熔体通过底部流嘴,注入下方铸模11中,因此浮于坩埚2中金属熔体液面顶层的氧化物或夹杂等最后流入铸模11,集中分布于铸锭顶部,从而可在后序锯切缩孔时将其一并去除,降低了氧化物夹杂等进入铸锭组织内部造成缺陷的风险,有助于获得内部洁净无缺陷的高纯铜及铜合金铸锭。
39.以上所述的仅是本发明的较佳实施例,并不局限发明。应当指出对于本领域的普通技术人员来说,在本发明所提供的技术启示下,还可以做出其它等同改进,均可以实现本发明的目的,都应视为本发明的保护范围。