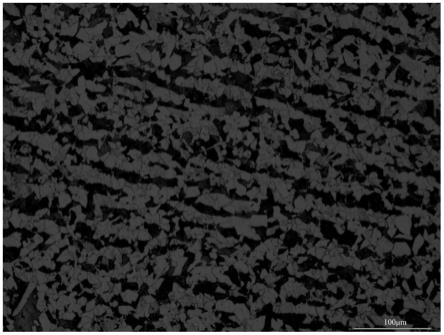
1.本发明涉及无缝钢管制造技术领域,尤其涉及一种高韧性厚壁无缝钢管及其制备方法。
背景技术:2.根据井柱设计,导套和表层套管较多为177.8mm规格以上的大规格k55钢级,起到连接作用接箍的原料一般为壁厚在20mm以上的厚壁无缝钢管。随着油气开采环境逐渐向环境恶劣、地质复杂的区域发展,对技术套管和油层套管提出了更高强韧性的要求,同时,对起到固封表层地质的套管也相应提出了更高的强韧性要求。为了保证良好的接箍连接效果,对接箍用无缝钢管的强韧性要求也随之提高。
3.采用热轧工艺制备厚壁无缝钢管一般存在轧后无缝管的晶粒粗大、内外壁组织不均匀等问题,导致冲击韧性较差,因此,得不到较好的强韧性匹配。目前为了提高无缝钢管的强韧性性能的主要改善措施一种是通过成分调整,即提高合金元素的含量来提高无缝钢管的强度和韧性,但是,接箍用无缝钢管要求具有良好的焊接性能,合金元素的增加将会导致焊接裂纹指数ce
pcm
的增加。另一种是采用轧制过程中常化处理或轧后热处理的方法,轧制过程中常化处理的方法在定径后需要采用加速冷却的方式,较难控制贝氏体的组成比例,若比例控制不当,也会造成冲击韧性的显著下降;再者,对于厚壁管由于其蓄热量大,很难保证钢管内外冷却均匀,内表面的冷却不易达到贝氏体转变温度,造成内外组织不均度变大。因此,目前采用较多的是轧后热处理的方式,即通过离线正火热处理的方法,但是,此方法能耗较高,增加了无缝钢管的制造成本。因此,有必要研发一种新的厚壁无缝钢管的制备方法,在保证强韧性相匹配的前提下,有效降低生产成本。
技术实现要素:4.针对现有接箍用厚壁无缝钢管中合金元素含量高,以及生产工艺能耗高、制备的无缝钢管强韧性不匹配的问题,本发明提供一种高韧性厚壁无缝钢管及其制备方法。
5.为解决上述技术问题,本发明实施例提供的技术方案是:
6.一种高韧性厚壁无缝钢管,其成分重量百分比为:0.20%≤c≤0.30%、0.15%≤si≤0.35%、1.45%≤mn≤1.70%、0.05%≤v≤0.10%、0.013%≤n≤0.020%、0.010%≤alt≤0.040%、s≤0.015%、p≤0.020%、ni≤0.25%、cu≤0.20%、nb≤0.03%,余量为fe及不可避免的杂质。
7.现对于现有技术,本发明提供的高韧性厚壁无缝钢管,合金成分体系简单,通过加入v元素细化晶粒,提高厚壁无缝钢管的强度,但是,v元素的加入会导致厚壁无缝钢管的韧性降低,因此,通过加入特定含量的n元素,使固溶态的v转化为vn,v(c,n)析出态,起到沉淀强化作用,从而提高厚壁无缝钢管的韧性,同时,适量的n元素的加入,可降低合金碳氮化物在高温奥氏体中的溶解,阻碍合金碳氮化物晶粒长大,从而起到细化晶粒的作用,进而进一步提高厚壁无缝钢管的强韧性。本发明各组分相互配合协同,使得制备的厚壁无缝钢管综
合性能优异,且力学性能稳定,抗拉强度可达669mpa~712mpa,屈服强度可达481mpa~523mpa,屈强比可达0.70~0.75,在具有足够使用安全余量的情况下,提高了使用的可靠性,有利于充分发挥材料的强度能力,同时,合金加入量少,还显著降低了合金的成本,完全适用于作为地层复杂的井况表层套管的接箍连接用的钢管,具有广阔的应用前景。
8.需要说明的是,本发明中所述厚壁无缝钢管指的是壁厚为20mm~30mm的无缝钢管。
9.优选的,所述高韧性厚壁无缝钢管的微观组织为微观组织为铁素体和珠光体,晶粒度为8~9级。
10.本发明还提供了上述高韧性厚壁无缝钢管的制备方法,包括如下步骤:
11.以废钢为原料,经电弧炉熔炼、钢包精炼和连铸工序制成连铸圆坯;取连铸圆坯经环形炉加热、穿孔后制成毛管、毛管经轧制后得到荒管、荒管经微张力减径、冷却,得到高韧性厚壁无缝钢管;其中,所述连铸圆坯的化学成分与所述高韧性厚壁无缝钢管的化学成分相同。
12.优选的,钢包精炼工序中,分2次加入石灰、铝粒和碳化硅调渣,第一次加入是精炼送电开始,一次送电时间≥15min,停电测温、取样,然后开始二次送电,第二次加入石灰、铝粒和碳化硅,使精炼渣碱度为5~6,同时,从底部吹入氩气保证熔池搅动良好,软吹时间≥15min。
13.优选的精炼工序,可使钢中非金属夹杂物充分上浮,降低钢中夹杂物水平,使制备的无缝钢管的夹杂物总和≤2.0。
14.优选的,连铸工序中,在钢包水口和滑板之间采用氩气保护,中间包钢液液面高度达到300mm~450mm时,向钢液表面快速添加覆盖剂隔绝空气,中间包到结晶器采用整体浸入式水口进行保护浇铸。
15.优选的连铸工序可有效降低钢中h、o含量,使钢液中h含量≤2.5ppm,o含量≤30ppm。
16.优选的,环形炉加热工序中,按照连铸圆坯的输送方向将环形加热炉依次分为预热段、加热段和均热段,所述加热段分为加热一段、加热二段和加热三段,各段分别进行温度控制;其中,所述预热段的温度控制为800~1000℃,所述加热一段的温度控制为1000~1200℃,所述加热二段的温度控制为1240~1270℃,所述加热三段的温度控制为1260~1290℃,所述均热段的温度控制为1240~1270℃。
17.优选的环形炉加热温度的控制方式,可促进v的充分固溶,且避免奥氏体在加热过程中晶粒粗化,且有利于控制连铸圆坯在理想的变形温度区间进行轧制,提高无缝钢管的表面质量、尺寸精度和性能。
18.优选的,所述预热段采用无喷嘴燃烧的方式进行加热,所述加热段和均热段采用脉冲式喷嘴燃烧的方式进行加热。
19.优选的加热方式可实现对环形炉各段温度的精准控制。
20.优选的,穿孔工序中,扩径率为24%~26%。
21.进一步地,穿孔工序中,采用两辊导板式穿孔机进行穿孔。
22.优选的,穿孔工序中,采用扩径导板进行扩径,扩径导板的出口角度为6.0
°
~7.0
°
,穿孔辊的出口角度为6.0
°
~6.5
°
,扩径导板的间距为230mm~245mm,且穿孔顶头规圆
段的直径为224mm~230mm,穿孔辊距为205mm~215mm。
23.优选的穿孔工艺可使钢管达到24%-26%的大扩径效果,通过变形强化有效提高钢管的强度。
24.优选的,轧制工序中采用等径轧制,轧制后荒管的温度为1030℃~1050℃。
25.优选的,穿孔后毛管在轧制机前台旋转自然冷却,穿孔轧制的总间隔时间为65s,进轧机前通过水除磷去除毛管表面的氧化皮。
26.进一步地,轧制工序中,采用accu-roll轧制机进行轧制。
27.优选的,微张力减径工序中采用5~7架微张力减径机进行减径,且由第一架微张力减径机至第三架微张力减径机的减径率依次增大,第三架微张力减径机至最后一架微张力减径机的减径率依次减少,总减径率为5.0%~7.5%。
28.进一步地,微张力减径工序中,采用6架微张力减径机进行减径,其中,第一架微张力减径机的单架减径率为0.8%~1.2%,第二架微张力减径机和第三架微张力减径机的单架减径率均为1.2%~1.6%,第四架微张力减径机的减径率为0.5%~0.7%,第五架微张力减径机和第六架微张力减径机的减径率均为0.2%~0.3%。
29.优选的微张力减径工艺可避免厚壁钢管减径过程中金属流动不均匀产生内六方影响尺寸精度问题的出现,使得最终成品钢管的椭圆度≤0.5%d(d为公称外径),壁厚不均匀度≤12%t(t为公称壁厚)。
30.优选的,微张力减径工序中,微张力减径结束后钢管的温度为860℃~920℃。
31.优选的微张力减径温度和减径率,可提高相变时的形核率,抑制析出相的聚集和长大,有利于细化晶粒和改善组织,进而显著提高材料的强度和韧性。
32.本发明提供了一种厚壁无缝钢管,合金成分体系简单,通过合理的成分设计以及独特的大扩径-大减径的制备工艺,增加奥氏体向铁素体的相变比例,使得制备的无缝钢管具有细密均匀的铁素体+珠光体组织,且铁素体晶粒细小均匀,晶粒度达到8~9级,从而显著提高了无缝钢管的力学性能,使强度和韧性相匹配,无缝钢管的抗拉强度可达669mpa~712mpa,屈服强度可达481mpa~523mpa,屈强比为0.70~0.75;延伸率为22%~31%,室温横向夏氏冲击功为66j~145j,且制备过程无需轧制常化处理或正火处理,工艺简单,能耗较低,可有效提高厚壁无缝钢管的生产效率,降低生产成本,从而显著提高企业的市场竞争力,具有较高的推广应用价值。
附图说明
33.图1为本发明实施例1制备的高韧性厚壁无缝钢管的金相组织图。
具体实施方式
34.为了使本发明的目的、技术方案及优点更加清楚明白,以下结合实施例,对本发明进行进一步详细说明。应当理解,此处所描述的具体实施例仅用于解释本发明,并不用于限定本发明。
35.为了更好的说明本发明,下面通过实施例做进一步的举例说明。
36.实施例1
37.本发明实施例提供一种高韧性厚壁无缝钢管,其化学成分为:
38.c 0.25%、si 0.25%、mn 1.55%、v 0.06%、n 0.016%、alt 0.020%、s 0.012%、p 0.010%、ni 0.15%、cu 0.13%、nb 0.01%,余量为fe及不可避免的杂质。
39.上述高韧性厚壁无缝钢管的制备步骤如下:
40.以废钢为原料,经电弧炉熔炼、钢包精炼、连铸工序制成与上述厚壁无缝钢管化学组分相同的连铸圆坯(断面直径230mm);将连铸圆坯经环形炉加热、穿孔后制成毛管,毛管经轧制后得到荒管,荒管经微张力减径、自然空冷冷却,制成外径为269.88mm、壁厚为22mm的厚壁无缝钢管。
41.其中,钢包精炼工序中,分2次加入石灰、铝粒和碳化硅调渣,第一次加入是精炼送电开始,一次送电时间为18min,停电测温、取样,然后开始二次送电,第二次加入石灰、铝粒和碳化硅,使精炼渣碱度为5~6,同时,从底部吹入氩气保证熔池搅动良好,软吹时间为20min。
42.连铸工序中,连铸工序中,在钢包水口和滑板之间采用氩气保护,中间包钢液液面高度达到350mm时,向钢液表面快速添加覆盖剂隔绝空气,中间包到结晶器采用整体浸入式水口进行保护浇铸。
43.环形加热炉工序,环形炉加热工序中,按照连铸圆坯的输送方向将环形加热炉依次分为预热段、加热段和均热段,所述加热段分为加热一段、加热二段和加热三段,各段分别进行温度控制;其中,预热段采用无喷嘴燃烧的方式进行加热,加热段和均热段采用脉冲式喷嘴燃烧的方式进行加热,所述预热段的温度控制为900℃,所述加热一段的温度控制为1100℃,所述加热二段的温度控制为1260℃,所述加热三段的温度控制为1275℃,所述均热段的温度控制为1250℃,在炉加热时间125min。
44.穿孔工序中,采用两辊导板式穿孔机进行穿孔,扩径导板的出口角度为6.7
°
,穿孔辊的出口角度为6.3
°
,扩径导板的间距237mm,且穿孔顶头均整区的直径为226mm,穿孔辊距为211mm,穿孔后得到的毛管的外径为285mm~290mm,壁厚为24~26mm。
45.轧制工序中,采用accu-roll轧制机进行等径轧制,进轧机前通过水除磷去除毛管表面的氧化皮,穿孔后毛管在轧制机前台旋转自然冷却,穿孔轧制的总间隔时间为65s,轧制后荒管的温度为1040℃,轧制后得到的荒管外径为285~295mm,壁厚为20~22mm。
46.微张力减径工序中,微张力减径工序中,采用6架微张力减径机进行减径,孔型椭圆度为1.0-1.02,其中,第一架微张力减径机的单架减径率为0.97%、第二架微张力减径机的减径率为1.32%,第三架微张力减径机的单架减径率均为1.38%,第四架微张力减径机的减径率为0.64%,第五架微张力减径机的减径率为0.29%,第六架微张力减径机的减径率为0.21%,微张力减径结束后钢管的温度为880℃。
47.实施例2
48.本发明实施例提供一种高韧性厚壁无缝钢管,其化学成分为:
49.c 0.2%、si 0.35%、mn 1.45%、v 0.05%、n 0.020%、alt 0.040%、s 0.015%、p 0.015%、ni 0.23%、cu 0.18%、nb 0.03%,余量为fe及不可避免的杂质。
50.上述高韧性厚壁无缝钢管的制备步骤如下:
51.以废钢为原料,经电弧炉熔炼、钢包精炼、连铸工序制成与上述厚壁无缝钢管化学组分相同的连铸圆坯(断面直径230mm);将连铸圆坯经环形炉加热、穿孔后制成毛管,毛管经轧制后得到荒管,荒管经微张力减径、自然空冷冷却,制成外径为269.88mm、壁厚为22mm
的厚壁无缝钢管。
52.其中,钢包精炼工序中,分2次加入石灰、铝粒和碳化硅调渣,第一次加入是精炼送电开始,一次送电时间为16min,停电测温、取样,然后开始二次送电,第二次加入石灰、铝粒和碳化硅,使精炼渣碱度为5~6,同时,从底部吹入氩气保证熔池搅动良好,软吹时间为18min。
53.连铸工序中,连铸工序中,在钢包水口和滑板之间采用氩气保护,中间包钢液液面高度达到450mm时,向钢液表面快速添加覆盖剂隔绝空气,中间包到结晶器采用整体浸入式水口进行保护浇铸。
54.环形加热炉工序,环形炉加热工序中,按照连铸圆坯的输送方向将环形加热炉依次分为预热段、加热段和均热段,所述加热段分为加热一段、加热二段和加热三段,各段分别进行温度控制;其中,预热段采用无喷嘴燃烧的方式进行加热,加热段和均热段采用脉冲式喷嘴燃烧的方式进行加热,所述预热段的温度控制为800℃,所述加热一段的温度控制为1000℃,所述加热二段的温度控制为1240℃,所述加热三段的温度控制为1260℃,所述均热段的温度控制为1240℃,在炉加热时间130min。
55.穿孔工序中,采用两辊导板式穿孔机进行穿孔,扩径导板的出口角度为6.7
°
,穿孔辊的出口角度为6.3
°
,扩径导板的间距为230mm,且穿孔顶头均整区的直径为226mm,穿孔辊距为209mm,穿孔后得到的毛管的外径为285mm~290mm,壁厚为24~26mm。
56.轧制工序中,采用accu-roll轧制机进行等径轧制,进轧机前通过水除磷去除毛管表面的氧化皮,穿孔后毛管在轧制机前台旋转自然冷却,穿孔轧制的总间隔时间为65s,轧制后荒管的温度为1030℃,轧制后得到的荒管外径为285~295mm,壁厚为20~22mm。
57.微张力减径工序中,微张力减径工序中,采用6架微张力减径机进行减径,孔型椭圆度为1.0-1.02,其中,第一架微张力减径机的单架减径率为0.89%、第二架微张力减径机的减径率为1.32%,第三架微张力减径机的单架减径率均为1.38%,第四架微张力减径机的减径率为0.64%,第五架微张力减径机的减径率为0.29%,第六架微张力减径机的减径率为0.21%,微张力减径结束后钢管的温度为860℃。
58.实施例3
59.本发明实施例提供一种高韧性厚壁无缝钢管,其化学成分为:
60.c 0.3%、si 0.15%、mn 1.70%、v 0.10%、n 0.013%、alt 0.010%、s 0.008%、p 0.020%、ni 0.19%、cu 0.16%、nb 0.02%,余量为fe及不可避免的杂质。
61.上述高韧性厚壁无缝钢管的制备步骤如下:
62.以废钢为原料,经电弧炉熔炼、钢包精炼、连铸工序制成与上述厚壁无缝钢管化学组分相同的连铸圆坯(断面直径230mm);将连铸圆坯经环形炉加热、穿孔后制成毛管,毛管经轧制后得到荒管,荒管经微张力减径、自然空冷冷却,制成外径为269.88mm、壁厚为22mm的厚壁无缝钢管。
63.其中,钢包精炼工序中,分2次加入石灰、铝粒和碳化硅调渣,第一次加入是精炼送电开始,一次送电时间为15min,停电测温、取样,然后开始二次送电,第二次加入石灰、铝粒和碳化硅,使精炼渣碱度为5~6,同时,从底部吹入氩气保证熔池搅动良好,软吹时间为16min。
64.连铸工序中,连铸工序中,在钢包水口和滑板之间采用氩气保护,中间包钢液液面
高度达到300mm时,向钢液表面快速添加覆盖剂隔绝空气,中间包到结晶器采用整体浸入式水口进行保护浇铸。
65.环形加热炉工序,环形炉加热工序中,按照连铸圆坯的输送方向将环形加热炉依次分为预热段、加热段和均热段,所述加热段分为加热一段、加热二段和加热三段,各段分别进行温度控制;其中,预热段采用无喷嘴燃烧的方式进行加热,加热段和均热段采用脉冲式喷嘴燃烧的方式进行加热,所述预热段的温度控制为000℃,所述加热一段的温度控制为1200℃,所述加热二段的温度控制为1270℃,所述加热三段的温度控制为1290℃,所述均热段的温度控制为1270℃,在炉加热时间120min。
66.穿孔工序中,采用两辊导板式穿孔机进行穿孔,扩径导板的出口角度为6.7
°
,穿孔辊的出口角度为6.3
°
,扩径导板的间距为245mm,且穿孔顶头均整区的直径为226mm,穿孔辊距为215mm,穿孔后得到的毛管的外径为285mm~290mm,壁厚为24~26mm。
67.轧制工序中,采用accu-roll轧制机进行等径轧制,进轧机前通过水除磷去除毛管表面的氧化皮,穿孔后毛管在轧制机前台旋转自然冷却,穿孔轧制的总间隔时间为65s,轧制后荒管的温度为1050℃,轧制后得到的荒管外径为285~295mm,壁厚为20~22mm。
68.微张力减径工序中,微张力减径工序中,采用6架微张力减径机进行减径,孔型椭圆度为1.0-1.02,其中,第一架微张力减径机的单架减径率为1.13%、第二架微张力减径机的减径率为1.32%,第三架微张力减径机的单架减径率均为1.38%,第四架微张力减径机的减径率为0.64%,第五架微张力减径机的减径率为0.29%,第六架微张力减径机的减径率为0.21%,微张力减径结束后钢管的温度为920℃。
69.实施例1-3制备的无缝钢管的组织主要为铁素体+珠光体,晶粒细小,晶粒度为8~9级,其中,实施例1制备的无缝钢管的金相组织如图1所示。
70.按照api spec 5ct第10版的标准要求从实施例1-3制备的无缝钢管中任意取样分析其屈服强度(rt
0.5
)、抗拉强度(rm)、延伸率(a)、室温横向冲击功(21℃,tv试样尺寸10*10*55mm),其统计分析结果如表1所示,其中,表中的样本数为所取的无缝钢管的个数,采取随机取样方式。
71.表1
[0072][0073][0074]
综上所述,本发明的厚壁无缝钢管成分体系简单、制造成本低,且强度、韧性匹配度高,可广泛用于环境恶劣、地质复杂区域的油井开采,具有广阔的市场前景。
[0075]
以上所述仅为本发明的较佳实施例而已,并不用以限制本发明,凡在本发明的精
神和原则之内所作的任何修改、等同替换或改进等,均应包含在本发明的保护范围之内。