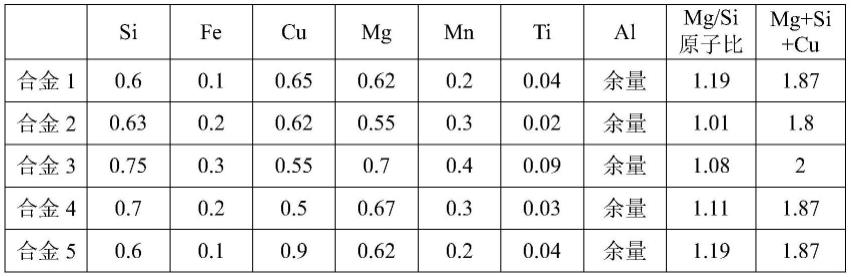
1.本发明属于铝合金材料技术领域,具体涉及一种6系铝合金、铝合金板带材及其制备方法和应用。
背景技术:2.为实现节能减排,汽车轻量化已成为汽车行业的迫切需求,而且轻量化有利于提高汽车的安全性能和驾驶性能。作为理想的轻量化材料,铝合金板材在汽车上的应用逐渐增多,尤其是新能源汽车极大推动了铝合金板材的应用。
3.为进一步实现轻量化,就有必要通过提高铝合金的强度来降低材料的厚度。
4.zl200910013544.0为提高合金强度添加有0.7-0.8%cu;且采用磁场辅助工艺进行坯料的制备,不适用于工业化生产。zl201811016743.2公开了一种高烘烤硬化性的铝合金板材及其制备方法,添加有0.06-1.5%zn,0.3-0.8%cu, 0.03-0.25%sn,以提高强度,并采用挤压法制备板材。cn201810658850.9公开了一种高强度高延伸率铝合金板材及其制造方法,含有0.8-1.5%mg,0.8-1.5%si, 1.2-1.5%cu。上述技术为提高强度添加有较高的cu元素,但cu含量过高会对合金腐蚀性能带来严重的不利影响。
5.cn202010950499.8公开了一种高强度汽车车身用6xxx系铝合金板材及其制备方法,采用100-250℃保温5-120s进行一级预时效+70-90℃保温4-10h进行二级预时效的处理工艺来实现高的烤漆强度。cn202010906770.8公开了一种向 al-mg-si合金中添加0.2-1%ag提高合金性能的方法,并采用三级时效处理工艺实现高的烤漆强度,第一级时效:在150-170℃下处理20min,第二级时效:在 180-200℃下处理20min,第三级时效:在220-240℃下处理20min。较高的时效温度会使合金t4p强度增加,不利于成形性能;ag的添加会带来成本的大幅增加。
技术实现要素:6.针对现有技术存在的问题,本发明提供了一种6系铝合金、铝合金板带材及其制备方法和应用,具体包括以下内容:
7.一种6系铝合金,其组分及各组分的质量百分含量为:si 0.6-0.75%,fe0.1-0.3%,cu 0.5-0.65%,mg 0.55-0.7%,mn 0.2-0.4%,余量为al和不可避免的杂质,其中,mg/si原子比为1.0-1.2,mg+si+cu=1.8-2%。
8.具体的,还包括质量百分含量≤0.1%的ti。
9.一种采用本发明公开的6系铝合金制备的铝合金板带材。
10.一种本发明公开的铝合金板带材的制备方法,包括以下步骤:
11.(1)将铝锭和中间合金按配比进行熔炼、铸造,得到扁锭;
12.(2)将扁锭的大面每面车铣10-15mm后进行加热处理,得到铸锭;
13.(3)对铸锭进行热粗轧,热粗轧前三个道次压下率为≤5%,随后道次压下率≥10%,热粗轧终轧温度380-420℃,厚度16-23mm,得到板锭;
14.(4)对板锭进行热精轧,精轧终轧温度260-300℃,终轧厚度4-8mm,得到精轧板带材;
15.(5)对精轧板带材进行一次冷轧,冷轧加工率控制在40-70%,得到冷轧板带材;
16.(6)对冷轧板带材进行中间退火,得到退火板带材;
17.(7)对退火板带材进行二次冷轧,冷轧加工率控制在40-70%,得到冷轧板带材;
18.(8)对冷轧板带材进行在线连续式固溶处理;
19.(9)对固溶处理后的板带材进行连续式三级预时效处理:板带材经在线加热炉以0.5-10℃/s的速率升温到90-130℃,保温时间≤15s;再以0.2-5℃/s速率降温至60-90℃进行收卷;收卷后以不高于2℃/h的速度冷到室温。
20.具体的,所述步骤(2)加热处理的温度曲线为:以30-100℃/h升温速率从室温加热到350-420℃,再以10-30℃/h升温速率升温到530-560℃并保温6-12h,然后以30-100℃/h降温速率降温到480-530℃,保温2h以上。
21.具体的,步骤(3)热粗轧总道次数≥11,其中第4-6个道次单道次压下率介于10-20%,第7道次至倒数第4道次单道次压下率介于20-35%,最后三个道次单道次压下率介于35-50%。
22.具体的,步骤(6)中间退火的工艺条件为:首先以≥5℃/s的速率升温至430-520℃保温30-120s,或以30-100℃/h的速率升温至450-480℃保温2h以上;然后再以30-100℃/h降温速率降温到室温,得到退火板带材。
23.具体的,步骤(8)固溶处理的工艺条件为:以≥5℃/s的速率升温到500-560℃保温5-180s,再以20-200℃/s的速度冷却到40℃以下。
24.具体的,所述步骤(8)与步骤(9)之间的间隔时间≤15min。
25.一种应用了本发明公开的铝合金板带材的汽车。
26.本发明的有益效果:
27.为实现高的强度,专利zl200910013544.0添加0.7-0.8%cu,zl201811016743.2添加0.06-1.5%zn、0.3-0.8%cu,cn201810658850.9添加有 0.8-1.5%mg、0.8-1.5%si、1.2-1.5%cu。与上述专利不同,本发明为避免cu、zn 含量过高对合金耐腐蚀性能的不利影响,将cu含量控制在较低水平: 0.5-0.65%cu,同时不加zn,通过调控mg/si原子比和mg+si+cu元素含量,来实现t4p好的成形性能和高的烤漆强度、耐蚀性。合金中mg元素含量控制在 0.55-0.7%、si控制在0.6-0.75%,可以使合金t4p具有合适的强度和良好的延伸率,满足成形要求;同时使mg/si原子比控制1.0-1.2范围内,有利于在预时效过程中形成mg/si原子比在1.0-1.2范围内的mg-si原子团簇,该类型团簇在烤漆时容易转化为强化相β”相,实现高的烤漆强度。添加0.5-0.65%cu,能在预时效过程中形成含cu的团簇,有利于在烤漆时形成含cu的强化相,进一步提高合金的强度。同时,通过mg+si+cu元素含量范围限制,调控三者元素总含量,在提高合金强度同时,能保持良好的成形性能、耐腐蚀性,满足汽车零部件的应用要求。
28.cn202010950499.8、cn202010906770.8公开的预时效温度相对较高,不适合用于本发明提供的合金,会造成本发明合金的t4p强度偏高而不利于成形。本发明结合在线加热炉的设备特性,公开了一种连续式三级预时效处理工艺,使合金具有良好的t4p性能、停放性能,又能保证高的烤漆强度,同时容易实现工业化应用。即材料经固溶淬火处理通过设备
加热工艺段时,使材料先以 0.5-10℃/s的速率快速加热到较高温度(90-130℃),保温时间≤15s,利用高温短时加速合金中有利于烤漆硬化的原子团簇的形成和长大;再以0.2-5℃/s降温速率使卷材降温到60-90℃进行收卷,利用收卷的保温进一步促进团簇的形成,提高烤漆硬化能力;通过对卷材冷却速度调控利用长时间的余温促进原子团簇的进一步增加,从而使t4p材料既含有一定尺寸、数量的原子团簇确保实现高的烤漆强度,以及保证材料停放稳定性,又不至于使t4p屈服强度偏高而不利于成形。该工艺结合设备开发,易实现量产且对成本或工业操作无影响。
29.综上所述,本发明的有益效果可以总结为以下两点:
30.(1)采用本发明提供的成分和工艺,可以避免为提高强度添加较高的cu 而降低合金的耐蚀性,可以使合金在t4p具有合适的强度获得良好的成形性,同时可获得高的烤漆强度。制备的6系合金板带材t4p态时具有良好的成形性能(t4p屈服强度为115-150mpa,断后延伸率≥27%;n
10-20%
值≥0.28,90
°
方向 r
10%
值≥0.55,δr≤0.2),烤漆后具有高的强度(屈服强度≥240mpa),同时又保持良好的耐腐蚀性能(晶间腐蚀平均腐蚀深度≤200μm,最大腐蚀深度≤250μm),能很好的满足汽车零部件轻量化的需求和下游应用要求;
31.(2)本发明提供的制备方法是基于工业化设备开发,工艺具备良好的批量操作性,具有高的生产效率,且不增加制造成本。
具体实施方式
32.下面结合具体实施方式对本发明进行详细说明。下面所示的实施例不对权利要求所记载的发明内容起任何限定作用。另外,下面实施例所表示的构成的全部内容不限于作为权利要求所记载的发明的解决方案所必需的。
33.一种6系铝合金,其组分及各组分的质量百分含量为:si 0.6-0.75%,fe0.1-0.3%,cu 0.5-0.65%,mg 0.55-0.7%,mn 0.2-0.4%,余量为al和不可避免的杂质,其中,mg/si原子比为1.0-1.2,mg+si+cu=1.8-2%。具体的,si的含量可以是0.60%、0.62%、0.64%、0.66%、0.68%、0.70%、0.72%、0.74%、或0.75%等;fe的含量可以是0.1%、0.12%、0.15%、0.18%、0.2%、0.22%、0.25%、0.28%、或0.3%等;cu的含量可以是0.5%、0.52%、0.55%、0.58%、0.6%、0.62%、0.63%、或0.65%等;mg的含量可以是0.55%、0.56%、0.58%、0.6%、0.62%、0.65%、 0.68%、或0.7%等;mn的含量可以是0.2%、0.22%、0.25%、0.28%、0.3%、0.32%、 0.35%、0.38%、或0.4%等;mg/si原子比具体可以是1.0、1.05、1.1、1.12、1.15、 1.18、或1.2等;mg+si+cu的占比具体可以是1.8%、1.82%、1.85%、1.88%、1.9%、1.92%、1.95%、1.98%、或2%等。
34.在本发明的一个实施例中,所述铝合金还包括质量百分含量≤0.1%的ti。具体的,ti的含量可以≤0.01、0.05%、0.08%、或0.1%等。
35.一种采用本发明公开的6系铝合金制备的铝合金板带材。
36.一种本发明公开的铝合金板带材的制备方法,包括以下步骤:
37.(1)将铝锭和中间合金按配比进行熔炼、铸造,得到扁锭;
38.(2)将扁锭的大面每面车铣10-15mm后进行加热处理,得到铸锭;
39.(3)对铸锭进行热粗轧,热粗轧前三个道次压下率为≤5%,随后道次压下率≥10%,热粗轧终轧温度380-420℃,厚度16-23mm,得到板锭;具体的,前三个道次压下率可以
为≤1%、≤2%、≤3%、≤4%、,随后道次压下率可以为≥10%、≥12%、≥15%、≥20%、≥30%等,热粗轧终轧温度可以是380℃、385℃、390℃、 395℃、400℃、410℃、415℃、或420℃等,厚度可以是16mm、18mm、19mm、 20mm、22mm、或23mm。
40.(4)对板锭进行热精轧,精轧终轧温度260-300℃,终轧厚度4-8mm,得到精轧板带材;具体的,精轧终轧温度可以是260℃、270℃、280℃、290℃、或300℃等,终轧厚度可以是4mm、5mm、6mm、7mm、或8mm等。
41.(5)对精轧板带材进行一次冷轧,冷轧加工率控制在40-70%,得到冷轧板带材;具体的,冷轧加工率可以为40%、45%、50%、55%、60%、65%、或70%等。
42.(6)对冷轧板带材进行中间退火,得到退火板带材;
43.(7)对退火板带材进行二次冷轧,冷轧加工率控制在40-70%,得到冷轧板带材;具体的,冷轧加工率可以为40%、45%、50%、55%、60%、65%、或70%等。
44.(8)对冷轧板带材进行在线连续式固溶处理;
45.(9)对固溶处理后的板带材进行连续式三级预时效处理:板带材经在线加热炉以0.5-10℃/s的速率升温到90-130℃,保温时间≤15s;再以0.2-5℃/s速率降温至60-90℃进行收卷;收卷后以不高于2℃/h的速度冷到室温。具体的,在线加热炉的升温速率可以是0.5℃/s、1℃/s、1.5℃/s、2℃/s、2.5℃/s、5℃/s、7.5℃/s、 8℃/s、8.5℃/s、9℃/s、9.5℃/s、或10℃/s等,保温温度为90℃、95℃、100℃、110℃、120℃、125℃、或130℃等,保温时间可以≤5s、≤8s、≤10s、或≤15s等;降温速率可以是0.2℃/s、0.5℃/s、1℃/s、2℃/s、3℃/s、4℃/s、4.5℃/s、或5℃/s 等;收卷温度可以为:60℃、65℃、70℃、75℃、80℃、85℃、或90℃等;收卷后的冷却速度可以不高于0.5℃/h、1℃/h、1.5℃/h、或2℃/h等。
46.在本发明的一个实施例中,所述步骤(2)加热处理的温度曲线为:以 30-100℃/h升温速率从室温加热到350-420℃,具体的,升温速率可以是30℃/h、 40℃/h、50℃/h、80℃/h、90℃/h、或100℃/h等,可以加热到350℃、360℃、 380℃、390℃、400℃、410℃、415℃、或420℃等;再以10-30℃/h升温速率升温到530-560℃并保温6-12h,具体的,升温速率可以是10℃/h、15℃/h、18℃/h、 20℃/h、25℃/h、28℃/h、或30℃/h等,保温温度可以是530℃、535℃、540℃、 545℃、550℃、555℃、560℃等,保温时间可以是6h、7h、8h、9h、10h、11h、或12h等;然后以30-100℃/h降温速率降温到480-530℃,保温2h以上,具体的,降温速率可以是30℃/h、40℃/h、50℃/h、60℃/h、70℃/h、80℃/h、90℃/h、或100℃/h等,保温温度可以是480℃、490℃、500℃、510℃、520℃、530℃等,保温时间可以是2h以上、3h以上、4h以上、5h以上、6h以上、8h以上、10h以上等。
47.在本发明的一个实施例中,步骤(3)热粗轧总道次数≥11,具体可以是11、 12、13、14、15或以上;其中第4-6个道次单道次压下率介于10-20%,具体可以是10%、11%、12%、15%、18%、19%、20%等;第7道次至倒数第4道次单道次压下率介于20-35%,具体可以是20%、22%、25%、28%、30%、33%、35%等;最后三个道次单道次压下率介于35-50%,具体可以是35%、38%、40%、 45%、48%、50%等。
48.在本发明的一个实施例中,步骤(6)中间退火的工艺条件为:首先以≥5℃/s 的速率升温至430-520℃保温30-120s,具体的,升温速率可以是≥6℃/s、≥8℃/s、≥10℃/s、≥20℃/s,保温温度可以是430℃、450℃、480℃、500℃、520℃等,保温时间可以是30s、50s、60s、80s、100s、120s等;或以30-100℃/h的速率升温至450-480℃保温2h以上,具体的,升温
速率可以是30℃/h、50℃/h、60℃/h、 70℃/h、80℃/h、90℃/h、100℃/h等,保温温度可以是450℃、455℃、460℃、 465℃、475℃、480℃,保温时间可以是2.5h以上、3h以上、4h以上、5h以上、6h以上;然后再以30-100℃/h降温速率降温到室温,得到退火板带材,具体的,降温速率可以是30℃/h、40℃/h、50℃/h、60℃/h、70℃/h、80℃/h、90℃/h、 100℃/h等。
49.在本发明的一个实施例中,步骤(8)固溶处理的工艺条件为:以≥5℃/s的速率升温到500-560℃保温5-180s,再以20-200℃/s的速度冷却到40℃以下。具体的,升温速率可以是≥5℃/s、≥10℃/s、≥15℃/s、≥20℃/s、≥30℃/s,保温温度可以是5s、10s、20s、50s、80s、100s、150s、170s、180s等,降温速度可以是 20℃/s、50℃/s、80℃/s、100℃/s、150℃/s、160℃/s、170℃/s、180℃/s、200℃/s 等。
50.在本发明的一个实施例中,所述步骤(8)与步骤(9)之间的间隔时间≤15min,具体的,间隔时间可以≤15min、≤10min、≤8min、≤5min等。
51.一种应用了本发明公开的铝合金板带材的汽车,所述汽车可以是家用汽车、货运汽车或其他种类的汽车。
52.本发明公开的铝合金板带材是一种兼顾成形、耐蚀的汽车用高强度6系铝合金板带材,是以si、fe、cu、mn、mg、ti等元素在特定含量范围内,余量由 al和不可避免的杂质组成的。其中:
53.(1)si:0.6-0.75%,mg:0.55-0.7%,mg/si原子比为1.0-1.2。si、mg元素质量分数确定范围的同时设定mg/si原子比,有利于使mg、si元素尽可能多的在预时效处理过程中形成易于转化为强化相β”相的mg-si原子团簇,保证高的烤漆强度。si、mg元素含量偏低导致烤漆强度不足;si、mg元素含量偏高会导致t4p强度过高,不利于成形;mg/si原子比控制不合理,对烤漆强度、成形会带来不利影响。
54.(2)cu:0.5-0.65%,且满足mg+si+cu=1.8-2%。加入一定量的cu可在预时效过程中形成有利于烤漆硬化的原子团簇,进一步提高合金的烤漆强度。cu 含量过高,会导致合金耐腐性能严重下降。cu含量偏低,对强度提升作用有限。mg+si+cu=1.8-2%,可以确保合金既有良好的成形性能,又有高的烤漆强度。
55.本发明公开的铝合金板带材的制备方法,是一种兼顾成形、耐蚀的汽车用高强度6系铝合金板带材的制备方法,包括如下步骤:
56.(1)铸锭加热温度曲线:以30-100℃/h升温速率从室温加热到350-420℃,再以10-30℃/h升温速率升温到530-560℃并保温6-12h,然后以30-100℃/h降温速率降温到480~530℃,保温2h以上。在低于350-420℃温度快速加热,可以降低能耗。在350-560℃温度区间较缓慢加热,有利于alcumgsi相的回溶;在 530-560℃并保温6-12h,有利于粗大mg2si相的回溶和含fe相的球化。
57.(2)热粗轧:热粗轧前三个道次压下率为≤5%,随后道次压下率≥10%,热粗轧终轧温度380-420℃,厚度16~23mm。优选热粗轧总道次数≥11,其中第4-6 个道次单道次压下率介于10-20%,第7道次至倒数第4道次单道次压下率介于 20-35%,最后三个道次单道次压下率介于35-50%。热粗轧时选择较大的道次压下率,可以使化合物破碎更充分,以及获得更均匀细小的晶粒组织,有利于保证后续板材各个方向组织、性能的均匀性。
58.(3)连续式三级预时效处理:板带材经在线加热炉以0.5-10℃/s的速率升温到90-130℃,保温时间≤15s;再以0.2-5℃/s速率降温至60-90℃进行收卷;收卷后以不高于2℃/
h的速度冷到室温。使材料先以0.5-10℃/s的速率快速加热到较高温度(90-130℃)并保温时间≤15s,利用高温短时加速合金中有利于烤漆硬化的原子团簇的形成和长大;再以0.2-5℃/s降温速率使卷材降温到60-90℃进行收卷,利用收卷中低温保温进一步促进团簇的形成,提高烤漆硬化能力,同时对温度的限制可使合金t4p强度控制在合理范围内,保证良好的成形性;通过对卷材冷却速度调控利用长时间的余温促进原子团簇的进一步增加,从而使t4p 材料既含有一定尺寸、数量的原子团簇确保实现高的烤漆强度,以及保证材料停放稳定性,又不至于使t4p屈服强度偏高而不利于成形。
59.下面结合具体实施例对本发明作进一步详细说明,此处所描述的具体实施例仅用于解释本发明,但不作为对本发明的限定。
60.实施例1-4、对比例1-2中铝合金原材料的组分及其质量百分含量见表1。
61.表1合金成分(wt%)
[0062][0063][0064]
实施例1
[0065]
将铝合金原材料按合金1成分进行配比、熔炼铸造出1900
×
550
×
6500mm规格的扁锭,将扁锭的大面每面车铣15mm后进行加热:以30℃/h升温速率从室温加热到400℃,再以30℃/h升温速率升温到550℃并保温6h,然后以50℃/h 降温速率降温到530℃,保温2h;接着进行热粗轧,热粗轧终轧温度420℃,厚度21mm;进行热精轧,精轧终轧温度260℃,终轧厚度7mm;进行一次冷轧,冷轧加工率控制在70%;进行中间退火:以50℃/s的速率升温至480℃保温30s;进行二次冷轧,冷轧加工率控制在40%;进行在线固溶处理:以50℃/s的速率升温到560℃保温5s再以200℃/s的速度冷却到40℃以下;进行预时效处理:板带材经在线加热炉以5℃/s的速率升温到90℃并保温15s,再以1℃/s速率降温至60℃进行收卷,收卷后以2℃/h的速度冷到室温。
[0066]
实施例2
[0067]
将铝合金原材料按合金2成分进行配比、熔炼铸造出1900
×
550
×
6500mm规格的扁锭,将扁锭的大面每面车铣15mm后进行加热:以50℃/h升温速率从室温加热到400℃,再以20℃/h升温速率升温到550℃并保温10h,然后以50℃/h 降温速率降温到480℃,保温4h;接着进行热粗轧,热粗轧终轧温度380℃,厚度19mm;进行热精轧,精轧终轧温度300℃,终轧厚度5mm;进行一次冷轧,冷轧加工率控制在60%;进行中间退火:以50℃/s的速率升温至480℃保温30s;进行二次冷轧,冷轧加工率控制在50%;进行在线固溶处理:以50℃/s的速率升温到540℃保温60s再以200℃/s的速度冷却到40℃以下;进行预时效处理:板带材经在线加热炉以5℃/s的速率升温到100℃并保温10s,再以2℃/s速率降温至80℃进行收卷,收卷后
以1.5℃/h的速度冷到室温。
[0068]
实施例3
[0069]
将铝合金原材料按合金3成分进行配比、熔炼铸造出1900
×
550
×
6500mm规格的扁锭,将扁锭的大面每面车铣15mm后进行加热:以100℃/h升温速率从室温加热到400℃,再以10℃/h升温速率升温到550℃并保温10h,然后以50℃/h 降温速率降温到510℃,保温4h;接着进行热粗轧,热粗轧终轧温度380℃,厚度19mm;进行热精轧,精轧终轧温度300℃,终轧厚度5mm;进行一次冷轧,冷轧加工率控制在60%;进行中间退火:以50℃/s的速率升温至480℃保温30s;进行二次冷轧,冷轧加工率控制在50%;进行在线固溶处理:以50℃/s的速率升温到540℃保温60s再以200℃/s的速度冷却到40℃以下;进行预时效处理:板带材经在线加热炉以5℃/s的速率升温到100℃并保温10s,再以3℃/s速率降温至80℃进行收卷,收卷后以1.5℃/h的速度冷到室温。
[0070]
实施例4
[0071]
将铝合金原材料按合金4成分进行配比、熔炼铸造出1900
×
550
×
6500mm规格的扁锭,将扁锭的大面每面车铣15mm后进行加热:以70℃/h升温速率从室温加热到400℃,再以20℃/h升温速率升温到550℃并保温10h,然后以50℃/h 降温速率降温到510℃,保温4h;接着进行热粗轧,热粗轧终轧温度380℃,厚度19mm;进行热精轧,精轧终轧温度300℃,终轧厚度5mm;进行一次冷轧,冷轧加工率控制在60%;进行中间退火:以50℃/s的速率升温至480℃保温30s;进行二次冷轧,冷轧加工率控制在50%;进行在线固溶处理:以50℃/s的速率升温到540℃保温60s再以200℃/s的速度冷却到40℃以下;进行预时效处理:板带材经在线加热炉以10℃/s的速率升温到130℃并保温3s,再以5℃/s速率降温至80℃进行收卷,收卷后以1.5℃/h的速度冷到室温。
[0072]
对比例1
[0073]
将铝合金原材料按合金5成分进行配比、熔炼铸造出1900
×
550
×
6500mm规格的扁锭,将扁锭的大面每面车铣15mm后进行加热:以70℃/h升温速率从室温加热到400℃,再以20℃/h升温速率升温到550℃并保温10h,然后以50℃/h 降温速率降温到510℃,保温4h;接着进行热粗轧,热粗轧终轧温度380℃,厚度19mm;进行热精轧,精轧终轧温度300℃,终轧厚度5mm;进行一次冷轧,冷轧加工率控制在60%;进行中间退火:以50℃/s的速率升温至480℃保温30s;进行二次冷轧,冷轧加工率控制在50%;进行在线固溶处理:以50℃/s的速率升温到540℃保温60s再以200℃/s的速度冷却到40℃以下;进行预时效处理:板带材经在线加热炉以5℃/s的速率升温到100℃并保温10s,再以3℃/s速率降温至80℃进行收卷,收卷后以1.5℃/h的速度冷到室温。
[0074]
对比例2
[0075]
将铝合金原材料按合金6成分进行配比、熔炼铸造出1900
×
550
×
6500mm规格的扁锭,将扁锭的大面每面车铣15mm后进行加热:以70℃/h升温速率从室温加热到400℃,再以20℃/h升温速率升温到550℃并保温10h,然后以50℃/h 降温速率降温到510℃,保温4h;接着进行热粗轧,热粗轧终轧温度380℃,厚度19mm;进行热精轧,精轧终轧温度300℃,终轧厚度5mm;进行一次冷轧,冷轧加工率控制在60%;进行中间退火:以50℃/s的速率升温至480℃保温30s;进行二次冷轧,冷轧加工率控制在50%;进行在线固溶处理:以50℃/s的速率升温到540℃保温60s再以200℃/s的速度冷却到40℃以下;进行预时效处理:板带材经在线加
热炉以5℃/s的速率升温到100℃并保温10s,再以3℃/s速率降温至80℃进行收卷,收卷后以1.5℃/h的速度冷到室温。
[0076]
表2给出了实施例、对比例的拉伸性能、烤漆性能(2%预拉伸+185℃
×
20min)。表3给出了各实施例、对比例的晶间腐蚀结果。
[0077]
相比于实施例1-4合金性能,对比例1合金具有更高的烤漆强度,但其晶间腐蚀深度大,难以满足主机厂对合金耐腐蚀性能的要求;对比例2合金晶界腐蚀深度较小,但烤漆强度较低,不利于轻量化,且合金停放稳定性也较差。
[0078]
实施例1-4合金的平均晶粒尺寸分布在25-35μm范围内,立方取向晶粒分数分布在4-7%范围内,可以保证合金板材具有良好的成形性能和表面质量。
[0079]
以上实施例1-4和对比例1-2的结果表明,采用本发明能够获得一种兼顾成形、耐蚀的汽车用高强度6系铝合金板带材,t4p时具有良好的成形性能,烤漆后具有高的强度,同时又具有良好的耐腐性能,能用于制造汽车外覆盖件和结构件,通过强度提高实现材料减薄轻量化。
[0080]
表2各实施例和对比例的合金90
°
方向拉伸性能
[0081][0082][0083]
表3各实施例和对比例的合金晶间腐蚀结果
[0084]
合金最大深度(μm)平均深度(μm)实施例1245175实施例2234173实施例3232166实施例4223174对比例1354231对比例2194155
[0085]
对所公开的实施例的上述说明,使本领域专业技术人员能够实现或使用本发明。
对这些实施例的多种修改对本领域的专业技术人员来说将是显而易见的,本文中所定义的一般原理可以在不脱离本发明的精神或范围的情况下,在其它实施例中实现。因此,本发明将不会被限制于本文所示的实施例,而是要符合与本文所公开的原理和新颖特点相一致的最宽的范围。