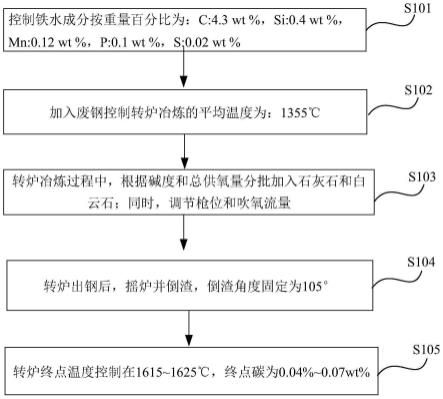
1.本发明涉及转炉炼钢技术领域,具体涉及一种低铁耗模式下降低转炉钢铁料耗的冶炼控制方法。
背景技术:2.随着国家对钢铁产能的控制,目前冶金企业想要发展,只能从降成本和提品种质量两方面入手。其中铁水耗和钢铁料耗是转炉成本控制的重要指标,并且由于国内长期的产能过剩,国内废钢量逐年累积,因此不论是从成本还是节约资源的角度,转炉生产都必须多用废钢。但是由于在低铁耗模式下,废钢加入量多导致转炉吹损大、终渣浮、喷溅多,从而使得低铁耗模式下转炉钢铁料耗居高不下,严重影响吨钢成本。
3.综上所述,现有技术中存在以下问题:低铁耗模式下,如何降低转炉钢铁料耗。
技术实现要素:4.本发明的目的是为了解决低铁耗模式下,如何降低转炉钢铁料耗的问题。
5.为此,本发明实施例提供了一种低铁耗模式下降低转炉钢铁料耗的冶炼控制方法,所述方法包括以下步骤:
6.控制铁水成分按重量百分比为:c:4.3wt%,si:0.4wt%,mn:0.12wt%,p:0.1wt%,s:0.02wt%;
7.加入废钢控制转炉冶炼的平均温度为:1355℃;
8.转炉冶炼过程中,根据碱度和总供氧量分批加入石灰石和白云石;同时,调节枪位和吹氧流量;
9.转炉出钢后,摇炉并倒渣,倒渣角度固定为105
°
;
10.转炉终点温度控制在1615~1625℃,终点碳为0.04%~0.07wt%。
11.具体的,根据碱度和总供氧量分批加入石灰石,包括:
12.石灰石分两批加入,当碱度为2.8,总供氧量8%时,加入第一批石灰石,加入量为总石灰石加入量的2/3,第二批石灰分在总供氧量为16%时加入,加入量为总加入量的1/3。
13.具体的,当碱度为2.8,终点渣mg含量为5%时,总供氧量为8%时,一次性加入白云石。
14.具体的,转炉冶炼过程中,保持转炉液面在865cm~880cm之间。
15.具体的,在转炉底面设置8个底吹孔,在不同吹炼阶段底吹氩。
16.具体的,经过倒渣后平均留渣量不大于3.0t。
17.具体的,调节枪位和吹氧流量,包括:总吹氧量在0~8%时,控制枪位在2600mm,控制瞬时吹氧流量为0~35000m3/h。
18.具体的,调节枪位和吹氧流量,包括:总吹氧量在8%~16%时,控制枪位在2200mm,控制瞬时吹氧流量为36000m3/h。
19.具体的,调节枪位和吹氧流量,包括:总吹氧量在16%~34%时,控制枪位在
1800mm,控制瞬时吹氧流量为34500m3/h。
20.具体的,调节枪位和吹氧流量,包括:总吹氧量在34%~46%时,控制枪位在1750mm,控制瞬时吹氧流量为32500m3/h。
21.产生的有益效果是:采用本发明的方法,转炉终渣全铁由15%降低至14%以下,转炉喷溅基本消失,转炉终渣变稠,转炉渣量减少,造渣料下降,转炉钢铁物料消耗由1078kg/t~1085kg/t降低至1065kg/t~1071kg/t,成本大幅度降低。
附图说明
22.图1是本发明实施例提供的一种低铁耗模式下降低转炉钢铁料耗的冶炼控制方法的流程图。
具体实施方式
23.下面将结合本发明实施例中的附图,对本发明实施例中的技术方案进行清楚、完整地描述,显然,所描述的实施例仅仅是本发明一部分实施例,而不是全部的实施例。基于本发明中的实施例,本领域普通技术人员在没有做出创造性劳动前提下所获得的所有其他实施例,都属于本发明保护的范围。
24.在本发明实施例中,如图1,提供了一种低铁耗模式下降低转炉钢铁料耗的冶炼控制方法,所述方法包括以下步骤:
25.控制铁水成分按重量百分比为:c:4.3wt%,si:0.4wt%,mn:0.12wt%,p:0.1wt%,s:0.02wt%;
26.加入废钢配比为:一类废钢占比35%,普通废钢65%,有利于转炉吹炼过程化渣并有效减少吹损和喷溅。一类废钢的硫含量<0.02%,普通废钢硫含量≥0.02%。
27.控制转炉冶炼的平均温度为:1355℃;废钢铁水按照热平衡比例合理装入;
28.转炉冶炼过程中,根据碱度和总供氧量分批加入石灰石和白云石;同时,调节枪位和吹氧流量;通过调节枪位和吹氧流量来调节氧气和铁水的反应程度。
29.转炉出钢后,摇炉并倒渣,倒渣角度固定为105
°
;经过倒渣后平均留渣量不大于3.0t。
30.转炉终点温度控制在1615~1625℃,终点碳为0.04%~0.07wt%。
31.根据碱度和总供氧量分批加入石灰石,包括:
32.石灰石分两批加入,当碱度为2.8,总供氧量8%时,加入第一批石灰石,加入量为总石灰石加入量的2/3,第二批石灰分在总供氧量为16%时加入,加入量为总加入量的1/3。
33.当碱度为2.8,终点渣mg含量为5%时,总供氧量为8%时,一次性加入白云石。
34.转炉冶炼过程中,保持转炉液面在865cm~880cm之间。
35.在转炉底面设置8个底吹孔,在不同吹炼阶段底吹氩。其在不同吹炼阶段底吹氩/氮气流量控制如表1(流量单位m3/h):
36.表1不同吹炼阶段底吹氩和氮气流量控制表
[0037][0038][0039]
其中,吹炼阶段1代表吹氧量在前20%,阶段2代表吹氧量在前40%,阶段3代表吹氧量在前60%,阶段4代表吹氧量在前80%,阶段5代表吹氧量在100%。
[0040]
吹炼过程不再加入铁矿石等氧化物料冷却。采用前期+后期脱磷方法,脱磷效率89%。前期脱磷,是利用冶炼前期温度偏低的有利条件尽最大能力脱磷。后期脱磷,是冶炼后期高碱度的炉渣基本形成,利用炉渣碱度和高氧化性脱磷。
[0041]
调节枪位和吹氧流量,包括:总吹氧量在0~8%时,控制枪位在2600mm,控制瞬时吹氧流量为0~35000m3/h。
[0042]
调节枪位和吹氧流量,包括:总吹氧量在8%~16%时,控制枪位在2200mm,控制瞬时吹氧流量为36000m3/h。
[0043]
调节枪位和吹氧流量,包括:总吹氧量在16%~34%时,控制枪位在1800mm,控制瞬时吹氧流量为34500m3/h。
[0044]
调节枪位和吹氧流量,包括:总吹氧量在34%~46%时,控制枪位在1750mm,控制瞬时吹氧流量为32500m3/h。
[0045]
针对150t转炉,采用自动炼钢的方式进行吹炼从而控制吹损和喷溅,过程控制偏返干,氧枪流量和枪位控制大体采用阶段性恒枪恒压(流)法,氧枪枪位整体控制方向为高—低—高—低,枪位与吹氧流量控制如表2:
[0046]
表2枪位与吹氧流量控制表
[0047][0048][0049]
采用本发明的方法,转炉终渣全铁由15%降低至14%以下,转炉喷溅基本消失,转炉终渣变稠,转炉渣量减少,造渣料下降,转炉钢铁物料消耗由1078kg/t~1085kg/t降低至1065kg/t~1071kg/t,成本大幅度降低。
[0050]
实施例1:
[0051]
本发明的一种低铁耗模式下降低转炉钢铁料耗的冶炼控制方法,如图1所示,所述低铁耗模式下降低转炉钢铁料耗的冶炼控制方法,其铁水成分为c:4.3%,si:0.4%,mn:0.12%,p:0.1%,s:0.02%。平均温度:1355℃,废钢铁水按照热平衡比例合理装入;
[0052]
所述低铁耗模式下降低转炉钢铁料耗的冶炼控制方法,控制铁水成分按重量百分比为:c:4.3wt%,si:0.4wt%,mn:0.12wt%,p:0.1wt%,s:0.02wt%;是一种较少渣吹炼的方法,转炉出钢后,摇炉至105
°
进行倒渣,倒渣角度固定为105
°
,经过倒渣后平均留渣量不大于3.0t。
[0053]
所述低铁耗模式下降低转炉钢铁料耗的冶炼控制方法,其转炉冶炼过程主要控制枪位、吹氧流量、加料顺序和加料批次。针对150t转炉,采用自动炼钢的方式进行吹炼从而控制吹损和喷溅,过程控制偏返干,氧枪流量和枪位控制大体采用阶段性恒枪恒压(流)法,氧枪枪位整体控制方向为高—低—高—低,枪位与吹氧流量控制如表2。
[0054]
石灰加入由碱度控制,其碱度控制在2.8,石灰分两批加入,第一批在总供氧量8%
时加入,加入量为总加入量的2/3,第二批在总供氧量为16%时加入,加入量为总加入量的1/3;
[0055]
白云石加入由终点渣mg和碱度控制,碱度控制在2.8,终点渣mg含量控制在5%,在总供氧量8%时加入,一次性加入;
[0056]
低铁耗模式下降低转炉钢铁料耗的冶炼控制方法需要控制转炉炉况,保持转炉液面在865cm~880cm之间。
[0057]
所述低铁耗模式下降低转炉钢铁料耗的冶炼控制方法是针对复吹转炉而言,转炉低面有8个底吹孔,其在不同吹炼阶段底吹氩/氮气流量控制如表1(流量单位m3/h):
[0058]
其中,吹炼阶段1代表吹氧量在前20%,阶段2代表吹氧量在前40%,依次类推阶段5。
[0059]
所述低铁耗模式下降低转炉钢铁料耗的冶炼控制方法吹炼过程几乎不再加入铁矿石等氧化物料冷却。
[0060]
废钢装入量为45t左右,铁水装入量124t左右;
[0061]
废钢配比为一类废钢占比35%,普通废钢65%,有利于转炉吹炼过程化渣并有效减少吹损和喷溅。
[0062]
本方法采用前期+后期脱磷方法,脱磷效率89%。转炉终点温度控制在1615~1625℃,终点碳为0.04%~0.07%。
[0063]
实施例2:
[0064]
采用本发明的方法,在150吨转炉进行冶炼,首先执行倒炉操作,确认转炉留渣量约为3t,然后进行溅渣护炉,护炉完毕后转入45t废钢,再加入124.5t铁水,铁水温度为1345℃,c含量4.2%,si含量0.39%,mn含量0.12%,p含量0.11%,s含量0.0325%,装料完毕后进行点火吹炼,过程控制如下表3:
[0065]
表3冶炼过程控制表
[0066]
[0067][0068]
按照上述冶炼方法,冶炼终点温度1612℃,tso测样成分:c:0.0463%,si:0.01%,mn:0.10%,p:0.021%,s:0.028。
[0069]
具体钢铁物料消耗情况如表4:
[0070]
表4钢铁物料消耗情况表
[0071]
月份3月份4月份5月份6月份钢铁料耗kg/t.1084108110691067
[0072]
采用本发明的方法,转炉终渣全铁由15%降低至14%以下,转炉喷溅基本消失,转炉终渣变稠,转炉渣量减少,造渣料下降,转炉钢铁物料消耗由1078kg/t~1085kg/t降低至1065kg/t~1071kg/t,成本大幅度降低。
[0073]
以上所述仅为本发明示意性的具体实施方式,并非用以限定本发明的范围。为本发明的各组成部分在不冲突的条件下可以相互组合,任何本领域的技术人员,在不脱离本发明的构思和原则的前提下所做出的等同变化与修改,均应属于本发明保护的范围。