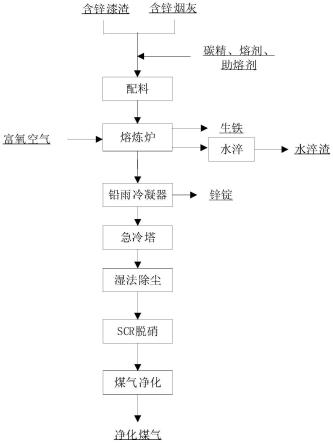
1.本发明涉及一种钢厂含锌烟灰与含锌漆渣的协同处理方法,属于有色金属综合回收技术领域。
背景技术:2.钢厂含锌烟灰主要以高炉瓦斯灰(泥)与电炉灰为主,瓦斯灰(泥)中的锌主要是由于原料低品位的锌在“大、小循环”过程中不断富集而来,而电炉灰主要是由于采用废钢冶炼过程中原料含锌较高,从而导致烟尘中具有较高的锌含量。
3.目前,对于含锌烟灰处置的火法工艺主要有回转窑还原法以及转底炉法,其产品主要以直接还原铁为主,锌则主要进入烟气再氧化后,进入烟尘得到次氧化锌产品。直接还原铁仍需配入高炉内进行熔炼,无法直接用于炼钢。
4.含锌漆渣危废类别为hw12燃料、涂料废物。其中,含有锌、铁、有机物等有价成分,同时具有硅、钙等造渣成分。传统的油漆渣处理方法是用低温焚烧或热解的方法进行处置,但仅能对其中有机物进行利用,对其中的金属回收率较低。因此,有必要研究开发一种能有效处理废油漆渣、生产环境清洁、金属回收率高的工艺,以满足废油漆渣危废处理的现实需求。
5.中国发明专利申请cn103740939a公开了一种利用钢铁厂含锌尘泥生产铁水并回收锌的方法。该方法包括以下步骤:将干燥的钢铁厂含锌尘泥与粘结剂、水混合均匀得到混合原料;将混合原料进行冷固结成型,得到球团或砖块;将冷固结的球团或砖块送入烘干机或链篦机上烘干到含水量≤1wt%;将经过烘干的球团或砖块与焦炭、熔剂混合进行还原冶炼,得到铁水和锌蒸汽;将含有锌蒸汽的煤气引出,利用热旋风除尘器除去粗粒粉尘,利用余热锅炉回收煤气显热,经过换热器进行换热,再利用布袋除尘器进行精除尘,得到高锌粉尘。该方法需要在较高温度下(》1500℃)才能进行,与常规炼铁工艺无异。
技术实现要素:6.针对现有技术的不足,本发明的目的在于提供一种能耗低的钢厂含锌烟灰与含锌漆渣的协同处理方法。
7.为了解决上述技术问题,本发明的技术方案如下:
8.一种钢厂含锌烟灰与含锌漆渣的协同处理方法,包括如下步骤:
9.s1、将含锌混合料、还原剂、造渣剂、钠盐和氟盐混合均匀,获得混合物料;
10.其中,含锌混合料由钢厂含锌烟灰和含锌漆渣混合而成;所述还原剂的添加量为含锌混合料的10-30wt%,所述造渣剂的添加量为含锌混合料的0-20wt%,所述钠盐的添加量为含锌混合料的1-10wt%,所述氟盐的添加量为含锌混合料的1-10wt%;
11.s2、将所述混合物料加入到熔炼炉中,于1300-1500℃条件下,通入富氧空气进行熔炼,获得富锌烟气和上、下分层的熔融渣和熔融铁水;
12.其中,熔炼期间,控制熔炼炉内co、co2的摩尔比>1.2;一般地,通过混合物料中还
原剂添加量以及熔炼过程中富氧空气通入量及浓度的控制,即可调控co、co2的摩尔比>1.2;
13.s3、对所述富锌烟气进行冷凝,获得金属锌和剩余烟气。
14.本发明将钢厂含锌烟灰与含锌漆渣的协同处理,可充分利用含锌漆渣的热值与钙、硅等造渣成分,高效回收其中的锌、铁有价组分。同时,本发明通过添加钠盐、氟盐,构建出cao-sio
2-mgo-na2o-caf2五元渣系,可有效的降低整个熔炼体系的熔点与黏度,从而实现低温处置钢厂含锌烟灰和含锌漆渣,并且通过熔炼和冷凝处理即可获得产品金属锌与生铁,处理流程短,有助于节能降耗。
15.本发明中,熔炼炉内反应体系的酸碱度(cao+mgo)/(sio2)=0.6~1.4(即cao、mgo的总质量与sio2的质量之比),可优选控制为0.6~1.0。
16.进一步地,s1中,所述钠盐为硫酸钠、碳酸钠、氯化钠中的一种或几种,优选为碳酸钠;所述氟盐为氟化钠、氟化钾、氟化镁、氟化钙中的一种或几种,优选为氟化钙。
17.进一步地,s1中,所述还原剂的添加量为含锌混合料的15-35wt%,更进一步为20-30wt%;所述造渣剂的添加量为含锌混合料的5-15wt%,更进一步为8-12wt%。
18.进一步地,s2中,富氧空气的浓度>40vol%,优选为50~80vol%,从而有效降低烟气产生量以增加锌蒸汽浓度,降低后续冷凝工序的作业压力。
19.进一步地,s2中,控制熔炼炉的烟气出口处的烟气温度>1000℃,优选为1050~1150℃,如此,可进一步防止烟气中锌的氧化。
20.可选地,富锌烟气中锌蒸汽的浓度≥5vol%。
21.进一步地,s2中,熔炼期间,控制熔炼炉内co、co2的摩尔比为1.4-1.8,优选为1.5-1.7。
22.由此,通过控制熔炼炉内co、co2的摩尔比,控制还原气氛,既保证了铁与锌的充分还原,又防止了锌冷凝过程中被二次氧化。
23.可选地,s2中,熔炼温度为1350-1450℃。
24.可选地,对熔融渣进行水淬,获得水淬渣。水淬渣可外售。
25.熔炼过程中主要反应如下:
26.(1)氧化还原反应:
27.2c+o2=2co
28.znfe2o4+c=zno+2feo+co(g)
29.zno+co=zn+co230.2zn+o2=2zno
31.2fe2o3+c=4feo+co232.feo+c=2fe+co233.fe2o3+co=2feo+co234.feo+co=fe+co235.zn2sio4+na2o=2zno+na2sio336.*2feo*sio2+na2o=2feo+na2sio337.fe+c=fe3c
38.(2)造渣反应
39.na2o+sio2=na2sio340.mgo+sio2=mgo
·
sio241.cao+sio2=cao
·
sio242.进一步地,s3中,采用铅雨冷凝器对富锌烟气进行冷凝,使得富锌烟气温度降低至500℃以下。在500℃左右锌蒸汽具有一个较低的饱和蒸汽压,从而保证锌的高效回收,锌蒸汽以锌液的形式冷凝至铅雨池,经沉淀分层排出得到锌锭。
43.可选地,对剩余烟气依次进行降温、除尘、scr脱硝、煤气净化后,获得干净煤气。可选地,通过急冷塔进行降温;可选地,进行湿法除尘。具体地,经铅雨冷凝后的剩余烟气经碱液急冷塔进行喷淋降温,降温区间为500~200℃,从而避开二噁英合成区间,防止含锌漆渣燃烧后可能产生的含氯烟气再次合成二噁英,同时脱除烟气中可能存在的二氧化硫。随后经湿式除尘,煤气净化等工艺得到干净煤气。
44.进一步地,s1中,所述还原剂为碳精、废活性炭、焦煤、无烟煤、碳精、焦炭中的一种或几种;所述造渣剂为石英石、石灰石、白云石中的一种或几种。
45.进一步地,s1中,所述还原剂的添加量为含锌混合料的15-25wt%,更进一步为18-22wt%,所述造渣剂的添加量为含锌混合料的2-18wt%,更进一步为5-15wt%。
46.进一步地,s1中,所述钢厂含锌烟灰中,zn含量为10~50wt%,fe含量为20~50wt%。
47.可选地,所述钢厂含锌烟灰中,zn含量为15~30wt%,fe含量为22~35wt%,si含量为0.5-3.5wt%,ca含量为0.5-3wt%,mg含量为0-1wt%,mn含量为0-1.5wt%,cu含量为0-0.8wt%。
48.进一步地,所述含锌漆渣中,zn含量为1~50wt%,fe含量为1~20wt%。可选地,含锌漆渣的热值(低位热值)为2000~4000kcal,进一步为25000-3500kcal。
49.可选地,所述含锌漆渣中,zn含量为5~20wt%,fe含量为5~20wt%,si含量为0.5-5wt%,ca含量为0-1.5wt%,mg含量为0-1wt%,c含量为15-45wt%,h含量为1-8wt%。
50.进一步地,所述钠盐的添加量为含锌混合料的2-8wt%,优选为4-6wt%。
51.进一步地,所述氟盐的添加量为含锌混合料的2-8wt%,优选为4-6wt%。
52.进一步地,s1中,含锌混合料由钢厂含锌烟灰和含锌漆渣按1-5:1(优选为1-3:1)的质量比混合而成。
53.进一步地,s2中,熔炼时间为0.5-2h,更进一步为0.75-1.5h,优选为1-1.25h。
54.含锌漆渣具有较高的热值,通过对钢厂含锌烟灰和含锌漆渣进行配比,可保证还原剂仅用于还原锌、铁氧化物,无需再添加额外的煤作为燃料。同时,通过熔炼,含锌漆渣中的有机物可被充分燃烧,熔渣经水淬得到无害化水淬渣,从而达到无害化的目的。
55.申请人研究发现,本发明通过钠盐与氟盐共同造渣,可以得到低熔点低黏度渣型,实现含锌烟灰的低温熔炼;而单一添加钠盐或氟盐,无法获得预想的效果。
56.与现有技术相比,本发明的有益效果如下:
57.1)本发明通过以废治废的方式,对含锌漆渣与钢厂含锌烟灰进行协同处置,充分利用含锌漆渣附带的高热值的同时,对其中的锌、铁进行回收。并且通过合适的配比,可实现仅靠漆渣提供热源,仅需添加少量无烟煤等物质作为锌、铁的还原剂,极大的降低了能耗。一般的,对钢厂含锌烟灰的直接炼锌、铁工艺,煤耗大概为650~800kg/t-含锌烟灰,熔
炼温度需要到1600℃;本发明通过配入高热值含锌漆渣,同时开发低熔点渣型,同时通过富氧熔炼,可将煤耗降至200kg~400kg/t-含锌烟灰。
58.2)本发明解决了含锌漆渣、钢厂含锌烟灰无法一步高效回收其中有价金属的问题,同时通过富氧熔炼对含锌、铁危险废料进行一步分离提纯直接得到产品锌锭与生铁,极大的缩短现有工艺流程,增加能源利用率,降低碳排放。同时,可实现含锌漆渣与钢厂含锌烟灰的无害化处置。
59.3)常规工艺采用硅钙镁三元渣型,此渣型熔点高,因此需要配入足量的煤用以保证熔炼温度,而本发明在熔炼过程中通过构建cao-sio
2-mgo-na2o-caf2五元渣型,可在降低渣相熔点的同时,获得较好的流动性,实现含锌烟灰低温熔炼的目的。
60.4)本发明通过钠盐的添加,破坏硅酸盐结构,促进锌的释放与还原,提高了熔炼效率,并且使锌尽可能的还原进入烟气中。同时可弱化feo中的fe-o键,使氧化铁更易被碳还原,从而促进铁氧分离,进一步释放铁酸锌中的锌,加快还原速率,增加锌的回收率;
61.5)本发明通过氟盐与钠盐协同作用,可降低渣熔点和黏度,实现低温熔炼。
附图说明
62.图1为本发明的一种钢厂含锌烟灰和含锌漆渣的处理方法流程图。
63.图2为实施例1的cao-sio
2-mgo-na2o-caf2五元渣相图。
具体实施方式
64.以下将结合实施例来详细说明本发明。需要说明的是,在不冲突的情况下,本发明中的实施例及实施例中的特征可以相互组合。若无特别说明,相关百分数是指质量百分数。
65.实施例1
66.表1钢厂含锌烟灰主要化学成分组成
67.元素feznsicamgmncu含量/wt%26.324.81.42.60.60.80.2
68.表2含锌漆渣主要化学成分组成
69.元素feznsicamgch低位热值含量/wt%13.612.72.40.80.434.23.523100kcal/kg
70.本实施例中,钢厂含锌烟灰与含锌漆渣的成分组成分别如表1和表2所示,参见图1,具体处理方法如下:
71.(1)将钢厂含锌烟灰与含锌漆渣按2:1的比例配比混合,得混合料;
72.(2)将混合料、无烟煤、碳酸钠、氟化钙混合均匀,得混合物料;
73.其中,碳酸钠添加量为混合料的3%,氟化钙添加量为混合料的1%;无烟煤的添加量为混合料的15%;该物料配比自然碱度(cao+mgo)/(sio2)即为0.8,在最佳范围之内,因此无需额外添加造渣剂。
74.(3)将所述混合物料加入熔炼炉,通入富氧空气,进行熔炼,获得富锌烟气和上、下分布的熔融渣、铁水;
75.其中,熔炼温度为1400℃,熔炼时间为60min,还原气氛为co/co2=1.6(即co、co2的摩尔比),富氧空气的氧气浓度为80vol%,通入量以满足还原气氛要求为准;炉顶出口处的
富锌烟气的温度为1300℃,锌蒸汽浓度为12vol%。
76.(4)将富锌烟气从炉顶输入铅雨冷凝器冷凝至500℃,获得锌直收率为99.2%,锌品位为99.6%的锌锭产品;
77.将铁水排出,得到含铁95%、含碳2.5%的生铁产品,铁回收率达97%。
78.对熔融渣进行水淬处理,获得水淬渣;其中,含锌漆渣中有机物焚烧率大于99.9%,玻璃化率大于97%,铁含量为2.48%,锌含量为0.6%。
79.对比例1
80.重复实施例1,区别仅在于:不添加碳酸钠。
81.结果显示:炉顶出口处的富锌烟气的温度为1300℃,锌蒸汽浓度为12vol%。锌直收率为95%,锌品位为99.5%的锌锭产品;但是,熔融渣未完全熔融,无法实现渣铁分离,需要采用天然气补热,进一步提高熔炼温度至1550℃,才可实现渣铁分离,将铁水排出,得到含铁93%、含碳3.5%的生铁产品,铁回收率达94%。对熔融渣进行水淬处理,获得水淬渣;其中,含锌漆渣渣中有机物焚烧率大于99.9%,玻璃化率大于98%,铁含量为4.96%,锌含量为3.89%。
82.对比例2
83.重复实施例1,区别仅在于:不添加氟化钙。
84.结果显示:炉顶出口处的富锌烟气的温度为1300℃,锌蒸汽浓度为12vol%;锌直收率为98.5%,锌品位为99.4%的锌锭产品;将铁水排出,得到含铁91%、含碳4.5%的生铁产品,铁回收率达85%。
85.对熔融渣进行水淬处理,获得水淬渣;其中,含锌漆渣中有机物焚烧率大于99.9%,玻璃化率大于97%,铁含量为9,46%,锌含量为1.16%。生产现状表明,渣黏度过高,不易排出,且渣含铁较高。
86.对比例3
87.重复实施例1,区别仅在于:不添加碳酸钠,控制氟化钙的添加量为混合料的4%。
88.结果显示:炉顶出口处的富锌烟气的温度为1300℃,锌蒸汽浓度为12vol%;锌直收率为96%,锌品位为99.2%的锌锭产品;渣未完全熔融,无法实现渣铁分离,采用天然气补热,进一步提高熔炼温度至1500℃,才可实现渣铁分离,将铁水排出,得到含铁95%、含碳1.5%的生铁产品,铁回收率达98%。对熔融渣进行水淬处理,获得水淬渣;其中,含锌漆渣中有机物焚烧率大于99.9%,玻璃化率大于98%,铁含量为0.8%,锌含量为3.1%。
89.对比例4
90.重复实施例1,区别仅在于:不添加氟化钙,控制碳酸钠的添加量为混合料的10%。
91.结果显示,炉顶出口处的富锌烟气的温度为1300℃,锌蒸汽浓度为12vol%;锌直收率78%,锌品位为96.5%的锌锭产品;生铁产品含铁89%、含碳4.3%,铁回收率达87%。对熔融渣进行水淬处理,获得水淬渣;其中,水淬渣中有机物焚烧率大于99.9%,玻璃化率大于97%,铁含量为8.43%,锌含量为14.22%。试验结果表明,由于碳酸钠的过量添加导致炉况恶化严重,同时还原气氛减弱导致锌回收率显著下降。
92.对比例5
93.重复实施例1,区别仅在于:不添加氟化钙,熔炼时间为90min。
94.结果显示,炉顶出口处的富锌烟气的温度为1300℃,锌蒸汽浓度为12vol%。
95.锌直收率为99.2%,锌品位为99.4%的锌锭产品;
96.生铁产品含铁94%、含碳2.7%,铁回收率达95%。
97.含锌漆渣中有机物焚烧率大于99.9%,玻璃化率大于97%,铁含量为3.87%,锌含量为0.62%。试验结果表明,延长熔炼时间可提高锌、铁的回收率。
98.对比例6
99.重复实施例1,区别仅在于:不添加碳酸钠,不添加氟化钙,熔炼温度1550℃。
100.结果显示,炉顶出口处的富锌烟气的温度为1300℃,锌蒸汽浓度为12vol%。
101.锌直收率为97.4%,锌品位为98.3%的锌锭产品;
102.生铁产品含铁93%、含碳3.1%,铁回收率达82%。
103.含锌漆渣中有机物焚烧率大于99.9%,玻璃化率大于97%,铁含量为10.4%,锌含量为2.1%。
104.对比例7
105.重复实施例1,区别仅在于:不添加碳酸钠,不添加氟化钙,熔炼温度1550℃,熔炼时间90min。
106.结果显示:炉顶出口处的富锌烟气的温度为1300℃,锌蒸汽浓度为12vol%。
107.锌直收率为97.6%,锌品位为98.7%的锌锭产品;
108.生铁产品含铁94%、含碳2.8%,铁回收率达95%。
109.含锌漆渣中有机物焚烧率大于99.9%,玻璃化率大于97%,铁含量为3.82%,锌含量为1.75%。
110.对比例8
111.重复对比例5,区别仅在于:提升熔炼温度至1550℃。
112.炉顶出口烟气中锌蒸汽浓度为10.8vol%。步骤(4)中锌直收率为99%,锌品位为99.6%的锌锭产品。与此同时,铁以生铁的形式排出,得到含铁95%、含碳2.2%的生铁产品,铁回收率为96%。水淬渣中有机物焚烧率大于99.9%,玻璃化率大于95%,铁含量为1.66%,锌含量为0.39%。
113.对比可知,需要采用本发明的处理方法才能实现的钢厂含锌烟灰与含锌漆渣的低能耗、高质量处理。
114.实施例2
115.重复实施例1,区别仅在于:碳酸钠添加量为混合料的5%,氟化钙添加量为混合料的2%。
116.炉顶出口烟气中锌蒸汽浓度为12.2vol%。步骤(4)中锌直收率为99.8%,锌锭产品的锌品位为99.6%。与此同时,铁以生铁的形式排出,得到含铁96%、含碳2.3%的生铁产品,铁回收率达98%。水淬渣中有机物焚烧率大于99.9%,玻璃化率大于97%,铁含量为0.8%,锌含量为0.1%。
117.对比例9
118.重复实施例1,区别仅在于:碳酸钠添加量为混合料的12%。
119.炉顶出口烟气中锌蒸汽浓度为8.7vol%。步骤(4)中锌直收率为82%,锌锭产品的锌品位为98.5%。与此同时,铁以生铁的形式排出,得到含铁89%、含碳4.3%的生铁产品,铁回收率达75%。水淬渣中有机物焚烧率大于99.9%,玻璃化率大于97%,铁含量为
10.36%,锌含量为7.02%。
120.上述实施例阐明的内容应当理解为这些实施例仅用于更清楚地说明本发明,而不用于限制本发明的范围,在阅读了本发明之后,本领域技术人员对本发明的各种等价形式的修改均落入本技术所附权利要求所限定的范围。